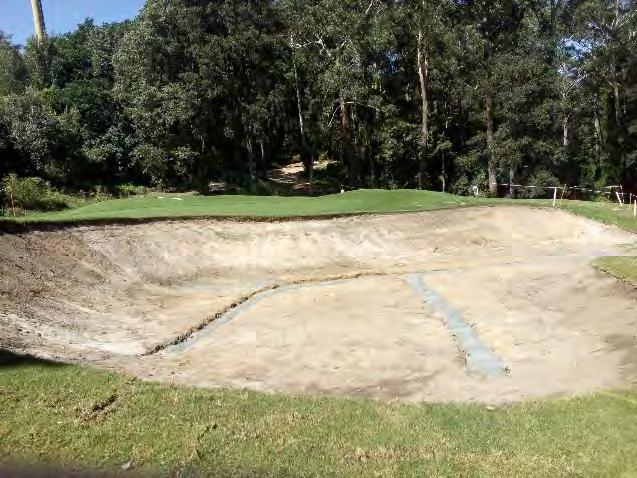
19 minute read
A hiatus.
Unfortunately, the cost of continuing using the same technology for the remaining bunkers, along with the supplier of the capillary concrete no longer assuring supply, meant the program was placed on hold.
The decision of club members to support the major redesign and rebuild of the clubhouse in 2017 temporarily limited funding for major work on the course.
In late 2019, when Steve Walker was re-elected President, he identified rebuilding the remaining bunkers as the highest priority project. The decision was made to completely rebuild most bunkers by scraping them back to the base material, removing the old drainage and any intruding roots etc, changing the profile to ensure shallower bunkers with flat base area, and then rebuilding with improved drainage, relining with Biddum liner, and filling with the high quality Elite sand, identified by Richard Kirkby as the best available. The program commenced in May 2019 and by October 2019, 23 of the 48 greenside bunkers had been fully refurbished. The program was put on hold and resumed in March 2020 and the remaining greenside bunkers were completed by June 2020. The fairway bunker refreshment program started in June, and all fairway bunkers had been reworked by September 2020.
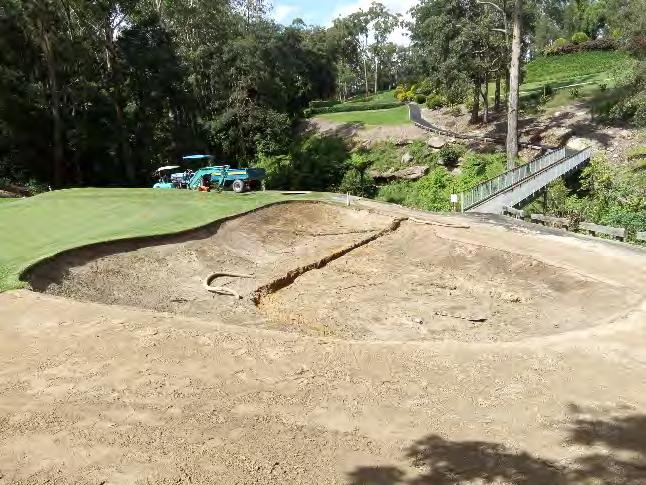
The next stage.
In 2019, the Board started a program which when completed would involve a redesign and rebuild of the green complexes (greens, bunkers and surrounds), and also investigation of the feasibility of reconfiguring holes 1, 2, 3 and possibly 5 to reduce the balls out of bounds risks. The greens are very old, most built in the 1950s and 1960s. They are inadequately drained and subject to disease. Re-building them, and the allied work on the bunkers and surrounds, is considered vital for the longer term viability and competitiveness of our Club.
In 2022, the Black Night Group were engaged to produce a concept design for the course, to achieve these objectives. The draft proposed design was presented to several focus groups to receive member feedback.

Our b ridges.. the dreams of our club forebears are now a reality. Our bridges are SO important, they need repair and even replacement.

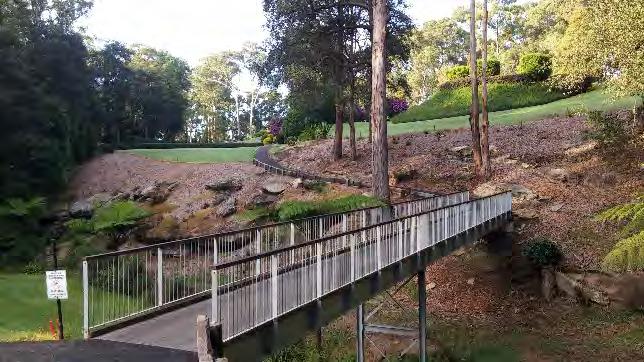
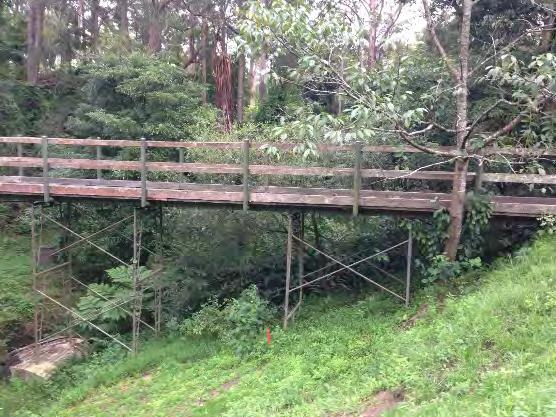
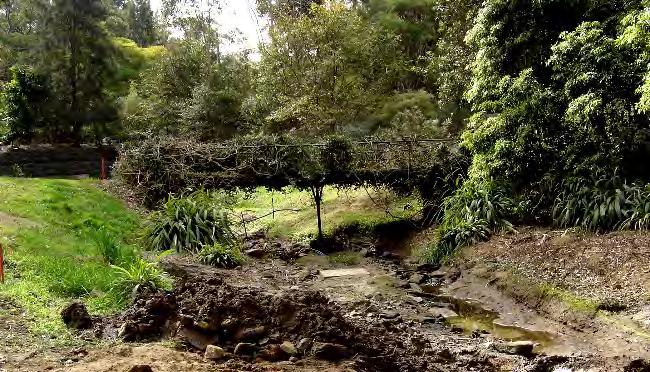
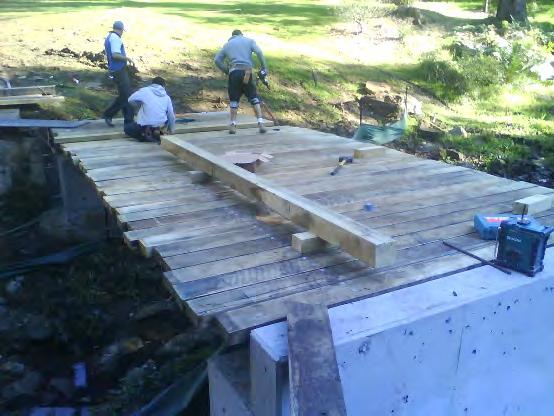
Our bridges… the dreams of our Club forebears are now a reality.
The gully through which Devlins Creek runs has been a challenge for Club members since the start of the Club. Bridges have forded the gully at four points and now provide easy access for members and ground staff alike.

In brief, up until 1999, there was a high level bridge serving the 1st and 18th holes built in 1961, (rebuilt in 2010), a low level bridge at the 1st built in 1965 (replaced in 2009), the 10th in 1964, (reworked in 2013) and the 9th in 1985 (replaced 2016).
The ravages of time made it necessary to perform extensive maintenance and/or remedial work on all the bridges as noted in the bracketed dates above.
Low level Bridge in front of 1st Tee
44 years after its original construction, the low level bridge across the creek below the 1st tee, which had given vehicular access to the clubhouse from the course for the first time in 1965, needed replacement. This was to be able to cope with the increased traffic, both in terms of frequency, but also in terms of the size and weight of course equipment and golf carts, which were now in much more frequent use by golfers.
Photos taken during the removal of the old structure show clearly that it had reached its ‘use by date’ and posed potential safety issues and risks.
The new structure was proposed in January 2009 and completed in July 2009.
The new structure was located a little to the north of the old bridge. Club member, Peter Trickett, through his structural consulting company designed the steel beams to span the creek.

All the other trades were organized and work was carried out under the supervision of Club Captain Rob Stevenson, whose experience in the construction industry was invaluable. His construction company carried out the work ‘at cost’ for the Club. The work was achieved for the pre-work budget of around $27-30 K.
The location of the bridge posed logistical problems to manage the lifting and installation of the steel beams.
The beams were 10m long and the use of a crane would have caused significant damage to the course and was therefore rejected. The beams were successfully installed with the help of the Club’s course machinery.
During construction, a temporary low level bridge was constructed in front of the 18th tee, to provide for vehicular course traffic. The new structure has robust concrete footings and heavy steel beams to span the creek and provide support for the timber decking.

High level bridge between 1st Tee and 18th Tee
Built in 1961 after many years of ‘hope and expectation’, in 2010 the high level bridge serving the 1st and 18th holes was found to be deteriorating to the point that some boards underlying the rubber / asphalt decking appeared to be full of rot. When removal work commenced it was quickly apparent that the deterioration was not only rot but aided and abetted by significant termite activity. When the old carriage way was removed it was found that there were three to four layers of resurfacing overlaying the timber boards.
The use of timber decking in the original bridge construction was less than ideal as in August 1964, three years after construction, maintenance was required on the bridge. It was suggested that prior to the Eisenhower Cup teams using the course in September for practice, the bridge should be more firmly stayed as a significant gallery was expected to follow the players. The timber decking, while providing an adequate surface for foot traffic, did not provide any stability against lateral movement and was deemed to sway under heavy traffic.
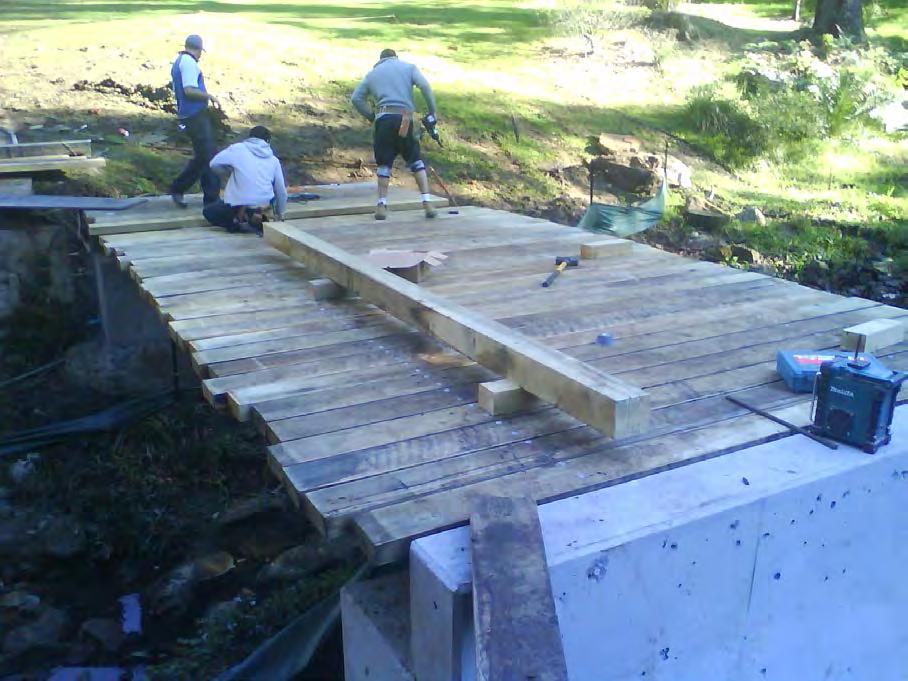
A steel angle strut was placed on one side between the decking near the centre and connected to an adjacent eucalypt. There were concerns that an additional stay may be required on the other side. However this was found not to be necessary. The stay remained in place until the new decking was installed in 2010. The strut can be seen connecting the bridge to the tree in the left.
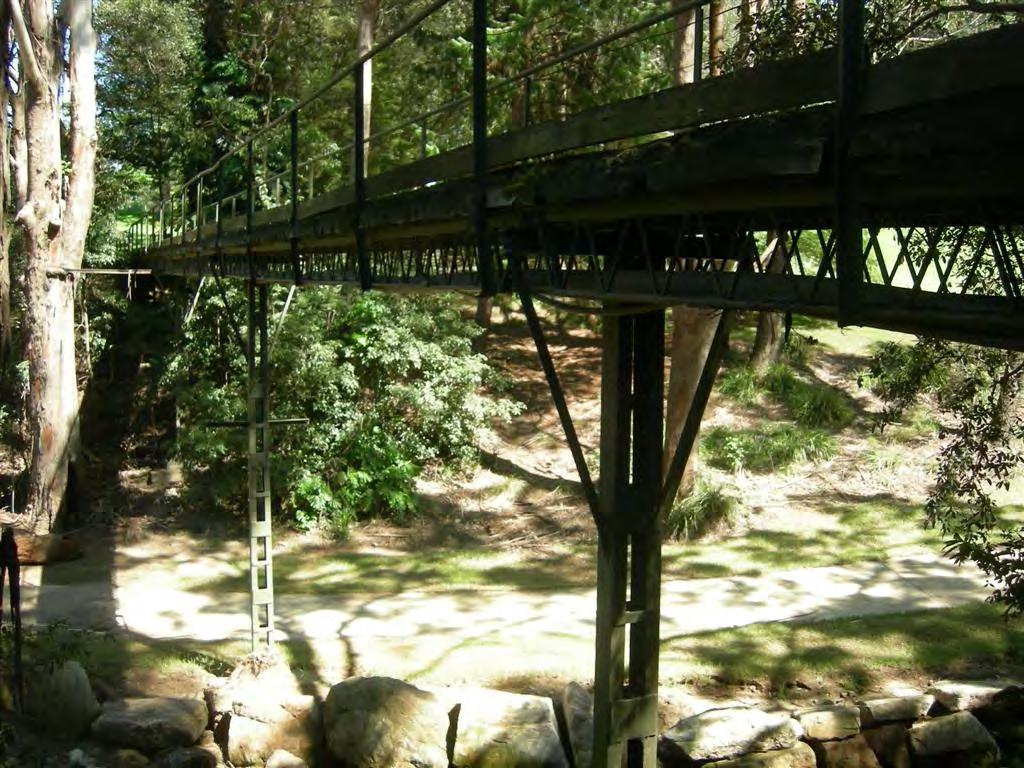
During reconstruction in 2010, Rob Stevenson recounts that being on the bridge prior to the placing of the concrete, there was significant lateral movement.
The design of the new carriageway was carried out by Peter Trickett and his consulting company. Their innovative design allowed the rapid installation of steel frames into which Bondek formwork was placed.
Concrete was poured into the formwork and this provided a strong deck platform. The lateral stiffness provided by the steel frames and the concrete overcame the need to persist with the stabilizing strut.
New hand-railing was bolted onto these frames, to provide protection to the concreters when placing the concrete.
Work on the bridge was organized and carried out by Rob Stevenson’s construction company ‘at cost’ to the Club.
The pillars and steel span structure of the original bridge were still sound, however the footings for the steel pillars were strengthened with additional concrete in 2014, to help avoid possible erosion when flash flooding occurred in the creek.
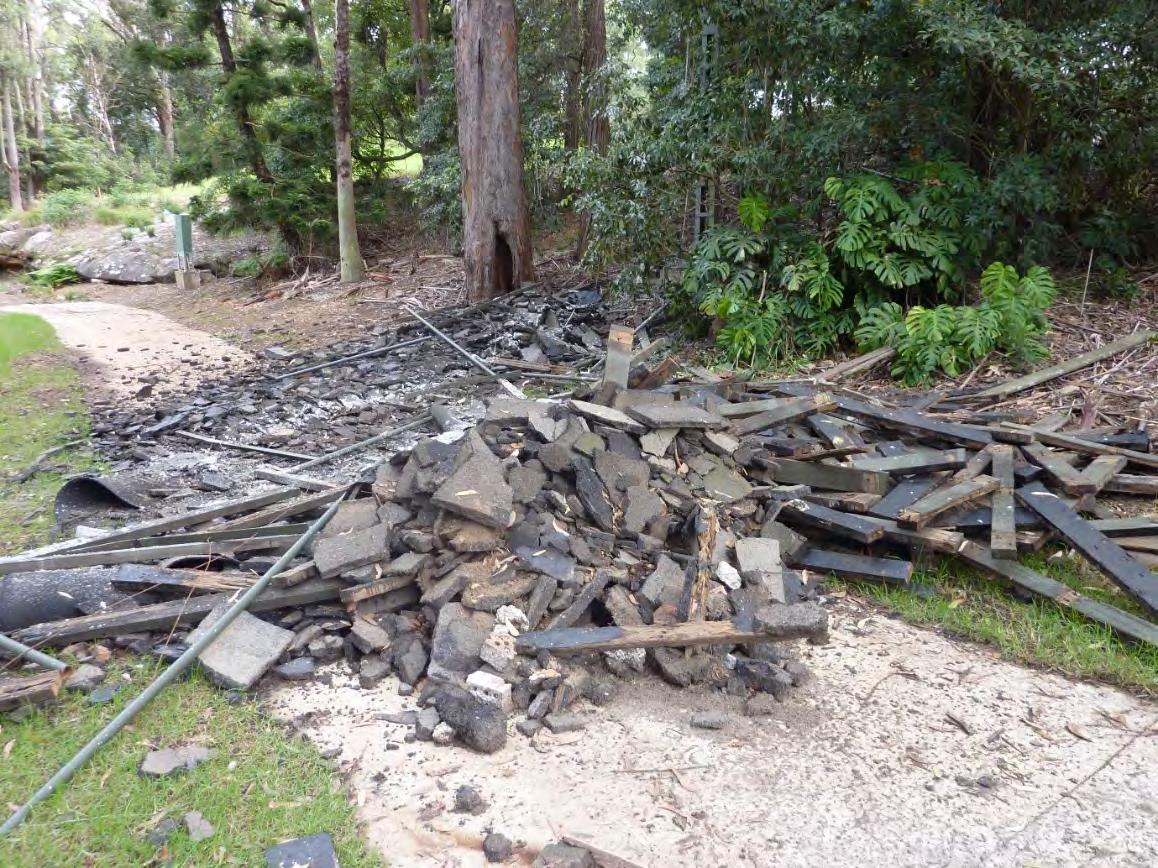

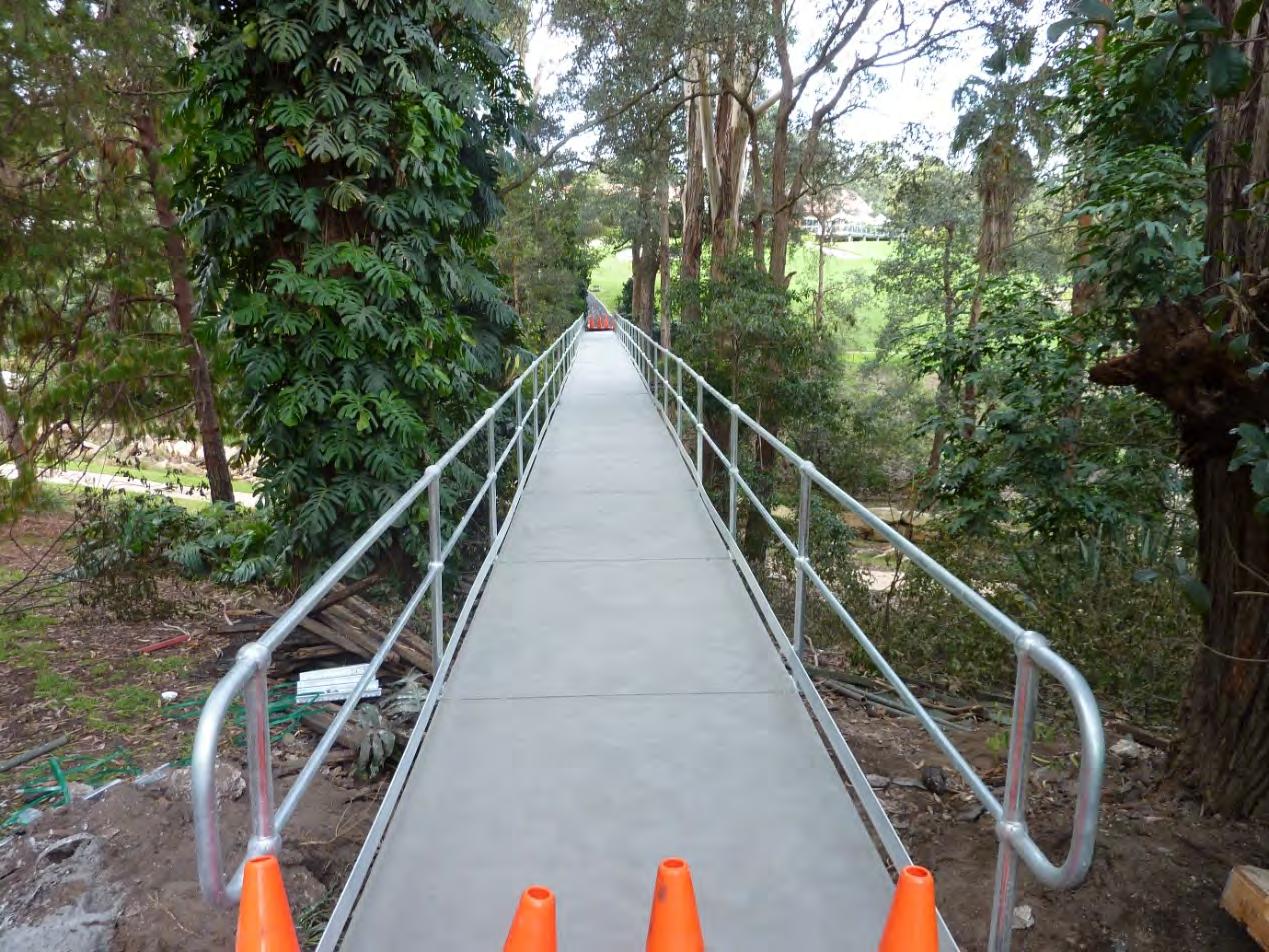
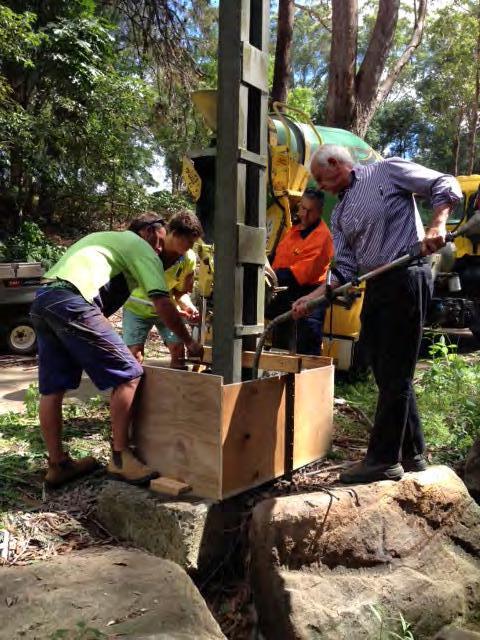
10th Bridge
The concrete span bridge across the gully leading from the 10th tee was opened in 1964. It replaced the original ‘swing’ bridge which had been the first bridge built in 1927. It was a prestressed concrete span costing £3600 and was opened in October 1964, a date scribed in the concrete pylon of the old swing bridge.
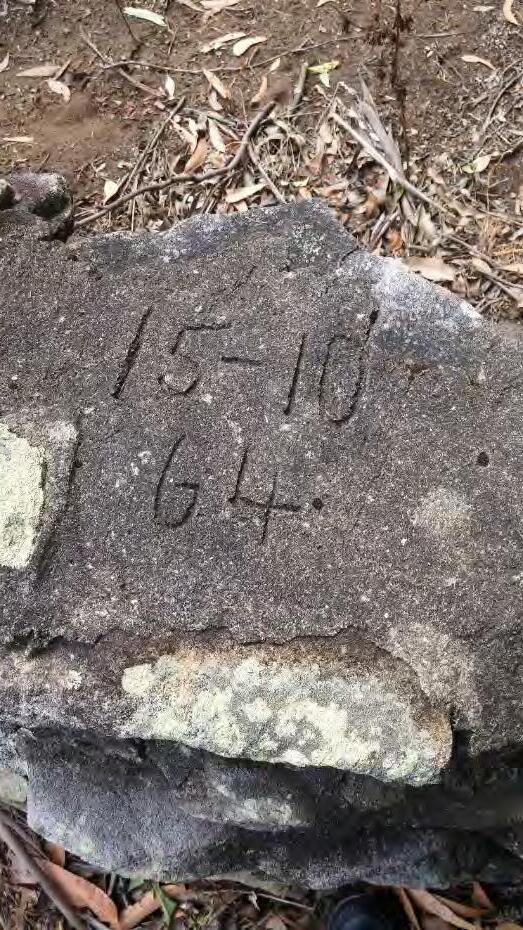
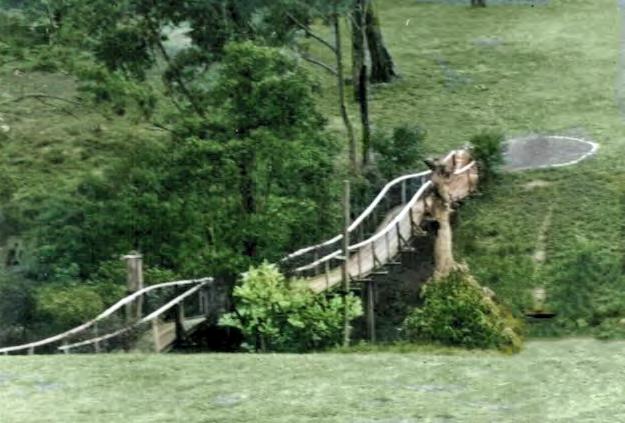
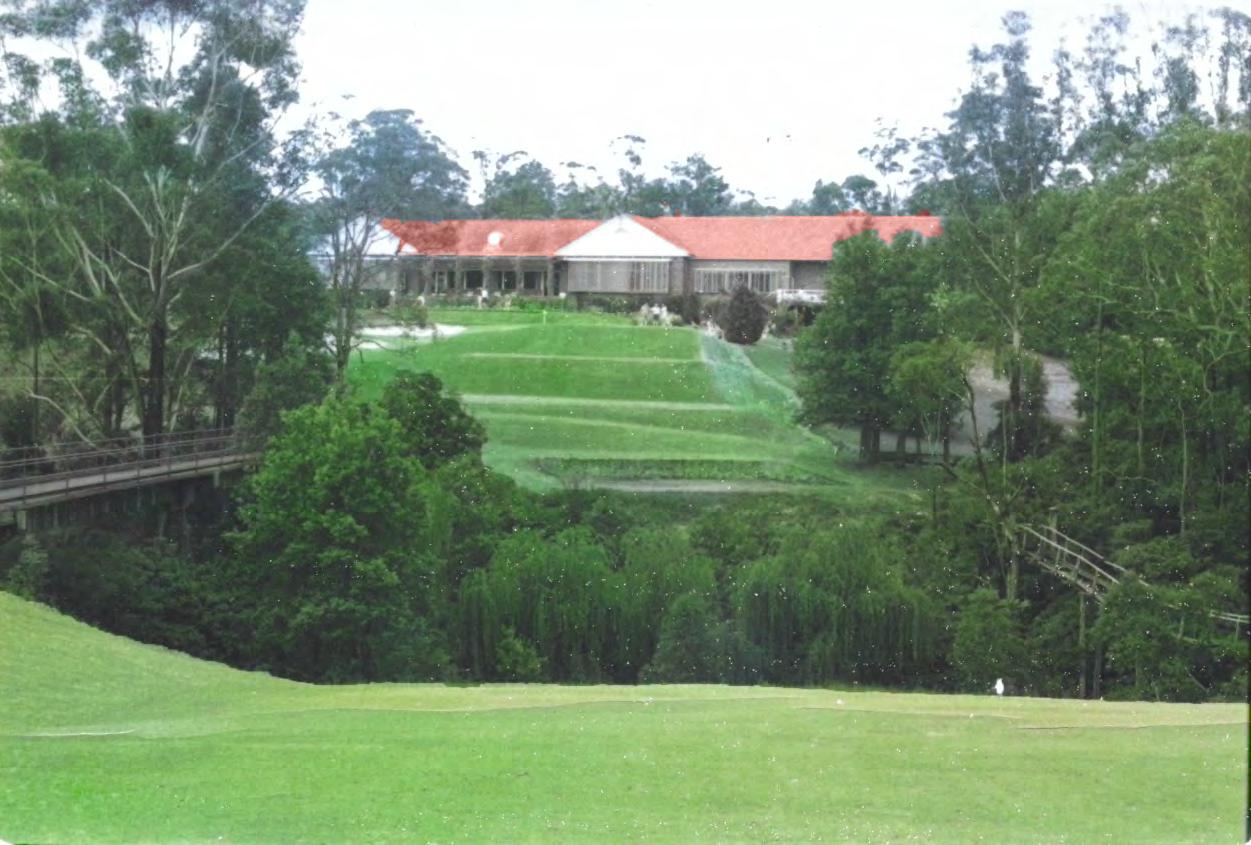
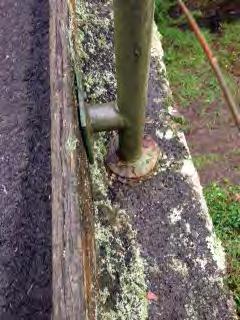
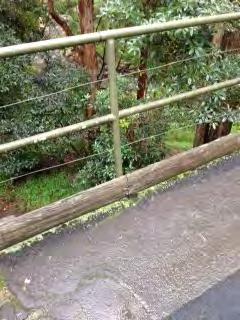
Disaster !
Late in the afternoon of Saturday 15 December 2018, a massive storm, somewhat akin to a mini–tornado blew through the golf course and adjacent district. It tore down many trees and branches throughout the course. It uprooted a massive eucalypt adjacent to the clubhouse end of the 10th bridge and it fell across the first span and completely demolished it.
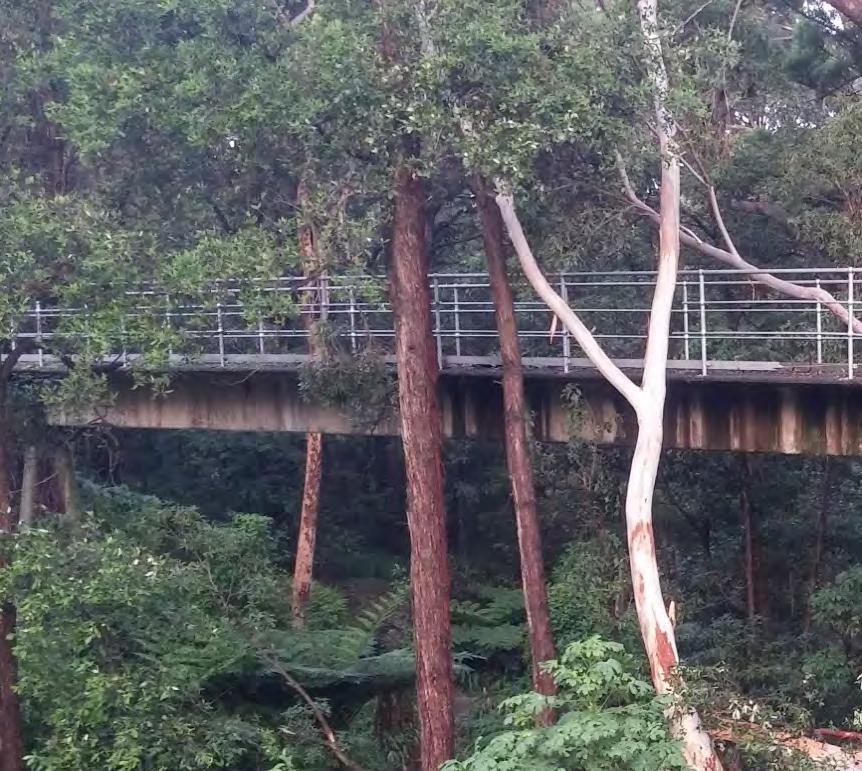
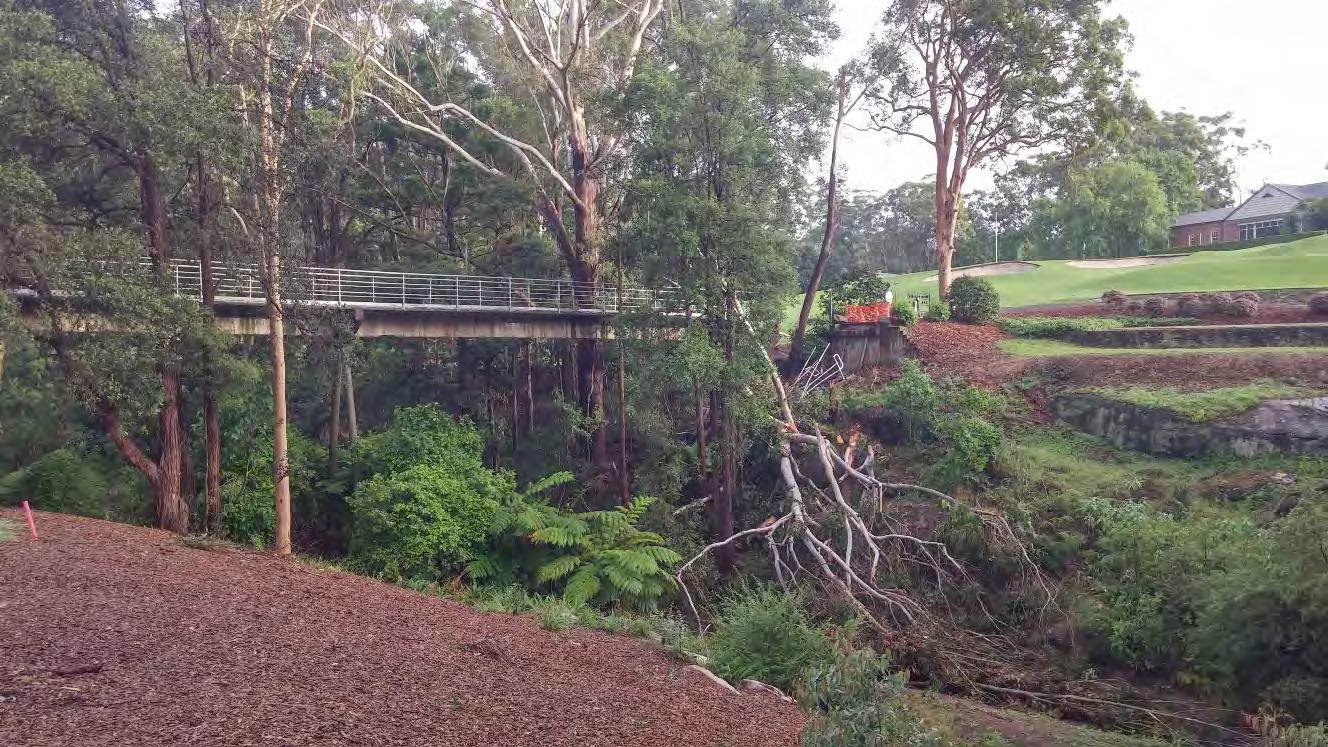
The process to repair or replace the bridge was a frustrating one for members and no doubt for the Board also. While this process was happening, members hitting off the 10th tee, needed to progress to the 10th fairway by way of the 9th bridge and a pathway constructed through the trees between the 8th green and 10th fairway. This added extra time to each round.
The process to repair or replace the bridge was first to assess whether there had been structural damage to the support pillars either through movement or even structural damage. Engineering assessments were carried out both by the Club, and by the insurer and there was extensive negotiation before it was decided that only the broken span required replacement and not the whole structure. The new span replacement design was a steel frame which spanned the gap, and was then infilled with concrete.
However an important issue arose as a result of the changes to State laws relating to safety compliance standards. While the bridge would not have been required to comply with the new standards if there had been no damage, any new work required compliance. This added significant cost as the standards required the side railings to meet high impact standards, to protect the vehicles which use the bridge and also required the infill to be all closely spaced vertical members to prevent climbing footholds.
The resulting design of the side railings was quite massive compared with the earlier rail and post structure. However, the problems did not end there.
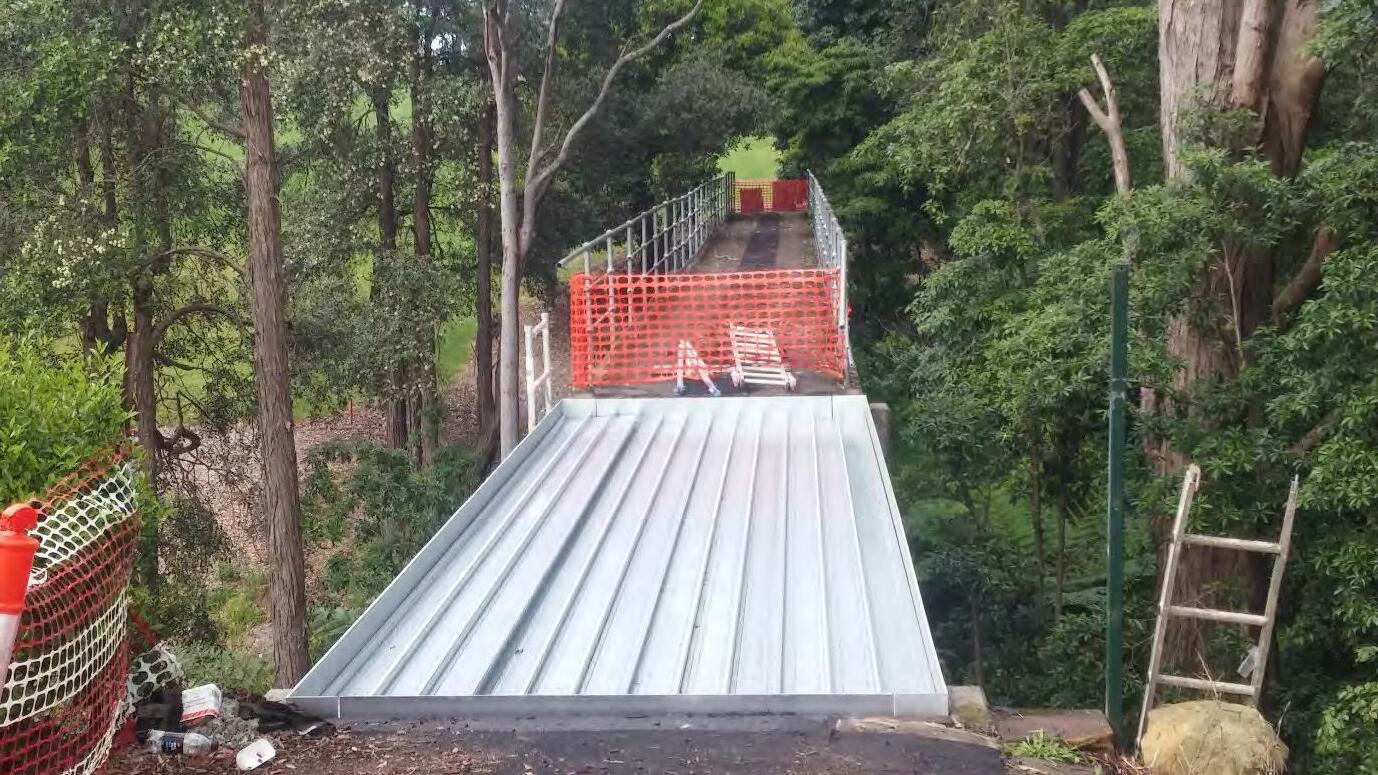
The design of the original prestressed beam was such that the thickness of the decking at the edges where the new side railings were to be secured, was only 50 mm. This was considered to be now too thin to support the stronger fence now demanded for the bridge. An innovative solution now was required to allow the fence to be secured to the bridge deck.

The design was for fabricated steel angles which were placed at the point where each vertical post was to be fixed and extended to provide extra support for securing the posts.
Whilst this design was being approved, the bridge, with the new span but the original fencing, was allowed to be used for pedestrian traffic, but all carts still had to access the 10th fairway via the 9th bridge.
The work was all completed in December 2019, just over one year after the day of the storm.
Bridge at 9th
The bridge across the gully at the 9th hole had been installed in 1985 as a ‘temporary’ solution to replace the earlier bridge which had been ruled as unsafe by a structural engineer. There had been reluctance by the Board over a number of years to spend the major money to replace the existing bridge, which was deteriorating, because of possible major changes to the design layout of the course arising from the possible acquisition of a significant part of the golf course by the Department of Main Roads to accommodate the future M2 motorway.
The earliest photo of a bridge at the 9th, is of the then President E J Hyde and his son, crossing it in 1925.
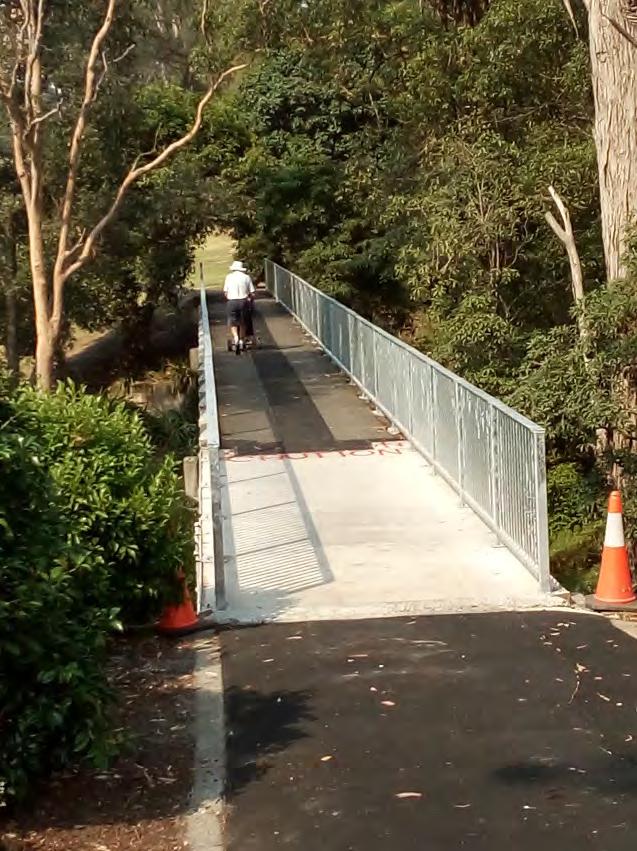
There was a subsequent bridge built at a higher level in 1940 but unfortunately no known photographs exist of it. It was built using timber from on the course, and over the years suffered ravages of termite and weather damage, but was kept safe and operational for over 45 years.
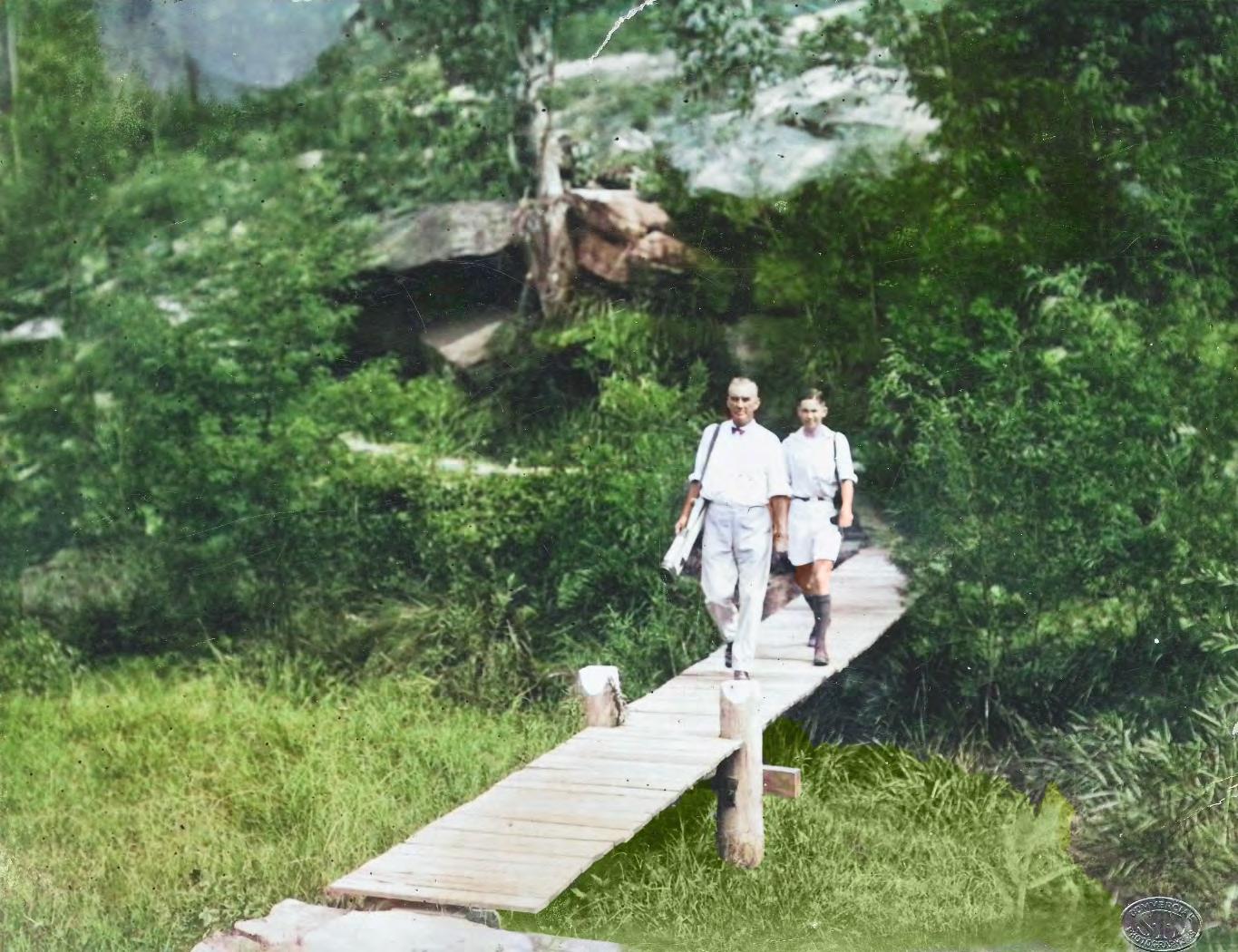
The next bridge, which was erected in 1985, was a forced decision as the state of the bridge, in spite of the continual repairs and maintenance, was considered to have become a danger to staff and members using the bridge. This replacement bridge when installed, was considered to be a ‘temporary’ solution. It was supported by a scaffold of steel pipes.
However over the years, this bridge too constantly needed to be maintained with repairs. In 2003, during a flash flood in Devlins creek, the footings were badly eroded and had to be replaced. In 2005 it was necessary to replace many deck timbers because of rotting along with some underlying timber beams.
.
Eventually it was recognised that the bridge needed replacement with a properly designed bridge suitable for all traffic and with a long life and low maintenance requirement. In 2013 the steel scaffold and support structure was found to be corroding and the bridge required replacement rather than repair. The ‘temporary’ bridge had lasted for over 30 years and the Board decision to purchase the steel scaffold rather than lease it ultimately proved to be a wise choice.
In the first week of June 2016, 273mm of rain fell and following wind, a large tree on the 9th tee side of the bridge fell across the path taking out other trees, the protective barrier on the right and badly damaged the pathway.
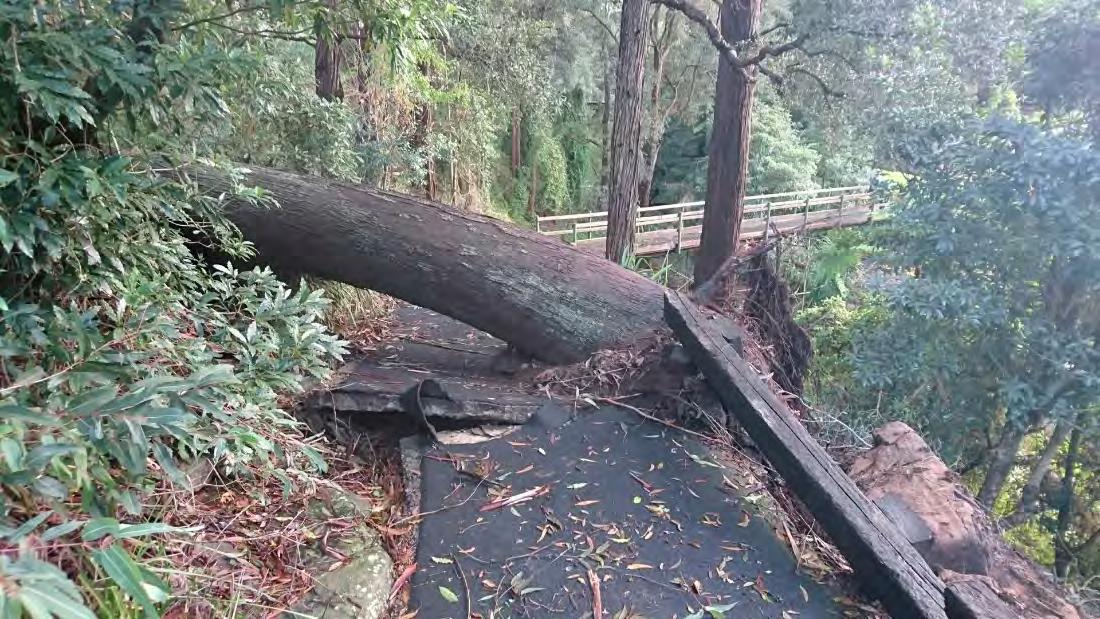
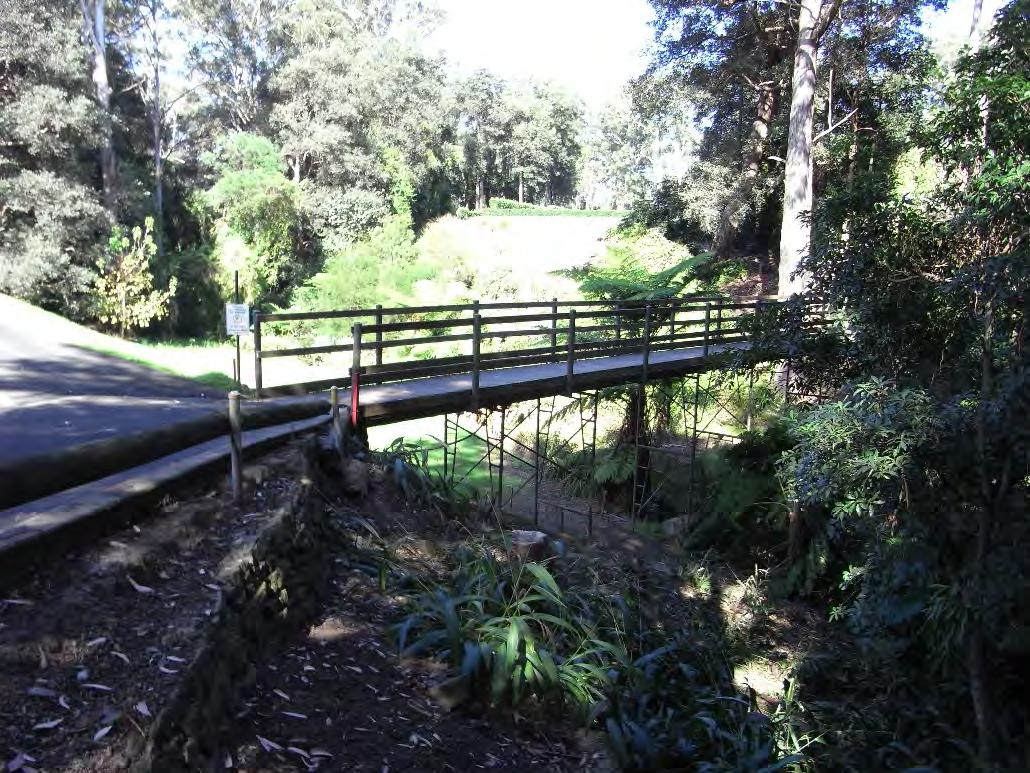
Some felt it unfortunate that it did not fall onto the old bridge as it might have attracted insurance! However, at that time the decision to replace the old bridge had been made and the installation of the new bridge was imminent.
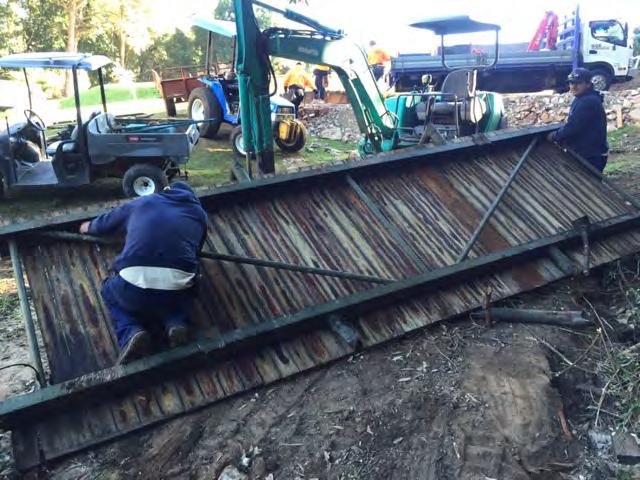
A new bridge was designed by Fleetwood Urban and was installed in June 2016 in the same location as the bridge being replaced.
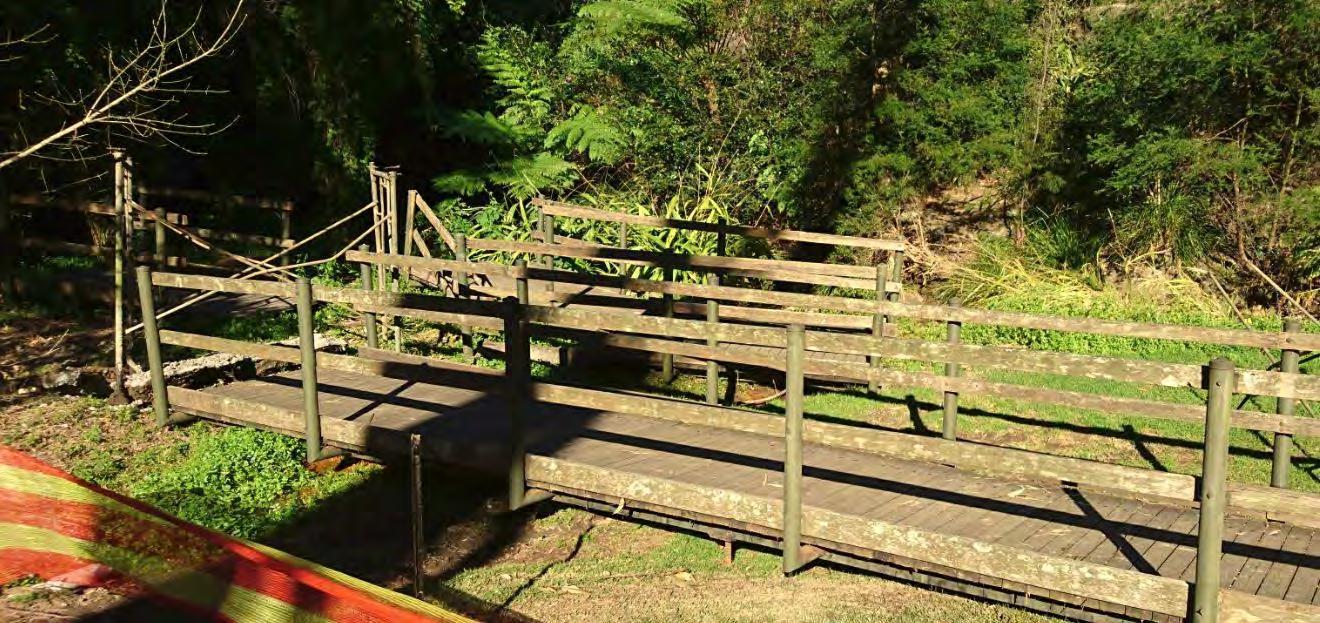

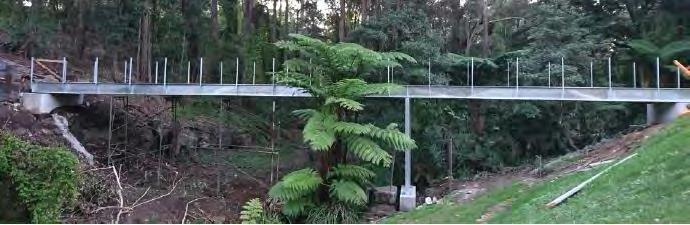

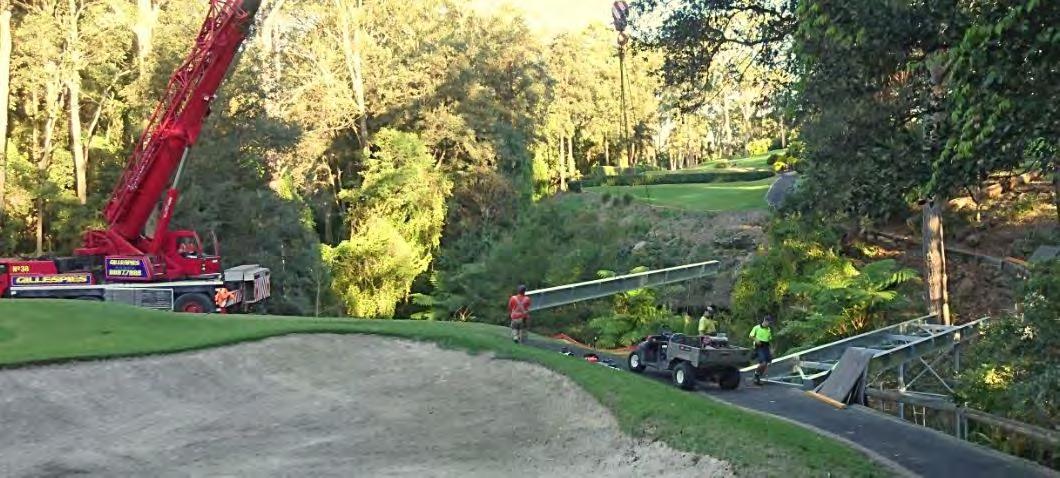
To cater for carts, it was necessary to cut into the bank on the left of the path from the 9th tee. Additionally at the corner turn onto the bridge, some of the large rock had to be removed to provide a safe width for carts to turn in either direction.
In December 2018, a mini tornado blew through the course causing many trees to fall. Several trees on the left of the path from the tee fell, but fortunately caused no damage to the bridge or path.
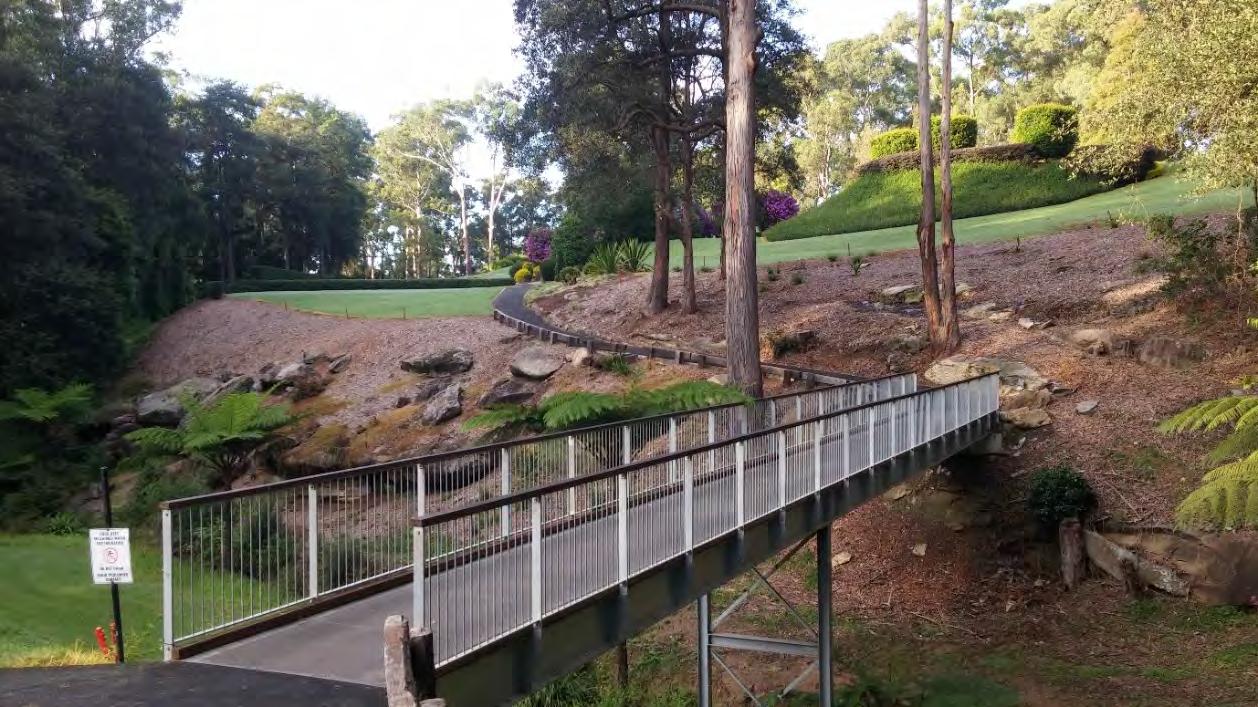
The new bridge is unlikely to need any sort of ongoing maintenance and is structurally so strong, its expected lifetime should be longer than that of even the youngest current Club member.
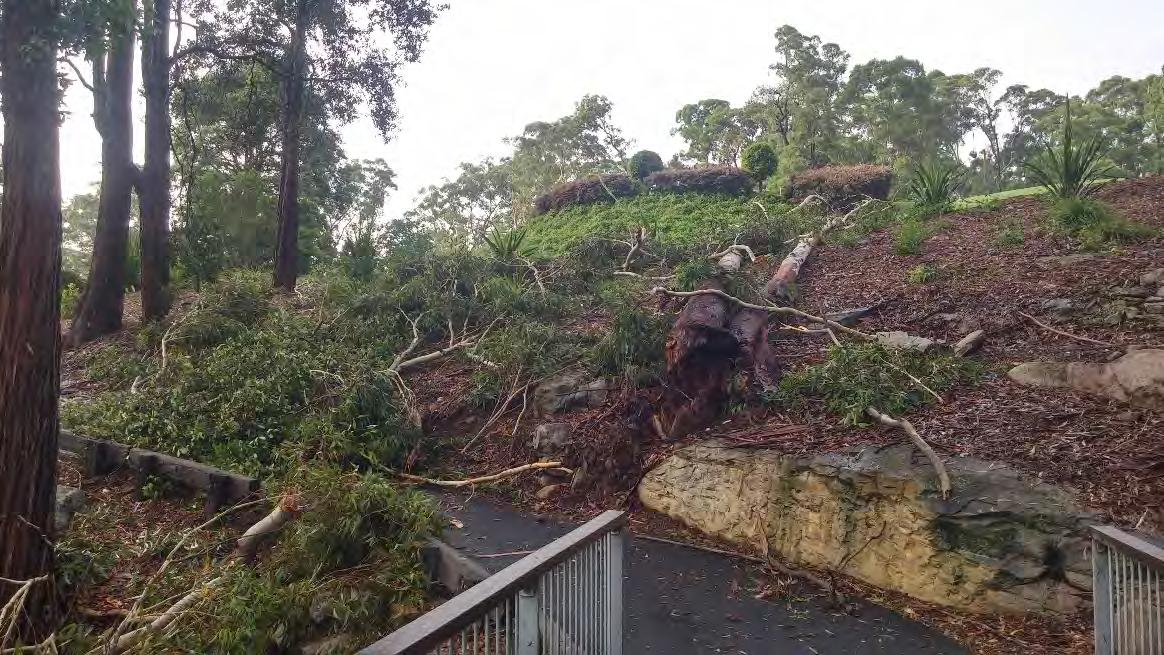
The bridge cost was $165,000 + GST.
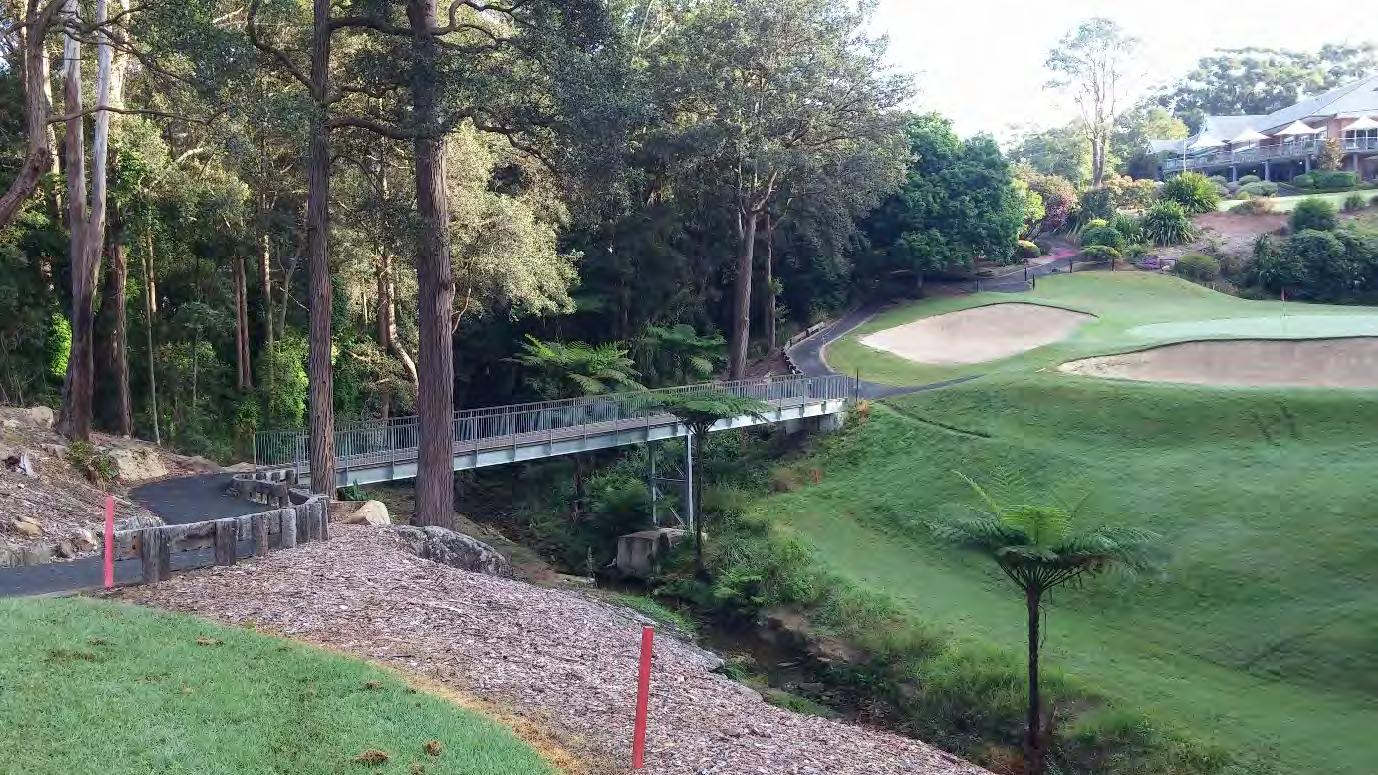
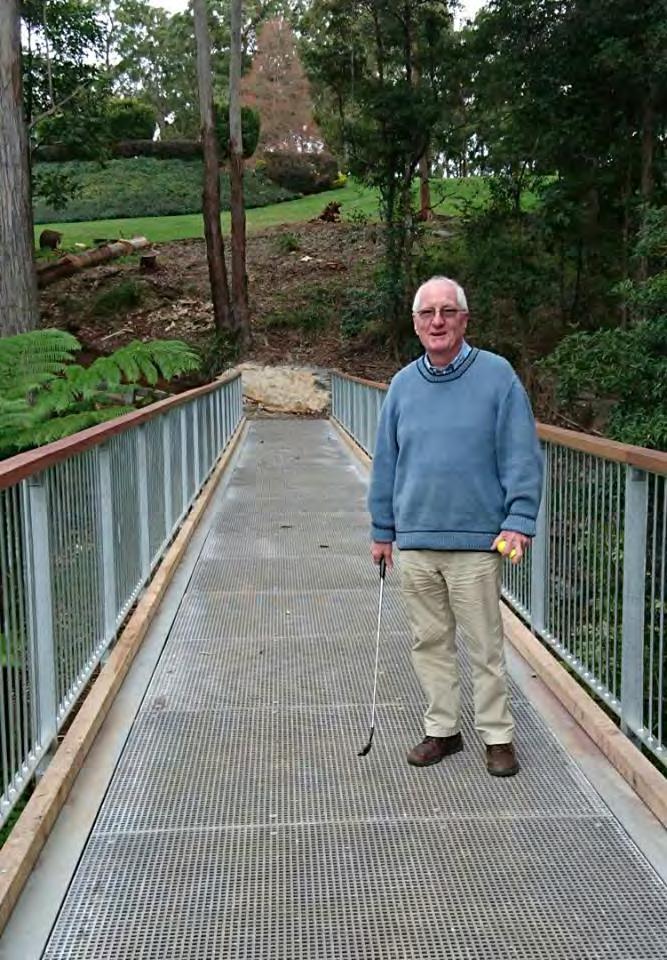
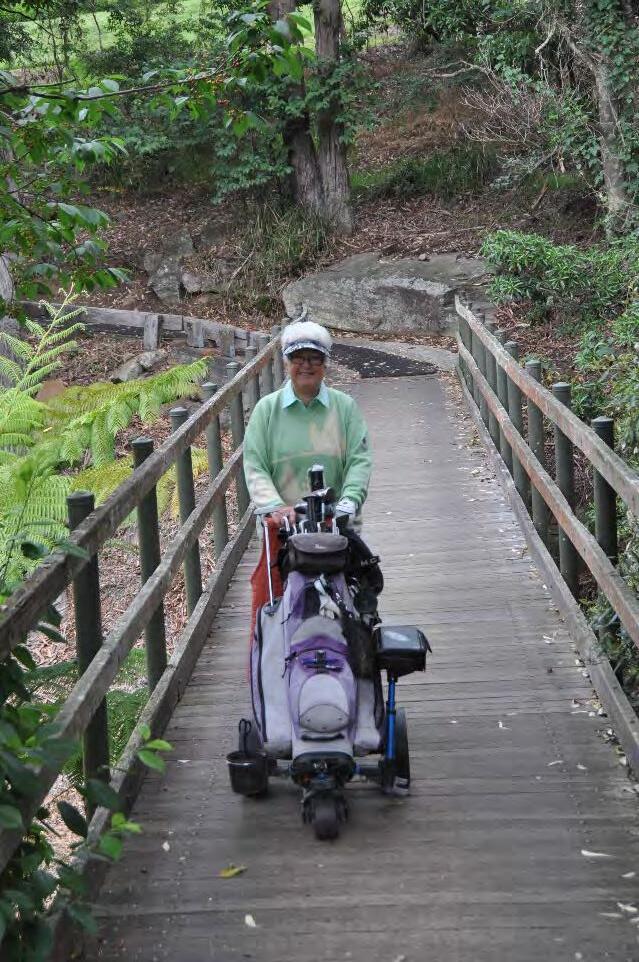
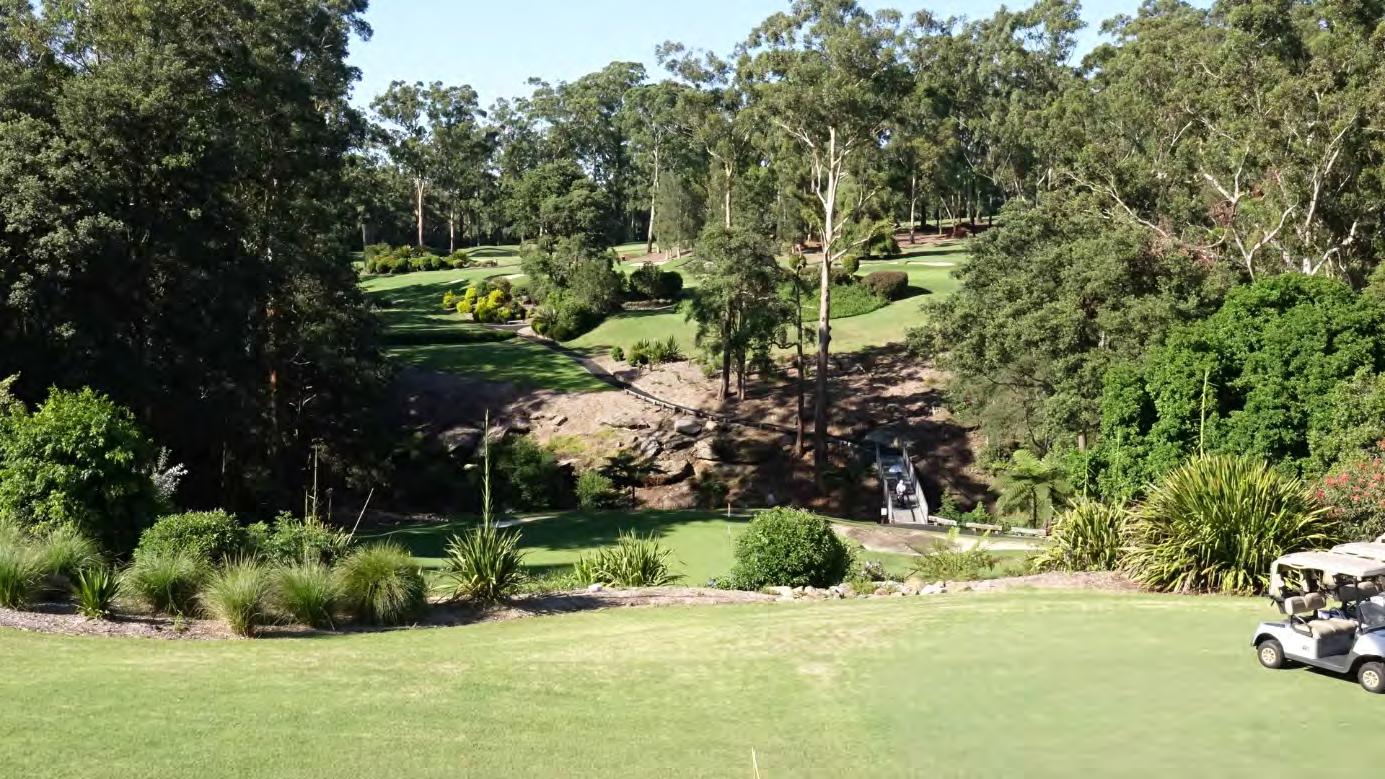
From wood chips to concrete/Rubaroc

Not quite a “super highway” yet!
From the early years, all paths throughout the golf course were either dirt or covered with some form of mulched vegetable material. Extensive permanent concrete paths were an expense beyond the budget of the Club for many years. In later years apart from cost, this solution had been chosen because of the long running threat by the Department of Main Roads, to possibly resume a major slice of the golf course, to use for the future M2 motorway. Successive Boards were extremely reluctant to commit capital to any area which might require replacement if the course needed major redesign should the acquisition occur. The threat was not removed until January 1996, when the RTA advised their road design would not require any Club land.
Paths around clubhouse.
In the garden areas adjacent to the clubhouse, 1st tee, pro shop and putting green, the path layout and surface material changed with each different layout of the garden beds.
The path leading to the terrace and past the putting green was flag stones
From the mid 1950s until the mid 1990s, the garden beds were filled with impressive displays of bright coloured annuals and beds of roses.
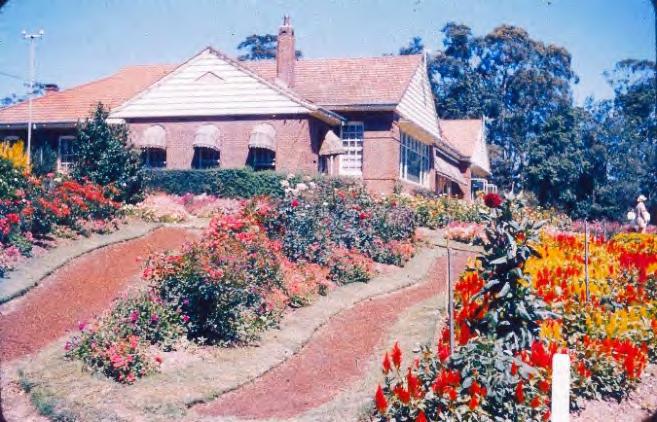
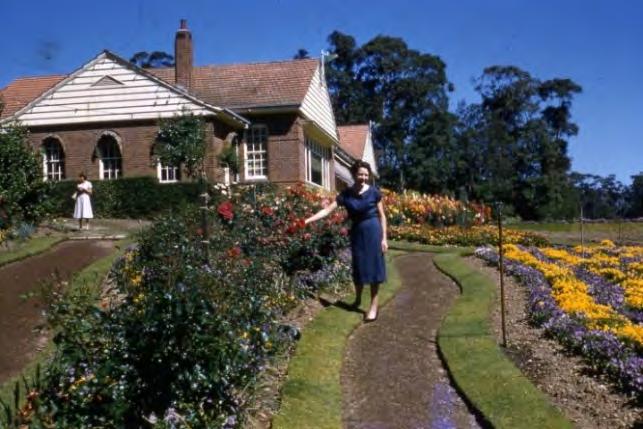
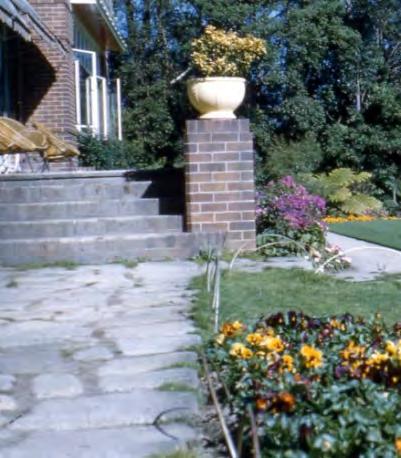
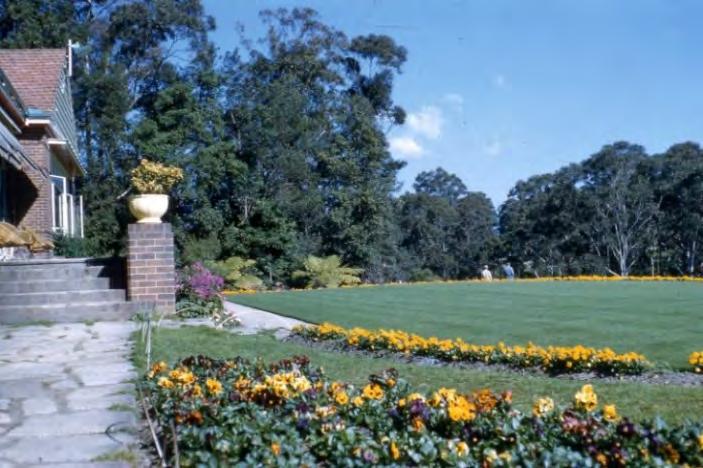
For the Australian Bi-Centenary year 1988, the Club prepared the gardens with a wonderful display as seen in the photo below.
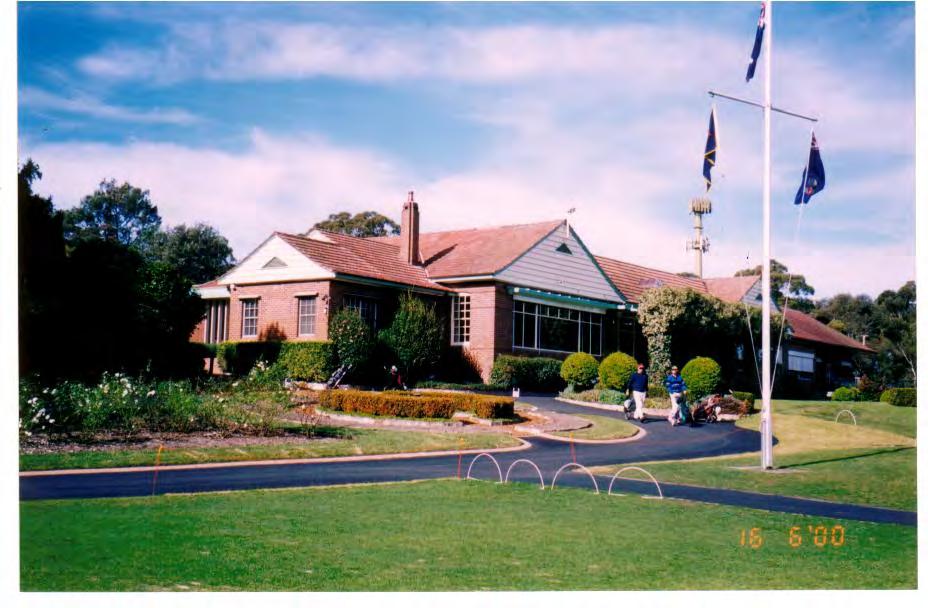
The aerial photo taken of the Bi centenary gardens, shows the path layout which linked the carpark, clubhouse, pro-shop, putting green and 1st tee. There was no path to the left of the 1st tee leading to the bridge. This was installed by 1993.
Photos of the gardens from these early years show the materials used to form the paths. Around the gardens, the paths were covered with fine eucalypt mulch and later reddish bark. The edges did not have concrete or stone edging until the 1980s and 90s when the layout was formalised.
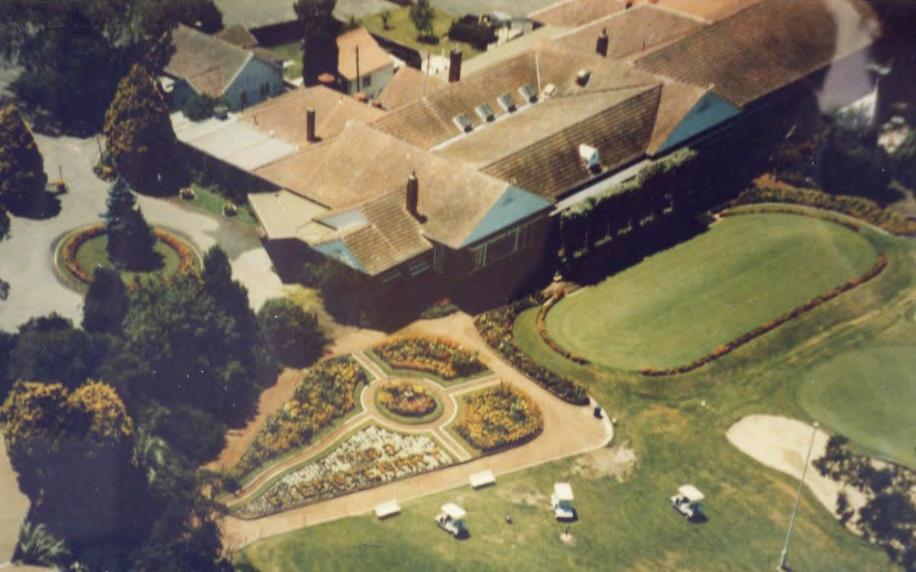
In 1969, Syd Gresham, Tony Gresham’s father, donated a sundial, which was mounted on a sandstone pedestal and made the centre piece of a circular garden.
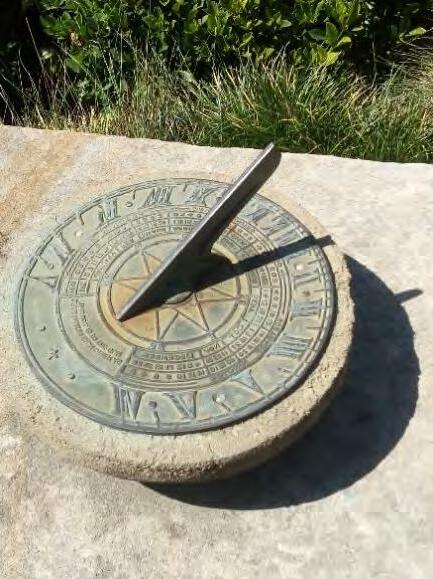
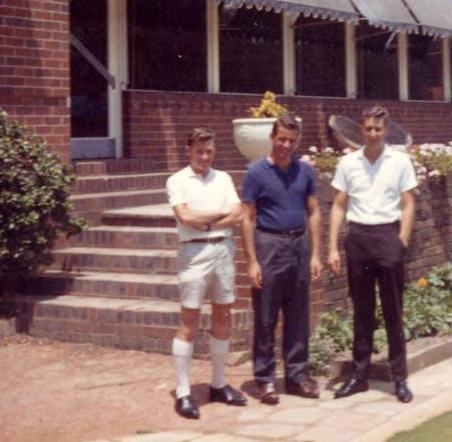
There was a formal path made of sandstone flagstones which led to the steps of the Beecroft Terrace from these mulch covered paths, and then with a single step down, across the front between the terrace and the putting green. This had been laid in the 1950s and was only wide enough for walking and narrow pull buggies.
By 1966, the flagstone path and the step had been removed. The path levels had been lowered to provide a slope to replace the previous step. In 1967 it was then proposed to widen the walk between the clubhouse patio and the putting green to allow this to be generally used as a mode of passage from the 10th tee to the 1st tee or vice versa. The design to widen the path was to be such that no interference would be caused to the garden in the front of the clubhouse patio. This required a small intrusion into the putting green surface.
In 1981 it was decided to re-lay the path to overcome drainage problems. The flagstones were found to be unsuitable for re-laying.
This work was done soon after but in 1982 the path levels were found to be such as to allow puddles to form from the sprinklers. So it was lowered and paved with interlocking paving bricks as seen here is 1997.
In December 1982, it was proposed to widen the path again, this time to cater for golf carts which were now in wider use. However this was deferred and not executed until May 2000. So the paths around the gardens near the clubhouse were mulch covered.
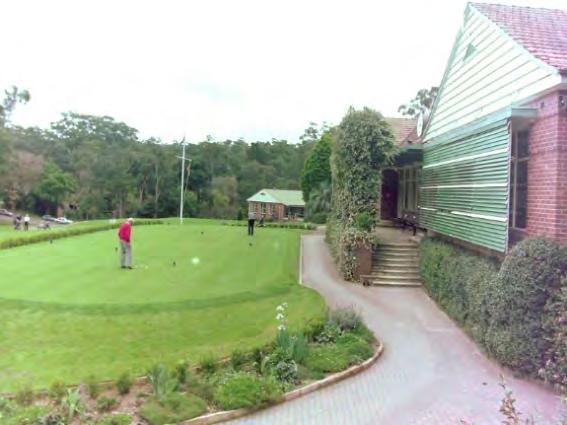
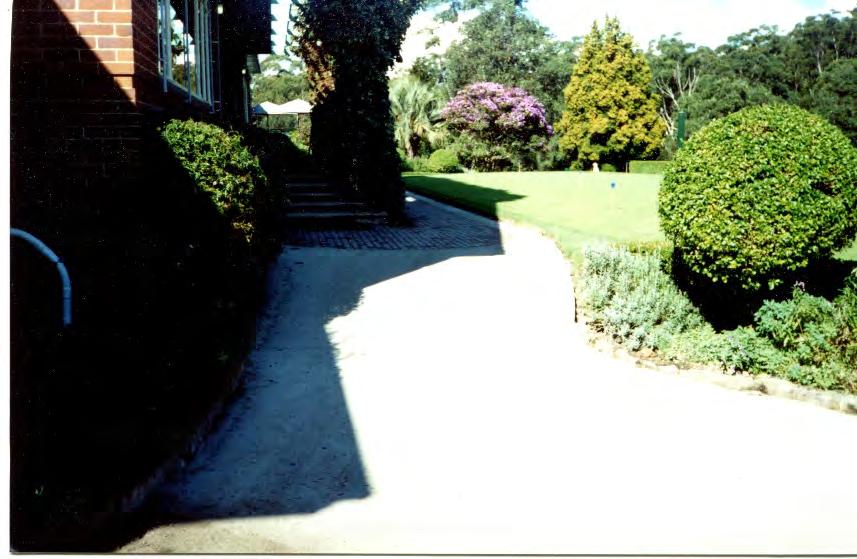
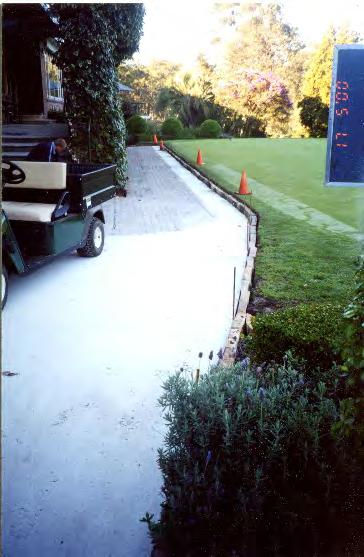
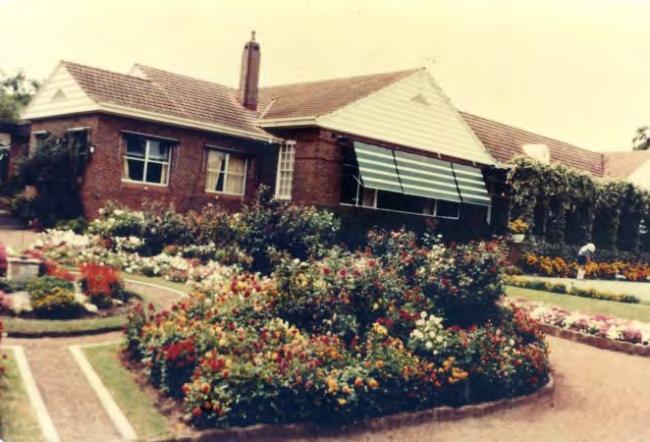
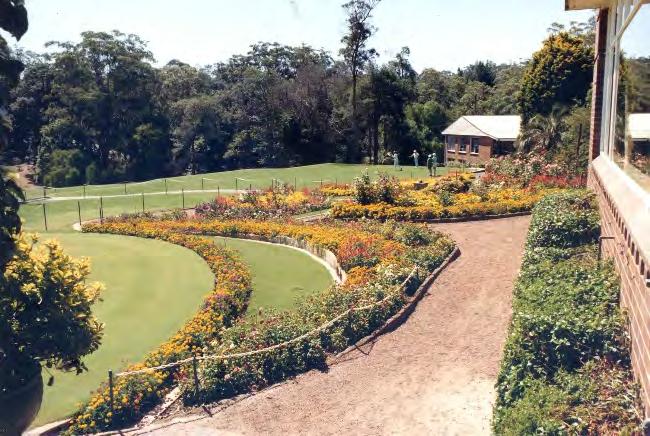
At the same time, all the paths between the clubhouse and the pro shop, previously covered with eucalyptus chips, were replaced with concrete bases and then overlaid with rubberised bitumen.
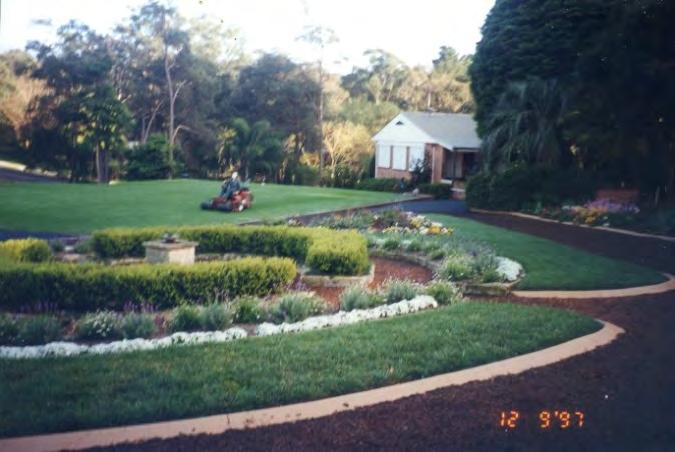

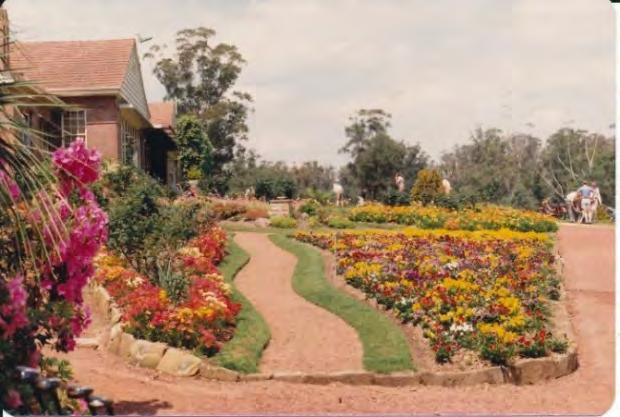
The photos following illustrate the sequence of paving materials around clubhouse, putting green and pro shop between 1956 and 2001.

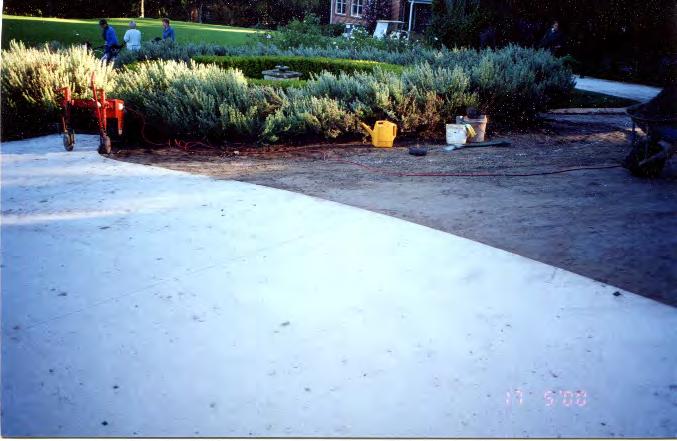
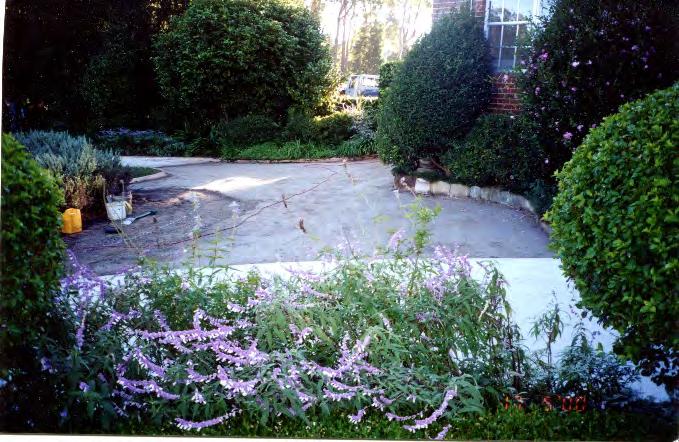
Paths on the golf course
During the 1980s many paths near tees and greens were covered by eucalyptus chip mulch. These suffered washaways from heavy water flow after storms and required regular repair.
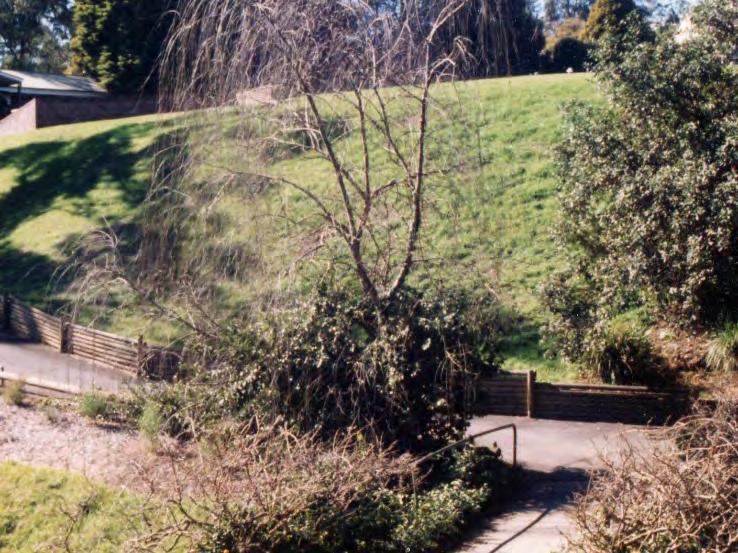
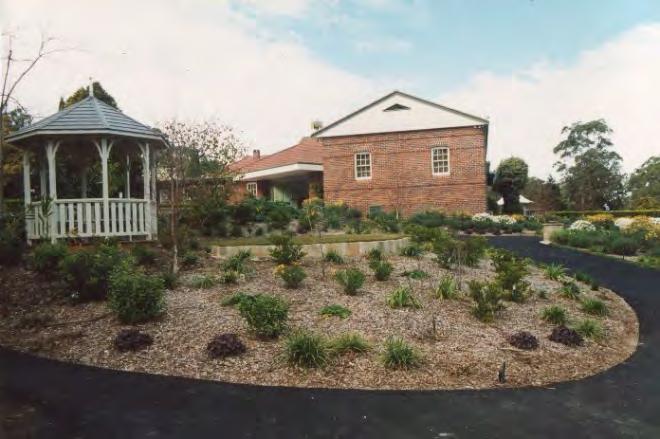
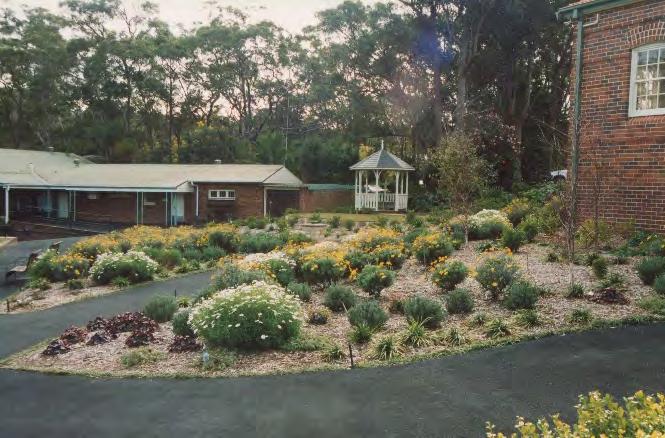
A few tees with steep slopes leading to and from them, had concrete based paths laid. Specifically, approaches to bridges at 1, 9 and 10 and the downhill left side of 15th tee Some had rubberised bitumen covering, others were dual concrete strips with rubberised insert between them for easy walking by golfers with metal-sprigged shoes, common until about 2000. All non-concrete materials regularly required repair due to lifting or erosion.
The path from 1st tee/pro shop to the low level bridge was concrete based Cart paths on the course itself.
Until the mid 1990s, the use of golf carts on the course was very restricted and permitted for use only by golfers with medical certificates. Hence the need for extensive cart paths was not a high priority. Paths were essentially for walking golfers and pulling their golf buggies.
Use of crushed concrete and Bago Gravel for paths
In February 1998 a policy on paths was formulated which proposed that “Paths were to be constructed in areas that will otherwise show permanent wear from foot traffic, but with as small an area covered with artificial surface as possible. Surfaces were to be consistent in appearance and wearing capacity” It was noted that many of the current pathways needed to be resurfaced and artificial surface was to be used for steep and low lying wet areas and eucalyptus mulch for flat areas.
There was a strong desire to restrict the use of ‘artificial’ materials eg. concrete, to areas which were deemed essential to manage slopes and areas affected by rainfall and drainage.
From 1994 to 1999, paths on the course had been surfaced with eucalyptus mulch. The ongoing cost of maintaining these necessitated finding another solution. Concrete surfaces are not friendly on golf courses, and covering them with rubberised materials came at a great capital outlay. After investigating various gravel options, naturally occurring gravel from the Broken Bago Range near Wauchope was chosen as being the most effective.
When introduced in 1999 the initial suggestion was to use crushed concrete as a base, covered by Bago gravel, a fine yellowish gravel mined in a Bago pit. In July, Bago gravel were trialled on pathways, beginning with the 18th tee. This was to be over recycled concrete to a depth of approximately 100 mm with the Bago gravel topping rolled to approximately 50mm depth. This provided a very firm and pleasant surface for walking and also for pulling buggies.
When the gravel was trialled it met with overwhelming approval by the members. A number of paths were "Bagoed" during this year. Not only did the Club have attractive all-weather paths, but also it was expected to greatly reduce maintenance costs. Some members went so far as to say this was the most significant decision taken around the course for many years!
However, the use of Bago was not a panacea to overcome maintenance, as it was soon discovered that the design of the paths needed to be changed to prevent erosion and water runoff after heavy showers.
In August 1999, it was decided to undertake the construction of the pathway to the 2nd tee with Bago gravel as a further trial of the product. The photos show the path beside the 2nd tee before and after use of Bago gravel.
The path on the right of the 2nd tee was a simple dirt track in the 1990s which was later improved in 1999 using Bago gravel.
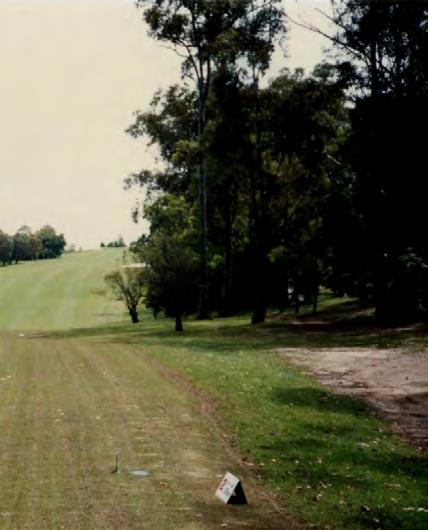
In reviewing the benefit of Bago Gravel, it was noted that if it washed away, it was repairable. The Course Superintendent advised that it would wash away in heavy rain but it was able to be rolled back in. Therefore the design of the path and surrounding areas was important to deflect as much water as possible, by making them slightly crowned at the centre, allowing water to run off to the sides.
As a result of the initial trial of Bago paths, in January 2000 it was decided to proceed with Bago gravel pathways beside the 2nd green, between 5th green to 6th tee and to the left of the 6th fairway carry.
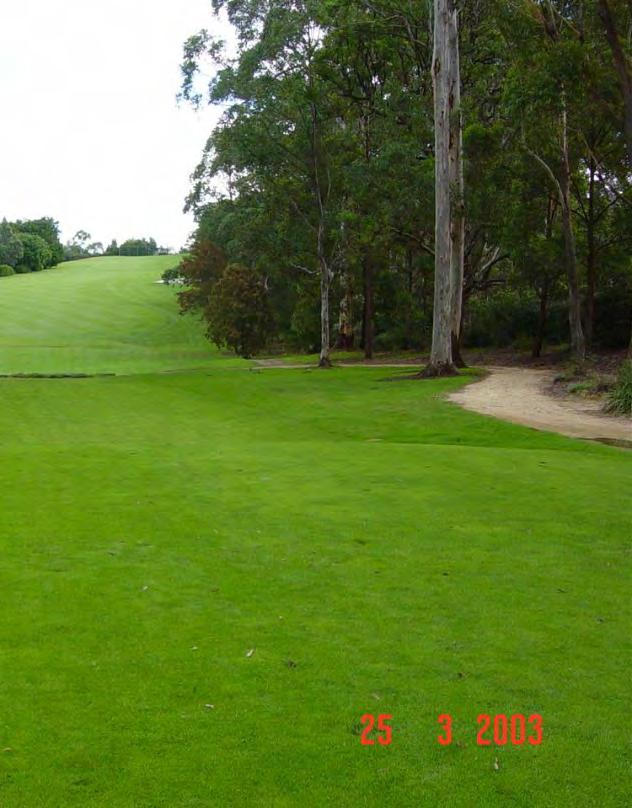
The use of Bago as a surface material however was still not universally successful. When applied to the area outside the clubhouse office area, it was replaced by fine wood chips until a permanent solution was found.
The crowning of the path contour did prevent scouring of the centres of the pathways however washaways on the sides became a problem. So design changes were investigated to disperse the water off the sides of the paths.
As one third of the Bago pathways were laid on slopes and subject to erosion it was decided to concrete the affected paths as funding became available. So the previously formed Bago pathways across the front of the 2nd tee and from the 12th tees were concreted at a cost of $13,000.
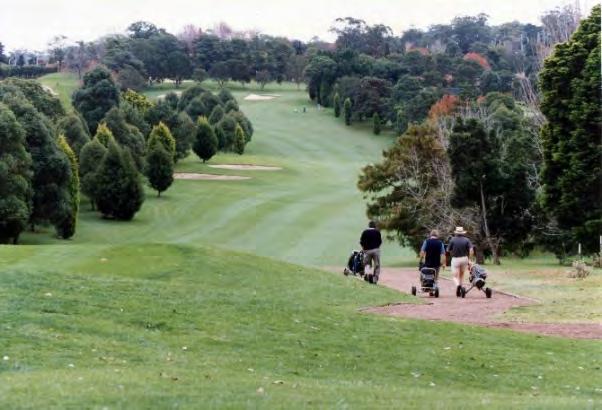
A report was prepared to identify the real cost of maintaining the current system of Bago pathways versus the cost of permanent concrete pathways so that an informed decision could be made regarding providing extra paths and more permanent surfaces on sections used by the course staff and other steep areas of the course.

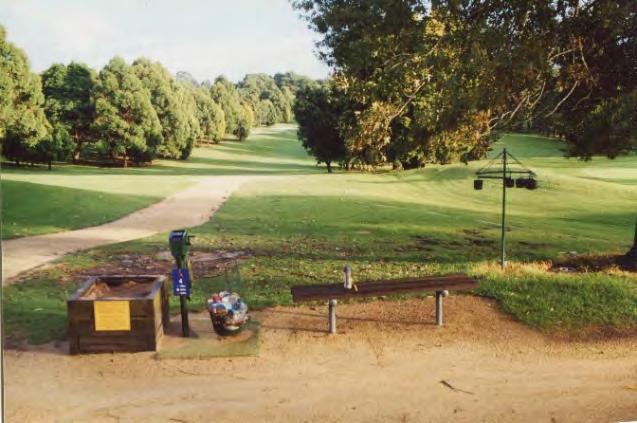
Eucalyptus woodchip mulched paths. Prior to the introduction of Bago gravel, most formal paths were covered with eucalyptus woodchips. While these provided a generally satisfactory surface for foot traffic and pull buggies, as noted above they suffered severely from water damage after heavy rains caused washaways.
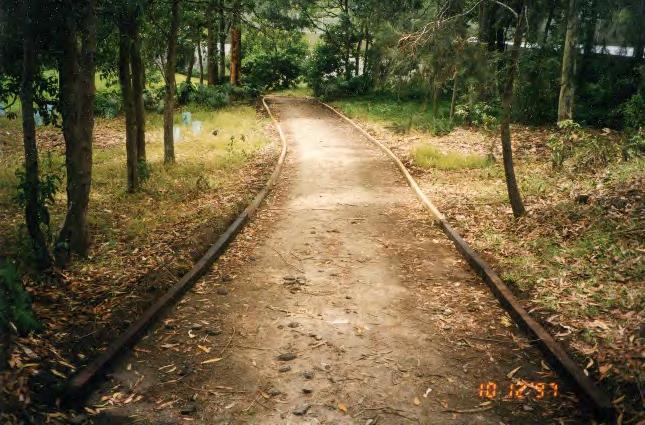
The policy of using Bago and wood chips for paths continued after 2000 and the consensus for using concrete paths was that a minimalist approach, which had been in force, would continue. This was that concrete paths need only be provided at points of concentration of wear adjacent to, and leading from, tees and greens.
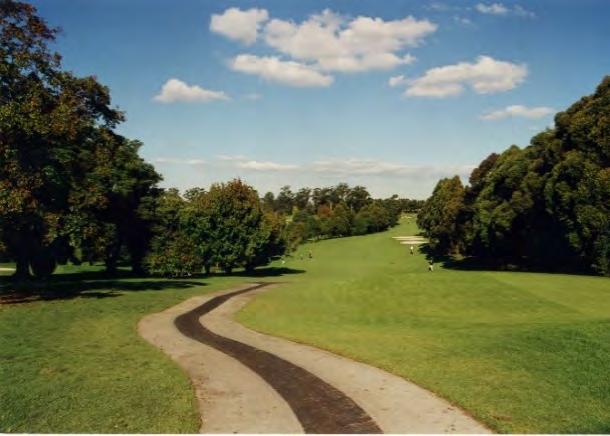
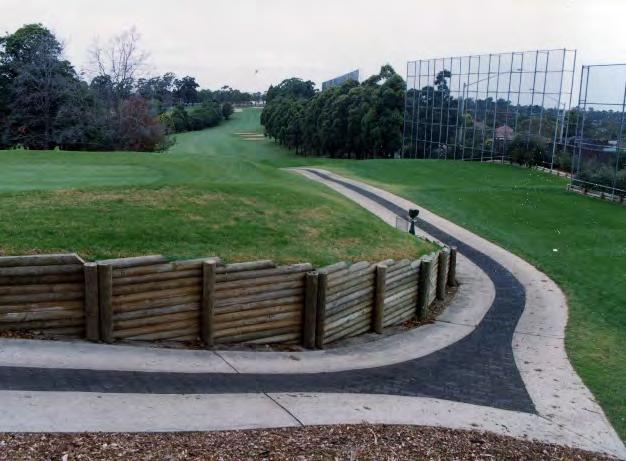
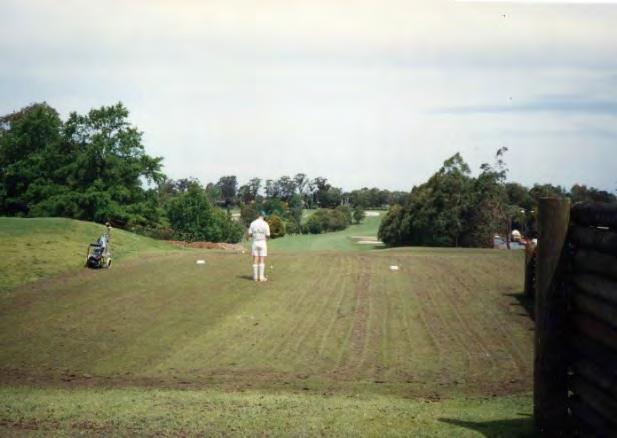
In March 2003 Bago paths continued to be a maintenance problem. Many were washed out during the rain and they were now becoming a costly recurring item. The Course Superintendent suggested that the Board expedite a program of permanent concrete pathways
A study was carried out to compare the cost of repairs versus the cost of permanent concrete paths. This was done to be able to justify options of providing extra paths and more permanent surfaces on sections used by the course staff and other steep areas of the course and as an aid to prepare budgets for the future financial years.
Over the next several years, due to budget limitations, small lengths of concrete paths were laid as part of the minimalist policy. However by 2007 several significant forces were helping direct a revision of this policy. These included the continuing cost and diversion of labour to repair Bago and woodchip paths following heavy rain, the increased use of Golf Carts by members, and the recognition that competing clubs had invested significantly in providing extensive concrete cart paths throughout their courses.
There were approximately 500m of Bago pathways and 800m of existing/planned pathways (total approximately 1300m) around the course. While there were budgeted amount sufficient to commence a program of concrete paths, it was be necessary to fund further amounts into the coming budget years.
In January 2008, it was agreed that replacement of Bago paths should be a priority as they required too much maintenance particularly after heavy rain. It was decided to use ‘Rubberoc’ surface laid over concrete for most of the paths. This was the first stage in the longer term plan to upgrade pathways around the whole course.
Instead of using external contractors to provide all material and labour, major cost savings were identified by the use of the Club’s course staff to do all excavation work using their own machines and by purchasing the steel in bulk. The contractors would then prepare all formwork, lay the steel and place the concrete and the rubberised surface.
A priority list of work was prepared and executed from the end of 2008 until early 2010, replacement of all Bago and woodchip paths was carried out as well as new paths.
This work was done under the general supervision of Captain Rob Stevenson. While the budget was slightly exceeded because the scope of works was increased, ie. the overall length of cart paths and roadways , the cost of concrete negotiated was highly beneficial to the Club. The external contractors carried out their work at for the Club at actual cost. All in all the Club got excellent value.
Bago Path from 3rd green
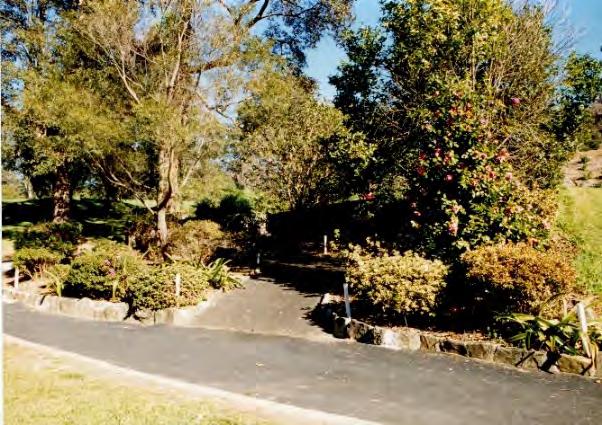
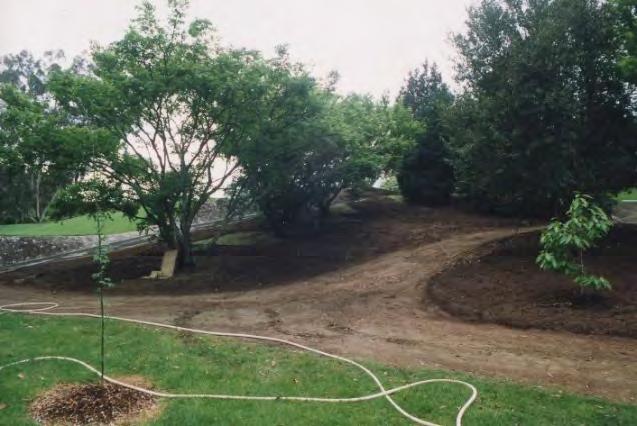
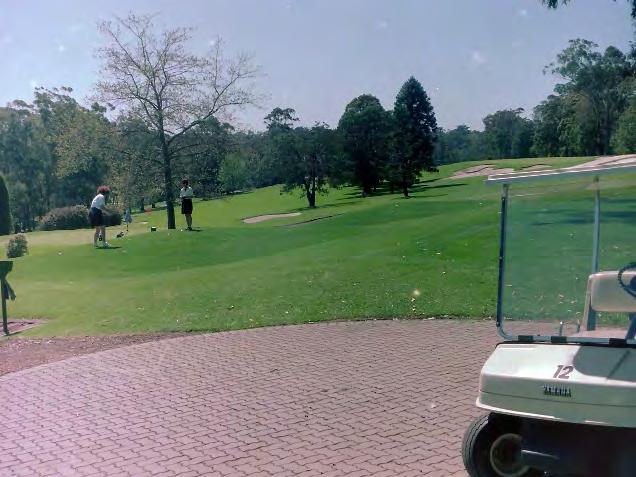
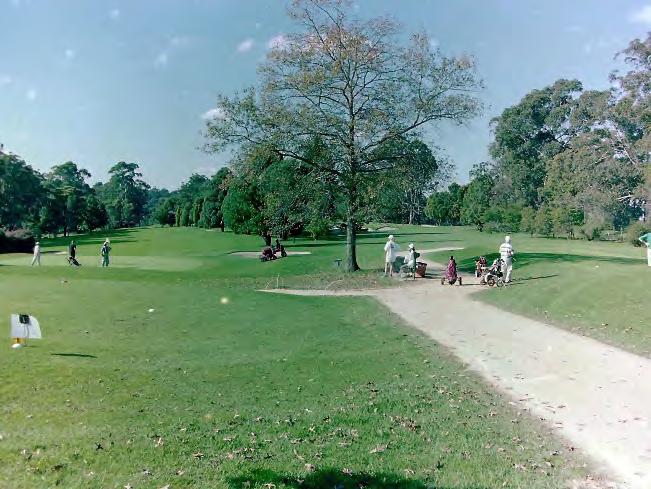
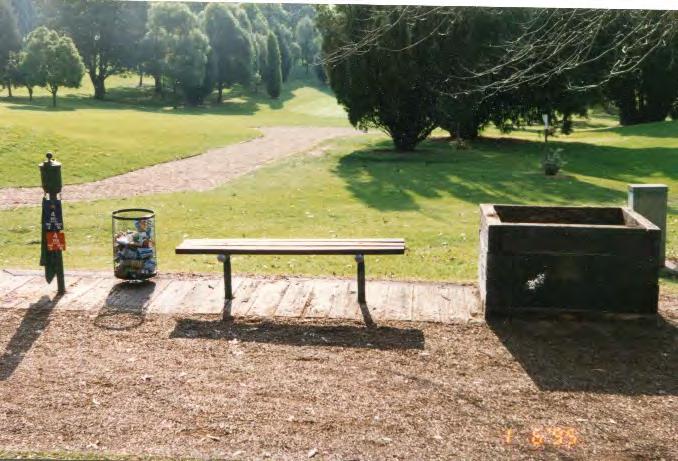
Interlocking bricks cart turning circle The following series of photo show the evolution of path material on various parts of the course.
Bago path to left of 10th tee. Later concrete with rubberised bitumen surface
9th tee to bridge.
There had been a rubberised bitumen, concrete edged path from the 9th tee to the bridge since the 1960s, however the surface constantly suffered erosion and the repair costs were high but lower than replacing with a concrete path. However because of the continuing uncertainty of the impact on the whole course of the M2, there was a necessary reluctance to spend funds on big infrastructure items, which may need replacing.
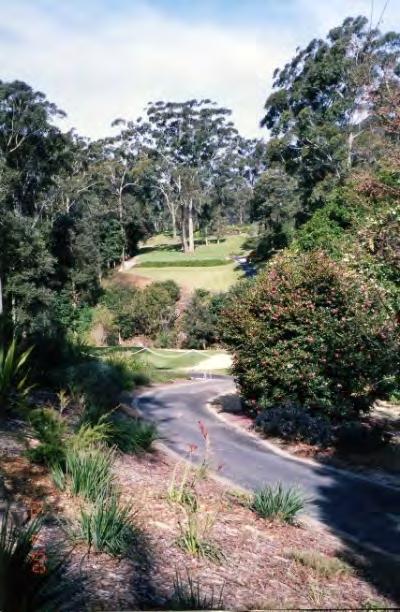
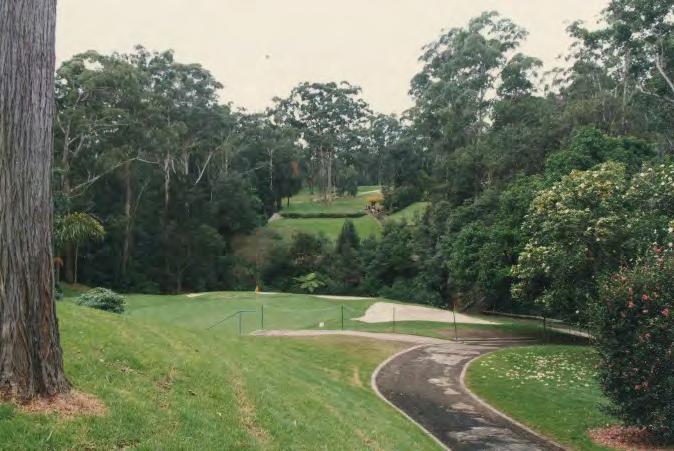
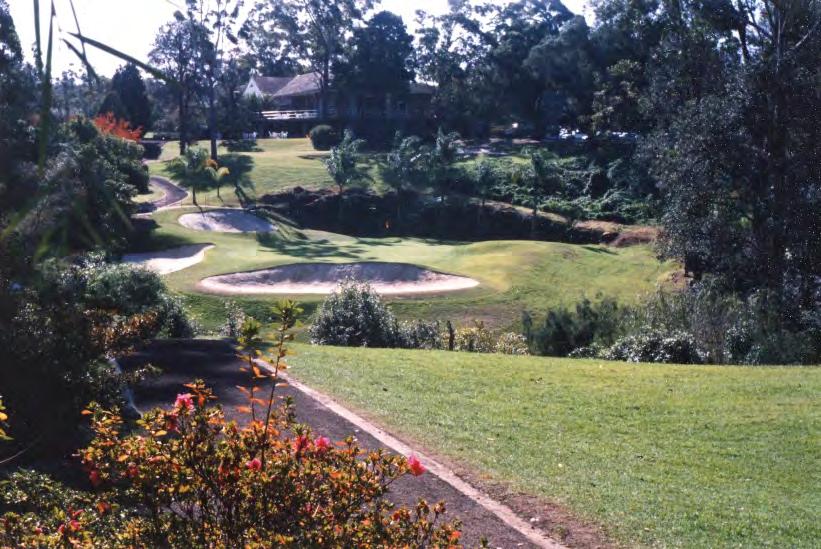

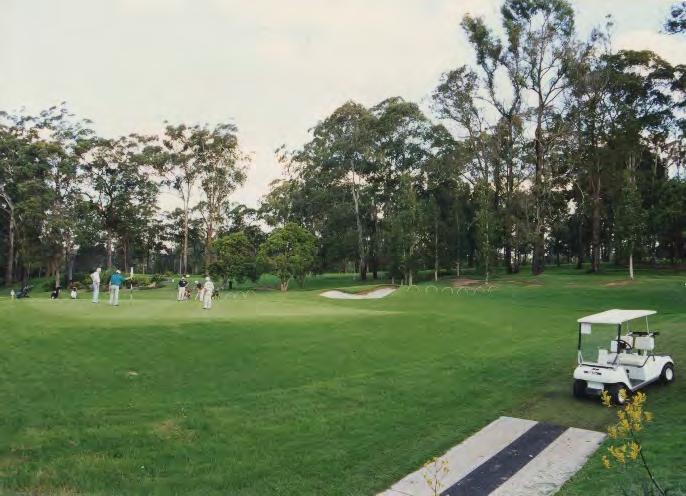
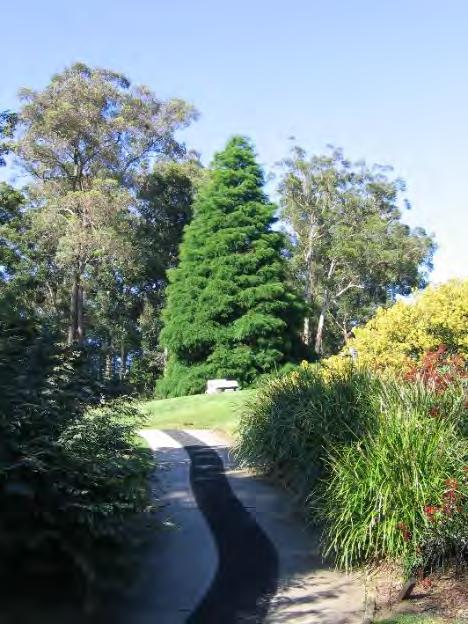
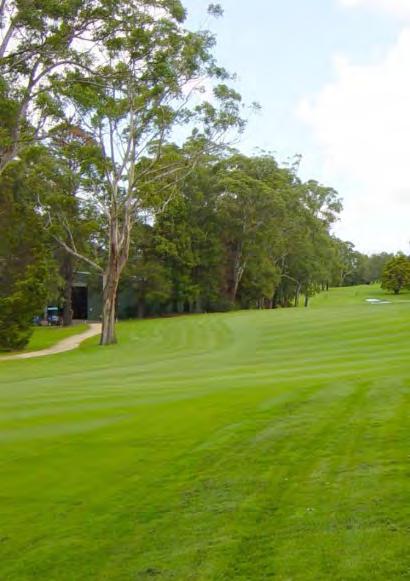


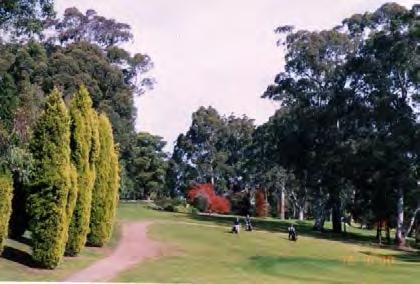
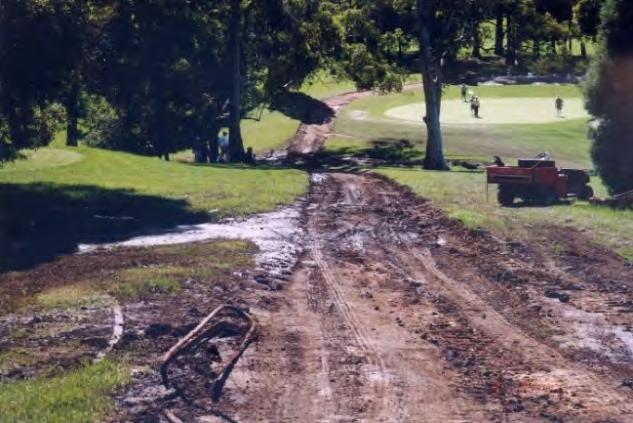
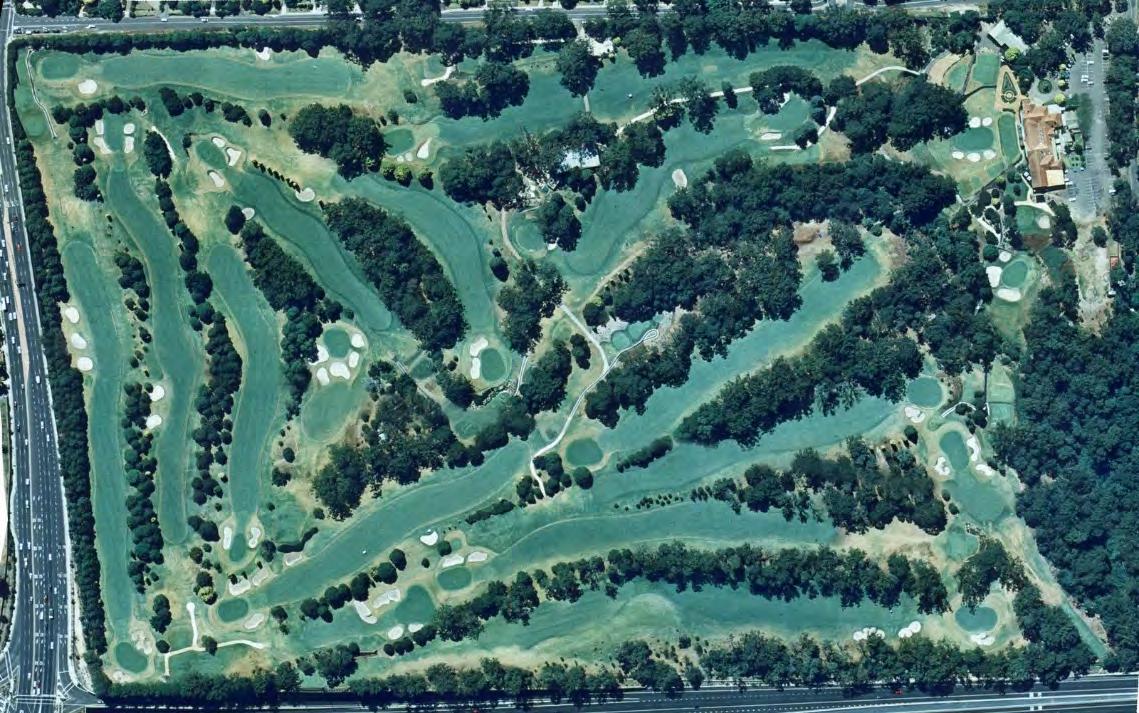
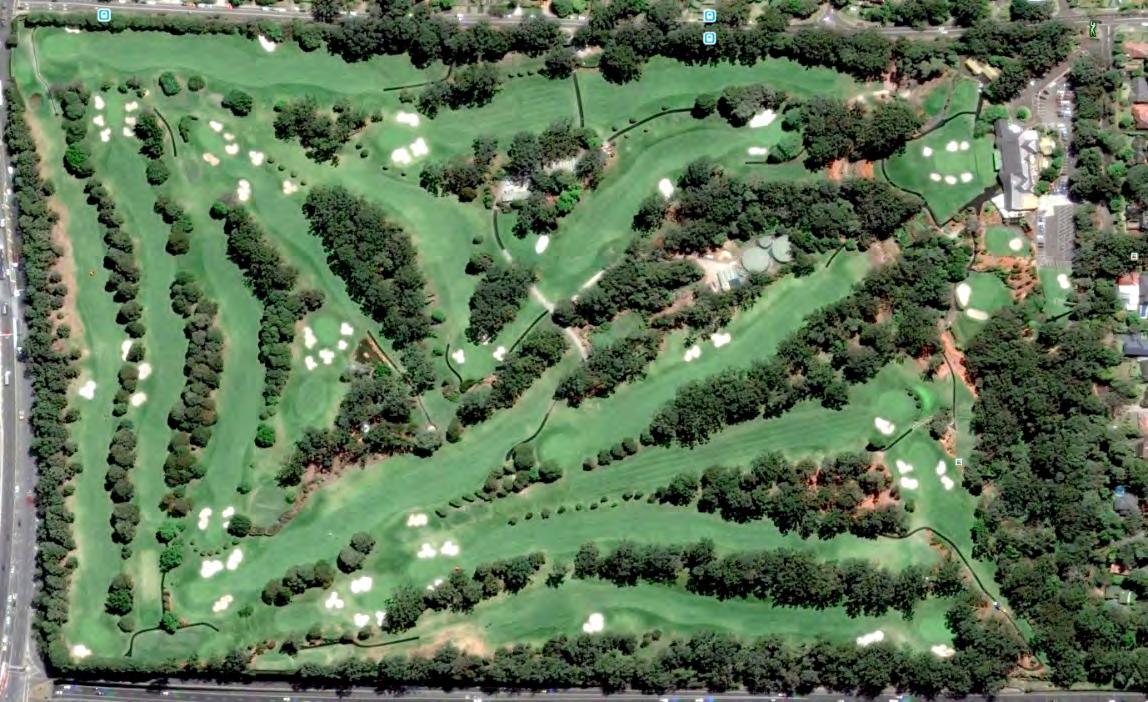