
35 minute read
In bloom
Singapore in bloom
At Gardens by the Bay in Singapore, Tekla Structures helped bring to life a forest of ‘Supertrees’ crafted from steel and concrete.
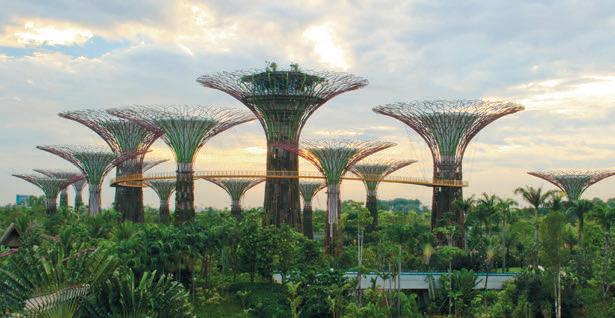

Gardens by the Bay is a nature park spanning 101 hectares (250 acres) of reclaimed land in central Singapore, adjacent to the Marina Reservoir. The park consists of three waterfront gardens: Bay South Garden, Bay East Garden and Bay Central Garden.
The park houses conservatories that showcase plants native to more temperate climates as well as themed gardens that explore the different cultural traditions of Singapore. One of the park’s highlights, however, is mineral rather than vegetable in nature: 18 giant steel and concrete trees, each between 25m and 50m high.
These ‘Supertrees’ consist of concrete trunks, topped by a canopy made of complex steel tubes that form the branches. Some of them also integrate solar cells that generate power for use in the conservatories below.
The trunks of the Supertrees are similarly clad in a steel frame and draped with many types of climbers, flowers and ferns. To add to the complexity, a 128m long suspension bridge, the OCBC Skyway, links two of the taller trees together and allows visitors to soak in the view from 22m above ground level.
Critical component Steel was a critical component for the entire project, from the frames around each trunk to the network of branches that form the canopy. As the complex design geometries were vast, Singaporebased TTJ Design and Engineering turned to Tekla BIM software for the entire project. Having used Tekla Structures for over ten years, the software is key to TTJ’s operations and the firm relies on it for intricate designs and highly complex jobs like this one.
TTJ worked closely with the architects and structural construction consultants to fabricate the parts needed for the Supertrees. Working with the design drawings for construction, TTJ began by using Tekla Structures to create the general arrangement drawings, together with connection details, before sending the drawings to all relevant parties for approval.
“Any time you have curved parts, it is good to use Tekla,” says Madam Tan Yumin, engineering manager at TTJ. This is because the other software products used by TTJ have difficulty in handling curved shapes.
Tekla BIM software was especially useful on this project because of the complex geometries involved in constructing the canopy. The interlocking branches at the crown of each tree reveal a delicate network of steel tubes encircled by a stainless steel cable that pulls the structure together. The cable ensures that the branches do not start sagging and put undue stress on the entire canopy. To reduce the weight of the overall structure, the steel used in this canopy is very thin, just 3.2mm thick in parts. As a result, only 920 tons of steel was used to build the soaring Supertrees.
Steel fabrication benefits According to Madam Tan, Tekla has numerous attributes that make it ideal for steel fabricators; in particular, it speeds up the fabrication process. It is able to handle changes on the fly, for example, so that any amends proposed by the architect to the original drawing are automatically reflected in the general arrangement drawing. TTJ took about six weeks to model each tree with Tekla. “If we had used ordinary CAD software to create the models, it would have taken us three times longer,” Madam Tan claims. Part of what speeds up the process is the extensive library of parts that exist in Tekla and that also supports manual additions. Once the architects and the consultants approved the general arrangement drawings for the tree, TTJ used Tekla Structures to generate the shop drawing for fabricating the joints and every steel part required, right down to the bolts.
At the factory, the drawings were used to fabricate the necessary parts. Apart from shop drawings, this factory also relies on Tekla’s 3D models to help fabricators visualise the structure – a vital step, given its complex geometries. After the parts were made, they were preassembled at the workshop for checking, and disassembled before being blasted, painted and then sent to site for erection.
At the site, workers from TTJ began assembling the different parts to reassemble each tree, relying on the drawings and the 3D models to help them. Overall, the project took about two years to go from ideas on a drawing board to the actual structures being in situ, ready to welcome many thousands of visitors.

Aconex goes global
In March 2016, Australian SaaS construction collaboration provider Aconex acquired AngloGerman Conject, with its eye on international expansion. Aconex CEO Leigh Jasper speaks with Paul Wilkinson about the drivers behind the acquisition, as well as more general worldwide developments in areas including cost management, BIM and digital transformation.
Caption to go in here, roughly this length, roughly this length, roughly this length, roughly this length,
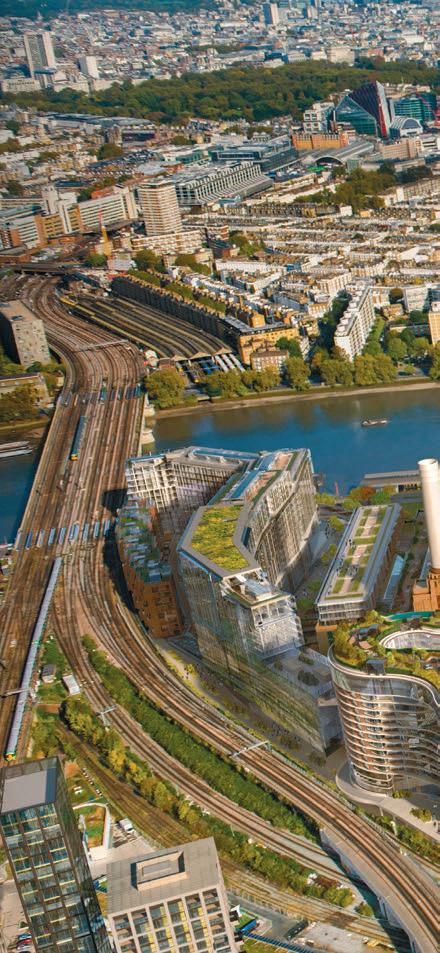
The day after Aconex presented to investors in Melbourne was a good day to get an update on the software-as-a-service provider’s recent progress from CEO Leigh Jasper — but our meeting took place in Woking, UK rather than in the company’s Australian home town.
Founded in Australia in 2000 by Leigh Jasper and Rob Phillpot (now the company’s senior vice president of product), Aconex grew rapidly in its domestic market before expanding into other markets including Europe, southeast Asia and the Middle East. In December 2014, it floated on the Australian Securities Exchange (ASX) in Melbourne.
Today it has over 40 offices worldwide, and its online platform has been used to help deliver over £600bn worth of construction and engineering projects. Customers include AECOM, Bechtel, Dubai Airport, Fluor Corporation, Lendlease, Marriott and Mace, while supported projects range from London’s Battersea redevelopment to a Japanese liquid natural gas terminal, and from a copper mine in Peru to Seattle’s $1.4bn State Route 99 tunnel.
Since Leigh Jasper was in the UK to visit offices once occupied by BIW Technologies and then its subsequent owner Conject, a company that Aconex acquired in March 2016 for A$96m, it seemed a more than appropriate venue for a conversation on how the integration of the Anglo-German business has progressed so far.
The Conject merger The background to the Aconex/Conject deal is a little complicated, so it’s worth clarifying that first. BIW Technologies, or BIW, was a privately held British company providing electronic collaboration technologies to the construction and property sectors, which was acquired by a German company Conject in 2010.
Conject’s merger with BIW was a prolonged process and one that delayed development in key areas such as mobile technology and BIM at a time when, particularly in the UK, rival vendors were investing heavily in product development. As a result, Conject found itself lagging behind rival SaaS collaboration companies such as Aconex, Viewpoint (formerly 4Projects) and Asite in adding mobile applications to its portfolio, while the same rivals were also pushing ahead with support for BIM.
Enter Aconex, a company with an eye on expanding its market presence and user network in Europe. It swooped, and Conject (along with BIW) became part of the wider company.
Among Conject customers, reaction to the acquisition has been very positive, Jasper says. They are not being forced to switch over to the Aconex platform and current projects managed on Conject will continue to be supported until they are complete — even if this takes five or six years. And the number of customers lost since the deal? “Maybe only one,” he says
In fact, some Conject customers, including international construction firm Mace, have already started new projects on the Aconex platform. Jasper puts that down to what he sees as a strengthening of the Aconex proposition with the addition of Conject, among customers that might previously not have considered either.
“In the UK market, we are selling in to new customers where Aconex wouldn’t have won them, but the strength of the product, combined with the strength of the sales team, means that we now have a very strong combination. There The Aconex project cost management team and a was probably a bit of under- collaboration platform is powerful cost tool, Connected investment in the UK-based being used on London’s Battersea Power Station Cost. (The Worksite acquisiConject products and having a redevelopment tion, he adds, was fundamenstronger Aconex platform has tal to this, bringing the comhelped,” he explains. pany forward several years in being able
The upshot is that UK and European to get Connected Cost to market.) customers can now be confident they are Aconex Connected Cost was beta-testdealing with a company with a strong ed with some customers, and then made regional presence. But above and beyond generally available in late 2016, and enathat, he said, the deal has also extended bles Aconex to compete with US-based the technology capabilities on offer. vendors whose systems have historically been stronger on cost control than on Connected Cost document collaboration. It has proved a Foremost among the acquired capabilities strong differentiator. was Conject’s Financial Control module, a “We are seeing really big interest, and mature construction project cost manage- a number of deals have already been ment application that, in its early days, done on the product,” he reports. US carhelped differentiate BIW from UK rivals. maker and energy storage company Tesla
Coupled with Aconex’s July 2015 is now a customer and it’s one that Jasper acquisition of US-based vendor Worksite feels his company wouldn’t have won from ARES, Aconex now has a strong without Connected Cost in its arsenal,

“so it’s helping us win more work, and it’s really important to our customers.”
Particularly in the US, he adds, cost is more important than collaboration. “I think our cost product is the best SaaS solution on the market, particularly when you compare it to some of the products built 10 or 15 years ago.”
Collaborative BIM Meanwhile, Aconex has been working for some years on its Aconex Connected BIM product, which was launched in October 2014. It is marketed as part of the core platform, rather than a module for which customers have to pay extra, as part of a wider ‘digital operating system’ strategy, Jasper explains.
“As it’s part of the platform, in a sense, everybody uses it — but obviously, to varying degrees,” he says. Some companies will use it very heavily and put “loads” of models into the system. Others might use it at a more shallow level.
“But BIM is a critical part of what we do — it wasn’t going to be something that was optional. We are putting digital building together enabling us to create a collaborative operating construction system for the industry, and BIM is part of that operating system, as is mobility, how we handle documentation, workflows, costs. All of these interlink. Everything needs to be able to link to everything else.”
Jasper says he has seen growing use of Aconex for BIM, bolstered by an approach embracing open BIM standards, such as IFC and BCF. The Aconex website features a BuildingSmart video, showing how its platform can be used to share model ‘viewpoints’ generated in Solibri Model Viewer, and to manage the underlying workflow). The company’s open philosophy also extends to open APIs, he stresses:
“The more open companies are on the market, the better it will be for adoption of technology. Everything we build, we put an API around it, and then our customers can consider to what degree they want to integrate with internal systems or even other providers in the market.”
The Australian domestic market is not as far advanced as the UK in BIM adoption, Jasper says, partly because the UK has benefitted from the collective incentive of a government mandate. That said, BIM adoption in Australia still outstrips that in the US — something he’d like to put right.
“In the US, BIM became really topical about three or four years ago, and we need to get that back. One of the challenges in the US is that people only look at it from their point of view. BIM is one Management Program, FedRAMP. This, of those things that, the more that own- Jasper believes, will enable Aconex cusers and contractors work together, the tomers to win US federal government better the results for the project team.” projects, through compliance with
Asset information management, he advanced security compliance requirefeels, is probably the next step for the ments. In the UK, meanwhile, it is industry. “Owners need to be specifying already registered on GCloud. early what they need and then moving He also talks about incorporating towards full asset lifecycle and the oper- scheduling information (currently domiations phase,” he says. As yet, however, nated by Oracle Primavera and he hasn’t seen any huge demand from Microsoft Project) and geolocation sercustomers to develop a facilities man- vices into the platform. The once-familagement (FM) solution. iar Aconex product set is constantly
“We see FM as part of that entire story, evolving and expanding and he’s cognibut the reality is that… in our development zant of the need to keep reminding longstack, there is still a lot to do in the design standing customers of that fact. and construction phase,” he says. In five years, he predicts, Aconex will offer a Digitising construction SaaS-based FM product as part of the A former McKinsey consultant himself, suite, but it’s not in develop- Jasper has been gratified to ment right now. see his former employer‘s Interestingly, Conject already Digital Transformation had such a product, “but reports, released by the whether that’s the tool we McKinsey Global Institute, end up taking forward, we showing how developed are reviewing at the moment. economies are pushing forIt’s a bit separate to other ward in digitising their parts of the business,” he construction industries. explains. While many companies in these regions are startMobile tools By contrast, the functionality of Conject’s mobile tools ‘‘ Everything we ing from a low base of technology adoption, he believes that this points to will be retained. “We are build, we put an untapped opportunity for pulling it all into one platform. Any functionality that we don’t have in API around it, and then our technology companies such as Aconex to help them adopt new ways of Aconex Field, we are pull- customers can collaborating. In the US, ing into our solution,” consider to for example, only agriculJasper says. He says the company is aiming to go ‘deep, not wide’ on mobile. what degree they want to ture and hunting are less digitised than construction, according to “If we are going to add a integrate with McKinsey. In Europe, confunction or a module, we want to make sure it’s really good.” internal systems or even struction was bottom of the league in digital transformation.
He summarises the com- other providers “The nature of the induspany’s four functional priority areas as: • Deepening its collaboration tools try is that it’s quite conservative in terms of its adoption of technology. The McKinsey ’’ (developments include currently report shows that all the countries that extending configuration to man- have been early adopters of technology age packages of work); — collaboration or more general digiti• Expanding field and mobility; sation — have increased labour produc• Extending BIM capabilities; and tivity in construction.” • Connected Cost (where Jasper Either way, if technology can take IT talks about “making cost more spend from just one percent to two or collaborative”). three percent in what is, after all, a $10 trillion construction market, he says, Aconex also wants to stay ahead of the “the potential is massive.” Getting just a game on security. As of March 2017, small slice of that business would be a Aconex was seeking certification under major coup for Aconex. the US Federal Risk and Authorization ■ aconex.com
A Q&A with Space Group
Space Group CEO Rob Charlton shares his thoughts on the level of maturity within the built environment in the UK, digital construction methods and processes from design stage through to asset handover
Now in its 60th year, Space A: At Space Group we are driven by Group has seen significant “Making Buildings Smarter” We can’t do change in our industry and this alone, and if we are to make a contribuwas a very early adopter of 3D tion to the industry we need to work with a design and modelling. Rob Charlton tells wide range of companies and people. All of us not just from an industry perspective our most successful projects, which have how far we’ve come, but from personal achieved the best outcomes have had great experience what influences change and teams all working together and sharing most importantly the desire to change. knowledge to achieve a common goal. expertise is something you feel very Traditionally we know design and conQ: What level of maturity do you think struction has been contractual and siloed. we’re at right now in the UK Digitisation helps to break in our ability to truly meet down these barriers and to Level 2 BIM requirements? share information. Fortunately, now we have A: The reality is we are a projects which have comlong way from the entire pleted successfully by focusindustry achieving level 2. ing on collaboration through I even doubt we will ever get a digital framework. This there. The standard is very provides the opportunity to structured for obvious rea- turn talk into reality. sons which may mean consistent delivery will be a challenge. ‘‘ All of our most Q: Do you see Space Group as initiator of change? However, I believe there is commitment from most that construction is digitising successful projects have A: I have never seen our role to drive change in our and very few are now ignor- had great industry. There are many ing it. I think Level 2 pro- teams all great groups and instituvides a great framework for the industry to work within working tions far better placed than we are. We are driven by and to use to suit their together and improving the outcomes of requirements. sharing our clients. Innovation I’m a great believer in that the tail should not wag the dog. knowledge to achieve a helps us achieve this. We need to work with great companies and organ-
Ultimately, we are all striv- common goal isations to help us achieve ing to improve outcomes across the construction sector. If Level 2 standards help us achieve this. We want to bring all of these great people together which was why we started BIM Show ’’ this then that’s great. Live. This is a great place for sharing Q: It’s clear that the art of collaboration built some fantastic relationships and and sharing knowledge, skills and partnerships through the show. and learning and over the years we have strongly about. Is this a key driver for Q: How do you engage with built Space Group? environment stakeholders to offer new technical solutions and smarter ways of working?
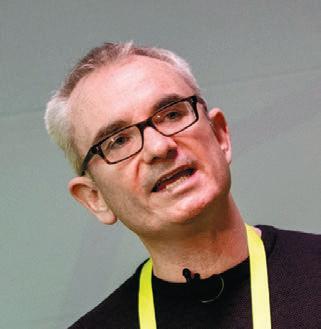
A: We spend time trying to truly understand the challenges faced by our clients. This often means you need to understand their business. When we work with real estate investment trusts their priority is to maximise shareholder investment. Greater predictability and the reduction of risk is all important.
When working with discount retailers their priority is pace of delivery therefore we need to consider standardisation and information exchanged.
We are continually developing new ideas and testing these on our clients.
Q: What is the next step on the UK construction industry’s digital journey?
A: We have proven over the past decade what can be achieved across construction in a short space of time. The industry is now full of clever digital experts who would not have joined the industry a few decades ago. There is now a now a culture of innovation and challenge. We are already looking at technologies from other sectors and how they can improve our industry.
The increasing influence of millennials will continue to challenge and change the culture, digital skills will increase exponentially as new people enter the industry and software will become increasingly intelligent, by using data to allow artificial intelligence to influence decisions.
Hardware will also continue to develop. This will be beyond processing and will start to include hardware such as robotics, reality capture and 3D printing.
It is certainly an exciting time for construction and hopefully we will be able to compete with other sectors to attract the best talent in the years to come.
HP Z2 Mini workstation
HP’s impressive micro machine is great for bread and butter 3D CAD but, with rigid specs, buyers need to be confident that workflows won’t change
Small Form Factor (SFF) workstations like the HP Z240 SFF are becoming much more prevalent in design and engineering offices. What were once considered entrylevel workstations, with compact chassis of around 100 x 350 x 400mm, are now powerful enough to satisfy the requirements of most 2D and 3D CAD users.
HP has now gone one step further with an even smaller workstation called the Z2 Mini. Similar in stature to the Apple Mac Mini, HP’s beautifully styled machine is small enough to be held in one hand. A mere 58 x 216 x 216mm in size, it can happily sit on a desk, but can also be mounted on the back of a display or under a desk.
There are many advantages to this new mini form factor. First, and most obvious, is it takes up less desk space, which can be a big benefit in a world of rising property prices. HP reckons there has been a 60% space reduction per person in the US over last 10 years. One could argue that you simply get around this by putting your workstation tower under your desk. However, when kept down by your feet they become serious dust magnets and need to be cleaned regularly to keep fan noise in check (clogged fans need to work harder to achieve the same cooling). Floor standing machines can also create a micro climate under your desk. This can be great in winter to warm frosty toes, but not so much in summer. Even when your office is air conditioned, the environment can become unbalanced. We have heard anecdotes of people wearing jumpers on top and shorts down below.
The second benefit is portability. The HP Z2 Mini is so small and light (it starts at 2.04kg) that you can easily pop it in your bag to take home or to a meeting. And with an optional built-in Intel 8265 WLAN 802.11ac module you can connect to WiFi wherever you go.
The third is, admittedly, subjective, but we think it looks rather cool. HP has obviously paid a lot of attention to the styling of its mini workstation, but the corner detail is actually derived from functional requirements. The Product spec Intel Core i3 / i5 / i7 — but a custom entry-level ‘mobile’ custom cooling system, which ■ Intel Xeon E3-1245 GPU, the Nvidia Quadro M620 features dedicated fans for both GPU and CPU, draws in air from the front two corners v5 (3.5GHz, 3.9GHz Turbo) (4 Cores) CPU ■ 16GB (2 x 8GB) DDR4-2133 non-ECC (2GB). The machine can support up to 32GB of DDR4 RAM across two SODIMMs, which and out at the rear two cor- SDRAM memory should be plenty for most CAD ners. As the vents shouldn’t ■ 512GB HP Z Turbo Drive G2 (NVMe SSD) workflows. become obstructed for obvi■ Nvidia Quadro Despite the thermal challengous reasons, they are protect- M620 GPU (2GB) es of producing such a small ed by the chamfered edges of ■ Microsoft Windows machine, the Z2 Mini offers the main chassis. A lot of sci10 Pro 64-Bit pretty much the same level of ence went into this. HP’s ■ 216mm x 216mm x 58 mm (w) x (d) x (h) CPU performance as one can workstation team told AEC ■ 3-year (3-3-3) find in a SFF workstation. Our Magazine that, in designing limited warranty and test machine’s top-end Intel the HP Z2 Mini, it did more service offering includes 3 years of Xeon E3-1245 v6 (3.7GHz up to simulation and analysis cooling work than on any other product. Computational Fluid parts, labour and on-site repair ■ £1,219 + VAT 4.1GHz) is only a shade slower than the Intel Xeon E3-1270 v6 (3.8GHz up to 4.2GHz), the Dynamics (CFD) was even hp.com/go/z2mini fastest model available in the used to optimise the individu- HP Z240 SFF. al spacing of the cooling fins. In use, such subtleties will likely go
This attention to detail results in a unnoticed. Indeed, in our multi-threaded remarkably quiet design, which is impres- KeyShot rendering benchmark, the HP Z2 sive for a machine of this size. When idle, Mini was only 9% slower than the Armari the workstation is virtually silent and Magnetar V25 we tested back in February noise levels are still perfectly acceptable 2017 (tinyurl.com/magnetar-AEC), which when the CPU is being pushed to its limits. had an overclocked 4.7GHz Intel Core i7 One minor criticism would be that fan 7700K CPU. speeds are not always consistent. When While the CPU is on par with most rendering a scene in KeyShot, for example, CAD-focused desktop machines, the same we found the fans cycled from can’t be said of the GPU. The Quadro M620 is very much an entry-level 3D GPU. But this doesn’t mean it’s not suitable for 3D CAD or BIM. Indeed, while our benchmark scores show it to be significantly slower than the fastest GPUs you can expect to find in a SFF workstation — the Nvidia Quadro P1000 or AMD Radeon Pro WX 4100, for example — in practice we found it to be a very capable 3D graphics card. However, it is important to acknowledge its limitations. The bulk of our tests were done at FHD (1,920 x 1,080) resolution. In shaded with edges mode in SolidWorks 2015 we had a perfectly 1 good experience with all our test models, recording frame rates in excess of 20 FPS. The Z2 Mini even kept pace when RealView was enabled on low to high every 30 sec- the PC computer model onds, or so. The noise taken from the SPECapc would actually be less for SolidWorks 2015 benchnoticeable if the fans remained on high for mark. However, the machine did become the duration of the render. Hopefully this sluggish when we switched on Ambient might be remedied in a later BIOS update. Occlusion, something that wouldn’t happen with a more powerful GPU like the The power inside Radeon Pro WX 4100. The Z2 Mini features a combination of We had a generally good experience in desktop and mobile technologies. It has a Autodesk Revit, but this came as no surdesktop CPU — Intel Xeon E3-1200 v6 or prise as this ‘BIM’ application is very

CPU limited, meaning that the performance bottleneck usually comes from the CPU, rather than the GPU.
The HP Z2 Mini started to show its limitations in the ‘game engine’ viz application LumenRT, which places a big emphasis on visual quality. Here, frame rates dropped to as little as 5 FPS which really impacted the experience.
At 4K resolution, with four times as many pixels to render, the HP Z2 Mini started to slow down. While it kept pace in Revit and SolidWorks (shaded with edges mode), in the game engines LumenRT and Autodesk LIVE (based on Stingray) it became largely unusable as frame rates dropped to as little as 2 FPS making it almost impossible to move your model into the right position. For such graphics-intensive workflows you really need a higher-end GPU like the Quadro P4000, which is only available in a desktop tower like the HP Z240 Tower.
When designing a machine of this size, the temptation would be to go all in for Solid State Drives (SDDs). However, HP has allowed room for both 2.5-inch HDD/ SSD and an NVMe, M.2 form factor SSD (HP Z Turbo Drive G2). This is a nice design choice as it gives users access to up to 1.5 TB of total storage (when configured with a 512GB HP Z Turbo Drive G2 and 1TB HDD). It also helps bring down the price of entry-level models, configured only with a 2.5-inch drive, though we would never recommend buying a workstation without an SSD.
Our test machine came with a single 512GB HP Z Turbo Drive G2. This PCIe NVMe SSD is actually a Samsung SM951, but HP also repackages SSDs from other manufacturers that offer similar performance and durability characteristics. The HP Z Turbo Drive G2 is exactly the same SSD you get in most HP workstations and plenty fast enough for standard CAD workflows. Boot up time was impressive — a mere 17 seconds.
The drive itself sits directly under the GPU blower, directly on the motherboard. Should it fail, you’ll need to remove the entire GPU fan assembly, which should only be done by experienced users. The only components that are easily serviceable are the 2.5-inch drive, which sits on top of the GPU blower, and the memory, which can be found under the CPU fan that flips up on a hinge. Opening up the machine is easy. Simply pull on the cover latch at the rear and the lid pops off. The 200W power supply is external, borrowed from a HP ZBook mobile workstation, we believe.
Despite its compact size, the Z2 Mini is well equipped with ports. There are 2 USB 3.0 and 2 USB 3.1 Gen 1 Type-C at the rear and 2 USB 3.0 (1 charging) on the side. The ‘always on’ port has the obvious benefit of being able to charge phones and other devices when the machine is off, but also has an added benefit. Once enabled in the BIOS, you can plug in a USB keyboard, then simply press any key to switch on the machine when it is powered down. This is particularly useful when the machine is out of sight. Indeed, while the Z2 Mini will look great on any desk, HP has gone to great lengths to help it be hidden away. To this end, HP has developed an ingenious VESA Mount solution, which encloses the HP Z2 Mini in a metal sleeve that can be mounted behind a display, on a wall or under a desk. The sleeve also doubles as a security device, featuring a Kensington lock slot and pad lock loop, plus a means of restricting access to the USB ports. Simply rotate the security sleeve by 90 degrees and all the ports get physically blocked off.
Considering the ease with which the Z2 Mini can be attached to a desktop display, one wonders what the future holds for HP’s All-In-One workstation, the HP Z1.
Conclusion Having spent several weeks testing the HP Z2 Mini, we have to say we are very impressed. It delivers pretty much everything one needs for bread and butter 3D CAD work and does so in a beautifully styled micro chassis. With temperatures hitting 26°C in London over the past few days, we’ve also noticed a big difference in comfort when using the 200W Z2 Mini on the desk and a 400W tower on the floor.
Of course, there are tradeoffs in having such a small machine, mostly centring on 3D performance. While the Z2 Mini should be able to handle most mainstream CAD and BIM workflows, it will struggle in more demanding 3D workflows, such as game engine design viz, particularly at 4K resolution. You can also forget about VR, which is an important consideration if you intend to keep this machine for 3-4 years, as is typical for most of our readers. With a standard tower you can always upgrade the GPU, so if your workflows change then you can adapt. This is simply not possible with the Z2 Mini.
In summary, if you want a small, stylish workstation with exceptional portability, then the Z2 Mini ticks all the boxes. It’s perfect for entry-level to mainstream 3D CAD work now, but it could leave you short in the future.
Greg Corke
1 HP Z2 Mini with 24-inch display for scale 2 HP Z2 Mini with HP Z240 SFF for comparison 3 HP Z2 Mini mounted behind a display 4 By rotating the metal sleeve by 90 degrees, IT managers can block off USB ports for security

2 3
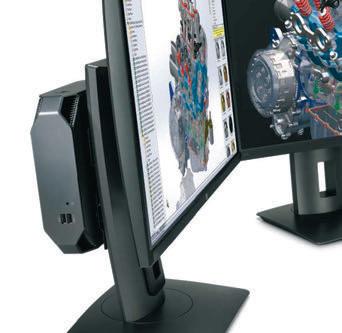

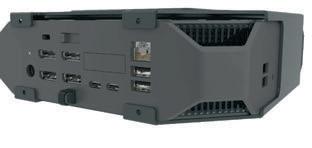
Letter to the Editor The developer’s story behind Revit
Dear Editor:
In your announcement of Dr Jonathan Ingram’s March 28 presentation at DEVELOP3D LIVE you referred to him as the man behind the foundations of Revit, a viewpoint expanded upon by Dr. Ingram in his presentation (tinyurl.com/ History-BIM). I thought your readers might be interested in the real story connecting Revit and Dr. Ingram’s AEC design product, Reflex.
In 1997, Leonid Raiz and I founded Revit after having been key developers of several Mechanical CAD systems, most notably PTC’s Pro/Engineer. Our goal was to bring many of the innovations that PTC had spearheaded in the MCAD market to the AEC market.
Soon after leaving, we agreed to provide PTC consulting services in exchange for a non-exclusive development license to Reflex, which PTC had recently acquired. Although we were planning to develop our software from the ground up, we thought this license would be useful for three reasons. First, it might help us in negotiating with venture capitalists; second, it would protect us if PTC asserted we were violating our non-compete agreements; and finally, we thought there might be some low level utilities we could extract from the code.
After receiving several hours of instruction in the software architecture of Reflex from Reflex developers, we decided not to use it as our starting point because of several important differences at the very foundations of the software. At that point, we put it aside and never looked at it again.
These foundational differences had their roots in our product vision. Prior to writing a single line of code we spent considerable time interviewing architects and studying their workflow. We wanted our users to express their design intent graphically, because that was their natural language and because that allowed for a much greater variety of designs than any dialogue boxes could. We did not want our users to have to do any programming, so they would need a graphical way to specify not just a static design, but also the relationships between elements, so the software could keep the design coordinated through continuing design modifications.
Reflex components are created using a specialised programming language (VEL), whereas Revit components are created in a graphical “family editor”. What’s more, some of the relationships between Reflex components are programmed by the user into the component definition, whereas no such coding would be possible in the Revit family editor. Instead, Revit handles relationships through a centralised change propagation engine that gathers all the elements to be changed, sorts them in a context-dependent way, and then executes all the changes.
Our decision not to use Reflex as a foundation was probably influenced by our earlier experience at PTC. Like Revit, Pro/Engineer had also been built from the ground up. We had found that maintaining bi-directional associativity between components, views, and annotations required all code to be tightly interconnected, so we thought that starting from a system with a different foundation would be more difficult than starting from a clean sheet. It would have been like building the Freedom Tower on the foundation for the Empire State Building.
During Dr. Ingram’s presentation, he speculated that Revit was based on Reflex. As the dozens of programmers and architects who created Revit could testify, that is not the case: Revit was not based on Reflex. No code from Reflex was used, and we were less familiar with Reflex than with many other architectural design packages, such as ArchiCAD. In fact, we found the most inspiration from a $50 product called 3D Home Architect (a home version of Chief Architect), which had a clean, simple user interface. No design decisions in Revit were influenced by our modest familiarity with Reflex, and any similarities between the two were either well known ideas in the industry or purely coincidental.
Dr. Ingram provided various lines of evidence to support his hypothesis that Revit was based on Reflex, but that evidence does not stand up to scrutiny.
First, he asserted that several bugs in Revit were identical to bugs in Reflex. He gave the example of a complex wall joint. However, the Revit and Reflex behaviours are actually quite different in this case: in Reflex no wall component layer extends the full length of the vertical wall, and many of the Reflex layer boundaries end in space with no connecting layer boundary. Furthermore, the behaviour in Revit is not in fact a bug — it is one of several possible ways this wall joint can be built. Revit has an “Edit Wall Joins” command that allows users to specify which of these valid constructions they intend. So, it turns out this is an example of a difference between the two systems, not a similarity.
Dr. Ingram’s second line of evidence was a list of features common to both systems, such as “Instance based building model providing coordinated drawings, model, and information”.
All of the features he listed were in Pro/ Engineer, or were construction-industry analogs of Pro/Engineer capabilities, and Leonid and I had helped implement them a decade before we had ever heard of Reflex. Many of those features also existed in other AEC systems, including 3D Home Architect. To assert these commonalities as evidence that one system was based on the other would be like asserting that one car design is based on another because both have an engine and doors.
Finally, Dr. Ingram states that 100 manyears of effort went into Reflex, and he doubted Revit could have been built from scratch as quickly as it was. However, by the time Revit was acquired by Autodesk in 2002 it had a comparable amount of development effort. Revit raised more than $50 million of venture capital, more than enough to fund such development. We had an elite team of talented developers who had experience developing parametric systems and knew what they were doing.
It turns out, though, that Reflex did have a role in the history of Revit, but it is one that Dr. Ingram was not aware of. The team that helped PTC evaluate whether to acquire Reflex included both Leonid Raiz and me, as well as several consultants from the AEC industry.
Those consultants were very impressed with Reflex, and considered it to be the state of the art for that industry. Leonid and I were surprised to hear that, because the software lacked many of the capabilities that we had come to expect in mechanical design systems. For example, at the time, if you moved a wall in Reflex, all of its doors and windows stayed where they had been, hanging in space, instead of moving with the wall. Pro/Engineer had been able to correctly handle that kind of thing for more than a decade. That helped us recognise that there was an opportunity to provide better software for the AEC industry.
Dr. Irwin Jungreis Revit Founder
Dr Jonathan Ingram has the right to respond.
The Evolution of Going Small
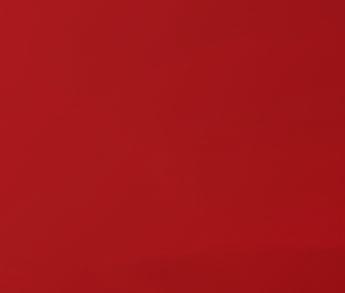
FUJITSU Workstations CELSIUS W570 & J550/2

Previous generation W Series 28 liter CELSIUS W570 Desktop Workstation 21 liter up to NVIDIA® Quadro® P4000 CELSIUS J550/2 Small Form Factor Workstation 10 liter up to NVIDIA® Quadro® P2000
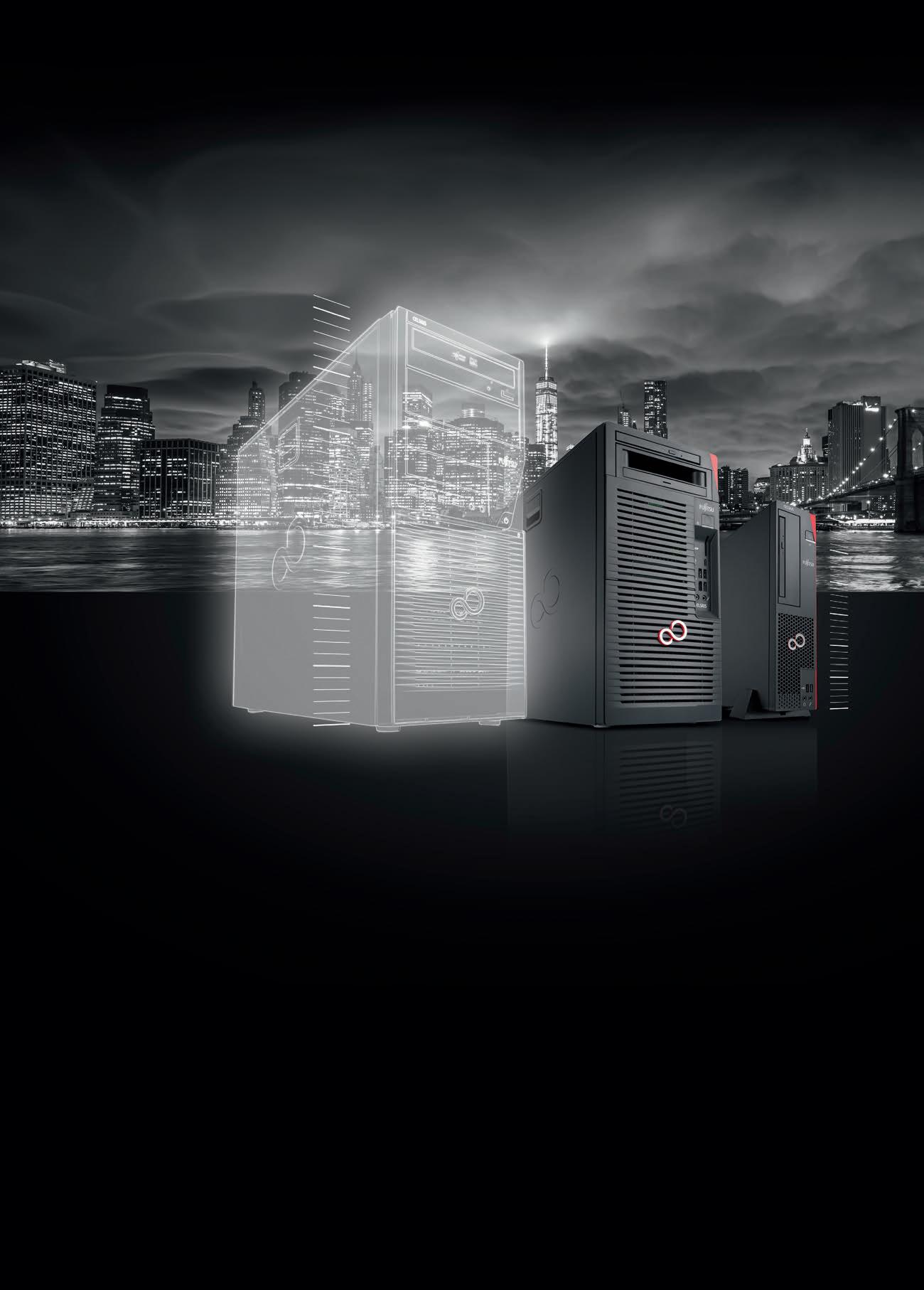
Fujitsu Workstations – Made for Innovators and Creators
The fi rst-ever desktop workstation in 1995 was a pioneer of its era, and Fujitsu has never stopped innovating and enhancing the products since. FUJITSU CELSIUS workstations, featuring NVIDIA® Quadro® graphics, provide the ultimate in performance and reliability to increase application effi ciency for CAD users, architects and engineers. All products are whisper quiet thanks to their excellent thermal management and are optimized for use with a host of leading workstation applications, like Autodesk, Dassault Systèmes, Siemens PLM or PTC.
More information around Virtual Reality: www.fujitsu.com/global/products/computing/pc/vr/

Copyright 2017 Fujitsu Technology Solutions GmbH Fujitsu, the Fujitsu logo and Fujitsu brand names are trademarks or registered trademarks of Fujitsu Limited in Japan and other countries. Other company, product and service names may be trademarks or registered trademarks of their respective owners, the use of which by third parties for their own purposes may infringe the rights of such owners. Technical data are subject to modifi cation and delivery subject to availability. Any liability that the data and illustrations are complete, actual or correct is excluded. Designations may be trademarks and/or copyrights of the respective manufacturer, the use of which by third parties for their own purposes may infringe the rights of such owner. All rights reserved.