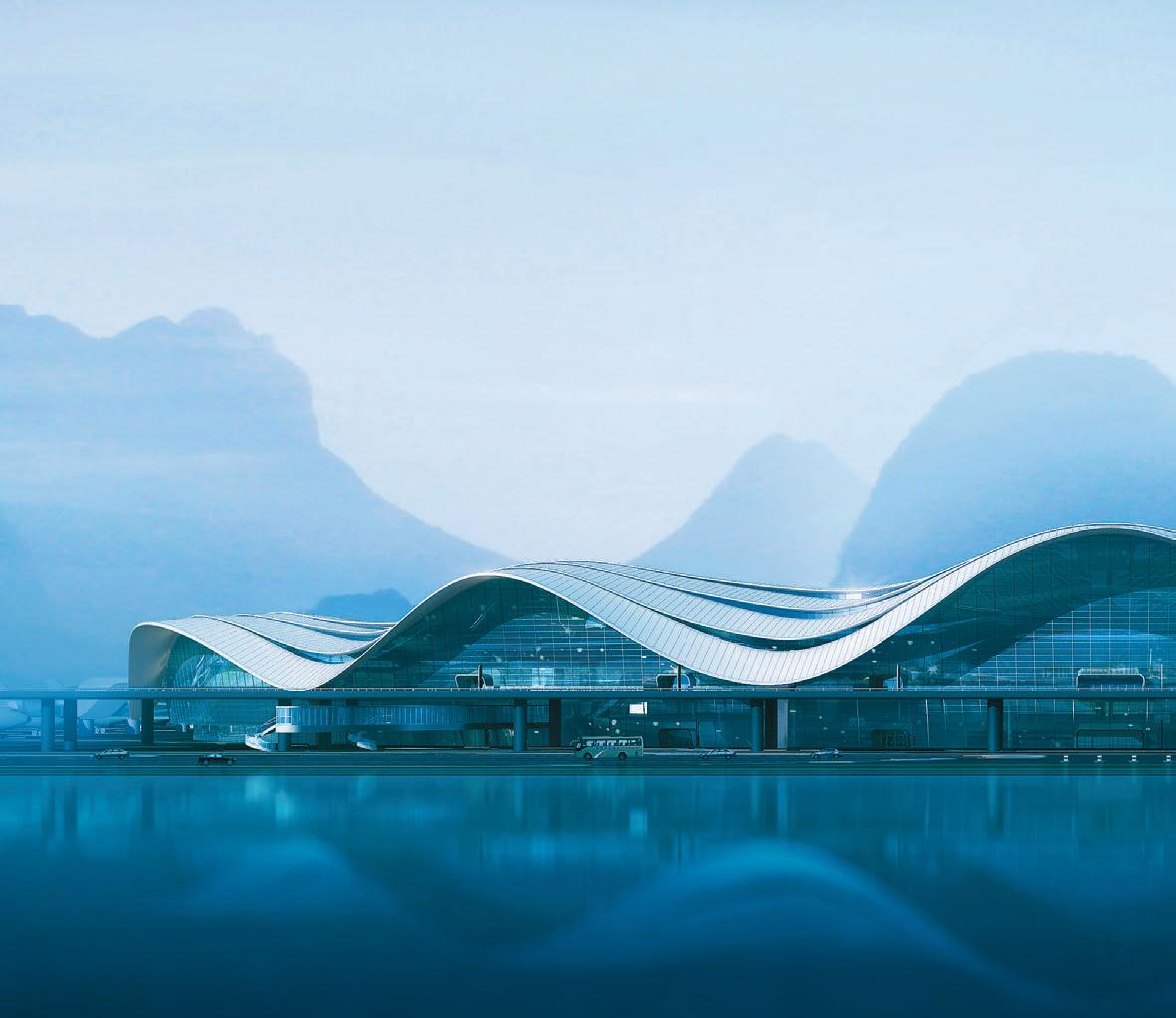
7 minute read
Scenic harmony
Scenicharmony
Smart steel detailing software from Autodesk has helped a new airport terminal in Guilin, China to blend in with the distinctive landscape of its surrounding area.
Boasting one of the world’s most dramatic landscapes, it is no surprise that Guilin in China is an increasingly popular tourist destination. Visitors travel vast distances to see how its distinctive karst limestone hills and waterways combine to form unique views. The area’s thriving manufacturing sector, meanwhile, helps to attract business travellers, too.
Guilin’s beauty has historically been a source of inspiration to artists and photographers. More recently, it inspired architects at the Beijing Institute of Architectural Design (BIAD) to design an airport expansion that resonates with the area’s natural beauty.
Each year, nearly 6 million people pass through the Guilin Liangjiang International Airport, with the airport’s single terminal, a 1990s-era structure, serving more than 31 airlines.
Recognising that the volume of traffic was rapidly outgrowing the airport’s capacity, Chinese authorities decided to add a second terminal at Guilin. When this opens in 2018, Terminal 2 will cover more than 100,000 square meters and add 24 new gates.
Qichen Jiang, director of the BIM centre at the Steel Structure Engineering Company (SSEC), gives her perspective on the airport: “The airport’s roof features a double-arching design and peaked shapes that mimic Guilin’s landscape. Beautiful limestone hills provide a backdrop to the new terminal and harmonise with the design. The unusual shape presented many steel engineering, detailing and construction challenges, but the project team overcame each one to deliver a terminal suited to the area.”
A new design for Guilin SSEC, part of China Construction Eighth Engineering Division (CCEED) of the state-owned China State Construction Engineering Corporation, is responsible for the steel detailing, fabrication and construction of Terminal 2 and is playing a crucial role in realising BIAD’s design.
The Guilin Liangjiang International Airport Terminal 2 project will span more than 100,000 square meters and add 24 gates to the airport’s capacity. Images courtesy of Beijing Institute of Architectural Design

The U-shaped Terminal 2 includes four floors: three above ground and one below. The curving steel roof is a large-span, double-curved arch structure. Additional steel components include supports, boarding-gate structures and connection bridges. In total, SSEC will use more than 11,000 tons of steel in the terminal structure.
Fabricated off-site, each piece of steel must be placed and welded according to a precise plan. Any fabrication or construction error could delay the project or add unexpected costs, so precision steel detailing is crucial to its success.
Legacy tools require a rethink To address the project’s challenges, the SSEC team decided to rely on BIM tools for detailing – but its legacy tools for steel detailing didn’t enable smooth data flow from engineering designs which were in Autodesk Revit and couldn’t handle the complexity of the structure’s curves.
“We saw that we might need to change our detailing application to meet the challenge presented by the project,” says Jiang. “It was essential to choose a tool that could help us deliver the project. At the same time, we didn’t want something that would take our team a long time to learn.”
In evaluating its options for modelbased detailing, SSEC prioritised ease of use and the ability to handle curves. The team decided that Autodesk Advance Steel seemed to meet its criteria, but it wanted to be sure, so it launched a pilot to put Advance Steel through its paces. Not only was Advance Steel able to handle curves, but also stood out in other ways, says Jiang.
“Advance Steel could clearly help with the complex aspects of the project. It was also faster for many more traditional detailing tasks. We liked the fact that its interface is based on AutoCAD software, which is familiar in the industry. This helped our team learn to use it much more quickly than is typical with unfamiliar software.”
The SSEC team found it could bring models created in Autodesk Revit into Advance Steel without the loss of data and, should the need arise, establish a bidirectional link between the two packages, making it easier to incorporate late design changes into their process.
Just as importantly, Advance Steel offers support for Industry Foundation Class (IFC) standards, and the project team planned to follow IFC standards to exchange data on the project.
“We were pleased with the interoperability of Advance Steel,” says Jiang. “It was easy to bring the structural models created in Revit into Advance Steel. We did not have to redraw elements, which was common with our prior software.”
With the decision to use Advance Steel, the SSEC team began detailing the structural steel model. That meant it was time to confront the

1 The U-shaped Terminal 2 includes four floors: three above ground and one below 2 SSEC uploaded its detailed models into Autodesk Navisworks to turn them into 3D visualisations 3 Computational design tool Dynamo was used to find the optimal way to section the arch for fabrication
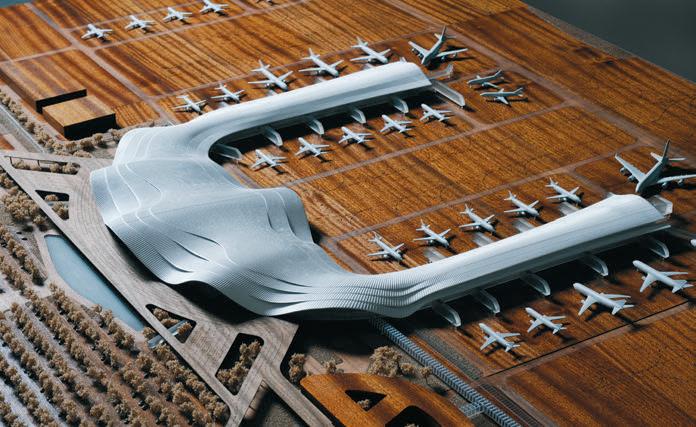
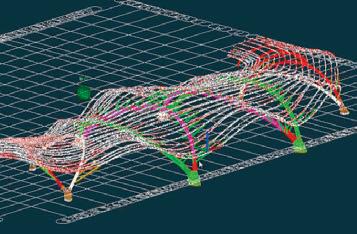
next major challenge: detailing the compli- 2 3cated double-curving arch quickly and efficiently. The SSEC team needed to determine the optimal way to section the arch for fabrication. Working with the structural engineer, it turned to Dynamo for computational design. Dynamo lets designers create visual logic to design workflows that drive the geometry of design models. Using Dynamo, the team computed how to divide the arch into 250 parts. It then synchronised with the design model in Revit, track costs throughout a project.” “Once you have a 3D model, it becomes and exported the model into Advance After overcoming its challenges detail- a tool for sharing information and collabSteel. Once in Advance Steel, the detailers ing the double-curving arches, the SSEC orating,” says Jiang. were able to detail the arches, readying team decided to use its detailed models to “We were able to explore the best ways them for fabrication. help the construction team, since it antici- to erect the steel in the office, seeing what
“Dynamo helped us find efficient ways pated that the non-traditional arches might worked well before construction even to section the arches,” says Jiang. “Such be difficult to install. For instance, welders began.” calculations would have taken much might be unsure of the optimal sequence. longer without BIM-based computation- Figuring this out in the field could poten- Terminal taxis for take-off al design. With the 3D shapes automati- tially lead to wasted time and materials. As Terminal 2 advances towards its 2018 cally generated, we simply brought them SSEC uploaded its detailed models into opening date, steel detailers at SSEC say into Advance Steel. Then it they are proud of their work was intuitive and time-efficient to create and detail the arch models.” ‘‘ Once you have a 3D model, it becomes a and the ways that BIM has helped to improve the whole project. tool for information sharing and “BIM opens so many possiFaster, smoother Bill of materials (BOM) crea- collaboration. We were able to explore the bilities to use models in new and innovative ways,” says tion highlights the advantages best ways to erect the steel in the office Jiang. “The models behind of the BIM process, because the intelligent data in the before construction began the design, detailing, and fabrication are intelligent and design and detailing models Qichen Jiang, SSEC getting smarter. As the modmakes it easy to track materi- els improve, so do the proal types and quantities. As the engineers Autodesk Navisworks, which turned cesses they drive.” created their design models, Revit soft- them into 3D visualisations. The team “The airport project shows how that ware automatically tracked material use. then sequenced the construction of the progress happens,” she adds. “In moving The detailing process added more materi- arches and other portions of the terminal, from our prior detailing tool to Advance al and quantity information to the models creating a 4D construction plan based on Steel, we reduced the time spent on labour as the team worked, enabling the SSEC their explorations, with the 4th dimen- by 20%. Our team saved a full month on team to generate BOMs automatically. sion being time. After generating a video detailing. Interoperability between our
“We simply selected the BOM template of the plan, this was shared with the con- detailing tools and other BIM tools saved we wanted to use,” says Jiang. “The pro- struction team, so that steel installers additional time and helped us create a cess was then largely automatic. It saves could easily visualise what tasks they better construction plan.” significant time, and makes it easy to needed to perform, and in what order. ■ autodesk.com
