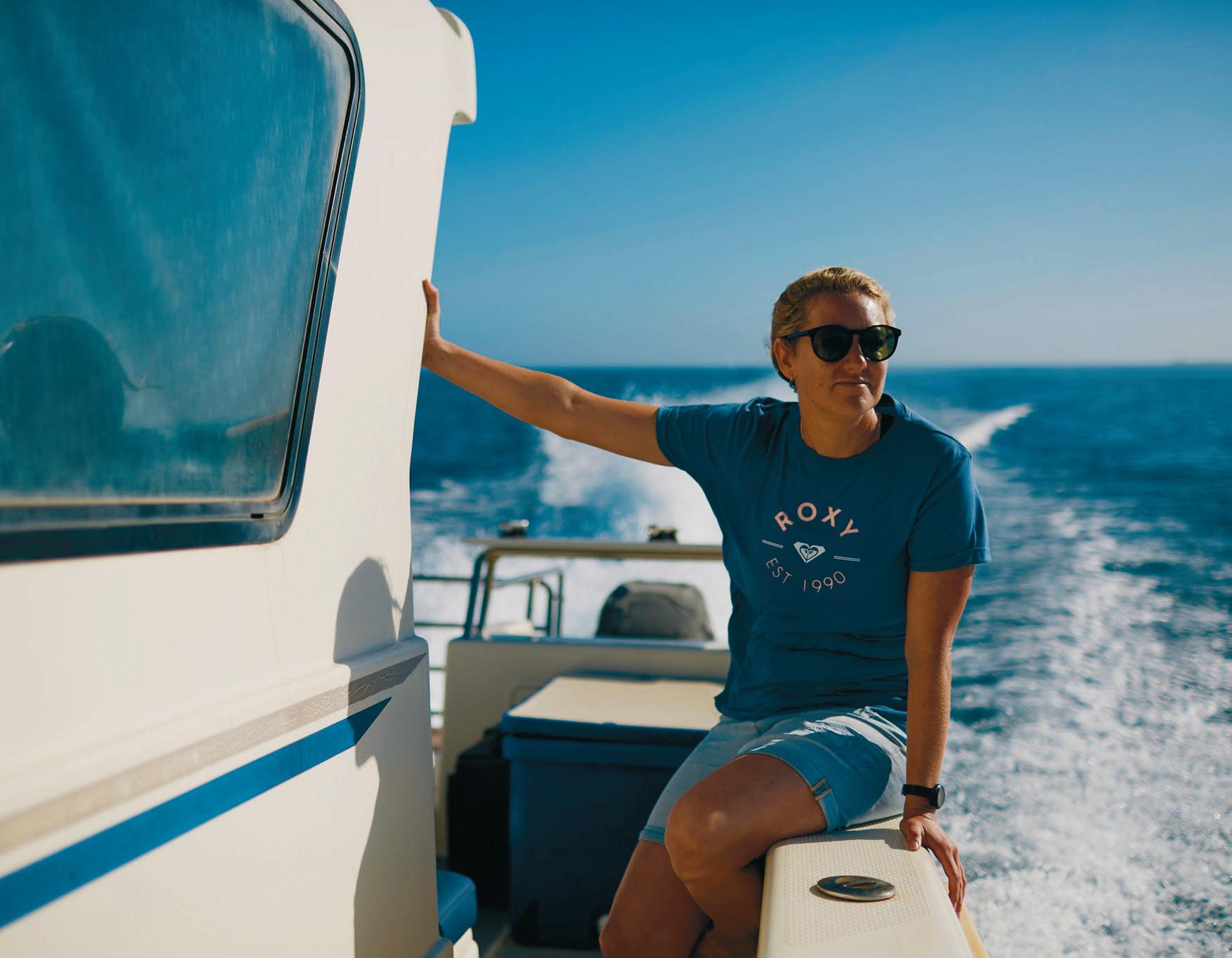
2 minute read
ENGINEERING NEW GROWTH
The struggle to repopulate Australia’s damaged coral reefs with new growth is too great for manual work alone. Stephen Holmes speaks to the team at Coral Maker about how it is using product development and manufacturing know-how to scale up the fight like, how that would work, how she would interact with that in the water, how the seeding would work, and how we could use things like robotics to automate the seeding and assembly of the skeletons.”
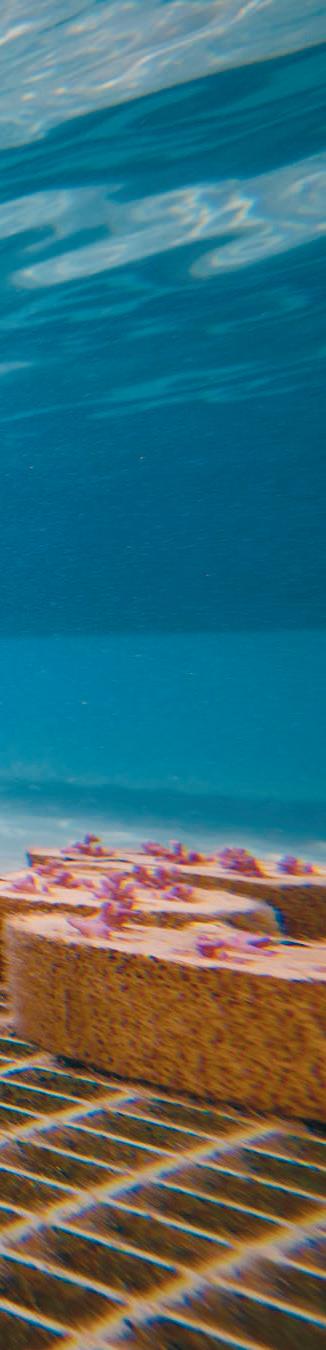
With the global Covid pandemic forcing Foster to leave San Francisco and return to Australia, the team was forced to work across multiple time zones. “It was almost impossible for us all to be on a call at one point, so throughout this whole project, we’ve had to collaborate remotely,” says Bowerman.
“Fusion has been amazing for that, because it’s enabled us to have this one location where we can all work on the same design data. We can all have input to the same design, but we can also have a design up on screen, we can all be commenting on it, we can be saying we want things to be changed, we can do those changes in real time and get Taryn’s feedback straight away.”
If the whole team can’t be in a meeting at the same time, he adds, “we can make some changes, she can then see the changes have happened, review the design, make comments and we can come back to it at a later date.”
Accelerated Growth
The dome-shaped skeleton, with square sockets in which to dock coral seed plugs, appears quite simple, but a lot of design iteration has gone into devising this optimal shape.
A key factor is that it enables the accelerated growth of the coral, which would naturally arrive at this domed form anyway. Furthermore, this skeleton can be quickly and cheaply produced using the dry-stone casting process.
“It’s a process that is robust. It’s fairly crude in its method, but it’s certainly able to give us the rate that would be needed to try and solve this problem,” says Bowerman.
Initial prototypes could be shared as files to be 3D printed, allowing the Australian team to test them for size and handling them underwater. Once the form had been tested, back in Birmingham, the team began to cut the tools for mass producing the skeleton using its array of 5-axis CNC machines.
Bowerman explains that the UK team is not only making prototypes, but also proving out the manufacturing process, so that when the skeletons go into production, the design can be given to a local manufacturer and it’s ready to go.
“We know there are no kinks in it, and we can even get to the point where we have the code that can run on that local manufacturer’s machine, so we know that they’re going to get a like-for-like part of what’s already been tested over here in the UK. We’re nurturing and incubating that technology here, and then we can deploy it to wherever she is locally.”
With the volumes of coral needing to be seeded already daunting, and with ocean temperatures continuing to rise, local production to ensure successful deployment of new coral will be key. As water temperatures continue to change, reef regeneration may need to be relocated from the tropics to cooler high latitude ‘fringe’ reefs. To accomplish that effectively, reef restoration needs to be mobilised as a bigger, more organised effort.
While the versatility of the design allows skeletons to be built using local aggregates, or in different shapes to better aid different species of coral, the need for millions or potentially tens of millions of structures per year has seen the team having to look further at the manufacturing process.

To overcome the challenge, Coral Maker wants to automate coral propagation using robotics and artificial intelligence for onsite deployment, with capabilities able to work collaboratively with humans and also freeing them up to do more complex work.
With many other ecological challenges to be tackled, the technology that allows designers and engineers around the world to work together to develop solutions at scale might just be the seed that helps nature regenerate elsewhere. www.coralmaker.org

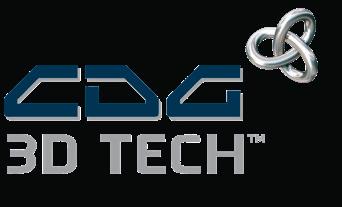
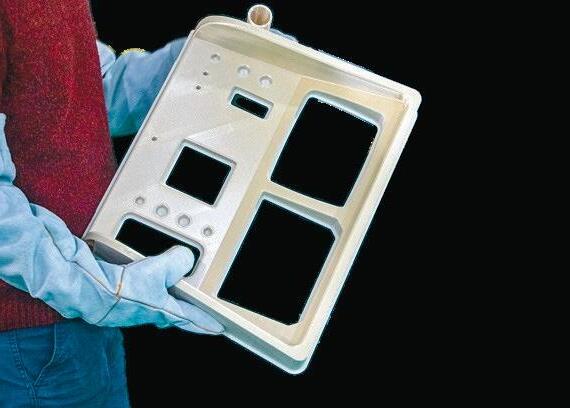
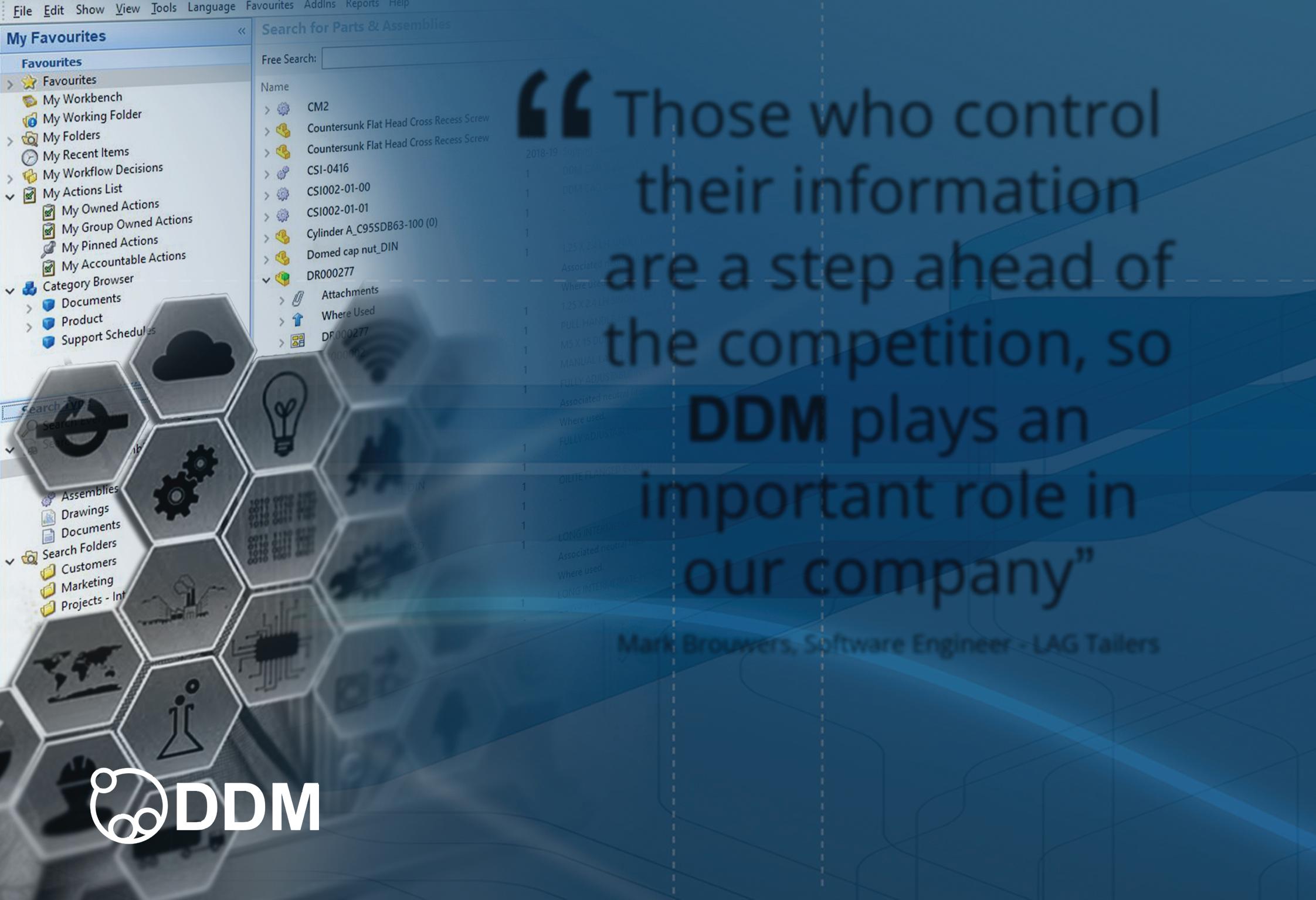