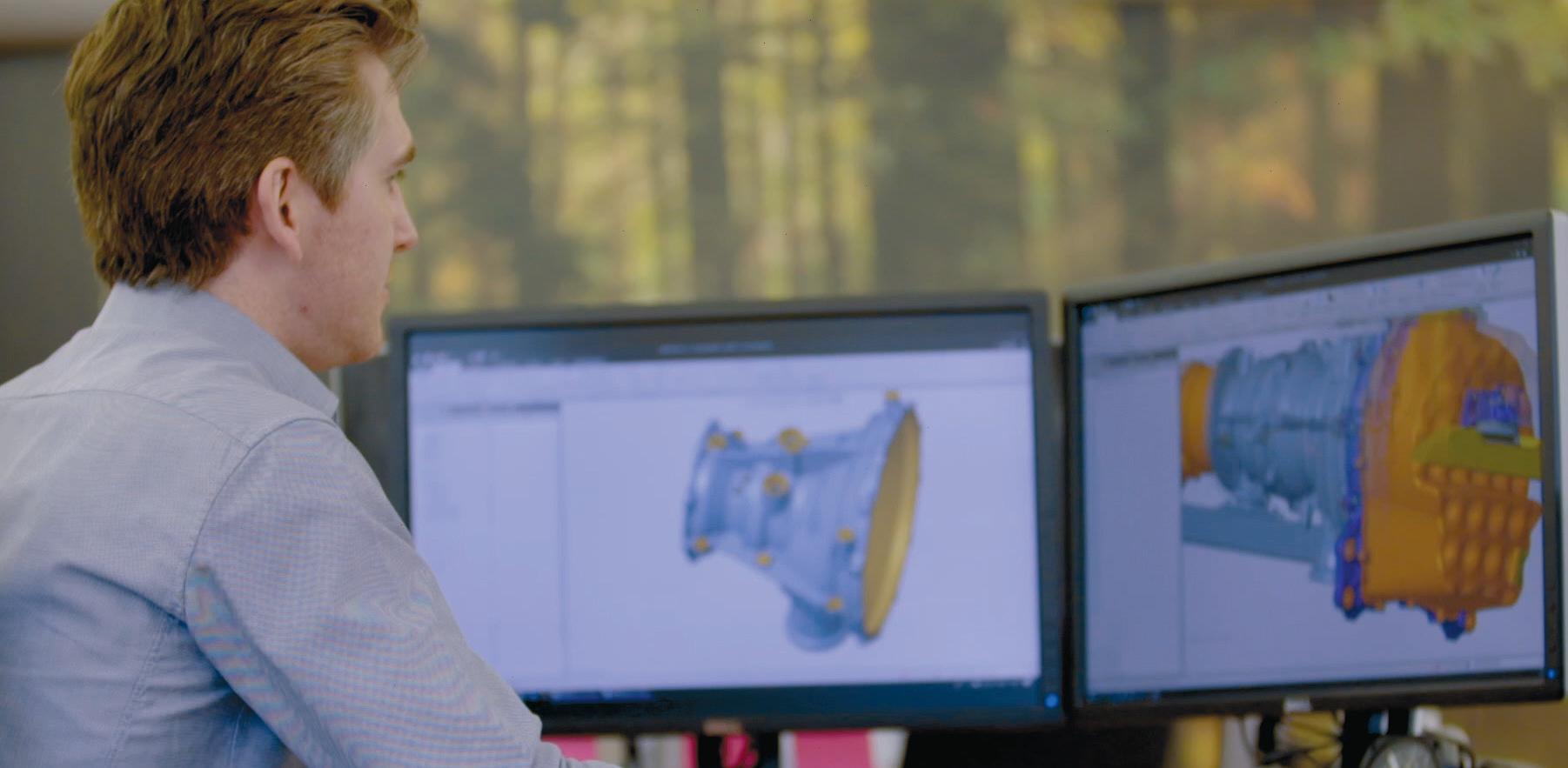
6 minute read
AWAY
All the pieces are coming together,” says Steve Lindsey, CEO of Lontra, with evident pride and satisfaction. After years of hard work, Lontra is now entering a new phase of its journey in producing energy-efficient rotational industrial equipment, working towards achieving sustainable development and reducing the environmental impact of industrial processes.
The last time DEVELOP3D caught up with Lindsey was back in late 2017 (www.tinyurl.com/D3DLontra), when he talked us through his invention of a new kind of energy-efficient positive displacement air compression technology.
Since then, things have moved on considerably. In April, one of the largest pieces of the picture fell into place, when the company’s brand-new, £17 million manufacturing centre in Doncaster, UK, began production of its flagship product, the LP2 Blade Blower.
Built from scratch with the help of a £7 million grant and loan package from the South Yorkshire Mayoral Combined Authority, combined with approximately £10 million of private-sector match-funding from Lontra, this is a state-of-the-art smart factory.
From the electric vehicle (EV) charging points outside to the smart lighting inside, every effort has been made to ensure that the factory is as sustainable as possible. Its 60,000 square feet of floor space is home to many millions of pounds’ worth of machinery, all connected using Internet of Things (IoT) technology. Eventually, the level of automation planned here will support lights-out manufacturing, with machines running through the night, with little to no human intervention required.
Blow By Blow
The LP2 Blade Blower can also boast some pretty impressive sustainability credentials itself. Heavy industry depends on air compressors to deliver power to manufacturing lines, drive furnaces and convey materials. They are used for pneumatically conveying granules in cement factories and crumbs in biscuit factories, for example, as well as for aeration in water and wastewater treatment facilities.
But all that blowing comes at a heavy cost to the environment. Compressors account for a staggering 10% of Europe’s industrial electricity use and as much as 40% in some plants. In wastewater treatment, 70% of total energy used is for blowers. In total, that equates to more than 10TWh (Terawatt-hours) of electricity every year and some 4.3 million tonnes of CO2 emissions.
Independent trials of the LP2, by contrast, have found it capable of offering energy savings of up to 34% when evaluated against comparable market-leading alternatives, so the potential advantages for buyers are huge. Plus, according to Lindsey, this new compressor is also built for reliability and longevity; intensive testing and analysis have demonstrated results of more than 80,000 continuous operating hours without the need for repairs.
Tooled Up For Growth
Software is another important piece of the picture, and an area in which Lontra gets a lot of valuable help and advice from PTC reseller Inneo. Lindsey says that using a modern 3D CAD system, in the form of PTC Creo, was critical to achieving the LP2 Blade Blower’s complex geometry.
Meanwhile, Creo add-ons for FEA (finite element analysis) and behavioural modelling in particular have greatly assisted in achieving the necessary stability and distortion requirements that make the LP2 Blade Blower so energy-efficient.
Where simultaneous optimisation of mechanical and thermodynamic performance is required, data from PTC Creo feeds directly into BladeSim, a software suite built in-house at Lontra for the virtual prototyping of positive displacement compressors, vacuum pumps and their ancillaries. As well as improvements to compression, internal leakage and heat transfer, these tools tune silencers and ancillaries for optimisation of the complete system.
Another key element of the portfolio is Windchill, PTC’s product lifecycle management (PLM) suite, which makes a big difference to Lonta’s efficiency and sustainability, by saving not only time but also waste.
Windchill ensures that the company’s record of the materials and components used in its products are kept up to date, helping to capture learning from the design and development process, as well as reducing errors, scrap and wastage on the factory floor.
“Both of our sites have access to Windchill, and our team also works remotely – designers, purchasing, manufacturing engineers, CNC, assembly, and quality,” says Lindsey. “These tools ensure that everybody is working off the most up-to-date data. In the future, we plan to provide certain suppliers with access to this data too.”
Next Smart Steps
Digital technology at the heart of the next exciting stages of Lontra’s expansion, bringing to life all the benefits of the connectivity built into the LP2’s design, with its 25-plus internal smart sensors. This work will be overseen by Lontra Digital, a new arm of the business, responsible for the design and development of an app that will enable the company and its customers to monitor units once they’re hard at work in factories and water treatment facilities.
“For context, almost every factory will have a maintenance person or team, whose job it is to keep machines running. They spend their days in and around those machines and, regardless of whether an alarm has been triggered or not, they can tell when something that doesn’t sound right or is running hot, signalling that there may be a potential problem,” Lindsey explains.
However, that kind of experience is in short supply and dwindling fast as older members of the workforce retire. And even in facilities that have these people on staff, it’s often the case that their expertise could be put to better use.
“Now, thanks to data collection and machine learning, instead of the need for full-time expertise on-site, the units can be monitored remotely from one centralised location,” Lindsey explains. In this way, Lontra Digital will help to increase reliability and reduce downtime for customers.
This monitoring capability is built on a cloud-based, proprietary IoT platform, designed from the ground up with data and network security treated as a priority.
Blowers will be connected via a private cellular network to Lontra’s cloud, with no networking infrastructure or capability required of customers, because Lontra manages the machine connectivity.
Data will be uploaded in real-time from the LP2’s sensors and then made available to customers for analysis, download and/or integration via a cloud-based portal. Numerous connectivity and control options are available, encompassing smartphone and tablet apps to transitional industrial protocols such as Modbus and Ethernet/IP. Customers will get secure, real-time remote support via the managed cellular connection on request, Lindsey promises, as well as fast development and turnaround of new features and fixes.

“The LP2 Version 1 is just the starting point,” he says. “With the secure platform foundations in place, upcoming iterations will focus on features such as machine interconnectivity with advanced control strategies, along with improved anomaly detection powered by machine learning models.”
A Digital Thread
In effect, what Lindsey is describing is a digital thread - a continuous, seamless strand of data that connects each stage of a product’s lifecycle, from design through to manufacture and onwards to maintenance and repair. At all these stages in the lifetime of the LP2, says Lindsey, a digital twin of each and every blower is maintained, delivering insights and driving optimisations that are passed on to the customer in the form of a more efficient machine, more predictable maintenance cycles and, ultimately, increased value from their investment.
What Lindsey hopes to do, he says, is bring a userfriendly, modern, consumer-like experience to the industrial space. “Things like Amazon one-click are just not seen in the manufacturing world. That needs to change,” he says.
The hard work of getting all these pieces into place directly supports that vision, he adds. “The power of all this lies in our ability to start completely from scratch and say, ‘Okay, if you were to redesign the industrial environment with a fresh pair of eyes, how would you do it?’ That’s why, for Lontra Digital, we’ve brought in people who are not from the industrial arena. They’ve come from developing mobile apps for fintech, for example. Because that’s the kind of fresh thinking that is needed here and the core underlying technology is absolutely key to that.”
This fresh thinking and core underlying technology will be a launchpad for new products and approaches as Lontra grows and expands, he says. He’s already thinking about compression at different levels. The LP2, for example, is low pressure, but there are plenty of applications out there that require higher air pressure, as well as vacuum applications. Lontra has already patented its idea for a non-return valve, which would be a valuable addition to its product line-up. Finally, Lindsey is also considering refrigerants for heat pumps that could bring the same Lontra efficiency to another class of products entirely.
“It’s an incredibly exciting time for us,” he says. “Weaving all these pieces together is going to enable us to do some amazing things.”
Watch this space. ww.lontra.co.uk

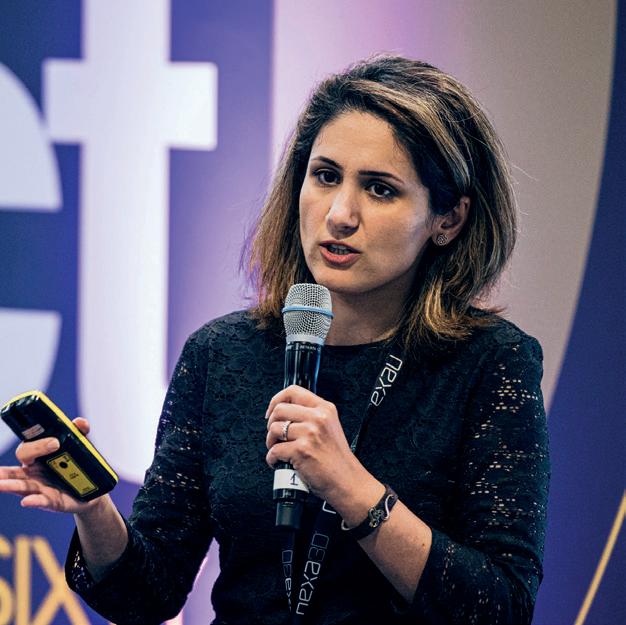
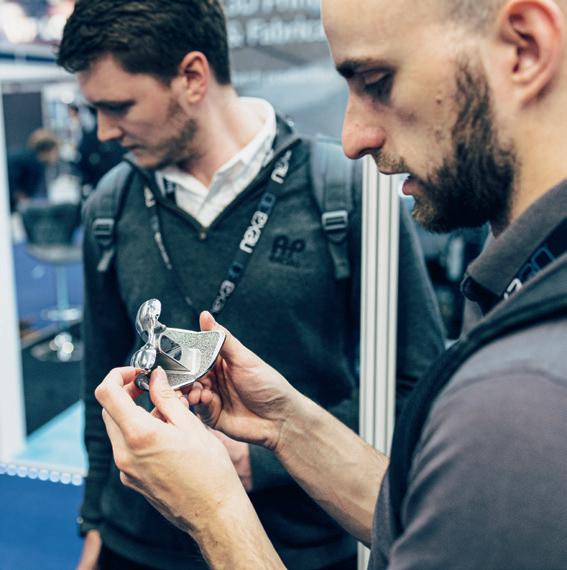



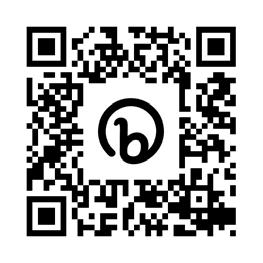