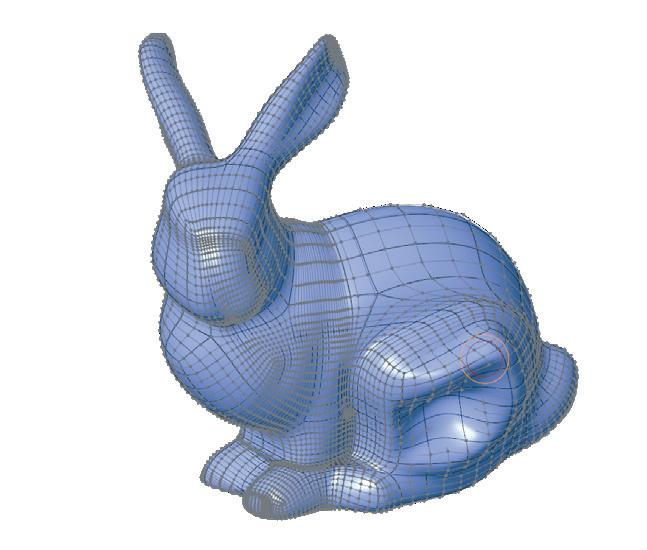
20 minute read
PTC Creo 9 highlights
FIVE KEY UPDATES IN PTC CREO 9
» The latest release of PTC Creo includes enhancements to core tools, a raft of new technologies and more tempting simulation nuggets that look to streamline design work and speed time to market
With Creo 9, released in May 2022, PTC has delivered a host of productivity and usability enhancements that it claims will help users to deliver “your best designs in less time.”
In other words, there’s a strong emphasis here on product improvement and faster time to market.
According to Brian Thomson, divisional manager and general manager of Creo at PTC, Creo 9 “is an important release, and our customers’ feedback played a big part in making that happen.”
As an overview of what’s new in the release, Thomson provided the following detail: “We made core improvements, such as the divide surface capability and stronger design intent management to benefit our users. We focused on advanced technologies transforming product design – including simulation, generative design and additive manufacturing.”
And to better support users, Thomson added, “we’ve strengthened Creo’s ergonomics capabilities. All these enhancements are about helping engineers get their best designs to market more quickly.”
There’s a lot packed in to this latest PTC Creo edition – and, according to Thomson and his team, even more enhancements already lined up and ready to be added in when the first maintenance release comes around.
For now, here’s a brief guide to some of the highlights of this Creo 9 release.
1
FREEFORM CAPABILITIES
Creo’s Sub-D Freestyle modelling functionality was originally introduced way back in Creo 2.0. This allows users to manipulate a control mesh around a CAD model, which is clearly very useful. In Creo 9, however, PTC has gone further, by adding the ability to modify that mesh using brushes. What this means is that, instead of picking an individual vertex of the control mesh, users can now use their mouse as a brush. From there, they can choose both the diameter of the brush head and the hardness fall-off, in order to better control the sensitivity of brush strokes that manipulate all of the control vertices touched. This can then be used to push and pull surfaces as needed, mirror them, or even to attach them to an imported STL file and sculpt over it.
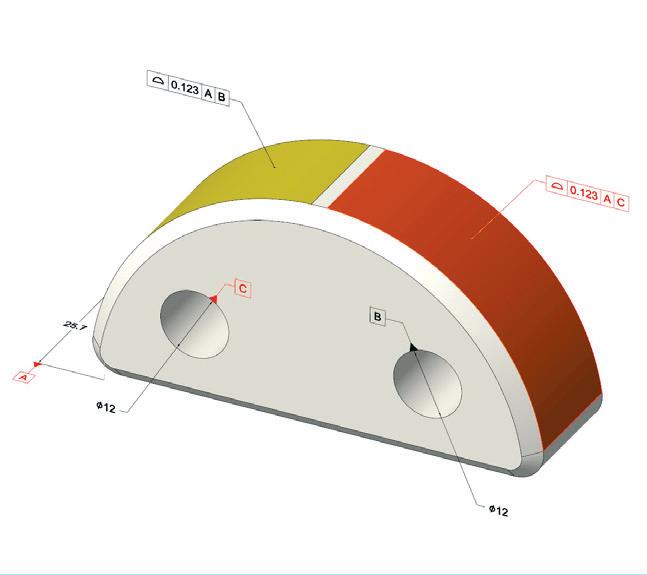
2
DIVIDE/UNIFY SURFACES
The ability to divide and unify a surface supports a bucketload of valuable use cases. For example, it can be extremely helpful when it comes to rendering aesthetics, simulation load regions, engraving and generative design load and constraint surfaces. Likewise, it works well in simpler contexts, too, enabling a user to switch a surface colour, so you can find it in an assembly quicker, for example. The new Divide Surface command inside Creo lets the user take either a given chain of curves, a loop of curves or a sketched entity and project that onto the surface, and split a single surface or multiple surfaces. This allows you to then isolate those surfaces and do your thing. And, should you wish, you can unify the surfaces again using the Unify Surface command.
FIVE KEY UPDATES
3
CURVE FROM POINT
The ´curve from point’ tool in Creo 9 enables users to specify a point on a surface or geometry, give it a direction, and it will then create a geodesic curve between two points that represents the shortest distance following along the surface. This builds on the geodesic curve functionality introduced in Creo 8 and, in its newest incarnation, may prove particularly valuable for designers and engineers creating composite design products; for example, when a users is looking to lay fabric down over a shape with a straight edge to it and needs to ensure that the material conforms to the shape of their geometry. Being able to quickly and easily identify this geodesic curve speeds up the overall design process and provides users with an additional level of control.
4
CUSTOM MANNEQUINS
Expanded ergonomic tools have been included in this release, in order to help designers create products that comply with safety, health and workplace standards. While Creo has shipped for years now with a library of mannequins built to fit specific standards, some customers said that they wanted to be able to create their own custom dummies to fit specific demographics. Creo 9 now includes this capability. Mannequin reach has also been added as a constraint: this means that if changes are made to a CAD model, the model will regenerate and so will that constraint. If, for any reason, a mannequin is unable to reach a particular area, it still moves to its extremities of reach, but Creo displays a dimension that tells the user how far short of that location it is.
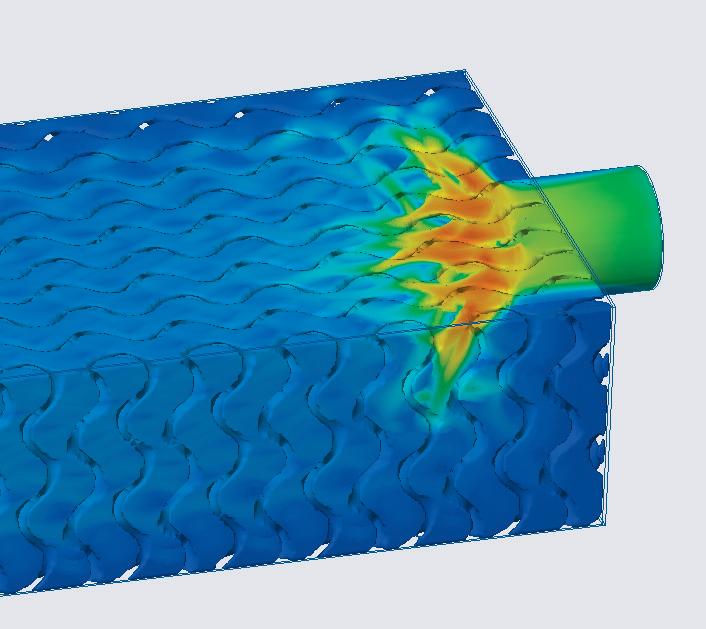
5
FLUID FLOW LATTICE SIMULATION
Creo 9 also sees an expansion of formula-driven lattice structures to create gyroids. That’s great for a snazzy concept of a heat exchanger, but it’s a capability that Creo 9 backs up by enabling users to perform fluid flow simulations using Creo Simulation Live. PTC has worked hard to make these features more user-friendly, with an ‘initial simulation’ option available. This enables users to quickly ensure that a given optimisation study is set up correctly, saving them valuable time that might otherwise be spent making painstaking corrective tweaks. PTC has also introduced support for variable wall thicknesses, allowing users to vary thicknesses, to block off volumes entirely, as well as to explicitly control how fluid will flow through a product.
WIDE BLUE WONDER
» With her maiden voyage now under her belt, Wonder of the Seas is preparing for a busy 2022. At shipyard Chantiers de l’Atlantique, engineers explain how CAD integration with digital twin technology helped to turn this complex design concept into competitive advantage
Wonder of the Seas is exactly as described – an engineering marvel. At 362 metres in length, and weighing in at 236,857 gross tons, the world’s largest passenger ship boasts a cruising speed of 22.5 knots.
The ship was built by Chantiers de l’Atlantique in Saint-Nazaire, France. The company is one of Europe’s most renowned shipyards and the name behind some of the world’s most legendary ships, including the SS Normandie and the Queen Mary 2.
“At our yard, we are aware that we have designed and built one of the most exceptional ships in the history of the cruise market,” says Laurent Castaing, general manager of Chantiers de l’Atlantique. “Wonder of the Seas is a unique synthesis of innovation, state-of-theart technologies and the savoir faire of thousands of engineers and skilled workers.”
The numbers are incredible. Wonder of the Seas’ 18 decks contain 2,865 staterooms, capable of handling up to 6,988 passengers, as well as 2,300 crew. There are 24 elevators, 20 restaurants and 35 bars, not to mention water parks with giant, swirling, deck-to-deck slides, a zipline, theatres, a casino and climbing walls. One of the special features on board is the Central Park, home to over 10,000 real plants.
Construction began in April 2019 and cruise line Royal Caribbean took delivery of the ship in early November 2021. Against a backdrop of pandemic-related delays, the delivery timeline was as impressive as the ship’s size and amenities.
“Harnessing complexity for us is a matter of process,” explains Yves Pelpel, technical director at Chantiers de l’Atlantique. “This is especially true for engineering. We have a robust process that we have developed over a number of years. In terms of competitiveness, the more complexity we have, the happier we are because it will be more difficult for Far East competitors to enter the market.” SMOOTH SAILING
One of the key ways Chantiers de l’Atlantique manages complexity is by using a customised, integrated digital twin built in Intergraph SmartMarine software. The CAD system is directly linked to its SAP enterprise resource planning (ERP) system, which contains the entire structure, its piping, HVAC and cable trays.
“Around that we have different tools connected with that system,” says Pelpel, explaining that this keeps the company one step ahead of its competition, allowing it to undertake pre-outfitting and conduct engineering phases in advance
Immense as the digital twin is, the entire model is updated nightly, so that all stakeholders are working with the correct data and information.
Like most ships from Chantiers de l’Atlantique, Wonder of the Seas contains millions of parts, thousands of components and a huge variety of finished products, ranging from the floors of prefabricated cabins, elevators, engines and HVAC systems, to water slides and swimming pools. All this needs to be designed and integrated in the digital twin before it is integrated into the physical vessel.
During the process, hundreds of designers, engineers, integrators and production specialists work on each project. To manage this complexity, the entire company works on an object-centric process following the bill-ofmaterials (BOM) throughout the workflow
“From the initial design to building the ship, we want to stay object-centric,” explains Sébastien Blanchard, PDM and CAD manager of Chantiers de l’Atlantique. “We have a system with an automatic BOM and we directly go from the 3D model or the 2D model in the CAD system to the ERP every night.
“For one ship, we send nearly 100,000 parts in our BOM from the 3D model to the ERP system every single night. This is the only way that everyone involved can be up-to-date.” Wonder of the Seas is a unique synthesis of innovation, state-ofthe-art technologies and the savior faire of thousands of engineers and skilled workers ’’
Cruise operator Royal Caribbean took delivery of Wonder of the Seas in November 2021
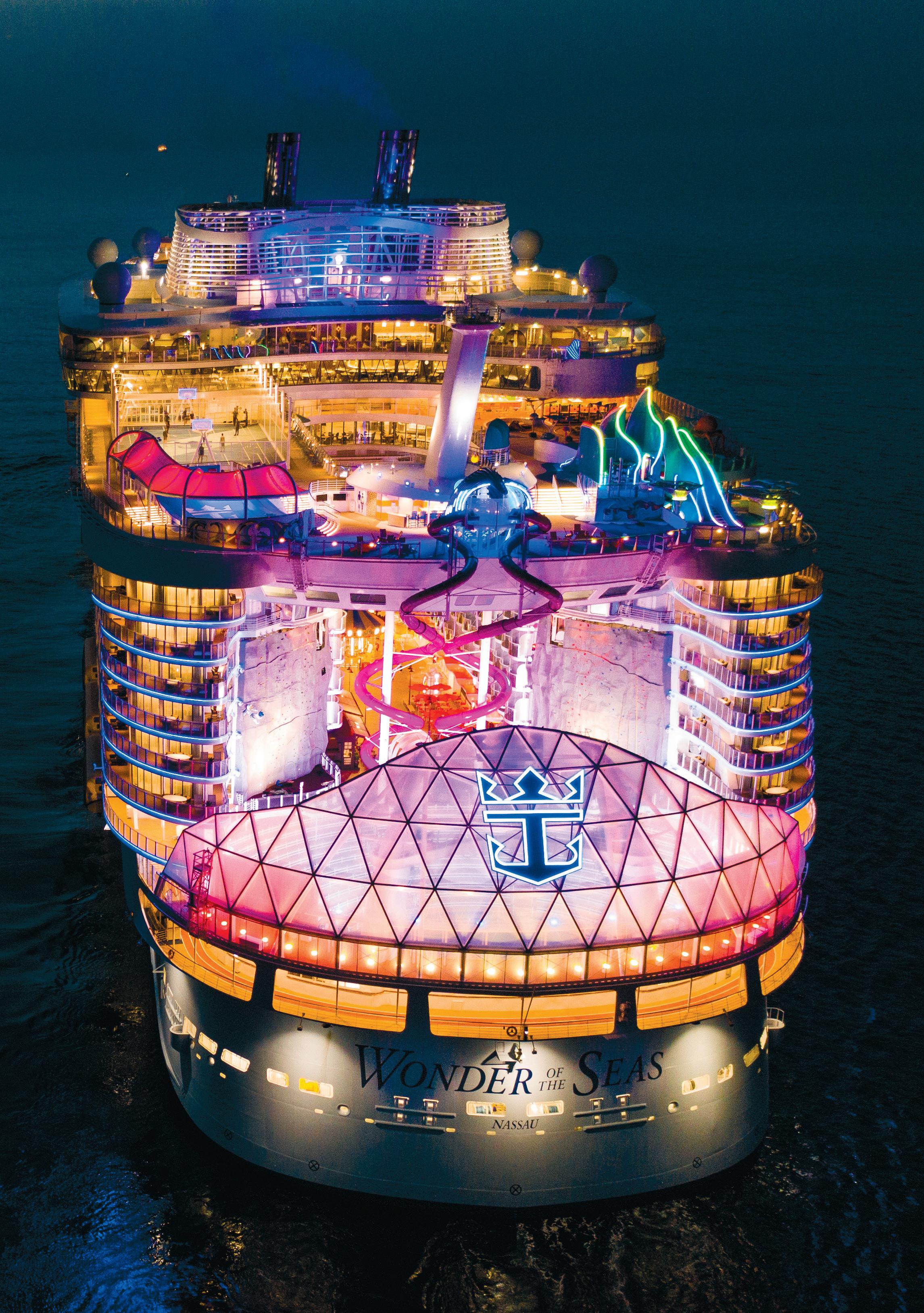
1
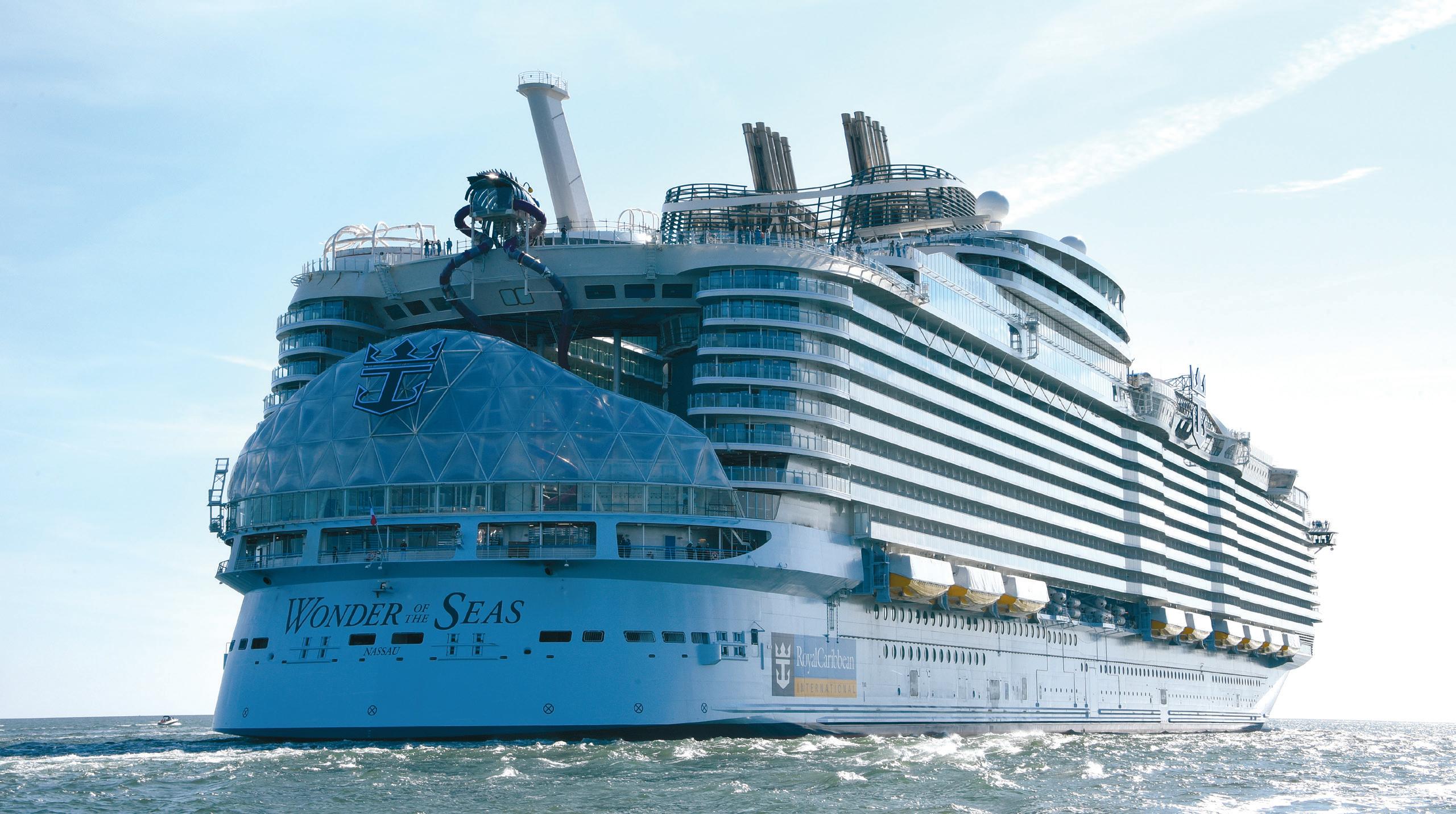
CABIN FEVER
To fit out the thousands of cabins onboard, Solid Edge is used, with each prefabricated layout tailored to the personality of each individual ship. Solid Edge is used to design and verify the initial integration of the cabins into the vessel via the SmartMarine digital twin. This is an important part of the ship’s design and requires many iterations between teams at Chantiers de l’Atlantique, shipowners and third-party architects and designers.
Once a basic layout has been agreed, specialists from the design and engineering teams create each cabin in precise detail, including basic room design, bathroom layout and electrical cabling, as well as design elements such as lighting, bespoke woodwork and unique furnishings. The entire process is completed in Solid Edge, from the first conceptual phase to the second, more detailed design phase.
“Working in Solid Edge lets us go from a general design phase to a much more detailed phase without losing information,” says Gwenael Enet, cabins design department manager, Chantiers de l’Atlantique. “Solid Edge allows us to improve the quality of our cabin design models. We can communicate better – not only with the different designers and architects on the customer side – but also with our suppliers and colleagues in production who have to integrate our cabin designs into SmartMarine.”
Cabins are constructed on a dedicated assembly line in the shipyard, where they construct between 25 and 30 cabins per day. Each prefabricated layout is ready to be placed into the cruise ship under construction, saving time and boosting the overall quality of the integration process.
The advantages of Chantiers de l’Atlantique process, says Gossiaux, is that it enables designers to create concepts while interfacing with other teams and design studios working on concepts for other sections of the ship, while coordinating the entire vessel digitally throughout the company, using the SmartMarine interface.
“You have to remember that our main job is as an integrator,” says Gossiaux. “We have to be able to work together extremely well, so it is not just everyone working on their own in their own camp, so to speak.”
She continues: “The main idea is to utilise both solutions to our advantage and make a little flowchart: what do we do with SmartMarine and what do we do with Solid Edge.”
The process of creating this massive digital infrastructure is still a work-in-process, especially as the teams look to further homogenise the process, adding a more detailed standard catalogue and data structure, even as cruise ships continue to grow in scale and complexity.
And as part of staying at the cutting edge of development, Chantiers de l’Atlantique is adding more environmentally friendly technology to its ships, developing its own fuel cell technology and launching its first vessels with sail propulsion by 2025, helping to bring the wonder of ocean travel to passengers for many years to come.
www.chantiers-atlantique.com ● 1 At 362m in length, and with a cruising speed of 22.5 knots, this ship is a majestic sight to behold ● 2 A digital twin of the ship was built in Intergraph SmartMarine
2
INTEGRATION SKILL
“We handle an enormous number of objects and need a tool that can interface between hundreds of different jobs,” says Marie-Gabrielle Gossiaux, technical manager of hull integration. “So it is extremely important to have a unique digital twin that every person can consult easily based on SmartMarine. On the other hand, Solid Edge helps us develop concepts that are more mechanical, more complex.”
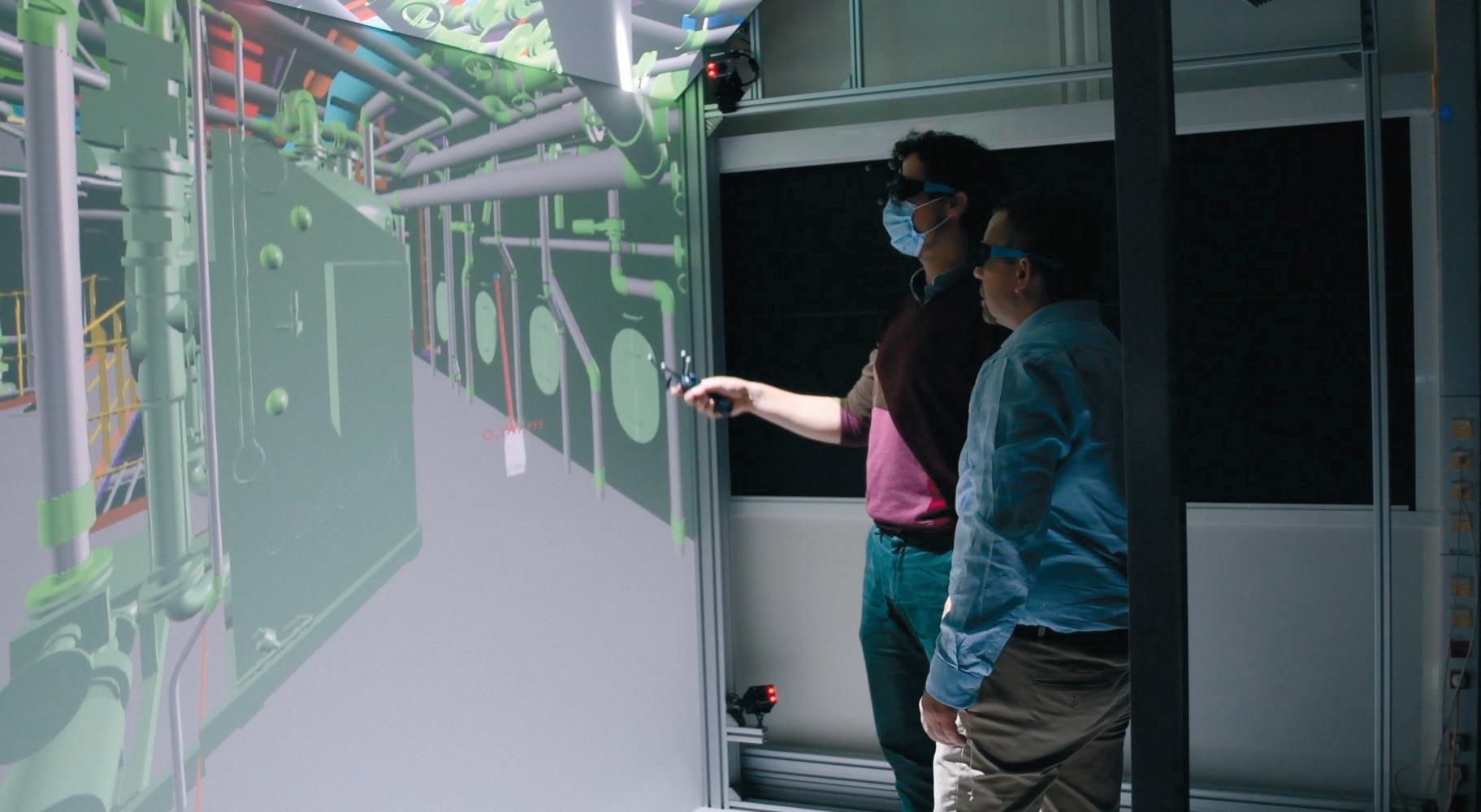
Lenovo ThinkPad P16
The new ThinkPad P16 packs the high-end performance of a 17-inch mobile workstation into a compact 16-inch form factor, powered by new 12th Generation Intel Core HX processors
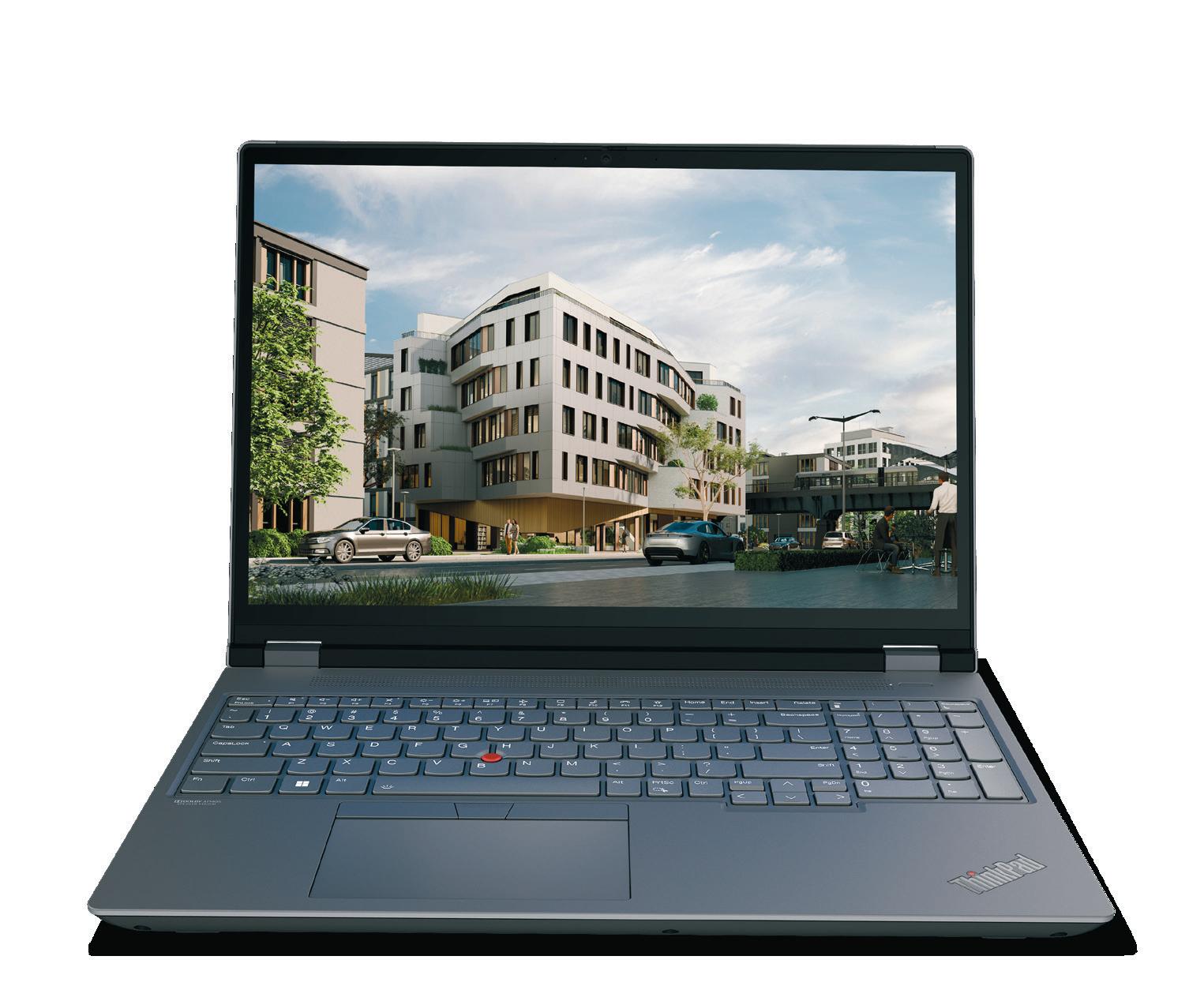
he ThinkPad P16 is one of the most
Tambitious mobile workstations to come out of Lenovo in recent years. It marks the convergence of two different form factors – the 15-inch and 17-inch – into an innovative high performance 16-inch chassis.
But it’s not just its size that’s different. With a brand new industrial design, the ThinkPad P16 brings Lenovo’s legendary mobile workstation family bang up to date with a sleek, modern aesthetic and premium materials, including an anodised aluminium ‘storm grey’ cover. With a 16:10 aspect ratio on the display, which includes a 4K OLED option, and thin bezels on each edge, the chassis is equivalent in size to a more traditional 15.6-inch laptop.
Optimised performance
The high-end mobile workstation is designed for the most demanding professionals, including product designers, architects, engineers, and visualisation specialists.
Performance is up front and centre. Powered by the new 12th Generation Intel Core HX processors, the ThinkPad P16 delivers processing performance that can rival desktop workstations.
With up to eight ‘Performance’ cores and eight ‘Efficient’ cores, for a total of 16 physical cores and 24 threads, the processor excels in both single-threaded workflows, such as CAD and Building Information Modelling (BIM), and multithreaded workflows, such as engineering simulation, ray trace rendering and reality modelling.
In addition, the ThinkPad P16 offers a choice of high-performance professional GPUs up to and including the NVIDIA RTX A5500 (16 GB) for the most demanding real-time visualisation and VR workflows.
Other specs include up to 128 GB of DDR5 memory, up to two high performance NVMe SSDs and the very latest in wireless connectivity including Intel WiFi 6E AX211 and 4G.
Cool operator
Despite offering similar core specifications, not all mobile workstations are the same. Due to cooling constraints, processors can be fed different levels of power and can sometimes be ‘throttled’ to stop them getting too hot. This is not the case with the ThinkPad P16.
Thanks to its innovative dual vapour chamber, the powerful mobile workstation excels in its thermal design, delivering exceptional performance while running cool under heavy loads.
Learn how the ThinkPad P16 was designed tinyurl.com/P16-D3D
ThinkPad P16 - tech highlights
With a brand new industrial design, the ThinkPad P16 delivers exceptional performance in a stylish, strong and durable 16-inch form factor
16-inch pro display
With a 16:10 aspect ratio, the 16-inch display has 11% more pixels and a significantly greater viewable working space. It also creates a ‘deeper’ system which allows for thinner bezels and an improved screen-to-body ratio.
Resolutions go up to WQUXGA (3,840 x 2,400). There are IPS or OLED options for exceptional colour saturation and dark blacks, up to 600-nit peak brightness, 100% Adobe RGB colour gamut, X-Rite colour calibration, and low-blue light for reduced eye strain
ThinkPad keyboard
The ThinkPad keyboard has been enhanced with a ‘soft landing’ design that provides more shock absorption for smoother and more responsive typing. The keyboard is backlit, spill resistant and also aids cooling, by drawing in air between the keys to increase air flow through the fans
FHD camera
The FHD (1,920 x 1,080) camera delivers a higher resolution for better video conferencing and comes with hardware noise reduction. There’s also a ThinkPad Webcam Privacy Shutter and an IR option for Windows Hello support
KEYSHOT SCREEN IMAGE COURTESY OF LUXION / SERGIO LOZA
Touchpad & TrackPoint
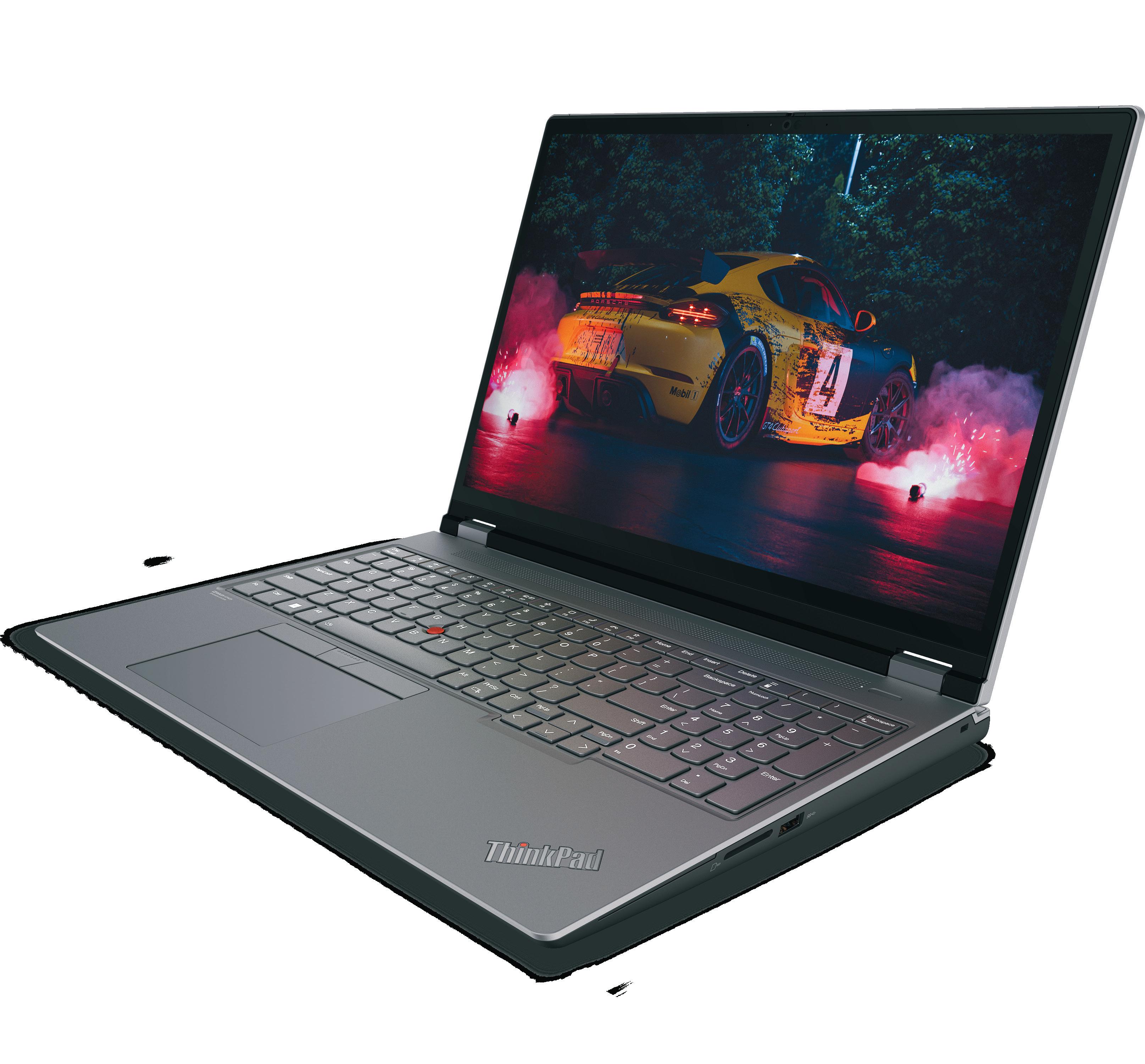
For improved control, the 115mm wide touchpad is 15% wider than before, while a new ‘glass like’ mylar surface decreases friction for a more premium experience. The TrackPoint cap has also been improved to deliver ‘more certain and precise movement’ and decrease wear
Strength and style
The palm rest is crafted from ABS plastic and polycarbonate. To echo the aesthetic of the anodised aluminium ‘A Cover’, it is coated with advanced anti fingerprint paint. Meanwhile, a solid magnesium sub frame or ‘roll cage’ gives the laptop its renowned ThinkPad strength and rigidity
Power and security
The power button features an integrated on chip fingerprint reader for enhanced security and a cleaner, less cluttered design. Engineering simulation was used to optimise the shape and spring force of the button
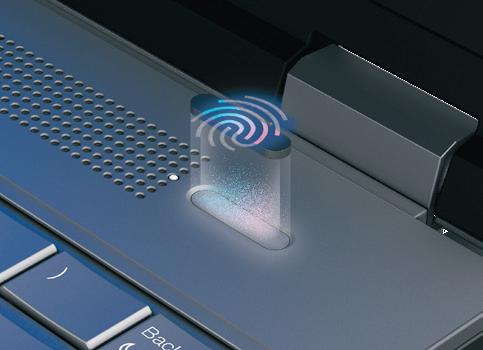
Antenna performance
The ThinkPad P16 comes with a range of options for wireless connectivity, including Intel WiFi 6E AX211 and 4G. To optimise the performance of the antennas, a window is cut out of the anodised aluminium ‘A Cover’
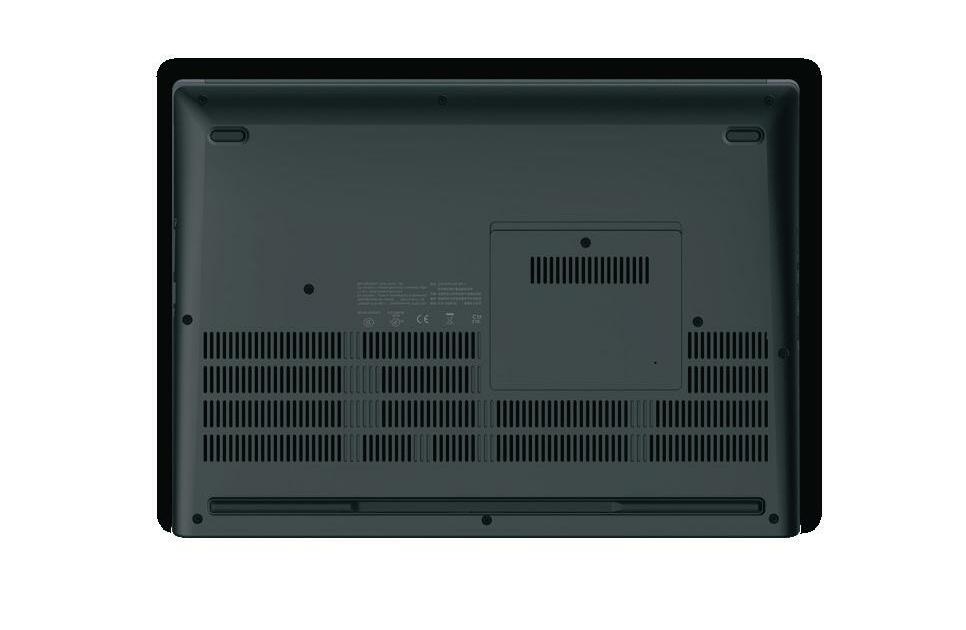
Serviceability
To minimise downtime in the rare event of a failure, or to extend product life through easy upgrades, the ThinkPad P16 was built with serviceability in mind. A service hatch with a single screw gives easy access to one of two NVMe drives and two (out of four) memory slots, while the second NVMe drive, Wi-Fi and 4G modules can be accessed by opening the entire bottom cover
Premium frame
For strength and rigidity the ‘A Cover’ features a magnesium subframe, finished in anodised aluminium for a premium look and feel, with a ‘storm grey’ finish
Tough cookie
To help ensure long term durability, the ThinkPad P16 goes through a rigorous process of in-house ‘torture tests’, including thousands of open-close cycles for the zinc alloy hinges. To demonstrate its toughness, the ThinkPad P16 is also put through the US Department of Defense’s MIL-STD 810G standards, which include tests for mechanical shock, humidity, cold, heat, sand & dust, vibration and more
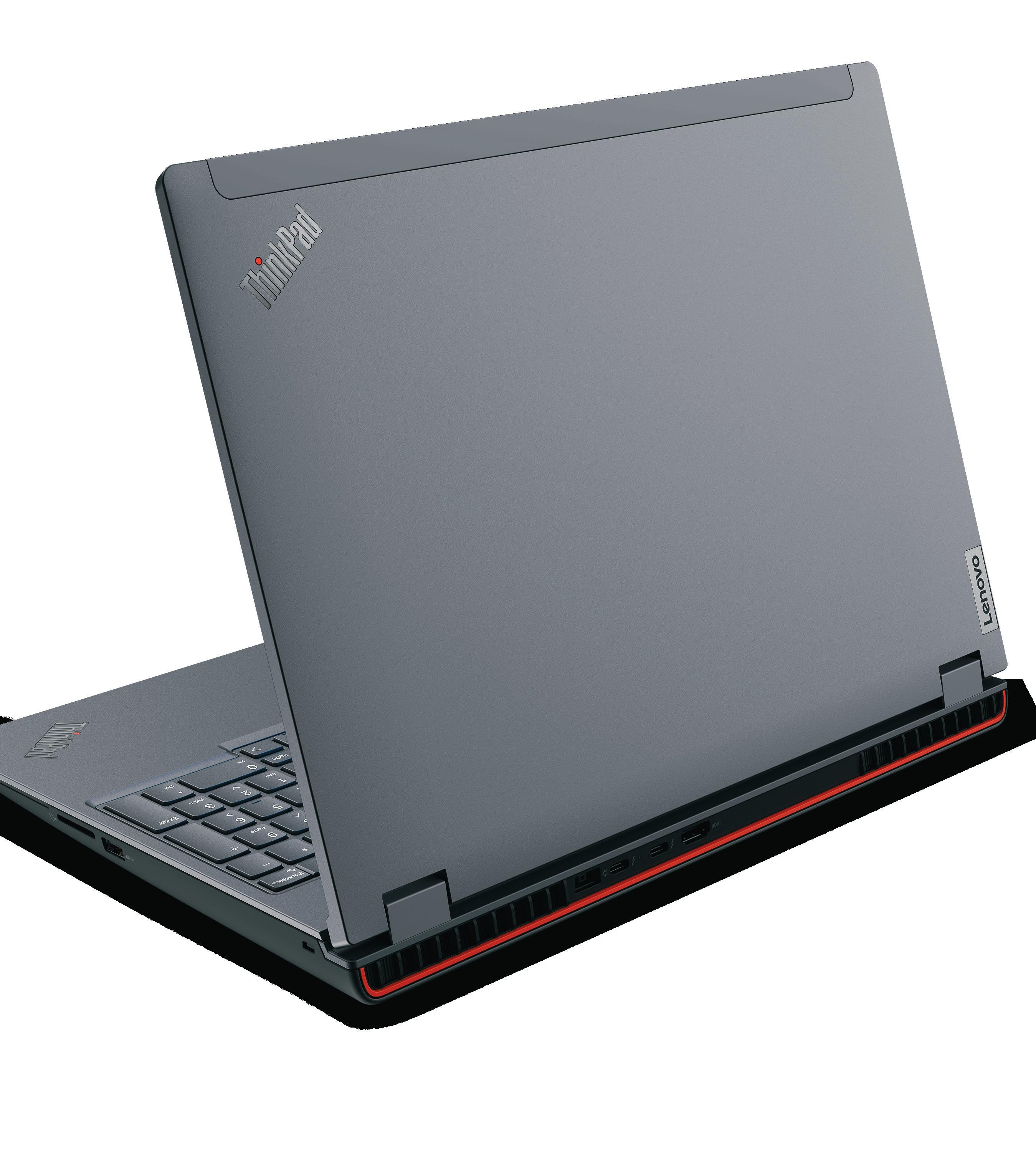
Thermal exhaust
The ThinkPad P16 features an advanced thermal design to keep the system running fast and cool. Cool air is drawn in from the bottom and through the keyboard, then expelled at the rear, rather than the side, so it does not heat up the user’s hands
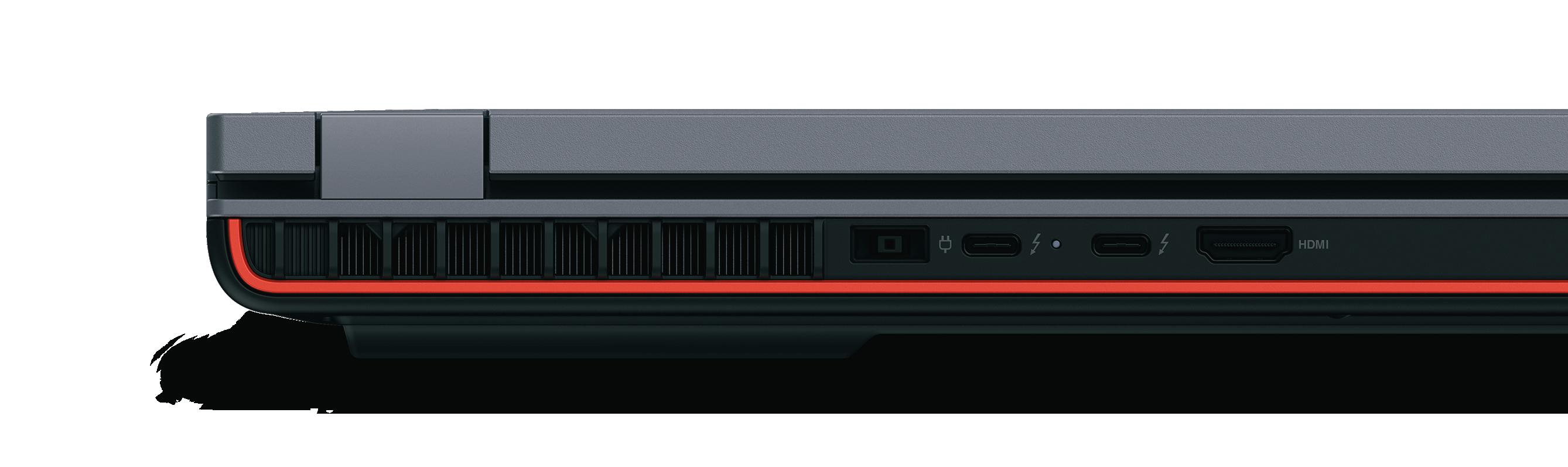
Rear connectivity
Many of the ThinkPad P16’s ports, including HDMi, power and Intel Thunderbolt 4, are located to the rear of the machine for a clutter free desk
Sustainability
The ThinkPad P16 follows Lenovo’s commitment to environmental sustainability, utilising 30% postconsumer recycled plastic material (PCC) in the speaker enclosure and 97% PCC in the batter pack frame and FSC certified materials used in the carton and accessory box. Lenovo has also launched a CO2 Carbon Offset Service based on ‘realistic’ five year product emissions covering production, shipment and typical usage
Game changing performance
With a new hybrid architecture, the Intel ‘Alder Lake’ HX series of mobile processors, at the heart of the ThinkPad P16, give a phenomenal performance uplift in multi-threaded workflows like ray trace rendering
ew 12th Generation Intel Core
Nprocessors are different to all previous Intel processors. They are the first to feature a hybrid architecture with two different types of cores: Performance (P) cores for primary tasks and Efficient (E) cores, which are heavily focused on maximising performance per watt. Intel calls this its biggest architectural shift in a decade.
The idea behind Intel’s hybrid architecture is that critical software, including your current active application, runs on the P-cores, while tasks that are not so urgent run on the E-cores. This could be background operations such as Windows updates, anti-virus scans, or hidden tabs on a web browser. No processing power is ever wasted. If the software is highly multi threaded then it will run on both sets of cores.
P-cores are not only faster than E-cores, but they also support hyperthreading, Intel’s virtual core technology. This means every P-core can run two threads at the same time, which can help boost performance in certain multi-threaded workflows, such as ray trace rendering.
12th Gen Intel Core HX
The Lenovo ThinkPad P16 features 12th Generation Intel Core HX processors. Specifically designed for high-end laptops and mobile workstations, they offer more cores than the 12th Generation Intel Core H processors, found in the super slim Lenovo ThinkPad P1 Gen 5.
With 8 P-cores and 8 E-cores, for a total of 16 physical cores and 24 threads, 12th Generation Intel Core HX processors are designed to take performance to new levels.
They offer a significant performance uplift compared to 11th Generation Intel Core processors, which maxed out at 8 cores and 16 threads.
The performance benefits are likely to be felt most strongly in highly multithreaded workflows such as ray trace rendering. Here, applications such as Luxion KeyShot and Chaos V-Ray should be able to harness the full processing capabilities of both sets of cores.
That’s not to say 12th Gen Intel Core HX processors won’t deliver improvements in single threaded workflows. With a higher Instruction Per Clock (IPC) than 11th Gen Intel Core processors, the ThinkPad P16 should also deliver a significant uplift in Computer Aided Design (CAD) and Building Information Modelling (BIM) software, in applications including Solidworks, Inventor, AutoCAD and Revit.
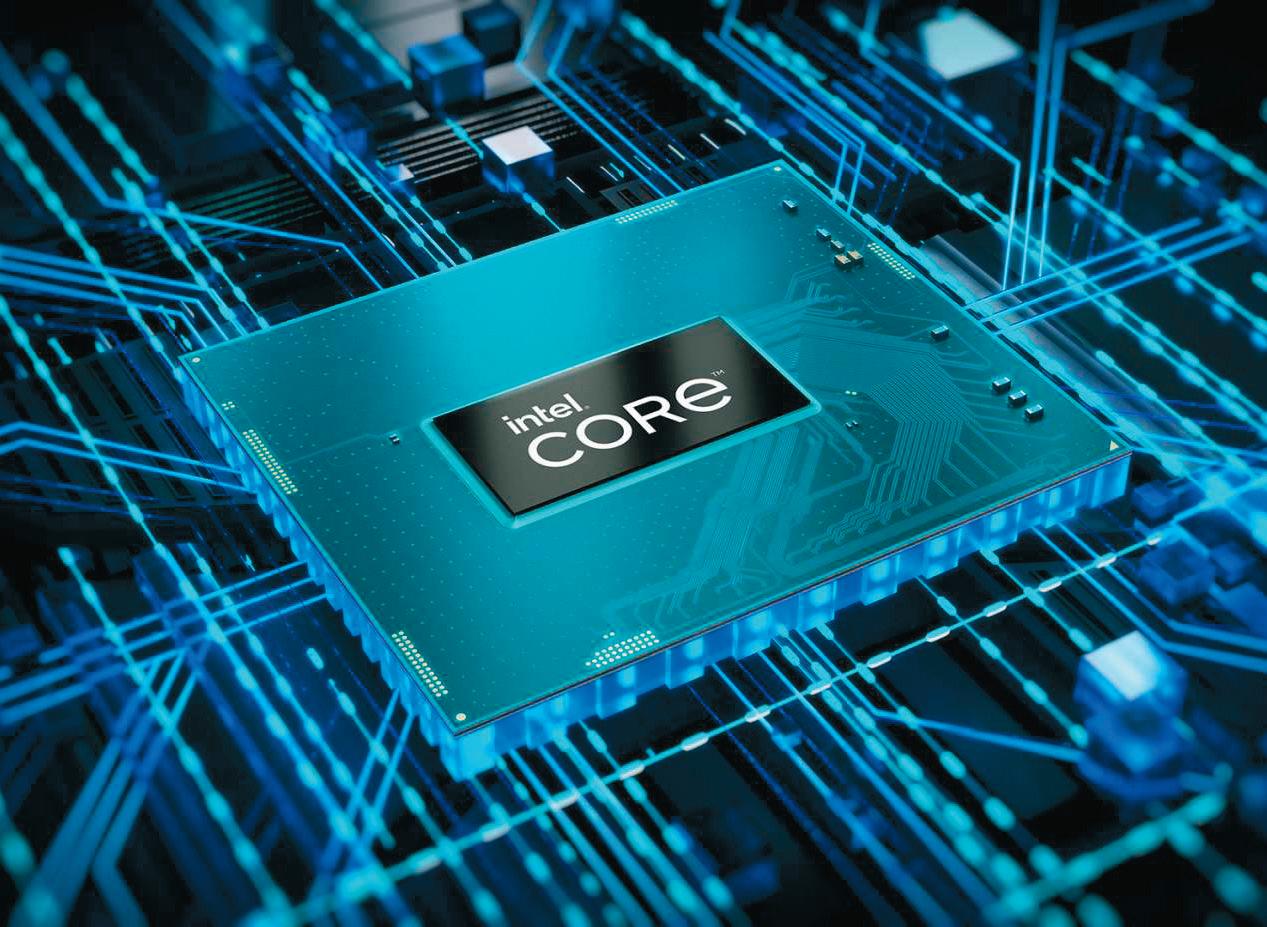
Optimised cooling, optimised performance
The Lenovo ThinkPad P16 features an advanced thermal design to help it run cool and quiet and maintain exceptionally high levels of performance over extended periods.
The system is built around a dual vapour chamber cooling solution that balances the thermal load between the CPU and GPU. So, if you have a workflow that stresses the CPU, such as ray trace rendering, but hardly uses the GPU, the system can automatically borrow some of the GPU’s thermal budget so more power can be delivered to the CPU.
In the ThinkPad P16, each processor has its own fan and vapour chamber, which are connected to one another by a copper plate and a shared heat pipe. This effectively creates one very large cooling assembly which can spread heat very quickly.
According to Lenovo, using this vapour chamber design can increase the total Thermal Design Power (TDP) capability of the system by 10W to 20W, leading to a 6% to 12% improvement in thermal performance.
In other words, it can pump more power into the CPU and GPU as and when required, to increase frequencies for faster processing.
In fact, it can deliver up to 55 watts to the Intel Core HX processor and up to 125 watts to the GPU, the kind of power traditionally associated with a larger 17-inch mobile workstation and way above that of a typical 15-inch mobile workstation.