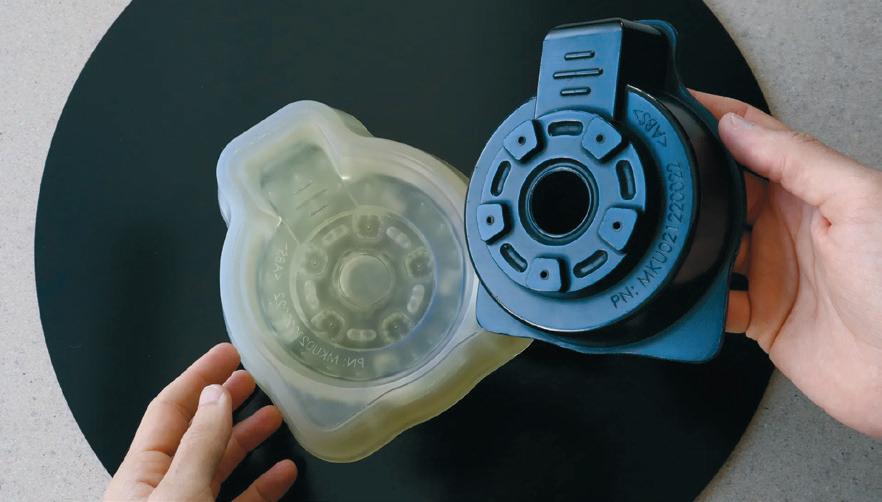
5 minute read
materials
of product-design data — demonstrated at launch using Adobe’s Substance 3D tools — to create brand-accurate, photoreal ‘digital twins’ of client products.
Using text prompts, the models can then be placed in surroundings or have text placed around them using tools like Adobe Firefly generative AI models and what WPP says is exclusive visual content from Getty Images created using Nvidia Picasso, a custom generative AI software.
“This new technology will transform the way that brands create content for commercial use, and cements WPP’s position as the industry leader in the creative application of AI for the world’s top brands,” said WPP CEO Mark Read.
The new content engine will be made available soon exclusively to WPP’s clients around the world. www.wpp.com | www.nvidia.com
for the Mayku Multiplier
Mayku has announced the launch of three engineering materials for the Mayku Multiplier: ABS, PMMA and UHMW. The manufacturer of desktop vacuum formers explained that, traditionally, working with these materials has involved complex and costly processes or limited moulding methods.
However, by seamlessly integrating ABS, PMMA, and UHMW into the Multiplier workflow, users can now capitalise on their properties, such as heat resistance, transparency and friction reduction.
Acrylonitrile Butadiene Styrene (ABS), is a widely used thermoplastic polymer in the manufacturing industry. Polymethyl methacrylate (PMMA) is a transparent thermoplastic commonly referred to as acrylic. Ultra-high-molecular-weight
Round Up
Vrgineers and ManoMotion have announced they are introducing an AI hand-tracking algorithm exclusive to XTAL Mixed Reality headsets, which was developed to enhance the immersive experience of pilot training in virtual and mixed reality environments www.vrgineers.com
Formlabs has announced the release of a new Flame Retardant (FR) Resin, the company’s first selfextinguishing material as well as its first UL 94 V-0 certified resin, for creating stiff, creep-resistant and functional plastic parts that perform well in hightemperature environments www.formlabs.com
With a new integration between Materialise Magics and CO-AM, users can benefit from enhanced traceability in the 3D printing process, thanks to a revision tree that logs every action that is performed on a part or build, including tracking which user carried out a particular action www.materialise.com
Based on Massivit's Cast In Motion technology, the company's new 10000-G machine should facilitate the digital production of complex moulds, mandrels, master tools, jigs and fixtures for a range of industries including automotive, rail, marine and defence www.massivit3d.com polyethylene (UHMW) is a thermoplastic renowned for its exceptional strength, durability and wear resistance. www.mayku.me
Integrating these engineering materials into the Mayku Multiplier workflow should be seamless, said the company, thanks to the thorough testing already conducted.
ABS offers high levels of resistance to impact, heat and chemicals
Coloro and KeyShot have said they will integrate a library of 3,500 standard Coloro colours with the KeyShot platform, in order to enable product designers to accurately visualise colours on 3D models and facilitate precise colour specifications with production suppliers www.keyshot.com
What’s happening in the world of simulation? In short: nothing much, but it’s been a long time coming.
I’ve been in the simulation business for a while, since the 1980s in fact. That’s the best part of 40 years, during which I’ve generally worked in the mid-market sector. There isn’t really a low end for simulation, and I’ve never been a part of the big industrial aero and auto worlds.
From this, you can neatly divide my career into two halves. During the first half, I spent all my time having to explain to people that they couldn’t have what they wanted, and certainly not at a price point that made any sense to them.
And what did they want? They wanted CFD of rotating components, integrated vibration and durability workflows, fluid structural interaction, rapid analysis of bolted connections, achievable optimisation technologies, models which considered the structure of the material in the overall representation of the part — I could go on.
But these things just weren’t possible, not unless people were tackling truly high-end problems and were equipped with high-end budgets to match.
Yet oddly, the second half of my career has been spent trying to get these same people to invest in these same simulation technologies — only now, those technologies are far more usable and affordable. They’re within reach.
You might imagine that, as a result, there should have been some golden era of simulation technology adoption, when people could suddenly have what they wanted and were prepared to pay for it. If there was, I don’t remember it.
There’s no better demonstration of where we are today than the abundance of pointless simulations that are regularly shown off across the internet. These, and the promotion of ‘new’ workflows that would actually seem to hail from the 1990s. They are the equivalent of people who’ve just discovered ‘exciting new bands’ like Oasis and Blur. The world needs a lot of things, but fluid–structure interaction (FSI) simulations of cows falling over simply aren’t on the list.
REAL WORK, VALID USE CASES
What all this shows is that we’ve now got technology in abundance. It’s usable and it’s available at a price point where it is prone to waste (in other words, it doesn’t take a lot of costly compute power in relative terms).
But at the same time, it isn’t being used much for real work, because if it was, people would be busy actually selling, supporting and using it in proper, real-life industrial cases.
There would be no time for worthless bovine digital twins and nor should there be, in my opinion. Today, it’s arguable that for a lot of simulation work, cost isn’t a factor at all. I’ve got perfectly usable FEA and CFD systems that I downloaded cheaply from the internet. I’ve even got a pretty serious smoothedparticle hydrodynamics code that was a free download.
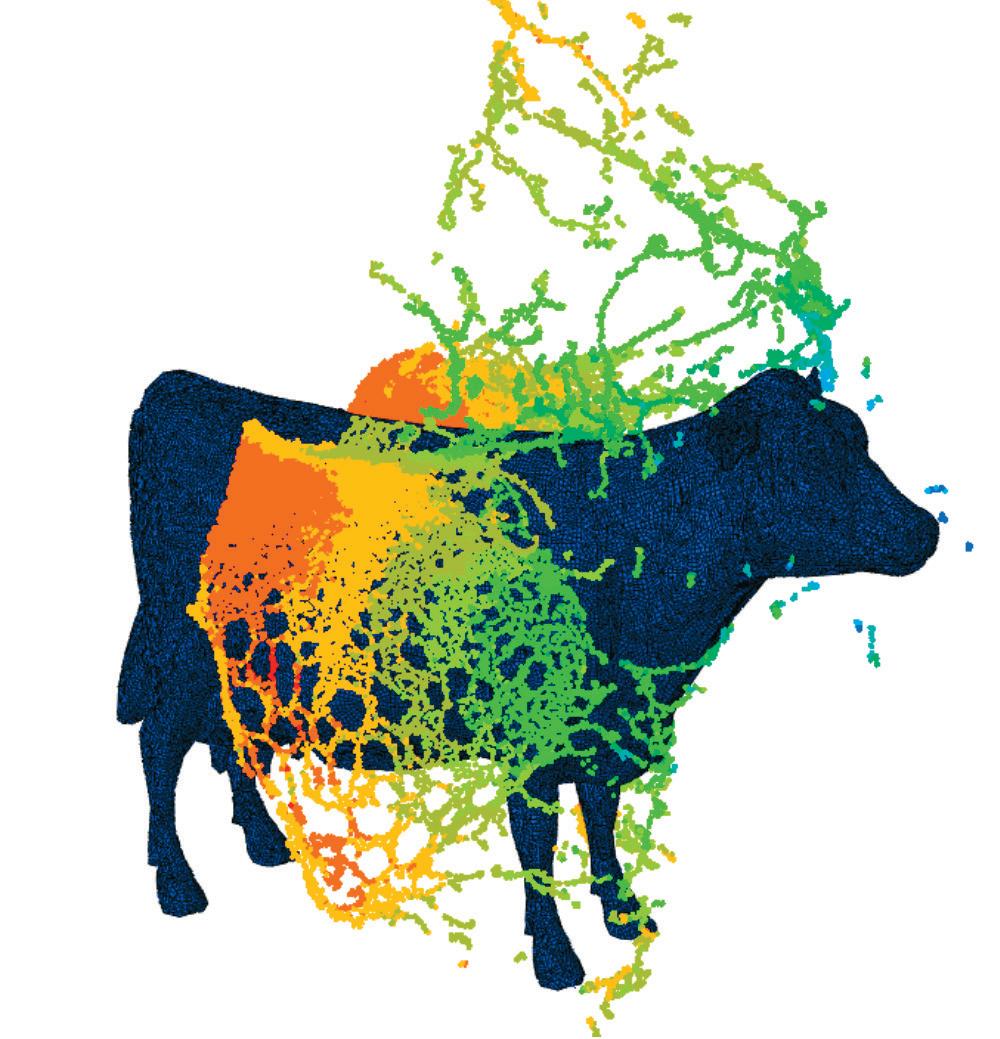
There are also systems out there like Altair OpenRadioss, a publicly available, open-source code base for non-linear problems, which is being worked on by a global community of researchers and developers. While I can say that I’m pleased I have this, I still can’t work out quite why they built it.
Twelve-core workstations and a decent GPU are achievable for many, allowing most tasks to be tackled in-house, and doing a respectable job of crunching the numbers without much of this having to head off into the cloud.
With Python now around, capable of stringing everything together into usable workflows, you’d expect every technical operation worth its name to be running extensive simulations wall-to-wall, night and day, chasing an ever-deeper understanding of the fundamental processes of their product’s make-up and function.

However, all the available evidence tells me that this isn’t happening.
LACK OF VISION?
I wish I knew why. For a long time, I ran a fantastic team of simulation engineers with extensive skills in composites, fracture and damage, FSI, biomechanics, CFD, production processes and much more. And what did they spend most of their time modelling? Machined, bolted and welded structures, mainly made of steel.
It strikes me that what we are up against here is not a failure of simulation itself, but more a lack of vision across the board when it comes to applying simulation to engineering challenges.
So now it must be, as it possibly always was, about the people. As I’ve made clear, the technology is out there, literally for the taking.
We need to lose the trivial stuff, to focus on real engineering simulations that will improve products, our understanding of how they work and of how they might be made better. Because if we don’t, nobody will – and that’s a scenario almost as depressing as those FSI cows.
ABOUT THE AUTHOR: Laurence Marks has spent more than three decades working with simulation technologies and is currently a visiting research fellow at Oxford Brookes University working on projects that combine two of his passions: life sciences and motorsports
Creo 10 includes numerous enhancements to help you deliver your best designs in less time, with new tools for designing with composites, additive, and subtractive manufacturing. There are also improvements in electrification and ergonomics. Creo also continues to add simulation-driven design capabilities. Creo 10 provides an on-premises solution, while Creo+ delivers a SaaS solution, with cloud-enabled collaboration and license management tools. To learn more about Creo 10 to go www.ptc.com/creo https://www.ptc.com/hill-helicopters ptc.com
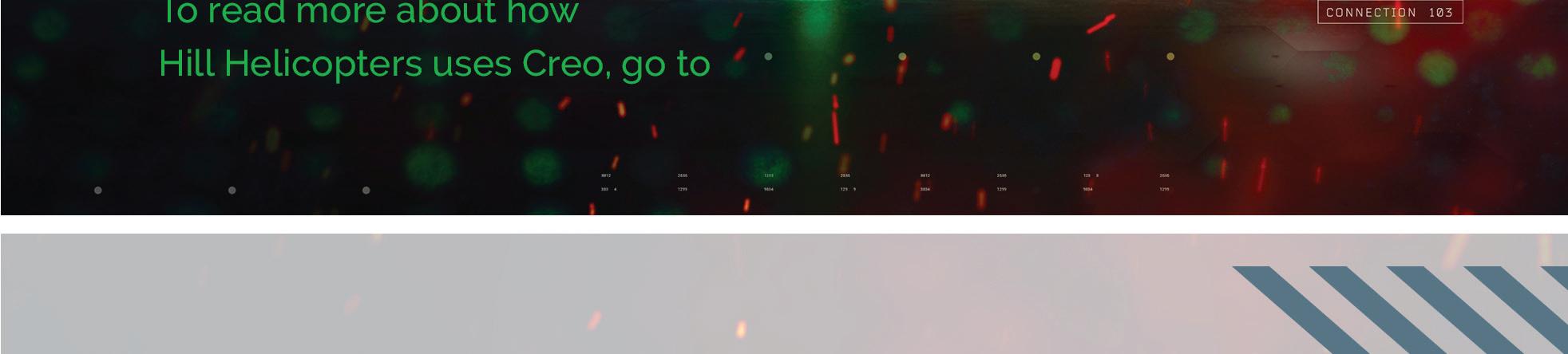

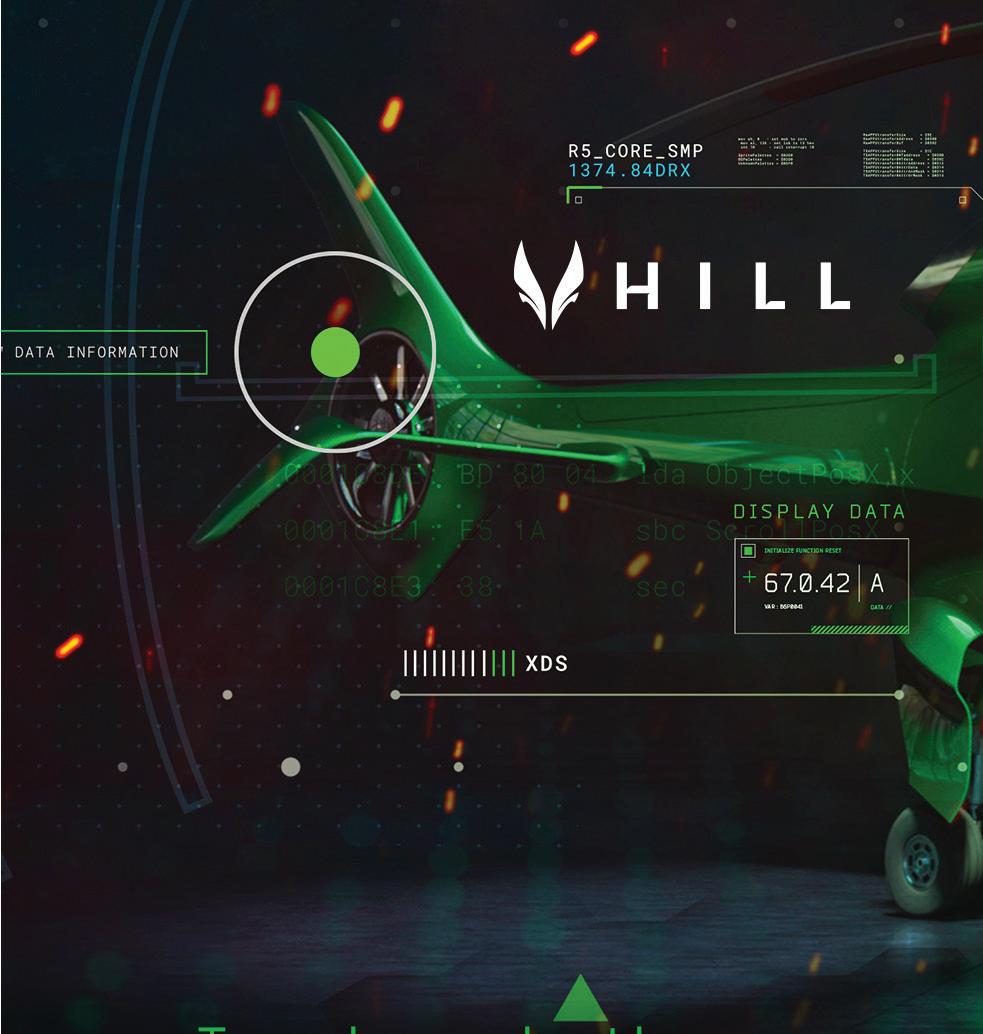


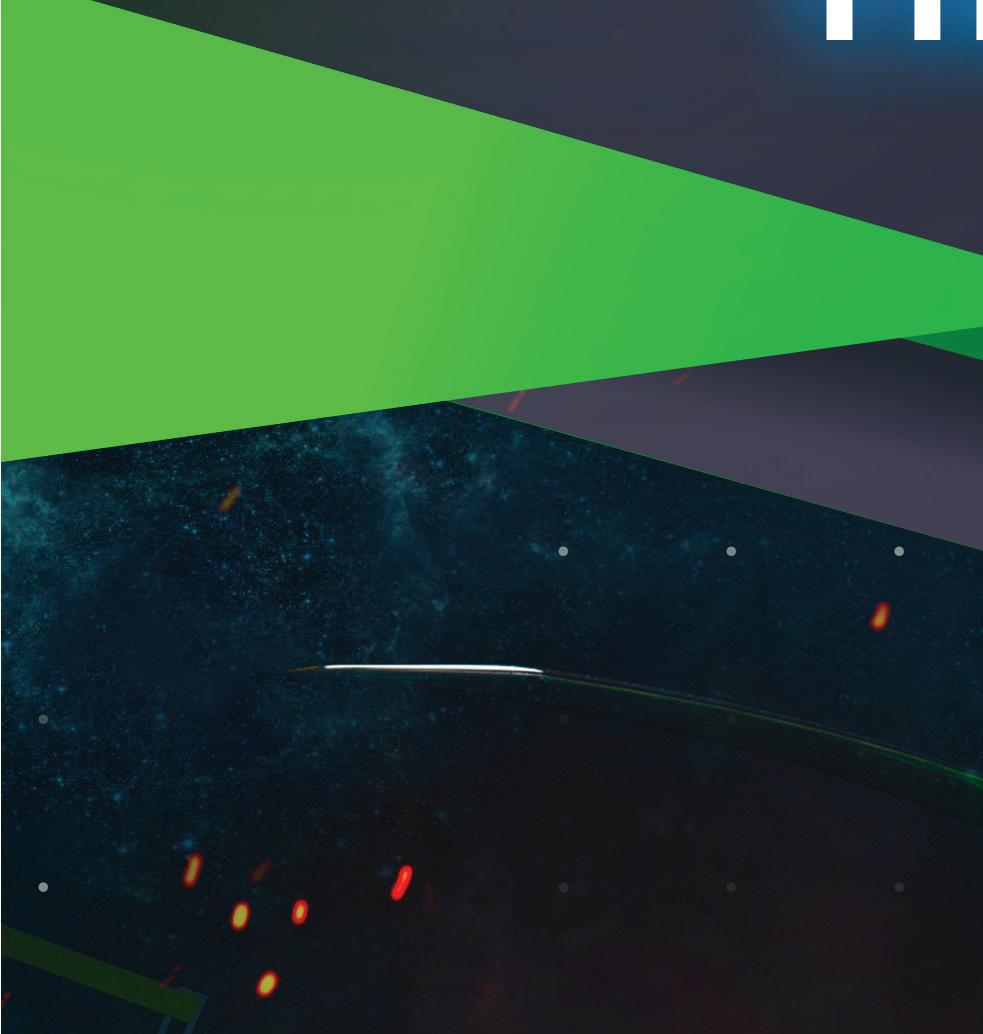
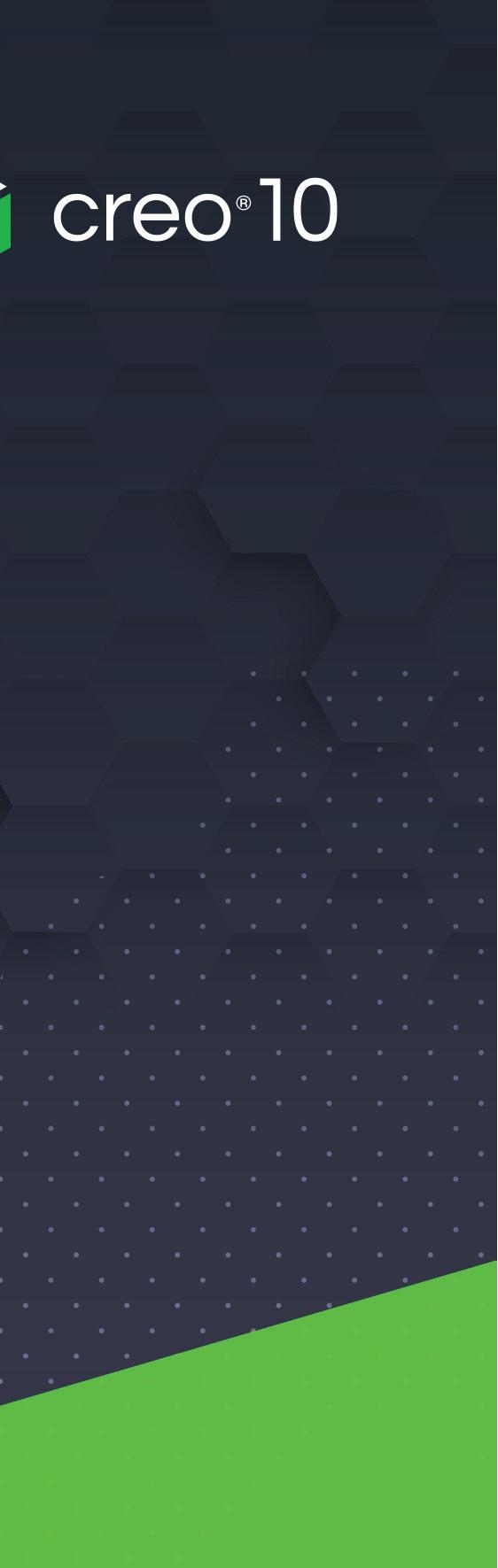
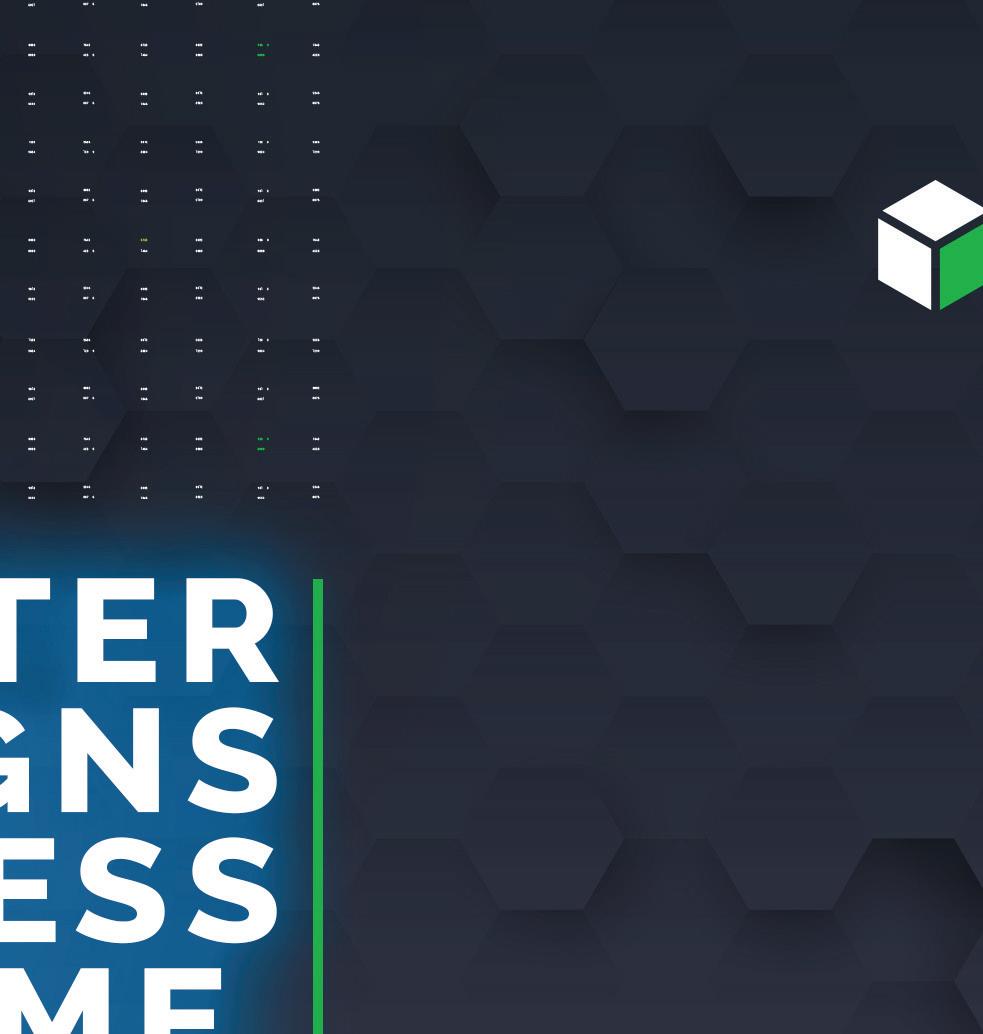
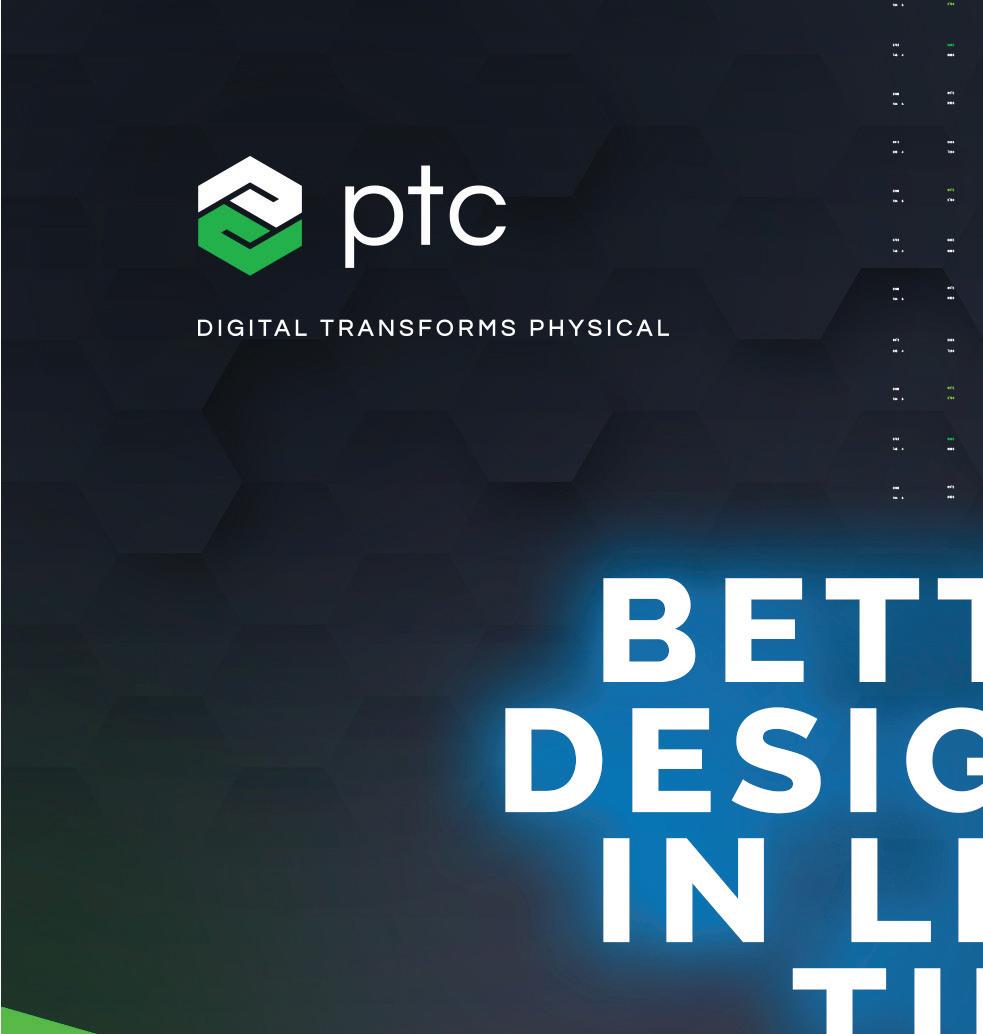