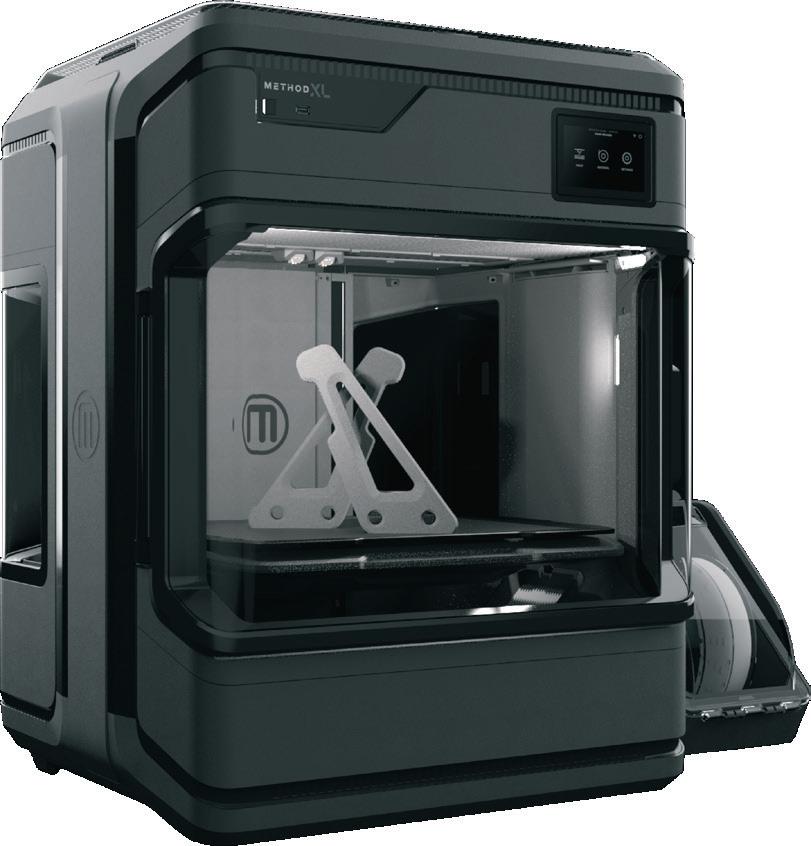
3 minute read
INTRODUCING ULTIMAKER’S METHOD XL –For Large Production Parts Straight From your Desk
UltiMaker’s latest breakthrough in the world of 3D printing –the Method XL – allows users to 3D print large production parts right from their desktops, using manufacturing-grade ABS.
“We saw that there was a lack of production-level industrial capabilities in more accessible and easy-to-use 3D printers,” stated CEO Nadav Goshen when asked about the strategy behind UltiMaker’s launch. “With Method XL, we believe we are bringing customers the best 3D printing solution in the market for engineering applications.”
With An Emphasis On Production
The Method XL launch is part of UltiMaker’s mission to accelerate the adoption of 3D printing for true manufacturing applications. To do this, the XL boasts an expansive build volume of 305 mm x 305 mm x 320 mm. The system also includes a temperature-controlled heated build chamber and a heated build plate which, alongside a water-soluble support material, enable precise and durable parts in a range of industrial-grade materials including injection molding plastics like ABS. All with the affordability of a desktop system.
Since UltiMaker’s merger with MakerBot last year, Method XL is the second product launched under the newly formed brand, following the UltiMaker S7 introduction in January. The transformation of its brand has reaffirmed the company’s commitment to manufacturing and product development, with a powerful and comprehensive professional offering. The Method series will particularly focus on specific manufacturing applications which benefit from the heated build chamber, specialty thermoplastics materials, and high levels of dimensional accuracy.
Redefining The Accessibility Of Production
Method XL can print production plastics at a fraction of the cost of the incumbent industrial machines used today, with the ease-of-use of a desktop system. Synching directly with CloudPrint, a seamless CAD file-to-printed part workflow is enabled. This allows customers to easily upload, monitor, and track print jobs directly on their web browser, streamlining 3D printing journeys and improving efficiency. As a result, Method XL is poised to transform manufacturing with 3D printing and better serve professionals across sectors.
“Method XL is a game-changer in terms of making manufacturing accessible to all kinds of people, businesses and industries,” Goshen commented.
“It allows engineers and designers to bring their ideas to life right from their desktops with a simple workflow and high-quality, long-lasting parts. It’s an important step forward in democratizing the production process.”
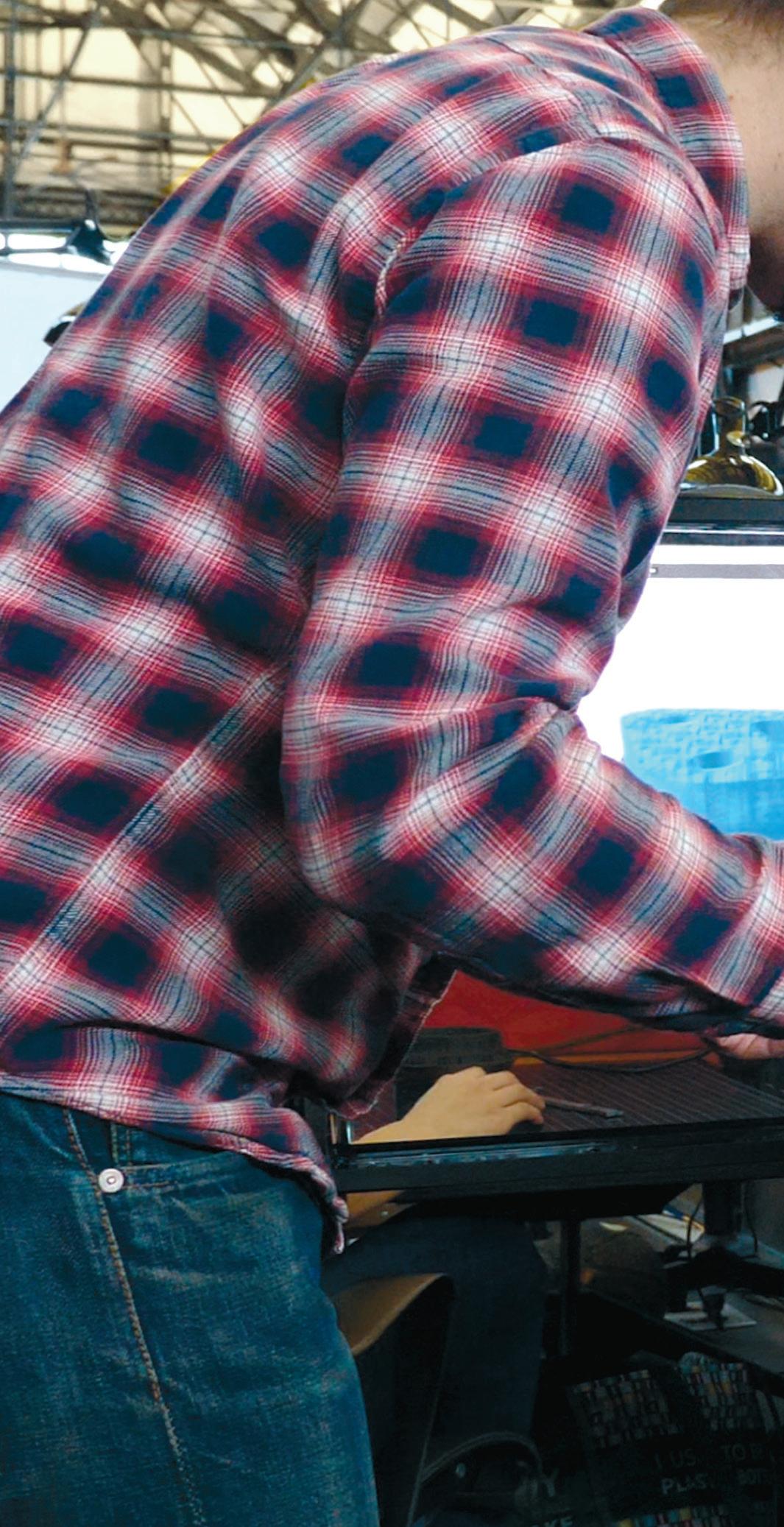
Method XL also comes equipped with a HEPA filter and an activated carbon filter for safer 3D printing indoors.
Precision And Durability
The heated build plate featured in the Method XL is a new addition to the Method Series. It enables more precise and durable parts by maintaining a stable environment during the printing phase, resulting in an avoidance of warping or layer adhesion issues and a seamless printing experience for customers.
To further ensure accurate printing of strong parts of any size accommodated by the Method XL, UltiMaker has designed the heated building plate to work in tandem with a temperature-controlled heated build chamber. This ensures temperatures remain constant throughout the production environment, parts aren’t subjected to fluctuations, and consistently and reliably meet a dimensional accuracy of ± 0.2 mm .
INDUSTRIAL-GRADE MATERIALS UNLOCK NEW POTENTIAL
Not only is the Method XL specifically engineered to create large, complex, and durable parts, but it also offers professional printing applications using industrial-grade materials like ABS-R and ABS Carbon Fiber materials. Throughout the entire design and engineering process of the Method XL, a key objective for UltiMaker was to ensure optimal results when printing with ABS. ABS is one of the most popular materials to 3D print with on a professional scale yet poses a challenge for successful desktop 3D printing due to its tendency to warp and deform. However, the innovative heated chamber of the Method XL can reach up to 100°C and prevents warping and deforming, accomplishing spectacular 3D printing results.
Combined with RapidRinse, a fastdissolving, water-soluble support material, Method XL makes ABS parts with a more refined surface finish and enables one of the fastest support removal for complex FDM parts, as the support material simply dissolves away. Method XL also offers an external moisture-controlled material case, ensuring peak performance from professional-grade materials.
UltiMaker ensures customers have access to the optimal materials whatever the application. Customer choice is expanded through UltiMaker’s open materials platform and the LABS Experimental Extruder. Four of the most popular materials available through the LABS program include Jabil SEBS, a soft material with flexible, rubber-like properties; Polymaker PolyMax™ PC, a polycarbonate material that combines strength, toughness and heat resistance, and LEHVOSS PAHT 9891, a carbon fiber-enforced nylon able to withstand high temperatures.
An Attractive Price Point
With a choice of industrial-grade materials now available on a desktop 3D printer, UltiMaker offers a pragmatic alternative to the expensive industrial systems such materials were previously exclusive to.
In fact, a large attraction of the Method XL for many is the price point – it is currently the only 3D printer in its price bracket with a heated chamber and heated build plate, and consequently offering large, accurate parts with injection molding plastics like ABS.
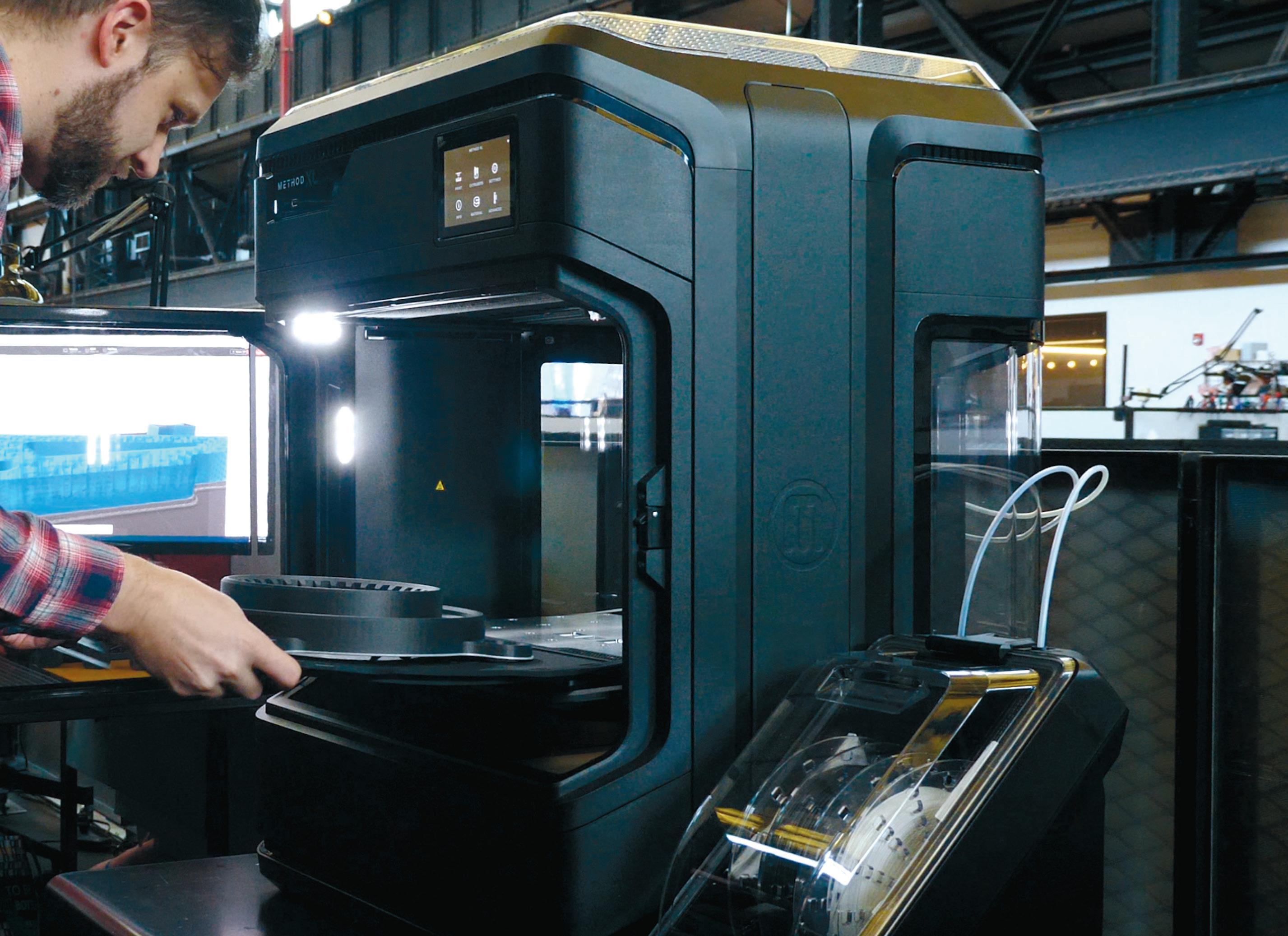
Goshen believes that Method XL will deliver game-changing economics and productivity to many customers: “With the ability to print large form parts on an accessible platform, Method XL will enable customers to scale up their 3D printing output efficiently and effectively. The addition of Method XL to UltiMaker’s portfolio catapults the company ahead in its pursuit of building the world’s leading 3D printing ecosystem and shaping the future of manufacturing.”
1 ± 0.2 mm or ± 0.002 mm per mm of travel (whichever is greater). Based on internal testing of selected geometries.