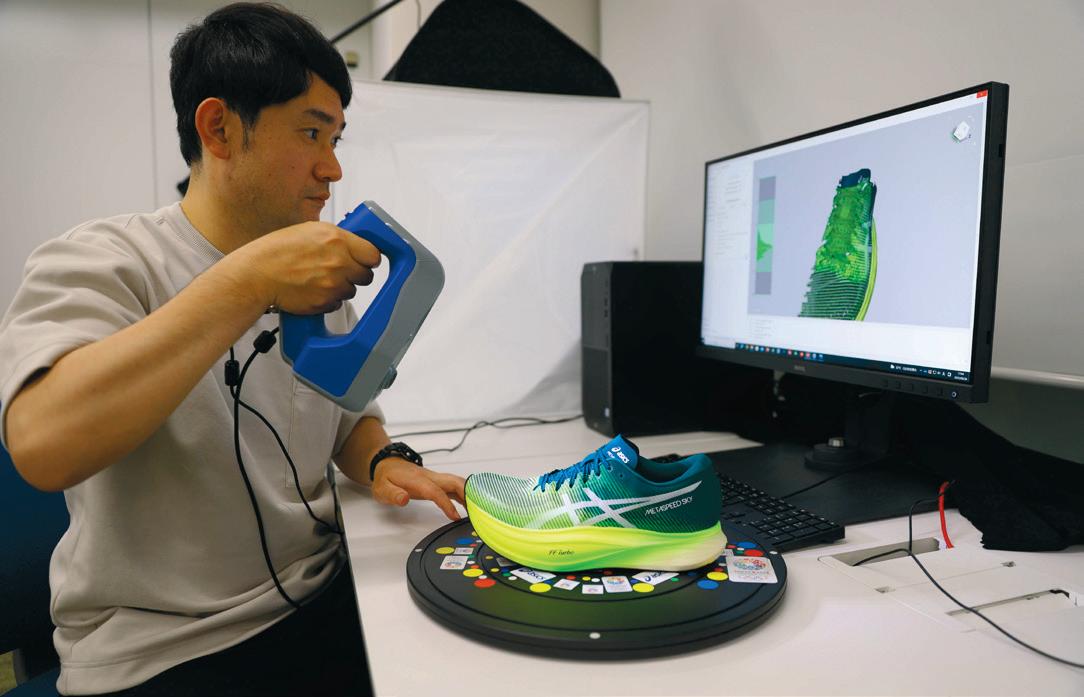
2 minute read
RUNNING THE
Japanese sporting goods company Asics has expanded its arsenal of digital tools and adopted 3D scanning in order to transform its workflow, as Claudia Schergna reports
When Asics decided to adopt the Artec 3D scanning technology, its main challenge was not only to capture its famous running shoe’s external and internal features, but also to retain the signature bright colours and unique textures that define the company’s products.
The vivid hues are undoubtedly a hallmark of the Japanese sports equipment manufacturer, but even the most hi-res photography didn’t do justice to their brightness and intensity.
The Asics marketing team was therefore on the hunt for a technology that would allow the company to fully digitise its products, particularly running shoes.
While 3D scanning has long been used by Asics’ design and marketing teams, previous hardware proved inadequate for capturing more detail: “We had been using a 3D scanner from another manufacturer, but the quality of the textures was not sufficient,” explains Shintaro Nagata, a member of the Asics footwear digital technology team.
“Therefore, we decided to use Artec, which utilises photogrammetry technology and can add high-quality texture information.”
When the Asics team got to try Artec’s precision bluelight based technology Space Spider, what immediately got their attention was its ability to capture smaller objects in high resolution and brilliant colour.
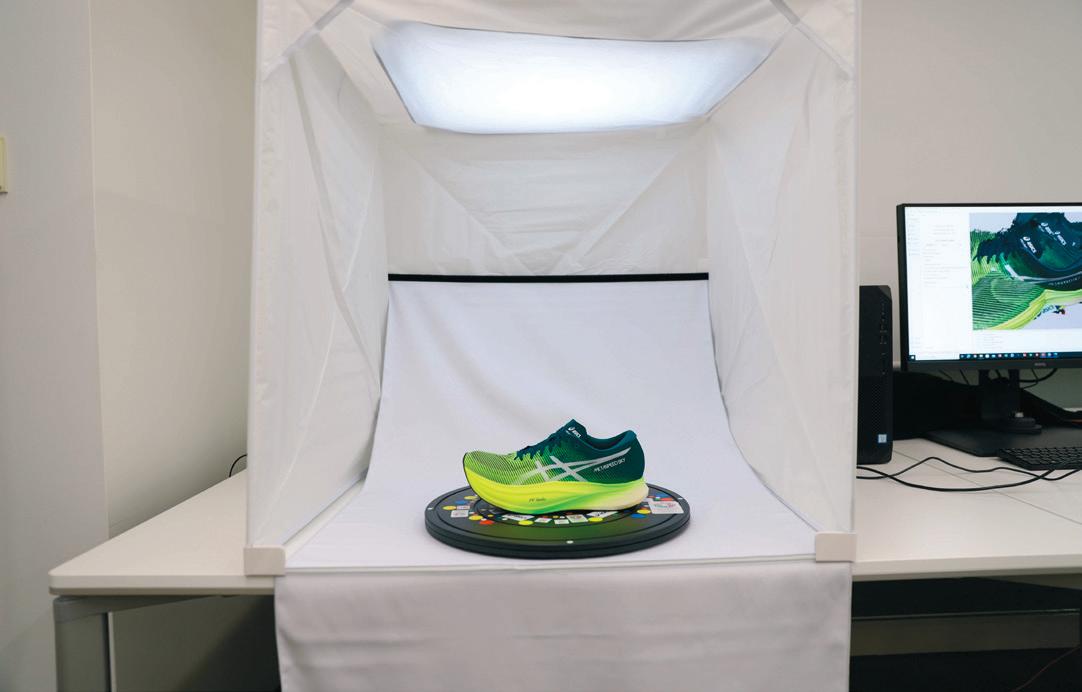
DataDesign, an Artec reseller in Japan, offered Asics a comprehensive demo that featured Artec Space Spider as the right solution to meet the project’s needs. With the choice made in Artec’s favour, the design journey began. “We think that 3D scanning works very well when it comes to the editing of finished goods, such as an experiment with new products by changing the colour of existing ones,” says Nagata.
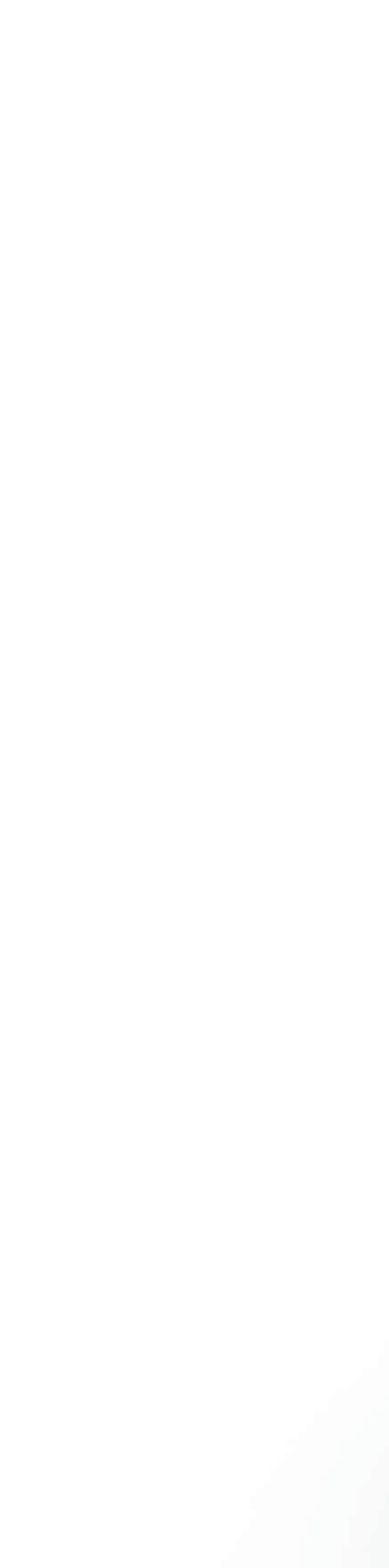
“Artec Studio enables 3D scanning and photogrammetry in a single software. It has made it possible to create a high-quality 3D model efficiently by combining the positive sides of both methods while compensating for any disadvantages.”
Asics’ workflow with Artec Space Spider is straightforward: once a pair of shoes is made and ready for purchase, the team then 3D scans a sample pair with Space Spider.
This requires virtually no preparation: The shoe is placed on a mat and scanned from three different angles, then turned and flipped for full capture. While the 3D model is being constructed from scan data, numerous photographs are taken with a DSL camera.
The pictures are then imported directly into Artec Studio, where the 3D model is mapped to the images for photo texturing. The team uses the Manual Mode in Artec Studio for maximum control and flexibility.
The resulting ultra-realistic 3D models of sports shoes are used for quality inspection, as well as for video and animated marketing content. If the model is needed for quality control, additional steps in Oqton Geomagic Control X may be required.
In that case, the model is inspected dimensionally, and a report is generated in the software, excluding any possibility of inaccuracy.
● 1 An Asics running shoe is placed on a mat and scanned from three angles
● 2 A 3D model is constructed from the scan data in Artec Studio
● 3 Photographs are taken of the running shoe using a DSL camera
● 4 Photos are imported into Artec Studio and the 3D model is mapped to the images for photo texturing
● 5 Bright colours and unique textures define Asic’s products