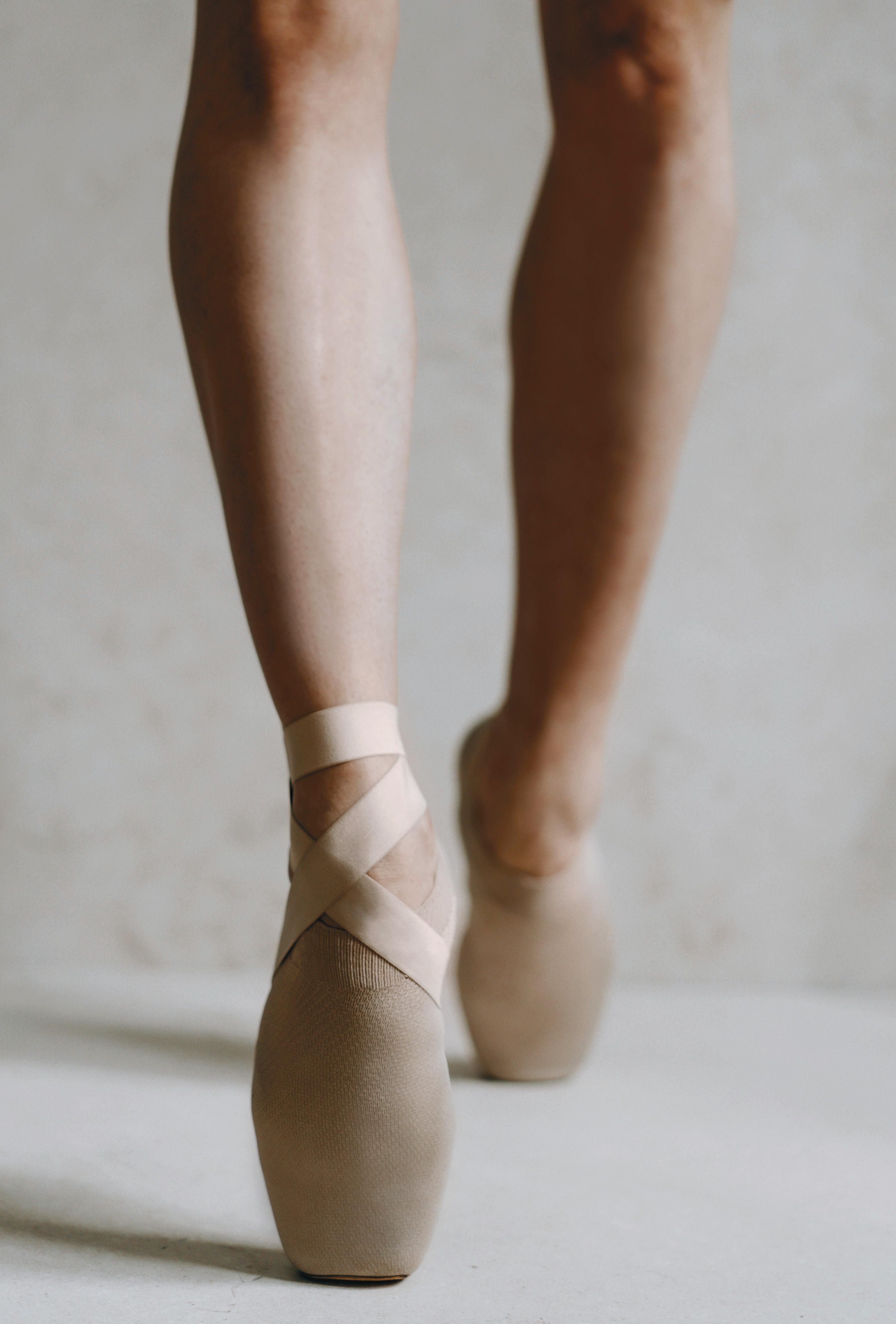
5 minute read
AN ‘EN POINTE’ REVOLUTION
Ballet is both a sport and an art form, requiring extreme dedication, punishing training and rehearsal schedules, endurance and strength. Having the right footwear makes a big difference to dancers and Act’ble intends to play a starring role in making that happen, as Claudia Schergna reports
In 2013, the New York City Ballet ordered 8,500 pairs of pointe shoes, to ensure that its 180 ballerinas were well-equipped for the whole performance season. This might sound like a dramatic oversupply, with great potential for waste, but it’s not unusual for classical dancers to require regular replacements.
Very regular, in fact. “The lifespan of those shoes is only one day in professional dance,” explains Sophia Lindner, founder, CEO and creative director at Act’ble, a German start-up aiming to revolutionise the design of pointe shoes.
If we assume that a professional dancer wears a new pair maybe five times per week, they would buy and throw away roughly 260 pairs of shoes a year.
Pointe shoes aren’t cheap to purchase, nor are they easy to dispose of. They are made of multiple materials – leather, cotton, satin, other fabrics, cardboard and glue – making them hard to recycle. Nor are they easy to manufacture. In professional dance, each pair is custommade according to a ballerina’s physical features and dancing style. No two pairs of shoes are identical. Dancing in the wrong shoe, meanwhile, can be so painful that you wouldn’t wish it on your worst enemy. Lindner learnt this the hard way: “I danced ballet for 14 years and experienced all the problems myself that dancers have with finding pointe shoes – the pain, the injuries. I saw the need to solve a huge problem and wanted to make an impact in the dance world,” she says.
Made For Unique Feet
Lindner started working on solving the problem as her graduation project for her Bachelor’s degree in industrial design. “With the design, we created a custom fit and modular pointe shoe, matching each dancer’s unique feet for increased support, movement range and durability, as well as to reduce pain,” she says.
“The dancer’s needs are the basis of our design decisions,” she says. Regular pointe shoes need ‘breaking in’ by a dancer, typically for at least one hour, in order to prepare them for more extended wear.
These shoes, by contrast, don’t demand this kind of preparation, due to their TPU material and sole geometry. “The 3D printed structure of the sole allows flexibility and stability simultaneously, making the shoes last up to five times longer. The box is designed to adapt to the foot width for a custom fit,” says Lindner.
Finding the right kind of pointe shoe is a challenge that can take years for many dancers, according to Violetta Keller, principal dancer with the Finnish National Ballet and an Act’ble customer. She herself has extremely arched and small feet, and struggled to find the right shoe. But the fitting experience with Act’ble was an entirely different experience, she says.
“It looked like my foot, but in a shoe. It elongated my line when I was dancing, making my foot look slimmer and prettier,” she says. “They were so comfortable, I didn’t want to take them off! They gave me the possibility to adjust in every possible way.”
Keller was one of 50 professional dancing athletes who took part in the beta phase with Act’ble. “We collected their feedback and incorporated it into the product until it was ready for the market. On top of that, we are working with experts from the performance shoe industry, research institutes and dance medicine specialists to create the best product possible,” says Lindner.
A Break With History
What’s innovative about the product – besides the fact it employs 3D printing – is the durability, the health benefits, and the unique modular system used by these dance shoes.
Anyone familiar with the ballet industry knows that pointe shoes haven’t changed much in hundreds of years. Nor have the materials used. They are typically made of satin for the outer part, with the toe box made of densely packed layers of fabric, cardboard and paper, hardened with pointe shoe pastes. The shank consists of cardboard layers, and the sole is usually made of thin leather.
So the Act’ble shoe represents a real break from history. “Our shoe is ready to wear and adapts to the foot of the dancer,” says Lindner. “The sole is recyclable and lasts up to five times longer, which means you also save money in the long run. The most important part for us are the health benefits. The pain level when dancing in Act pointes is reduced to a minimum, thanks to our hidden and patented lacing system, which helps distribute the forces in an optimal way.”
‘‘ I danced ballet for 14 years and experienced all the problems that dancers have with finding pointe shoes — the pain, the injuries
Act’ble’s pointe shoe is ready-to-wear and adapts to the foot of the individual dancer
About three years passed between Lindner’s initial idea and a dancer finally putting on a pair of Act’ble pointe shoes. During that time, her team had to find investors and partners. One of these partners is HP, which now provides Act’ble with the 3D printing equipment needed to make the shoes. “In over hundreds of iterations, we adapted the 3D-printed geometry to the feet of professional athletes,” she says.
In terms of CAD and 3D modelling, the team uses a mixture of Rhino 3D, Fusion 360, and Blender. The prototyping phase takes place both in-house using filament 3D printers and with the help of some independent bureaus, which have assisted Act’ble in identifying the right materials and technologies.
Dancer Wellbeing
Research at Act’ble is conducted by an all-female team of six designers, all with different backgrounds within the design realm and a passion for ballet and dancers’ health.
“We receive great feedback from the dancers. Some dancers get very emotional, because they thought they would never find their perfect pointe shoe,” says Lindner.
“Finally, someone is taking care of their health issues and listening to their needs and problems. We see a huge potential in shifting something for the dance community in terms of health and sustainability.”
Despite the fact Actable shoes are receiving positive feedback from customers, the company is still on the hunt for the perfect material for the outer layers, the ‘skin’ of the shoe. The most difficult part of the process, according to Lindner, has been combining all elements of the shoe – namely laces, the sole and skin – to achieve the desired effect.
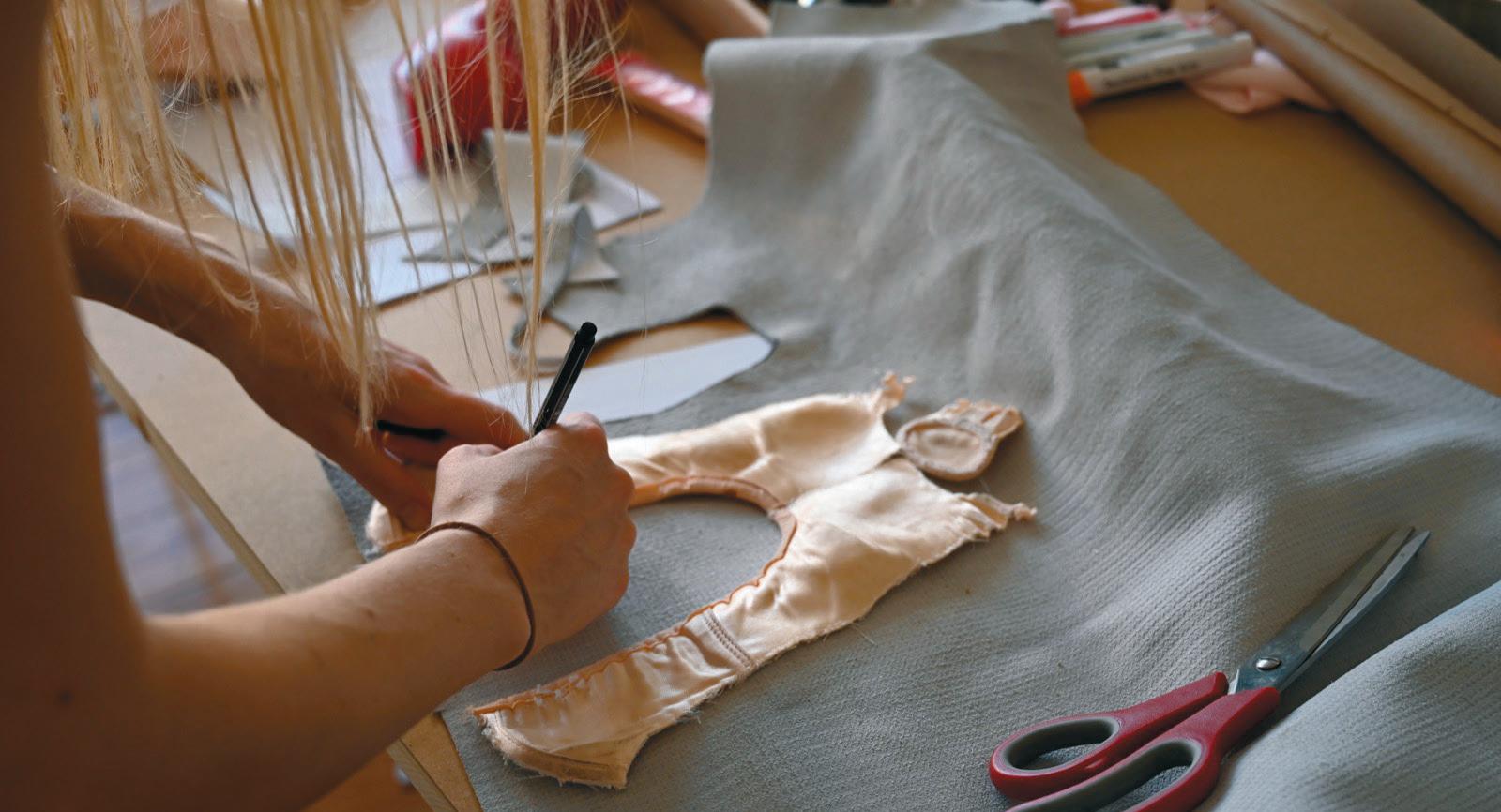
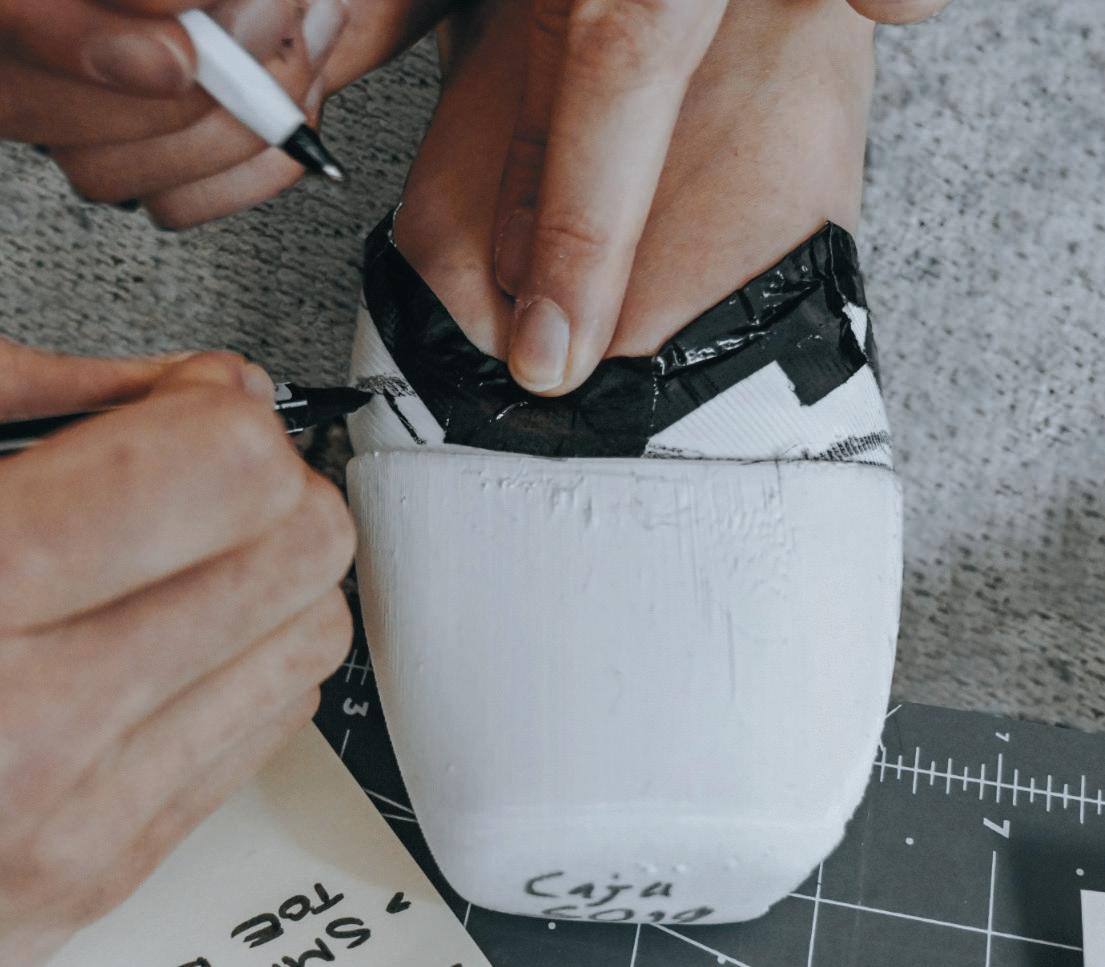
Although 3D printing is not a new technology in many industries, it is very innovative to use it in ballet shoe design. It’s also an extremely convenient technology, says Lindner: “In 3D printing, we have found a tool that offers the same precision and individuality as the athletes themselves.”
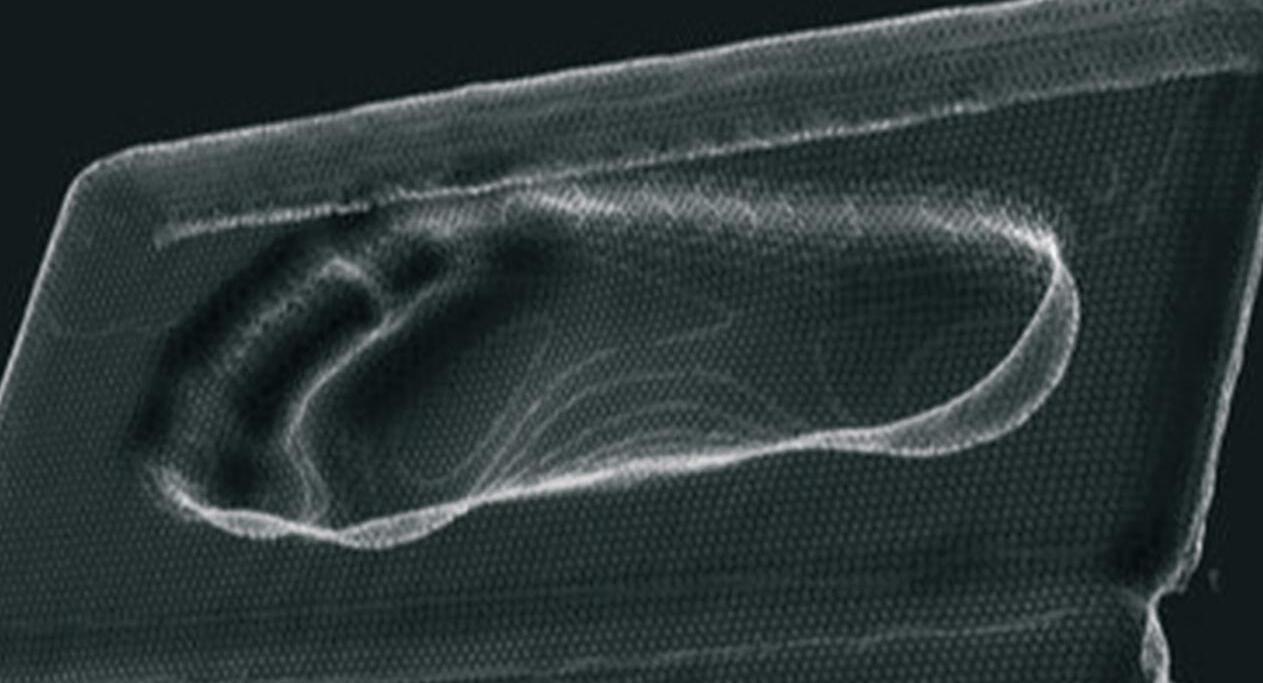
Mass personalisation and motion capture also open up possibilities that were previously unheard of in this industry, she continues. “In over a hundred iterations, we 3D printed an individually generated prototype every one to two days, further optimised it, and tested it with high-level athletes from surrounding state theatres and companies, with extremely positive feedback.”
Due to the high precision of the additive manufacturing process, says Lindner, the Act’ble team has been able to develop a performance sole with rapid prototyping that never existed before and to radically rethink and revolutionise a 200-year-old history. www.actable.me
●
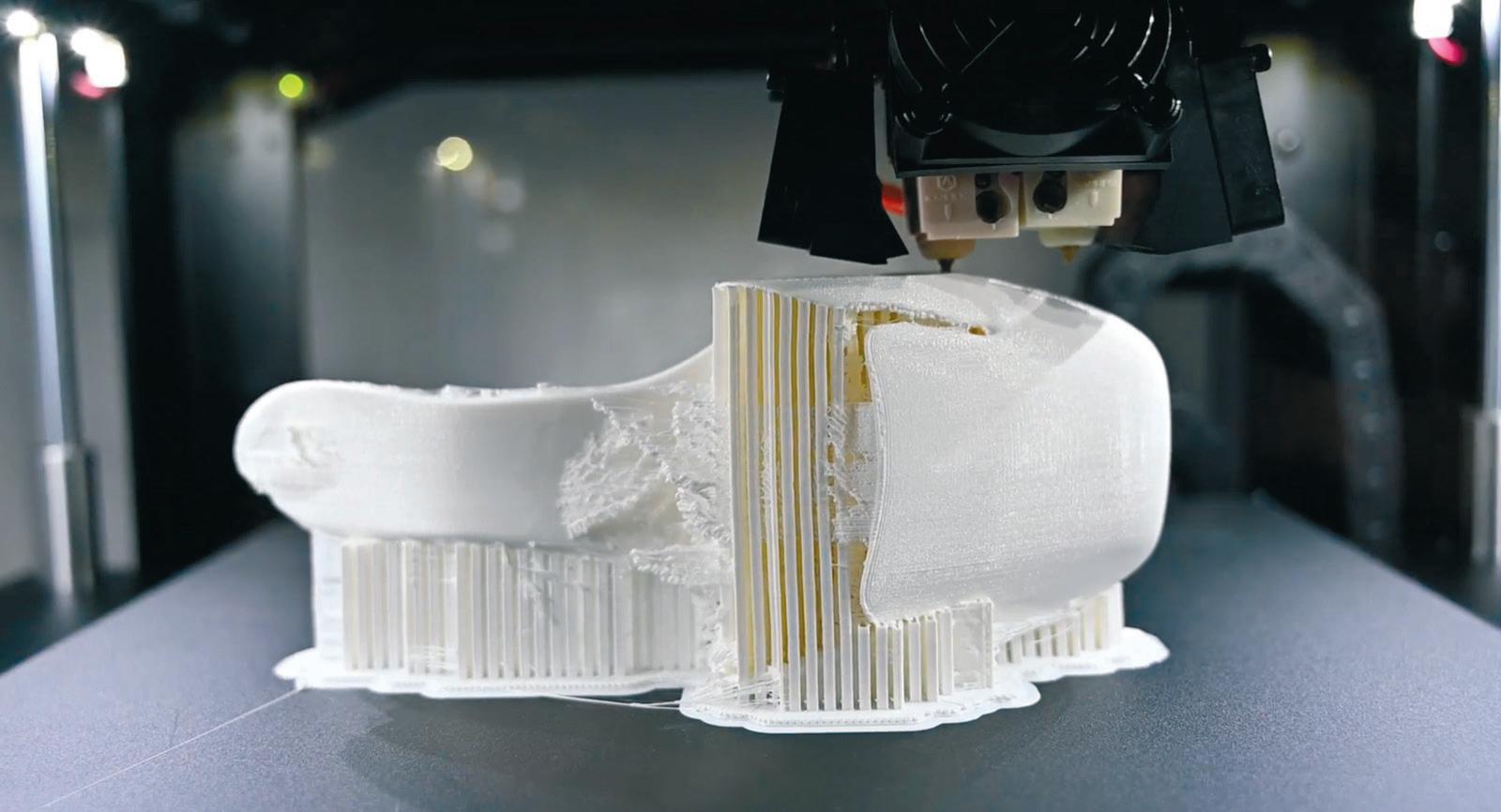

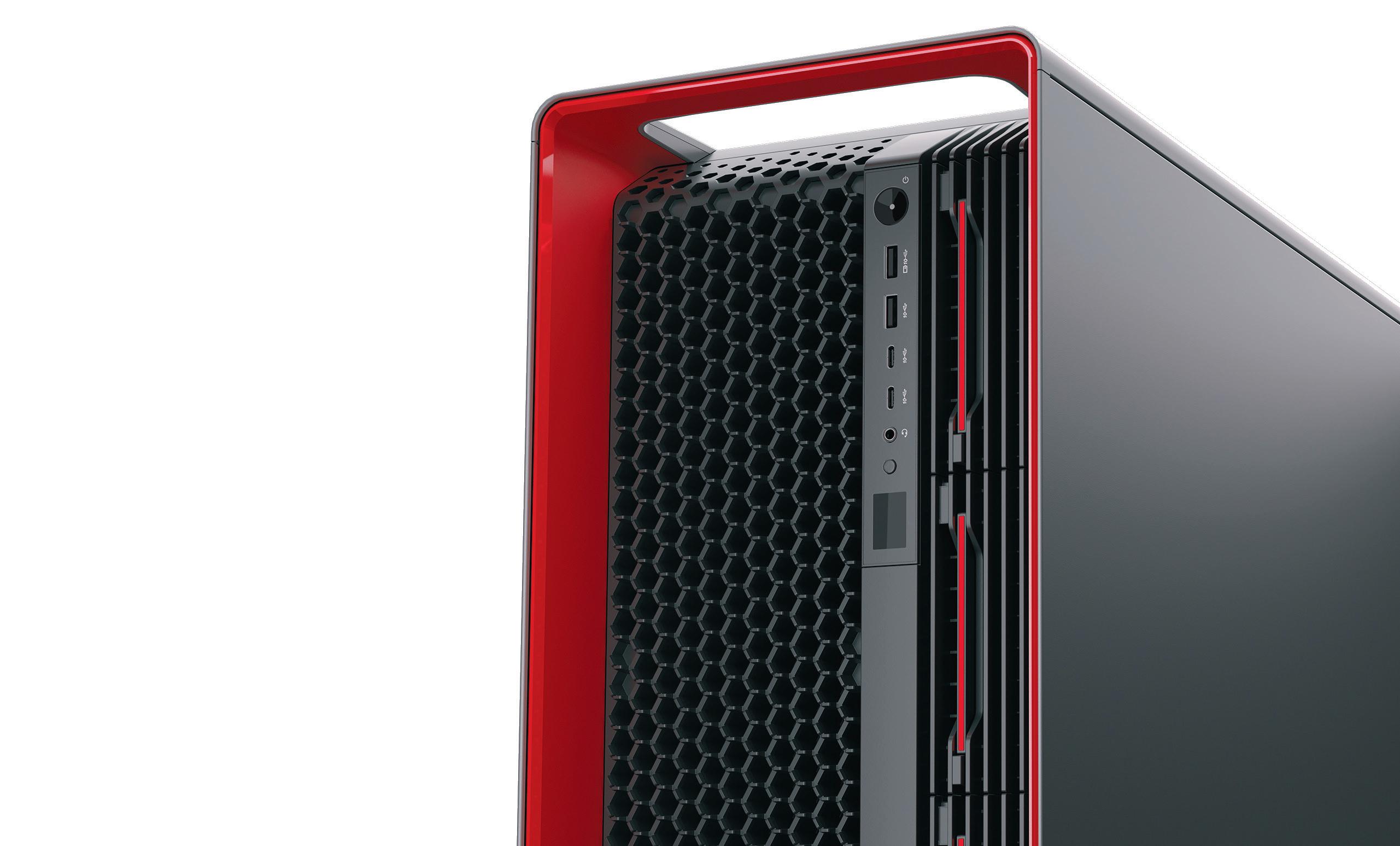

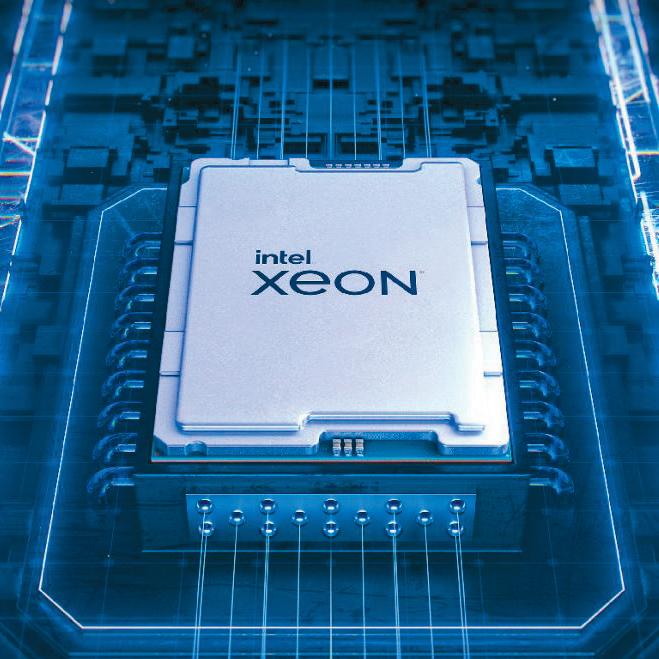