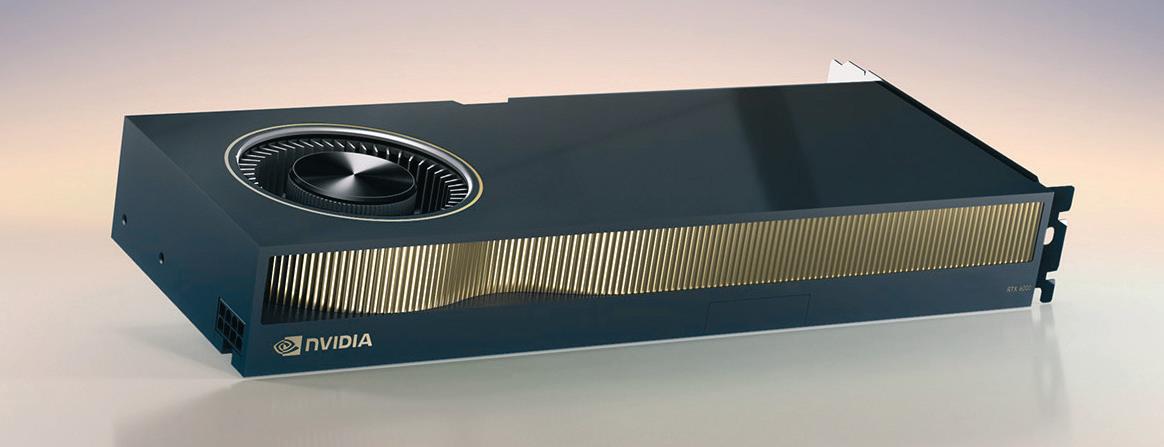
34 minute read
Workstation news
NVIDIA RTX 6000 GPU DELIVERS BOOST FOR BOTH VISUALISATION AND SIMULATION
» High-end workstation GPU not only boasts more powerful hardware, but promises to boost performance further by changing the way viewports and scenes are rendered
Nvidia has launched the Nvidia RTX 6000, a high-end workstation GPU built on the company’s new 'Ada Lovelace' architecture.
The RTX 6000 is said to deliver up to two to four times the performance of the previous generation ‘Ampere’ RTX A6000 and promises to deliver big advances in real-time rendering, graphics, AI and compute, including simulation.
The RTX 6000 is a dual-slot card with 48GB of GDDR6 memory (with ECC), a max power consumption of 300W and support for PCIe Gen 4.
The GPU offers all the generational improvements you’d expect from a new architecture – third-gen RT Cores for ray tracing, fourth-gen Tensor Cores for AI compute, and next-gen CUDA cores for graphics and simulation – but there are also significant changes in the way the GPU carries out calculations to increase performance in graphics workflows.
One of these is Nvidia Deep Learning Super Sampling 3 (DLSS). DLSS has been around for several years and, with the RTX 6000, is now on its third generation. It uses deep learning-based upscaling techniques, where frames are rendered at a lower resolution and the GPU’s ‘AI’ Tensor cores are then used to predict what a high-res frame would look like.
With Nvidia’s previous generation ‘Ampere’ GPUs, DLSS 2 took a lowresolution current frame and the highresolution previous frame to predict, on a pixel-by-pixel basis, what a high-resolution current frame would look like.
With DLSS 3, the AI generates entirely new frames, rather than just pixels. It processes the new frame, and the prior frame, to discover how the scene is changing, then generates entirely new frames without having to process the graphics pipeline. According to Nvidia CEO Jensen Huang, this approach means DLSS 3 will benefit both GPU and CPU limited games.
The RTX 6000 is a dual slot card with 48 GB of GDDR6 memory (ECC), a max power consumption of 300W and support for PCIe Gen 4
Huang made no reference to how DLSS 3 might benefit professional 3D applications. But while DLSS 2 was used mainly in GPUlimited viz applications such as Enscape and Autodesk VRED, we wonder if DLSS 3 might deliver big performance gains for 3D CAD, which tends to be CPU-limited.
The RTX 6000 also supports Shader Execution Reordering (SER). Huang explained that GPUs are most efficient when processing similar work at the same time. However, with ray tracing, rays bounce in different directions and intersect surfaces of various types. According to Huang, this can lead to different threads processing different shaders or accessing memory that is hard to coalesce or cache.
With SER, the RTX 6000 dynamically reorganises its workload, so similar shaders are processed together. According to Nvidia, SER can deliver a two to three times speed-up for ray tracing and a frame rate increase of up to 25%. The company did not announce which applications will take advantage of this technology.
Nvidia also explained how the new GPU can benefit simulation, demonstrating computational fluid dynamics (CFD) examples in Ansys Discovery and Ansys Fluent. It highlighted how, with the RTX 6000’s 48GB of memory, designers can increase the fidelity of the solver to perform more accurate simulations and still obtain the results in near real time. www.nvidia.com/RTX
AMD boosts 3D performance in Solidworks and other OpenGL apps
AMD has launched a new professional graphics driver that is said to provide a major performance uplift in CAD and other 3D applications that rely on the OpenGL graphics API. This includes Dassault Systemes Solidworks, Autodesk Maya, Trimble SketchUp and McNeel Rhino.
The re-architected driver (AMD Software: Pro Edition 22.Q3) works with current generation and older generation Radeon Pro GPUs.
AMD has released performance figures that show gains ranging from 0% to 76% in the SPECviewperf 2020 benchmark.
Initial testing in DEVELOP3D's labs demonstrate performance gains can be even higher — close to 300% faster in visualisation software Autodesk VRED Professional 2023 and over 200% faster in Solidworks 2022. However, our testing shows that performance can also go down.
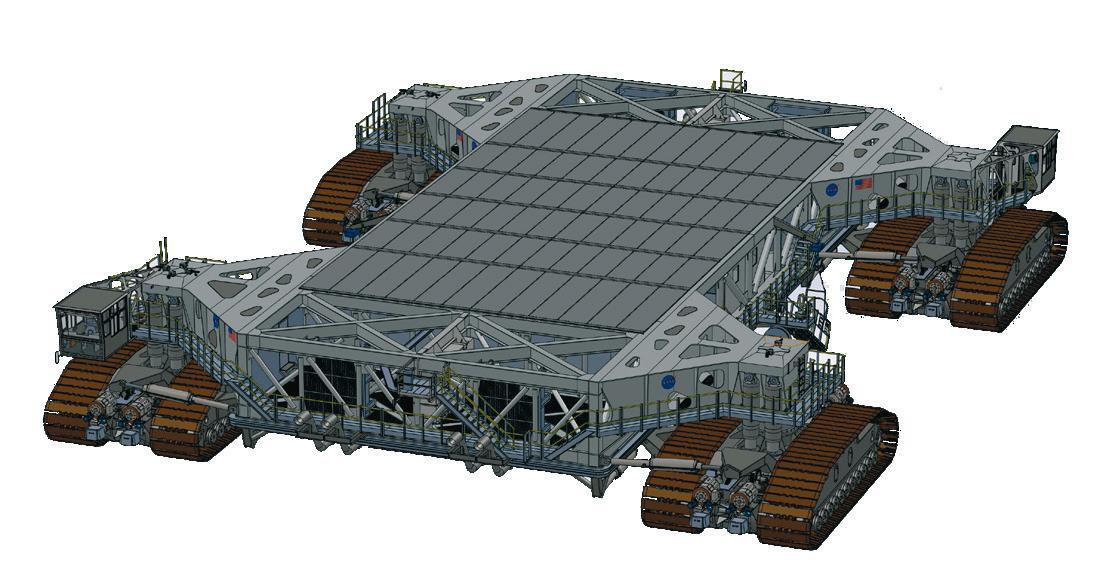
This can be with certain applications, when using large assemblies that do not fit entirely into GPU memory, or with particularly old GPUs such as the Radeon Pro WX 5100, which was released in 2016.
DEVELOP3D's benchmarks show AMD's new driver can boost performance in Solidworks by 200% WHAT DEVELOP3D THINKS
It’s good to see AMD innovating in an area that can potentially bring huge benefits to users of 3D CAD. OpenGL might not be the future of graphics APIs, but it’s still used extensively in many 3D applications. Getting more out of your computer hardware for free is always a good thing, but it’s perhaps those with ageing graphics cards that can benefit most here. While our tests show that the Radeon Pro WX 5100 slows down in Solidworks when using the new driver, AMD’s previous generation Radeon Pro W5500 gets a new lease of life, which in certain workflows, could deliver a big boost in productivity. www.amd.com
INTEL GETS FIRST DISCRETE ARC PRO GPU WIN WITH LENOVO
» CAD-focused discrete Intel Arc Pro A30M available now in the Lenovo ThinkPad P16 mobile workstation
Lenovo has become the first major workstation vendor to offer a discrete Intel professional GPU in a mobile workstation.
The Lenovo ThinkPad P16 Gen 1 can now be configured with the Intel Arc Pro A30M (4GB), as an alternative to the standard Nvidia options, which range from the Nvidia RTX A1000 (4GB) up to the Nvidia RTX A5500 (16GB).
The Intel Arc Pro A30M is an entry-level pro GPU, and is part of Intel’s much-anticipated entry to the world of discrete workstation graphics.
By offering the GPU in the powerful ThinkPad P16, it should give prospective buyers more choice for less demanding 2D and 3D workflows, such as CAD and BIM.
The Intel Arc Pro A30M also includes hardware-accelerated ray tracing and hardware-assisted AI (XeSS). On paper, this should make it suitable for ray trace rendering in applications that support Microsoft DX12/DXR, and ray tracing using the Vulkan API. However, those who take design visualisation seriously will likely be better served by one of the higher-end Nvidia RTX GPUs.
For less demanding users, the Intel Arc Pro A30M GPU does offer considerable cost savings.
On Lenovo’s UK website, configuring the ThinkPad P16 with the Intel GPU instead of the lowest cost Nvidia option – the Nvidia RTX A1000 (4GB) – will shave £183 off the price of the laptop. Selecting it in place of the Nvidia RTX A2000 (8GB) will save £413. This is a significant first step for Intel as it looks to take on Nvidia and AMD, which both have a strong pedigree in workstation GPUs. We have yet to hear news of any major workstation vendor offering Intel’s desktop pro GPUs – the Intel Arc Pro A40 and Intel Arc Pro A50. However, with 13th Gen Intel Core ‘Raptor Lake’ CPUs rumoured to launch in Q4 2022, any announcements could coincide with the new desktop workstations that will certainly follow. www.intel.com/ arcprographics
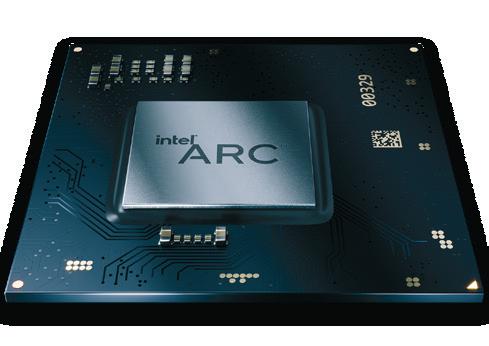
With the Intel Arc Pro A30, Lenovo has broadened the choice of GPUs in the ThinkPad P16 beyond Nvidia RTX
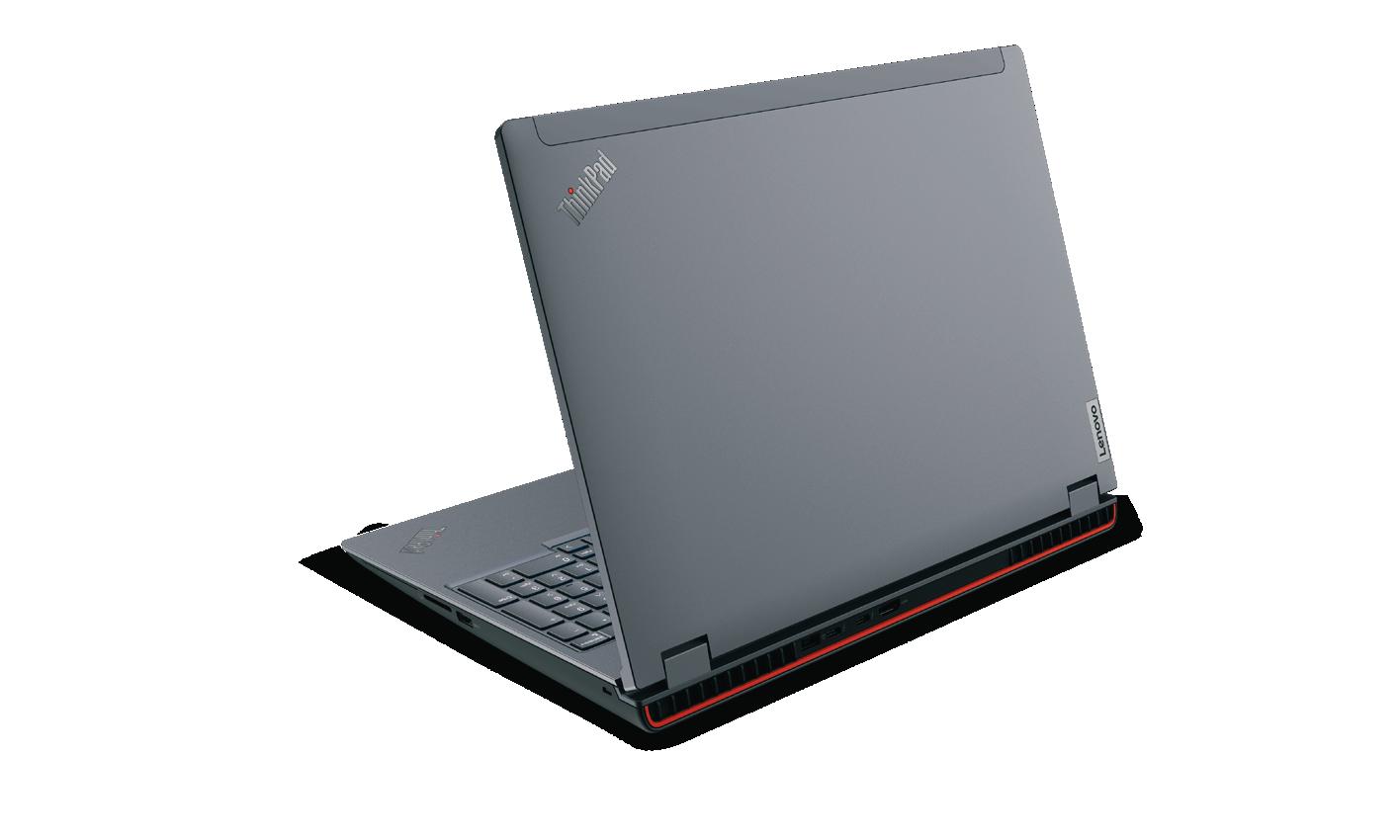
Automotive giants test Nvidia OVX GPU systems
BMW Group and Jaguar Land Rover will be among the first companies to test second generation Nvidia OVX systems with Nvidia L40 GPUs, designed to power large-scale Omniverse digital twins.
“Planning our factories of the future starts with building state-of-the-art digital twins using Nvidia Omniverse,” said Jürgen Wittmann, head of innovation and virtual production at BMW Group. “Using Nvidia OVX systems to run our digital twin workloads will provide the performance and scale needed to develop large-scale photorealistic models of our factories and conduct true-to-reality simulations that will transform our manufacturing, design and production processes.”
“Nvidia OVX and Drive Sim deliver a powerful platform that enables us to simulate a wide range of real-world driving scenarios to safely and efficiently test our next generation of connected and autonomous vehicles as well as to recreate the customer journey to demonstrate vehicle features and functions,” said Alex Heslop, director of electrical, electronic and software engineering at Jaguar Land Rover. “Using this technology to generate large volumes of high-fidelity, physically accurate scenarios in a scalable, cost-efficient manner will accelerate our progress towards our goal of a future with zero accidents and less congestion.”
Second-generation Nvidia OVX systems will be available from Inspur, Lenovo and Supermicro by early 2023. www.nvidia.com
HP display boasts deeper and richer blacks
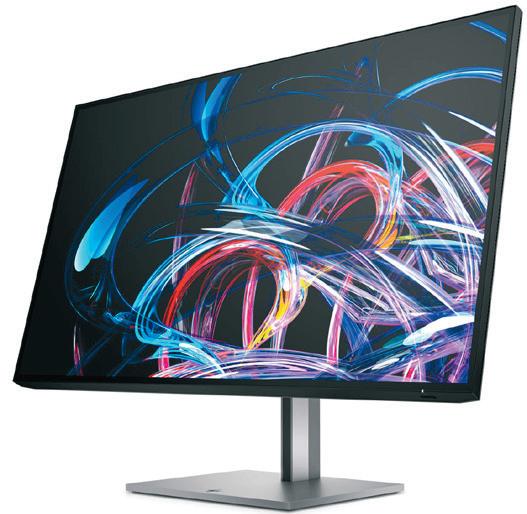
HP has introduced the HP Z32k G3 4K USB-C display with IPS Black Panel, a technology that offers double the contrast ratio of a traditional IPS panel for “deeper and richer” blacks.
The 31.5-inch 4K display is said to offer ‘ultimate colour accuracy’ with support for 100% of the sRGB colour gamut and 98% of DCI-P3. According to HP, it allows users to experience anything from CAD drawings to product renders in tangible, lifelike detail.
Beyond image quality, the HP Z32k G3 4K USB-C display also offers several practical features.
Through a single Thunderbolt 4 connection, the display drives 4K resolution at 60Hz, supports daisy chaining for a second 4K monitor without a dock, as well as high-speed data and internet — all while charging a device up to 100W.
‘Single power on’ allows users to turn on their workstation by simply pressing the power button on the bottom right of the display. “You no longer need to open the laptop and hunt for the power button,” says HP’s Aaron Slessinger. KVM switch allows easy switching between two workstations – a laptop and a desktop, for example. Users can also save space by attaching a HP Z2 Mini Workstation at the rear. www.hp.com
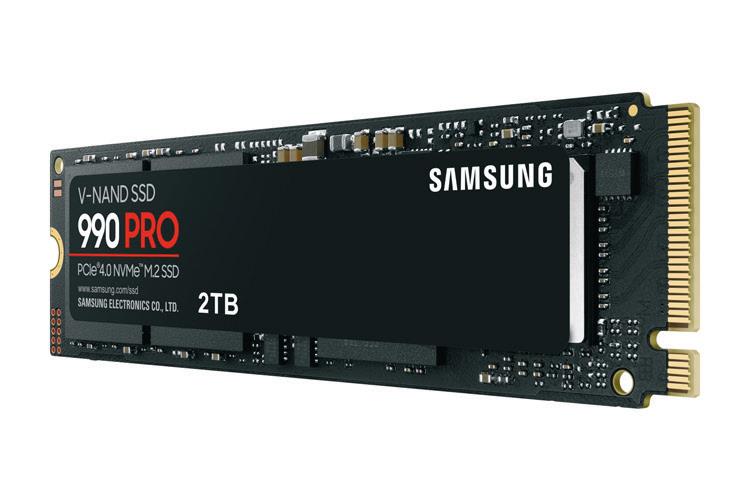
The HP Z32k G3 4K USB-C display offers double the contrast ratio of a typical IPS panel
Samsung 990 Pro SSD launches
Samsung has announced the SSD 990 Pro, a new highperformance PCIe 4.0 NVMe SSD designed for desktop and mobile workstations.
Samsung claims the M.2 form factor SSD offers the highest speed currently available from the PCIe 4.0 interface.
Compared to the 980 Pro it replaces, the 990 Pro is said to deliver faster sequential read and write speeds and even bigger gains in random read/write performance. www.samsung.com/ssd
AMD RYZEN 7000 SERIES CPUS LAUNCH WITH BOOST FOR CAD AND RENDERING
» ‘Zen 4’ CPUs feature a 5.7 GHz boost frequency and a significant Instructions Per Clock (IPC) increase, compared to AMD's previous generation ‘Zen 3’ architecture
AMD has launched the Ryzen 7000 Series, a new family of desktop processors based on its 5nm ‘Zen 4’ architecture. This includes the flagship 16-core Ryzen 9 7950X, which AMD claims is the fastest desktop CPU in the world, featuring a 5.7 GHz boost frequency and a significant Instructions Per Clock (IPC) increase, compared to its previous generation ‘Zen 3’ architecture.
According to AMD, the Ryzen 7000 Series will outperform 12th Gen Intel Core processors in both single-threaded workflows (which is important for CAD and BIM) and multi-threaded workflows, such as ray trace rendering.
In V-Ray Render, for example, AMD claims the Ryzen 9 7950X offers 62% more performance than the Intel Core i9-12900K, Intel’s current flagship mainstream CPU which has 8 Performance cores and 8 Efficient Cores. Performance gains in other rendering benchmarks are smaller, with Cinebench R23 NT quoted at 41% and Blender Render at 36%. However, with 13th Gen Intel Core ‘Raptor Lake’ CPUs just launching now (see below), AMD will soon face increased competition.
AMD’s Ryzen 7000 Series also marks a significant improvement over AMD’s previous generation ‘Zen 3’ Ryzen 5000 Series. Compared to the Ryzen 9 5950X, the Ryzen 9 7950X boasts a single-core performance improvement of up to 29% and up to 48% more performance when rendering in V-Ray and Cinebench R23 nT.
The Ryzen 7000 Series also offers “leadership energy efficiency”, claims AMD. The company states that the Ryzen 9 7950X is up to 47% more energy efficient than the Intel Core i9-12900K when ray trace rendering in the Chaos V-Ray Benchmark.
With a TDP of 170W, the Ryzen 9 7950X is more power-hungry than the 105W Ryzen 9 5950X it replaces. However, the 7950X wins out in performance per watt. It delivers the same performance as the 5950X, while using up to 62% less power, says AMD.
The Ryzen 7000 Series also marks the launch of the new Socket AM5 platform, which features dual-channel DDR5 memory and support for PCIe 5.0, including next-generation SSDs.
There are currently four models in the AMD Ryzen 7000 Series – the 16-core Ryzen 9 7950X, 12-core Ryzen 9 7900X, 8-core Ryzen 7 7700X and 6-core Ryzen 5 7600X. The lower-core count CPUs, which are perhaps best suited to entry-level CAD and BIM workflows, also have slightly lower boost frequencies than the higher core count models. www.amd.com/ryzen
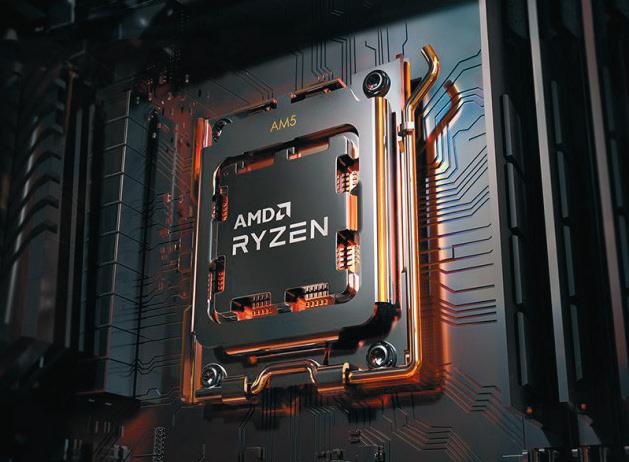
Intel unveils 13th Gen Intel Core CPUs to set up battle with AMD
Intel has announced its 13th Gen Intel Core processor family, led by the Intel Core i9-13900K, which features 24 cores and a max turbo frequency of 5.8 GHz. The new ‘Raptor Lake’ CPUs will be available in desktop workstations later this year and will go head-to-head with the new AMD Ryzen 7000 Series, competing on a range of workflows from CAD and BIM to rendering and simulation. 13th Gen Intel Core processors pick up where 12th Gen Intel Core left off, with a hybrid architecture that features two different types of cores: Performancecores (P-cores) for primary tasks and slower Efficient-cores (E-cores). Workloads are split ‘intelligently’ using Intel’s Thread Director.
The big difference with 13th Gen Intel Core is that it has more E-cores than its predecessor. The flagship Intel Core i913900K, for example, has 16, double that of the Core i9-12900K. This should deliver a big performance lift in multi-threaded workflows such as rendering - as much as 41% faster, according to Intel.
Of course, the P-cores have also been enhanced and while their number remains the same (a total of eight in the Core i913900K), Intel says users can expect up to 15% better single-threaded performance compared to the previous generation.
While the spotlight is on the flagship Core i9-13900K, Intel has launched six 13th Gen Intel Core processors – three with integrated graphics and three without. The Core i7-13700K and Core i513600K could be of more interest to price conscious architects and engineers with predominantly single threaded workflows, such as CAD and BIM. WHAT DEVELOP3D THINKS
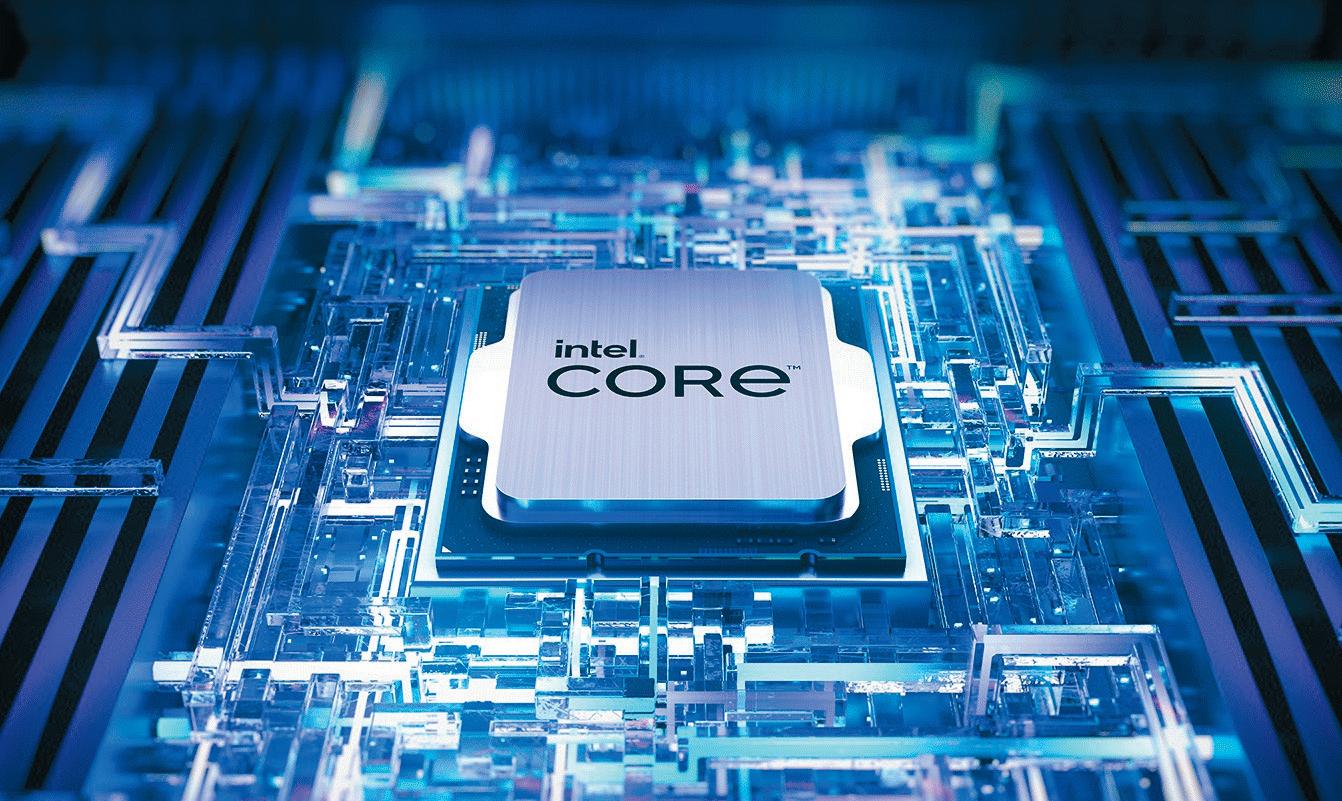
This is an incredibly exciting time for mainstream computer processors, with Intel and AMD both launching new architectures within weeks of each other. In recent years, AMD has certainly had a significant advantage for ray-trace rendering, but we now expect Intel to compete much more strongly in multithreaded workflows, as it did already in single threaded workflows like CAD.
Of course, when it comes to workstations, customers don’t always get a choice, with many large manufacturing firms being tied to procuring IT only from major manufacturers.
While we expect both 13th Gen Intel Core and AMD Ryzen 7000 Series workstations to be widely available from custom system builders like Scan, BOXX, Armari and Workstation Specialists, we still expect Intel to dominate among the tier ones. To date, Lenovo is the only one out of HP, Dell and Fujitsu to offer an AMD Ryzen processor in a mainstream workstation. Whether Ryzen 7000 becomes the catalyst for others to follow suit remains to be seen. www.intel.com
Professional Graphics Begins Here
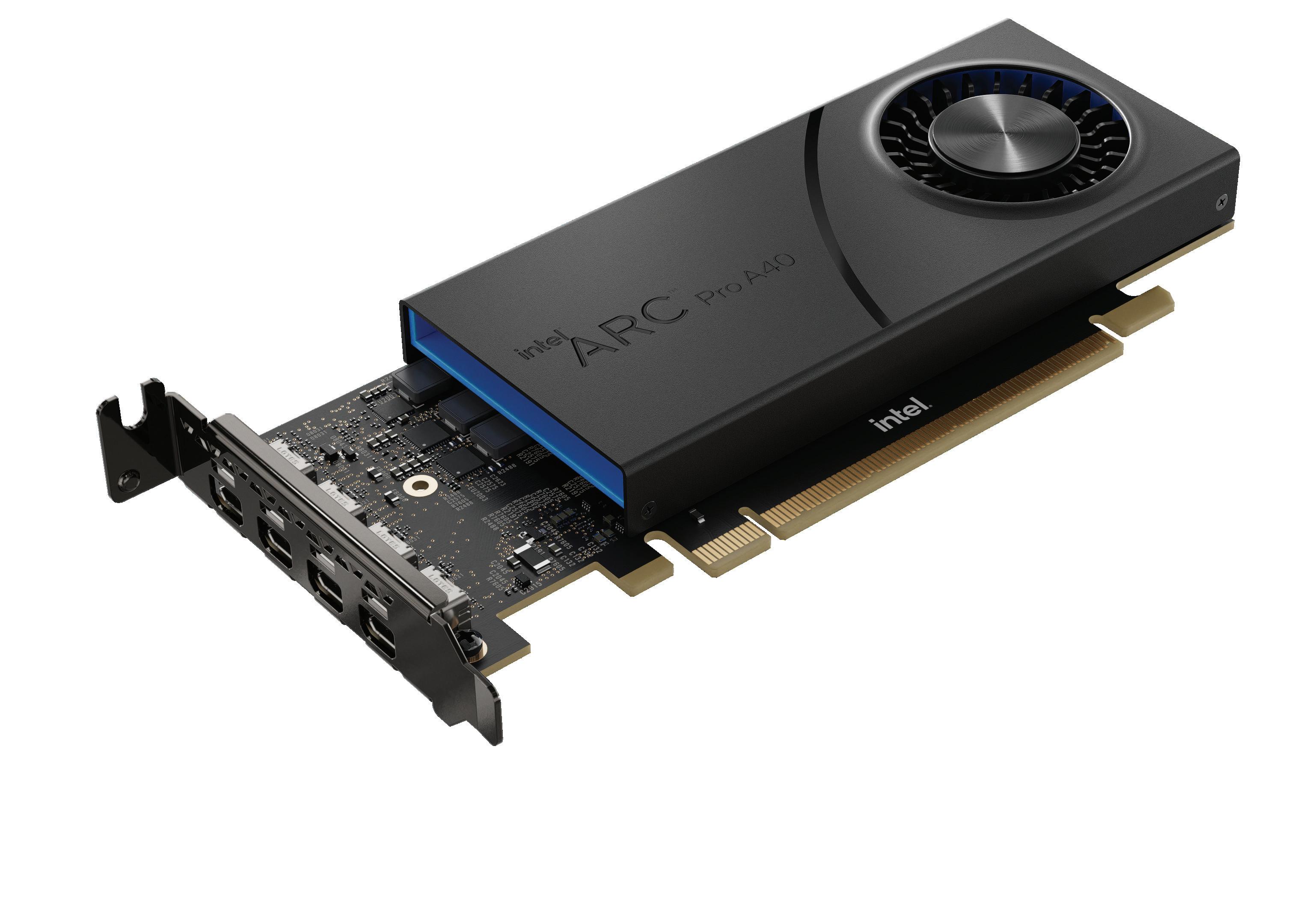
Image provided for illustrative purposes only. Actual product may differ.
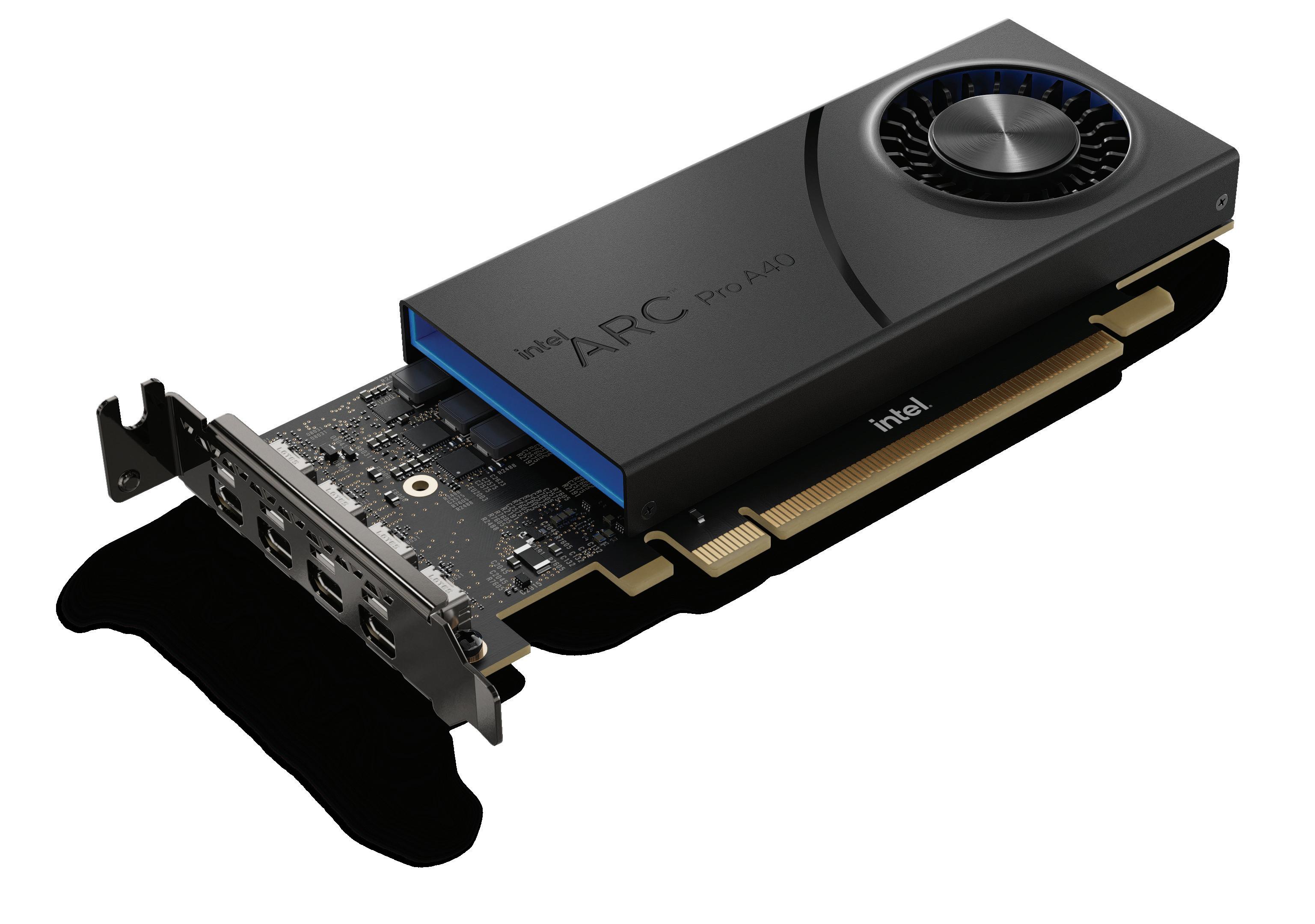
With built-in ray tracing hardware, graphics acceleration, and machine learning capabilities, the Intel® Arc™ Pro A40 GPU unites fluid viewports, the latest in visual technologies, and rich content creation in a condensed half height, half length form factor.
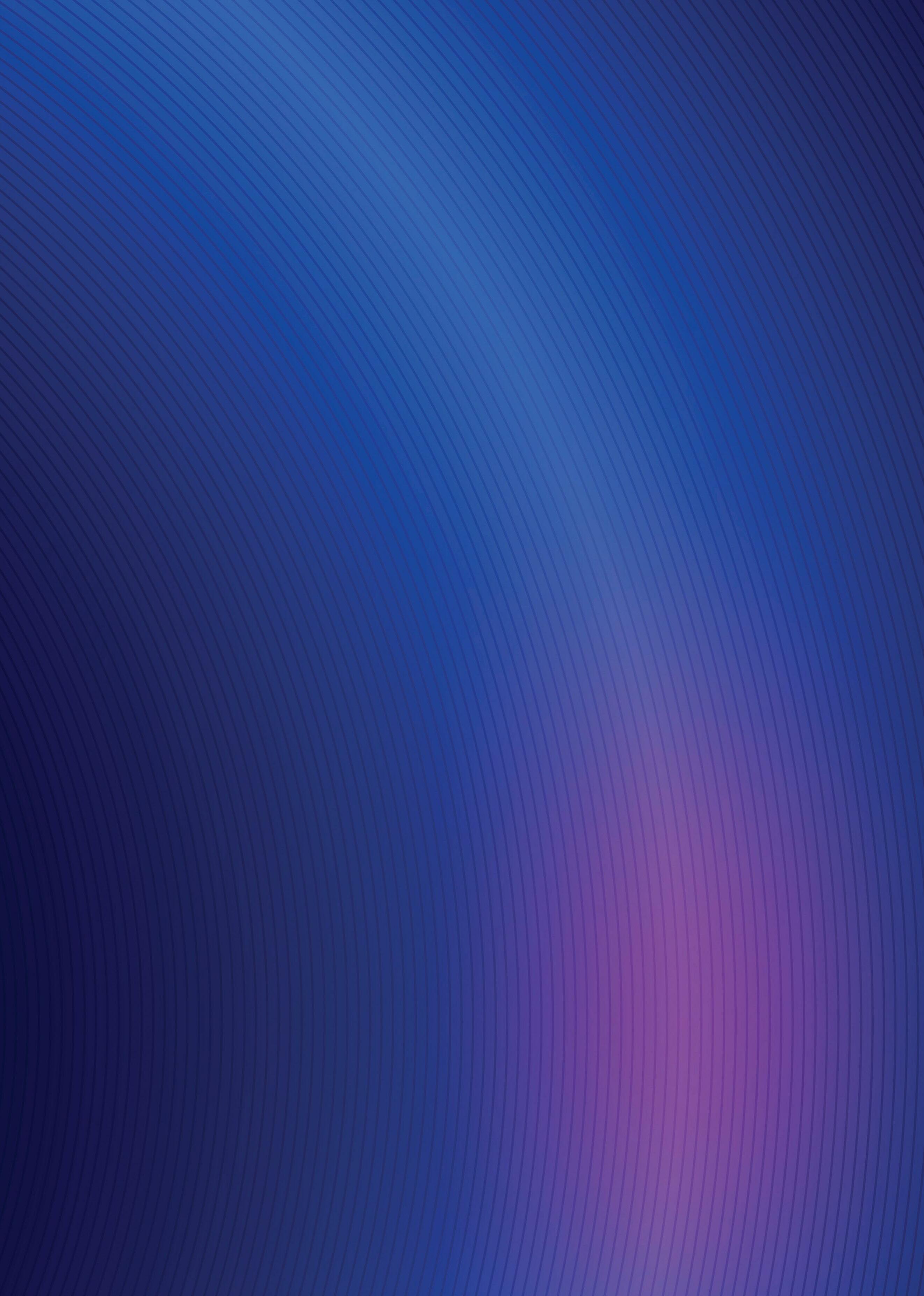
• Ray Tracing Hardware
Acceleration
• Dedicated AI Acceleration • Industry First AV1 Hardware
Encode
• 6GB High Speed Memory • Software Certifications • Up to 4x Displays, with Audio Support and
Latching Mechanism • Single Slot,
Tiny Form Factor • Premium Components • Extended Warranty
Intel.com/ArcProA40
Diversity in product design can be a matter of life or death. As our columnist SJ recounts, her recent experience with a pulse oximeter drives home the point that a lack of inclusive thinking can have devastating consequences

Diversity, equity, and inclusion – or DEI. Convenient lip service paid by companies and industries to show that they care about employees and customers. But does it really matter for design? I mean, diversity of thought always makes for better products, sure — but is it ever going to be important enough to be life or death?
I’m positive it is. “Yes, I’m positive” – the three most overused words since the 2020 outbreak of the Covid pandemic.
With shaky hands, I turned to my wife and showed her the tiny little rectangle with the two lines that matched hers.
We both had Covid. We both had underlying conditions. And we were both black, which makes us statistically twice as likely to be hospitalised with Covid, according to the Mayo Clinic.
As I lay there, barely able to pull air into my lungs, my wife’s hands shook as she struggled to fit the pulse oximeter onto my finger. “I can’t take you to the hospital for COVID treatment unless your oxygen reads less than 93%,” she mumbled.
A bunch of expletives flew from her lips as she took it off one finger and placed it onto another, over and over, trying to find a reading. There was none.
She took the device off my hand and tried it on hers – 99%. It worked, just not for me. A sob choked out of her lips as she whispered, “It’s not fair.”
My wife has always had complicated feelings about her biracial heritage. Hovering somewhere between not quite dark enough to be ‘black’, and not quite pale enough to pass for ‘white’, her identity and origin are always questioned whenever she enters a room.
How many drops of blood does it take to be considered black? For our marriage, it never mattered. But as I lay there, barely able to breathe, unable to obtain a pulse ox reading, we both felt the immense distance, this chasm between us – all down to nary but a few drops of blood separating us. ONE SIZE DOESN’T FIT ALL
Pulse oximeters were widely adopted in standard medical practice in the late 1980s. They are a non-invasive way to measure oxygen, using light absorption. The LED in the device sends light through the patient’s finger and then calculates their oxygenation, by figuring out how much of the light was absorbed by haemoglobin in the blood.
For people with darker skin – especially those of Black, Asian and Hispanic descent – skin pigmentation also absorbs this light, resulting in inaccurate readings.
For these patients, incorrect readings (which often report oxygen levels as being higher than they actually are) have prevented them from receiving critical oxygen support in Covid wards.
Many people have died as a result of this systemic exclusion. All because the original design of the device was tested on primarily white patients. And that comes as no surprise when you consider that the desegregation of the US-wide hospital system didn’t pass until 1964.
So, as I lay there listening to my lungs rattling against my ribcage, my blood ran cold not from lack of oxygen, but from the knowledge that it was a lack of diversity – of DEI – that could inevitably bring about my downfall.
I thought of all the social media posts I’d been bombarded with over the past two years. All of it sounding like lip service, because I know and deeply understand how slowly mindsets shift. The pulse ox was designed when civil rights was in its infancy – and this is just one example of 50 years of systemic inequality having the potential to literally kill someone. But in this case, not just anyone. Me.
DIVERSITY MATTERS
It’s DEI or die, right? As a black, gay, nonbinary person, I have many intersections when navigating predominantly white engineering spaces. And I’m often reminded that when one considers diversity, it is about so much more than skin color. There’s the diversity of gender – not just men and
Not recognising what makes each of us unique can have a drastic impact on how we navigate the world
women, but non-binary and trans humans as well. Additionally, there’s diversity of mind – also called neurodivergence – which includes members of our communities struggling to disguise their autism, their ADHD. You can’t forget that one coworker who always has the answers to every problem but can’t seem to figure out how to convert a word doc to a PDF – that may be diversity of age. Finally, I’d also like to bring attention to our colleagues with disabilities, because making and creating spaces that are accessible make them safer and better for all.
All of this diversity gives us a magnanimous, wide-ranging horizon as we go forward creating new companies and new technologies. I think of the excitement sparked by the first iPod; the grimace (but also curiousity) generated by the Croc sandal; and the wonder that the first VR headsets sparked.
Those designs were novel and exciting – first-of-their-kind wonders that left us all hungering and hopeful for more. But, in my opinion, the single greatest attribute of a design that is determined to make an impact is that it is inclusive. For everyone and anyone at all intersections – no matter our race, gender, body shape or size, disability, age, neurodivergence or any combination thereof.
When it comes to engineering design, DEI is truly life or death. We are shaped by our environment – impacted by our diverse intersections – and this in turn shapes the products we produce.
Some would argue that recognising the physical or mental differences between us is in itself discriminatory, but not recognising and appreciating what makes each of us unique can have drastic consequences down to the healthcare we are given, on how we navigate the world.
ABOUT THE AUTHOR: Contributor SJ is a metal additive engineer, aka THEE Hottie of Metal Printing. SJ’s work involves providing additive manufacturing solutions and #3dprinting of metal parts to help create a decarbonised world.

The means of manufacture has always had bearing on design, writes Matt Batchelor. For all its benefits in prototyping, 3D printing can disconnect designers from the end process and its overall impact
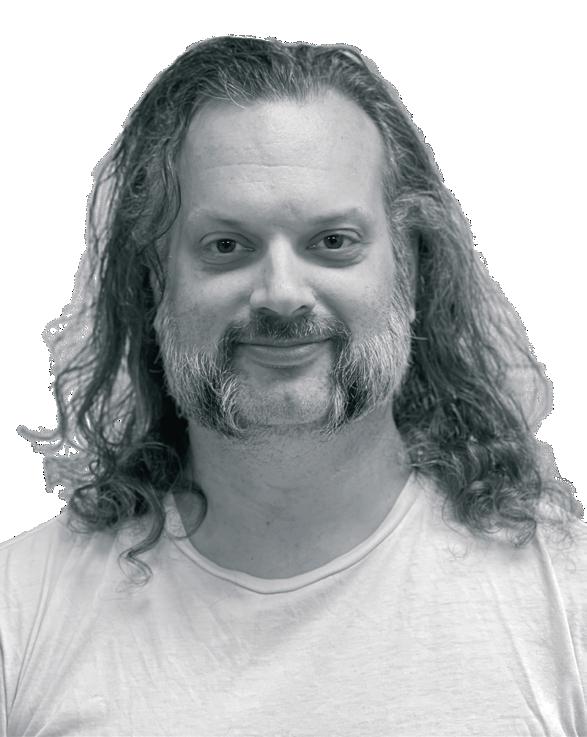
For most of my career, there has been pressure to prototype digitally, driven by desire to cut time to market and R&D expenditure.
When I worked at Fiat, a new virtual reality (VR) cave, bought for a rumoured sixdigits in 2007/8, was still only as expensive as one of tens of prototype tractors built for mechanical testing. But in most cases physical prototypes crept back in, either to test hard-to-model jobs like harness and hose routing, or else to enable us to mock things up in cardboard, full-size, as real ‘rapid prototypes’.
In the broader industry, the twentieth century succession of design-isms gave way to the generic organic-ergonomic-smoothgoodgrips-sex-toy-potato school of styling, made possible by the wide adoption of CAD/CAM and the move towards making everything in lightweight, low-maintenance, no-finishing-ops injection-moulded plastic, typically in low-wage countries.
Somewhere along the way, it seems, many of us forgot the link between material, process and form that made many classic industrial designs elegant, appropriate and, crucially for a mass-produced product, efficient to make.
You couldn’t produce the Blueberry G3 iMac in anything other than injectionmoulded plastics, in the same way as if you started to make a car front wing with a sheet of aluminium and an English roller, it would come out looking like an E-type or Ferrari 250.
A handsome iron casting, drop forging, ceramic insulator or hardwood table leg can only ever look like what it is, by letting it be what the material and process will permit.
A REFRESHING CHANGE
Fast-forward to 2022, and it was refreshing to walk around the New Designers this year, looking at tables full of FDM prototypes.
Low-cost, reliable FDM machines and maybe the end of ‘digital’ being a novelty means that cost and lack of workshop machinery are no longer a barrier to a designer making quite a sophisticated ‘looks-like’ or ‘works-like’ model. The trouble is that these are rarely ‘made-like’ models; but why is that a problem?
On a minor level, things like less- controlled tolerancing, shrinkage, warpage and non-precision surface finishes compared to moulded or machined parts mean that even with state-of-the-art bureau machines, we’ve often had to debug the AM prototyping process before we debug the design.
The real problem is that design is not just the shape of an object, or even just its physical properties. In the design and engineering professions, we know about anthropogenic climate change, the many impacts of resource extraction, processing and disposal, and the impossibility of infinite consumption on a demonstrably finite lump of rock.
As a result, there is a consensus that we should be responsible for at least minimising or even eliminating the impact of the things around us.
I’ve heard it said that 95% of the cost of an object is determined in the first 5% of the design process. I would argue that the same is true of the broader resource cost of that object in its existence, use and eventual disposal.
INFORMATION LOSS
In the prototyping phase, 3D printers need an explicitly defined 3D shape to print, which means we lose some information about the material and the energy needed to turn it into an object.
Standing in an iron foundry, the enormous amount of thermal energy going into melting the iron is obvious. But then the complexity of shape that sand casting provides allows objects to be made more efficiently of one or several castings — rather than, say, a complex welded assembly or machining job.
Extrusions are an amazingly efficient way to get a complex functional cross-section, If we are to meet the ultimate design requirement of making sure that humans can continue to live without causing our own extinction, we need to be careful about the tools we use and when we use them
provided that complexity can be in two dimensions.
Many early cultures independently learned how wood can be split, steam-bent and shaped to make high-performance sailing ships. A Viking ship on a close reach looks a thousand years more advanced in its speed and efficiency than a Maersk E-Class forcing its way through the water.
At Instrument, we’re working on a sustainability concept that involves some very involved metal forming to replace plastics.
And while our SLA printer has let us iterate a forming process very quickly by printing tool inserts, we could not make any progress if we weren’t working on a material of the right grade and gauge to make sure it all works in practice. By prototyping the process as well as the part, you naturally tend to design for the minimum of wasted material, energy or complexity; which details work and which can be forgotten. It may be financially convenient to have a little shape-it-all box in the corner, but if we are to meet the ultimate design requirement of not making ourselves extinct, we need to think carefully about which design tools we use and when. 3D printing is amazing, but I sometimes worry that it belongs to the bad old ways.
ABOUT THE AUTHOR: Matt Batchelor is an industrial and engineering designer, and co-owner of Instrument Industries, a London-based design and manufacturing firm. He tolerates the company’s SLA machine, but wishes it was a Bridgeport. www.instrument.industries
VISUAL DESIGN GUIDE SENNHEISER MOMENTUM 4
Focusing on sound quality, comfort and ease of use, the new Sennheiser Momentum 4 wireless headphones deliver an array of new technologies, neatly packaged in a minimalist lightweight design
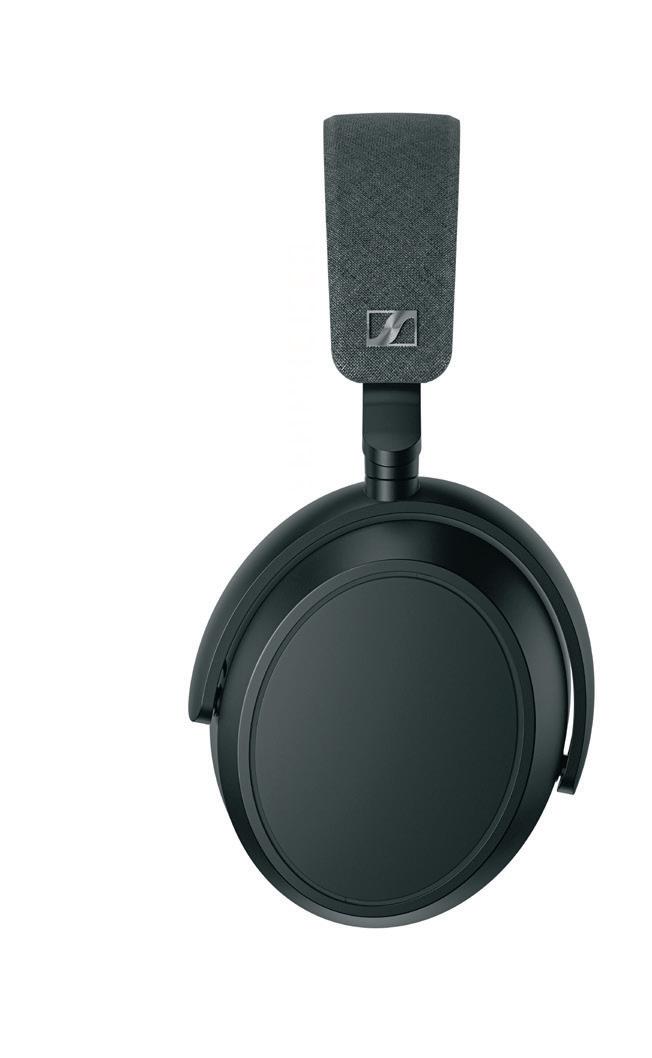

INVISIBLE MOVEMENT
A rotary axis above the clamp holding the ear cups is cylindrical in shape, allowing the slider to disappear into the headband. In this way, a uniform profile is maintained, regardless of how the user modifies the headband’s length or rotates the ear cups
SOFT AS CLOUDS
Cushioned ear pads ensure long-lasting comfort. The low-friction hinge mechanism adjusts to give a great fit without placing excess pressure on the head
UNLIMITED LISTENING
LED lights display battery level. Should the battery run out, typically after some 60 hours of use, an audio cable is provided for wired listening
ALL ABOUT BALANCE
The dent in the centre of the headband is intended to account for users sensitive to pressure on the top of their head, with the design ensuring even weight distribution
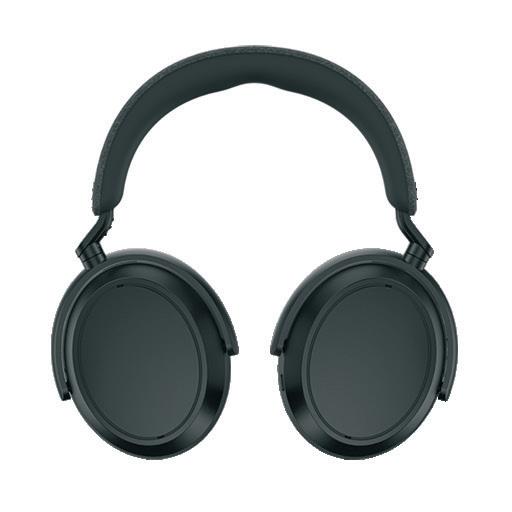
FULL IMMERSION
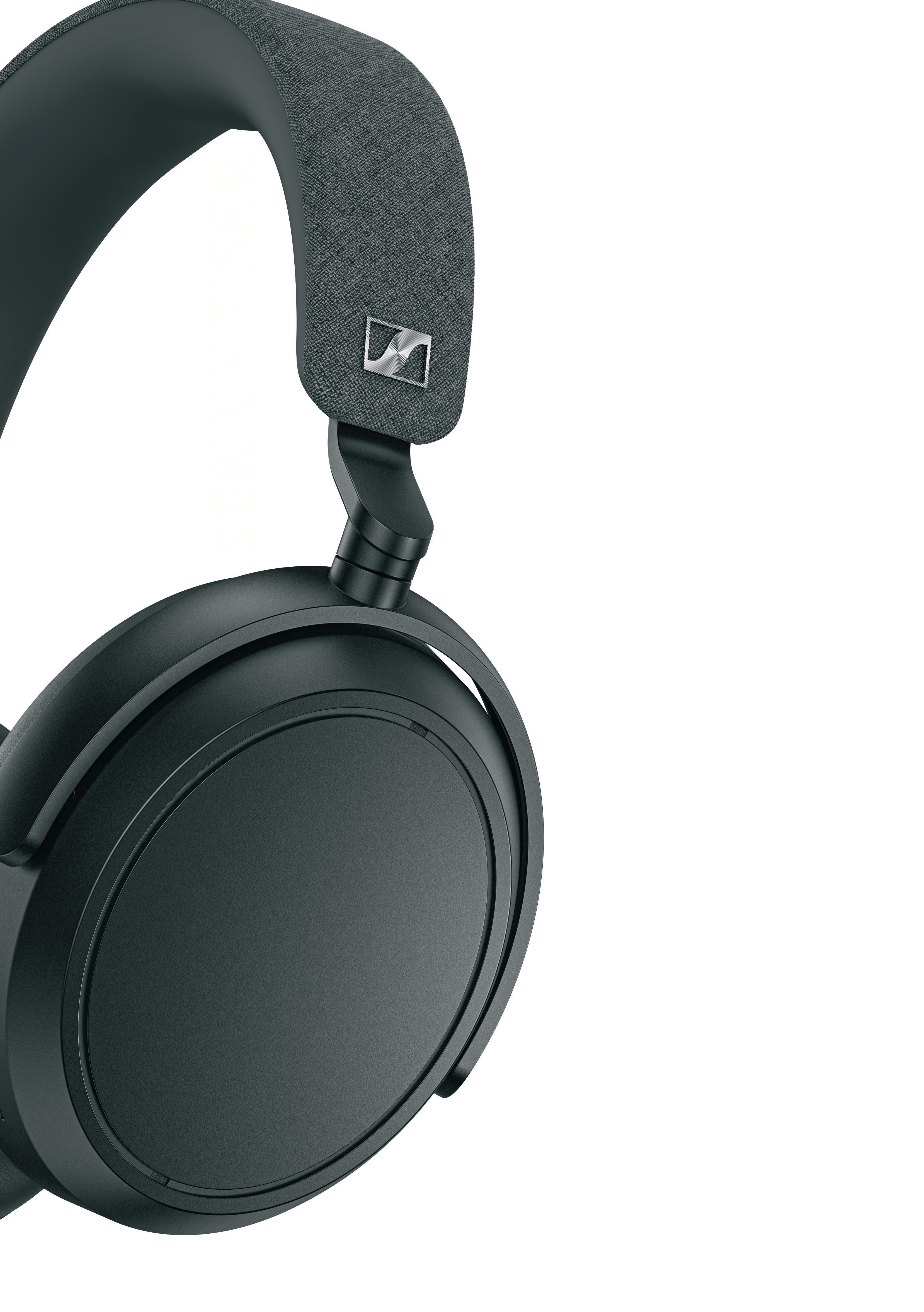
The headphones feature dual sets of outer and inner noise cancellation microphones, helping to keep out unwanted sound
PRICE AND AVAILABILITY Momentum 4 is available from Sennheiser, RRP £299.99 www.sennheiser.com
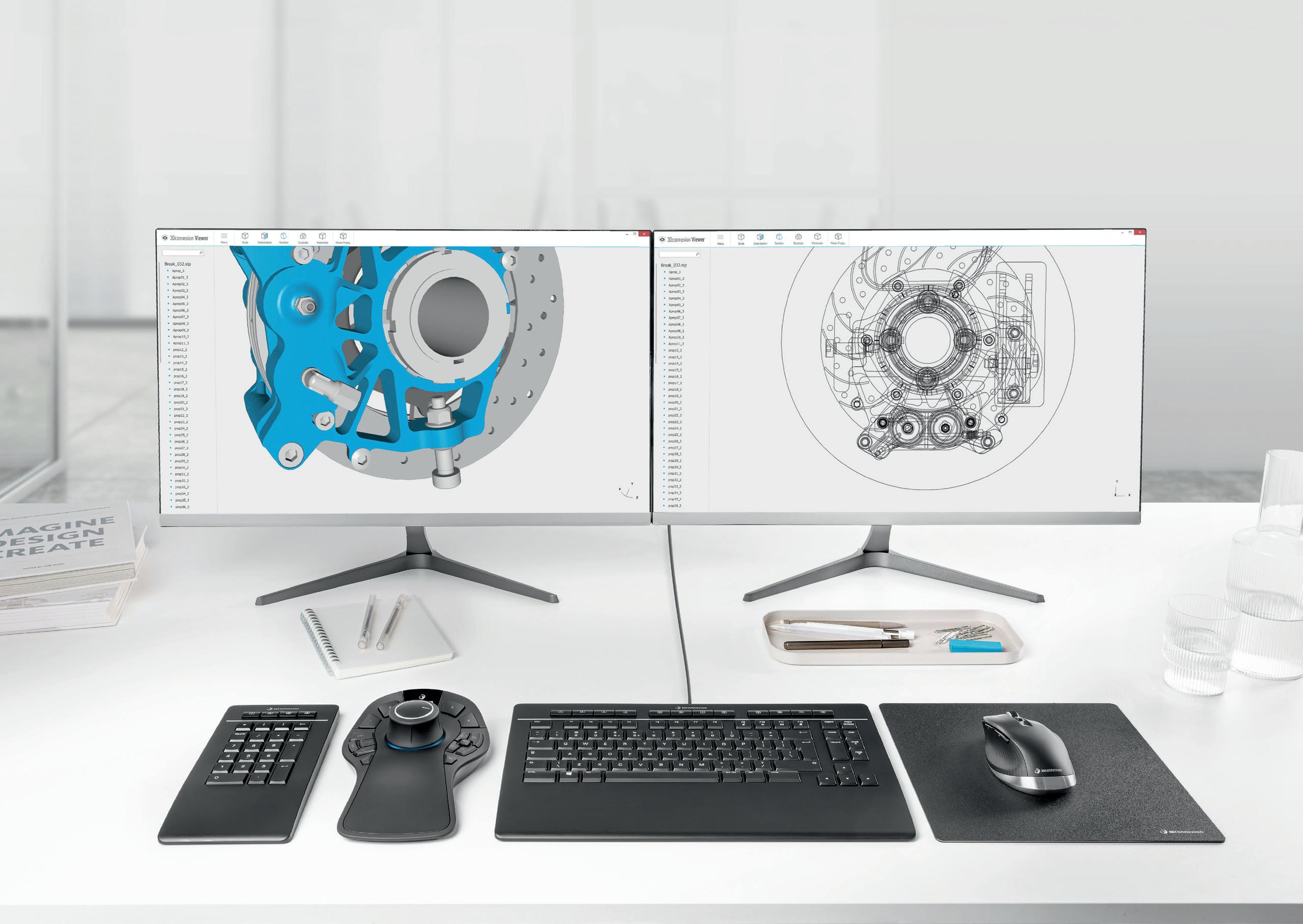

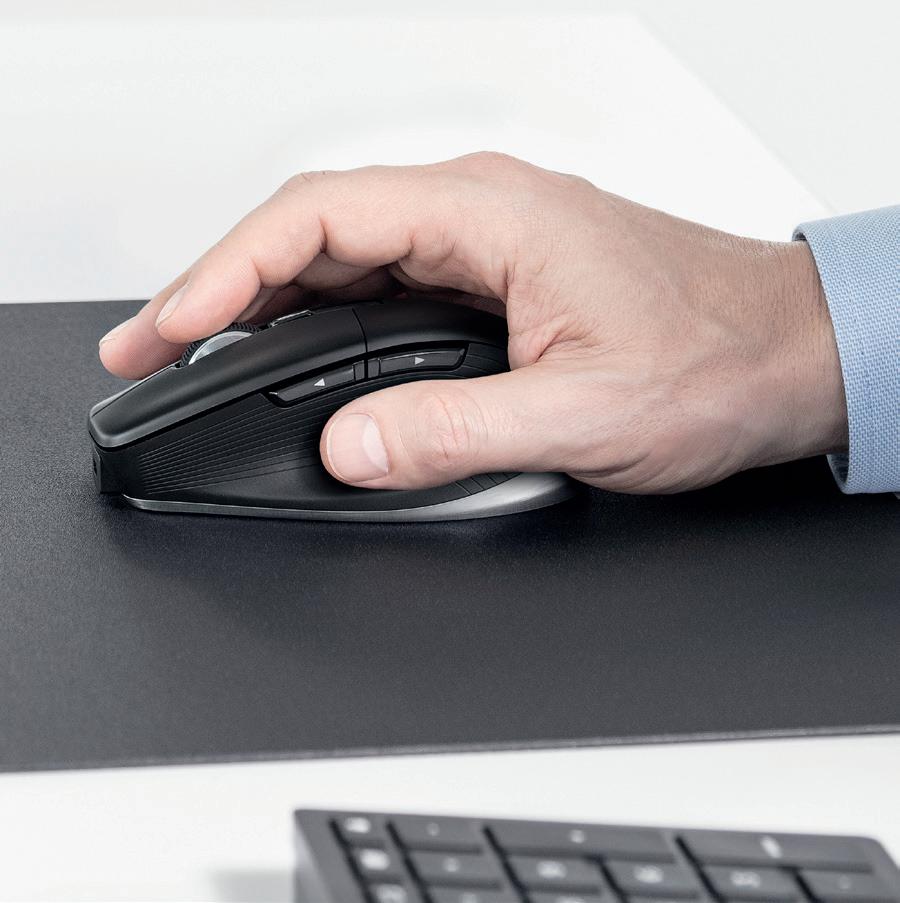



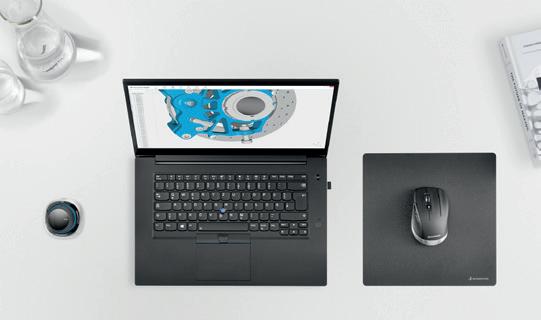
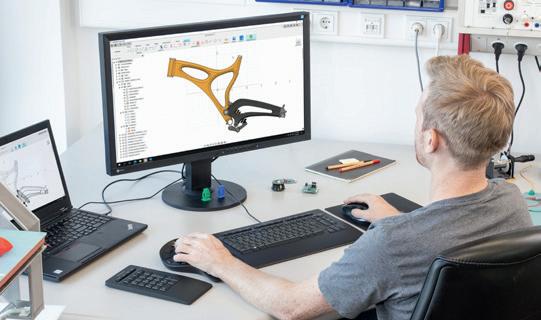
DREAM MACHINE
» Inspired by cafe racers and electric violins, the Arc Vector promises a truly unique experience for motorcycle enthusiasts looking for a high-end, all-electric ride. DEVELOP3D went behind the scenes to hear about the motorcycle’s design from Arc Vehicles CEO Mark Truman
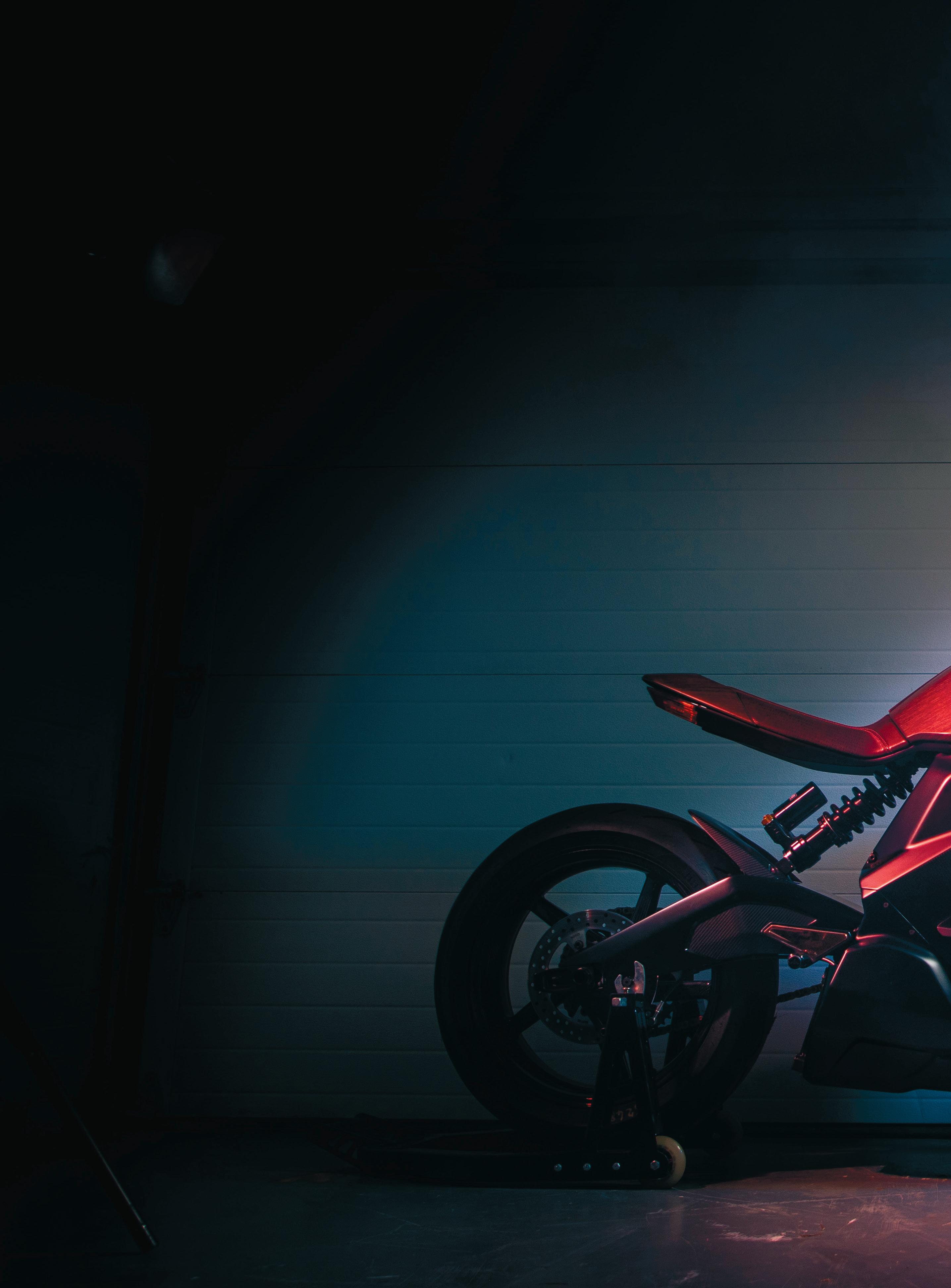
DREAM MACHINE
Every Arc Vector is handcrafted in the UK to the individual owner’s requirements
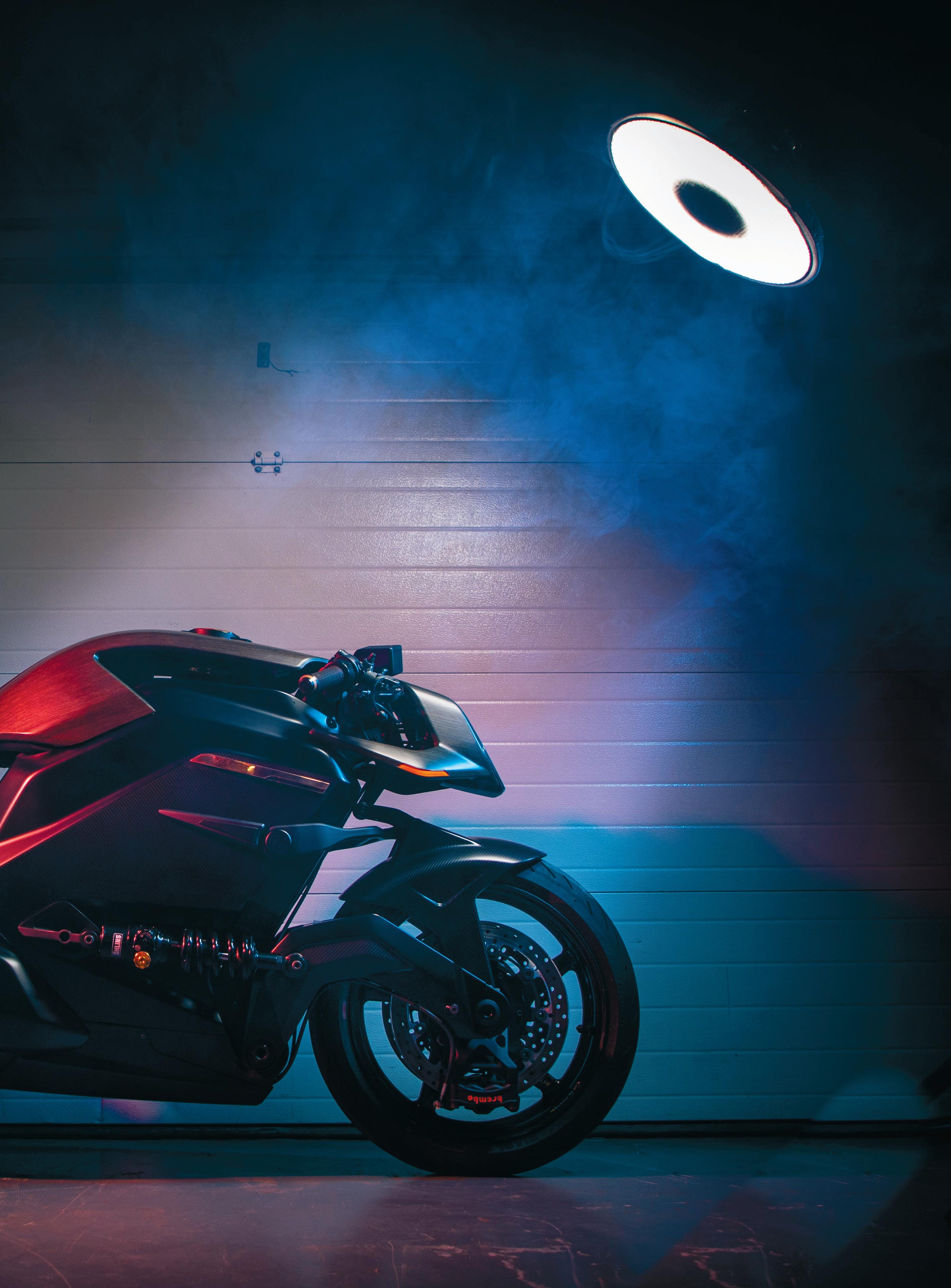
It takes a very special motorbike to impress former British Superbike Championship runnerup and MotoGP rider James Ellison. In the Arc Vector, it looks like he has found that bike.
Over the summer of 2022, Ellison has been working with the team at Arc Vehicles, a spin-off from automotive company Jaguar Land Rover (JLR), to finesse the final spring and damper settings on the Vector’s innovative suspension system.
He certainly enjoyed the experience. “The way the machine carves up corners is incredible. Vector is definitely big on ‘grin factor’,” he says. “It’s just so different to anything else you will ride. I’ve been really surprised by the agility. The bike changes direction like a much smaller bike due to the steep steering angle it can run. This means the bike can be flicked from side to side with little effort.”
That glowing praise is all the more striking when you consider that the Arc Vector is the world’s first fully electric neo-cafe racer. And the team that designed it, led by Arc CEO Mark Truman, is no less infatuated with their creation.
Truman, a self-confessed motorcycle fanatic, regularly takes the bike out himself and jumped at the chance to ride alongside Ellison, to hone the final settings before the Vector goes into production. “Riding the Vector alongside James has been fantastic,” he says. “His perception and feeling for the slightest change to the settings are second to none and his experience goes without saying.”
CAFE RACERS AND ELECTRIC VIOLINS
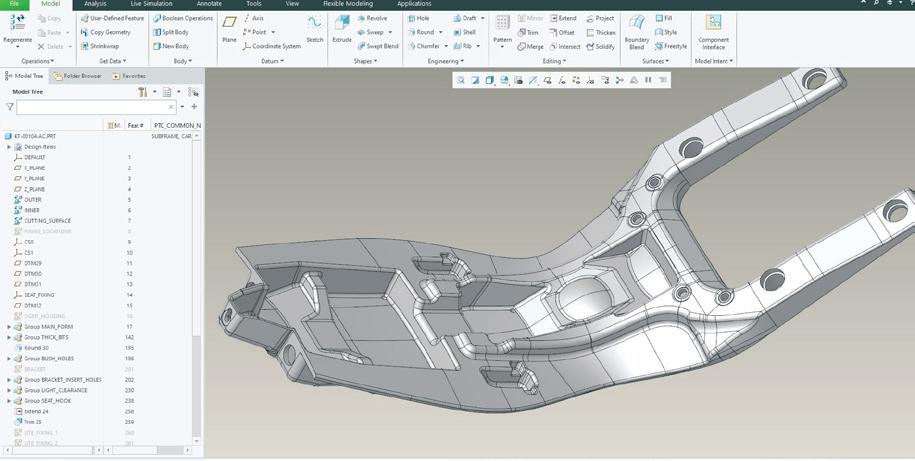
Arc Vehicles was spun out of JLR in 2017. Truman, who previously led JLR’s White Space innovation team, developed an electric motorbike prototype during his time there. Management were so excited by the idea, that they happily gave their backing to the spin-out and to Truman’s ambition to build a market leader in electric recreational vehicles.
What Truman and his team also have is the freedom to work from first principles. “We’re very lucky in that our products are more at the premium end of the market, so that means we are able to deliver a vehicle from scratch each time and develop innovative products that really break the mould, rather than working from carry-over content from previous vehicles to save time and costs,” he says.
“So we can go right back to basics: ‘What are the use cases here? What would be the perfect product to fit those use cases?’ From there, we try to work in a way that is as unrestrained as possible, carrying that concept right through into production so that the final product is very much a representation of the idea we had right at the start of the project.” So what was that idea for the Arc Vector? The answer is two-fold. First, the team wanted to create a very futuristic motorcycle, with retro flourishes. “We were thinking in terms of how a cafe racer would look, if the term ‘cafe racer’ was first coined ten years from now,” Truman says.
Second, they were inspired by the appearance of electric violins. “We found some beautiful pictures of instruments that had everything in place that they needed to make a beautiful sound, but where anything that wasn’t required had been taken away. We thought they were stunning and that seemed a really nice philosophy for our product, as well as other products from us in the future.”
To take these eclectic concepts to a production-ready product, the initial ideation process at Arc is very manual, but quickly moves into PTC Creo for 3D CAD. Arc has used PTC Creo since Day One of its existence, supported by Cambridge-based Root Solutions, part of the worldwide PDSVision group and PTC’s longest standing Platinum Partner in the UK.
Initial ideation involves a lot of “whiteboards, blackboards, Post-it notes and mind maps”, says Truman, then 2D sketches, Illustrator, Photoshop and so on. A lot of 3D printing goes on, too, in an effort to move away from the traditional clay modelling processes typically associated with designing this kind of product. Rapid prototyping using 3D printing, Truman explains, makes it easier for designers and engineers to be working concurrently.
But work in Creo starts early, he says. “We’ll have designers working on surfacing in Creo and engineers using it to work on parts pretty early on, figuring out how parts will fix to the product, how we get that quality right, the gapping right and so on. We want to be thinking about all of that as early and as upfront as we possibly can.”
He and his team wanted to avoid a situation where designers create something and then throw it over the fence to engineers, who then have to try to make it work.
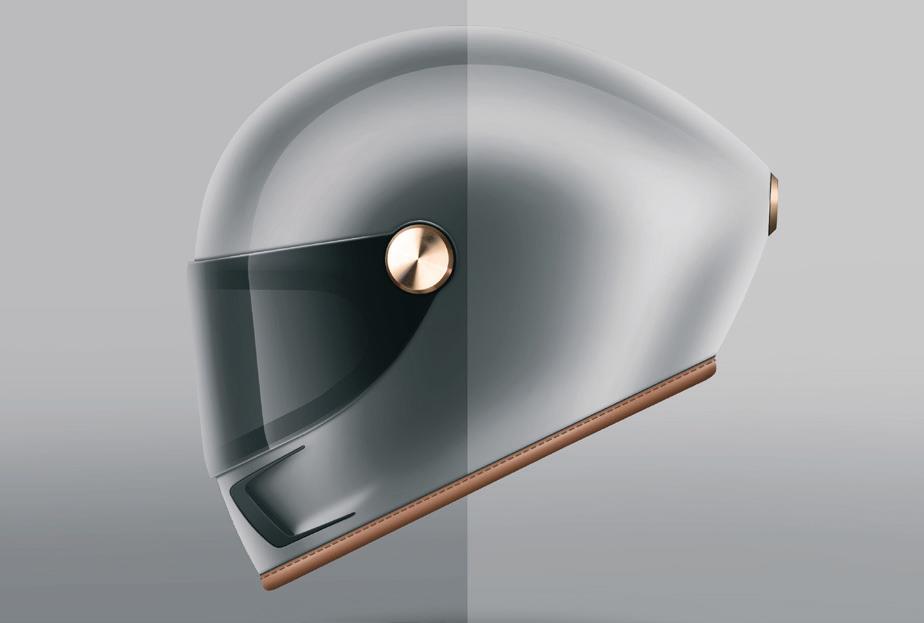
1
2
We try to work in a way that is as unrestrained as possible, so that the final product very much represents the idea that we had right at the start of the project ’’
●1 Arc Vehicles uses PTC Creo for 3D CAD, including for the design of this seat bracket for the Arc Vector ● 2 The futuristic Arc Zenith helmet, developed in partnership with helmet specialist Hedon, was also designed and modelled in Creo ● 3 FEA capabilities in Creo enabled the team to judge the likely performance of a proposed sidepanel design for the Arc Vector
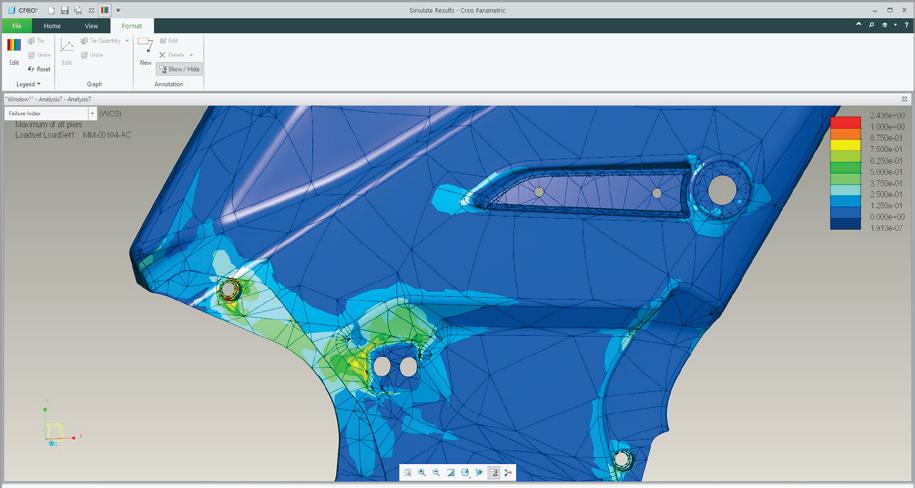
The Arc Vector is the world’s first fully electric neocafe racer

4
“That often results in a very argumentative process. The designer gets engineering back that isn’t quite the same as what they designed. Or engineers get stuck with trying to figure out something that’s just not possible or that’s going to be too expensive to achieve.”
Collaboration tools in Creo support that process, helping designers and engineers to share ideas easily and keeping all relevant, up-to-date information in one software package. The team at Arc is also using Creo’s generative design and design for additive manufacturing (DfAM) capabilities more and more, he says. They’ve given the team the ability to think more creatively and to assess manufacturing methods based on different attributes such as cost or weight, he says.
“We do a lot of reverse engineering on our early prototypes, to decide how we could create individual parts better. When you first set out, you’re probably not as concerned about costs, but when you start getting to the end of the process, you can really start to understand how much things might cost and then make changes,” he explains.
“So at that point, there’s a lot of scanning that goes on of those initial parts and then reverse-engineering the CAD that we’ve created, with reference to generative design, which informs us of improvements we might make. It’s fantastic to have that ability to revisit and refine with a high degree of accuracy.”
Since around 50% of the manufacture of the Arc Vector is outsourced to specialists, these collaborative features are also a help in working with suppliers. “Obviously we don’t really share the full bike with anybody in the outside world, but Creo helps us to share relevant 3D CAD information and drawings with the companies we work with.

5
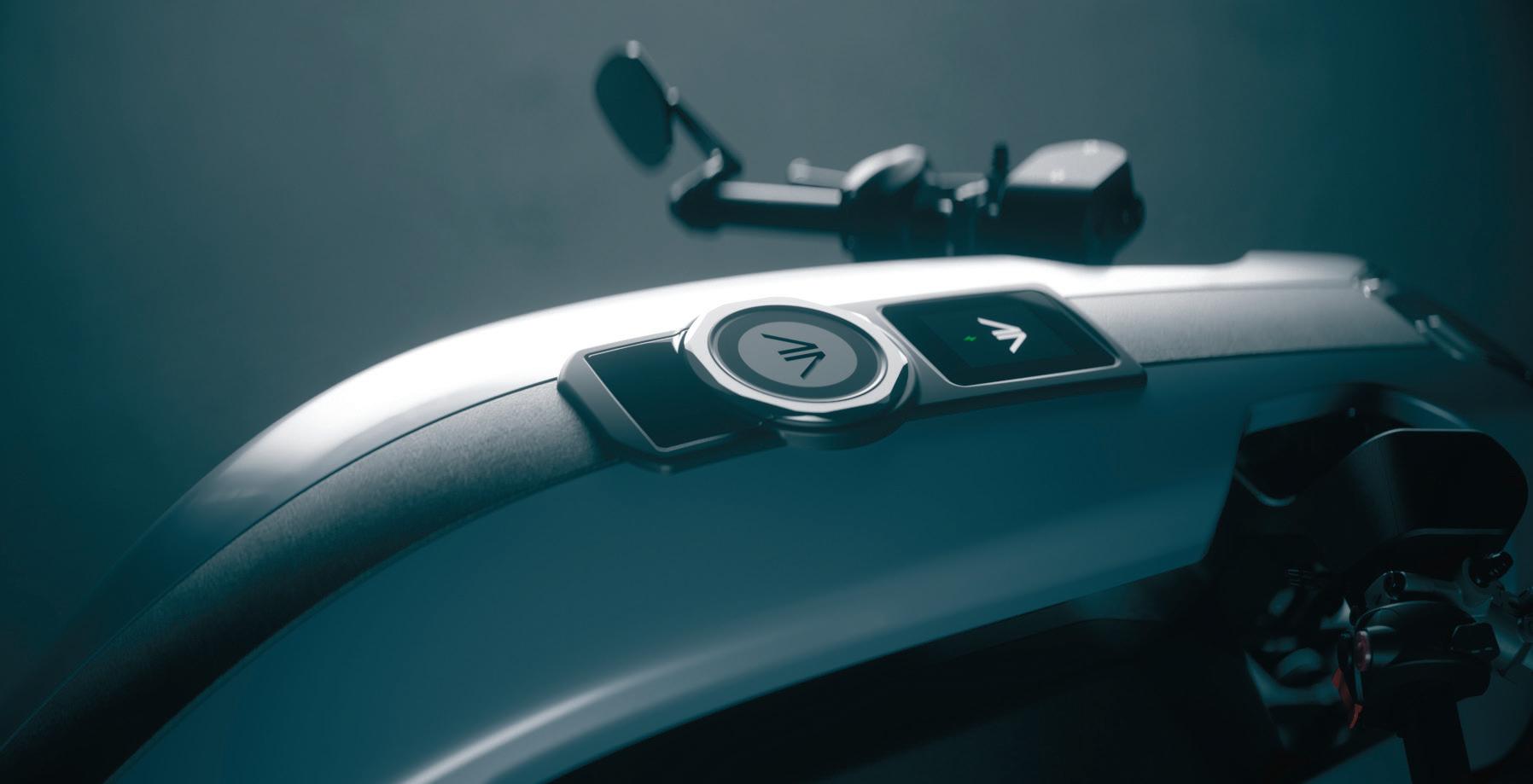
ACCELERATING INNOVATION
All this has led to a final design that can boast some truly innovative features. The Arc Vector utilises a carbon front-swing arm and hub centre steering, resulting in a bike that feels similar to one that uses front forks, but offers increased stiffness and the ability to run on steeper steering angles. With hub centre steering, for example, the Vector runs a 20-degree rake angle.
The company is also looking to get great feedback from 10 customers who will participate in a programme to help develop the Arc’s human-machine interface (HMI) system. Each participant will receive an Angel Edition (AE) Vector motorcycle and engage with a testing programme to try out prototype versions of the HMI system on tracks in the UK and US. Their direct feedback will be incorporated into the system until it is ready for the open road. According to Truman, it’s not just the “ultimate peek behind the curtain” for participants, but also a way to create a system that will boost enjoyment and safety of the product for future owners.
And since this is a premium product, those owners are given extensive opportunities to customise their Vector, resulting in a vehicle that is truly bespoke. Invited to Arc’s commissioning suite at its Coventry headquarters, they can choose between a wide range of finishes and extra features.
On top of this, an augmented reality (AR) experience will enable them to ‘see’ their Vector, parked in their own garage or on their front drive, both before and after those bespoke touches are added. This AR application was developed for Arc by Root Solutions.
“We are putting all our best creative thinking into ensuring that buying, owning and riding an Arc Vector will be a truly unique experience for owners — something very special indeed,” Truman promises.
●4 The Arc Vector’s charge port delivers a 40-minute charging time from flat ● 5 Arc Vehicles CEO Mark Truman ● 6 The front end of the Arc Vector, featuring its innovative hubcentre steering
6
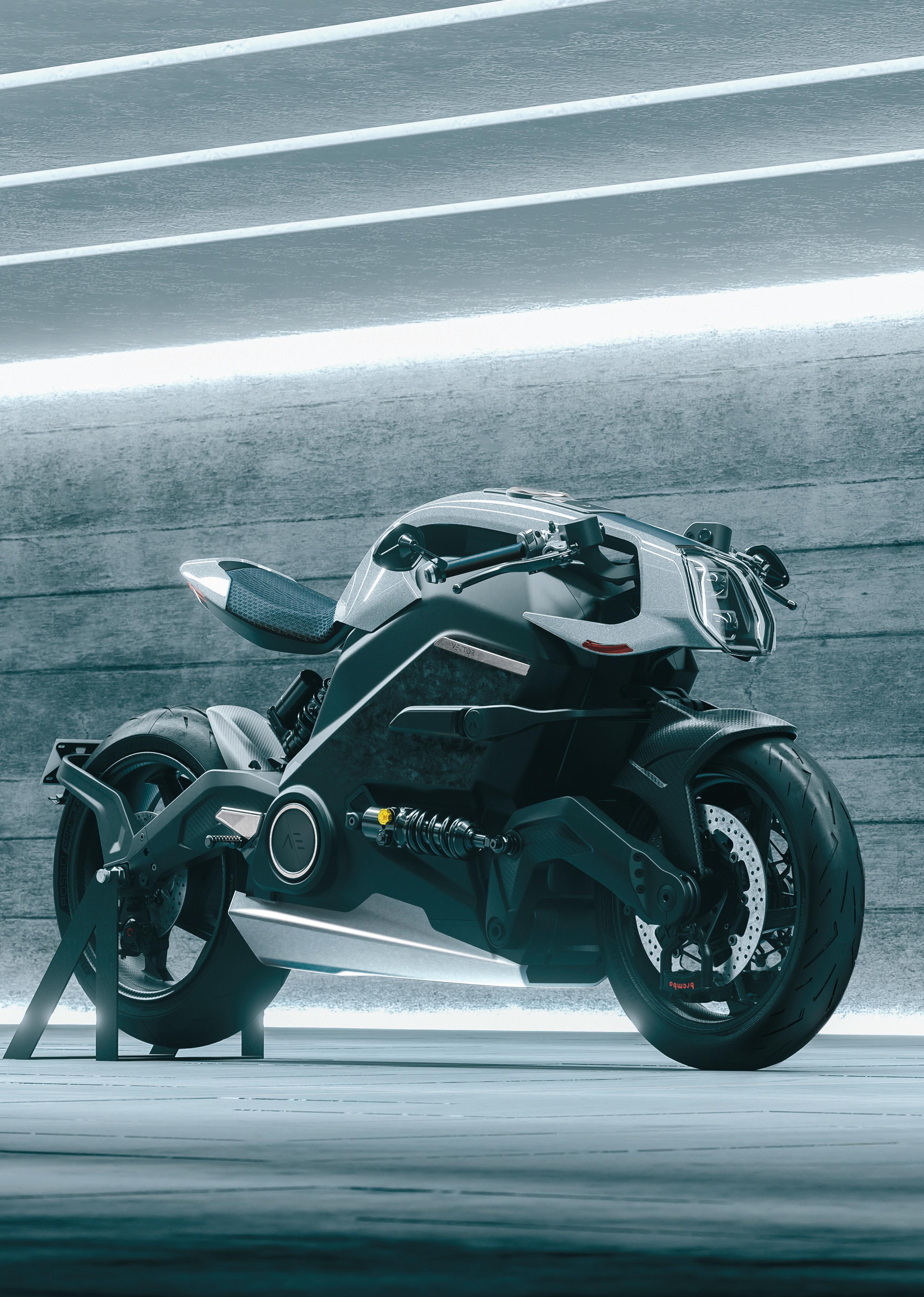