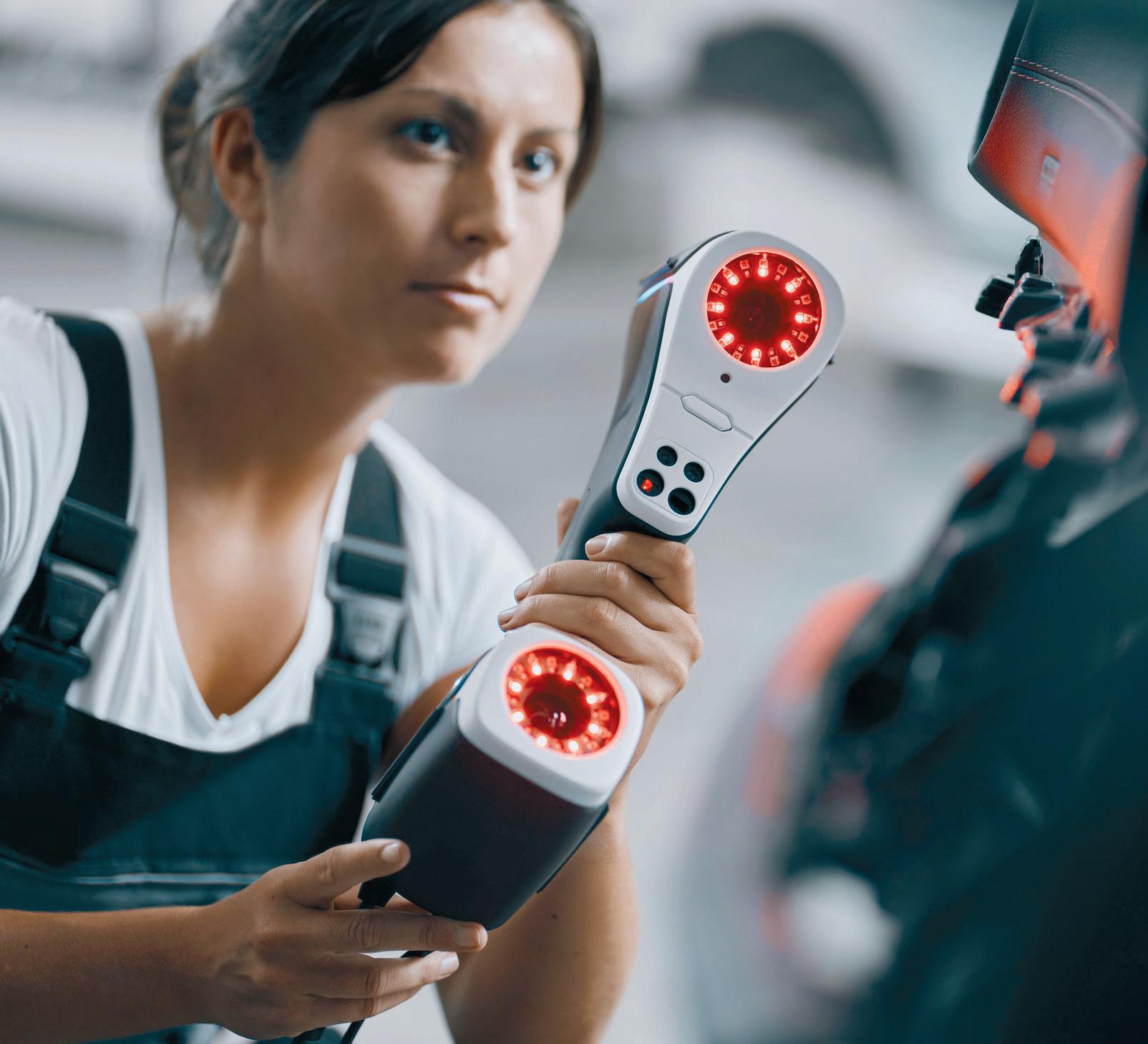
16 minute read
3D scanner round-up
BEST 3D SCANNERS
for the DESIGN STUDIO
» Buyer beware: choosing the right 3D scanner can be hard. There are lots of models available, at lots of price points. Performance varies widely, as does suitability for specific use cases. Claudia Schergna takes a look at some of the best of the bunch, with the needs of product designers firmly in mind
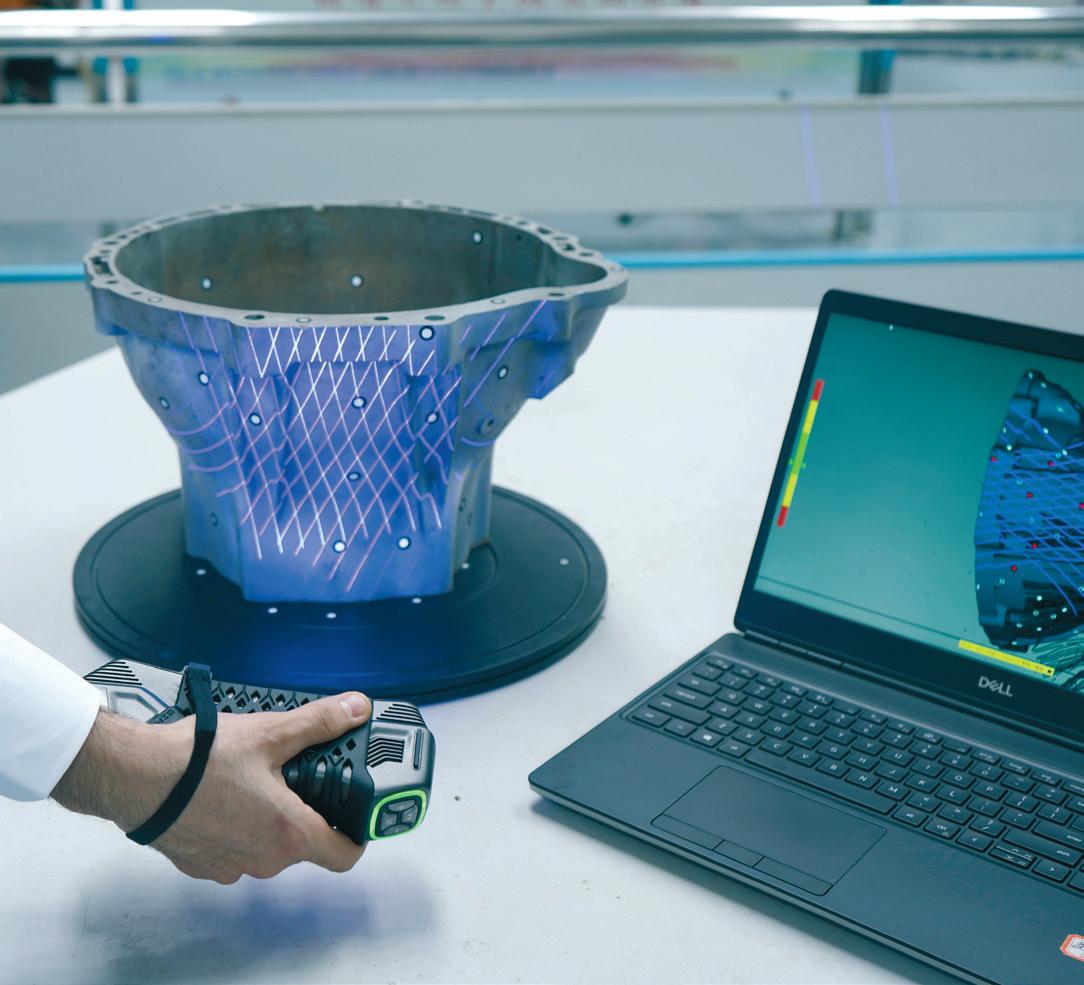
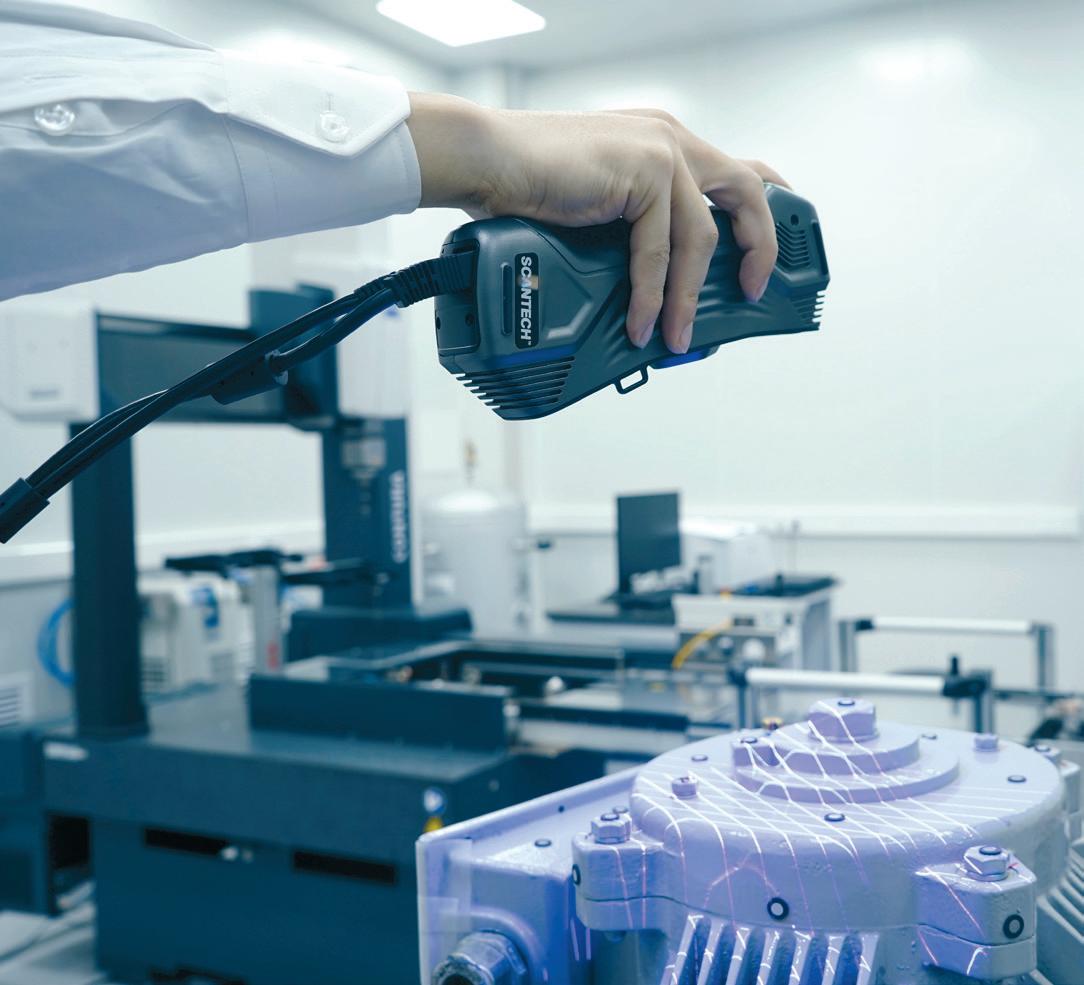

T
he transformative impact that 3D scanners have had on manufacturing and design in recent years can’t be overstated. Whether they use light, laser or photogrammetry, these devices offer a serious helping hand when it comes to reverse engineering and rapid prototyping tasks. Along the way, they have revolutionised workflows. But these days, you don’t need to work for a major design consultancy or multinational engineering giant to have access to some outstanding 3D scanning technology. The technology has gone mass-market, and there are now options to suit every budget. The huge variety can make it really challenging to choose the right tool for your trade. Here, we’ve showcased some of the best models on the market, taking into consideration such features as accuracy, resolution, ease of use, weight and price-performance ratio.
1
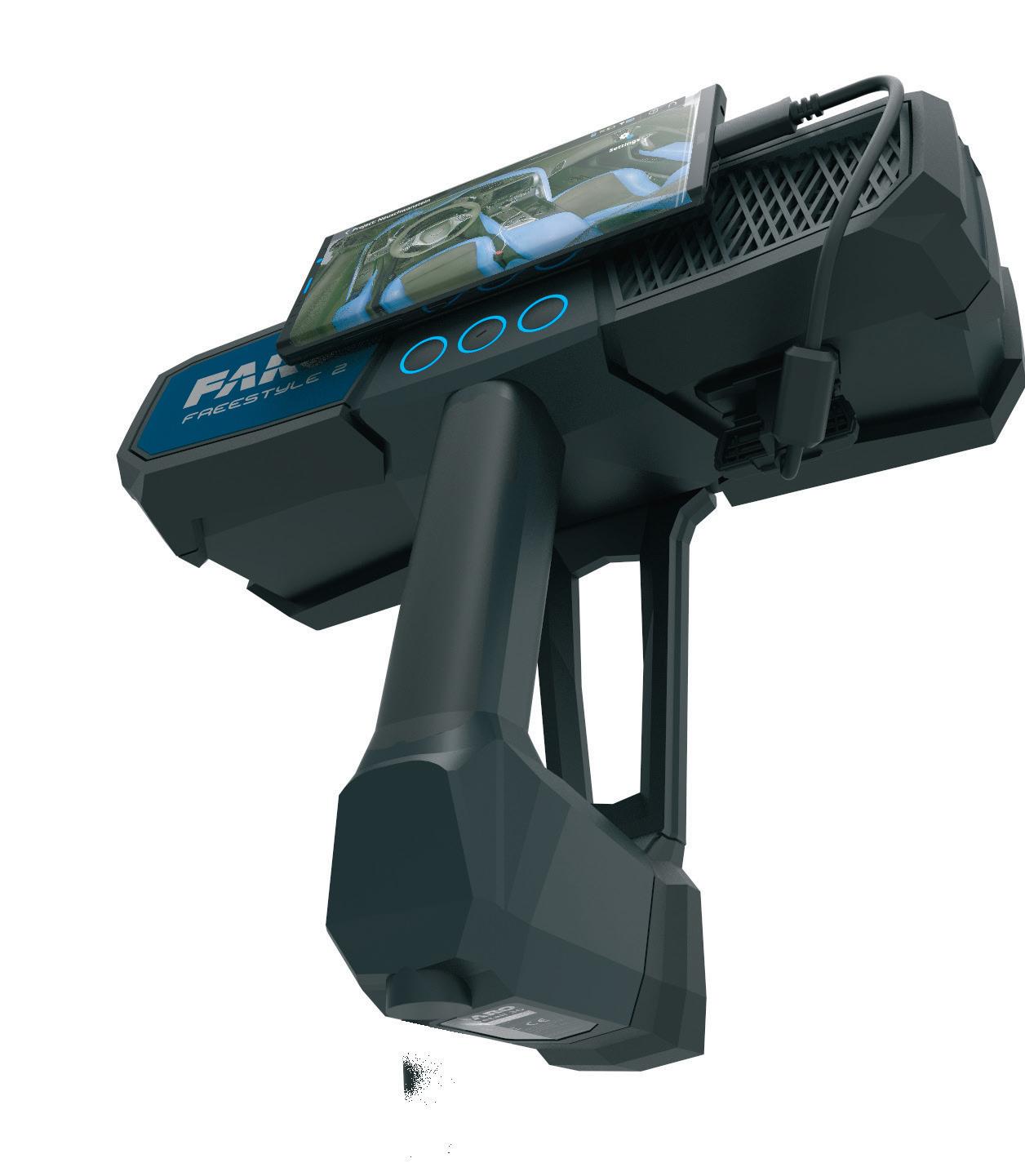
EINSCAN PROHD SHINING 3D
The EinScan proHD is a versatile, accessible physical form capture technology. With a weight of 1.13kg, it can be operated with a single hand, or combined with a dedicated tripod. The device offers two sub-modes: Rapid and HD, with the former providing faster scanning, and the latter providing a higher level of detail. Thanks to this device’s structured light projection technology, it is capable of scanning dark and casting metal surfaces at 3,000,000 points/second.

2
FREESTYLE 2 FARO
Originally developed for forensic investigators and crime scene documentation, features of Freestyle 2 also make it useful for product development. The scanner’s infrared laser projects a 100 x 100 grid of invisible dots onto the target and is interpreted by two cameras built into the T-shaped casing of the device. It performs strongly both indoors and outdoors, including in overcast conditions and complete darkness.
3
POLYGA H3 POLYGA
Powered by two industrial-grade cameras at a high speed of 700 frames per second, the Polyga H3 can scan up to 1.5 million points per scan using a structured light technology. Marketed as Polyga’s first ‘point and shoot’ system, it doesn’t require calibration. The H3 is powered by LMI Technologies’ FlexScan3D, the same 3D scanning software that all Polyga’s stationary 3D scanners run on.

» Price: £££££
www.polyga.com
4
KSCAN MAGIC SCANTECH
Released in 2021, this handheld unit features a built-in photogrammetry capability, 22 crossed blue lasers, a single laser for deep pockets, 7 parallel lines for fine detail scanning on small parts, and 12 infrared parallel lasers specifically aimed at large parts.
KScan Magic can be fitted with a portable CMM probe, with point repeatability of 0.03mm, allowing users to measure holes, hidden points and hard-to-access features.

5
HANDYSCAN 3D SILVER SERIES CREAFORM
The HandySCAN Silver Series comes in two models: the 307 and the 700. The 307 offers accuracy down to 0.04mm and a resolution of 0.1 mm. The 700 offers accuracy down to 0.03mm and resolution of 0.05mm. HandyScan 3D Silver features seven red laser crosses, which allow scanning in most light situations and of most materials, including dark and reflective ones. Thanks to in-built optical reflectors, it can triangulate positions, so there is no need for external tracking or targets.
6
GO!SCAN SPARK 3D CREAFORM
Go!Scan is Creaform’s top product in the category of handheld scanners aimed at professional users. The ergonomic design features four inline cameras for faster 3D scanning and colour acquisition. Dynamic referencing technology allows users to hold an object with positioning targets on it and move it around during scanning. Files are captured using 99 white-light scanning lines.
» Price: £££££
www.creaform3d.com

7
HANDYSCAN 3D BLACK SERIES CREAFORM
HandyScan 3D Black Series scanners use a laser triangulation technology with nine blue lasers in the standard model and 11 in the elite model. Weighing a featherweight 940g, the scanners have a resolution of 0.025mm. Like the Go!Scan Spark, they come equipped with Creaform’s own VXelements software to produce CAD-ready data.
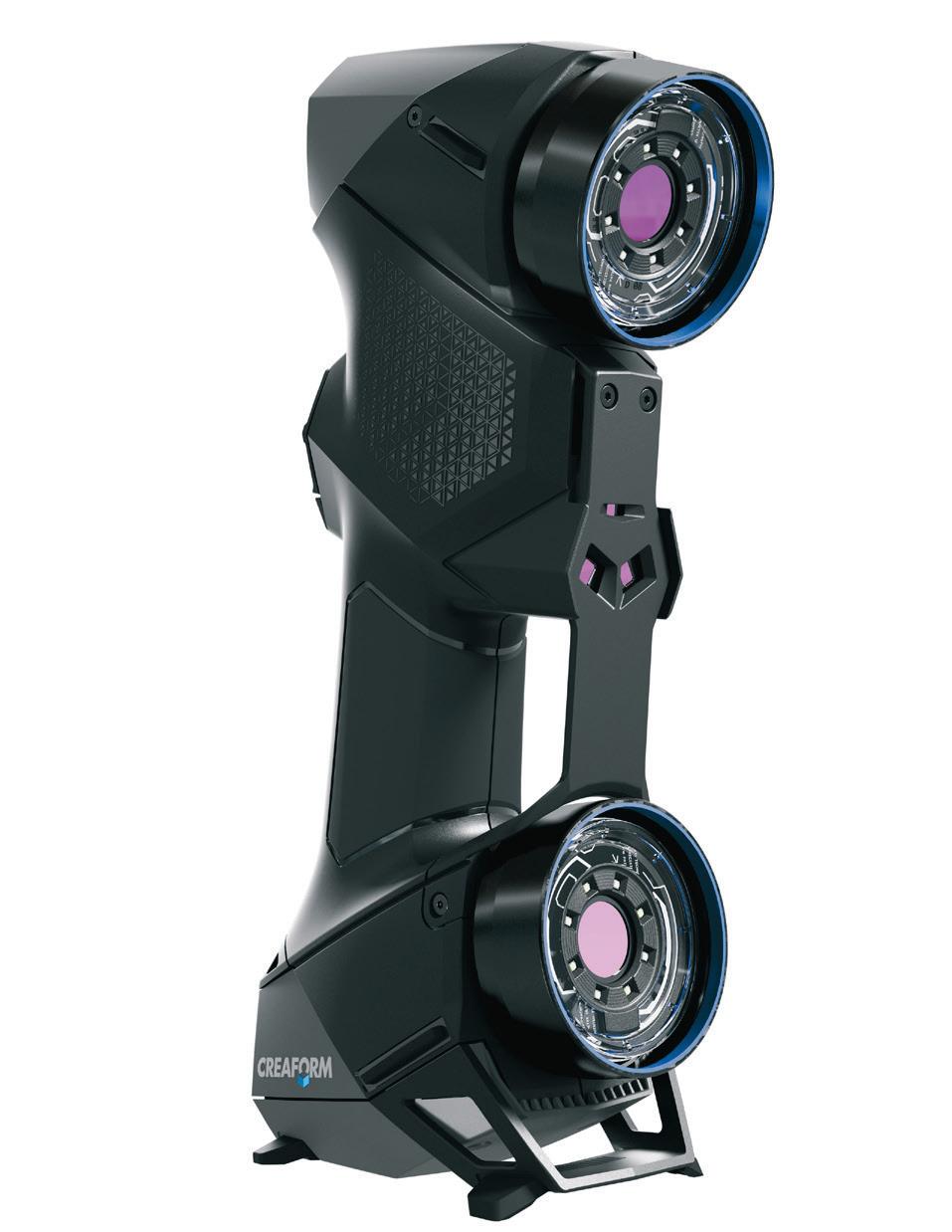
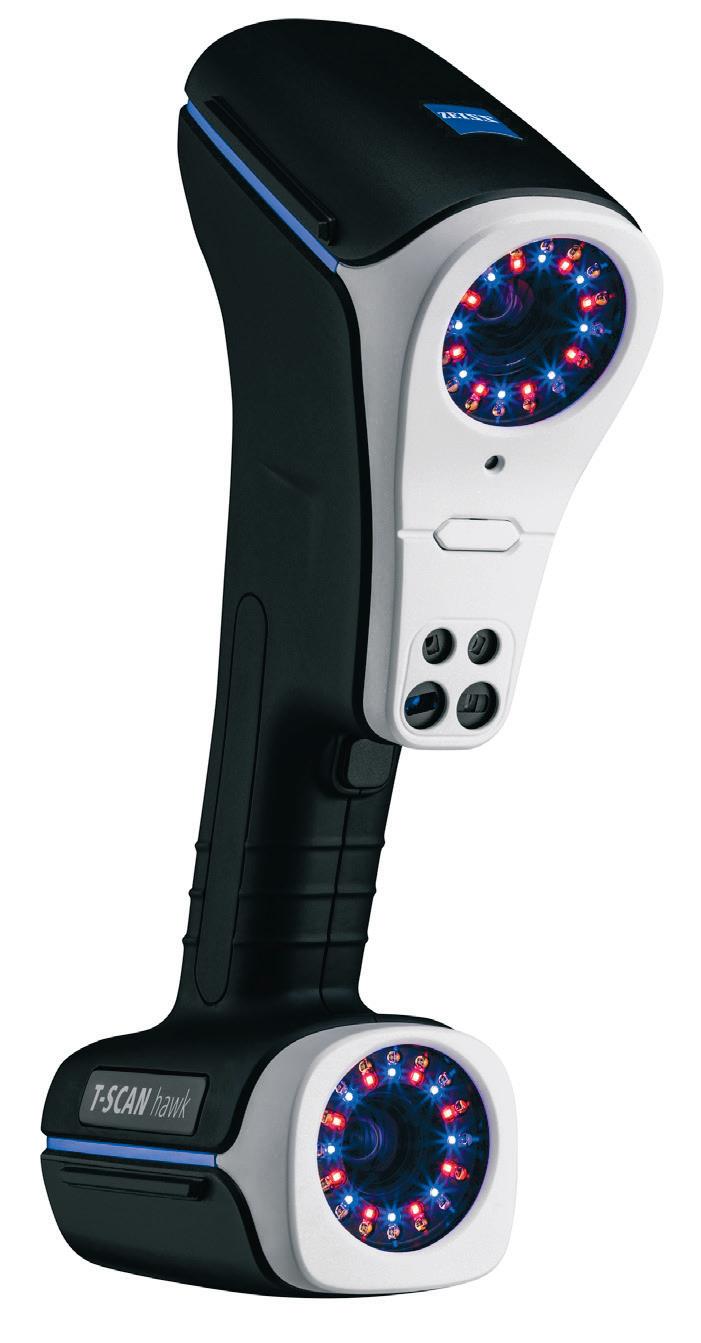
8
T-SCAN HAWK ZEISS
For users with a more generous budget, T-Scan Hawk by Zeiss offers an advanced laser triangulation system and high accuracy. It works on dark and reflective surfaces and even deep pockets. It has 3 scanning modes: red crosses mode, for scanning large sections; single red line mode, when the scan requires precision (good for hard-to-reach areas); and finally, blue lines mode, for scanning dark, shiny or reflective surfaces.

10
LEO ARTEC
With its 5.5-inch touchscreen, Leo enables a user to monitor a scan as they go, with no need for a computer. The device uses vertical-cavity surface-emitting laser (VCSEL) structured light, which works well even in low lighting conditions. Hybrid geometry and texture tracking allows users to scan without targets. On the downside, it is amongst the heaviest handheld scanners on the market, weighing in at 2.6 kg.
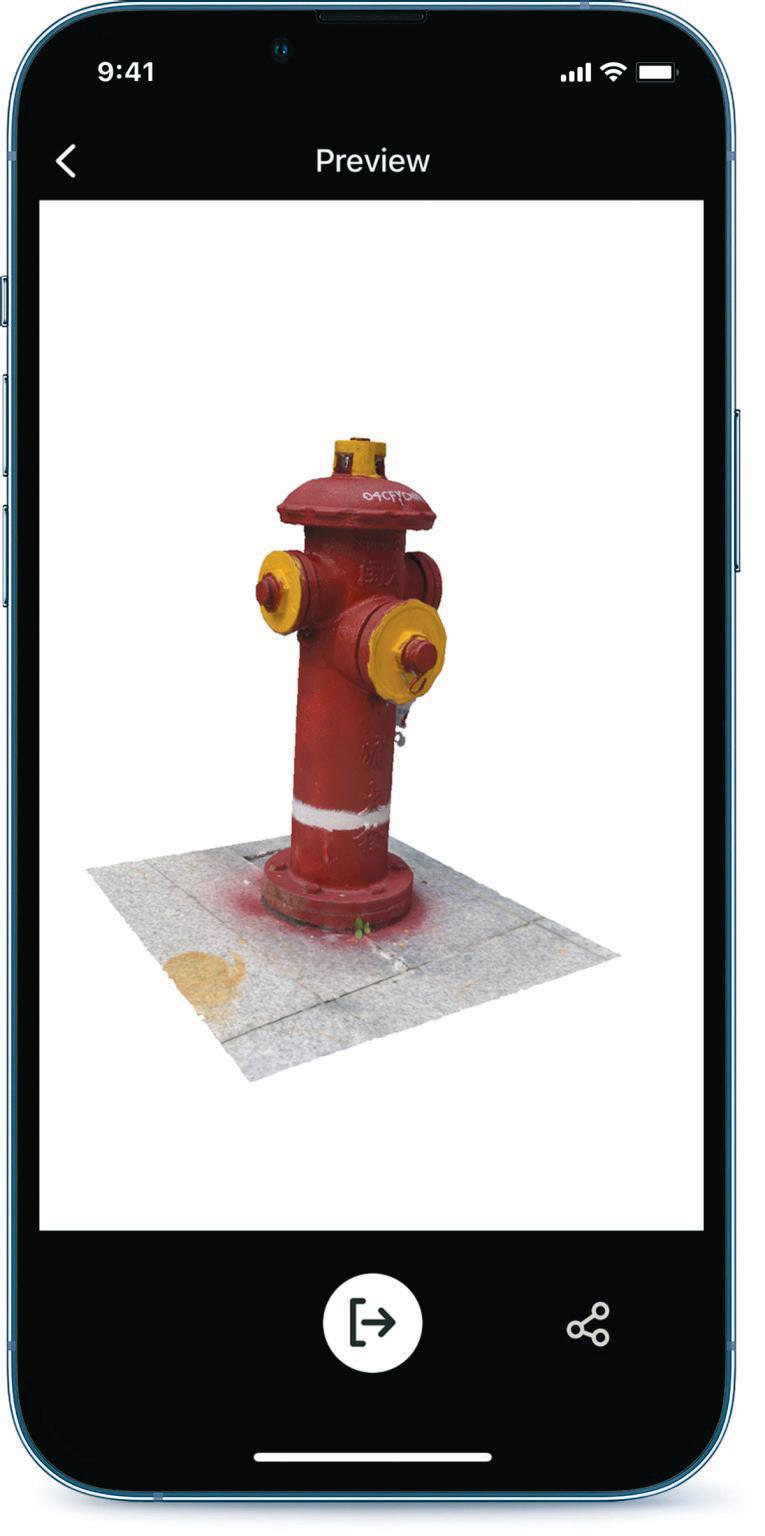
9
KIRI ENGINE KIRI INNOVATION
An app rather than a 3D scanner, Kiri Engine still deserves a spot on this list. Available for both Android and iOS, Kiri can scan any 3D object and turn the data into printable files.
The app is based on photogrammetry and its AI algorithms reconstruct an object in 3D based on photos. The app has a free and a premium (paid) version. Kiri does not come equipped with modelling software.
» Price: From free
www.kiri-innov.com
11
SIMSCAN SCANTECH
Marketed as the only hand-sized 3D scanner on the market, SimScan weighs under a half-kilo — just 570g, to be precise. Released in 2021, it uses eleven crossed blue lasers, offers accuracy to 0.02 mm and can scan in three different modes. These are ultra-fast scanning, hyperfine scanning and deep hole scanning. While the device features an impressive acquisition speed of up to 2,020,000 points/second, it is not able to scan textures or colours.
12
LEICA BLK2GO LEICA
Very much a premium model, the Leica BLK2GO can digitally capture space with no interruption. Easy to manoeuvre and lightweight at 775g, it features a 12-megapixel detail camera, plus three panoramic cameras for navigation. It is operated by a single-button operation system and can be wirelessly linked with a Leica iPhone app, so that the user can see the data it gathers in real time, in both 2D and 3D.

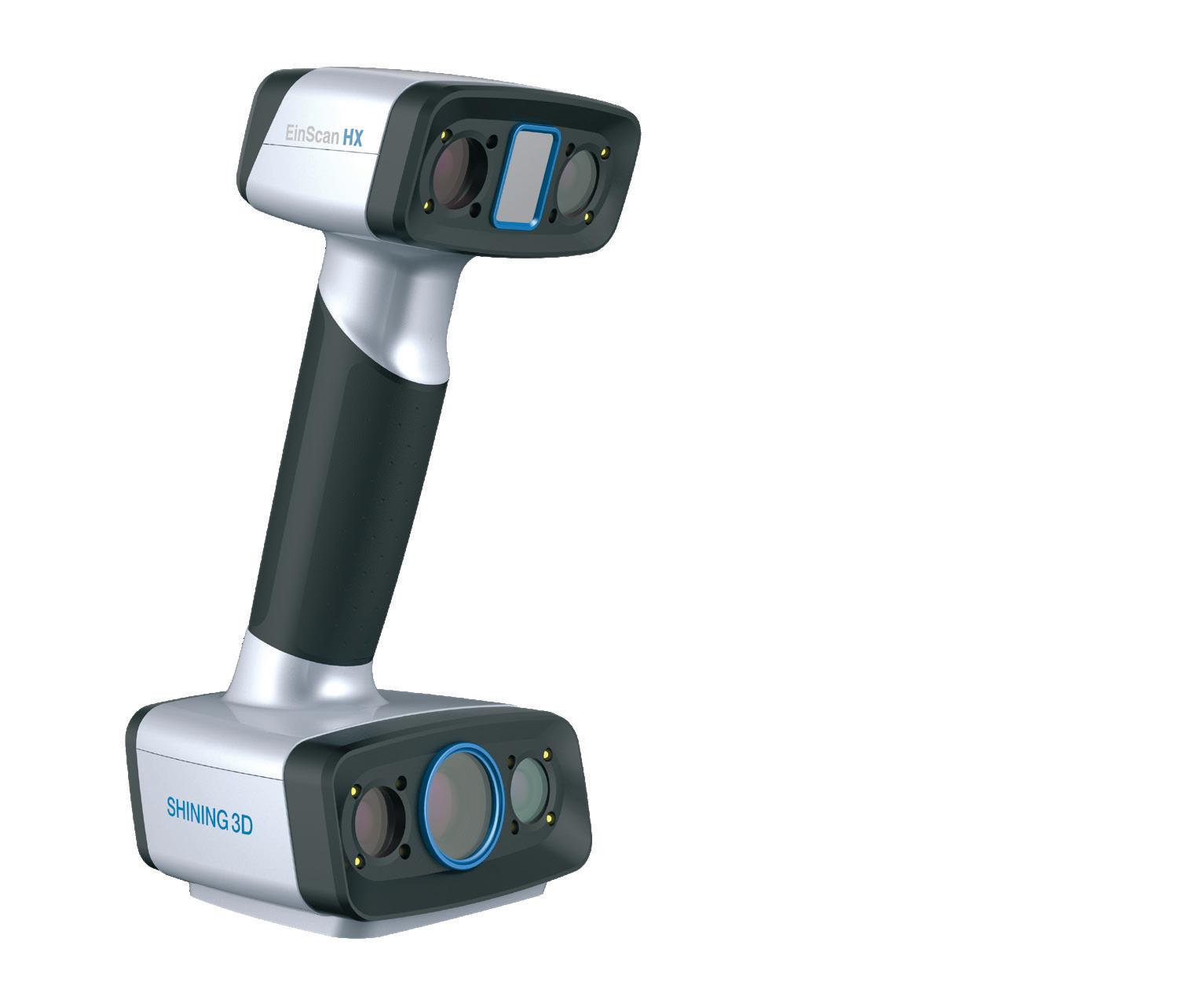
13
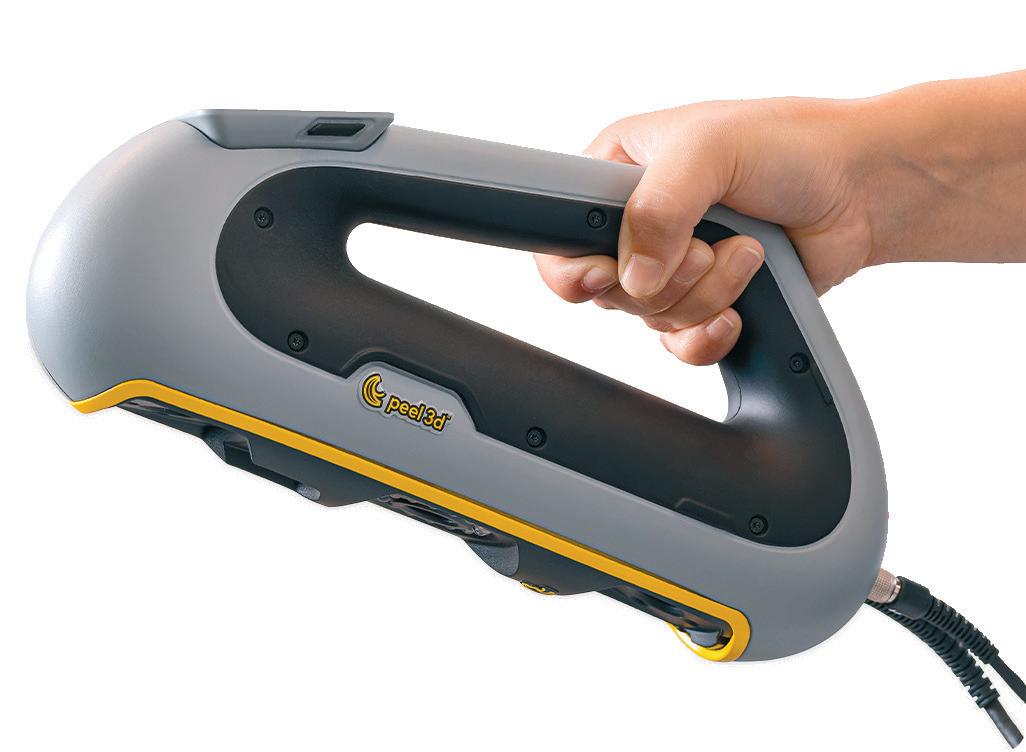
EINSCAN HX SHINING 3D
» Price: £££££
www.leica-geosystems.com
With a reputation for affordability, Shining 3D aims to bring physical form capture technology to the mass market. Its EinScan HX offers both a rapid mode and a laser scanning mode. The former uses structured light technology and allows the user to capture data quickly without registration targets. The latter offers higher resolution and volumetric accuracy, but a slower scanning process that relies on targets. Users can also opt for a hybrid approach which combines elements of both modes.
14
PEEL 3 PEEL 3D
Originally aimed at hobbyists and creatives, the third generation of Peel 3D is suitable for more professional reverse engineering applications. With its slick LCD screen, it can also be used as a distance meter, enabling the user to easily scan without looking at their computer. Recognisable vibration patterns guide the user around narrow and hard-to-reach places without a direct line-of-sight, giving them real-time feedback.
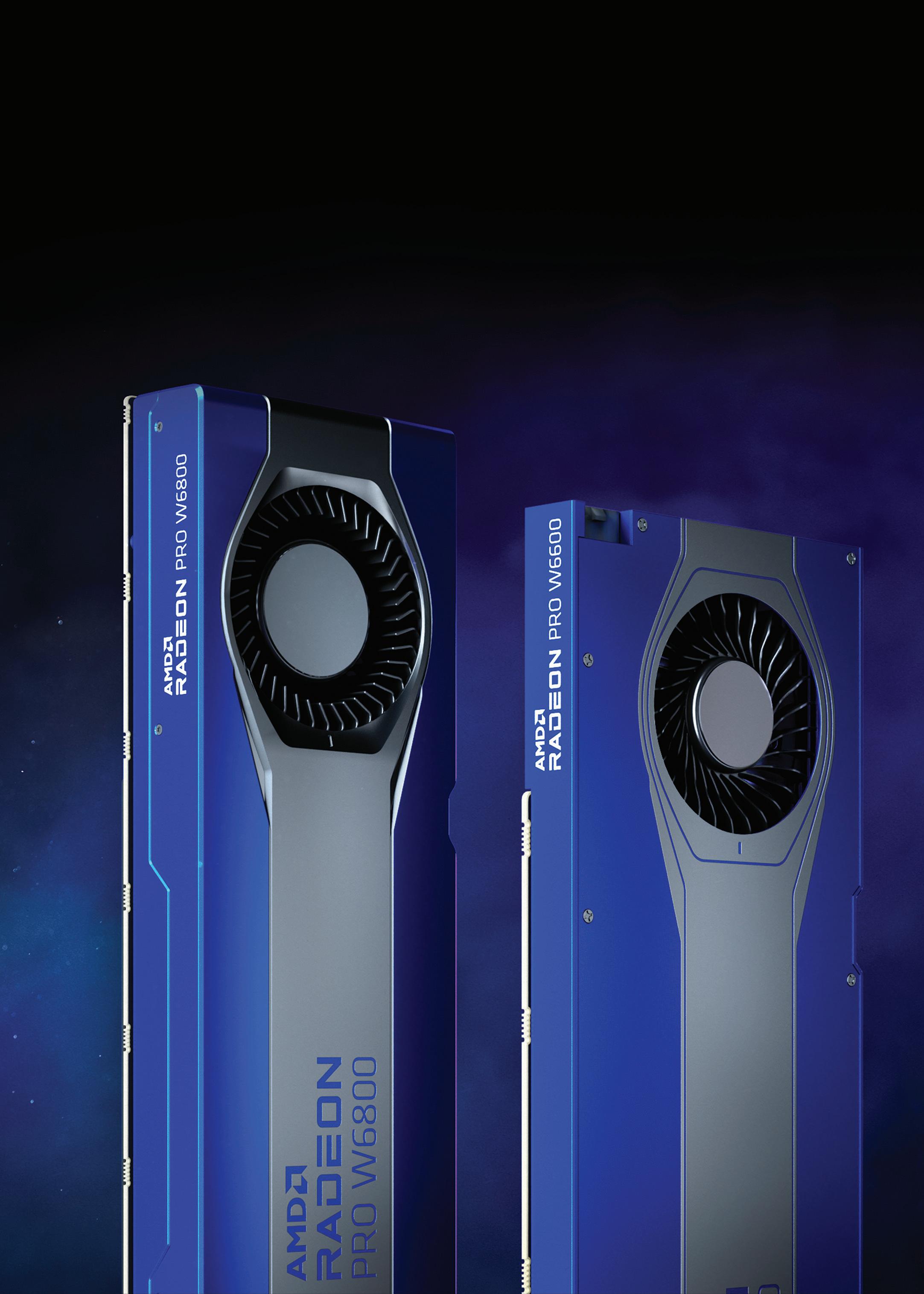
AUTODESK REACHES FOR THE CLOUD
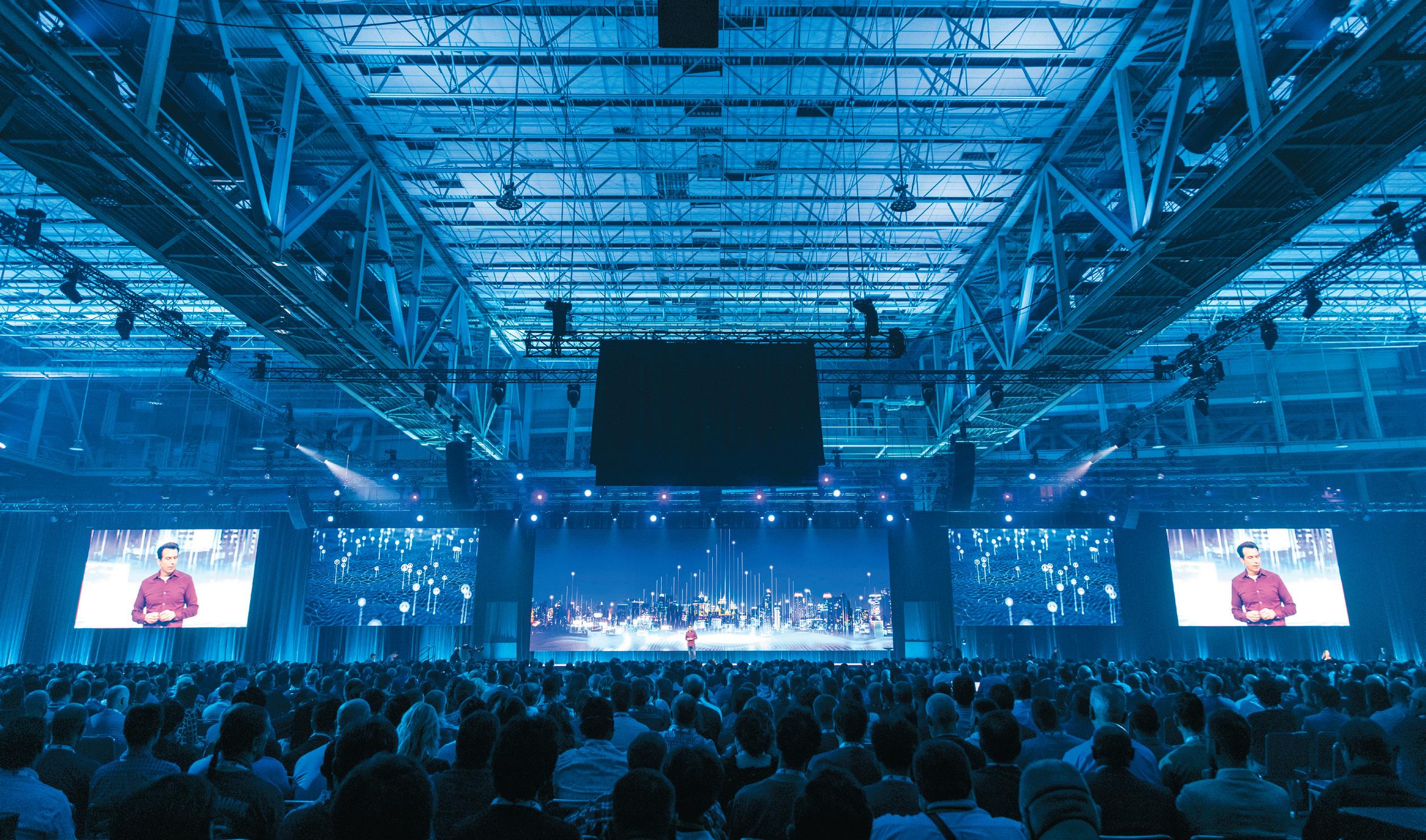
After a three-year hiatus, Autodesk University is finally back in person to get users up to speed on all the latest updates to its widely used software, to exchange feedback, and to discuss how to address the challenges of our time, as Claudia Schergna reports
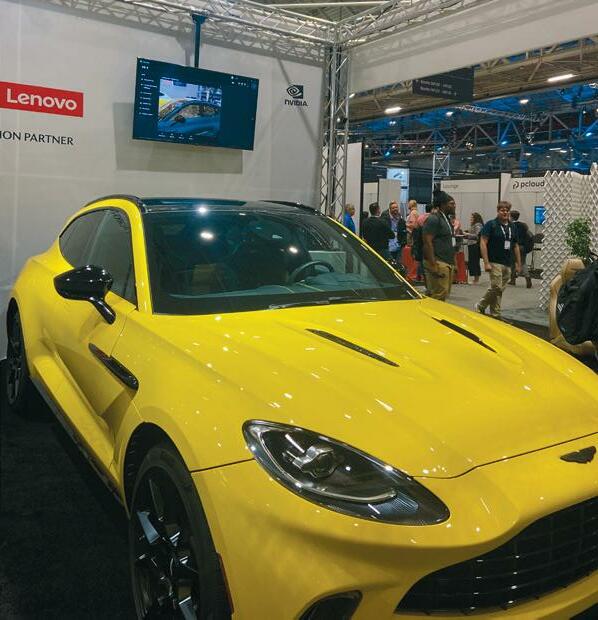
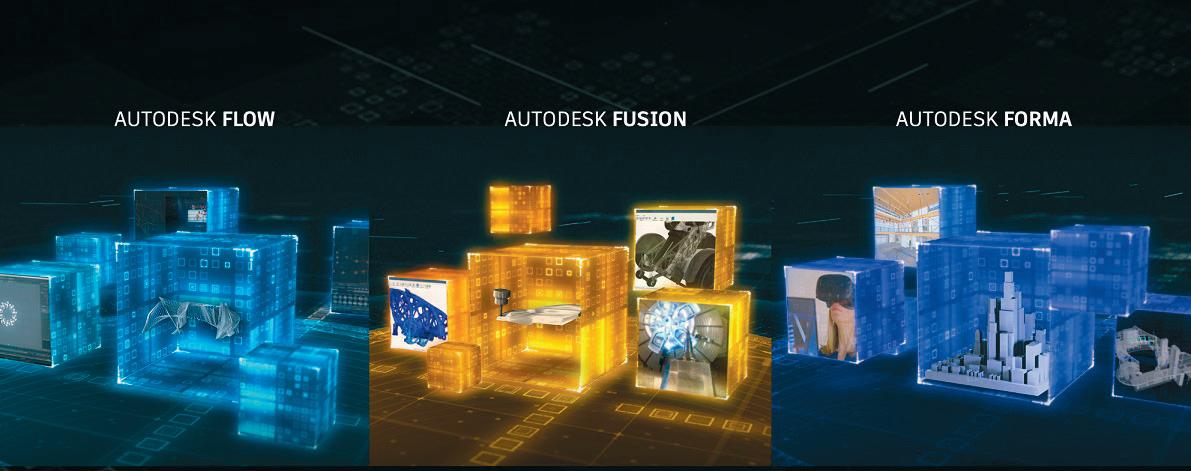
Flexible, device independent, connected: these were the buzzwords of Autodesk 2022. During the first in-person event since the pandemic, designers and engineers from around the world had a chance to find out about its troubled history and historical resilience. The first guest was Meagan William, Urban Water program manager for the city of New Orleans. William, a New Orleans native, was 16 when Katrina happened and clearly remembers the devastation that it brought Autodesk’s plan to fully embrace the cloud. The software to her city. Her job aims to safeguard and protect new giant aims to facilitate the growing demand for tools to generations from issues caused by climate change and keep remote teams always connected, and to make sure the rise of sea levels. everyone in the supply chain has access to the data they Andrew Anagnost took back the microphone to need precisely when they need it. talk about one of the biggest problems that design,
The aim is to reduce production times, save resources, engineering, and architecture teams all around the world facilitate the connection between team members and face daily: dysconnectivity and lost-in-translation data. democratise tools, making them accessible on any device. These are issues that Autodesk is looking to resolve by
Another big theme for the three-day event, with the introducing three industry clouds: Autodesk Fusion approach of Hurricane Ian towards US shores making it (for design and manufacturing) Autodesk Forma seem ever more urgent, was sustainability. (for architecture, engineering and construction) and
Autodesk’s big eco announcement was its collaboration Autodesk Flow (for media and entertainment). with Makersite to develop a plug-in for Fusion 360, which Given the multitude of industries Autodesk users work aims to provide designers with the sustainability data within, the keynote sessions were split into three parts. they need at any step of the design process. For manufacuring, Jeff Kinder, Autodesk executive VP of
Makersite is a software company that develops data product development and manufacturing solutions, took management tools for the global manufacturing the stage with some exciting news about Fusion 360. industry, empowering companies to manage product Besides the Autodesk Fusion cloud offering, Kinder sustainability, cost, and compliance. announced new Fusion 360 extensions powered by
Thanks to the plug-in, currently in the trial phase, Ansys and ModuleWorks, which aim to unlock advanced designers should be able to visualise the environmental product design and manufacturing capabilities. impact of every single iteration they make to the project The integration of Ansys simulation technology looks and be provided to provide useful with options to insights about help them meet printed circuit board cost and emission (PCB) signal quality targets, taking as part of the board into consideration design process, while the entire product the collaboration lifecycle. with ModuleWorks
The plug-in has should offer new been tested by the capabilities to British company Fusion’s Machining Pembree Pedals. Its founder Phil Law, joined by Extension, to generate higher-performance, collision-free Makersite CEO Neil D’Souza and Autodesk sustainability toolpaths for efficient multi-axis milling. strategy manager Zoé Bezpalko, presented a demo of It seemed that all the updates on Fusion 360 are part how it has helped the bicycle part manufacturer develop of a bigger move that aims to build out a complete pedals that are as sustainable as they can possibly be, platform, able to connect all phases of the process, from while at a reasonable cost. design to make, going through CAD, CAM, simulation,
Meanwhile, on the exhibition floor, attendees could and rendering, while being device-independent, always try on some of the latest AR, VR and XR technologies, connected to other users and applications or, as Kinder starting with a Varjo headset powered by a Lenovo defined it, a “click-to-make” tool. ThinkStation workstation that attendees could test on a gleaming yellow Aston Martin. Parked next to the THE JOURNEY TO THE CLOUD physical car, at the very entrance of the exhibition floor, During the media Q&A, Anagnost addressed journalists was standing its incredibly realistic digital twin in XR. and analysts, curious to know what the future holds, the
Further down the exhibition, Faro was inviting visitors purpose of developing three different industry clouds, to try its newest 3D scanners, including Faro’s Freestyle 2 and how Autodesk is working to make its cloud offering (featured in our handheld 3D scanner round up on page accessible from any location across the globe. 30) and Focus Premium. As Anagnost explained, not all of these questions have
In the ‘Factory’ area of the exhibition, Autodesk a definitive answer yet, as the recent announcements are offered a live demo of how a VR headset can help teams only the beginning of a bigger strategy, which will see collaborate from their remote locations. more tools connected not only in the cloud but into one single piece of software. THE KEYNOTES While we might have to wait a little longer to see the Welcomed by music and dance performances, in proper final results of this ambitious move, there was plenty New Orleans style, the keynote session brought everyone to take away from New Orleans, with the chance to be together in the main hall to officially announce what was in-person among an international community of users already in the air. talking positively about how the industry can tackle the
Autodesk CEO Andrew Anagnost started by thanking world’s most pressing issues. all attendees and the city of New Orleans, talking about www.autodesk.com/autodesk-university
●1 Autodesk CEO, Andrew Anagnost, addresses the masses in his keynote ● 2 As part of its new Autodesk Platform, Autodesk introduced three industry clouds at Autodesk University: Fusion, Forma, and Flow ● 3 On the show floor, Lenovo used XR to showcase a gleaming yellow virtual Aston Martin DBX alongside the real one
IN THE FRAME
Kalkhoff’s efforts to accelerate physical prototyping for its bicycle frame looked to have hit a rut, until Materialise got them back on track. Stephen Holmes reports on how the company 3D printed an aluminium prototype in record time
With over 100 years of experience, Kalkhoff knows how to build a bike that goes the distance. But even the German manufacturer is impressed with the speed at which its latest e-bike moved from concept to physical prototype testing.
It can take years to ready a bike for production, with product development for any new Kalkhoff product always a balancing act. Designers need to maintain the unique geometry now synonymous with the visual identity of Kalkhoff e-bikes, while also considering functional ability and the necessary components for the design.
The company strives for its bikes to be comfortable, agile and reliable, giving every customer a smooth and enjoyable riding experience. To achieve this, the company tests each bike’s frame well beyond the industry standard.
Usually, a bike frame must pass loads of up to 150 kg. In comparison, Kalkhoff’s frames are pushed to tolerate loads of around 170 kg. “Our business prides itself on providing our customers with the opportunity to cycle freely without limitations,” says Kalkhoff industrial designer Rik Maes. “Cycling should reflect our company motto: ‘Kalkhoff moves you everywhere,’” he says.
For prototyping to begin, rideable models must be first produced – an expensive and time-consuming process that requires tooling to be cut, and which cannot be undertaken with plastic form models.
With this obstacle in mind, Kalkhoff contacted its polymer additive manufacturing supplier Materialise, to discuss a potential solution through metals 3D printing.
●1 Materialise Magics was used to segment the bike frame for 3D printing, optimising the build process ● 2 The 3D-printed aluminium parts were precisely welded together and heattreated to form a complete frame ● 3 Once kitted out with wheels and fittings, Kalkhoff’s frames are pushed to tolerate test loads of around 170kg
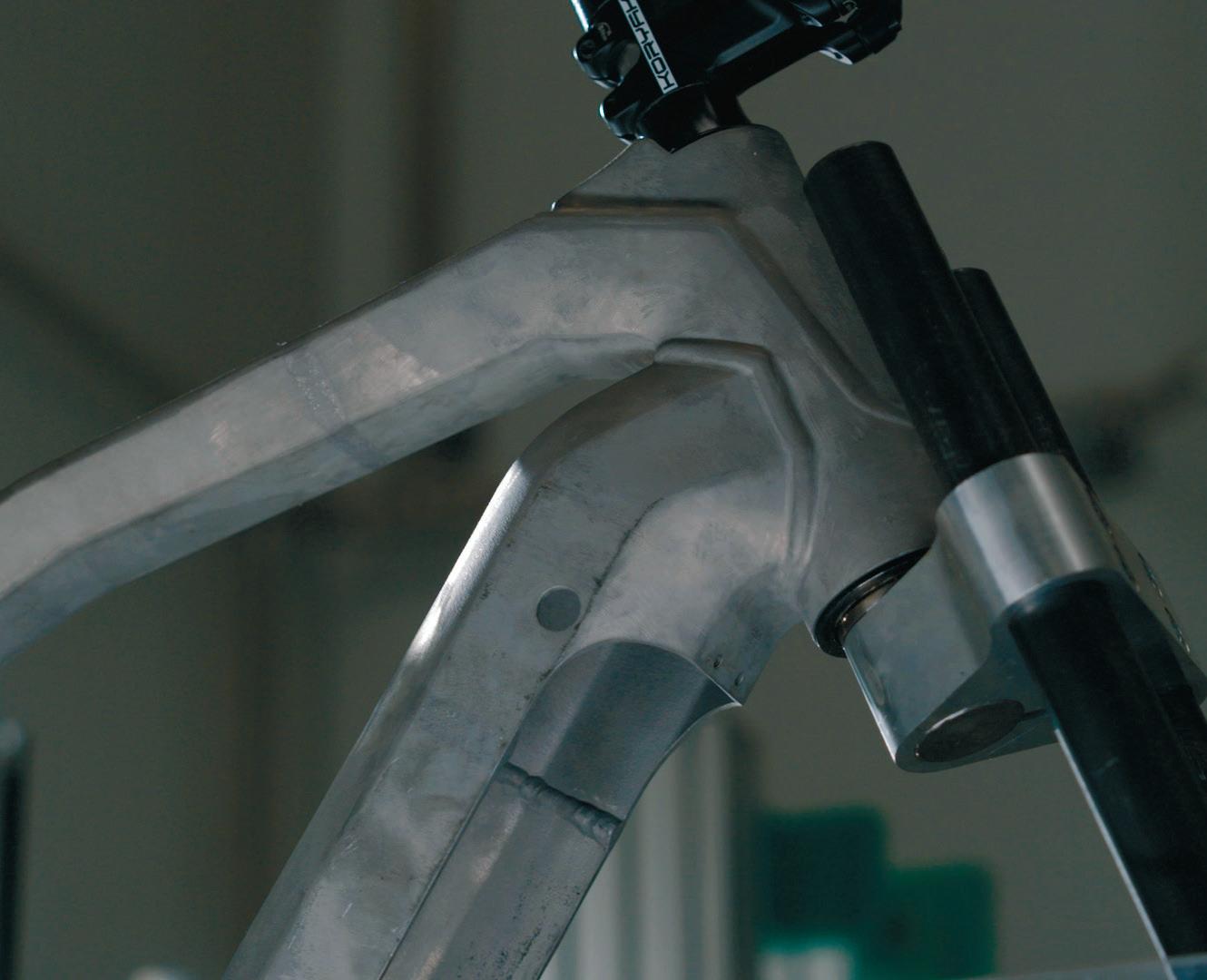
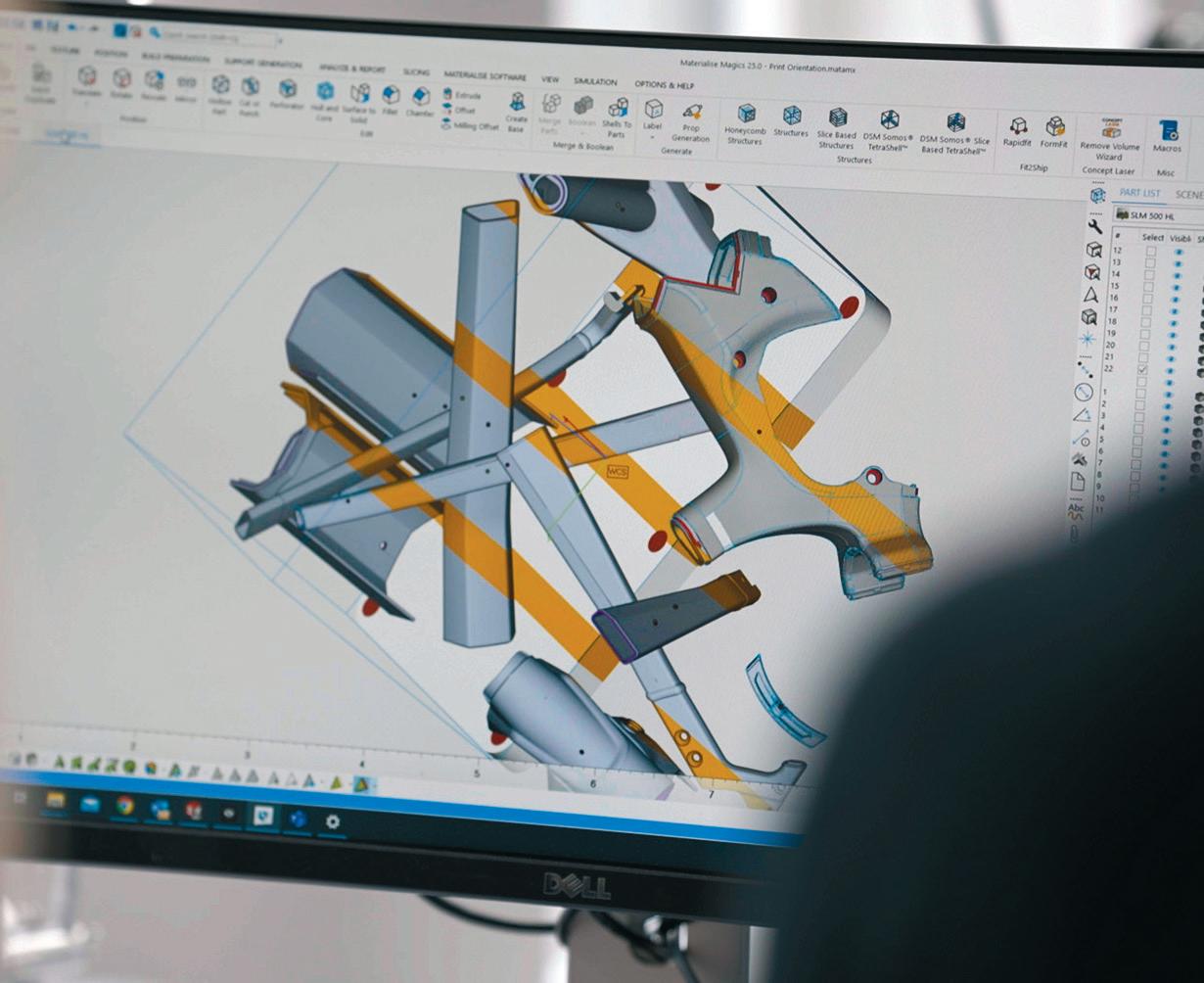
3
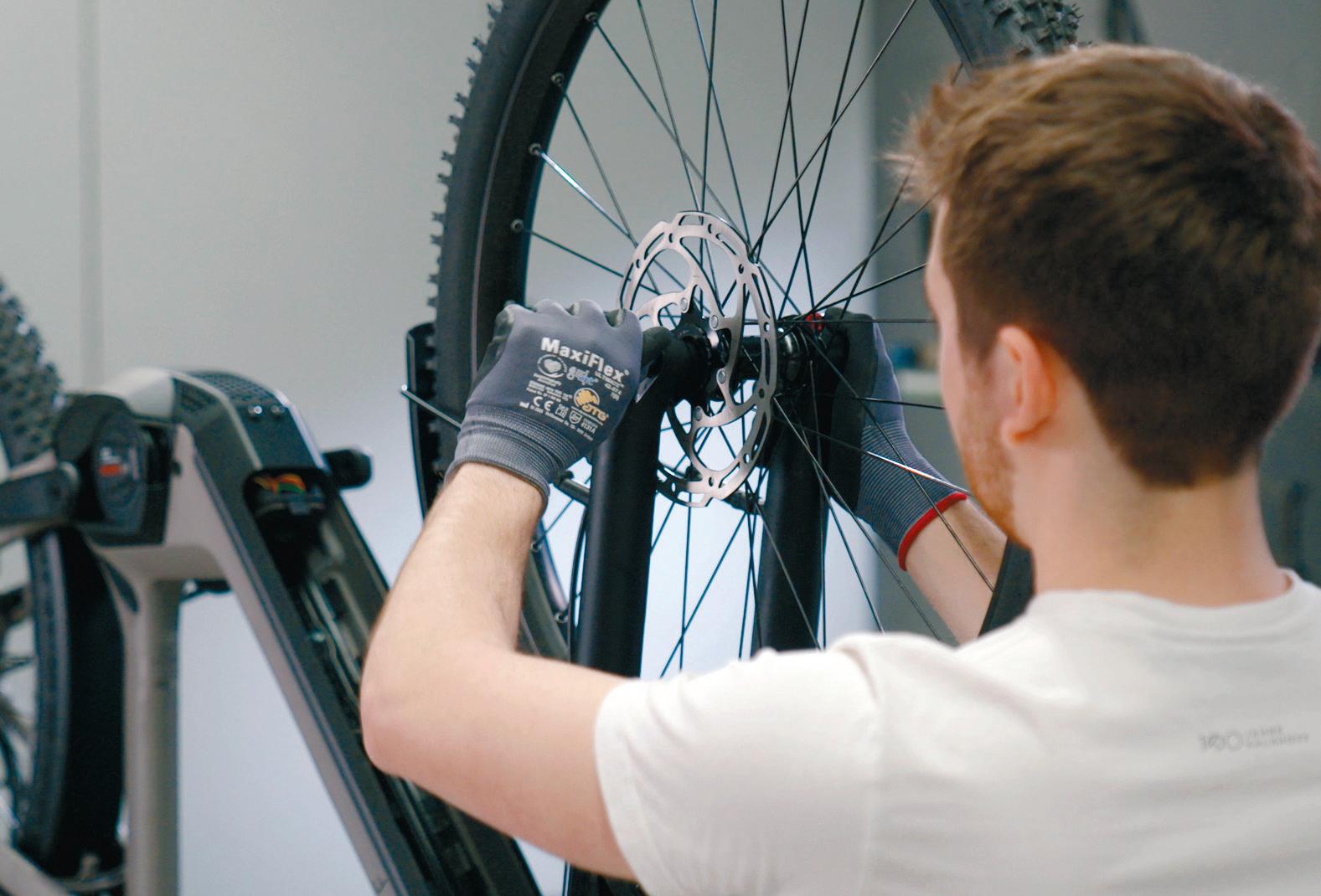
METAL HEADS
With Materialise’s Metal Competence Center (MCC) for 3D printing located in Bremen, close to Kalkhoff’s headquarters in Cloppenburg, the teams met to begin optimising the bike’s design for additive manufacturing in aluminium.
With the maximum part size for Materialise’s SLS 3D printers set at 500 x 280 x 315mm, building the full frame as a single piece was not an option, so the first step was to convert the 3D CAD model of the bike into printable sections.
The optimal segmentation of the design was determined in Materialise Magics, positioning the cuts on the frame to consider existing loads to avoid peak stress in the welded joints and ensuring that an entire bicycle frame would fit into the 3D printer’s build chamber.
Optimising the build strategy also helped to reduce machine time and post processing efforts. Once the joining segments were defined, the end segments were redesigned in CAD to create a better welded surface once printed.
Welding and testing was performed by Seefried, a company specialising in small series welding and located near the MCC. ACTech, a Materialise-owned specialist in metallurgy and low volume production took care of heattreating the welded frame, performing this task via two processes — solution annealing and artificial ageing.
While components were being printed, the simulation for the welding and heat treatment of the frame was run simultaneously using the 3D CAD data, helping streamline the process even further.
“Situations like this and moments such as after the annealing stage that require real-time measurements of the frame with millimetre-accurate geometry are not possible without close cooperation and the expertise of all those involved,” explains Michael Röhner, product manager metal 3D Printing at ACTech.
EXPECTATIONS SURPASSED
Typically, the complete development of a bike takes between two and two-and-a-half years. By using metal 3D printing and the expert know-how at Materialise, the whole prototype frame was delivered in six weeks from start to finish — an overall saving of three months in the development phase.
“Metal 3D printing has surpassed our expectations,” states Maes. “We can make changes at short notice, because no tools or moulds were specifically needed to be built for this model. In the development phase or the ‘engineering design freeze,’ we will have mobile design prototypes where we can test all the selected parts. This has never been possible!”
Additionally, producing the frames with local partners meant Kalkhoff could save time, get the test results faster and feed any changes back into the design without worrying about long transportation waits from Asian suppliers.
“That’s a good thing for us, as we’re first to market with innovative bikes for our customers!” concludes Maes.
Once testing is complete, the test bikes go on to fulfil other purposes. For example, new designs are available for showcasing at marketing events and for test rides long before the production models reach the market. The process also acts as an exploratory step towards more sustainable future production methods that will help shape the next century of Kalkhoff’s designs. Metal 3D printing has surpassed our expectations. We can make changes at short notice, because no tools or moulds were specifically needed to be built for this model ’’