Denton’s Shed
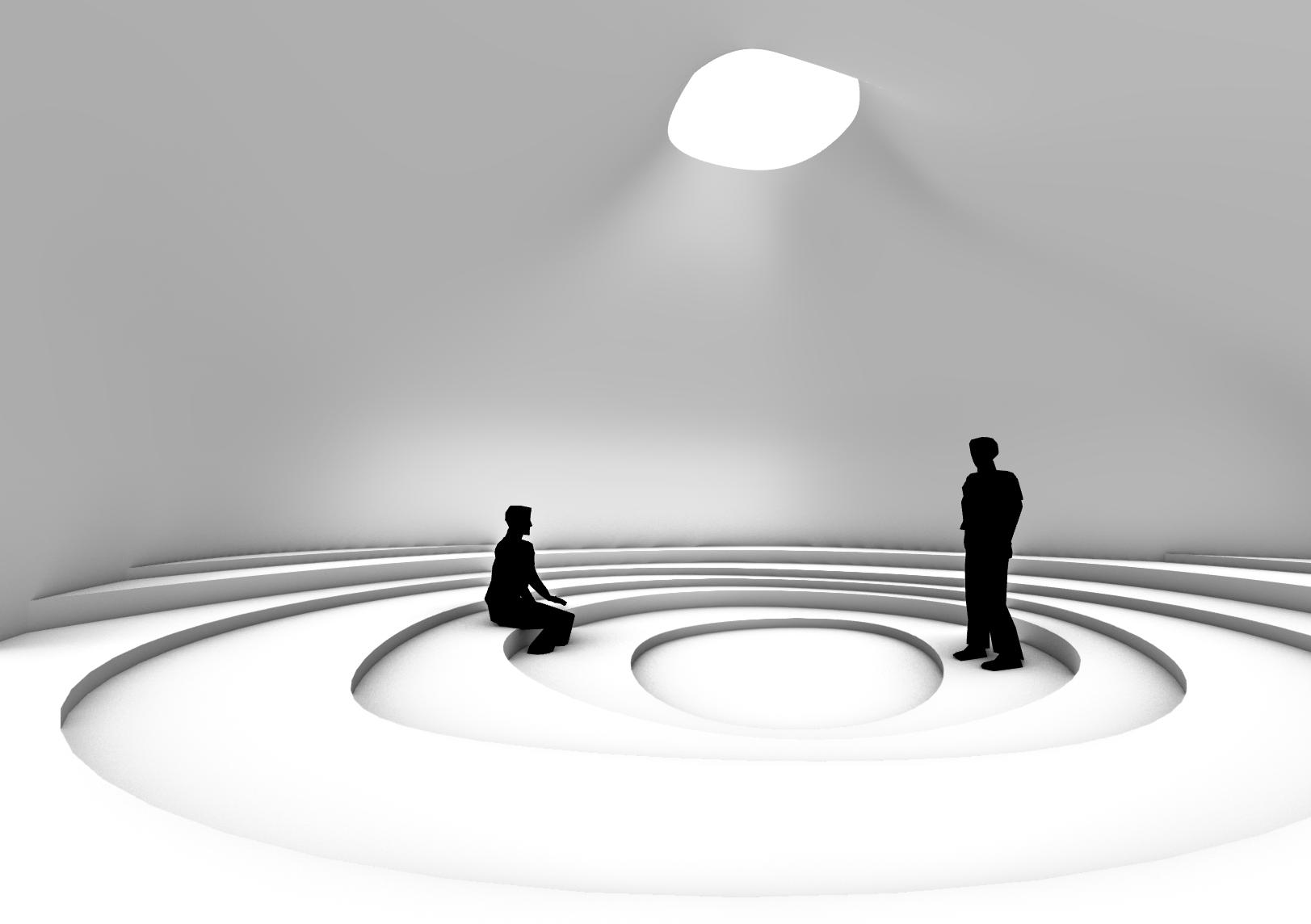
Plan Iteration 1
Plan Iteration 2
Plan Iteration 3
Plan Iteration 4
Plan Iteration 5
Section Iterations 14 Final Plans
Final Sections 19
Airform RC Details 20 Rammed Earth Details
Steel and Glass Details 24 Digital Workflow
The approach of the initial plan iteration was to better encapsulate the idea of the cave. Our refined concept was “A journey of immersion and exploration through cave-like forms, creating feelings of being within the earth”. In the first iteration, this was encapsulated through following a series of voids and skylights through the space. The voids guide the user through light, drawing the user through the space as they follow the light.
The next iteration built on the first by further encouraging feelings of exploration through the spaces. By making the circulation less linear, the user is encouraged to become immersed in the space and explore. The space experiments more with open versus enclosed spaces, immersing the user in the journey through caves that we wanted to achieve. The idea of the voids being a central guiding aspect is still paramount to the iteration. The iteration further experiments with heavy versus light massing, rather than homogenous wall thicknesses, creating a cavelike experience.
The third iteration improves further upon the second iteration by having a more circular flow. The aspects of immersion are still clear by having the user explore the space through the voids, however the spaces are slightly more separated and distinct, with each new space bringing a new immersed experience.
Iteration 4 takes the idea of the cave through a new approach, further experimenting with enclosed and open space. By creating a “pinch” effect on the centre of the space, the users are squeezed through spaces, reflecting crevasses found in a cave. On the other side of the pinch is an open chamber with another void, drawing light into the space, with the voids again providing the key indication of the spaces to explore next.
The final iteration was the plan that was chosen to become finalised. The iteration focusses on open vs enclosed space to create immersion, creating a series of cave chambers that are discovered through multiple pinches in the form. The circulation is far less linear than the other iterations, with the journey of exploration truly immersing the user in the space, having the freedom to choose the next space they want to discover.
Concurrently, sections were being developed following the same concept in order for the spaces in plan in section to reflect each other. The final selected section can be seen, which informed the following plans and sections.
>
The final sections of the space were then created, from a conglomeration of Iteration 5, and a new digital model from Iteration 5 to infrom the new section. It was paramount to the design that not all spaces take place on a single level, with the journey through the site needing to be on the Z axis as well as X and Y, to truly immerse the user in the experience of the cave.
The voids as a central guiding feature are still paramount in the sections, creating natural light in an otherwise dark space.
The initial iteration of a detailed design features a pneumatic airform structure. Prefabricated airforms are created from a composite tarpaulin, fabricated off site to the size of a desired gridshell. High pressure fans are installed on site, with the prefabricated airform being hooked into an in-situ concrete slab at nessesary intervals.
The high pressure fans inflate the airform, with an initial concrete layer being applied to the exterior of the airform. Reinforcements are then placed within the concrete, with a finishing layer of concrete then applied to the form. The airform is then removed, creating an interior space to be sprayed with Polyeuthane foam and an interior finish.
In this instance, with the addition of the void structures, extra reinforcements have been placed on the exterior with a retaining wall to support the void.
SKIRTING AND CABLE TRAY TATE RAISED FLOOR SYSTEM TATE PEDESTAL BASKET
AIRFORM ANCHOR BOLTED TO SLAB
REINFORCEMENTS BOLTED TO SLAB IN-SITU SLAB TO ENGINEER’S SPEC
RC AIRFORM SHELL GROUND CONNECTION DETAIL 1:10
SHOTCRETE, 20mm, FINISHING LAYER PREFABRICATED AIRFORM
POLYEUTHANE FOAM
REINFORCEMENT TO ENGINEER’S SPEC IN-SITU CONCRETE APPLIED TO FOAM DISPLACED EARTH MOVED AROUND SHELL
PRECAST RETAINING WALL TO ENGINEER’S SPEC REINFORCEMENTS BOLTED TO RETAINING WALL REINFORCEMENTS WELDED TO REBAR LAYER IN SHELL
EXCAVATED EARTH REPLACED AFTER STRUCTURE COMPLETION
SHOTCRETE, 20mm, FINISHING LAYER PREFABRICATED AIRFORM POLYEUTHANE FOAM REINFORCEMENT TO ENGINEER’S SPEC IN-SITU CONCRETE APPLIED TO FOAM
REINFORCEMENT CONTINUES TO SLAB
AIRFORM COMBINATION POINT
TATE RAISED FLOOR SYSTEM AIRFORM CONTINUATION
ANCHOR POINT, BOLTED TO SLAB
CHAMBER COLLISION
RC AIRFORM SHELL VOID STRUCTURE DETAIL
1:20
The second detail iteration features a rammed earth design. The structure is created using rammed earth blocks, creating a dome. As extra reinforcements, a reinforced concrete beam encircles each dome, which also serves as reinforcements for the meeting point of two separate domes.
In order to reinforce the void, an additional steel beam encircles the base of each void structure, bolted into the blocks. The void rammmed earth blocks are then built atop the beam, with a finishing layer then applied to the exterior of the structure before returning the displaced soil to the site.
LOW-E DOUBLE GLAZING WITH ARGON AIR GAP
100X150 RAMMED EARTH BLOCKS
BLOCKS FIXED TO BRACING STRUCTURE
FINISHING MORTAR LAYER
DOME FROM RAMMED EARTH BLOCKS, FABRICATED IN-SITU
STEEL CIRCULAR BRACING, BOLTED TO EARTH BLOCKS
1:10
EARTH FINISHING LAYER
DAMP PROOF MEMBRANE
EXCAVATED EARTH REPLACED POST-COMPLETION
DOME FROM RAMMED EARTH BLOCKS, FABRICATED IN-SITU
LAYER OF LIGHTWEIGHT COMPRESSED EARTH
DAMP PROOF MEMBRANE
FINISHING MORTAR LAYER
DRAINAGE GUTTER
400MM REINFORCED CONCRETE TRANSFER BEAM 90MM INTERNAL DOWNPIPE
100X150 RAMMED EARTH BLOCKS
TATE RAISED FLOOR SYSTEM
The third detail iteration features a steel and glass diagrid system, with each triangle resembling a unitised curtain wall system. The form is constructed using 100mm vertical steel bars, and 90mm transverse bars. Each transverse bar is bolted to 120mm steel node. Each vertical steel bar is welded to the node for additional vertical stability.
The form is then clad to create the cave-like effect within the space, using concrete cladding connected through stack joints that are bolted to the mullions. Where voids are nessesary, the stack joints connect glass panels. The exterior of the form is then clad with concrete and the displaced earth is returned to site.
STEEL AND GLASS SHELL CURTAIN WALL DETAIL
1:5
STEEL AND GLASS SHELL CURTAIN WALL DETAIL 1:5
IN SITU CONCRETE REINFORCED TO STEEL SHELL
100MM RADIAL BARS, WELDED TO NODE
90MM BATT INSULATION
IN SITU CONCRETE REINFORCED 100MM RADIAL BARS, WELDED
90MM BATT INSULATION
90MM CURTAIN WALL MULLION, BOLTED TO STACK JOINT 12MM PLASTERBOARD
90MM CURTAIN WALL MULLION, 12MM PLASTERBOARD
CABLE TRAY SKIRTING
CABLE TRAY SKIRTING
CURTAIN WALL STACK JOINT, BOLTED TO NODE
BASE STRUCTURE NODE, BOLTED TO SLAB
TATE RAISED FLOOR SYSTEM
CURTAIN WALL STACK JOINT,
BASE STRUCTURE NODE, BOLTED
TATE RAISED FLOOR SYSTEM
CONCRETE SLAB TO ENGINEER’S SPECIFICATION
CONCRETE SLAB TO ENGINEER’S
100MM RADIAL BARS, WELDED TO HEAVY GAGUE STEEL NODE
90MM TRANSVERSE BARS, BOLTED TO NODE SOCKET AT REQUIRED ANGLE
20MM BOLTS
10MM NODE SOCKET, WELDED TO NODE WELDED CONNECTION
STEEL AND GLASS SHELL GROUND CONNECTION DETAIL 1:20
100MM RADIAL BARS, WELDED TO HEAVY GAGUE STEEL NODE
90MM TRANSVERSE BARS, BOLTED TO NODE SOCKET AT REQUIRED ANGLE
20MM BOLTS
10MM NODE SOCKET, WELDED TO NODE WELDED CONNECTION
100MM RADIAL BARS, WELDED TO NODE
90MM TRANSVERSE BARS, SPAN DEPENDENT ON ANGLE OF PLACEMENT
AREA DEPENDENT ON CORRESPONDING SPANS AND ANGLES
120MM BASE NODE, BOLTED TO SLAB
CONCRETE SLAB TO ENGINEER’S SPEC
100MM RADIAL BARS, WELDED TO NODE
90MM TRANSVERSE BARS, SPAN DEPENDENT ON ANGLE OF PLACEMENT
AREA DEPENDENT ON CORRESPONDING SPANS AND ANGLES
120MM BASE NODE, BOLTED TO SLAB CONCRETE SLAB TO ENGINEER’S SPEC
STEEL AND GLASS SHELL GROUND CONNECTION DETAIL 1:20
STEEL AND GLASS SHELL NODE DETAIL 1:2
STEEL AND GLASS SHELL NODE DETAIL 1:2
The next step was the paramaterisation and analysis of the forms digitally. The forms use two kinds of digital structures, a simple pneumatic form for the single chambers, and subdivided freeform geometry for the continuous forms of the model. The pneumatic forms were optimised through form finding, while the free forms had to be optimised through a genetic algorithm and fitness landscape.
Both forms had a FEM analysis conducted. The various digital forms for analysis are seen in the left figure. The digital workflow can be seen on the following page.
Final
The following is a FEM analysis of certain geometry digitally paramaterised to be analysed. The forms are analysed using reinforced concrete parameters reflecting the reinforced airform shell details. In future, the details shall be altered to allow for a more accurate representation of pneumatic inflation.
Material: Concrete C100
Height: 3100mm
Maximum Displacement: 0.48cm