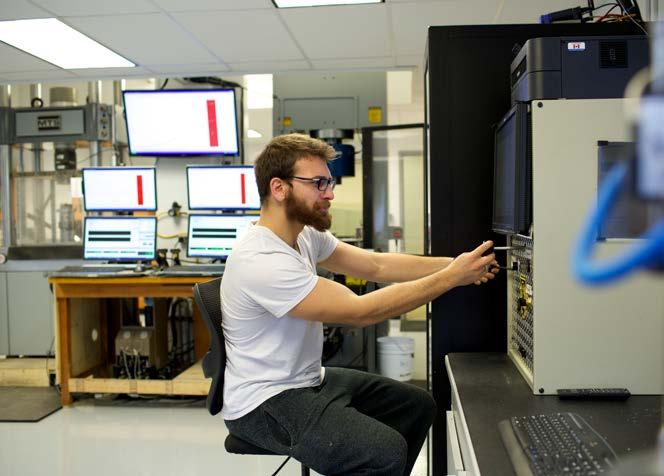
3 minute read
Queen’s Rock Mechanics Lab on solid ground
Students enjoy the hands-on learning environment of the Rock Mechanics Lab.
Advertisement
“ W e brought the Rock Mechanics Lab back to life,” says Oscar Rielo, Senior Program Coordinator at the Robert M. Buchan Department of Mining, who led the transformation of two dark, dusty, inefficient spaces into state-of-the-art student learning facilities.
Now, just over a year later, students are hard at work in the orderly second-floor Rock Mechanics Lab and basement lab in Goodwin Hall. “Students remember what they’re taught more easily, and I relate that back to the renovations,” Rielo says. “Before, the chaos and noise of our labs was distracting for them.”
Upgrades include two arrays of computers with customized software, which make it easy for learners to monitor results even as they watch their rocks being tested. And more students can work in the once-cluttered labs. “In my Mine 202 course, ‘Instrumentation,’ we can fit 35 students in the second-floor lab, versus only 10 before,” Rielo says. “So we get a lot more done.”
Two new workstations enable students to build sensors, for example, and test them, with oscilloscopes, voltmeters, soldering irons and
”shop for rock testing.”
materials close at hand. New benches and technology, such as computers, data acquisition systems and a force transducer for compressing rock, were introduced. Funding included $40,000 from the departmental budget, plus a good part of a $300,000 investment from the Faculty of Engineering and Applied Science.
Today, everything runs smoothly, so lab time is optimized and it’s easier to stage experiments. But the rock lab’s makeover was no easy task. “First, we cleaned up about three tons of garbage,” Rielo recalls. Then, labs were painted, reorganized and upgraded, with much
Queen’s Rock Mechanics Lab on solid ground
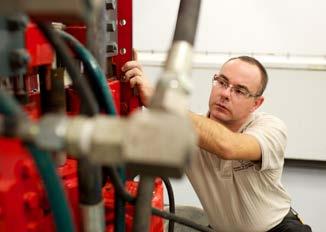
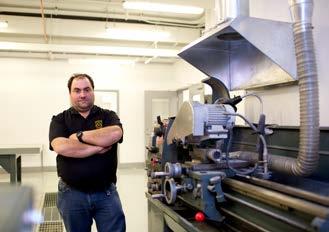
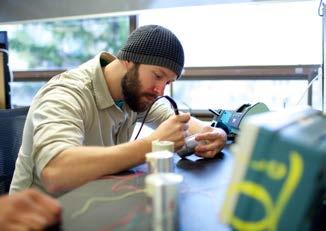
improvisation to solve problems and save money. “We are engineers, after all,” Rielo says with a smile.
Using funds generated from rock testing for commercial customers from around the world, Rielo’s team developed an automatic direct shear machine that is capable of collecting large amounts of quality data to enable accurate analysis. “In the long run, these efforts pay for themselves. Customers get value for their money,” Rielo says. “Our rock testing turnaround time has gone from two weeks to three days,” he adds.
In fall 2015, the Rock Mechanics Lab purchased a new piece of equipment earned from commercial work. “It’s a fire assay analysis machine, which will give the content of the rock,” says Rielo. “It will be used for research in our mineral Equipment/features list:
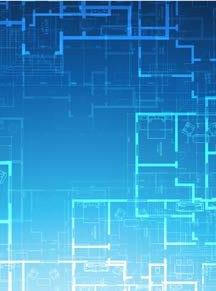
4 data acquisition systems 2 compression frames made by MTS 1000 kN and 3000 kN high resolution digital servo hydraulic controller oscilloscope State-of-the-art analytical software specifically designed for laboratory Commercial/research facility
Principal investigators include: Dr. Jamie Archibald Oscar Rielo
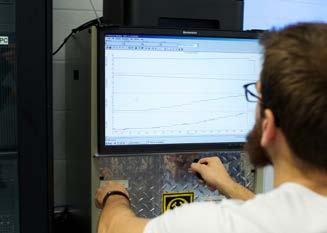
processing laboratories. It will also help our commercial testing efforts. The new machine, he adds, “fits with our commercial strategy to become a onestop shop for rock testing.”
Last year’s upgrades to the rock lab mean the facility is now modern looking and well equipped, Rielo says, and supports better student learning. Upon this solid foundation, the lab will build capacity for commercial work and conduct more ambitious research.
One research project in its early stages is the development of microseismic measurement equipment. “We are creating our own acoustic emission system, and if all goes well, it will enable us to predict rock failure long before it happens. Eventually, we could create a warning system for seismic events.”