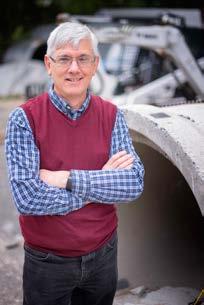
4 minute read
GeoEng Lab is one of a kind
In the wee hours of May 12, 2006, 16-year-old Skye Whitman was driving to her Sudbury home after a late shift at work. Things were clearing up after heavy rains earlier that night, but as she drove along Bay Street to where it crosses Fairbank Creek, the pavement dropped away and her car plunged into a gaping trench that cut across the road. It was a terrible crash and Whitman was killed.
The culprit was a steel culvert buried under the road that had rusted, leaked and buckled over the years. The rains that day were finally too much and the culvert collapsed, taking the soil column and road surface with it.
Advertisement
Queen’s Civil Engineering Professor Ian Moore is exploring how joints between pipes fail.
It’s easy to take buried pipes for granted, but when they fail, the results can be disastrous. Sewer pipes that leak or collapse can cause environmental damage and high water-treatment costs to cities. Water distribution pipes that leak or break can compromise drinking water. Replacing culverts is expensive and disruptive to traffic. Sometimes buried pipe can be repaired in situ, but that’s expensive, too.
So, how do you design and build systems that are durable and cost effective? How can pipes be repaired and made safe without tearing up the ground or breaking the bank? Researchers at the GeoEngineering Laboratory at Queen’s are trying to answer these questions.
“I’m interested in fundamental engineering behaviour as a scholar, but almost all of my work is directed toward solving practical problems,” says Civil Engineering Professor Ian Moore, who oversees the lab with his colleague Richard Brachman.
Inside the facility are pits where researchers can bury pipe samples under various fill materials. Hydraulic actuators can apply loads at ground level to simulate trucks or heavy equipment parked overhead. Steel pipe can be tested under conditions of accelerated corrosion. Polyethylene pipe can be tested under varying temperatures to examine long-term behaviour over short periods. Joints between pipe sections can be tested for strength and integrity.
The controlled environment lets Dr. Moore and his team “know reasonably precisely what the soil conditions are, which we don’t always know in the field. We can take our time, so we’re not under the gun with contractors, and at the end of the exercise we can load the systems up to collapse.”
Their work defines many current international practices for these structures and guides engineers and builders. And when a company develops new pipe-system components or repair methods, Moore and his team can test the new products.
Unlike culverts, which are typically buried under only a few metres of fill, many sewer and water lines—gravity-fed systems—must be buried tens of metres deep to work properly. In those cases, the weight of the soil column is a bigger factor than that of overhead trucks and equipment. Different conditions call for a different test rig. There is already a deep-burial simulator at the lab, but it “ ” We’re already in a unique position internationally, and we’re going to be extending our capabilities. can accommodate only pipes up to 60 centimetres in diameter under specific fill conditions. To take research to the Equipment/features list: > Full scale buried pipe testing facility > 2000 kN force servo-hydraulic load actuator and control > Two 2.6 MN force servohydraulic load actuators > 500 kN force servo-hydraulic load actuator > 200-channel computer data acquisition system > Nuclear densometer > Dynamic fiber optic analyzer > Total station with several prisms > Skid steer loader > Mini excavator > Forklift truck/extendable boom > Aerial lift platform > Pipe burst simulator Principal investigators include: Dr. Ian Moore Dr. Richard Brachman Dr. Neil Hoult
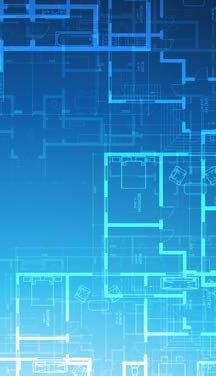
next level, Moore and his team needed something larger and more sophisticated.
Now, thanks to a grant from the Canada Foundation for Innovation, that something is under construction. A 4.5-metre-deep pit has been dug to hold the deep-burial simulator. Ground-level hydraulic actuators will press down on large steel plates to simulate forces applied by tens of metres of soil. Water can be pumped in and out of the pipe samples and surrounding fill to determine the effects of erosion around deeply buried pipes and the joints between them.
“There are lots of fundamental questions nobody has the answers to,” says Moore. “We’re already in a unique position internationally, and we’re going to be extending our capabilities.”
Research gathered will help engineers design water and sewer systems to last longer and leak less. It will inform new ways to maintain and repair pipes without having to dig through tons of earth. It will save municipalities and provinces untold millions and allow them to provide safe and reliable drinking water for years to come.