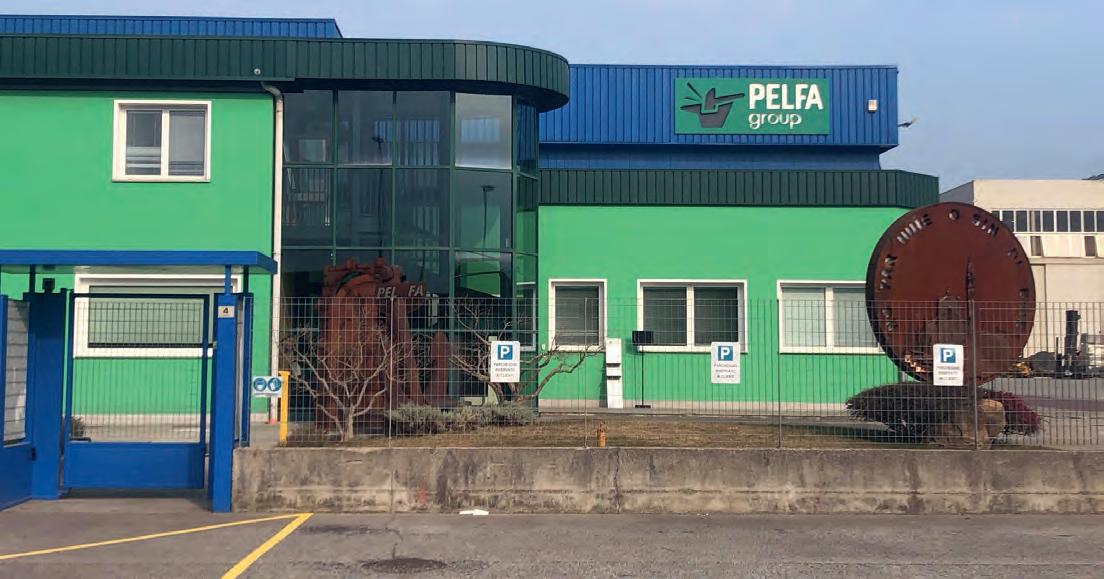
8 minute read
Pelfa Group is expanding its hydropower production capacity
from zek HYDRO 2022
by zek Magazin
photo credit: PELFA Group
For more than 15 years PELFA Group has been a reliable partner in the hydropower industry, proving its competence with a series of international large-scale projects.
Headquartered in Buja near Udine, Northern Italian steelwork engineering specialist PELFA Group is taking its performance capacities to the next level. PELFA is currently delivering variable-speed turbines for hydropower plant Segozerskaya in the Karelia region in Northern Russia. The project is implemented by the world’s second-largest aluminium manufacturer, EN+ Group. For PELFA this marks a further significant business development milestone – yet another impressive proof of the firm’s professional competence and flexibility in serving a variety of markets.
According to business news platform Bloomberg, the overall technical hydropower potential of Russia, the world’s largest country, amounts to a whopping 800 TWh. Currently it is Sibiria’s hydropower potential in particular that is attracting a growing number of investors. One of them is EN+ Group, a conglomerate of Russian aluminium manufacturer Rusal and a group of hydropower operators. Today EN+ Group not only ranks as the world’s second-largest aluminium manufacturer but is also considered Russia’s largest independent energy provider. The firm is currently investing in a series of hydropower plants in Siberia. First and foremost among them is project Segozerskaya in the far Northern region of Russia. This plant is designed to provide the energy for a new data centre, DCLab Karelia. It is a groundbreaking hydropower project not far from the Finnish border, whose implementation involves a number of challenges that had – and still have – to be overcome.
photo credit: zek
KAPLAN TURBINE WITH VARIABLE ROTATIONAL SPEED
“Project Segozerskaya was planned by the Russian planning office PMCB – Power Machine Construction Bureau. They put their full trust in our competence. What makes this particular plant so special are the highly fluctuating water levels of two lakes where the new facility is situated,” explains Andrea Forgiarini, who has been serving as PELFA Group’s CEO since 2004. The machine concept calls for a single-regulation direct flow Kaplan turbine with a diameter of 2.8 m and variable rotational speed. This means that only the guide vane assembly can be regulated. The facility is to be equipped with three identical, horizontally aligned machine units in a highly compact design. “This specific design with variable rotational speed is used because the altitude varies between 1.9 m and 8.6 m up to four times a day. As a result, the rotational speed varies between 60 and 183.3 rpm,” as Forgiarini explains. Owing to the low installation height, and not least because of the cost saving potential, high-speed direct current generators are coupled up
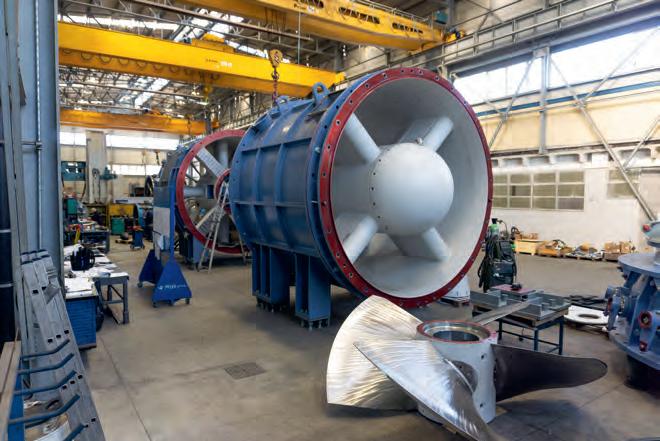
With a total length of around 12 m and a rotator diameter of 2.8 m, the machines for the Segozerskaya power plant in Russia have impressive dimensions.
photo credit: zek photo credit: zek Foto: PELFA Group

For large-scale project HPP Segozerskaya PELFA provided all the machine parts up to, and including, final assembly. Housing components for machine 2 are being worked on at the CNC controlled floor type boring and milling machine.
Once hauled into place, the gearing is shifted into its exact final position.
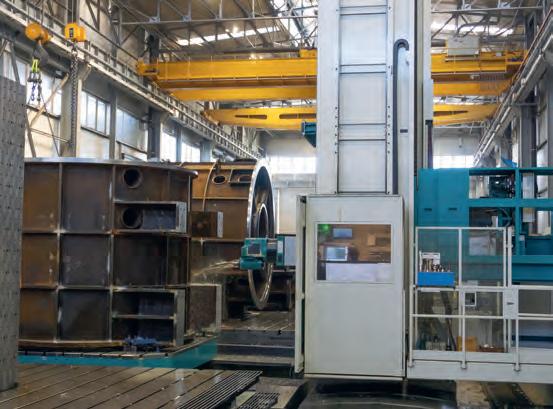
directly to the turbine shaft. A complete machine combination measures around 12 m. It consists of the turbine, a planetary gearing that weighs around 6.7 tonnes and is provided by Czech-based manufacturer WIKOV, as well as a 360 to 1100 rpm high-speed generator, an inverter, and a rectifier unit. However, the turbine shaft is held in place at only two points, resting on a plain bearing and an anti-friction bearing at each point. Except for the drive units, all engineering parts were manufactured, assembled, tested, disassembled again and prepared for transport by PELFA. Final delivery (machine units 1 to 3) wad begun in late April. The generator housings were also manufactured in Buja before they were transferred temporarily to Moscow, where they are to receive their winding from a Russian generator manufacturer. When completed, the power plant is expected to achieve an installed capacity of around 8.1 MW. “We’re proud to be part of this innovative project. Our long-standing experience allowed us to contribute significantly to this sustainable project,” says Andrea Forgiarini. Final installation of the turbine units at their destination nearly 3000 km away is scheduled for 2023.
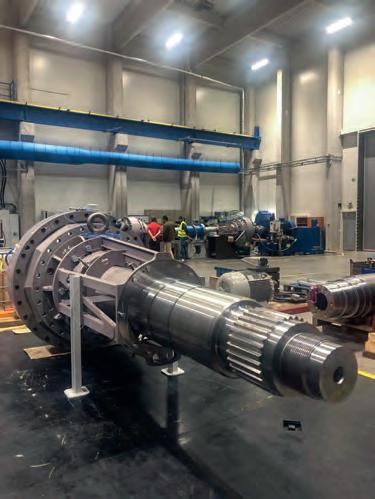
GAINING GROUND IN THE HYDROPOWER SECTOR
With the machine units for this new project in Russia’s Karelia region PELFA has once again proven its efficiency, know-how and great flexibility in serving current market needs. By successfully completing numerous international projects in the face of constantly growing challenges, the firm has by now evolved into a well-established, competent partner in the hydropower industry. However, the firm has risen from very modest beginnings. It was in 1979 when Redento Fabbro founded the firm that was to evolve into today’s PELFA Group. Starting out as a pure steelwork construction operation, PELFA in the following 45 years developed into an industry specialist that today provides a wide product portfolio, from facility construction and machines to mechanical and welded components for a variety of industries on the worldwide market. PELFA Group is a tradition-steeped provider that specialises in the manufacture of large-scale products for the steel industry, from construction to assembly of plant components or fully equipped systems, including ladle carriages, turrets, ladle tilters, oscillators, continuous casting segments, straightening machines, stave coolers, flame cutters, roller conveyors, roll stands, and shearing machines. The firm also serves the oil and gas sectors with a variety of equipment for plant components that are custom tailored to suit the individual requirements of its international customer base. Further business segments that profit from PELFA Groups’s long-standing experience in manufacturing industrial components include civil engineering, industrial equipment engineering, earth moving, hoisting technology, and even the recycling industry. PELFA covers the entire production process, from receipt of order to the final ‘turnkey’ product. All processing steps can be performed on-site, including comprehensive contract management, engineering, materials purchasing, cutting of sheet metals and structural shapes, pressing, bending, calendering, welding, heat treatment, machining, sand blasting and painting, as well as pre-assembly and mechanical final testing. The mid-sized industrial firm currently employs about 150 staff, generating an annual turnover of around € 30 m. On its premises with 70,000 sqm floor space, PELFA Group processes around 15,000 tonnes of steel each year.
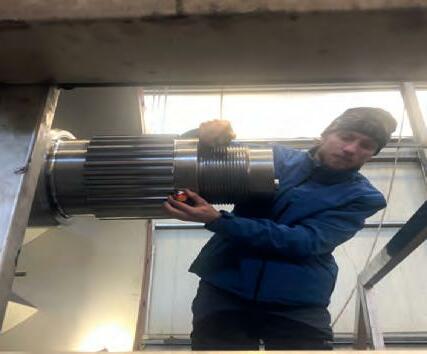
INVESTING IN THE HOME BASE
Steady investment in new machine generations is a proven, forward-looking strategy, especially when it comes to maintaining a competitive edge in completing orders. “This creates added value, both environmentally and in terms of technological progress. And it boosts quality along the entire production chain,” says Andrea Forgiarini. The firm has invested around € 5 m in its local facilities in 2021 alone. To further optimise the manufacturing processes, a large-scale boring mill with a working height of 3.5 m, a fully equipped processing centre, and a new grinder for cylindrical components with lengths of up to 8 m have
photo credit: PELFA Group
Each of the three machine units is being fitted with a 6.7-tonne planetary gear by Czech gearing manufacturer WIKOV. The transport lock doubles as an installation aid.
A surveying technician from DS Machine (also headquartered in the Czech Republic) is finetuning the turbine shaft’s exact positioning.
photo credit: PELFA Group
been installed. This enables streamlined workflows, allowing projects to be implemented even more efficiently. The engineers’ specialist skills need consistent further development as well: “To be ready for future challenges, we have reinforced our staff training programmes and intend to expand them even further in the future,” says Forgiarini. Another priority at PELFA Group is the improvement of air quality in its production halls. The firm’s management is currently reviewing various concepts to reduce dust pollution throughout the entire production environment. Also high up on PELFA’s list of priorities is sustainability. The in-house photovoltaic system was upgraded only recently by a full 200 kW. Together with the existing system, the firm is profiting from a panel area with a total output of 500 kW, which covers around 60 to 70 percent of energy costs. “Combined with our newly installed LED lights, this translates into overall cost savings of around 80 per cent,” says Forgiarini.
HYDROPOWER: ALL COMPETENCIES UNITED IN-HOUSE
Staying its course through the crisis of 2008, the firm has since increased its focus on the energy sector, which proved a highly successful move. In addition to hydropower equipment, PELFA today also provides components for wind power, offshore, oil and gas projects, as well as for the nuclear energy sector. The majority of business activities is dedicated to the hydro sector, which accounts for more than 60 per cent of the firm’s productive capacity, as Forgiarini explains. PELFA Group offers all their products in the form of turnkey solutions, from individual turbine components to fully assembled machine units in various designs, including Francis, Kaplan and Pelton turbines, as well as hydrodynamic screws. All production steps are performed at the firm’s premises. Apart from the manufacture of new facilities, PELFA also provides the services required for overhauling and restoring existing ones. “In recent years we have acquired all the necessary knowledge to manufacture high-quality system components for hydropower projects, and to repair and service existing facilities. By now we have consolidated all these competencies in-house. And that’s precisely our strong point,” says Forgiarini. This comprehensive knowledge, as well as the firm’s reliability in terms of contract implementation and deliveries, have convinced a long list of hydropower businesses to choose PELFA Group as a trusted project partner.
photo credit: zek
Left to right: Erich Feldtänzer, Regional Head of Sales for German-speaking markets, Igor A. Zharov, Head of Technology at PMCB, J. Hovorka, DS Machine.
