
20 minute read
Kelag commissions new showcase power plant [ MONTENEGRO
from zek HYDRO 2021
by zek Magazin
Mithilfe von Bruchsteinen und Schüttungen wurde die Wasserfassung The Vrbnica power plant in far north-west Montenegro für das neue Kraftwerk Alvierbach im Vorarlberger Brandnertal has been in operation since November last year. The new naturnah gestaltet. Die Anlage, die seit Februar letzten Jahres small power plant with an installed capacity of 6 megawatts in Betrieb ist, erzeugt grünen Strom für rund 1.700 Haushalte. was built by Kelag's subsidiary Interenergo d.o.o. The energy transmission through the wooded hills had to be specifically built for this.
KELAG COMMISSIONS NEW SHOWCASE POWER PLANT IN MONTENEGRO
photo credits: Interenergo
Foto: zek
In autumn 2020, KELAG-Kärntner Elektrizitäts-Aktiengesellschaft commissioned a new small hydropower plant in northwest Montenegro. The energy service provider carried out the project over a period of three years with its Slovenia-based subsidiary Interenergo d.o.o. Kelag did not just pay special attention to the technical design of the 6 MW power plant, it mainly paid attention to winning over the Montenegrin population. Numerous discussions were held in the run-up to the project, local residents were included in the plans and the benefits of the project as well as the unavoidable impact on surrounding nature were communicated in a clear and transparent way. The operators used modern Coanda systems from Wild Metal GmbH, the South Tyrolean hydraulic steelwork specialist, in order to operate the power plant with as little maintenance as possible.
Montenegro is seen, quite rightly, as a hydropower country. The hydropower plants in this small Balkan state produce around 5.4 billion kWh per year (Source: Laenderdate.info). This means that hydropower provides the lion's share of around 69 % of the country's total electricity generation. One of its hydropower plants stands out from the rest and is known beyond the county's local borders: It is the Piva power plant which has a total installed capacity of 360 MW. This is a megaproject dating from the Yugoslavian era which was realized in the first half of the 1970s. Mratinje dam's specially built 220 m high concrete arch dam was one of the highest in the whole of Europe for a long time. The damming led to the formation of the Piva Lake, which is Montenegro's second large lake covering 12.5 km2. The small town of Plužine, which was lost in the process, was rebuilt on the shores of the dam. All that was preserved was the famous Piva Kloster, which was previously removed piece
by piece and later reconstructed at its new location from the original pieces.

A NEW SINGLE-STAGE POWER PLANT CONCEPT Plans were simultaneously pored over during the implementation of the project, such as how to get the best possible use out of the body of water in the upper reaches. Taking the Vrbnica River as an example, engineers from Titos had envisaged a three-stage project with a small dam wall. However nothing was to come of it, as Sebastjan Rozman, engineer at Interenergo and proven expert in all questions relating to hydropower in the Bal-
photo credits: Interenergo
kans, confirms: “Such a project would come nowhere close to being approved today". It was therefore obvious to us that we required a completely new concept at this site. The question that we'd been asking ourselves for a long time was: Should we build two stages, or will it work with one?" Interenergo subsequently carried out preliminary investigations at the site and developed the first project designs with the Kelag planning team in 2015. It became apparent that the optimal solution would be a single-stage high pressure power plant with a 6-jet pelton turbine. This would also determine the winner of the 2017 internal concession tender. Mountains scatter the region close to the border with Bosnia-Herzegovina, reaching 2,000 m above sea level, along with woodland. An area where questions of accessibility were raised, and energy transport do not play an insignificant role.
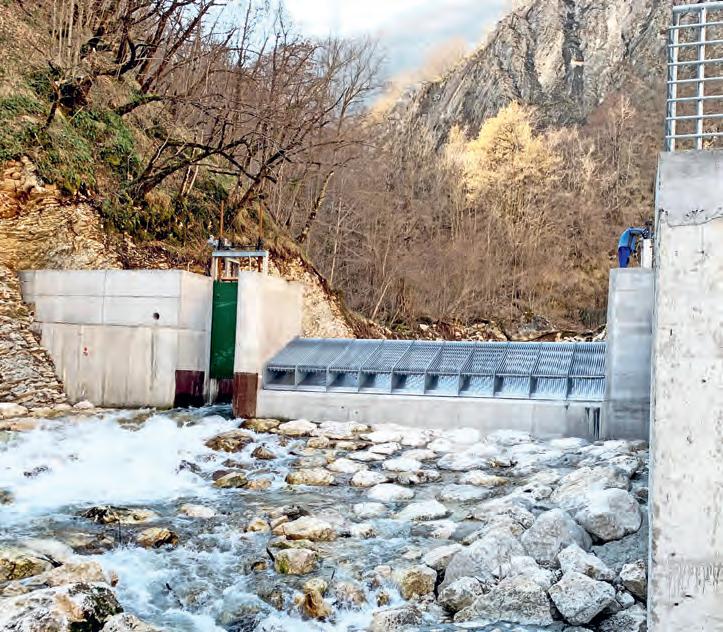
UPHILL STRUGGLE FOR BACKING However, the challenges of the technical realization caused the team fewer headaches than the social aspect of the project. "You can have approval by the State in Montenegro, but if you don't have the support of the Montenegrin population and each of the affected municipalities and residents, you don't build. This causes so many projects to fail”, explains project manager Sebastjan Rozman, adding: “It was therefore part of our strategy to involve the local population and all those affected as much as possible in the project. That was very time-consuming and roughly took a year but was ultimately the reason for the project's success. Some of things that we endeavoured to do was to create a synergy effect so that the municipalities, the local residents and the population also benefited. Evidence of this was the construction of a penstock whose route followed a country road where a drinking water pipeline had been built covering long stretches of land. The old drinking water supply network had already reached the end of its technical service life, therefore a decision was made to replace it when laying the new pipes. Another example was a small tunnel through which the mountain road leads: "The rockfall gallery had to be urgently restored. Therefore we came to a compromise with the community in which we would restore the tunnel from top to bottom. In return we were allowed to lay the pressure pipeline here," says Rozman. A win-win situation for both parties.
Foto: illwerke vkw A Coanda system of the type Grizzly Protec Vibro Bars 2500 from Wild Metal was installed for water catchment. The 10 Coanda modules are designed with a suction capacity of altogether 3,000 l/s.
Aufgrund des äußerst starken Grundwasserdrangs wurde die Baustelle komplett umspundet.
MAINTENANCE-FREE SOLUTIONS The small power plant is a high-pressure system that uses water from the Vrbnica. A Tyrolean weir with an installed Coanda system was built at 980 m above sea level for this purpose, downstream from a small desanding structure. The operators opted for the Grizzly Protec Vibro Bars 2500 System by Southtyrol-based Wild Metal, a company well-known in the industry. This type of rake is a further development of the well-known Grizzly Protec. Like its classic predecessor, it consists of a coarse screen and an underlying fine screen. The special placement of the protection bars prevents material i.e. bed load or floating debris from settling or causing jams. This reduces the already minimal maintenance costs and increases the operating reliability even in winter.
photo credits: Interenergo
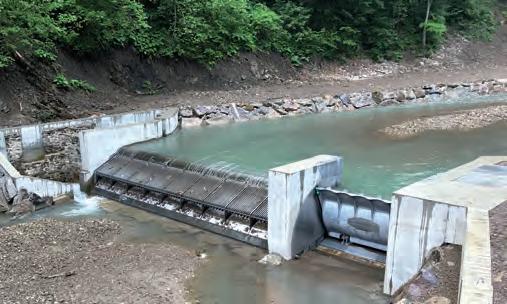
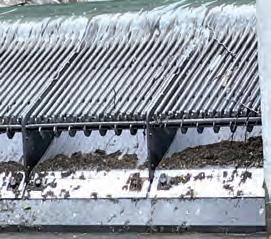
Wild Metal GmbH
• Hydraulic steelwork • Patented Coanda-system GRIZZLY • Trash rack cleaning machines • Different type of gates • Safety valves • Different fine and course screens • Entire water intake system made of steel
Wild Metal GmbH Handwerkerzone Mareit Nr. 6 • I-39040 Ratschings (BZ)
Tel. +39 0472 759023
Fax +39 0472 759263 www.wild-metal.com info@wild-metal.com We clean water
Foto: zek Foto: MUHR Foto: MUHRphoto credits: Interenergo
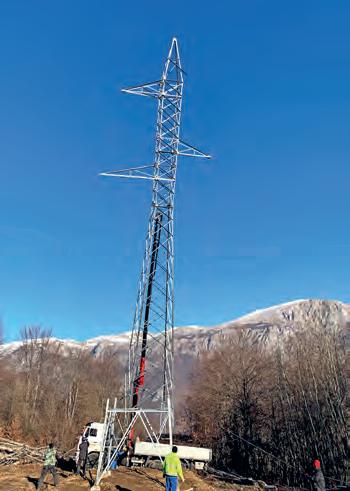
GRP pipes of the type Superlit DN1400 type (picture on the left) were laid over a total distance of around 3 kilometers. The pipe route largely followed an existing country road.
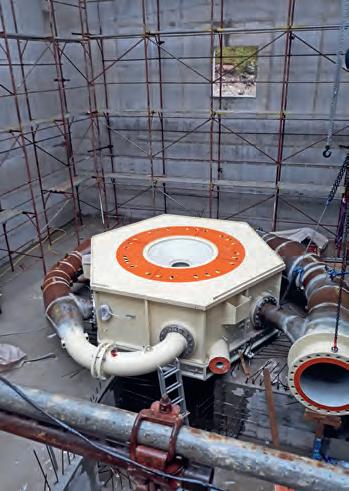
Image to the left: Turbine assembly: The volute casing and distribution pipeline were delivered and lifted into position in May last year. It is a 6-jet vertical axis Pelton turbine with 6 MW of power. Image to the right: The construction works for the construction of the 8 kilometre long 35 kV power line took approximately one year.
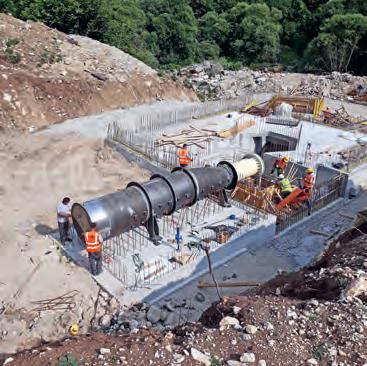
CONSTRAINTS OF SPACE WHEN INSTALLING PIPES The work water is then fed from the desanding structure into a penstock which was built using GRP pipes manufactured by Superlit. The route extends over around 3000 m from the water catchment to the power house and overcomes a natural gradient of around 263 m. Most of the pipeline was laid in the existing country road. The plastic pipes, reinforced with glass fibre, proved not only to be the most economical solution for the penstock, but also a very practical one. Last but not least, the low weight eases handling and installation. In specific terms, the pipes that were used had a pressure class of PN16 to PN32 with a diameter of DN1400. Rozman mentions the confined space as the main constructural challenge: "Since the drinking water pipe had been laid in the road over a large distance, the space for the pressure pipes was quite narrow in many areas of the narrow mountain road, since around 2.5 m was required along with bedding."
photo credits: Interenergo ELABORATE CONSTRUCTION: CONSTRUCTION OF THE HIGH-VOLTAGE LINE The power house, where the mechanical heart of the system is located, was built at around 718 m above sea level: a 6-jet, vertical-axis Pelton turbine, designed for an expected 30 to 40 days full load. The turbine has a power rating of 6.4 MW, with a suction capacity of 3 m3/s. It drives a brushless, directly coupled synchronous generator at 600 rpm. A powerful, robust machine that guarantees a reliable power supply for centuries. The new Vrbnica power plant will generate around 18.5 GWh of clean electricity in a normal year, which meets the needs of around 8,000 households. The energy is transported via an 8 km long 35 kV line, which had to be specially built for this purpose. "The energy transmission from the dam was quite clearly one of the key challenges of the project. The terrain through which it leads is rugged, steep in areas, densely wooded and difficult to access. It therefore took around a year to erect the high-voltage line, including a substation", remembers Rozman. The high-voltage equipment, the substations and the transformers were realized by Siemers, as well as the entire control and pneumatical machinery of the power plant.
photo credits: Interenergo FLOODING AND CORONA PULL THE BRAKES The course of the construction work in the remote mountainous region of north-west Montenegro would ultimately prove to be very challenging, as civil engineer Rozman confirms: "We were confronted with several smaller and larger challenges". This con-
Technical Data
• Flow Rate: 3.0 m3/s • Head: 263 m • Turbine: 6-nozzle Pelton Turbine • Nominal Output: 6.4 MW • Generator: Synchronous Generator • Runner Speed: 600 rpm • Desanding: Coanda-System • Manufacturer: Wild Metal • Type: Grizzly Protec Vibro Bars 2500 • Rake Field Width: 11.5 m Modules: 10 pcs. • Clearance Fine Screen: 1.0 mm • Intake Capacity: 3.000 l/s • Coarse Screen: Clear Width: 30 mm • Penstock: DN1400 Length: 3.050 m • Material: GRP Manufacturer: Superlit • PN16 - PN32 SN10.000 • Electrical Equipment & Control: Siemens • Commissioning: November 2020 • Average Output: 18.5 GWh p.a.
photo: zek


photo credits: Interenergo An efficient yet extremely low-maintenance solution for water catchment: the Coanda system by Wild Metal. Project manager Sebastjan Rozman from Interenergo on the construction site.
Foto: illwerke vkw photo credits: Interenergo
cerned securing an unstable slope, or also reinforcing one or the other bridges on the access routes. This also presented logistical questions: For instance, the trucks were not allowed to exceed a certain height or weight." Yet it was the torrential nature of the Vrbnica that caused the largest number of headaches, causing some minor floods and two severe floods. "Thankfully, there were no injuries, however a few structures and sheet pile walls were torn away, which led to small delays". Another difficulty which by far caused the greatest loss of time was Corona. The pandemic slowly began to hamper the progress of the work. "Unfortunately not all work can be done via "remote-control." You often need to have specialists on site. We ran into certain obstacles as travelling in particular, but also opportunities for subcontractors, were limited. Great flexibility was needed to progress the audit in the difficult phase. We likely lost half a year due to Corona" said the project manager.
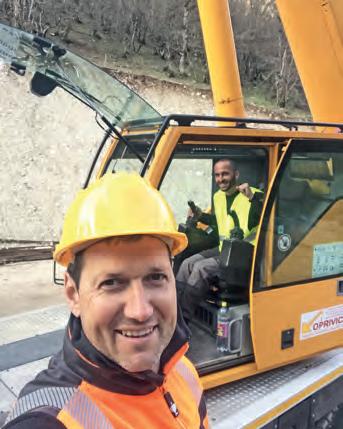
The rockfall gallery was renovated at the same time as the pipes were laid. INVESTOR WITH RESPONSIBILITY The final milestone was finally reached in November last year: The Vrbnica power plant fed electricity to the public grid for the first time. Since then the plant is in the first few months of operation and has already proven its operative worth. Nowadays it not only makes an important contribution to the region's supply, but also serves to stabilize a distribution network that is not always entirely secure, as Rozman confirms: "There always used to be power failures in this area during the winter. The new power plant is now helping to reduce these power failures to a minimum." With almost 19 GWh of standard operational capacity, it is a small hydropower plant, yet one of the largest in the country. "Strictly speaking it is actually the third largest hydropower plant in Montenegro", according to Rozman. He does see significant potential for further expansion, but a strong headwind for new projects. "NGOs voiced their disapproval for a new power plant. The main reason for this is that it is not only serious investors who tender. We can only distance ourselves from that. After all, we see ourselves a longterm owner who has responsibility towards nature, the environment and the local population; we are not short-term speculators. We decommission a power plant if, for example, too little water flows. Unfortunately, this does not apply to all investors in the Balkans. Rozman: There must be more positive examples like that of KW Vrbnica so that new power plants in the Balkans are not categorically refused. This would be twice as regrettable especially in the case of Montenegro, but at the same time the country does have the highest hydropower potential per inhabitant in the whole of Europe.

photo credits: Interenergo
The power plant produces around 18.5 GWh of clean electricity during a normal year.

photo credits: Interenergo

Foto: Rittmeyerphoto credits: Global Hydro
The new Holsvirkjun power plant in northern Iceland. Equipped by Global Hydro with the latest technology it contributes significantly to a reliable power supply in the small town of Akureyri.
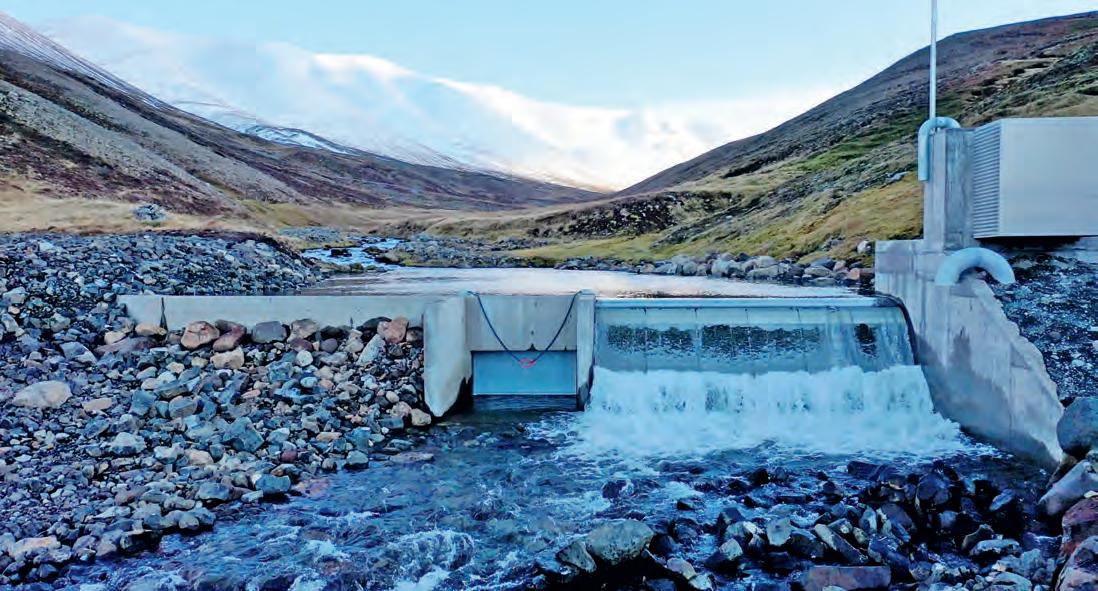
UPPER AUSTRIAN HYDROPOWER SPECIALIST EQUIPS INNOVATIVE ISOLATION-MODE POWER STATION IN ICELAND
Last summer, at the northern end of Iceland, the Holsvirkjun hydroelectric power station, yet another small-scale hydropower plant went online in an island state dominated by hydroelectric production. The plant was equipped to the very latest standards of hydropower technology, most of the infrastructure being provided by the internationally active Upper Austrian hydropower specialists at Global Hydro. As well as the 6-nozzle 6.7-MW Pelton turbine, the turnkey provider also supplied the entire control infrastructure for the power plant, the latter being the central technical pillar of the project. Ultimately, the aim was to guarantee a sophisticated regulation approach to balance out the peaks and troughs in demand on the grid serving the small local town of Akureyri, the frequency deviations, and for the plant to be able to guarantee isolated operation.
Iceland is a country with far more to offer than glaciers, volcanos and geysers. It is also a country of hydroelectric power production. No less than three quarters of the island’s energy demands are covered by hydropower plants. Hence, the island in the far north of Europe is one of the continent’s hydropower hotspots. Experienced hydroelectric station managers are increasingly relying on the practical and theoretical expertise offered by businesses from the central alpine regions – businesses like Global Hydro Energy. The innovative Upper Austrian hydropower specialists have already successfully implemented around 30 hydroelectric projects in Iceland. One of their latest reference projects is the Holsvirkjun hydropower plant in the north of the island – a drive of around 30 minutes from the small town of Akureyri. The order to equip the smallscale hydropower plant in the north of the island was submitted to the Upper Austrian water power experts by Orkuver, a local Icelandic partner, at the end of January 2019. The comprehensive overall order was for a vertical 6jet Pelton turbine, a ball inlet valve, hydraulic generator, synchronous generator, and for the plant’s electrical and control infrastructure. The contract was successfully completed over the following 16 months. POTENTIAL FOR GRID OPTIMISATION Preparations for the Holsvirkjun smallscale hydroelectric power plant had been underway since 2011. The goal was to realise a significant improvement to the previously unsatisfactory grid power supply to the small town of Akureyri. Until recently the power
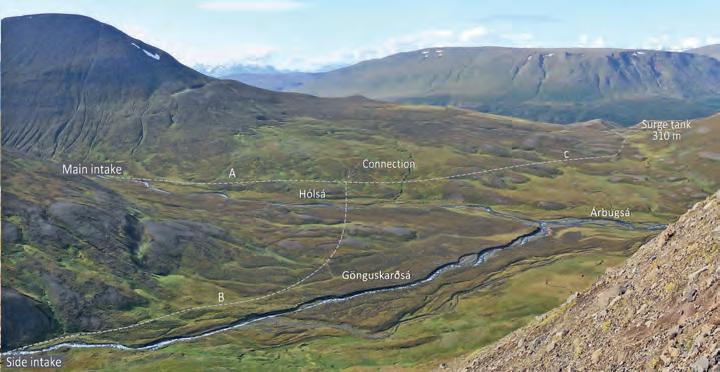
photo credits: Global Hydro
The new plant harnesses the power of rivers from two different valleys.
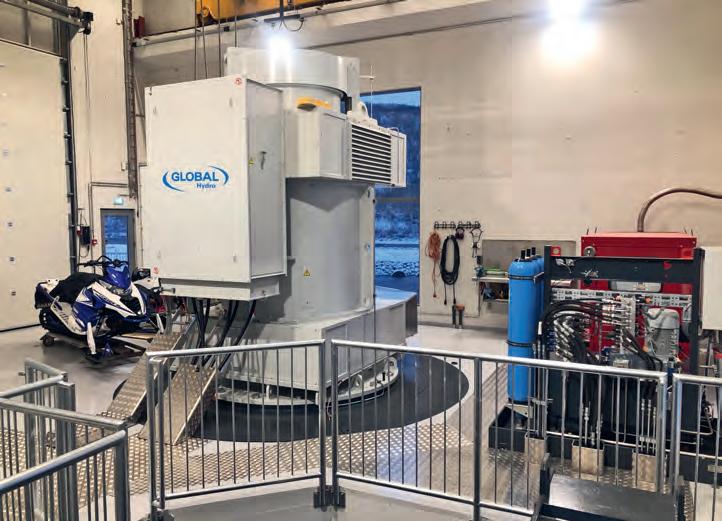

supply had been dependent upon several diesel generators; an unacceptable situation for a country with such a climateconscious population. Following a comprehensive period of preliminary planning, a concept was developed for a plant served by two separate rivers – and was finally ready for implementation in 2018. This required the construction of two transverse structures to produce a certain degree of water volume buildup. Philipp Meindl, Global Hydro’s project manager, outlines the operation of the plant as follows: “The two reservoirs were established in their respective valleys at approximately 315 m above sea level. The penstocks leading down from each reservoir join in a surge tank at around 310 m above sea level, from which the works water is guided down a single pipeline to the machine room at just 60 m above sea level.” The penstock down to the power house consists of about 6000 m of glassfibrereinforced piping (GRP) and transports a maximum water volume of 3.2 m³/s.
SPECIAL TURBINE HOUSING The power house was given a compact design that blended well with Iceland’s natural surroundings. A 35ton indoor crane was installed in order to manoeuvre the heavy machinery and components correctly, and for conducting maintenance tasks. Delivery of the electromechanical infrastructure postponed until last March due to construction delays caused by extreme weather at the construction site. The machines were transported from the Global Hydro works in Niederranna to Rotterdam, and from there to Reykjavik by ship. The experience, expertise and technical flexibility of the Upper Austrian turbine manufacturers were also required to find the best way of arranging and installing the turbine to suit local conditions. Philipp Meindl explains: “Part of our job is to adapt solutions to the prevailing conditions on site and to the special requirements expressed by the customer. In this case the customer asked for welding activity at the plant to be kept to a minimum. The response of our construction designers was to produce a solution for the turbine housing that involved just one single screwed joint, although the overall diameter was around 7 metres.” Global Hydro sent two supervisors to Iceland to ensure all challenging assembly procedures ran smoothly – one for mechanical and one for the electrical aspects of installation. Obviously, protective Corona rules and restrictions also had to be strictly adhered to, as did the legallyrequired quarantine measures, all of which was subject to continuous monitoring.
photo credits: Global Hydro Foto: PI Mitterfellner The vertical-axis 6-nozzle Pelton turbine drives a directly coupled synchronous generator. It has been set up to produce around 6.7 MW of power.
COMPENSATION OF LOAD JUMPS The main challenge for the Global Hydro team was to guarantee island mode operability; a common requirement in and on Iceland
Global Hydro is an experienced turnkey hydroelectrics provider and also delivered the DN800 PN40 ball inlet valve.
photo credits: Global Hydro
Technical Data
• Flow Rate: 3.2 m3/s
• Head: 235 m
• Turbine: 6-nozzle Pelton turbine
• Manufacturer: Global Hydro • Runner Speed: 600 rpm • Nominal Output: 6,686 kW • Generator: Synchronous • Control & Communication: Global Hydro • System control: HEROS Connect • Water Catchment: Coanda-System Wild Metal • Penstock: Length: approx. 6,000 m • Material: GRP
• Ball Inlet Valve: DN800 PN40
• Commissioning: August 2020
photo credits: Global Hydro
Global Hydro supplied the entire control infrastructure, the medium-voltage system (left), the main transformer and the auxiliary transformers.

– in this case to compensate power demand changes of up to 600 kW within a maximum frequency deviation of 2 Hz. “Variations of this scale can account for around 10% of the turbine’s intended output. This would require an immense change of momentum which, in view of the weight involved, would negatively affect the working life of the bearing. That’s why we settled for another, more intelligent solution,” Philipp Meindl stated. The sophisticated hydraulic regulator meant equipping the Pelton turbine’s six jet cutouts with a specially devised hydraulic valve, allowing the jet cutouts to be precisely positioned within 700 to 800 milliseconds, so any power demand changes can be detected and compensated for in a fraction of a second. In the engineering phase a CFD simulation of a cutoff device designed especially for the purpose showed that the jet could be cut cleanly without being destroyed, thus avoiding damage to the Pelton wheel. When tested in practice in Iceland, the sophisticated solution was an immediate success. Meindl: “In cooperation with RARIK, the local Icelandic energy corporation, the system was put through a latenight test, and the plant easily coped with power consumption variations of 700 kW and frequency deviation of 1.7 Hz.”

MODERN CONTROL SYSTEM All machines, auxiliary and support generators are also controlled and monitored by the HEROS power plant management system developed by Global Hydro. Specifically, HEROS Connect was the system chosen, and was enhanced by linking up to an intuitive web application. Hooking up to HEROS Connect enables the customer to check the operational status and condition of the turbine, simply and without the installation of software. The broad spectrum of functions offered by the automation solution enables the operators to choose from a variety of operational options, as project manager Philipp Meindl details: “The large dimensions of the 60,000 m³ intake reservoir ensure a customer using the HEROS system has great flexibility in terms of adjusting to grid requirements. Theoretically, the plant could work at full capacity for over five hours without any additional water. There’s also a preprogrammable calendar function to allow the output to be set in advance for any part of a day, on any day. Furthermore, HEROS automatically regulates the turbine when works water is lost over the edge of the overflow.”
photo credits: Global Hydro CUSTOMER CONFIRMS SUCCESS The heart of the power plant is a 6jet Pelton turbine that generates 6,686 kW from a head of 235 m and a capacity flow volume of 3.2 m³/s. This drives a synchronous generator directly coupled to the vertical shaft at a speed of 600 rpm. The newlyinstalled machine group guarantees efficient and, most importantly, reliable operation for the coming years and decades. After being successfully installed at the beginning of June 2020, the system commenced gridparallel power generation at the start of August. The new Holsvirkjun power plant is another key building block in Iceland’s strategy of expanding its use of renewable resources. Furthermore, the plant has now taken on the important task of guaranteeing the stability of grid power provision for the town of Akureyri. It is equipped to secure island mode operation and black start capacity. The success of the implementation was convincingly confirmed by the same Icelandic customer, who in the meantime awarded a subsequent project to Global Hydro.
The generously-sized intake reservoir stores up to 60,000 m3 of works water.