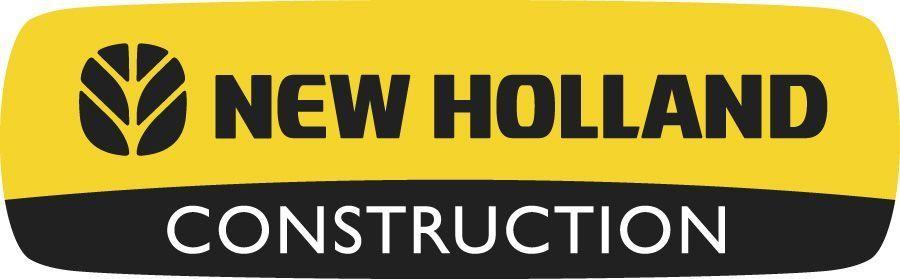
SER VICE MANUAL
E215C Standard model
E245C Mass excavator model
Engine
INTRODUCTION
[10.001] Engine and crankcase
[10.202] Air cleaners and lines
[10.216] Fuel tanks
[10.254] Intake and exhaust manifolds and muf fler
Engine cooling system
Hydraulic systems
[35.000] Hydraulic systems
[35.102] Pump control valves
[35.106] V ariable displacement pump
[35.300] Reservoir , cooler , and filters
[35.304] Combination pump units
[35.352] Hydraulic swing system
[35.353] Hydraulic travel system
[35.355]
[35.356] Hydraulic foot control
[35.359] Main control valve
[35.736] Boom hydraulic system
[35.737] Dipper hydraulic system
[35.738] Excavator and backhoe bucket hydraulic system
Frames and ballasting
Upper frame
Swing ring assembly
Ballasts and supports
T racks and track suspension
T rack frame and driving wheels
T racks
T rack tension units
T rack rollers
Cab climate control
[50.100] Heating
[50.200] Air conditioning
Electrical systems
Electrical system
Engine control system
Hydraulic system control
Cab V and (HV AC) controls
Battery
Electronic modules
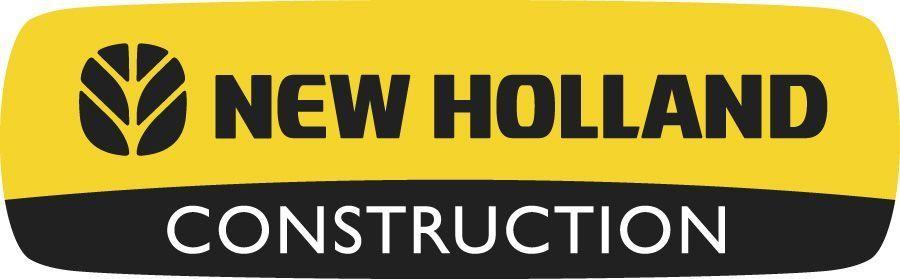
T orque – Bolt types
Basic instructions - Shop and Assembly
T orque Minimum tightening torques for normal assembly
T orque - Standard torque data for hydraulics
General
Advice - Important notice regarding equipment servicing
All repair and maintenance work listed this manual must carried out only qualified dealership strictly complying with the instructions and whenever the special
Anyone who performs repair and maintenance operations without complying with the procedures provided herein shall responsible for any subsequent
The manufacturer and all the organizations its distribution chain, including - without limitationnational, regional, local reject any responsibility for damages caused parts and / components not approved the facturer , including those used for the servicing repair the product manufactured marketed the manufacturer any case, warranty given attributed the product manufactured marketed the manufacturer case damages caused parts and / components not approved the manufacturer
The information this manual - - date the date the the policy the manufacturer for continuous Some information could not updated due modifications a technical commercial type, changes the laws and regulations dif ferent countries. case refer your Sales and Service
Foreword - Ecology and the environment
air , and water are vital factors agriculture and life
When legislation does not yet rule the treatment some the substances required advanced technology , sound judgment should govern the use and disposal products a chemical and petrochemical nature.
NOTE: The following are recommendations that may assistance:
• Become acquainted with and ensure that you understand the relative legislation applicable your country
• Where legislation exists, obtain information from suppliers oils, filters, batteries, fuels, antifreeze, cleaning with regard their fect man and nature and how safely and dispose these
• Agricultural consultants many able help you
Helpful hints
• A void filling tanks using cans inappropriate pressurized fuel delivery systems that may cause considerable
• avoid skin contact with all Most them contain substances that may harmful your
• Modern oils contain additives. not burn contaminated fuels and waste oils ordinary heating systems.
• A void spillage when draining f used engine coolant gearbox and hydraulic brake not mix drained brake fluids fuels with lubricants. Store them safely until they can disposed a proper way comply with local legislation and available
• Modern coolant antifreeze and other should replaced every two They should not allowed get into the but should collected and disposed properly
• not open the air - conditioning system contains gases that should not released into the Y our NEW HOLLAND CONSTRUCTION dealer air conditioning specialist has a special extractor for this purpose and will have recharge the system properly
• Repair any leaks defects the engine cooling hydraulic system immediately .
• not increase the pressure a pressurized circuit this may lead a component
• Protect hoses during welding penetrating weld splatter may burn a hole weaken allowing the loss

Safety rules DANGER
Improper operation service this machine can result accident. not operate this machine perform any lubrication, maintenance, repair until you have read and understood the operation, lubrication, maintenance, and repair information. Failure comply will result death serious injury
D0010A

W ARNING
Maintenance hazard!
Always perform all service procedures punctually the intervals stated this This ensures optimum performance levels and maximum safety during machine operation.
Failure comply could result death serious injury . W0132A

W ARNING
Pressurized system!
Before attempting any service procedure, your responsibility know the number accumulators the and the correct procedure for releasing the pressure each accumulator
Failure comply could result death serious injury .
NOTICE: Extreme working and environmental conditions require shortened service
W0136A
Use Case fluids, lubricants, and filters for the best protection and performance your machine. All fluids, lubricants, and filters must disposed compliance with environmental standards and Contact your dealer with any questions regarding the service and maintenance this
Read the safety decals and information decals the Read the Operator ’ s Manual and safety Understand the operation the machine before you start any
Before you service the put a Not tag the steering wheel over the key Ensure the tag a location where everyone who might operate service the machine may see clearly One tag included with your new machine. Additional tags are available from your dealer .
Plastic and resin parts
• A void using gasoline, paint thinner , etc. when cleaning plastic parts, console, instrument cluster , etc.
• Use only water , mild and a soft cloth when you clean these
• Using gasoline, thinners, etc. can cause discoloration, cracking, deformation the part being cleaned.
Safety rules
Standard safety precautions
informed and notify personnel the laws force regulating safety , and provide documentation available for
• Keep working areas clean
• Ensure that working areas are provided with emergency They must clearly visible and always contain adequate sanitary
• Fire extinguishers must properly identified and always clear Their ficiency must checked a regular basis and personnel must trained proper interventions and priorities.
• Keep all emergency exits free obstructions and clearly
• Smoking working areas subject fire danger must strictly prohibited.
Prevention injury
• W ear suitable work attire and safety glasses with jewelry such rings and chains when working close engines and equipment
• W ear safety gloves and goggles when performing the following operations:
• T opping f changing lubrication
• Using compressed air liquids a pressure greater than 2 bar ( psi )
• W ear a safety helmet when working close hanging loads equipment working head
• Always wear safety shoes and fitting
• Use protection cream for
• Change wet clothes soon
• the presence voltages exceeding - V , verify the ficiency the ground and mass electrical Ensure that hands and feet are dry and use isolating foot W orkers should properly trained work with electricity .
• not smoke start open flame close batteries and any fuel
• Place soiled rags with diesel fuel solvents specially provided anti - fire
• not use any tool equipment for any use other than what was originally intended for Serious injury may occur
• running engine make sure there a suf ficient exhaust fan use eliminate exhaust
During maintenance
• Never open the filler cap the cooling system when the engine High temperature liquid operating pressure could result serious danger and risk W ait until the temperature decreases under ( 122 )
• Never add coolant overheated engine and use only appropriate
• Always work when the engine turned Certain circumstances require maintenance a running aware all the risks involved with such operation.
• Always use adequate and safe containers for engine fluids and used
• Keep engine clean any spilled fluids such oil, diesel fuel, and chemical solvents.
• Use solvents detergents during maintenance may emit toxic Always keep working areas W ear a safety mask necessary
• not leave soiled rags that may contain any flammable substances close the
• Always use caution when starting engine after any work has been prepared cut f intake air case engine runaway
• Never disconnect the batteries while the engine
• Disconnect the batteries prior performing any work the equipment.
• Disconnect the batteries place a load them with a load tester
• After any work verify that the battery clamp polarity correct and that the clamps are tight and safe from accidental short circuit and
• Before disconnecting any pipelines fuel verify that all pressure has been T ake all necessary precautions bleeding and draining residual Always wear the proper safety
• not alter the lengths any wires.
• not connect any electronic service tool the engine electrical equipment unless specifically approved NEW HOLLAND
CONSTRUCTION
• not modify the fuel system hydraulic system unless approved NEW HOLLAND CONSTRUCTION Any unauthorized modification will compromise warranty assistance and may fect engine operation and life
For engine equipped with electronic control unit
• not weld any part the equipment without removing the control
• Remove the case work requiring heating over ( 176 )
• not paint the components and the electronic
• not alter any data filed the electronic control unit driving the Any manipulation alteration electronic components will void engine warranty assistance and may fect the correct working order and life span the engine.
Respect the Environment
• Respect the environment should primary importance. T ake all necessary precautions ensure safety and
• Inform the personnel the laws regarding the dispensing used engine
• Handle batteries with storing them a well ventilated environment and within anti - acid container
Personal safety
Safety precautions
• Before servicing air conditioning read and comply with the following safety Make sure that any repairs are performed duly trained and skilled personnel only
• Never attempt remove the air conditioning Refrigerant leaks can cause serious burns the eyes and
• The refrigerant must always handled very carefully order avoid
• Keep the refrigerant packaging well the air conditioning system away from flames heat the resulting increase pressure may cause the package system explode.
• there direct contact with naked flames heated metal the refrigerant will decompose and will produce toxic products and
• Never discharge refrigerant into the A certified refrigerant recovery unit operated a technician should used repair air conditioning
• When discharging the refrigerant the a well - ventilated area with perfect air circulation and away from naked
• When charging discharging the system, always wear safety goggles and take adequate precautions protect the face general and the eyes particular , case accidental refrigerant
• The refrigerant and oil mixture inside the air conditioning system pressurised. Because this, never loosen the joints work with the tubes without first depressurising the
• Before loosening any connector , cover with a thick rag and use goggles and gloves prevent the refrigerant from coming into contact with the skin accident does proceed follows:
• refrigerant gets into the eyes, wash immediately with copious amounts distilled tap water , and take the victim hospital for specialist medical
• refrigerant comes into contact with the skin, wash with cold water and seek medical assistance immediately a
Personal safety — not operate tag

W ARNING
Maintenance hazard!
Before you start servicing the machine, attach a NOT OPERA warning tag the machine a visible area.
Failure comply could result death serious injury
Attach a NOT OPERA AG) the machine area that clearly visible whenever the machine not operating properly and / requires
Complete the tag information for the "REASON" the tag attached describing the malfunction service
V alidate the reason for attaching the tag signing your name the designated area the The tag should only removed the person who signed and attached the after validating the repairs services have been completed.

NOT REMOVE THIS T AG! - arning) The tag should only removed the person who signed and attached the after validating the repairs services have been
See Other Side - (Reference additional information opposite side the
CNH Part Number - (Request this part number from you
NOT OPERA -
arning!)
Service Parts Dealer obtain this NOT OPERA
REASON - (Area for describing malfunction service required before
F Signed - (Signature area - signed the person validating the reason for installation the