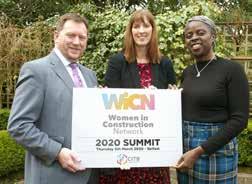
16 minute read
Inaugural Women in Construction Summit Inspires Change
Barry Neilson Chief Executive CITB NI, Nicola McCracken from Nicola McCracken Health and Safety and Siobhan Brown from Clanmil Housing.
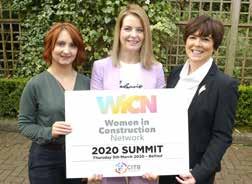
Charlotte Scullion from Henry Brothers Limited, Margaret Conway from McAleer & Rushe and Emer Murnaghan from GRAHAM Construction.
CITB NI, the Industry Training Board for the construction industry, and CITB NI Women in Construction Network has hosted their inaugural Women in Construction NI Summit in Belfast.
With a view to inspiring change and shattering stereotypes the Women in Construction NI Summit was a full day of inspirational stories, business advice and career development for women currently working in the construction industry, those thinking of joining and for employers who support diversity or best practice in the industry. It also provided thought-provoking tips on career management, helped identify role models and provided an opportunity to expand professional networks.
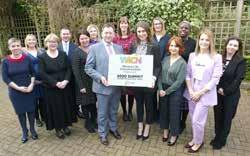
Barry Neilson Chief Executive CITB NI with summit guest speakers.
Hosted by Sarah Travers the conference featured leading industry professionals from local construction businesses such as Arup, Clanmil Housing, Farrans, Gilbert-Ash, GRAHAM, GRAHAMBAM Healthcare Partnership, Henry Brothers, McAleer & Rushe, Nicola McCracken Safety Services, NIFRS, Scottish Water, Turner & Townsend, White Ink, and Women’sTEC. Commented Barry Neilson, Chief Executive CITB NI: “With an ageing workforce, a skills shortage and the increasing use of new technologies, there has never been a better time to encourage more diversity in construction. “Increasing the talent pool and making it easier for women and other underrepresented populations to not just join the industry but to remain in the industry, is common sense for any employer. Given that it has been proven that more diversity in the workforce and particularly in leadership positions, can lead to higher profits and more innovation, it makes good business sense too.”
Thwaites Expand Irish Distribution Deal with TBF Thompson Group
Thwaites has expanded their distribution deal with Northern Ireland based machinery and truck dealer TBF Thompson Group, to now cover the Republic of Ireland.
TBF Thompson have a rich trading history spanning 50 years, today the business manages distribution deals across Northern and Southern Ireland with a selection of world leading construction machine manufacturers. Speaking on confirmation of the announcement TBF Thompson Director Seamus Doherty said: “TBF Thompson and Thwaites have been a winning combination in the North of Ireland for almost 30 years. This new expansion means we will be extending a full range of services to our depot in Dublin. We are proud to continue representing the Thwaites brand in this exciting venture and look forward to offering our support to customers across Ireland.” Added Thwaites General Sales Manager Andy Sabin: “Thwaites are delighted to have reached an agreement with TBF Thompson to enable them as the Thwaites distributor for the island of Ireland. We have a strong and successful relationship with Seamus and the TBF team, so I am confident that this new deal will deliver real value for Thwaites owners and operators across Ireland.” In support of the deal, Thwaites have appointed the experienced and knowledgeable Dave Webster as Distribution Manager. Dave will work with TBF Thompson to maximise the opportunity this expansion brings.
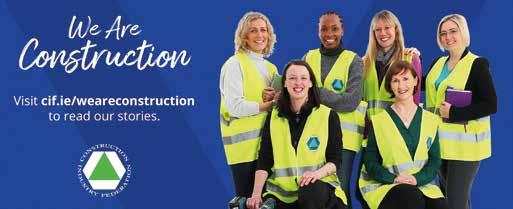
The women featured in the Billboard Campaign are: (Back Row) Patricia Power, Quantity Surveyor and Project Manager; Glorence Makharinge, Site Engineer, Marlet Property Group; Carole Smillie, Project Manager, Bennett Property; Nellie Reid, Managing Director, Meehan Green; (Front Row) Sally Jean Doherty, Apprentice Carpenter and Joiner, Sisk; and Jean Winters, Director of Industrial Relations and Employment Services, CIF.
CIF welcomes 76% increase in women working in the industry
Some 5,400 women have joined the industry since the Q4 2017 seeing the number of females working in construction grow to 12,500.
According to Central Statistics Office (CSO) statistics, women now make up 8.49% (Q4 2019) of the total workforce in the Construction Industry, rising
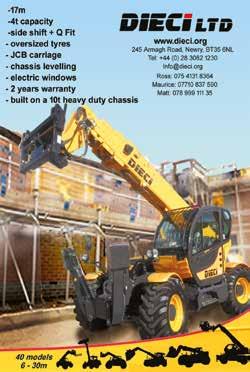
from just 5.3% in Q4 of 2017. A key part of the CIF’s Building Equality campaign, launched in 2017, has been to increase the visibility of women working in construction. The CIF’s Building Equality billboard campaign went live in a number of train stations around Dublin, in advance of International Women’s Day, which was on March 8th. CIF Communications Director, Shane Dempsey said: “Our billboards celebrate the women currently building Ireland. They challenge the tired stereotypes around construction. The women featured in the campaign come from across housing, contracting, property development, carpentry, quantity surveying and engineering. It shows the diversity of careers open to all people. In today’s construction industry, you are as likely to be using a computer than a hammer as the industry modernises and evolves. “A key part of our campaign has been to increase the visibility of women in construction as role models to the next generation. Since 2017, we’ve been actively highlighting the fact that there are rewarding careers in construction for women from the building site to the boardroom. “As the dust settles on this election, whatever Government emerges will turn to this industry to transform Irish society. We will have to double housing output from 22,000 to 45,000 per year and deliver over €115billion in infrastructure in the next five years. This will take a huge national effort and in simple terms we need to attract at least another 10,000 women into the industry to achieve this. There is no reason we should not aim to double the number of women in the industry from 12,500 to 25,000 in the next three to five years. “The increase of women working in the industry reflects efforts by our member companies to address gender equality, diversity and inclusion. Female participation remains relatively low and this threatens the sustainability of the industry in the long term. We need to do more to nurture female talent within the management structures of construction companies. “In 2016, SOLAS forecast that the industry would need about 100,000 additional workers to meet the Government’s commitments in housing and infrastructure. From 2013, we had been recruiting 1000 people per month until late 2018. That rate has slowed down and we’ve seen this growth plateau. Our ‘Building Equality’ campaign was launched to address the chronically low numbers of women in the industry.”

news Groundforce U.K. & Ireland appoints new Managing Director
Specialist construction solutions supplier Groundforce has appointed Paul Donovan as its new managing director for the U.K. and Ireland
Paul had previously been managing director at the Vp plc temporary roadway business, TPA, where he was responsible for overseeing the diversification of the business into new markets, which included modular pontoons, and Rapid Rail Access. Before joining TPA and the Vp plc group Paul held a range of senior commercial roles within several building and construction
Specialist excavation attachment manufacturer Hill Engineering have achieved recertification as one of Ireland’s best managed companies in the Deloitte Best Managed Companies Awards programme.
The company, which is based on the Carnbane Business Park in Newry, Co Down, demonstrated superior business performance for the sixth consecutive year – the third as a gold award companies, most recently Havelock Europa plc. He has a Diploma in Building Services Engineering and an MBA from Henley Management College. Paul said: “I am delighted to be given the opportunity to bring my experience across to Groundforce, leaving TPA in very capable hands. Groundforce is a dynamic business which prides itself on market leading products and service, the business has a wealth of experience and knowledge and I am looking forward to working with the team.” winner – and was recognised at a gala dinner in Dublin. The Deloitte Best Managed Companies programme, in association with Bank of Ireland, promotes and recognises excellence in Irish/Northern Irish owned and managed companies. It is the only awards scheme on the island of Ireland that considers a business’ performance from every perspective. Entrants to the programme compete for this designation in a rigorous

Paul Donovan
Contractors Complete Ballinagard Water Pumping Station Improvement Project

(Back Row): Paul Foley, Declan McGreevy Jacopa, Ciaran Diamond, Paul Wray and Gary McFadden, all NI Water. (Front Row): Barry Leake, Maurice McNulty (both Geda), Councillor Brian Tierney, Paul Davison, Raymond Nicell (both NI Water) and Robert Smith, McAdam Design. The £1.6 million upgrade of Ballinagard Water Pumping Station on the Culmore Road in Londonderry has been completed ahead of schedule by contractors Geda who partnered with Jacopa, with McAdam Design project management support.
The pumps and control panels at the station were upgraded to provide greater robustness and efficiency to enable water to be pumped to the local Croppy Hill Reservoir. Commented Infrastructure Minister Nichola Mallon: “This pumping station pumps water to Croppy Hill reservoir which supplies up to 16,000 customers in the West of Derry. I want to see more investment in sustainable water and drainage infrastructure because it will make a real
difference to people’s daily lives.” process that evaluates the calibre of their management abilities and practices. Gold standard best managed companies that receive the award for the fourth year in a row go through a Phase I and Phase II best managed companies awards programme application process, and after that can aim for platinum standard. Nine companies qualified for the first time in the 2020 Best Managed Companies Awards programme. They join a network of 130 companies representing 27 counties across Ireland, with a combined turnover of €11.4 billion, over €3 billion in annual export sales and the provision of 42,000 jobs. Commenting on the award, Hill Engineering general manager John Boyle said: “This award shows we continue to invest in the company in keeping our standards at a high level. We were never going to just stand still.”

CAMPBELL CONTRACTS DOUBLES MATERIAL WET PROCESSING ABILITY WITH CDE PLANT
Campbell Contracts Ltd, a family-owned and managed business headquartered in Tempo, a small village on the outskirts of Enniskillen in County Fermanagh, has doubled its materials processing ability since commissioning a new CDE wet processing plant.
Operating from its Letterbailey Quarry, Campbell Contracts has been extracting sand and gravel for over three decades. In recent years it commenced controlled blasting activities and now counts sand, gravel, crushed rock, rock fill and screened topsoil among its growing product range. In 2019, the Campbell family partnered with CDE, the industry-leading manufacturer of wet processing technologies, to support them to grow the business and diversify its portfolio of high-quality quarried aggregates. For over 30 years Campbell Contracts had utilised a traditional barrel washer, as company director Brendan Campbell explains: “The barrel washer was suitable to our business needs at the time it was installed, and it has served us well over its 30 years of service. “Increasingly, we need to ensure we can recycle and reclaim as much primary aggregate as possible during the quarrying process and the barrel washer had its limitations.” One of the earliest processes for washing aggregates, the Campbell Contracts barrel washer was efficient when processing cleaner virgin material. Its limitations became evident in its inability to wash heavier, claybound materials, rendering them as waste. “This material was then backfilled into the pits and buried,” Brendan says. “Similarly, the unwashed primary scalpings we generated were inevitably stockpiled as we didn’t have the technology to efficiently process the material.” Each stage of the quarrying process produces by-products in the form of overburden, scalpings and crushed rock fines. Often, quarry operators classify these as waste materials without commercial market value.
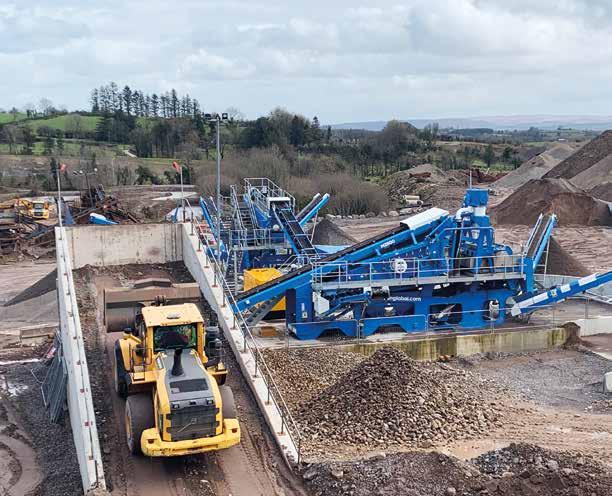
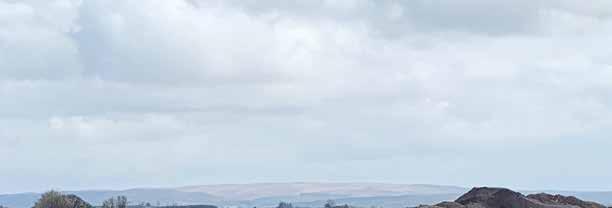

Enhancing Quality
David Kinloch, Regional Manager for CDE in the UK & Ireland, says, “CDE engineers state-of-the-art wet processing technologies that offers quarry operators the solutions to enhance the quality of products they currently produce while simultaneously supporting them to add huge commercial value to their enterprises by ensuring value is extracted from all available material – and that includes overburden, scalpings and crushed rock fines which are often perceived as quarry waste by-products.” CDE completed tests at Creagh Concrete on material extracted from the Letterbailey Quarry. Material was analysed and results used to develop a bespoke wet processing system that responds to the needs of Campbell Contracts and would support the family business to stimulate growth. “This was an important consideration for us,” Brendan says. “CDE understood our operation and what we wanted to achieve with a new wet processing plant. It’s very much a journey and a partnership with CDE that extends beyond the commissioning phase with first class proactive and preventative measures to ensure the plant is operating at maximum efficiency.”
Fully Integrated
Campbell Contracts’ new 120 tonnes per hour (tph) wet processing plant includes the L35 Feed Hopper, M2500 incorporating the twin-deck P2-75 Infinity Screen and EvoWash, and CDE’s AggMax83, integrating the RotoMax RX80 logwasher and H2-60 Infinity Screen. The fully integrated, modular plant combines feeding, screening, washing and stockpiling onto one compact and mobile chassis. With the support of its new CDE plant, Campbell Contracts is successfully processing three materials it previously categorised as waste from its quarrying
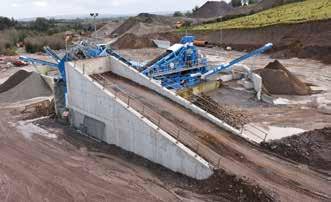
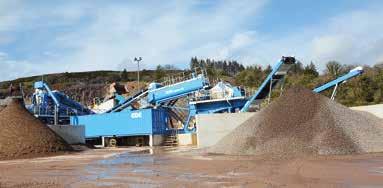
operations: clay-bound sand and gravel, primary scalpings and crushed rock fines. Brendan says it has had a transformative impact on the business. “We’re recovering high-quality materials and value that we had effectively written off as waste. In retrospect, we should have partnered with CDE to commission the plant sooner.” Virgin sand and gravel feed material is being processed at a rate of 120 tph producing 0-3mm and 0-6mm sand; 6-12mm, 12-25mm and 25-50mm aggregate; and +50mm oversize aggregate for a wide range of applications in the construction industry. David Kinloch adds, “Campbell Contracts is now processing three grades of material that it historically stockpiled or backfilled. CDE wet processing technology has demonstrated that all quarry by-products have the potential to be processed into marketable products that add significant value to a business.” Campbell Contracts has operations in civil engineering, quarrying, plant hire and haulage. It is one of Northern Ireland’s leading pipeline contractors, specialising in the installation of large diameter watermains, sewers and drainage systems. In 2019, company founder Jim Campbell was recognised for his contribution to the industry at the Plant & Civil Engineer Awards.
news Doosan Completes 30-40 tonne Stage V Excavators
With the launch of the new DX380LC-7 40 tonne model, Doosan has completed the company’s 30-40 tonne family of Stage V excavators. Together with the new Stage V DX300LC-7 30 tonne and DX350LC-7 36 tonne models, the DX380LC-7 offers a combination of high performance, operating features, fuel efficiency, reliability and durability.
With these new 30-40 tonne machines, Doosan has tried to ensure that productivity and environment protection are truly compatible. The DX380LC-7 is powered by the Scania DC09 Stage V compliant diesel engine, providing 240 kW of power at 1800 RPM. There are now four power modes available on all three machines, which help to simplify the operation of the new excavators compared to the more complex choice of eight power modes and SPC combinations in the previous generation machines. The operator is able to set the power mode (P+, P, S or E) in both one-way and two-way working modes. The DX380LC-7 features Doosan’s innovative D-ECOPOWER technology, providing operators with higher productivity and lower fuel consumption per hour, as well as smoother controls. It utilises an electronic pressure-controlled pump within a closed centre hydraulic system to accomplish increases of up to 26% in productivity and up to 12% in fuel consumption improvements, depending on the mode selected. A closed centred main control valve minimises pressure loss, while the electric pressure-controlled pump manages and optimises engine power more effectively. The D-ECOPOWER system uses nine sensors to detect the amount of hydraulic oil necessary to accomplish a specific task and precisely meter the amount of oil required rather than continuously forcing a fixed amount of oil through the system, thereby improving efficiency. Software is utilised to electronically reproduce the full benefits of an open centre hydraulic system with very little energy loss. The hydraulic system and engine horsepower are fully optimised and synchronised, further reducing losses within the system. Improved feedback to the operator through the joystick results in improved machine control and less operator fatigue. The acceleration and deceleration of the excavator workgroup functions are smoother, allowing operators to perform repetitive swinging and digging motions with less jerking movements. The new cab in the DX380LC-7 model takes operator comfort and ease of operation to another level. Like the other two Stage V models, the cab has a new high quality seat and offers more features as standard than other machines on the market, ensuring super controllability and high precision in all applications. As standard, 360° cameras provide full visibility around the excavator and allow the operator to see a top-down view of the area outside the machine. The camera array comprises a front camera, two side cameras and a rear camera. The camera display is separated from the gauge panel.
Montabert Now Komatsu Owned
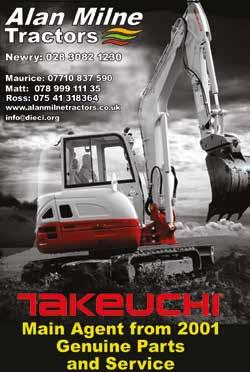
Montabert, one of the most renowned and respected names in rock breaking attachments, is now a Komatsu-owned company.
Whilst continuing to make its traditional products in their iconic green colour scheme, selling them through its longstanding dealership network, the latest coming together of Montabert breakers under Komatsu ownership has brought about another major development – the emergence of a new Komatsu-branded range of breakers made by Montabert. Produced in familiar Komatsu colours and branding at Montabert’s state-of-the-art plant in Saint-Priest, near the city of Lyon, and distributed in Ireland by McHale Plant Sales, this new Komatsu breaker range meets all of Montabert’s own exacting standards in terms of manufacturing quality. A worldwide leader in the design and manufacture of hydraulic demolition and drilling attachments and pneumatic equipment, Montabert invented the world’s first hydraulic concrete breaker in 1964. Since then, it has remained at the forefront of innovation and cutting-edge technology. Commenting, McHale Plant Sales director Tim Shanahan said: “Montabert is a respected name with a particularly strong following amongst those who are committed to investing in quality and reliability”. “Under Komatsu ownership, the French-based manufacturer has reaffirmed its goal to lead the industry for hydraulic attachments and, in that mission, we in McHale Plant Sales will play our full part.”