
14 minute read
JCB Electric Teletruk
GOING ELECTRIC WITH JCB AT SEAFORDE SCRAP METALS
Seaforde Scrap Metals located just outside Downpatrick in County Down has a long and successful history dealing with a wide range of customers, from the general public right through to multi-national companies.
A family run business established in 1920 by Peter Killen, it specialises in the reprocessing of ferrous and nonferrous metals and its continuing growth and success can be attributed to many things, not least its excellent high level of service, its ongoing investment in the most up-to-date plant and equipment and its commitment to the environment. Against that background, the company, headed up today by John Killen, recently acquired what was the first fully electric JCB 35-22E Teletruk to be sold in Northern Ireland by dealers Dennison JCB, with whom they have enjoyed a long and productive business relationship. When we caught up with Seaforde Scrap Metals, the versatile JCB Teletruk was engaged in a variety of tasks around the busy yard, taking everything that was required of it comfortably in its stride – from loading up 40-foot containers to shifting scrap cars. “Acquiring the electric JCB Teletruk was a no-brainer,” admits John Killen without any hesitation. “It’s not only a lot quieter in operation than the previous diesel powered model, it is emission free, more environmentally friendly - and it has the same 3.5 tonne lifting capacity.” The company has employed teletruks around the yard for many years; this latest JCB model is thought to be the fifth and it clearly hasn’t disappointed. Utilised both indoors and outdoors at the expansive scrap metal yard, a certified Authorised Treatment and fully licensed Waste Management facility, the JCB Teletruk has proved to be an invaluable workhorse, one which the operators love.
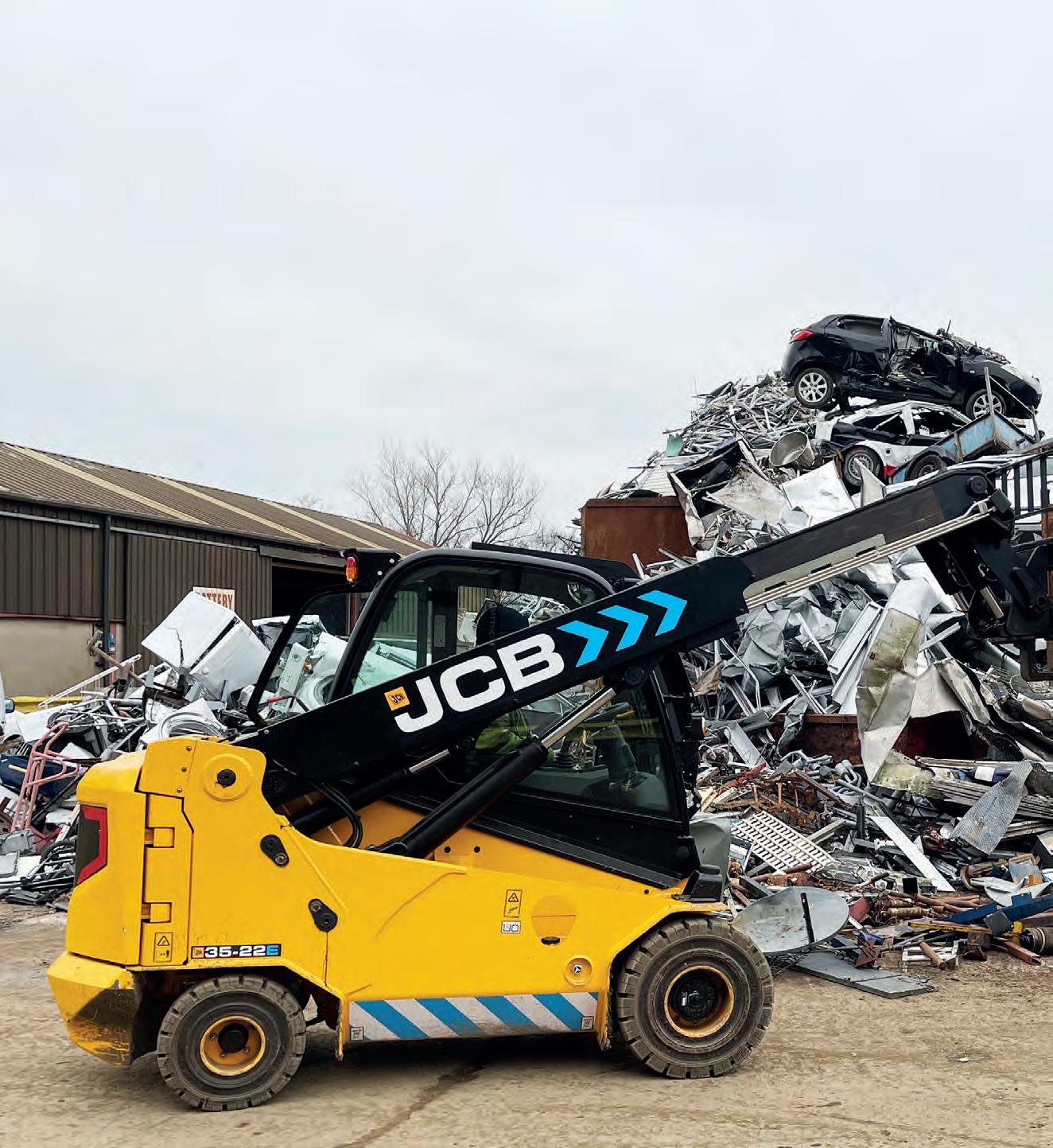
TIGHT TURNING CIRCLE
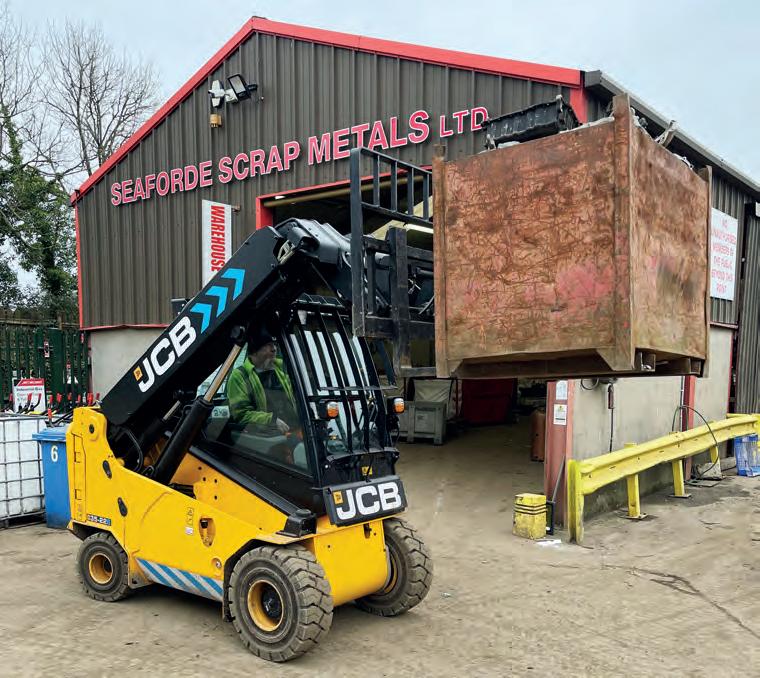
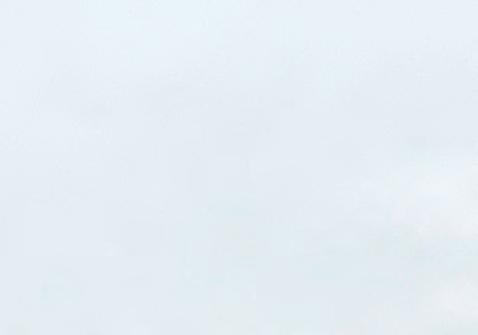
And what is there not to like about the machine? “Its enclosed canopy keeps the operators safe not only from the elements when working outdoors, but also safe from potential accidents and hazards. It is also a lot easier to manoeuvre as it has a much tighter turning circle than our previous machine and great all round visibility which is an added bonus, especially when working in restricted areas,” says John. Being electric powered – fitted with a lead-acid GNB/Exide Marathon Classic heavy duty - 80v, 625ah - we had to ask about the machine’s operational capacity. “It hasn’t created any problems for us; the battery doesn’t take very long to charge, we only have to charge it up twice some weeks, and certainly not every night – it all depends on the daily workload,” says John. Battery charging is as easy as lifting the battery cover and plugging in to the GNB high-frequency charger. It can be removed through the rear access door and comes with fork pockets and a single lift point as standard, meaning you can easily change the battery with either a forklift or crane within just two minutes! SAFE & COMFORTABLE
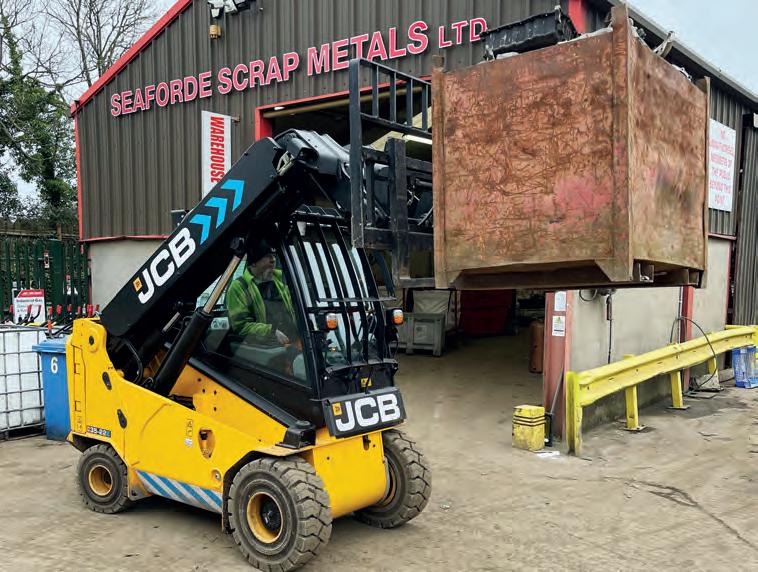
This new electric Teletruk features a new spacious JCB CommandPlus cab with greater internal space and a new seat design. Access into and out of the Teletruk is also safe and easy thanks to intuitive, well positioned grab handles and wide access. The JCB electric Teletruk’s unique side-mounted boom design provides unrivalled 360-degree visibility for the operator, as John mentioned. The design also allows total visibility of fork tips and attachments when fully retracted and lowered, even inside containers, providing exceptional on-site safety. The electric Teletruk, which incidentally comes with a two year JCB warranty on the machine, 3 year/ 6000 hours on Zapi drive and controls, plus a 1200 charge cycle warranty on the battery, also features a single lever control to make operation more straightforward and precise, thanks to SMART Hydraulics. JCB’s unique, active Load Motion Control feature alerts the operator and progressively stops the lift hydraulics when the maximum lift capacity is reached, preventing forward tip. The operator is informed through a simple progressive, green, amber and red warning light system. The unique benefit of 111 degrees of carriage rotation makes handling goods much easier and safer. The electric Teletruk can also easily recover tipped or fallen loads, removing the requirement for manual handling. Beacons and reverse alarms are fitted as standard for additional on-site safety with the option of a blue spot reverse light. “Without a doubt, the JCB Teletruk is a great all-rounder,” says John. “We couldn’t imagine doing without it, and the support we get from the team at Dennison JCB cannot be faulted.”
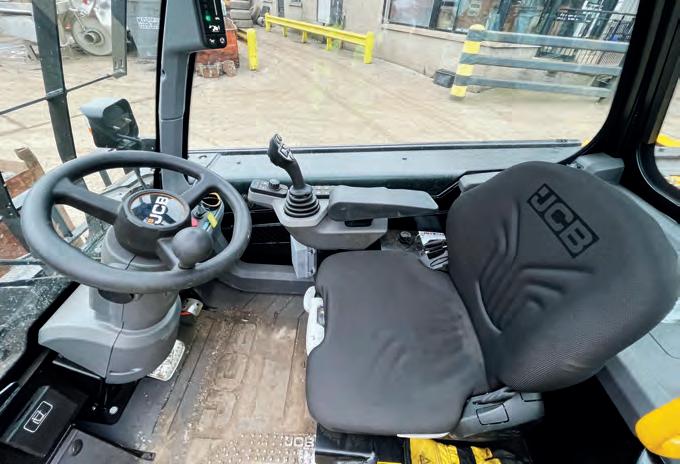
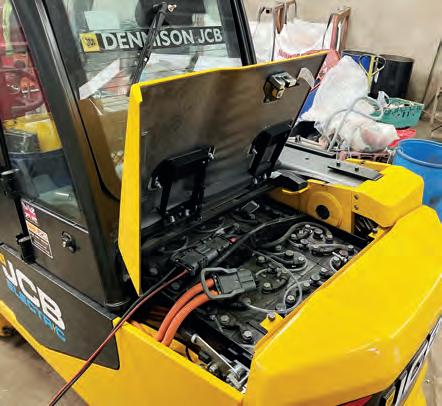
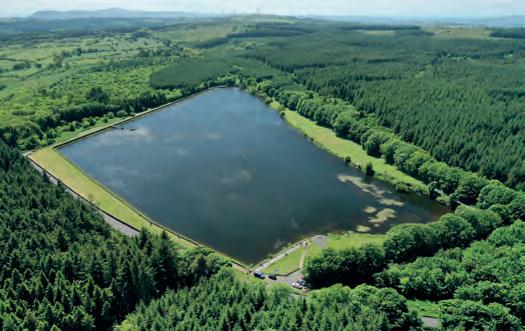
Woodburn Reservoir. Altnahinch.
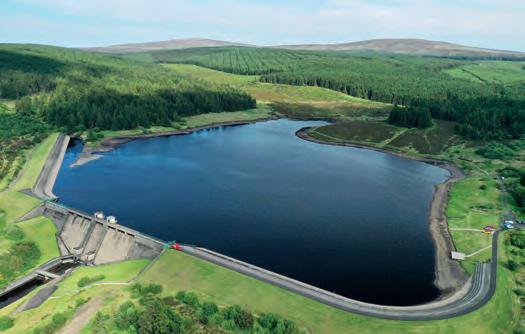
£6.4 Million Water Improvement Scheme gets underway to future-proof local Reservoirs
NI Water says that £6.4million will be invested in a major programme of reservoir improvements across Northern Ireland to refurbish and enhance the safety of the impounding reservoir portfolio.
This major programme of work has commenced with key improvements at Seagahan and Silent Valley reservoirs. Work will continue at various reservoirs until September 2024 and will involve completing improvements at 36 major reservoirs throughout Northern Ireland. The work is being carried out by BSG, and project managed by AECOM. Infrastructure Minister Nichola Mallon said: “This £6.4million investment in local reservoirs is an excellent example of what can be done with the necessary funding in place. It is important that funding levels are sustained throughout PC21 to ensure that NI Water can continue the Reservoir investment programme to maintain water supply as well as ensuring

Killylane.
compliance with the forthcoming reservoir safety legislation.” Mark Richardson, NI Water Senior Project Manager added: “Our impounding reservoir portfolio plays a critical role in the storage of raw water for future supply to our customers. NI Water is committed to the highest standards of reservoir safety and management and we are progressing with this key programme of maintenance and refurbishment work to future-proof our impounding reservoirs to continue to provide a world-class water supply service for our customers. “These improvements will also ensure our compliance with the requirements of the forthcoming Reservoirs Act, which is regarded as industry best practice in the supervision and maintenance of large reservoirs. “The enhancements cover a wide range of the reservoir components, including refurbishment of control valves, installation of drainage, repairs to spillway structures and improvement to monitoring equipment to ensure the safe and appropriate management of the reservoirs. This ensures the safety of these significant structures is maintained.” The major reservoirs that will benefit are as follows: Altmore, Cappagh, Glenhordial, Lough Fea, Lough Fingrean in County Tyrone, as well as Ballydoolagh in Enniskillen. Altnaheglish, Ballinrees, Dunalis, and Killea in County L’Derry. Altnahinch, Dorisland, Craigahulliar, Boomers, Copeland, Dungonnell, Killylane, Leathemstown, Lough Mourne, Quoile, Stoneyford and Woodburn in County Antrim. Seagahan and Clay Lake in County Armagh, as well as several reservoirs in County Down: Church Road, Ballysallagh, Conlig, Lough Cowey, Creighton’s Green, Lough Island Reavy, Lough Money, Lough Shannagh, Ben Crom, Silent Valley, Spelga, and Fofanny.
PLANT & CIVIL
Find us on
PLANT & CIVIL
CONSTRUCTION, QUARRY & RECYCLING MAGAZINE AWARDS2022 SAVE THE DATE THURSDAY 24th NOVEMBER 2022

CROWNE PLAZA, SHAW’S BRIDGE, BELFAST. www.plantandcivilengineer.com
HIGH SPEED, HIGH PERFORMANCE WITH TEREX ECOTEC’S NEW TBG 530T HIGH SPEED SHREDDER
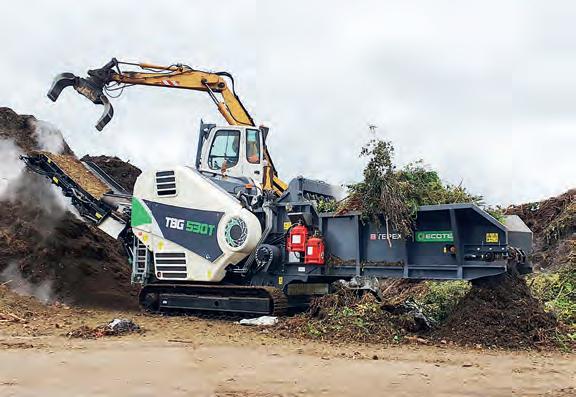

With an eye on innovation, leading environmental equipment specialist, Terex Ecotec, continue to expand their world class range of mobile equipment with the launch of the eagerly awaited TBG 530T.
A robust track mounted high speed shredder, the TBG 530T is ideal for medium scale producers requiring an accurate and consistent end product. Powered by a 493HP Scania DC13 engine, the TBG 530T has been expertly designed to give operators unrivalled performance, ease of maintenance and superb fuel efficiency. Extremely versatile, it excels in many applications and is particularly suited to waste wood processing and green waste shredding. Comments Tony Devlin, Business Line Director for Terex Ecotec: “The TBG 530T enhances our high speed shredder offering and allows our product range to further meet operators’ needs. Inspired by the successful TBG 630, the TBG 530T has been purposefully engineered to maintain the same key features in a smaller package. Easy to operate with excellent serviceability we are proud to have it in our portfolio and look forward to it dominating the market.” With a rapid set up time the TBG 530T is ready to work in a matter of minutes with no tooling required. The open fronted feeder enables the TBG 530T to be fed quickly and easily from the rear. The intelligently controlled feed system, comprising of heavy duty drag chains and aggressive feed wheel with unique lift/ downward assist, ensure optimum material flow resulting in class leading performance. SWINGING HAMMER ROTOR
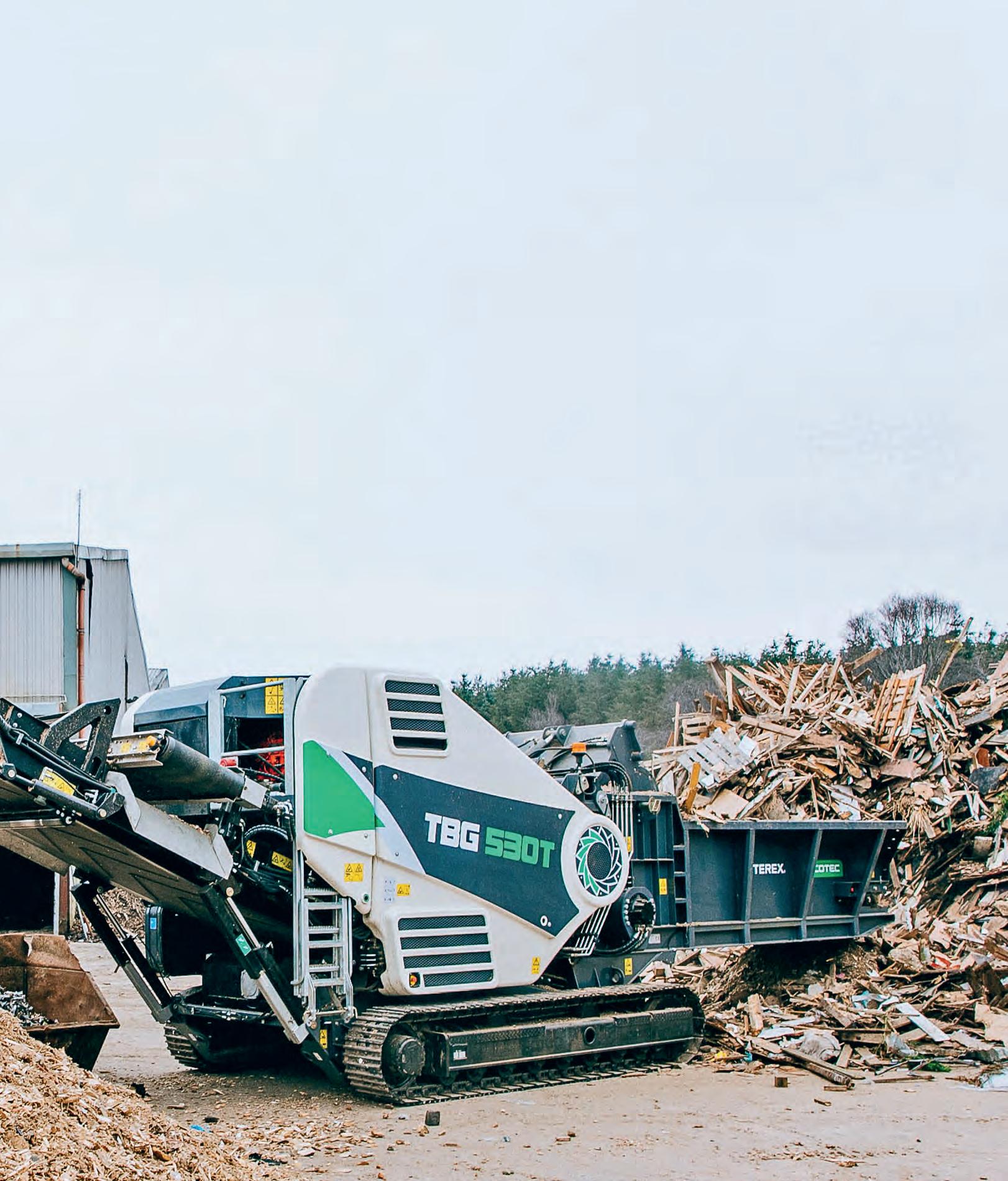

At the heart of the machine is the 1,100mm diameter x 1,490mm wide swinging hammer rotor. This robust, direct drive rotor rotates at 1000 RPM and incorporates 30 up-swinging hammers. A wide selection of hammer designs and interchangeable screens are available allowing the machine to be configured to suit the everchanging product requirements. The TBG 530T also benefits from the added protection of a screen kickback system. Should an unshreddable object enter the shredding chamber the screen will release allowing the material to quickly pass through, reducing the risk of accidental damage. Processed material is removed from the machine via a modular product conveyor with an impressive discharge height of 4.6m. This conveyor also lowers to ground level for inspection and maintenance. An optional overband magnet with hydraulic height adjustment can be fitted to remove ferrous metal from the product. Whether performing daily checks or carrying out maintenance, the TBG 530T offers unrivalled service access to all key areas of the machine. The electric/ hydraulic raise/lower of the screen and interlocked chamber access door allow the rotor and anvil to be inspected with ease. Designed with the operator in mind, the TBG 530T offers the perfect blend of performance, efficiency and serviceability. TELEMATICS STANDARD
The TBG 530T comes fitted as standard with the industry leading T-Link telematics solution designed to improve productivity, efficiency and profitability for the customer. Manufacturing of this latest high speed shredder will take place at Terex Campsie, a dedicated state of the art facility which will support the ongoing growth and development of Terex Ecotec’s ever-expanding product portfolio. The TBG 530T is available to purchase now via Terex Ecotec’s world class dealer distribution network that provide the sales and aftermarket service demanded for in the market. The addition of the TBG 530T will further enhance an already significant portfolio of products offered by Terex Ecotec and demonstrates their continued passion and commitment for new product development and innovation, positioning them at the forefront of the recycling market.
TEREX WASHING SYSTEMS PLANT IMPRESSES AT NEW SAND QUARRY
Terex Washing Systems have recently delivered a sand washing plant for Clarence Sands; this newly established site is now one of the premium sand quarries in Sydney, Australia.
The sandstone deposit located in the Blue Mountains produces premium quality construction sand that is washed and classified using a state-of-the-art Terex Washing Systems wash plant. The bespoke design of the plant can produce up to 300 tonnes of quality sand per hour and recycles roughly 90% of the water used during the washing process. To begin with, the wash plant features a H30 (50 tonne) Feeder that receives the raw sandstone feed material and distributes it evenly on the main conveyor. At this point any stones or rock that are larger than 100mm are removed from the feed material due to the grid covering the feeder. The H30 Feeder also features a hydraulic tipping grid that can be controlled from the cab so that any material stuck on the bars can be cleared. With the sand distributed evenly on the main conveyor it makes its way up to the modular 20x8 2 Deck Rinser Screen. This screen has been designed specifically to handle the tonnage needed for this operation. A total of 19 spray bars give the material an initial rinse as the vibrating screener shakes the sand and stone down through the polyurethane decks as it is classified by size. The polyurethane decks have a much longer wear life than that of metal decks. Any larger aggregates can pass through the screen onto aggregate and oversize conveyors where they are stockpiled as products for sale. Any sand, silt, clay or other fine impurities that were present within the feed material is washed to the split catchbox of the screener. Terex Washing System catch boxes have adjustable blending paddles, which assist in blending the correct amount of fines into the coarse fraction. This ensures the required spec is always achievable. The material is gravity fed into one of two FM 200C Sand Plants. Each sand plant receives a separate split, one coarse sand and one fine sand. For this application the standard units were upgraded to separators, rather than the standard hydrocyclones. This was done to cope with larger volumes of fines, as well as to deal with potential variation in feed stocks.
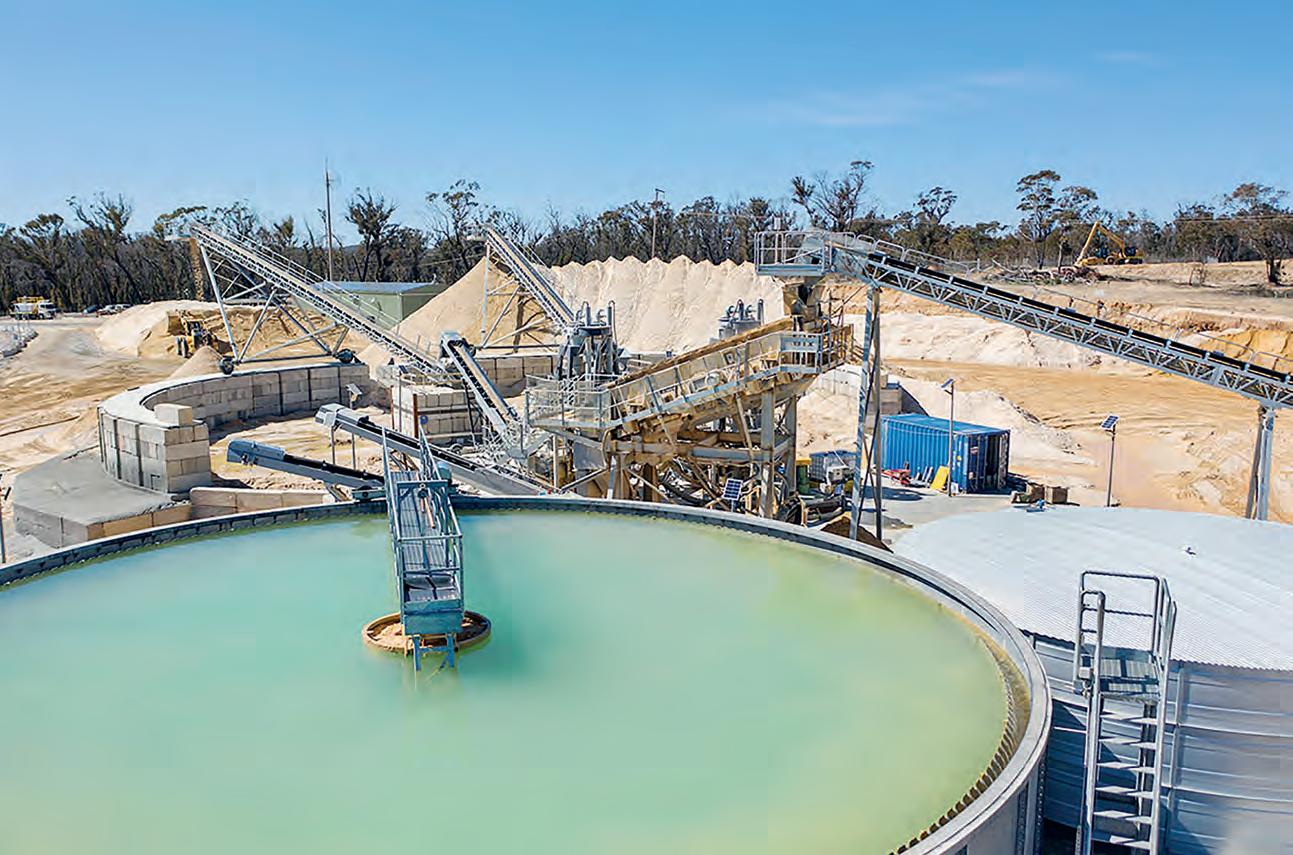
Separators use centrifugal force to remove the sand from the silt and clay so that it can be transferred onto the high frequency dewatering screens. These dewatering screens remove the remaining water within the sand so that only 10-15% of water is left. The sand that is now up to spec is then transferred onto a 26-metre radial stacking conveyor that offers a large stockpile capacity, which really suits the needs of the customer. The water that, up until this point, has been used to initially rinse the feed material, wash the sand within the FM 200C and has been recovered from the dewatering screen is pumped into the 17-metrerake thickener tank. The rake thickener allows the silt and clay particles within the sludge to settle at the bottom of the tank, while the clean water weirs over the edge to be re-used. The integral scrapers aid transportation of material from the outskirts of the tank to the outlet, thus accelerating the removal of sludge from the thickener. This process is sped up with the use of a Flocculant Dossing Unit, which dosses the sludge on its way to the rake thickener. The flocculant that is added to the sludge causes the waste particles to bind together, creating a particle with a larger mass, which then sinks to the base of the tank faster. Dossing the sludge with flocculant dramatically increases the speed at which the clean water can be recycled back into the wash plant. A wash plant can’t do its job without water, which can be a difficult resource to manage in Australia. Terex Washing Systems advised the customer of the need for a robust water management system that would be both environmentally friendly and save on running costs. Neil Rooney, Engineering Manager for Terex Washing Systems, explains: “Over the last number of years, Terex Washing Systems have developed our water management product range to the point that we’re confident we can meet the needs of any application”. He continues, “Our wash plant at Clarence Sands is a good example of how an efficient water management system can take an operation to the next level. For Clarence Sands settling ponds maintenance is drastically reduced, freeing up valuable machinery and time”. Servicing such a large market requires a robust and reliable wash plant, which is what Terex Washing Systems have delivered to the customer. The Terex Washing Systems engineers were faced with unique challenges during this project but managed to overcome them and deliver a wash plant that can meet the tonnage that was required for Clarence Sands.
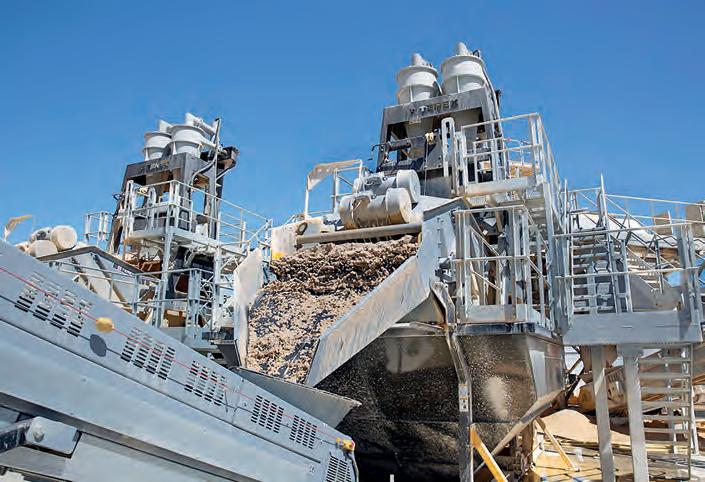
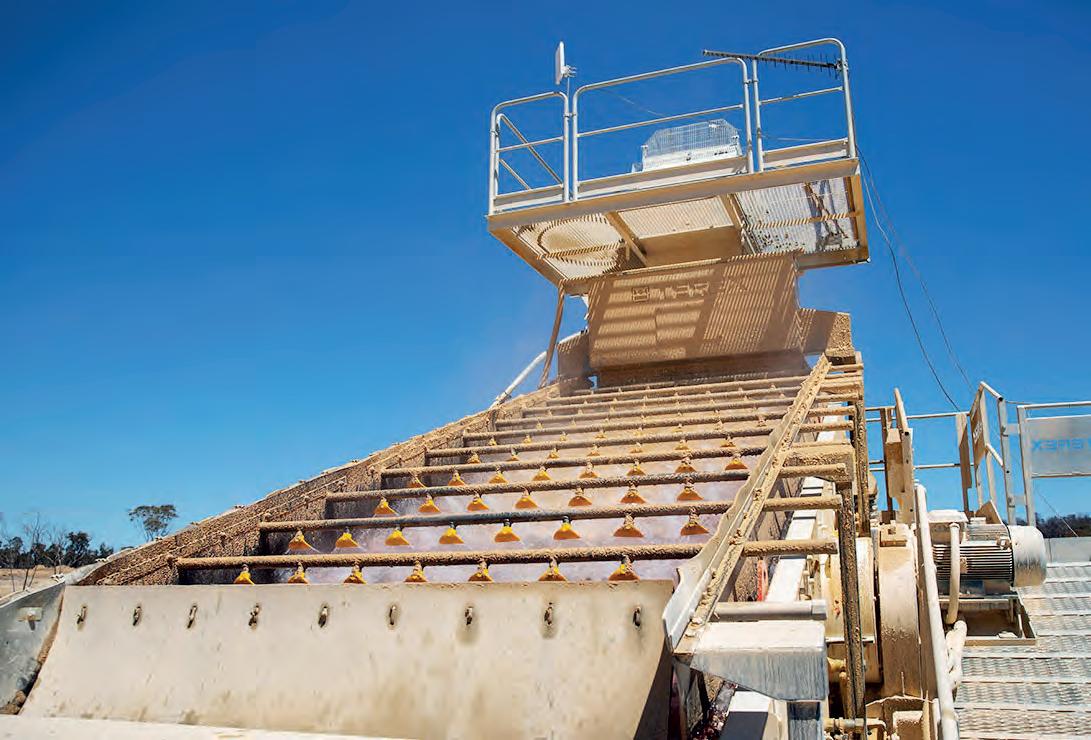