
30 minute read
Excavators
HYUNDAI LAUNCH EU STAGE V POWER FOR 13-15 TONNE A-SERIES EXCAVATORS
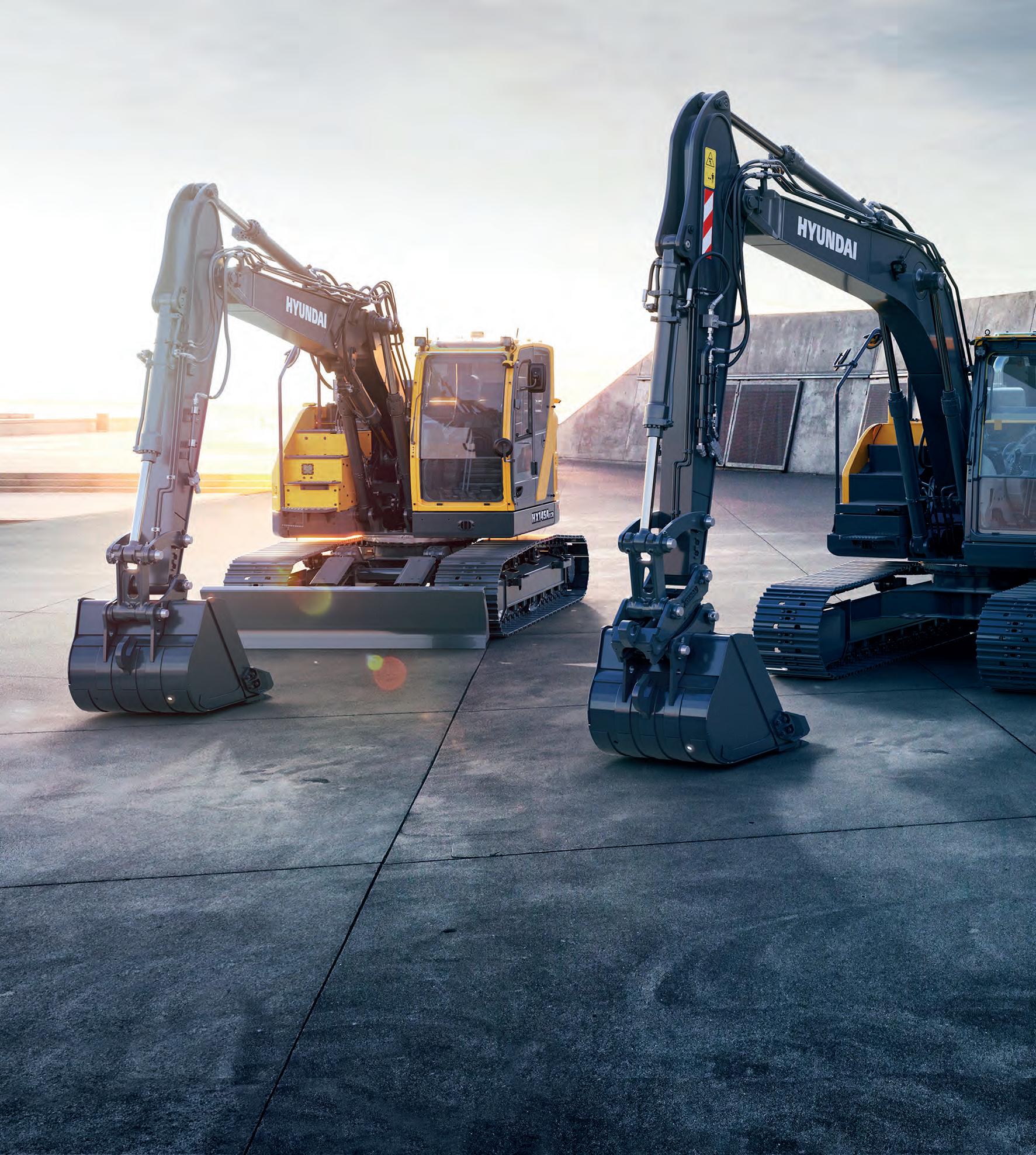
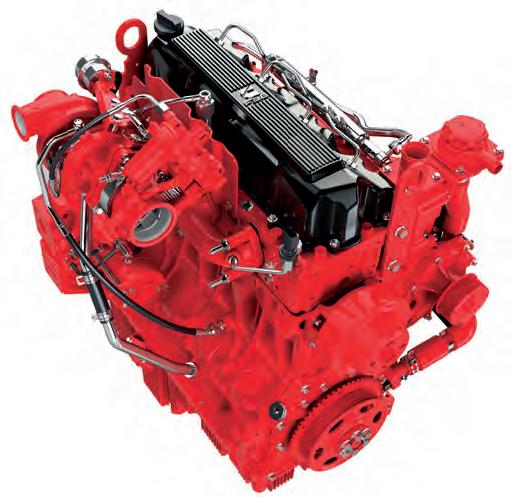
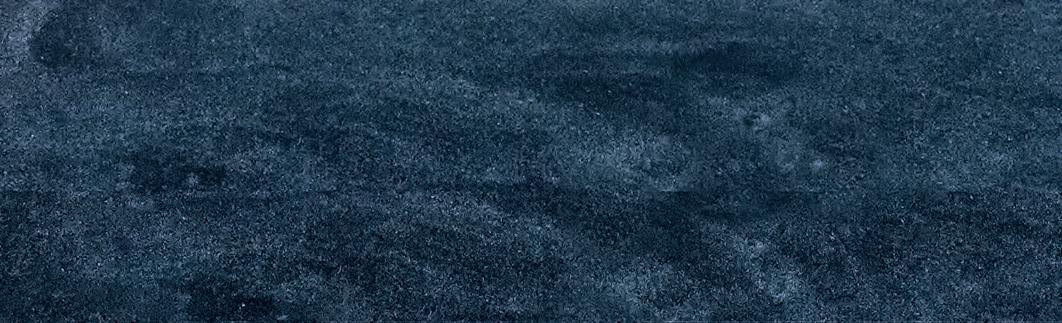
Hyundai Construction Equipment is launching three EU Stage V compliant A-Series crawler excavators in the popular 13-15 tonne sector.
Powered by the latest Cummins diesel engines, the reduced tailswing HX130ALCR, conventional HX140AL and the reduced swing HX145ALCR feature improved hydraulic control, for enhanced productivity and increased uptime. Though offering similar operating weights, the machines deliver very different performance operating envelopes, to suit a range of customer requirements. The reduced swing HX130ALCR, which will appeal to rental customers, is powered by a 55kW (74hp) version of the Cummins F3.8 engine. The engine meets the EU Stage V emissions standard without the need for an exhaust fluid such as AdBlue. When using a CK-4 E/G engine oil, this engine offers service intervals of up to 1,000 hours, twice as long as the previous machine. This reduces operating cost for the customer, boosting uptime on site. The HX130AL also benefits from Hyundai’s ECD engine connected diagnostics, providing remote diagnostics and ensuring that technicians arrive at the machine with the required parts and tools. The conventional counterweight HX140AL uses a more powerful 100kW (134hp) version of the Cummins engine, to deliver maximum digging forces and higher productivity. Appealing particularly to contractors and those looking for the ultimate digging and lifting machine in the class, the excavator offers 3% more power and 12% more torque than its predecessor. With easy, ground-based access to all filters and fill points, the HX140AL also benefits from 1,000-hour service intervals when using CK-4 engine oils. Engine connected diagnostics and Hyundai’s HiMATE remote management system, provide the fleet manager with the highest level of service and product support. The third model to benefit from the Stage V update is the HX145ALCR. Like the HX130A LCR, this reduced tailswing model is particularly suitable for applications where space to manoeuvre is at a premium, such as utilities, road working and housebuilding. Boasting the same 100kW (134hp) output as the HX140AL, the engine delivers an 8% power boost over its predecessor, while delivering a 4% fuel economy gain and a 60% reduction in PM emissions. The HX145ALCR delivers up to a 6% fuel improvement in levelling work and a 3% drop in consumption during truck loading, compared to the HX Series model working in P mode.

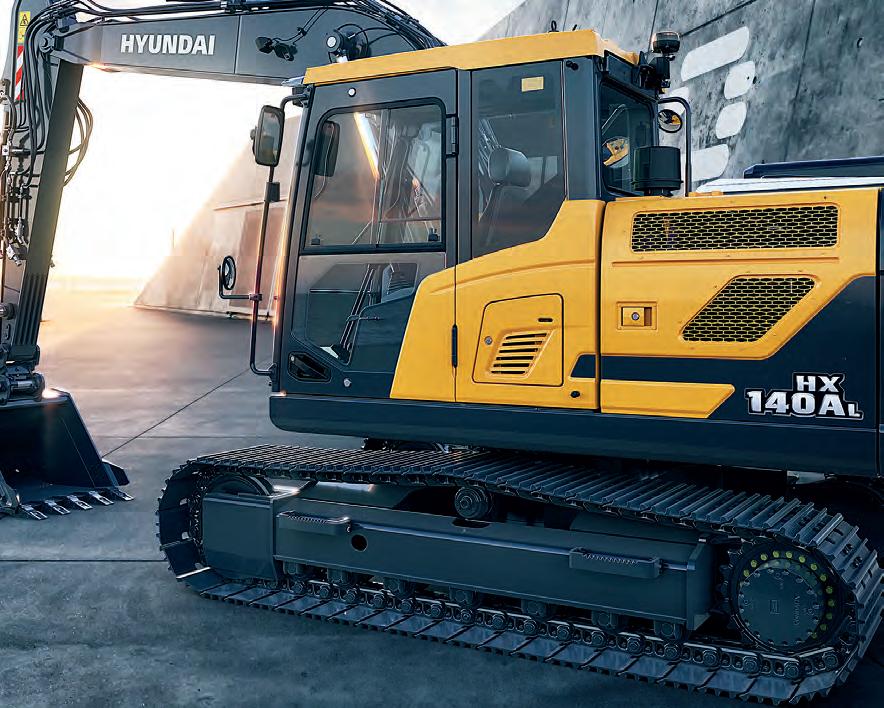
CONTINUED
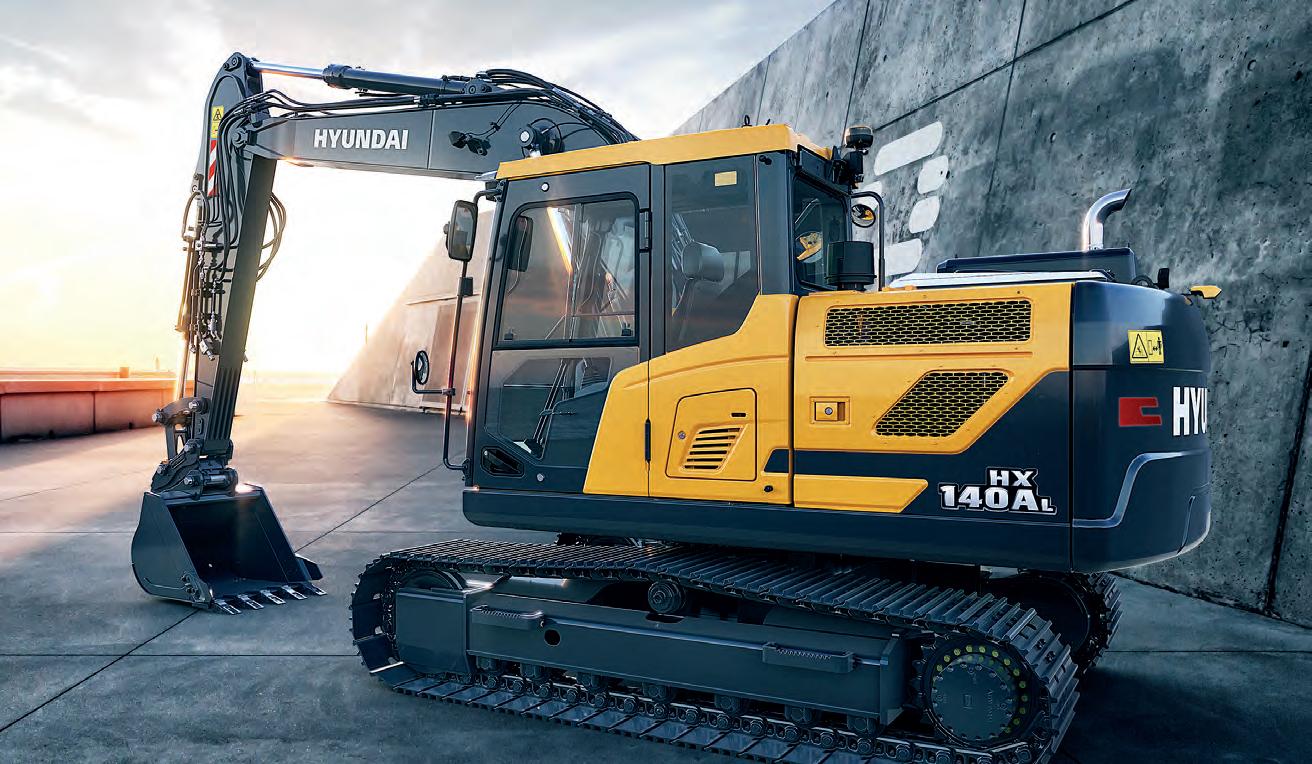
As with the conventional tailswing models, the compact radius excavator offers service intervals of up to 1,000 hours, when operating with CK-4 E/G oils. The machine also features Hyundai’s HCE-DT Air, permitting wireless connection to the excavator from a smartphone or laptop computer on site. This promotes rapid diagnosis and reduces costly downtime. HYDRAULIC SETTINGS
The HX A Series machines have an upgraded IPC system, tuning pump flow rate and power to meet operator demand. The design of the main control valve and the hydraulic pipe layout has also been optimised, to minimise energy loss throughout the system. A new Lifting Mode improves fine control and lift capability, reducing engine rpm, activating power boost and offering improved pump flow control. The machines are also offered with an optional Fine Swing Control, smoothing the movement of the boom at the start and stop of the swing movement. The operator can also set boom-lift speed compared to swing speed, by activating and deactivating the boom priority function. Dipper arm in speed can also be fine-tuned by activating and deactivating the arm regeneration function. It is now possible to save machine settings through the Key On Init work mode, to apply the settings on engine start-up. COMFORTABLE CONTROL
Cabin space in the three machines has been increased by 13% and they feature an improved grab handle design in the cabin door, making it easier to access the driver’s seat and improving visibility to the side of the machine from the cab. The excavators have a modern cab interior with an 8” capacitive-type touchscreen for all major information, which can also be controlled through an automotive-style jog/ dial module. This also controls the accelerator and remote air conditioner as well. Centralised switches below the display allow easy control of all functions and the excavators can be specified with optional proportional auxiliary controls in the servo lever heads. Single pedal straight travel is also offered as an option. Safety remains a priority for Hyundai and the HX A Series excavators benefit from a new electronic swing parking system, to control the swing brake function. An Auto Safety Lock prevents unintended operation of the machine and the excavators can be specified with mirror view cameras and Hyundai’s AAVM (Advanced Around View Monitoring) camera system. This includes IMOD (Intelligent Moving Object Detection) that informs the operator if people or objects are detected within the range of operation. For more information on the new Hyundai A Series, please contact Northern Lift Trucks on 028 9267 3111.
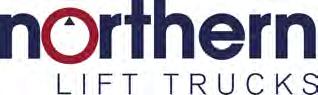
www.northernlifttrucks.co.uk
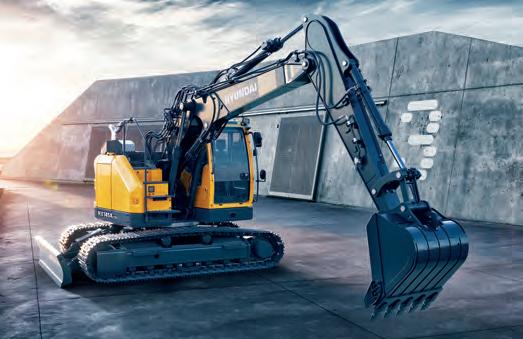
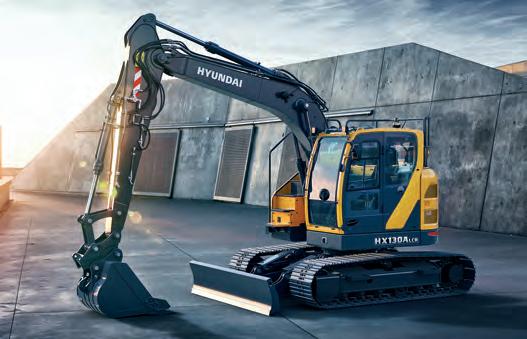
LATEST CAT® 336 EXCAVATOR DELIVERS LOW OWNING AND OPERATING COSTS
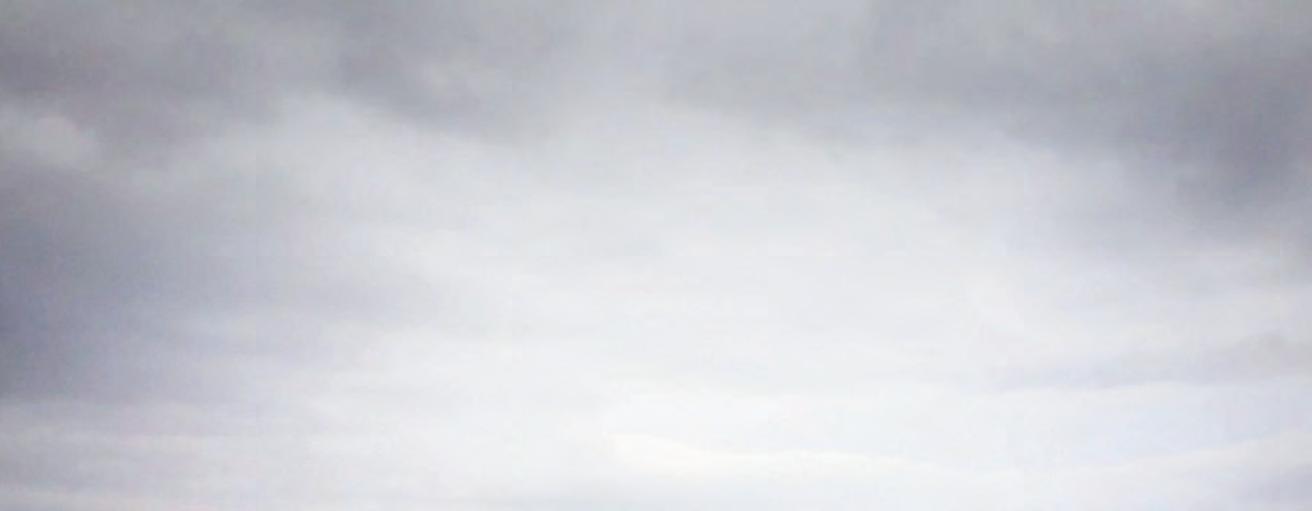
The new Cat® 336 hydraulic excavator offers classleading production and low-cost operation, says the manufacturer. Its powerful hydraulic system delivers strong digging forces and swing torque to boost production in the most demanding applications.
With its strong structures, the 336 excavator will deliver reliable operation in a variety of applications. The Cat C7.1 engine’s 4 million hours of service attest to its long-term reliability. Three engine modes match excavator power to the demands of the job while saving fuel. Power mode delivers maximum power to meet the most demanding tasks; Smart mode automatically matches engine and hydraulic power to digging conditions to lower fuel consumption. Reducing engine speed to a constant 1500 rpm, Eco mode minimizes fuel consumption. Synchronized 1,000-hour oil and fuel filter service intervals reduce downtime. The extended intervals also eliminate labor cost for nine oil and fuel filter changes and parts cost for 27 oil and fuel filters over 10,000 machine operating hours compared to many competitive 30-40 ton excavators. High-ambient temperature capability of 52˚ C (125˚ F), coldstart capability at -18˚ C (0˚ F), and the ability to work at up to 4500m (14,764 ft) above sea level enable the 336 to work in various climates. Auto hydraulic warmup in cold temperatures gets the machine to work faster and prolongs the life of machine components. The air intake filter with pre-cleaner features high dust capacity, and a highefficiency hydraulic fan offers optional automatic reverse to keep cores free from debris. Product LinkTM collects data automatically. View information like location, hours, fuel usage, idle time, maintenance alerts, diagnostic codes, and machine health online through web and mobile applications. Maximizing machine uptime, Remote Troubleshoot and Remote Flash allow dealers to remotely connect with the machine to diagnose fault codes and update operating software. SIMPLE, COMFORTABLE OPERATION
From Deluxe to Premium, Next Generation cab trim levels are available. Deluxe cabs come with a heated air-suspension seat; Premium cabs come with a heated and ventilated airsuspension seat. Both have a tilt up left-hand console for easier access in and out of the machine. A touchscreen monitor and jog dial offer quick navigation through machine controls and provide easy access to the machine’s digital operator’s manual. Keyless pushbutton start is standard, and Bluetooth® key fob is available. An Operator ID passcode allows for engine starting, and Operator ID can quickly save and restore joystick button, response, and pattern preferences for individual operators. Optional Cat Stick Steer makes travel and turning much easier. A host of standard technologies – Cat Payload on-board weighing, Grade Assist for maintaining grade, and 2D Grade with depth and slope indication – elevate operator efficiency and machine productivity. All Cat Grade systems are compatible with radios and base stations from top third-party technology suppliers. Operators can store up to four depth and slope offsets to quickly cut to grade without a grade checker. Auto Hammer Stop warns operators after 15 seconds of continuous firing and then shuts off the hammer after 30 seconds to prevent wear and tear. Auto Dig Boost and Auto Heavy Lift increase bucket penetration and lift capacity by 8%, and Lift Assist helps operators avoid tipping the machine.

With the introduction of 10 more new models, Doosan has completed the launch of its new medium-sized ‘DX7’ range of 17 Stage V crawler and wheeled excavator models from 14 to 25 tonne. As Plant & Civil Engineer’s David Stokes reports, the new models provide significantly higher performance in every area than the previous generation Stage IV machines.
The completed DX-7 line-up combine enhanced comfort, increased tool carrier capability and novel operator assist technology, with new features to boost fuel efficiency, uptime and return on investment, with a focus on increased power, robustness and agility. Maintenance of the diesel particulate filter (DPF) has also been greatly reduced, with no maintenance required until the machine has operated for 8000 hours. The 10 new models are DX140LC-7, DX140LCR-7 and DX160HT-7 14-16 t Crawler Excavators; DX235LC-7, DX235LCR-7 and DX255LC-7 23-25 t Crawler Excavators; DX165WR-7 17 t Wheeled Excavator; and DX170W-7, DX190W-7 and DX210W-7 18-22 t Wheeled Excavators. So, let’s take a closer look at some of these latest additions. The new DX235LCR-7 reduced radius crawler excavator, for example, offers superior digging performance together with flexibility, convenience and low operating costs in a compact design with a rear swing radius of just 1724mm. It meets increased demand for reduced radius machines for work near buildings and in confined areas. The trend towards reduced radius machines has been driven by the space premium, particularly on inner city and urban construction sites and by the requirement in road and rail construction to keep adjacent lanes and tracks open while working alongside them. The DX140LCR-7 is a reduced tail swing model, allowing operators greater flexibility where space is a premium without sacrificing performance. It also incorporates a new counterweight design that offers enhanced service accessibility, while the new DX160HT-7 High Track model is designed to meet the needs of customers requiring a combination of higher ground clearance, a reinforced track frame and a strong traction system with reinforced upper rollers for work in harsh environments and on projects where larger travelling distances are involved. This new High Track model is particularly suited for constructing roadways, mounding, earthmoving and other duties in the forestry industry. Meanwhile, the new DX170W-7, DX190W-7 and DX210W-7 Stage V compliant wheeled excavators all offer improved front movement for rotating tools such as mulchers and the working range for articulated fronts has been improved. The articulated boom cylinder stroke has also been increased whilst the mounting position remains the same. A lock valve has now been added on top of the boom cylinder, to prevent unexpected releasing of the articulated boom cylinder when doing digging work. The new wheeled excavators also have a new smart hydraulic system that offers an improvement of around 30% in attachment work, compared to the previous models. The new system applies a smart hydraulic logic for optimal distribution of the hydraulic flow rate when both the arm and attachment are working simultaneously, with a new priority valve and an additional hydraulic line maintaining continuous hydraulic flow to the attachment, even when the arm is being used. Completing this latest line-up is the DX165WR-7 Stage V compliant wheeled excavator, a new short tail machine that is perfect for jobs in tight spaces, particularly in urban areas or on narrow roads with heavy traffic. The DX165WR-7 is built with the same undercarriage as the new DX160W-7 Stage
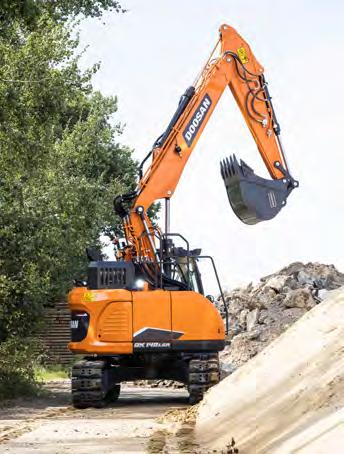
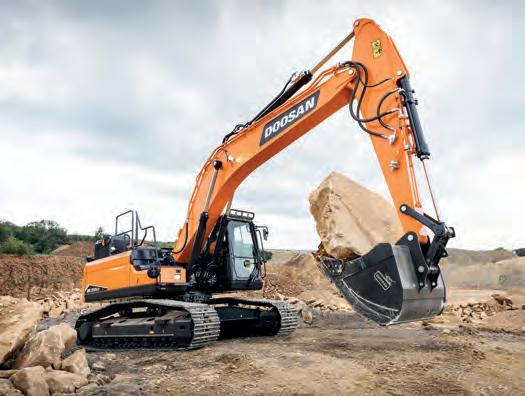

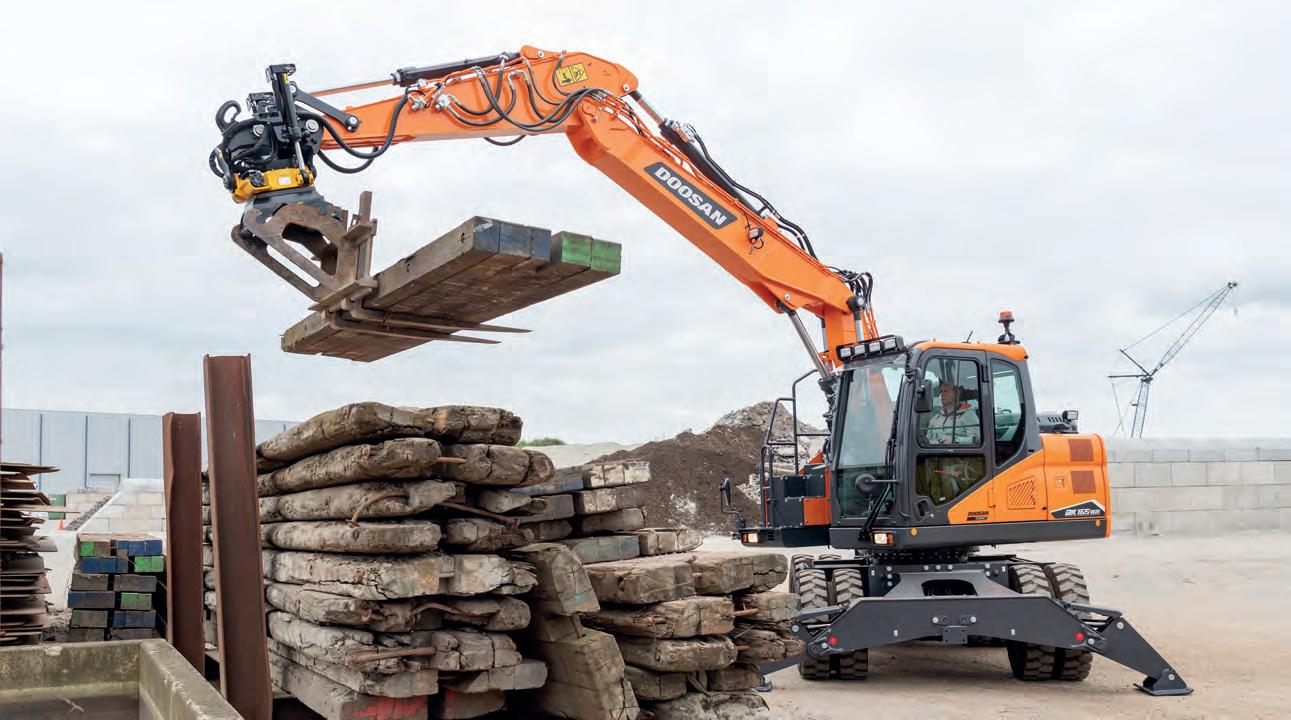
V model, providing an optimal centre of gravity thanks to the long wheel base and the ideal weight distribution. As a result, the DX165WR-7 offers maximum performance, combining the very short swing radius with the best stability and lifting capacities for this class of machine. TILTROTATOR MODE
Common to all of these new models is a new Tiltrotator Mode on the control panel, which can be selected to ensure an optimized hydraulic flow and helps to maximize the accuracy of tiltrotator work by eliminating back pressure. This new tiltrotator mode is a special two-way flow mode, but it is managed by the EPOS like a one way flow mode, with direct return to the tank in each direction, to avoid back pressure and increase flow and controllability. FINE SWING FUNCTION
Another standard new feature is the Fine Swing function which minimizes the shaking that a lifted object undergoes at the start or stop of a swing movement with the excavator, to increase the safety of nearby workers and to prevent damage caused by the object falling from the excavator. When Fine Swing activates, the overrun disappears, allowing the excavators to smoothly reach maximum swing speed, whilst removing the shock from the turn reversal at the moment of stopping, resulting in a smooth stop. The new excavators also incorporate as standard a new lifting eye that forms part of the casting for the push link for the bucket attachment at the end of the arm. The new lifting eye has a maximum capacity of 5 tonne and has a special bush insert to prevent deformation of the lifting hole. COMFORT AND CONTROLLABILITY
The state-of-the-art cab on the new excavators excels in terms of spaciousness and ergonomics, taking operator comfort and ease of operation to new levels. As well as a new high quality seat, the enhanced cab offers more features as standard than other machines on the market, ensuring super controllability and high precision in all applications. For example, the wheeled excavators offer as standard the new Auto Digging Brake feature, which automatically holds the service brake in position when the vehicle stops (speed is zero), without the driver having to step on the brake pedal. The driver can activate or deactivate the Auto Digging Brake function by pressing the Auto Digging Brake button on the control panel. When the accelerator pedal is then pressed, the Auto Digging Brake function is released. Joystick Steering is a new option, enabling the driver to steer the machine by using the joystick thumbwheel (without using the steering wheel) when working and driving in the work mode. The Joystick Steering system only works under 20 km/h when first or second speed gears are engaged. The function is activated or deactivated by pressing the thumbwheel steering button on the control panel for at least one second. The Load Isolation System (LIS) is another new option that enhances the operator’s driving comfort by mitigating the impact transmitted to the front of the machine, when driving off road on uneven and tough terrain. The Boom Suspension (LIS) function is also actuated by pressing a button on the control panel - it can be automatically activated when the driving speed is 5 km/h ± 0.5 km/h or higher, and the function is deactivated at 4 km/h ± 0.5 km/h. The cab features as standard a deluxe steering wheel with a chrome plated spoke and logo. The new two spoke wheel design provides increased operator visibility. The steering column also has a new design including an 80 mm telescopic function, which allows the operator to bring the steering wheel closer to them, so that they can find their optimal driving position. In addition, there is a new tilting lever, providing a 15-degree tilt towards the operator, to increase visibility over the top of the steering wheel, when they are doing trenching work, for example. The narrower design of the steering column also contributes to enhanced visibility. SPC3 SMART POWER CONTROLS
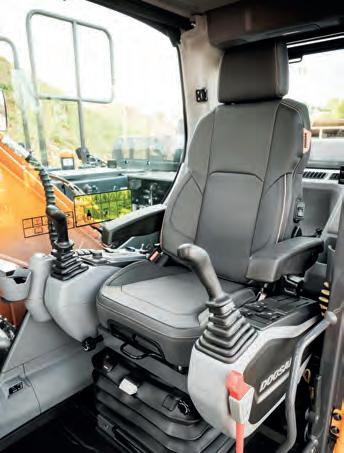
In all the new excavators, the enhanced fuel efficiency of the engines in combination with a new hydraulic main valve and the new generation SPC3 Smart Power Controls, provides increased fuel saving compared to the previous generation machines. There are four power modes now available on the excavators, which help to simplify the operation of the new excavators compared to the more complex choice of eight power modes and SPC combinations in the previous machines. The operator is able to set the power mode (P+, P, S or E) in both one-way and two-way working modes.
news
Growth in Construction and Forestry Sectors Creates Job Openings at McHale Plant
Evidence of growth within the construction plant and forestry sectors can be seen in a number of job openings at leading Komatsu distributor, McHale Plant Sales – all fuelled by what company chairman, Michael McHale says is “an uplift in the economy, renewed confidence on the part of plant users, and a need to expand and upgrade plant inventories”.
In their Komatsu construction plant division, openings exist at the Birdhill and Rathcoolebased firm for three Service Engineers, including one Leinster based and another based in the UK to service the needs of Irish contractors carrying out contract work in that market. In their Komatsu Forest division - which services clients across the entire 32-counties - openings exist for a Sales and Customer Support Manager and a Mobile Service Engineer. A number of construction plant apprenticeship vacancies also exist. Comments Michael McHale: “Currently experiencing significant growth, the plant sector offers a host of highly interesting, rewarding and career fulfilling opportunities. Being one of Ireland’s foremost operators with ‘big name’ distributorships, a well-managed structure and an all-island client base, the roles we have on offer provide solid, secure and exciting opportunities for qualified applicants. “In addition, for young applicants seeking a foothold in the industry and qualifications recognised and accepted in countries across the globe, we have a number of apprenticeships available,” he added.

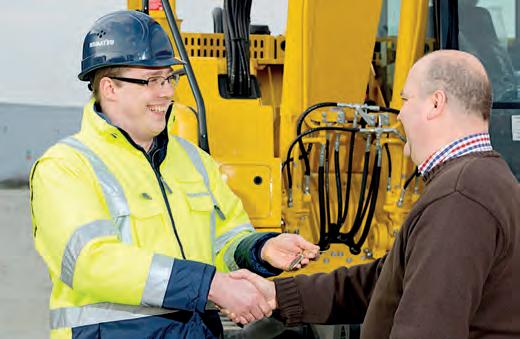
John Deere Reveals Fully Autonomous Tractor
John Deere has unveiled a fully autonomous tractor that’s ready for large-scale production. The machine combines Deere’s 8R tractor, TruSetenabled chisel plow, GPS guidance system, and new advanced technologies. The autonomous tractor will be available to farmers later this year.
The 8R410 looks very similar in appearance to a conventional tractor of the series but is equipped with state-of-the-art technology for controlling and monitoring the tractor and mounted excavator. • The autonomous tractor has six pairs of stereo cameras, which enables 360-degree obstacle detection and the calculation of distance. • Images captured by the cameras are passed through a deep neural network that classifies each pixel in approximately
100 milliseconds and determines if the machine continues to move or stops, depending on if an obstacle is detected. • The autonomous tractor is also continuously checking its position relative to a geofence, ensuring it is operating where it is supposed to, and is within less than an inch of accuracy. To use the autonomous tractor, farmers only need to transport the machine to a field and configure it for autonomous operation. Using John Deere Operations Center Mobile, they can swipe from left to right to start the machine. While the machine is working the farmer can leave the field to focus on other tasks, while monitoring the machine’s status from their mobile device. John Deere Operations Center Mobile provides access to live video, images, data and metrics, and allows a farmer to adjust speed, depth and more. In the event of any job quality anomalies or machine health issues, farmers will be notified remotely and can make adjustments to optimise the performance of the machine. Currently, the technology for the 8R410 is available in combination with a special John Deere chisel plow. A limited number of tractors will be delivered to North American customers this year. In the coming years, John Deere will work on the availability of the technology for further machines and attachments. Alas, the launch of the brand in Europe is currently not planned, as safety regulations currently do not allow the use of autonomous vehicles.
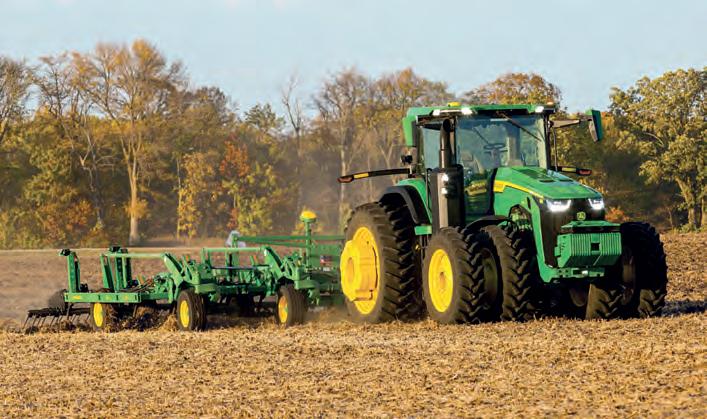
Doosan Infracore Europe has signed an exclusive supply agreement with Netherlands-based TobrocoGiant, a leading manufacturer of Compact Wheel Loaders for materials handling, construction, rental, agriculture and landscaping.
Under the new agreement, selected Compact Wheel Loader models will be manufactured by Tobroco-Giant in the orange colours of Doosan and will be sold under the Doosan name through the brand’s European dealer network. Chris Jeong, CEO at Doosan Infracore Europe, stated: “We are delighted with our new partnership with TobrocoGiant. Doosan Infracore is constantly looking at improving and extending the product offering from the company, to ensure our customers have the most innovative and competitive solutions for their needs. With Tobroco-Giant, we have a partner with long-standing experience and a high-performing range of Compact Wheel Loaders.” Toine Brock, CEO at Tobroco-Giant, said: “This new partnership with Doosan Infracore Europe is the next milestone in the growth of our company. Doosan is well known for their innovative products and customer service, which is a great fit for Tobroco-Giant. We are looking forward to working with Doosan Infracore Europe to grow the market for Compact Wheel Loaders.” Doosan Infracore Europe will introduce the first models to be supplied under the new agreement in the weight category from 3500 to 5000 kg in 2022. Overall, the new partnership covers a total of five Compact Wheel Loader models, which will be distributed across all of Europe. Doosan Infracore Europe will also provide more details on attachments for the range in 2022.
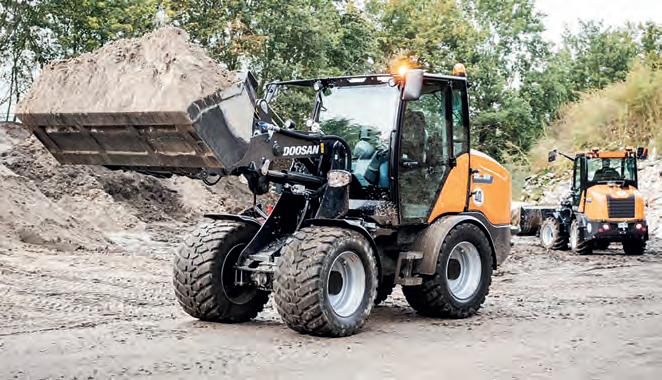
New smart creep for Cat D3 Series Skid Steer Loaders & Compact Track Loaders
Caterpillar will soon launch a new smart creep feature for the full range of Cat® D3 Skid Steer Loaders (SSL) and Compact Track Loaders (CTL) for operating Cat cold planer and wheel saw attachments.
Smart creep senses the load on the attachment and automatically adjusts the drive command to keep the cold planer or wheel saw running at the most productive speed. A combination of attachment sensors and proprietary software optimally balances attachment load and machine speed to maximize productivity. By continually sensing the load on the attachment, smart creep increases machine speed when encountering less resistance and automatically slows the machine when encountering higher load. Engine load remains constant, while the operator can monitor hydraulic pressure on the in-cab display panel. Smart creep takes the guess work out of setting the right creep speed for operating the attachment. Without the aid of this feature, setting creep speed too fast can lead to stalling the attachment, and too slow of speed results in productivity loss. Smart creep software smoothly and efficiently determines the optimal machine speed for cutting conditions. With this new smart attachment feature from Caterpillar, the operator needs only to activate the standard creep control system and set the maximum creep speed on the advanced display inside the cab. Once the tool engages the cut, smart creep measures load on the attachment and adjusts the drive command automatically as cutting begins. In the event of the cutter jamming or stalling, an auto reverse feature within smart creep quickly changes machine direction to allow the tool to clear the jam. Targeted availability for smart creep on Cat D3 SSL and CTL machines is the third quarter of 2022. A field installation kit consisting of sensors and machine software for operating the new feature will be made available for existing fleet loaders and attachments. Once commercially available, new cold planer and wheel saw purchases will be shipped from the factory with the required hardware installed, and new D3 SSL and CTL models will come smart creep ready from the factory.
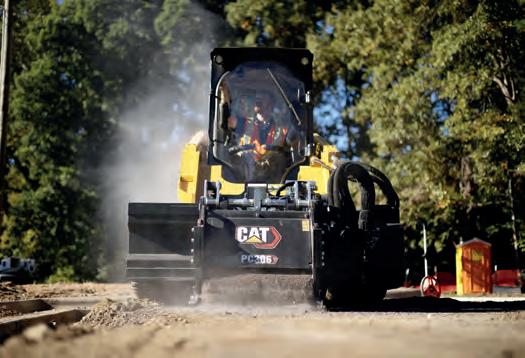
YANMAR’S PREMIUM RED MACHINES PAVE THE WAY TO A NEW ERA

Yanmar Compact Equipment has adopted an eye-catching Premium Red paint colour across all its machines globally, bringing Yanmar’s compact equipment in-line with Yanmar Group’s image; the colour was first introduced onto the North American market in 2020.
“Our dealers and our customers really like the new colour,” commented Jeff Pate, Sales Director, Yanmar Compact Equipment North America. “Everyone feels that Premium Red attracts attention on the jobsite, and just as the quality and reliability of our products stand out from the competition, in a sea of yellow competitive machines in North America, our Premium Red colour stands out too.” But this shift from the well-known Yanmar yellow is more than simply a cosmetic colour change. For Yanmar Compact Equipment, the symbolism of this change resonates on a deeper level. “Yanmar Compact Equipment is on a journey of transformation,” explains CEO, Giuliano Parodi. “We aim to be a global leader in Compact Equipment and, with the help of our dealer partners, deliver sustainable business solutions for our customers and the societies in which they operate. “Our acquisitions of the past few years are now fully integrated into a harmonised, Yanmar CE way of working, with common processes and customer focus right across our enlarged product and services portfolio. For us, Premium Red sends out a clear signal that we are one company, with a clear product strategy. But our transformation goes far beyond our machines. Indeed, we are challenging the way we think and the way we work, to transform our products, our business, and our brand to create even more value for our customers.” ALTERNATIVE FUEL
In product transformation, Yanmar CE is currently evaluating several alternative fuel and powertrain technologies and recently unveiled its first electric mini excavator prototype, the new SV17e. Proudly featuring the new Premium Red colour, the SV17e is aimed at customers in the European market in the 1.5 to 2.0 tonnes segment. “Our prototype is significant because it demonstrates our capability to bring the quality and reliability of our highly respected conventional engine technology into the arena of electrification,” explained Director Product Management EMEA, Cedric Durand. In business transformation, Yanmar Compact Equipment is continuing to invest in manufacturing infrastructure and in expanding their global dealer network to increase the proximity to customers, reduce lead times and improve service. Closely linked to these investments is the focus on creating an amazing customer experience. MORE CHANGES
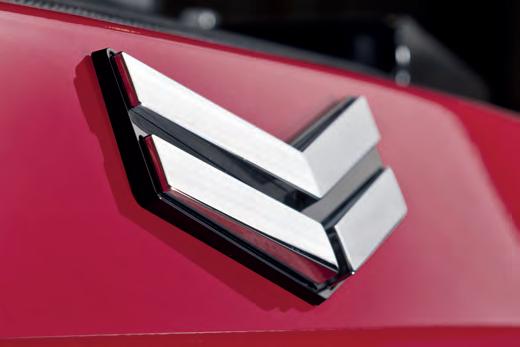
“Our move to Premium Red across our machines certainly signals a change and we are confident that our customers will start to see other changes too,” explained Elsie De Nys, Global Director Channel and Brand Development. “We have the ambition to be a leader, not only in machines but in the customer experience too and are working hard to get closer to our customers to identify new and innovative ways in which we can add value to them.” The change to the new Premium Red also heralds a new confidence in the Yanmar Compact Equipment brand and coincides with the launch of its new tagline, ‘Together We Build’. “Our aim, together with our dealer partners, is to build stronger relationships and create even greater customer value,” said CEO, Giuliano Parodi. ‘Together We Build’ really underlines our commitment to transforming Yanmar CE and, with the help of our dealers, to focus on creating a new and exciting experience for our customers.” For Yanmar Compact Equipment, change is in the air and the fresh, new image of the Premium Red machines certainly reflects the optimism running through the business. This milestone moment is about shared goals and ambitions and about building a better future for everyone.

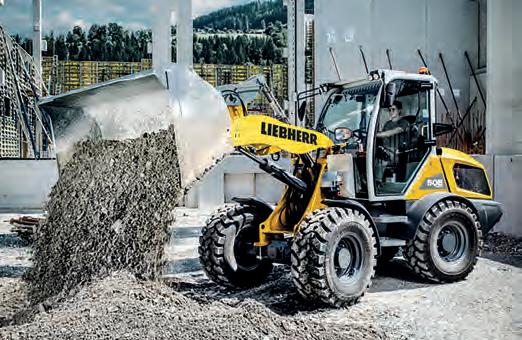
LIEBHERR EXPAND COMPACT LOADER SERIES WITH NEW L 504 COMPACT MODEL
The new Liebherr compact loader series comprises three models which have been optimally coordinated with one another; the new L 504 compact joins the company’s wheel loader range. Liebherr’s smallest wheel loader embodies the qualities of the larger Liebherr wheel loaders while also being an excellent value for the money. With numerous new features, the L 506 compact has consolidated its already strong position in the market.
As is the case for the L 504, the machine height of the L 506 remains under 2.5 metres, making it easy to transport on a trailer. The new L 508 compact, meanwhile, has become larger and wider than both of the other Liebherr compact loaders. Its powerful travel drive and high tipping load have received praise from customers. The new compact loaders have robust lift arms with z-bar kinematics, which facilitates the use of a wide variety of attachments. Liebherr has optimised the parallel guidance for safe and precise operation when working with forks. This is critical, for instance, when transporting palettes with paving stones or decking tiles in garden and landscaping applications. To increase versatility even more, Liebherr offers High Lift lift arms for the L 506 and L 508 models on request. This is an extended version of the lift arms with a greater reach. This enables the compact loaders to also load taller transport vehicles. Wheel loaders are confronted with a myriad of challenges when used in municipal services: Transporting materials with various buckets or forks, excavating with a 4 in 1 bucket, cleaning work with a sweeper, or winter services with a snow plough are just some examples of this. To ensure the mastery of this wide variety of applications, Liebherr offers its fully automatic quick coupler system LIKUFIX for the three compact loaders. LIKUFIX allows the machine operator to change between mechanical and hydraulic working tools from the cab within seconds at the touch of a button. This saves time and reduces the risk of accidents as the operator doesn’t have to leave the cab when changing the equipment. COMFORTABLE AND SAFE
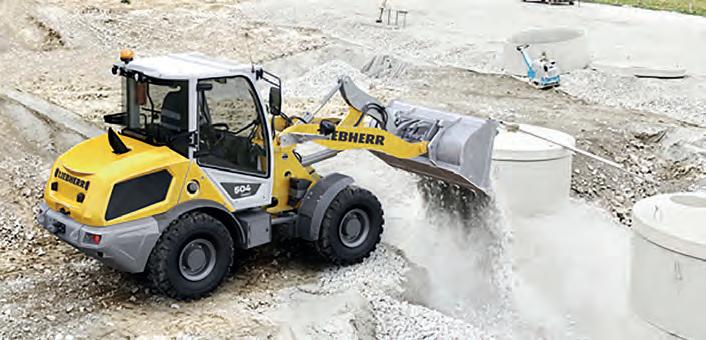
Well thought-out solutions can also be found in the redesigned cab, which can be entered via a sturdy, reinforced step. Of particular note, Liebherr has increased the amount of glass throughout the cab. The windscreen now even reaches into the foot area of the operator’s cab. This ensures better visibility in all directions, particularly of the attachment and in the articulation area. The rear screen is curved on the sides, enabling an unobstructed view of the rear area. The new compact loaders can be equipped with a backup camera on request, for even more safety when reversing. Numerous details, such as the clearlyarranged control elements or the practical storage areas, increase comfort in the operator’s cab. With the proven Liebherr control lever, the machine operator can operate the lift arms and the attachment safely. This also applies to the optional mini joystick on the control lever, which is used to control additional hydraulic functions. Optionally available is an infinitely-adjustable steering column; the display, standard on all machines, is also adjustable and located on the A pillar in the cab. These measures ensure simple and intuitive operation of the compact loader, which plays an important role, especially, for example, for rental construction machines. Liebherr’s new compact loaders feature a modern and functional design. The engine bonnet has a dynamic and clean design, with great visibility from the cab. The lift arms have a tapered design, which optimises the view of the attachment and the material. The compact design with a low centre of gravity ensures optimum weight distribution on the new compact loaders. The result is high stability and safe, comfortable operation, day in and day out.

FULL STEAM AHEAD FOR SPENCER ECA & HIAB

World leading provider of on-road load handling equipment, Hiab, was the supplier of choice for Llandysul-head quartered Spencer Environmental Care Associates, when investing in a new hooklift to support its ongoing work on the nationwide HS2 project.
The land and forest management company selected Hiab’s next generation hooklift, the MULTILIFT Ultima 21S, specially fitted to a Scania truck, to join its 10-strong fleet of trucks. The specialist equipment will be used by Spencer ECA to deliver construction vehicles, machinery and materials, including excavators and Signaroad temporary roadway, to gain access and facilitate development at various sites across the country.
Established in 1991, Spencer ECA is one of the most respected operators in the land, forest maintenance and groundworks sector and currently operates from locations across the UK, including Llandysul, Swansea, Exeter, Bicester and Colchester. Nathan Best, transport controller at Spencer ECA, commented: “Due to the nature of our work, precision and reliability is of paramount importance and so we needed a hooklift that would enable us to do our job with as much ease, accuracy and control as possible. “The MULTILIFT Ultima does exactly that and more. The Hiab name alone is one we associate with quality and reliability and this piece of kit goes to the next level with features that further boost our confidence in what we are doing.” One example of the technology featured on the MULTILIFT Ultima is its HookliftAssist camera-guided control, which provides exactly the level of control each loading task require, with four different levels designed to meet a range of needs. Dek Butler, MULTILIFT specialist for Hiab UK added: “We’re proud to have been selected by Spencer ECA who really are known as one of the best in their field and it’s great that they were able to find a product that met all of their requirements. “The MULTILIFT Ultima really does stand out from the crowd thanks its vast amount of features that have been expertly engineered to ensure ultimate precision and safety and therefore confidence for the operator.” The MULTILIFT Ultima forms part of Hiab’s wider MULTILIFT range which features a range of pioneering load handling solutions.

HOOKLIFT ASSIST
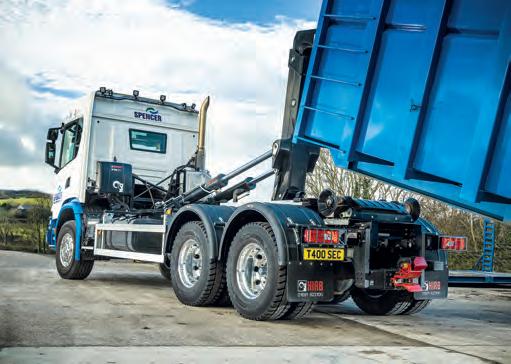
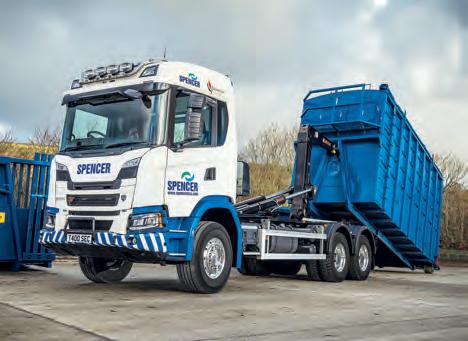
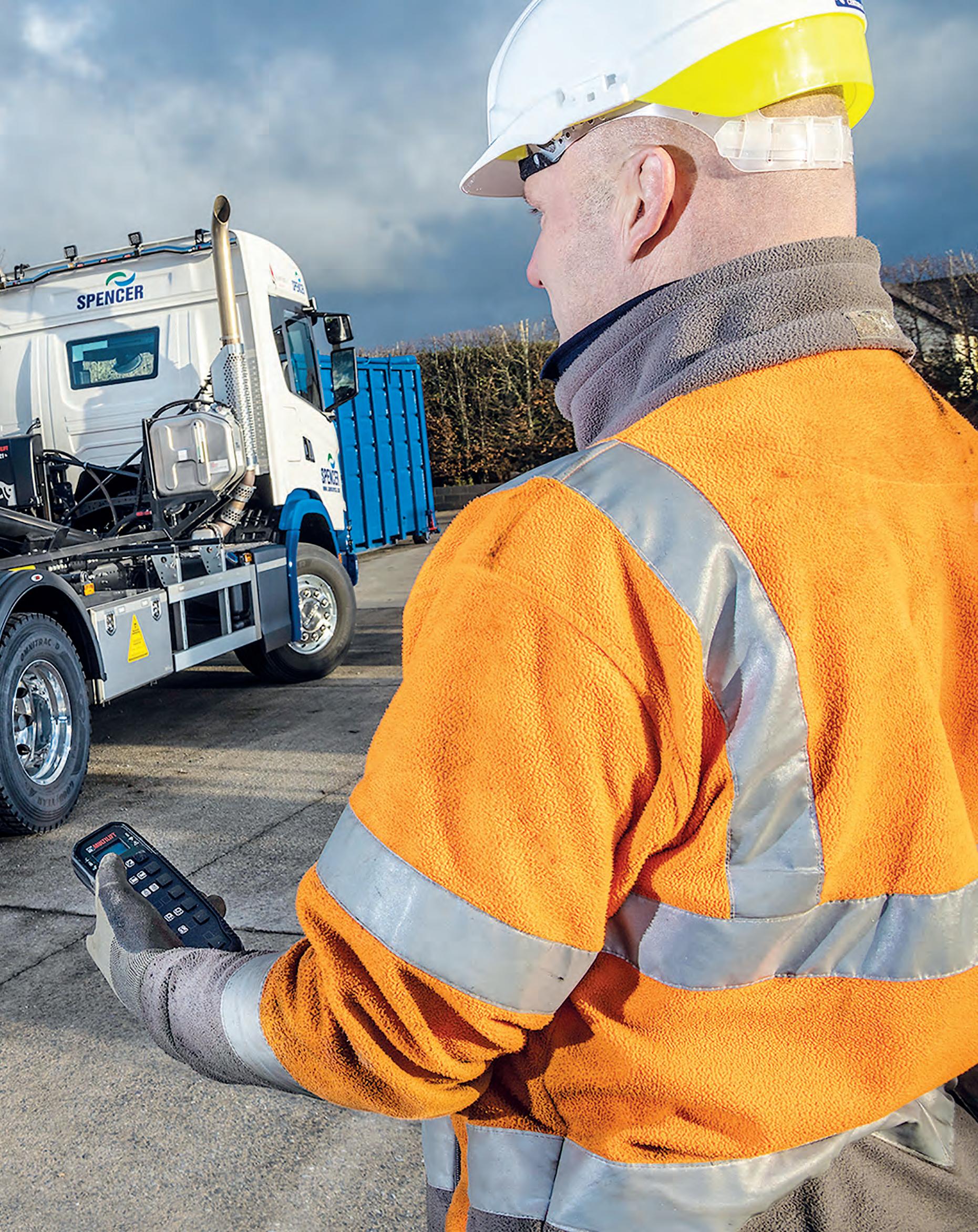
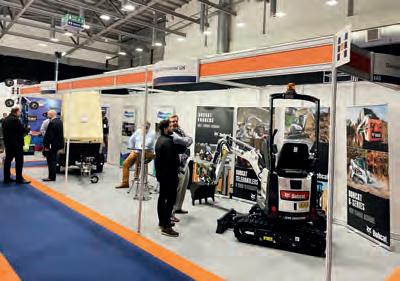

EXECUTIVE HIRE SHOW 2022 A SELL OUT
Regarded as the national event for tools, plant and equipment hire and first launched in 2007, this year’s Executive Hire Show was a sell out.
An unmissable national exhibition for the tools, equipment and plant hire industry, the two day event was staged at the popular Coventry Building Society Arena, located at the heart of the UK motorway network. There were 154 exhibitors and of those, an impressive 42 were making their firstever appearance at the Show. Many exhibitors also doubled their stand space this year, while the venue received a cash injection of more than £7.5 million for a revamp which has delivered a world-class exhibition, event, and conference centre. A trade-only event open to hire executives throughout the UK and Ireland, it also attracted hire industry visitors from Europe and beyond, with senior executives from the procurement and purchasing departments of the national hire operations attending, along with large numbers of independently-owned entrepreneurial hire outlets. Indeed, at this year’s Show, 86% of visitors were from independent hire companies. Plant & Civil Engineer was there to capture some of the show’s highlights on camera.
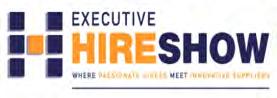
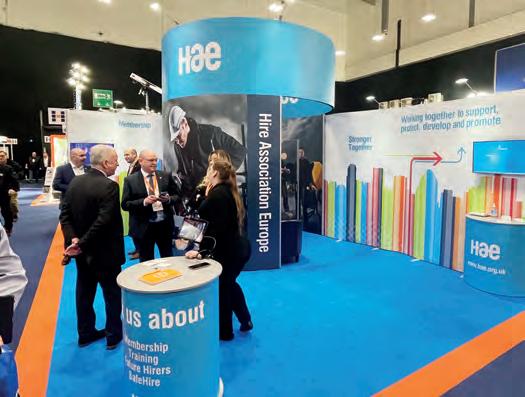
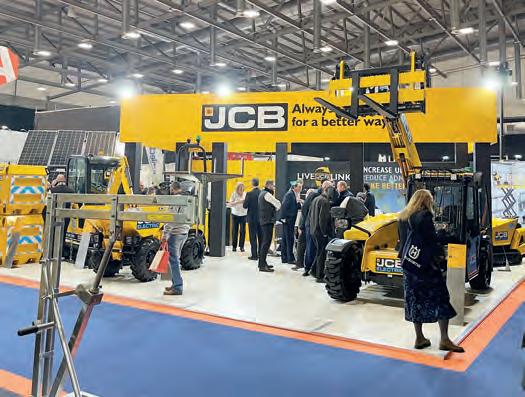
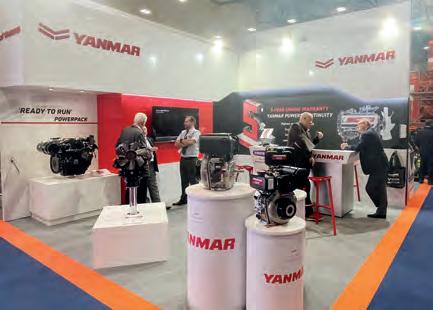
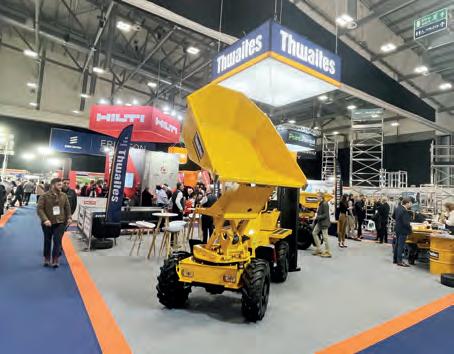
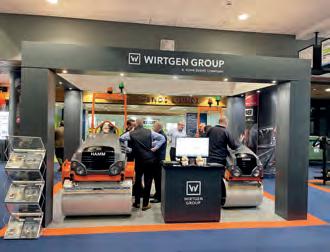