
20 minute read
Mallon looks back at two years as Infrastructure Minister
DEMOLITION WORK MUST BE PROPERLY PLANNED AND MANAGED TO PREVENT SERIOUS INJURY
Great Britain’s workplace regulator is asking demolition and construction firms to double-down on thorough planning, management and control of demolition and refurbishment work.
The Health and Safety Executive (HSE) is asking that businesses properly plan, organise, manage, and monitor their work and use competent people to avoid incidents and ill health amongst their workers and the public. It is reminding companies that the safer they are, the more efficient they are. Good health and safety management increases the likelihood of contracts coming in on time and within budget with fewer added costs, and often to a higher quality. In the past year HSE has dealt with prosecutions involving severe injuries and fatalities as a result of poorly planned demolition work. This has included: • A contractor who suffered serious injuries when a single-story roof he was demolishing by hand, collapsed at a construction site in Cobham, Surrey. • A 64-year-old man who was killed when a garage wall at a garden in Hampshire collapsed on him during demolition, after a contractor who was operating a digger failed to put an exclusion zone in place whilst carrying out the work. • A 21-year-old employee who was killed whilst dismantling a redundant grain drying tunnel at a farm in Kent when a farming partnership failed to ensure the integrity of the structure during the dismantling process. • An employee who sustained injuries to his shoulder, and a fractured heel and ankle when he was hit by falling debris from a garage wall in Clitheroe that was being demolished in an unsafe manner. • A contractor who was prosecuted for disturbing asbestos and damaging underground cables during demolition works at a site in
Blackburn, causing severe disruption to services. • The operator of a cherry picker who sustained lifechanging injuries when he became trapped during a demolition operation at a site in Greater Manchester. A HSE investigation found the vehicle he was operating was not suitable for the task and had not been fitted with propriety devices to avoid the likelihood of operators being crushed. INVESTIGATE & APPRAISE
HSE is reminding contractors that it is crucial to complete a survey ahead of demolition work including structural investigation and appraisal, which considers the age of the structure, type of construction, history of the building including alterations and design codes used to avoid an uncontrolled collapse. Specific consideration should also be given to the effect of additional weight of demolition machinery and debris on suspended floors; and the risks to nearby buildings and structures. HSE’s head of construction Sarah Jardine said: “Structural instability can be a problem in buildings that are old, decayed, poorly maintained, and in newer buildings that have been badly designed and constructed or abused in use. “Even sound structures can become unstable because of a lack of planning of construction and demolition work.” She added: “It is easy to get it wrong even on small, straightforward structures, which makes it even more important to put the planning in place when it comes to demolishing large, complex structures. Demolishing
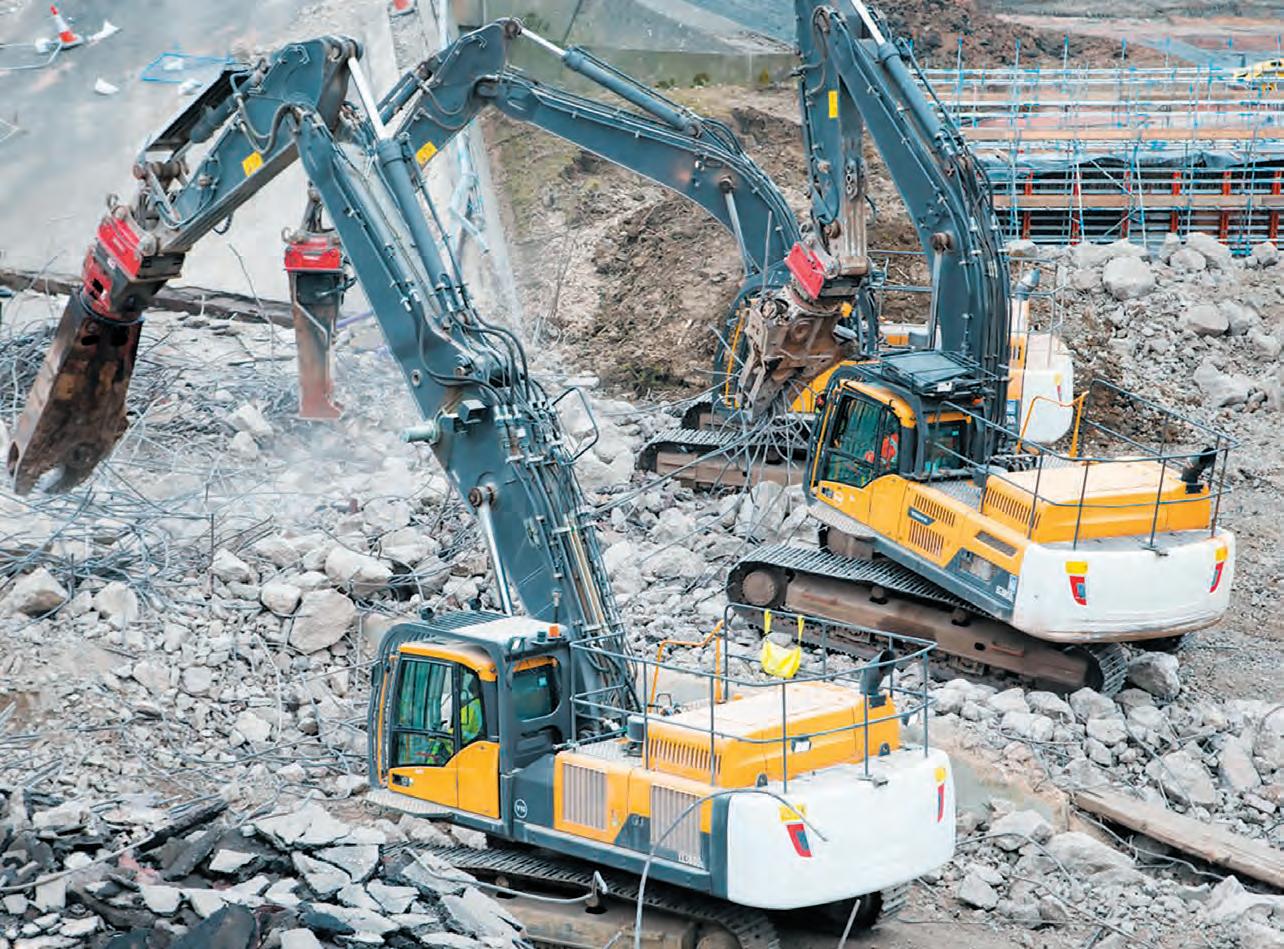
these types of structures is a particularly hazardous activity and doing it safely is highly complicated and technical, so relevant expertise is vital. These jobs require careful planning and execution by contractors who are competent in the full range of demolition techniques and have access to designers and engineers with the right knowledge, skills, and experience in this area.” A systematic approach to demolition projects should be a team effort. Clients must appoint professionals who have the relevant skills, knowledge, experience, organisational capability, and who are adequately resourced. Clients, with the help of the principal designer must provide essential pre-construction information to the relevant designers and engineers. This should include a range of surveys and reports to check for presence of asbestos, structural stability, and the location of above and below ground live services. RESPONSIBILITIES
It is the principal designer’s responsibility to plan, manage, monitor, and coordinate health and safety issues in the preconstruction phase to ensure principal contractors are provided with relevant information to enable them to put safety measures in place. Once the demolition work has begun it is the principal contractor’s responsibility to plan, manage and monitor the demolition activities and coordinate work to ensure that it is carried out without risks to health and safety. While site managers must ensure workers are supervised and are following safe working practice. Sarah Jardine added: “Incidents caused by poor planning and risk management can have substantial human costs that are felt for many years by the victims and their families. “In addition to the impact on people’s lives, incidents can also lead to substantial remediation costs, higher insurance premiums, and, if HSE investigates, court fines and prison sentences, which will inevitably impact reputations. “As well as being morally right, it is simply common sense and good business to ensure rigorous planning, organising, managing and monitoring of the whole project.”
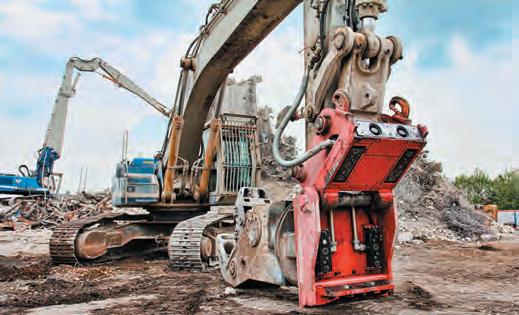
news Record-breaking Year for Safe Digging in the UK
LSBUD, the UK’s leading online safe digging resource, welcomed more than 3.4 million searches for underground pipes and cables pass through its central system in 2021.
This figure is up 13 percent on 2020, showcasing how all industries, particularly the farming, construction, highways, telecoms, water, gas and electricity sectors, are more committed to safe digging than has ever been the case before. Richard Broome, MD at LSBUD, comments: “In order to approach the 3.5 million milestone, our portal has received a search enquiry every two seconds during the average working day. This is more often than we blink, which is just phenomenal. These searches precede all sorts of activity, such as farmers checking before replacing fences and excavation workers keeping safe digging in mind before digging up a road to install broadband and electricity cables or water and gas pipes. “Clearly, operators from all industry sectors are taking the right steps to avoid the negative consequences that come from hitting an underground asset, chiefly health and safety disasters, plus significant financial and brand implications. It’s such brilliant news that the majority of people involved in digging work are taking note of the fact that this can all be avoided through asset searching. “We want to thank every farmer, construction, highways, telecoms, water, gas and electricity worker, that searches before they dig. They’re keeping themselves and those working nearby safe while protecting all-important infrastructure from unnecessary damages. It is also great to see more homeowners and consumers performing a search. Out of the 3,000 new registrations we are now receiving every month, domestic customers are actually one of the fastest growing groups. It is great to see. “We’re also seeing more and more decisionmakers appreciating the importance of data sharing through making their networks visible on our platform. They are able to benefit from the ‘safety of the herd’ effect – the more asset owners who share their information through one central portal, the more enquiries they receive, while keeping everyone safe.” LSBUD now has over 100 members signed up across industry, including two out of three of the UK’s utility operators, 90 percent of gas distribution networks, 92 percent of electricity distribution networks and 99 percent of fuel/ oil pipeline operators. This has led to LSBUD hosting over 1 million kilometres of the UK’s 1.5 million kilometres of underground network on its portal. Two thirds of this has been added since 2017, that is the equivalent to travelling around the world 25 times. As a result, the number of ‘affected’ notifications, the number of responses sent on behalf of Members are up to over 600,000 per month, compared to 250,000 just three years ago. Adds Richard Broome: “When you consider all of this, it’s laughable that the UK Government’s new National Underground Register (NUAR) is attempting to portray the safe digging industry as a disjointed community that needs Government intervention. The evidence wholeheartedly rejects this. “It’s therefore immensely disappointing to see the Geospatial Commission ploughing millions of pounds of taxpayers money into a ‘solution’ that will in fact only be able to help a small minority of LSBUD’s users. “The important thing is that industry continues its momentum with LSBUD to take safe digging in the UK to the next level.”
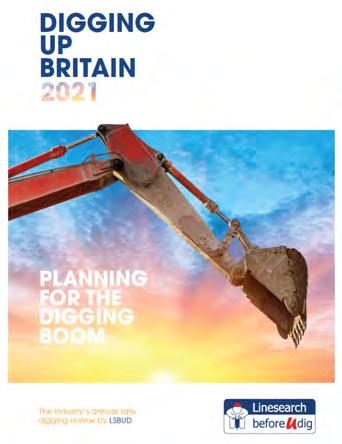
Molson Group Join Prostack as Authorised Distributor for UK
ProStack has welcomed Molson Group as their latest distributor; Molson are a long-established partner to Terex and will represent the full portfolio of bulk material handling and product stockpiling conveying equipment across the UK.
ProStack offers a comprehensive portfolio of products to address the needs of the bulk material handling and product stockpiling markets. Key markets and applications include aggregate, mining, recycling, agriculture, ports and terminals and many other bulk material handling industries. The ever-growing range of ProStack machines include tracked and telescopic conveyors, port hoppers and bulk reception feeders. Molson Group was formed over 25 years ago and has earned itself a place as the UK’s largest independent new and used equipment dealer. They currently have 13 locations strategically

Pictured together at the recent Molson Group Open day and launch of the partnership are (L-R) Lee Nesbitt, ProStack Global Sales Director, Jason Powles, Molson Group Chief Operating Officer, Kieran Hegarty, President of Terex Materials Processing, Thomas McKiver, Molson Group Sales Manager, Terence Bratton, ProStack Technical Sales Director and Steven Aiken, ProStack Business Line Director.
placed throughout the UK, from Cornwall to Inverness, allowing them to provide a truly local and prompt service. With over 85 fully trained service engineers and £8m worth of parts stock at any time, Molson Group are always there to keep operations running. A customer focused approach is what sets Molson apart, they are able to provide clients of all sizes a single source supply option of market leading products, backed up by a team that care about their customers’ business. Lee Nesbitt, ProStack Global Sales Manager said: “Molson have strong relationships with other Terex brands and we feel they are the perfect fit for ProStack. Their wealth of experience in the industry and reputation in the UK is invaluable to us and I am confident they can help us grow and dominate the bulk material handling market in the UK. We look forward to a long and prosperous working life together.” Commenting on their recent appointment, Jason Powles, Molson Group Chief Operating Officer said, “ProStack products are a fantastic addition to our product portfolio. Like the other Terex brands we already offer, ProStack are known throughout the world for their build quality and innovation. Their range bulk material handling and product stockpilers will further enhance our single source supply strategy, particularly to the Ports sector.” In addition to sales opportunities, Molson will provide parts, service and warranty support for ProStack equipment by factorytrained technicians. A range of financing options will also be available to qualified customers.
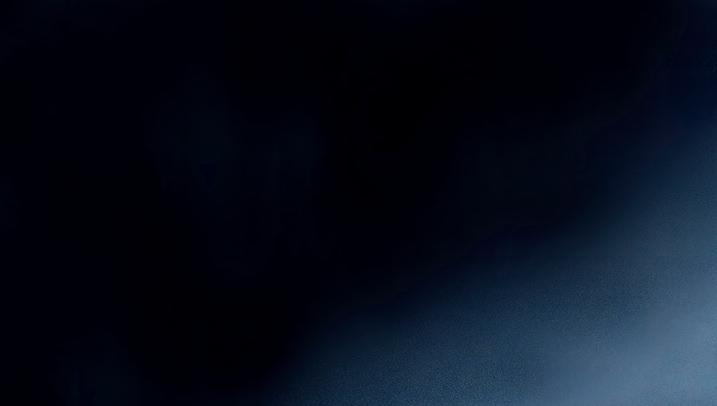
Doosan Bobcat unveiled its new, all-electric Bobcat T7X compact track loader at the recent CES 2022, the world’s most influential technology event, held in Las Vegas in the USA.
The T7X is the first machine of its kind to be fully electric, offering the full benefits of eliminating hydraulic systems, components, emissions and vibrations – all while providing a cleaner, quieter machine. The Bobcat T7X was honoured with two 2022 CES Innovation Awards in the categories of Vehicle Intelligence & Transportation and Smart Cities. The CES Innovation Awards programme recognises recipients in a multitude of technology product categories and distinguishes the highest rated in each. The Bobcat T7X was developed for the North American market initially, but internal testing and the gathering of customer feedback is planned for the Europe, Middle East and Africa (EMEA) region to identify its commercial potential. Scott Park, President and CEO of Doosan Bobcat, said: “Doosan Bobcat is at the forefront of innovation, and we are proud to debut the all-electric technology of the T7X to help customers maximize both sustainability and productivity. Our focus remains on providing solutions and products that empower people to accomplish more and build a better world.” The Bobcat T7X is the world’s first all-electric compact track loader. This machine is fully battery-powered, built to be more productive from the ground up with electric actuation and propulsion, quieter with high-performance torque and more powerful than any diesel-fuelled track loader that has ever come before it – all while eliminating any carbon emissions. “This machine is a technological feat for Bobcat and for the entire industry,” said Joel Honeyman, Vice President of Global Innovation at Doosan Bobcat. “We challenged the status quo to deliver a connected, all-electric machine designed for power and performance that previously was not possible. We are excited to share this advancement with the world and proud of the hard work that has gone into making this a reality.” ZERO EMISSIONS
In the T7X, the traditional hydraulic work group has been completely replaced with an electrical drive system consisting of electric cylinders and electric drive motors, which means virtually no fluids. The new, all-electric Bobcat T7X uses just under one litre of eco-friendly coolant compared to around 216 litres of fluid in its diesel/ hydraulic equivalent model. The all-electric platform enables instantaneous power and peak torque available at every operating speed. The operator no longer must wait for the standard hydraulic system to build up power. The T7X operates with zero emissions and reduced noise and vibration generated by the machine. It works quietly and efficiently in noise sensitive areas and indoors, which significantly lowers sound levels and improves the working environment. It can also significantly lower daily operating costs, when considering the reduction in annual maintenance costs and elimination of diesel, engine oil, diesel exhaust fluid and hydraulic parts. At the heart of the T7X is a powerful 62 kW lithium-ion battery from technology partner, Green Machine Equipment, Inc. While applications vary, each charge can support common daily work operations and the use of intelligent work modes for up to four hours of continuous operation time and a full day of operation during intermittent use. The intelligence of the power management system is programmed to sense when loads are increasing, automatically backing off power when not needed to preserve the total energy use and extend the machine’s runtime.
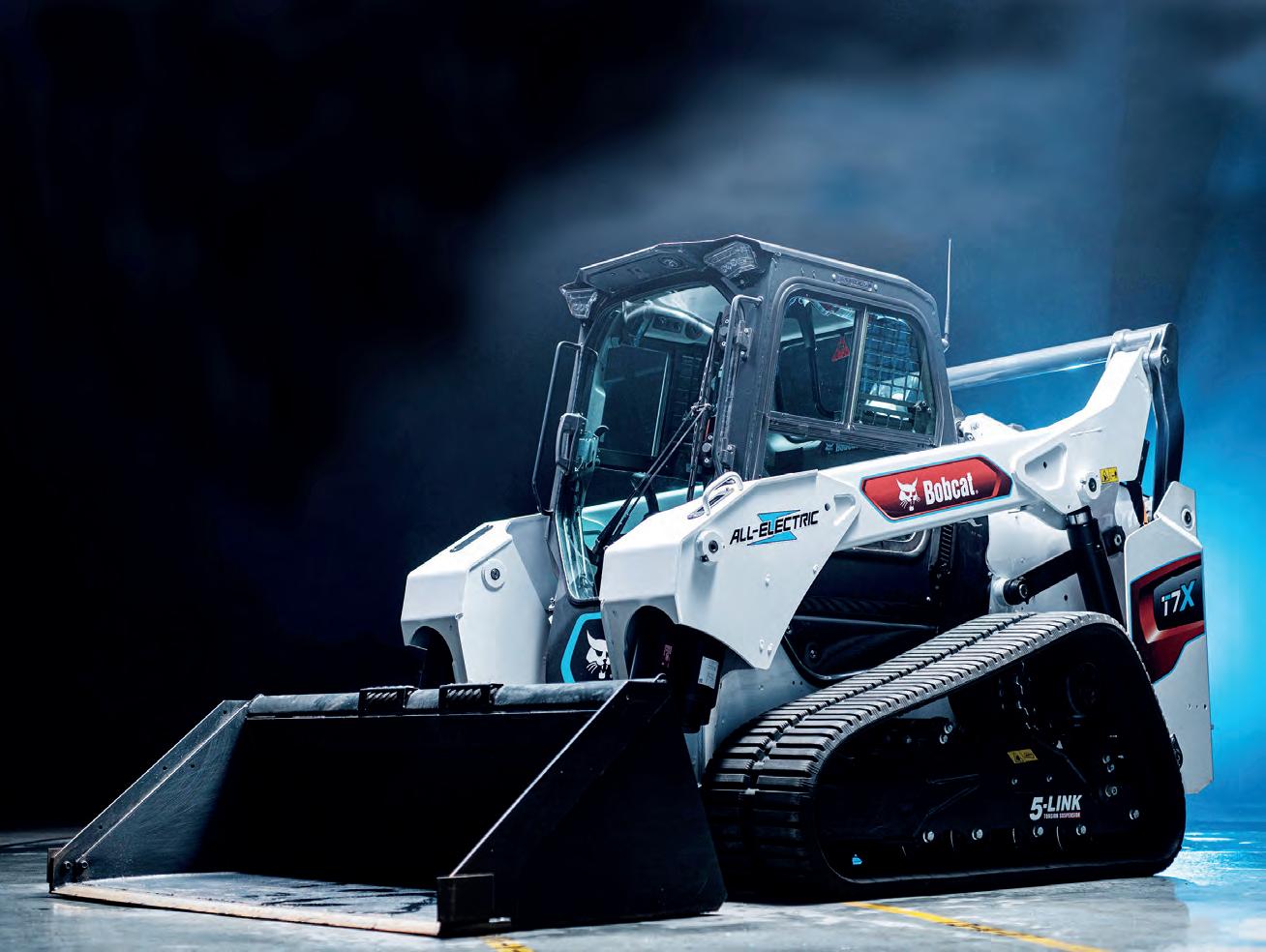
LARGEST CRANE IN LIEBHERR’S “TOUGH ONES” SERIES IS UNVEILED
Liebherr’s successful EC-B series has a strong new addition: the new 470 EC-B Flat-Top crane. With a maximum lifting capacity of 16 or 20 tonnes, this crane is now the largest in the “Tough Ones” family.
The flagship crane with intelligent assistance systems offers a jib length of 80 metres. This reach can be increased to 83 metres by means of a jib extension, thereby breaking new ground in the competitive market. At a jib length of 80 metres, the 16-tonne version of the 470 EC-B has a jib head load capacity of up to 3,200 kilograms; the 20-tonne version impresses with a jib head load capacity of up to 3,000 kilograms. The jib can be divided into twoand-a-half metre sections so that it can be perfectly adapted to meet a variety of operational requirements. The 470 EC-B went on sale in January of this year. The focus during development wasn’t only on performance but also on assembly and transport. As a result, the jib and counter-jib can be attached to the slewing platform easily, conveniently and safely. Liebherr’s proven quick assembly connections make it all possible. Only five trucks are needed to transport the slewing part with jib, including counter-ballast, to the construction site. This saves time and money, and also helps reduce emissions. The 470 EC-B features a connection for both 24 HC 420 and 24 HC 630 tower systems. The 24 HC tower system is a perfect match for large cranes with high lifting capacities. Its compact dimensions allow individual elements to be moved cost-efficiently from A to B. The 470 EC-B has been optimised for the 24 HC 420 tower system; together they are the most cost-effective combination for freestanding hook heights of up to 67.8 metres. The maximum freestanding hook height of up to 96 metres is achieved with the 24 HC 630 system. EXCELLENT SITE OVERVIEW
The top-slewing crane is available with one of three versions of the sophisticated LiCAB crane operator’s cab: LiCAB Basic, LiCAB Air or LiCABAirPlus. All three offer a floor space of more than two square metres, an unrestricted view for precision lifting and an ergonomic control stand. These and other comfort features enable the crane operator to stay fully focused on the job at hand. Thanks to the cab’s extensive field of vision, the crane operator has a clear view of the site and the load to be lifted, which contributes to the safety of both operator and machine. Also included in the cab is the newly developed twelve-inch display screen with intuitive operability. The Tower Crane Operating System (TC-OS) provides crane operators and assembly engineers with specific menus, an extensive choice of languages and user-friendly units of measurement. The intention is that every user should be able to find the parameters relevant to their work without difficulty. Users navigate their way through the streamlined menu structure via touchscreen. To maintain an overview during crane operation or scaling, display masks can be combined in various ways. The exceptional usability of the TC-OS means that training and familiarisation times are reduced. LED LIGHTING
LED advertising panel lighting can be configured to ensure a substantial longdistance effect and visibility, particularly at the onset of twilight and at night. With a total area of 8.6 square metres, the robust lighting is capable of delivering a powerful and effective promotional impact. The panels don’t have to be mounted separately during assembly and can remain in place on the counter-jib end section during transport. Signage is easily applied. As they don’t have a tower head structure, several EC-B series Flat-Top cranes are able to work together safely on the same site, even in tight conditions. Transport, assembly, handling capacity and safety: EC-B cranes are specifically designed to meet the requirements of modern construction sites. They cover a wide performance spectrum, ranging from small city to large handling cranes. The new 470 EC-B completes the top end of Liebherr’s successful series, with the crane reflecting the construction industry’s trend towards ever heavier components.
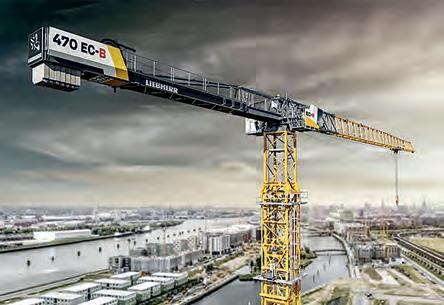
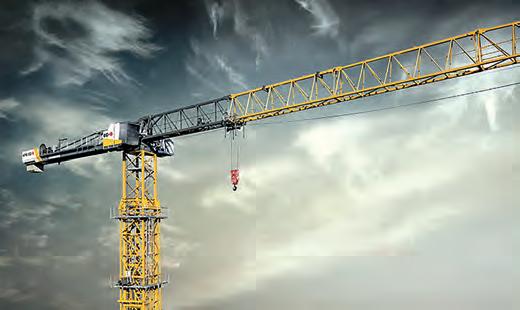

THE BENEFITS OF REBUILDING YOUR CONSTRUCTION DIESEL ENGINE
On brownfield construction sites, industrial diesel engines power equipment including cherry pickers, cranes and screeners. Each of these machines are vital in keeping projects on schedule, meaning construction companies must regularly maintain their equipment to ensure productivity and reliability. When the engine finally reaches the end of its life, construction businesses can then rebuild it so that it runs like new again.
Here Peter Hutyan, Product Manager for Energy and Transportation at Finning UK & Ireland, explains the benefits of an industrial engine rebuild and offers some tips. Industrial diesel engines can be found in a wide range of construction machines, on anything from small commercial sites to large infrastructure projects. Whatever the equipment or project size, it is essential that the engine can continue to provide the hydraulic and rotational power that these machines require. Traditionally, an industrial engine will last anywhere between 10,000 to 30,000 hours before requiring a major overhaul. When the engine reaches the end of its life, it may be tempting to simply replace it with a newer model. However, keeping the engine running until failure can increase costs and introduce various risks. MAINTAINING UPTIME
Most construction projects have tight deadlines and require specialised equipment at different stages. For example, this could be a specific type of crane, an excavator or any other machine. Project progress is vital for every construction firm, which means having each machine running so that work does not come to a sudden halt. While not every industrial machine is critical, most operators rely on engine uptime. For example, machines like crushers and cherry pickers are only on site when they are needed and having just one out of action can cause delays, extending lead times significantly. If operators keep their engine running until the end of its life, this can compromise performance because legacy engines are typically less productive and efficient than new machines. One example of reduced productivity is when a screener is unable to sort waste from
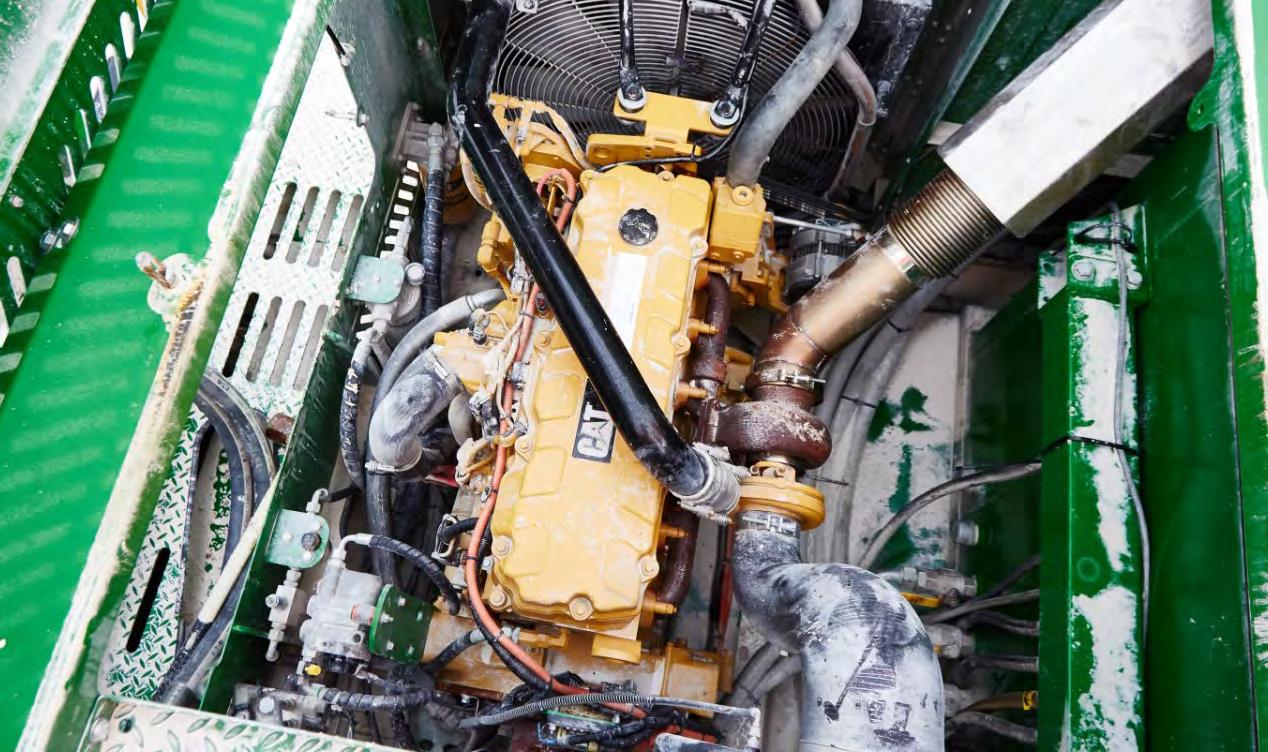
usable materials. If the screener is using an engine nearing the end of its life, it may not be running efficiently, and the operator will need to keep the machine running for longer to compensate. As well causing delays, extended runtime can increase costs, particularly if the operator faces downtime while they source a replacement from the original equipment manufacturer (OEM) when the machine does eventually fail. Rather than face unnecessary downtime, operators can order a complete overhaul of their engine before it reaches the end of its life. By planning in advance, they can they shut down part of the construction site in a controlled way without worrying about and extended period of unplanned downtime. Scheduling a rebuild also gives the operator time to source a rental replacement, ensuring business runs as normal. SELECTING A REBUILD
Many industrial engines are built in a similar way, with minor component variations. In reality, the difference between an engine in a crusher or a crane can come down to its turbocharger. Therefore, the repair strategy is often determined by budget and power restoration requirements, rather than by application. If construction companies have a limited budget and want to save time, a basic value repair will recondition the cylinder heads, piston rings and liners. This option is ideal if a cherry picker or crane, for example, is experiencing a slightly increased fuel consumption and a short-term solution is needed that will see the engine through to its next service. If the engine is experiencing a loss of power or excessive fuel consumption, operators can go that extra mile with a mid-range top and tail recondition. This approach involves renewing all major components, including the cylinder packs and heads, the injectors and pistons. All slowerwearing parts, such as lube oil and water pumps, are also replaced. If the engine is halfway through its 30,000-hour lifecycle, this option will restore vital power and can provide an additional 15,000 hours of runtime. Finally, if they require a like-new engine, operators can select a complete overhaul. During a full workshop recondition, all major components are stripped out, inspected and replaced. This includes the seals, gaskets, bearings and filters. Approximately three quarters of engine parts can be recycled and,with this more thorough option, operators can swap out these components so that they can be restored and reinstalled on another engine. GET THE SUPPORT YOU NEED
When rebuilding an industrial engine, it is essential that operators receive lifecycle assistance, which means having a partner that can offer good technical and commercial support. The rebuild process does not end the minute that the engine leaves the workshop - a good partner will reinstall the engine on the operator’s site and regularly service it to ensure that it is running as intended. By selecting a partner early on, construction companies can understand where the engine is in its lifecycle and collaborate with the service provider’s engineers to devise a tailored support strategy. Look for a partner that uses genuine OEM parts on all its engine rebuilds, supports its customers with preventative maintenance, using scheduled fluid analyses and offers machine telematics to regularly monitor engine condition and performance. Industrial engines are vital in keeping construction projects on track. By tailoring the engine rebuild to the machine and the application, construction firms and hirers can keep their equipment running as intended and ensure maximum uptime. If you partner with Finning, Cat®-certified engineers will carry out a thorough inspection and evaluation of your industrial engine and can replace up to 7,000 of its components with genuine Cat parts. We have engineers working across the UK and Ireland, meaning we can react promptly to your needs. Want to know more about our industrial engine rebuilds? Visit the Finning website.
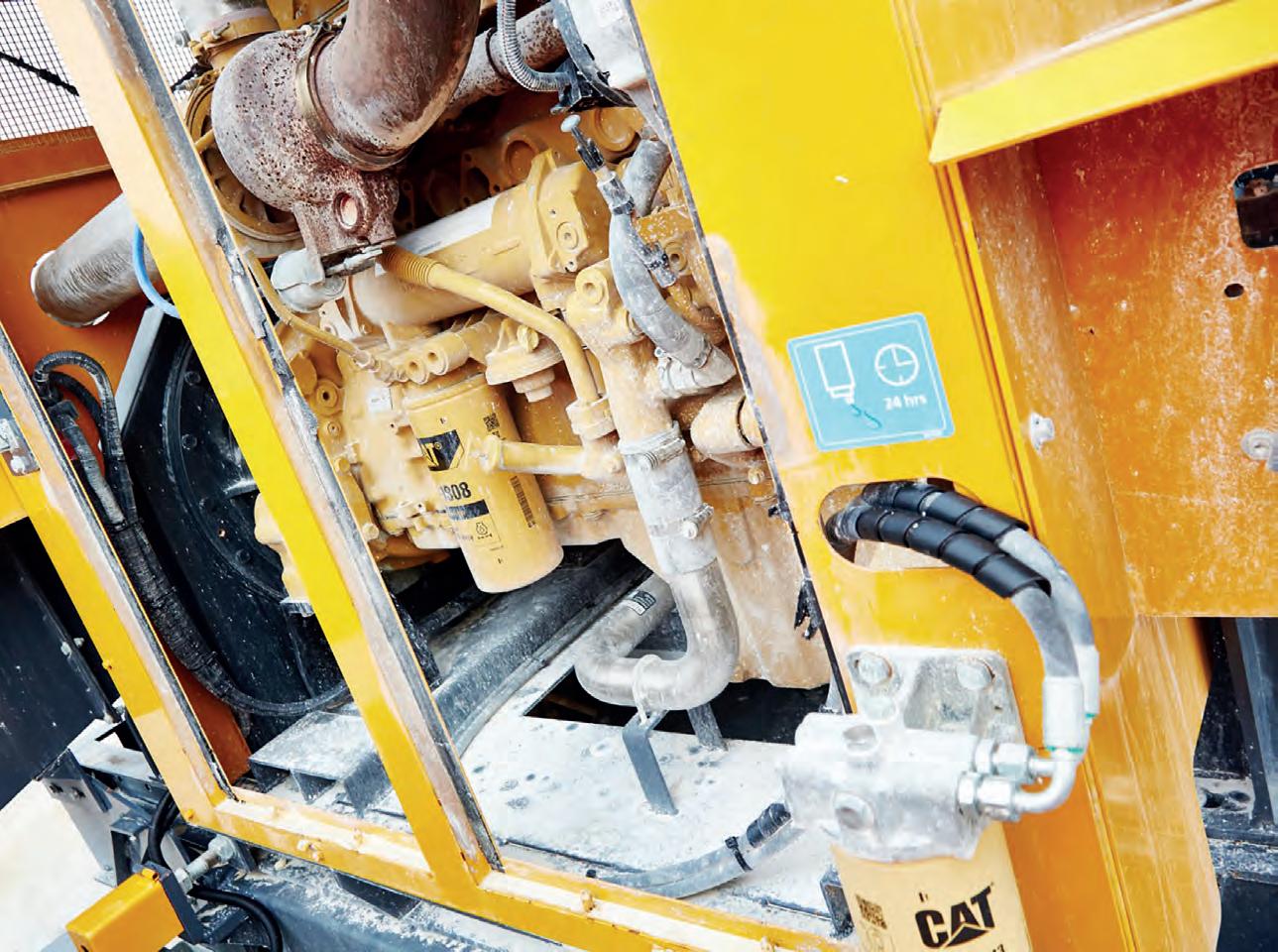