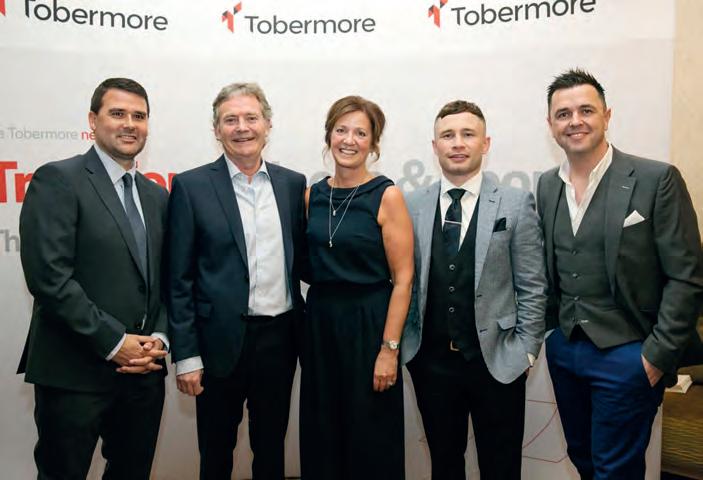
18 minute read
Tobermore opens new factory to expand production
TOBERMORE OPENS NEW £8.6 MILLION FACTORY TO EXPAND PRODUCTION
World-class paving and walling manufacturer, Tobermore has officially opened its new £8.6 million production facility which will enable it to further scale up production to meet the demand for its products.
This latest factory brings the total number of production facilities at the manufacturing headquarters in Tobermore to 10. With the capacity to produce an additional 3 million paving flags per annum, it will see flag production increase by a staggering 33% each year. Comments David Henderson, Managing Director of Tobermore: “We are delighted our latest production facility will generate additional job opportunities in our local area, as well as enable us to meet the growing demand for our paving flags. Boasting world-class machinery installed and tested by a team of expert engineers, we are passionate about producing outstanding products without the lead times.” The facility, which officially opened in June, boasts an industry-renowned SR Schindler Press, Shotblaster, and state-ofart packaging line. This press is only the second of its kind to be operational globally. It will facilitate the increased production of high-demand products including Braemar, Mayfair, Beaufort, Textured, Riven, and Classica Flags. This will ensure Tobermore can continue to proudly meet the growing demand for its products ensuring all its paving flags are in stock with zero lead times. Rigorous pre-launch machine testing was carried out by engineers from across the globe including from Germany, Slovakia, and Poland who were also involved in the machinery setup. Involvement from Northern Ireland companies, including Rapid and PIL, was also imperative to achieving the highest standard of operations. Tobermore has grown significantly over the past number of years increasing its workforce by a staggering 54.3% in the last two years, from 302 employees in May 2020 to currently employing over 460 staff across the UK and Ireland.
David Henderson & his wife Karen Henderson, David Healy, Carl Frampton and Pete Snodden.
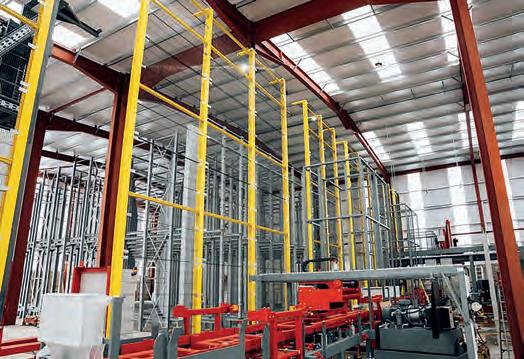
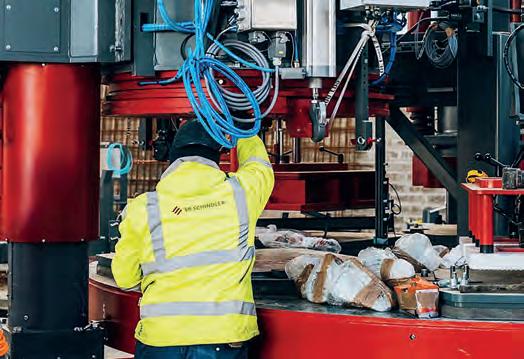
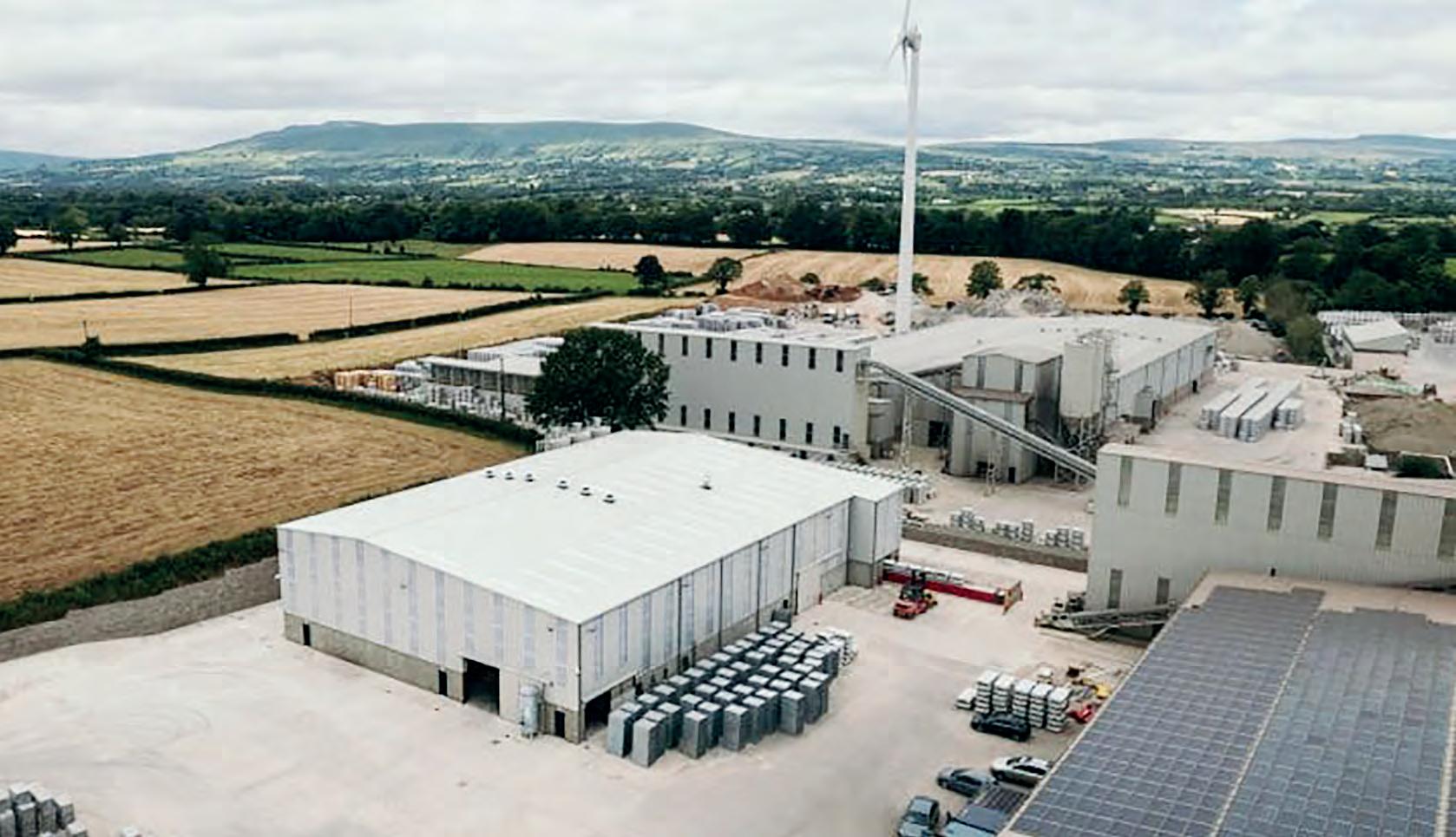
Moreover, the company’s turnover has increased steadily from £67m in 2020/21 to £85m in the year 2021/22. The Company was recently recognised in the Belfast Telegraph Top 100 Companies 2022, ranking at no 24. In December 2020, Tobermore celebrated the opening of its impressive 4416m² HESS facility which enabled the rapidly expanding company to ramp up production by an additional 30% and generated 95 new jobs locally. 80TH ANNIVERSARY
The company recently celebrated its 80th anniversary and the launch of the new company vision. The red carpet was rolled and champagne was popped as staff enjoyed an evening of fine dining and entertainment at the stunning Galgorm resort, Ballymena. Celebrities David Healy MBE & Carl Frampton MBE attended the event and took part in a question-and-answer session answering questions from Tobermore staff whilst Cool FM’s Pete Snodden hosted the evening. MD David Henderson delivered a heartfelt speech noting how business began at Tobermore back in 1942 and how he envisions the future of the company. He gave thanks to his sisters who were present on the evening for their support throughout the years and commended staff for their continued hard work and dedication to the company. Charitable giving is a core value at Tobermore and this didn’t go a miss at the company event. A charity collection was held to raise essential funds for the DEC Ukraine Humanitarian Appeal with a grand total of £2871.07 in donations which David Henderson kindly matched bringing the amount to an incredible £5277.14. “Celebrating 80 years in business was the perfect opportunity to bring together our staff from across the UK and Ireland, allowing us to show appreciation of their hard work and dedication to our company. People are at the heart of everything we do in Tobermore,” said David.
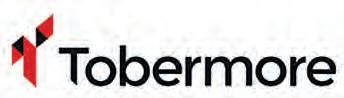
www.tobermore.co.uk
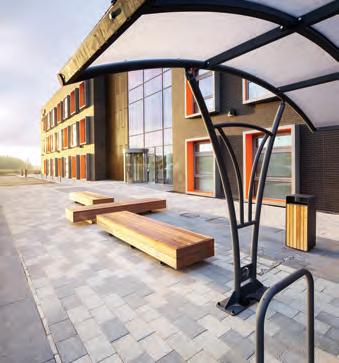
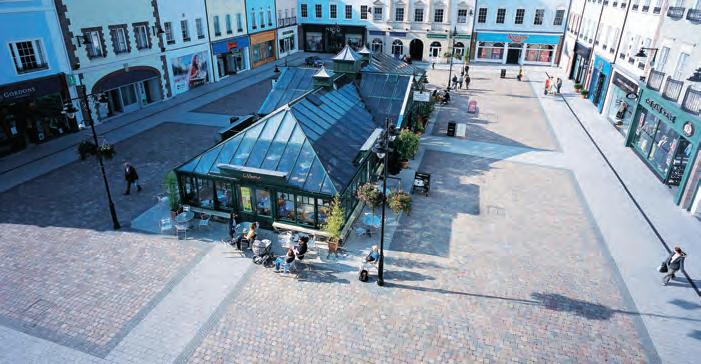
news Hill Engineering make the ultimate Connection
A revolutionary new coupler that can connect any hydraulic work tool safely and automatically from the operator’s seat has been launched by attachment technology specialists Hill Engineering.
Combining the versatility and functionality of the Tefra pin grabber coupler, and manufactured in high strength SSAB Strenx steel, the next-generation Tefra Connect sets new standards in on-site efficiency. Sites such as demolition projects, where hydraulic excavators are used with dedicated hydraulic tools, often also need an excavator to dig trenches or load out loose materials, using a pinned, non-hydraulic tool. With a Tefra Connect-equipped excavator, operators can maximise machine use and reduce or eliminate the need for other machines on-site, reducing machine costs, fuel consumption and transport movements - particularly beneficial on inner city or congested sites. The secret to the Tefra Connect is that it uses a patented “power coupling plate” bolted to the hydraulic tool which enables a rapid, leak-free and safe connection between the coupler and hydraulic tool. While similar systems for automatic hydraulic oil connections are already available, Tefra Connect has added an innovative twist - when the hydraulic powered tool is finished with, it can be released and placed to one side, revealing a regular variable pin centre Tefra coupler which can be used to pick up other pinned attachments in the usual way. So, unlike with other systems, operators will not need to invest in additional expensive adaptor plates for standard pinned attachments. Uniquely, Tefra Connect locks onto the attachment before engaging hose coupling plates, ensuring alignment and avoiding damage to hose couplings, and remains connected until the hose coupling plates have disengaged. In addition, the Tefra Connect requires no manual intervention at any stage, keeping operatives safe during connection and disconnection of high-pressure hydraulic lines, while the high-pressure oil lines remain sealed, staying free from contamination while helping site operators meet environmental obligations. Tefra Connect was originally planned for launch at Hillhead 2020 so the cancellation of that show enabled Hill Engineering to extend its field testing even further. The company selected several contractors who work primarily in Ireland, specifically so it could carry out regular product and performance reviews, on site and directly with the customers. Hill Engineering’s engineering manager Neal Loughran said: “Their feedback has been invaluable. These partners have been using the product every day, in their real work activities, and their suggestions have been incorporated into the final product. We believe Tefra Connect will become the new industry standard in attachment technology for specialist applications.” Suitable for use with all types of hydraulic work tools, such as hammers, grabs and munchers, Tefra Connect uses the same machine mounting and attachment versatility as a standard Tefra coupler and can pick up almost any type of pinned attachment. Special adaptor plates are only needed for hydraulic work tools, reducing the total cost of ownership, and since Tefra Connect is used in the same way as a standard Tefra coupler, no significant new operator training is needed.
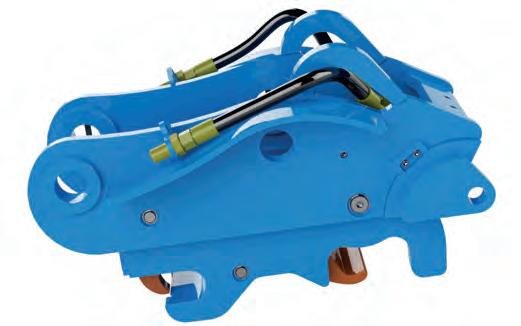

Merlo Validates ‘Better Mousetrap’ Theory Within Construction Sector Sales
The belief that if one ‘builds a better mousetrap, the world will beat a path to your door’ is playing itself out in the construction sector where Italian manufacturer Merlo has been quietly gaining an increasing share of telehandler sales.
Distributed here by McHale Plant Sales, recent deliveries have seen a number of machines go into service at the rapidly expanding Sligo-based plant hire firm Comet Contracts Limited. Headquartered in Ballinfull, the majority of Comet’s contracts are based in the greater Dublin and Leinster area. Specialising mainly in the data centre and pharmaceutical build sector, the firm provides plant hire solutions, logistics management and driver/operators. Recently Comet has taken delivery of two new high-spec
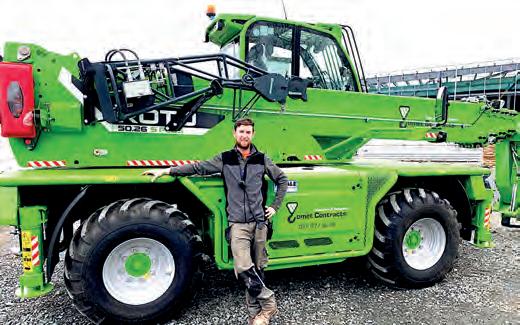
Comet Contracts managing director Eoin O’Boyle, pictured with his new Merlo Roto 50.26
Merlo Roto 50.26 S Plus rotating telescopic handlers, complete with 360° rotating turret, 5 tonnes lift capacity up to a height of 25.9 meters, hydrostatic transmission and intelligent hydropneumatic suspensions on axles as standard. The new Roto units bring to five the number of Merlo telescopic handlers now on Comet’s fleet – joining a P40.17 Plus, P40.13 and a TF50.8-170 Turbofarmer model, which, coupled with its lift capacity, is fitted out to tow a water suppression tanker. Impressed with his Merlo acquisitions to date, Comet Contracts managing director Eoin O’Boyle notes: “In the line of work we do, new, clean machines are a must. “What I’ve found with the Merlo units is that they are a wellbalanced machine and boast a high-spec across the board, from the hydraulics to the boom side shift. Nothing else is as precise, in our experience”. Equally praiseworthy of the aftersales service received from the distributor, O’Boyle adds “The team at McHale Plant sales are second to none. They go the extra mile for us every time”. Looking ahead, O’Boyle says plans are afoot to make further additions to the Company’s fleet of Merlo telescopic handlers over the next year or so.
Irish Experts Set To Make Waves Japanese Offshore Wind Market
Leading Irish Engineering and Geotechnical experts Gavin & Doherty Geosolutions (GDG), founded in Dublin in 2011, is furthering their global expansion with a new venture into the Japanese market to support them in achieving the ambitious offshore wind targets set out by the Japanese Government in the Basic Energy Plan.
The development of offshore wind farms in Japan brings some unique challenges, such as earthquakes, typhoons and unusual geological formation. In this new collaboration, GDG will combine their unique expertise in offshore engineering and geoscience with the local Japanese knowledge of Geo Marine Service Co., Ltd and Nikken Sekkei Ltd, to offer unparalleled survey specification, wind turbine foundation design and certification process support to the Japanese market.

GDG Founder and Executive Vice President of Engineering at Venterra Group, Paul Doherty PhD, with Executive members of Wakachiku, CSSE, Tokodenko and Nippon Geotechnology, at the signing of an MOU to combine GDG’s unique expertise in offshore engineering and geoscience with the local knowledge of the Japanese partners.
Speaking at the recent signing of a Memorandums Of Understanding (MOU) between the partners, Paul Doherty, Founder of GDG and Executive Vice President of Engineering at Venterra Group, said: “The GDG team are experts at finding innovative engineering solutions to support some of the most challenging offshore wind projects around the world and we look forward to building on our current base of foundation design projects in Japan. We’re delighted to partner with Japanese organisations who hold invaluable local knowledge of the marine regulatory regime, grid and development procedures. Together, we are committed to supporting projects that contribute to the global sustainability agenda.” To date, GDG has supported 35,000MW of offshore wind globally, that’s enough energy to power approximately 25 million homes. They are leaders in geotechnical engineering design and have already expanded to the UK, EU and the US. They will bring their unique capabilities to their latest target, Japan. The Basic Energy Plan, issued by the Japanese Government, has set a target of 45,000MW of offshore wind by 2040 and will go some way to helping Japan achieve its decarbonisation targets, as well as the growing need to reduce energy costs for consumers. However, the Japanese service supply chain required to make this happen has not been sufficiently established.
Ireland’s leading workshop specialist for haulage, transport, plant and fleet
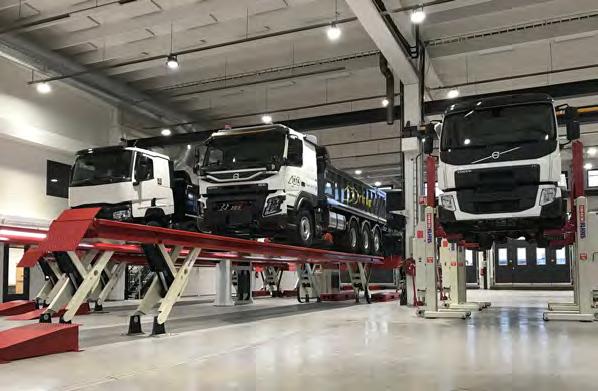
SWS is Ireland’s leading garage fit-out and workshop equipment specialist. With over 40 years’ experience and access to the world’s leading brands, we are trusted by operators who value our expertise, reliability and exceptional value.
TRUSTED FOR THE JOURNEY

•STERTIL KONI VL TEST SYSTEMS SAMOA MAJORLIFT• • •STERTIL KONI VL TEST SYSTEMS SAMOA MAJORLIFT• •
SALES TEAM (028) 7131 2225 • WWW.SWSNI.COM SALES TEAM • (028) 7131 2225 01 506 0572 sales@swsni.com www.swsni.com •
news
Topcon launches new GNSS network for Ireland
A new positioning network covering the island of Ireland has launched from Topcon Positioning Group, offering improved support and accessibility for construction businesses looking to accelerate productivity and advance accuracy.
The new network, which is part of the business’ plans to expand Topcon’s GNSS networks globally, offers users two additional satellite constellations to current available networks. The Topcon network will use Beidou and Galileo systems as well as the standard GLONASS and GPS systems, meaning access is easier and more reliable, and the accuracy it can deliver will be vastly improved. There is a dense network of stations already in place, with more planned in the coming weeks to achieve full coverage of the island with one subscription – something not currently available with other network providers. The network goals from Topcon are that businesses will experience no downtime, better accuracy, faster connections, and accessibility even in the most challenging environments that Ireland has to offer. The new network will also be maintained and supported by Topcon’s global professional services team around the clock, ensuring businesses have on-hand tech support for troubleshooting and better backup capabilities. Mark Fagan, Business Director for Ireland and Northern Ireland, said: “We’re pleased to be able to launch this new network and help businesses across the island of Ireland. All the benefits that the new network will bring will help industries take a big step forward in digital adoption; something that’s needed now more than ever as we continue to see the impact of the coronavirus pandemic. “This is an exciting development for Ireland as a whole. We’re delighted to be able to offer this to support businesses in digitalising their workflows to see productivity and efficiency boosts across the board.” The business is also offering a more flexible system for subscribers, with hourly packages available to be allocated as businesses see fit to their machines and projects across Ireland and beyond. Ian Stilgoe, Vice President of Emerging Business at Topcon Positioning Group, said: “At Topcon, we’re passionate about tackling the challenges of tomorrow, today. We’re proud to be a technology partner that enables businesses to work their own way more productively, and offering flexibility is paramount to that. “Our rapid expansion of Topnet Live correction services is helping businesses be mobile and reactive to their business needs without the frustrations of multiple subscriptions. Our services are also meeting the needs of the new mobility autonomous markets as the demand for precise positioning increases. This new network for Ireland is just another way we’re helping businesses to stay one step ahead.” Subscriptions will run through Topcon’s recently launched Topnet Live, a real-time GNSS correction service. Thanks to the new network, Ireland will become part of the European and global Topnet Live network, offering European roaming to users. Within Topnet Live subscriptions, users can access Starpoint, a service with provides a Precise Point Positioning (PPP) service anywhere on the planet, independent of local networks, and Skybridge, which provides and maintains position accuracy in case Real Time Kinematic (RTK) services are interrupted. Access to the new Irish network via Topnet Live is available at https://www. topconpositioning.com/ie/office-software-andservices/gnss-correction-services/topnet-live
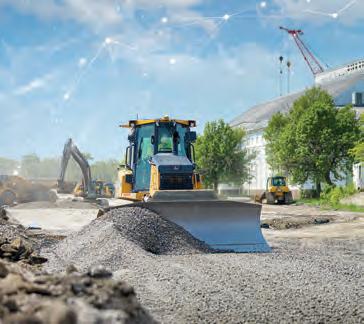
Nine out of 10 construction companies say they are unwilling to take on fixed price contracts given the ongoing exceptional increases in raw material costs. That’s according to a new Construction Outlook Survey from the Construction Industry Federation.
The survey also found that 91% of construction companies believe the economic sanctions arising from the conflict in Ukraine will lead to a further rise in construction costs over the next 3 months, while 85% expect the price of construction projects to increase during that period. As a response to these issues nine out of ten (89%) construction companies want to see the Government introduce an effective and fair price variation clause into public sector contracts, which would apply retrospectively. More than four out of five construction companies (82%) also note that the Ukraine conflict has led to the disruption of supply chains in the construction sector. Additionally, 98% of construction companies reported an increase in the cost of raw materials over the last 3 months. Other points of interest from the survey include almost four out of ten construction companies (38%) saying their turnover increased in the last three months with a similar number (39%) expecting a further increase over the next three months. While one in three construction companies (32%) also expect to grow their levels of employment over the next three months. Three out of four construction companies (75%) also believe the sector would benefit from attracting more women to work in the industry. The key challenges identified by the sector are the increased cost of raw materials (88%), access to skilled labour (72%) and fuel (68%). Speaking in reaction to the survey, Tom Parlon, Director General of the CIF said, “Over the last few months we have been highlighting the issues of hyperinflation in the industry and how that is going to impact on the pipeline of construction activity, particularly when it comes to public tendering. Well, here is the detailed figures which illustrate the extent of these problems. “Nine out of ten construction companies, which represents the vast majority of the industry, will not tender for fixed price contracts while these increases continue. No one could be expected to commit to a definite price for projects which could take years, when costs are rising on a daily basis. It is practically impossible to estimate where costs are going to go based on the levels of inflation we have seen in the industry over the last 18 months and especially since the turn of the year. “This also underlines the urgent need for the Government to reform the public works tendering process. There is a clear view in the industry that this needs to happen. Until that is tackled, issues around public tendering will continue, which is likely to have a knock on impact on the advancement of the Government’s various construction programmes,” he concluded. The Construction Outlook Survey was carried out by Accuracy Market Research, with 342 CIF member companies participating.
news Groundforce Training Services signs up to the Armed Forces Covenant
Specialist construction training provider, Groundforce Training Services, has formalised its long-standing support for the Armed Forces.
A proud employer of ex-service personnel, the company has officially signed the Armed Forces Covenant which commits them to support the Armed Forces community and to recognise the value that serving personnel (both regular and reservists), veterans and military families contribute to the business and the country. Groundforce Training Services, based in Worksop, already excels in this area, with a massive 86% of its instructors being ex-military, as well as 50% of its total workforce, which demonstrates their true commitment to the cause. The Armed Forces Covenant was signed by Neil Stothard, chief executive of parent group Vp plc, making Groundforce Training Services eligible for a Defence Employer Recognition Scheme (ERS) award. The covenant helps Groundforce Training Services to promote to its staff, customers, suppliers, contractors and the wider public that it is an Armed Forces-friendly organisation that actively seeks to support the employment of veterans through working with the Career Transition Partnership (CTP). It pledges to offer guaranteed interviews to veterans, young and old, if they meet the selection criteria in the job advert and to recognise military skills and qualifications when interviewing for these positions. It also pledges to supporting employees who are members of the Reserve Forces by offering five days’ paid leave for annual Reserve Forces training. Groundforce Training Services’ general manager Chris Gearren
said: “The covenant sets out the relationship between the nation, the Government and our Armed Forces. It recognises that the whole nation has a moral obligation to members of the Armed Forces and their families, and it establishes how they should expect to be treated. This is something we at Groundforce Training believe in passionately and it’s great to continue to build our reputation as a Forces-friendly business.” Groundforce Training Services offer a wide range of courses primarily for those working in utilities, construction and civil engineering, from short-duration Health and Safety awareness to more complex or specialist safety consultancy solutions. Industry-leading accredited excavation safety training is delivered both on-site and through a nationwide network of training centres, with full flexibility for customers who need to place small numbers onto an open course schedule 45493 GF Ireland P&CE Ad 180x131mm V2.qxp_Layout 1 29/04/2021 10:39 Page 1 or dedicated courses.

THEN...
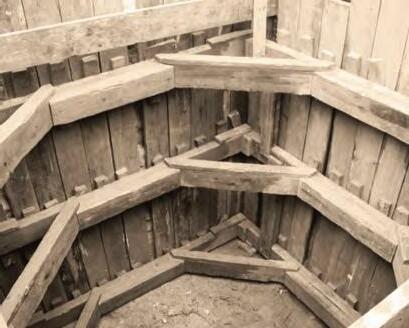
...NOW
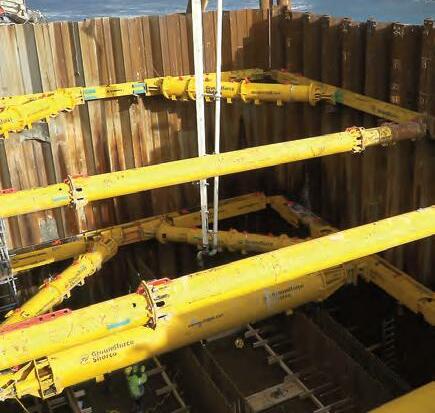
MountmellickHireDesk 1800 883 364 Lisburn Hire Desk 0800 783 2055 www.vpgroundforce.ie
DECADES OF EXCAVATION SUPPORT
Groundforce has continued to innovate excavation support systems for many years. Our team of experts are
committed to project success through continuous product development combined with the latest technical design and engineering processes.