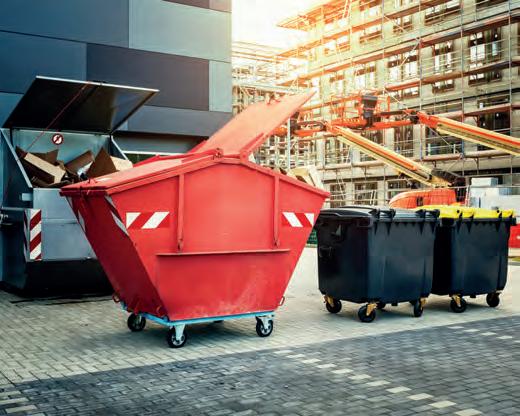
12 minute read
Recycling & Waste
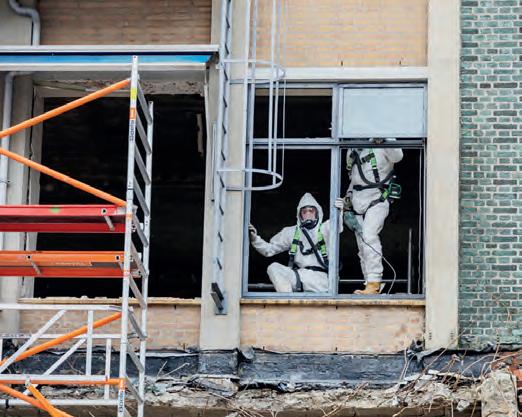
The construction industry produces a substantial amount of waste every year. In fact, according to a study by the Department for Environment, Food and Rural Affairs in 2018, this amounted to 62 per cent of all waste in the UK. And the Environmental Agency believes that the quantity of waste has increased in recent years due to the encouragement of brownfield remediation across the nation. So how do we tackle this?
The nation is tackling this issue with environmental legislation. In 2021, the Environmental Act introduced targets to improve waste reduction, including discouraging avoidable waste by 2050. To accomplish this, the shipment of hazardous waste will be regulated and a restriction will be placed on the export of these substances to countries that aren’t in the organisation for the economic cooperation and development (OECD). This will encourage the nation to create innovative ways to dispose of hazardous waste correctly and sustainably. Here, we will explore how the construction industry currently tackles hazardous waste and consider whether a circular approach is the solution for a sustainable future within the UK.
What is hazardous waste?
Hazardous waste represents any unrecyclable materials produced on a construction site. These materials contain substances that can harm the local ecosystem, wildlife, and human beings. Asbestos, microscopic fibres which are often found in materials from homes built before 2000, are among some of the most hazardous materials found on construction sites. Professionals in the sustainable waste management industry are trained to perform asbestos removal services correctly. It is imperative for professionals to dispose of asbestos correctly. Incineration, for example, is unsafe as the hazardous material contaminates the air and can cause harm to those who breathe in the fumes. Instead, these materials are sent to specialist landfills, so that they cannot contaminate the local ecosystem. This is problematic, however, due to the fact that asbestos cannot decompose naturally.
Polychlorinated biphenyls (PCB)
Polychlorinated biphenyls (PCB) are manmade toxic substances, varying from liquids to solids and black to yellow. Though they were previously used within electrical equipment, these hazardous materials are now banned within the UK. There are only a few exceptions to this, including research purposes and, until 2025, transformers that contain less than 0.005% of toxic fluids. PCBs can cause cancer in animals and disrupt the food chain within the sea. Therefore, it is important for professionals to correctly dispose of this chemical, trusting certified EPA disposal facilities. The general public is also advised against using appliances (such as fluorescent lighting to televisions) that were made before the 1980s.
Solvents (VOCs)
Solvents, otherwise known as volatile organic compounds (VOCs), are often used in the construction industry to dissolve or dilute substances, such as paints or glues. If solvents contain dichloromethane (DCM), they can cause harm to humans, animals, and wildlife. Solvent paints, for example, are considered a hazardous substance. Therefore, in order to dispose of this waste, it is important for professionals to follow the Hazardous Waste Regulation (2005). This involves classifying and properly disposing of hazardous solvent waste at a specialised facility. How does the construction industry recycle hazardous waste? One of the most environmentally considerate ways of discarding hazardous waste is through recycling. This encourages companies to adopt a circular process to waste management, an approach that minimises unnecessary waste throughout the design, production, and disposal processes.A circular economy is also beneficial for businesses, from lowering costs for the purchaseof new materials to a reduction in any carbon footprint associated with the corporation.
Solvent distillation
Solvents (VOCs) are commonly used substances. The construction industry can choose to recycle this type of hazardous waste through a process named solvent distillation. This filters hazardous solvents, distilling volatile vapours and preserving pure vapours. These can then be redistributed into the industry.
Water treatment
Liquid-based hazardous waste, from acids to oily water and latex paint, can also be recycled. Water treatment allows professionals to extract water from these substances. This water is then reused on industrial sites.
To summarise
Sustainability remains at the forefront of public concerns and discussions. The construction industry continues to generate a huge amount of waste, but adopting circular practices can help regenerate these materials. So, moving forward, the nation must continue to strive to attain reusability in construction materials beyond everyday solvents and polychlorinated biphenyls.
SKIPWAY INVEST IN NEW TROMMEL FINES
Skipway Waste Management in Lisburn has commissioned the first trommel fines plant in Northern Ireland in a bid to push the boundaries in sustainable innovation.
Designed and engineered by industry experts CDE, the new 50tph plant will significantly enhance the company’s current operations and contribute to a major improvement to the sustainability of the business. Skipway was acquired by the R. Heatrick Group in 2012. The company had many years of experience in the recycling of demolition wastes and acquired Skipway to further diversify into the recycling industry by providing skip hire and investing in the materials recovery facility. Following this acquisition R. Heatrick Ltd continued to grow under the Skipway trading name and became a major force in the recycling industry through investment, innovation and providing a fast and reliable service that’s unparalleled to their competitors. R. Heatrick Ltd is a family run business established in 1969 with hard work and dedication to quality at its core. Over the 53 years in business R. Heatrick Ltd has been able to diversify and establish itself in demolition, haulage, quarrying and the recycling industries to meet the demands of their client, helping to create an internal circular economy and reducing the amount of waste going to landfill helping to develop a more sustainable Northern Ireland. WASTE INTO RESOURCES
Skipway’s primary aim was to divert trommel fines from landfill and convert the material into a resource by producing recycled product with the same specification and quality as quarry grade sand, therefore making it suitable for concrete and building products while also improving the quality of other recycled aggregates such as pipe bedding and recycled hardcore. The company processes construction, demolition and commercial wastes through a dry waste processing plant and picking station to recover materials and divert them from landfill. Trommel fines are a by-product generated during the recovery process. The fibrous nature of trommel fines makes them difficult to separate and recycle so they have traditionally been sent to landfill, rather than addressing the challenge of upcycling this material. As they are traditionally high in lightweight, organic content, trommel fines generally fail to meet the specified Loss on Ignition (LOI) threshold of 10%, therefore incurring the standard, and higher, landfill tax rate. When the landfill tax was introduced in October 1996, as a measure to encourage waste producers and the waste management industry to switch to more sustainable alternatives for disposing of material, the standard rate was just £7. In April 2022, the
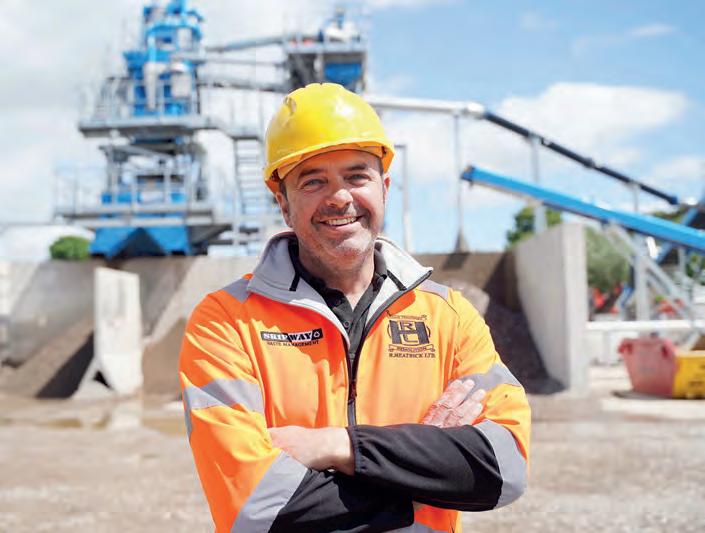
Trevor Heatrick, Director, Skipway.
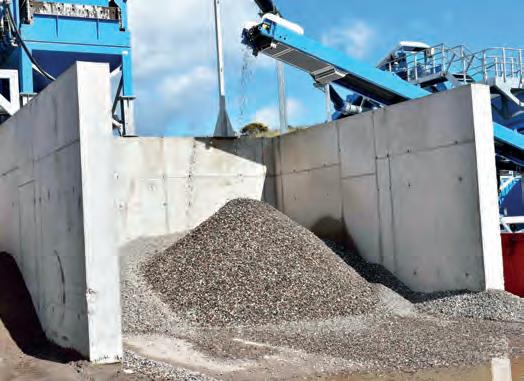
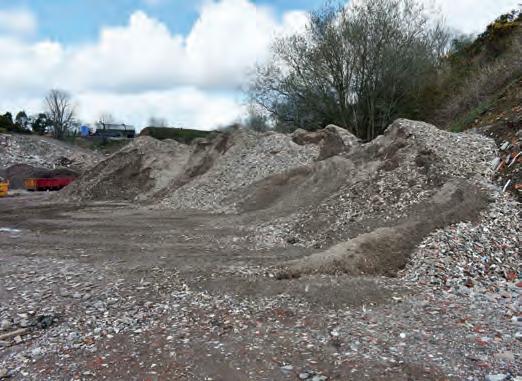
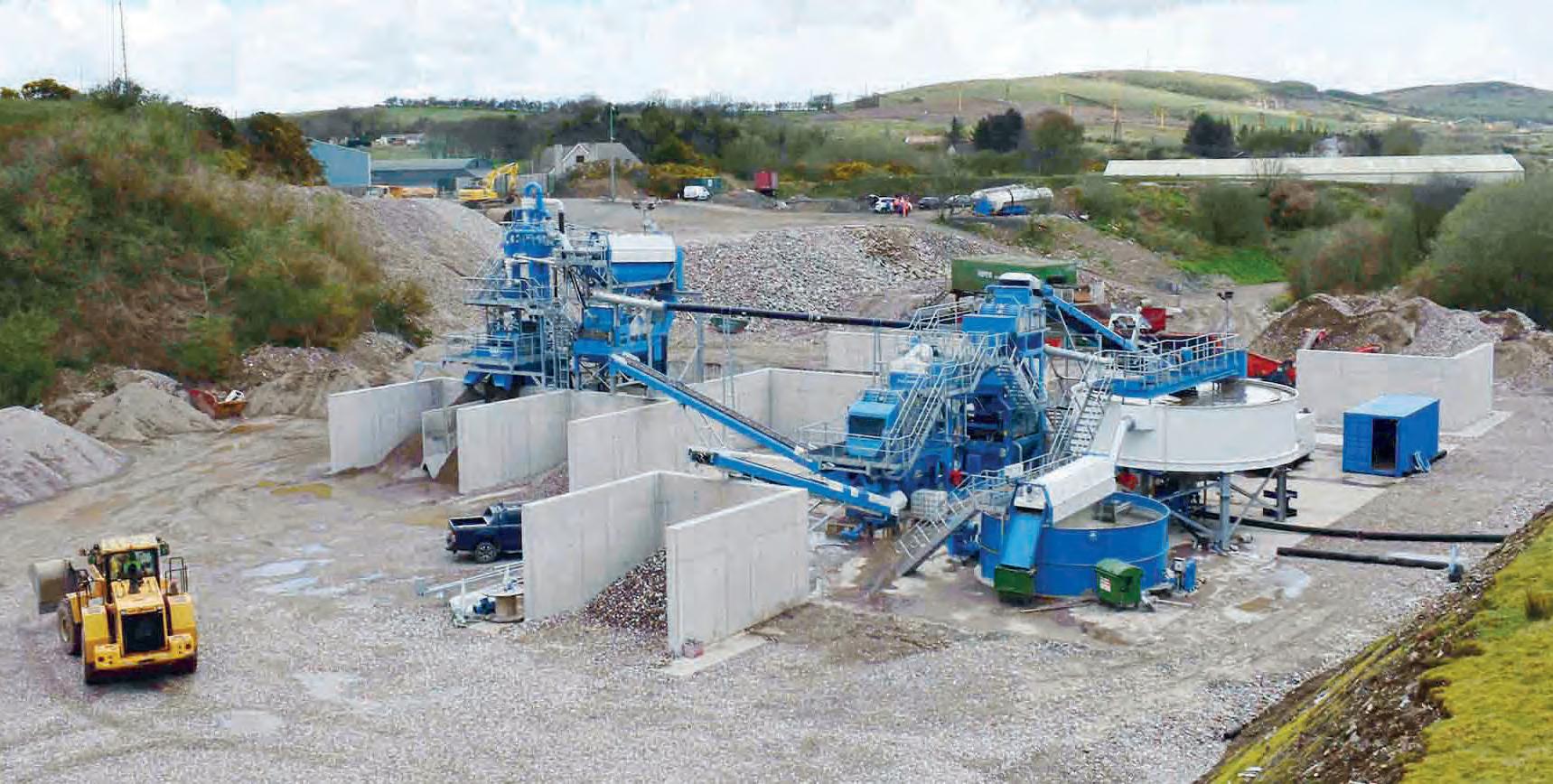
standard landfill tax rate which trommel fines incur was increased to £98.60 per tonne1. As a dual measure to reduce costs and decrease waste going to landfill, Skipway sought to find a solution to extract the potential value of trommel fines and so approached waste recycling experts CDE. Through their unique collaborative approach, CDE engaged with Skipway to fully understand their existing process and what they wished to achieve. Together they created a solution suited to Skipway’s stipulations to help them ultimately divert more waste from landfill which in turn contributes to their internal circular economy. THE SOLUTION
CDE proposed a trommel fines wet processing plant, the first of its kind in Northern Ireland, to equip Skipway with the means to wash & segregate material and recover materials from C&D waste. The plant, which incorporates AggMaxTM modular logwasher, EvoWashTM sand wash plant with Counter Flow Classification Unit (CFCUTM), AquaCycleTM thickener and static screens, operates at a rate of 50tph. Through the washing process, the plant removes the lightweight and organic material directly linked to LOI and transform the largest proportion of the trommel fines waste stream into sellable products for the construction market. Its trommel fines solutions segregate and concentrate lightweight and organic materials into isolated fractions so they are easier and more cost effective to dispose of, whilst converting the heavy fractions into sellable sand and aggregate products. Skipway’s CDE plant includes a CFCUTM which uses density separation to remove the fibrous, organic, and polystyrene materials which contribute to the high LOI content of trommel fines. Once these materials are removed a high-quality finished sand product remains, creating a fresh revenue stream while saving on landfill costs. Further sustainability contributions will be made through CDE’s EvoWashTM, which provides unrivalled dewatering performance, with InfinityTM dewatering screen technology to result in an increased power to weight ratio for lower running costs through reduced power consumption.

INCREASED VALUE
Following the commissioning and installation of this plant, Skipway are now producing coarse aggregates, coarse and fine sands for use in in concrete production, drainage, and construction bedding. By washing the inert materials to remove contamination, clean sand and aggregates extracted from the trommel fines waste can be resold and reused in the secondary aggregates market to close the loop on waste, contributing to a circular economy and opening new revenue streams for the company to ensure swift return on investment. Fergal Campbell, Business Development Manager for CDE, is delighted to see Northern Ireland showcasing the latest technology in trommel fines recycling. “At CDE we’re passionate about contributing to a circular economy and enabling our customers with our innovative technologies so they can play their part. Skipway’s local landfill is reaching capacity so it’s encouraging to see them so passionate about landfill diversion and extracting the value that we can get from waste streams like trommel fines and reusing outputs, such as sand for concrete. “Plants like this are the future of the industry in their ability to minimise waste and maximise value. It’s been a pleasure to work with Skipway and we really look forward to seeing how this partnership can contribute to Northern Ireland’s circular economy.” Trevor Heatrick, Director at Skipway, added: “It was an easy choice for us when we decided to invest in the new plant. Compared to other manufacturers, CDE has the edge. We had numerous other options in front of us, however CDE displayed their knowledge and expertise from the sales stage through to the delivery of the project. Every aspect of the material processing that they highlighted as being required, we can see the benefit of now. “One of our biggest issues was that our material contains a lot of polystyrene which can be hard to remove, and we found that CDE had the best and most robust solution in ensuring that this material could be removed “CDE were able to create a product tailored to us which is helping us achieve the goals that we presented them with. Close collaboration meant that we were able to have input on the design of the plant so that it addressed our needs and did the job we wanted it to do. Working with CDE was an easy process and we’re delighted to be able to push the boundaries in sustainable innovation.”
recycling & waste management
Ulster Shredders continue to develop marketing leading products, launching the T-50 Tetra 4-Shaft Shredder at the world’s leading IFAT 2022 Trade Fair Messe München.
Designed for maximum performance and high productivity, the T-50 has been efficiently designed as machine operator friendly and engineered to shred in different formats delivering an economical solution to customers. Consistent with the wellestablished low speed high torque design on their twin shaft machines, the T- 50 delivers a low noise and dust pollution shredder, with their welldeveloped direct drive system powered by two electric motors directly driving the four shafts through a series of reduction gears. The new T-50 combines the Ulster Shredders twin shaft shredders’ reliability and uses a sizing screen for particle size control. The upper two sets of knives clean the primary shafts with all knives on the four shafts sweeping the sizing screen to produce a desired particle size.
Sales and Service Director
Paul Atkinson explains “The T-50 4 Shaft Shredder is an excellent addition to our product range complementing our existing shredder range. We have creatively designed and engineered a robust solution for operators. We are excited at the opportunities that this addition to our range will generate”. Engineering Manager Damian O’Hagan discusses the design of the machine, “During the scoping of the design work we engaged with our customers to understand what their needs were to ensure that our final product is capable of delivering a solution to their shredding requirements. We developed a modular design allowing this to be tailored to the customers’ individual requirements. Our T-50 has been designed to allow versatile feeding from all sides via conveyor belt, forklift, lifting and tipping devices or by hand with a pusher available as an optional extra. Our robust design can fit easily into our customers’ production line as an upstream or downstream shredding solution allowing for flexible material discharge options” . Ulster Shredders T-50 is suitable for a wide range of challenging materials including, mixed material streams, plastics, piping, & wood focusing on delivering a high throughput to a regulated particle size.
T-50 Tetra 4-Shaft Shredder.
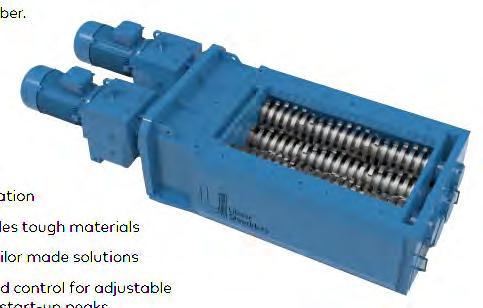
Ulster Shredders Expansion
Ulster Shredders has recently completed a 10,000 sq. feet expansion at its Headquarters Cogry Works in Castledawson.
The new workspace is a dedicated machine shop housing its state-of-theart machining centre where the in-house production team produce all machine components for its product range. Ulster Shredders Managing Director Enda Cushnahan said: “The new expansion is an example of Ulster Shredder’s proactive strategy to meet the growing demand for innovative shredding solutions as required by customers in markets at home and abroad. “Building on our rich heritage of over 50 years of engineering excellence this expansion houses world class machinery, for the tailor-made production of precision machined components used in the manufacture of the company’s product range.” Ulster Shredders Production Manager, John Currie added: “This expansion is testament to Ulster Shredder’s commitment to producing leading shredding solutions in the industry. The new facility at Cogry Works has allowed us to enhance the efficiency of our processes and remain competitive, assisting us in delivering quality products to customers with minimum lead time.” And Ulster Shredders Sales & Service Director Paul Atkinson said: “I am delighted with this expansion to our operational capabilities and this will further enhance our ability to meet the growing requirements of our customers.”
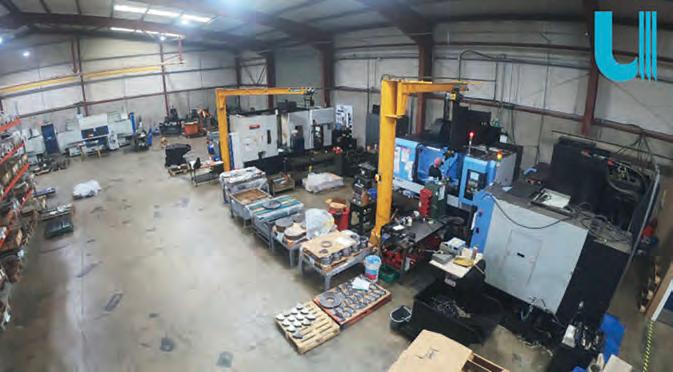
PLANT & CIVIL
CONSTRUCTION, QUARRY & RECYCLING MAGAZINE AWARDS2022 SAVE THE DATE THURSDAY 24th NOVEMBER 2022
