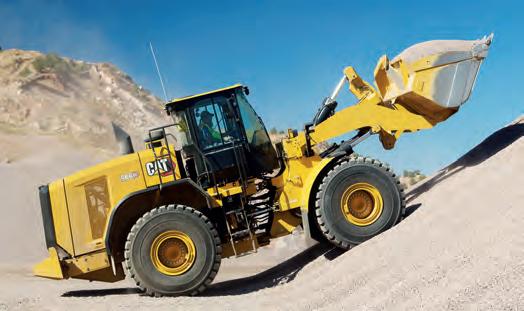
13 minute read
Cat Wheel Loader delivers

NEW CAT WHEEL LOADER DELIVERS HIGH PERFORMANCE & EASY OPERATION
Cat’s new 966 GC Wheel Loader is designed for reliable, performing and efficient operation, with features to keep fuel consumption and operating costs low, making it a versatile machine that also fits the needs of the rental and municipal markets.
The Cat C9.3B engine meets U.S. EPA Tier 4 Final, EU Stage V, Korea Tier 4 Final, China Nonroad Stage IV and Japan 2014 emission standards with a gross power rating of 239 kW (321 hp). The engine’s automatic Cat Clean Emissions Module including SCR catalyst and diesel particulate filter (DPF) works in the background without impacting the production schedule. The Cat Engine Idle Management System, Auto Engine Idle Shutdown , variable speed fan and load sensing hydraulics help result in low fuel consumption and reduced sound levels on this machine. An optional automatic reversing fan assists in cleaning cooling cores to improve performance in high-debris environments. The new loader features a 4-speed forward/reverse electronically controlled, automatic planetary powershift transmission with shift protection and single clutch gear shifting for efficiency, durability and smooth gear changes. Ensuring excellent material retention and increasing efficiency, the loader’s optional ride control improves operating smoothness over rough terrain. Optional limited slip differential axle configurations increase traction in poor underfoot conditions. FRONT LINKAGE
Field-proven, Caterpillar’s Z-bar loader linkage with cast crossmember and tiltlever provides both strong digging capabilities and high breakout forces when the new loader is equipped with Cat Performance Series buckets. The load-sensing implement hydraulic system continuously controls flow and pressure to precisely match requirements of the operating situation, reducing both the load on the pump and overall fuel burn. Using a system-based approach to balance bucket shape with the machine’s lift and tilt capacity, weight, and linkage, the Performance Series Buckets are available for a range of applications including general purpose, flat floor, heavy duty rock and light material. Design features enable operators of all experience levels to routinely attain 10% higher bucket-fill factors, compared with legacy designs, to improve production and reduce fuel consumption. The 966 GC can also be equipped with the Cat Fusion™ quick coupler and controls, and combined with optional thirdfunction auxiliary hydraulics, the coupler allows use of a wide selection of Cat work tools. An optional Cat Payload kit provides on-the-go weighing* for precise load targets with proven accuracy, flexible and simple installation, and easy calibration. Bringing payload weighing to the cab, Cat Payload weighs the material while moving to the truck and lifting, so there are no interruptions in the load cycle. It allows the operator to load to exact specification and load more trucks and move more material faster. OPERATOR ENVIRONMENT
The new 966 GC loader features a simple, intuitive and ergonomic control system with an operator interface display that includes six analog-like gauges, color indicator lights, and an LCD screen all within easy view, so operators can quickly monitor machine systems. Low-effort, pilot-operated implement controls feature a remote transmission kick down switch for operating comfort. Keeping safety in mind, inclined ladders and integrated handholds are located on both sides of the machine to provide access to the cab and to the engine air filter. A large roof-to-floor, distortion-free, flat glass front windshield; standard rearview camera; and exterior mirrors with integrated spot mirrors provide all-around visibility. The standard heating and air conditioning system with 10 louvered vents helps to keep the operator comfortable in all climates. Ground level access to service points reduces maintenance time and improves safety. Large gull-wing engine hood side panels and a tilt-up rear grill provide unrestricted access to daily service points, fuel and DEF fills, greasing points, filters, and fluid-sampling ports. Further reducing maintenance, an optional Cat Autolube greasing system is available. With Cat Product Link ready standard, 966 GC operating efficiency, preventative maintenance and servicing are enhanced. Deeply integrated into machine systems, Product Link captures critical operating data, remotely monitored via my.cat. com, the Cat app or VisionLink.
MECALAC’S CABBED DUMPER A FIRM FAVOURITE WITH HIRE CUSTOMERS
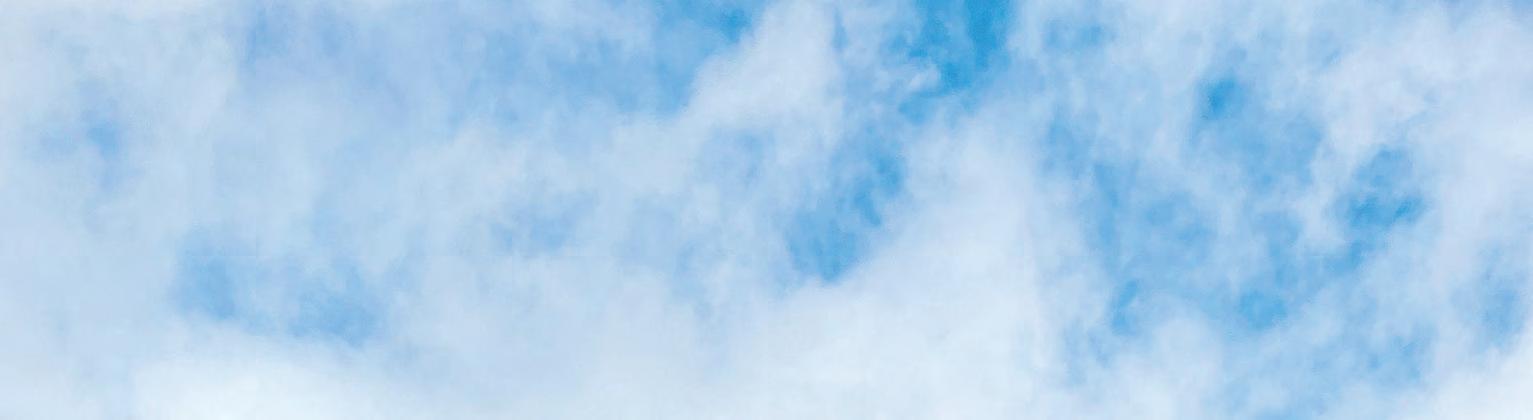
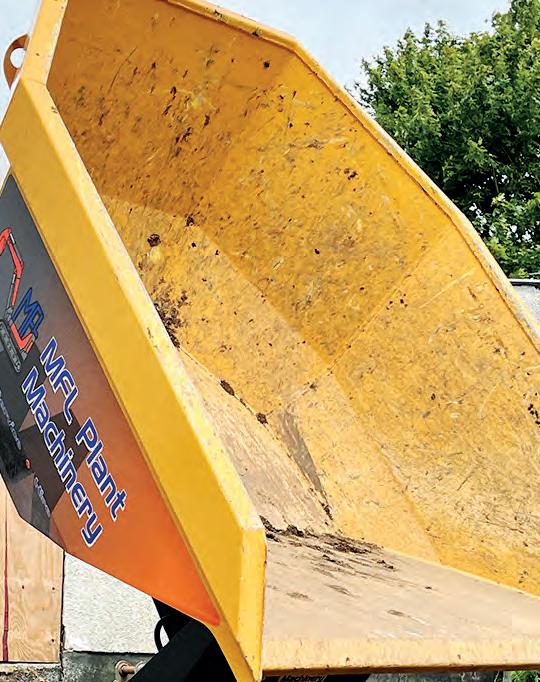
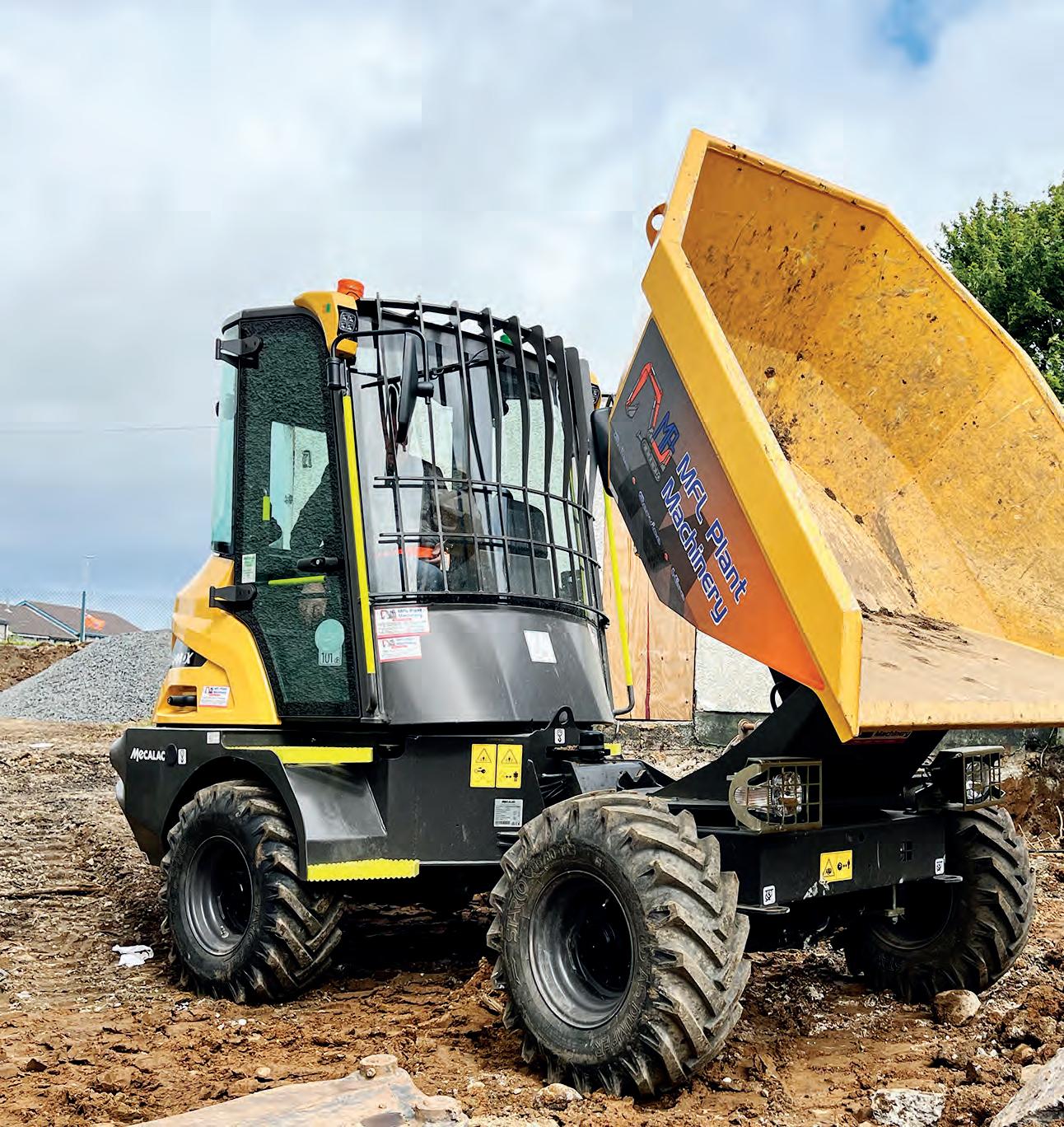
VIDEO STORY
MECALAC 3.5MDX CABBED DUMPER SCAN THE QR CODE TO WATCH THE VIDEO.

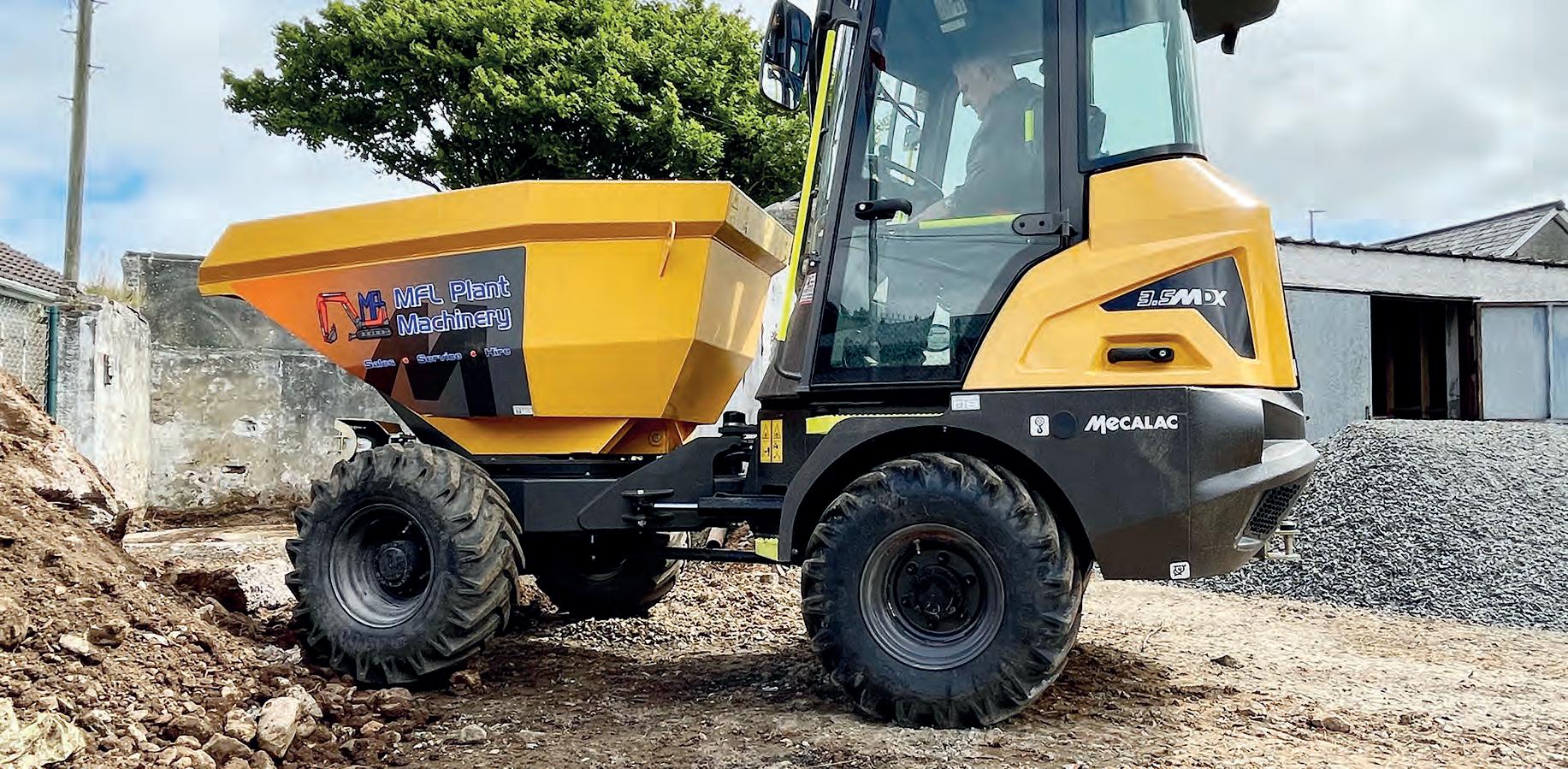
Cabbed dumpers from Mecalac have a bright future, according to Newtownabbey based dealers Sleator Plant, and John McGilligan, who heads up MFL Plant Machinery in Maghera, County Derry, totally agrees; he recently invested in a 3.5MDX model and is planning to add more to his growing hire fleet. Plant & Civil Engineer’s David Stokes has been finding out why.
John say the 3.5 tonne Mecalac cabbed dumper was initially acquired for a valued customer who needed it for a specific contract at the time, and it has since been out on hire with other operators, all of whom have given it glowing reports. MFL Plant Machinery was established nine years ago, a business that essentially grew out of a ‘hobby’ for John. “I was always buying and selling equipment and over the years have become a main dealer for C&F tracked mini dumpers and for Altrad Belle who manufacture a range of light equipment for the building and construction markets, but the bulk of my business is in the hire sector.” He currently has around 60 machines in his rental fleet, including diggers from one tonne up to eight tonne, mini tracked dumpers, one tonne up to nine tonne dumpers, telehandlers and access equipment, and while the Mecalac 3.5MDX dumper is his first, it won’t be the last. “My hire customers have nothing but good to say about the Mecalac,” says John. “I did look at other brands, but have no regrets opting for the Mecalac. Feedback has been extremely positive, so I guess we will need to get at least a couple more to meet demand, including a larger model. Since the 3.5MDX joined the fleet it has only been in the yard on two occasions – and that was for routine servicing. It is always out with customers for two or three weeks at a time.” He adds: “I did have some Terex dumpers before Mecalac acquired them five or six years ago, so I knew it would be a quality machine, and it hasn’t disappointed. I am convinced Mecalac cabbed dumpers have a big future in this part of the world, not least because of the weather and on site health & safety regulations, so I wanted to be among the first to add them to my hire fleet, and having enjoyed an excellent working relationship with the team at Sleator Plant I had no hesitation in doing so; they have always provided me with great service and support.” So, what does his customers like about the Mecalac? “Obviously the cab; it is very comfortable, comes with air conditioning, sensibly positioned, easy to use controls, a fully adjustable seat, great visibility, and lots of safety features, all of which make it ideal for the rental market,” says John. The machine is powered by a Stage V-compliant Kubota D1803 1.8L turbocharged 3-cylinder diesel engine, delivering 50hp (37kW) at 2700rpm and a peak torque of 150.5Nm at 1600rpm, and adds John: “It is easy on fuel. How do I know? Because my customers would be the first to tell me if they thought it wasn’t fuel efficient, and to date I have had no complaints, so that tells me all I need to know!” Taking a closer look at the Mecalac 3.5MDX; John opted for the swivel tip skip with its 180° rotation that enables precise lateral unloading without manoeuvres. A front tip skip version is also available.
Operators have torque on demand to effortlessly move loads in even the most challenging site conditions
The 3.5MDX uses high and low range gearing for both forward and reverse, as well as permanent hydrostatic four-wheel drive. This means that operators have torque on demand to effortlessly move loads in even the most challenging site conditions. This, combined with a maximum travel speed of 12.4mph (20kph) makes the unit quick and easy to move around site. An operating weight of 2990 kg, length of 3.8m, width of 1.9m and height of 2.8m
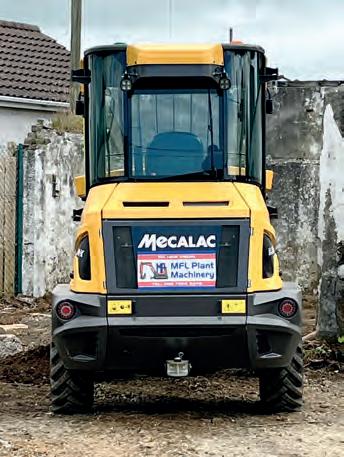
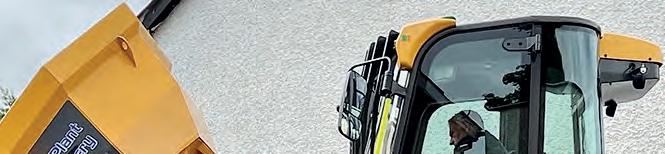

CONTINUED
make the 3.5MDX highly compact and manoeuvrable, providing an effective solution to carry high payloads in confined spaces and for a large variety of applications. The 3.5MDX prioritises the highest levels of operator comfort, as John noted, by adopting Mecalac’s proven MDX cab with air-conditioning to provide outstanding operator well-being in all weather conditions. Like all MDX models, the unique isolated cabin layout minimises vibration and noise, while ergonomic controls and an adjustable seat provide a relaxed environment when working for extended periods. Alongside featuring front and rear LED work lights as standard, the fully enclosed cab provides class-leading operator visibility thanks to large glazed areas and a curved windscreen, ensuring all-around natural visibility.
Easier and safer access to the machine thanks to high visibility and easy reach steps and handrails
With safety prioritised throughout the design process, the new Mecalac cabbed dumper incorporates MDX design characteristics, resulting in easier and safer access to the machine thanks to high visibility and easy reach steps and handrails, as well as an excellent engine access enabling all servicing operations from ground level. In order to ensure a higher level of operator protection in any situation, the certified ROPS/FOPS MDX cab has been additionally designed and tested by Mecalac to withstand impacts while loading the dumper skip. For additional safety, the 3.5MDX features Shield – Mecalac’s package of safetycritical operator features – as standard. Key technologies include start & drive interlock, handbrake warning, digital speedometer, fuel loss warning sensor, automatic idle shut-off, park brake test and Stop-Start Control. All Shield safety features are adjustable to suit different applications where these are not required.
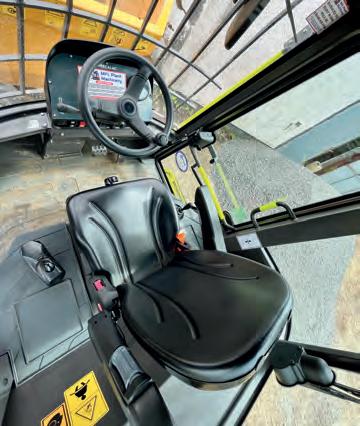
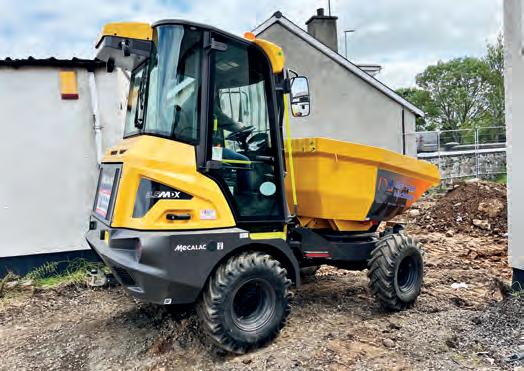
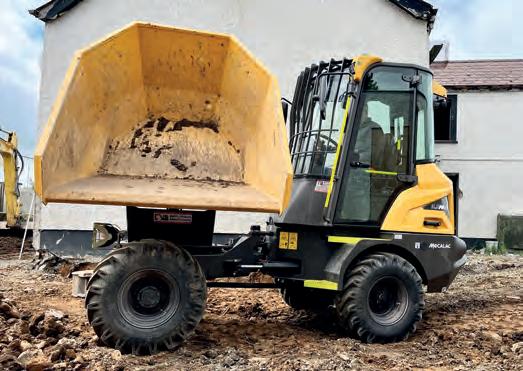
news
Opera Square’s sustainability programme giving old building materials new life
Limerick’s Opera Square is breaking new ground in the construction industry’s sustainability drive thanks to a unique reuse and repurpose programme that is giving new life to stone and brick that would otherwise be discarded.
In addition to the retention of 16 buildings deemed to be of historical importance on the site, conservation is also stretching to diverting huge volumes of materials from the demolition programme over the past 12 months into other projects elsewhere in the city and county. In a novel three-way partnership overseen by the Southern Region Waste Management Office and in conjunction with Opera Square developer Limerick Twenty Thirty and demolition and works contractor John Sisk & Son, over 1,000 tonnes of stone and brick materials alone that would otherwise have been destined for landfill have been salvaged and are being put to good uses. The ‘reuse’ programme commenced with what was the country’s first ever pre-demolition audit, which identified in advance of demolition works which materials could be reused. Among the projects the materials have since been diverted to are the Foynes Flying Boat museum, the Canal Harbour Building and bridge and old stone wall repairs around the county. Significant volumes also have been diverted to training programmes for young stone masons, which has been supported by the Economic and Social Intervention Fund through Limerick City and County Council Regeneration programme. It’s not just brick and stone that’s getting a new lease of life as other ‘reuse’ materials include palisade fence panels, which have been sent to Richmond Rugby Club; the metal gate and stone pillars from the entrance to the Granary Building, which are currently with the Civic Trust and items such as the historic limestone door case at 6 Rutland Street and cobble stones retained on site for future use. Modern materials have also been segregated for reuse on the development including carpet tiles, ceiling tiles, timber, and glass.
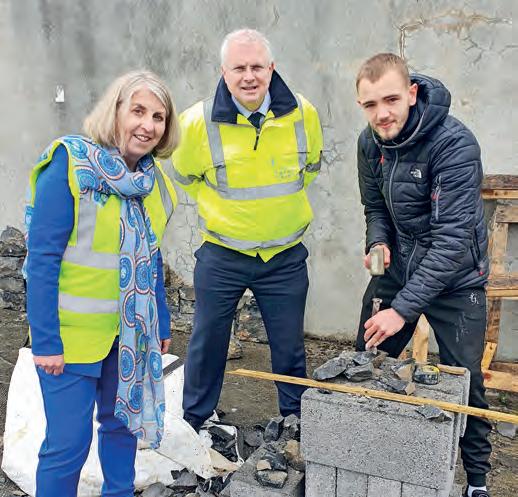
Marcus McCarthy, Old Cork Road, Limerick, an apprentice block-layer and stonemason working with stone recycled from the Limerick Twenty Thirty (LTT) Opera Square site. Also in picture are David Conway, Chief Executive of LTT and Philippa King, Coordinator with the Southern Region Waste Management Office.
Jobs Creation
The materials have been drawn from the site since the demolition and enabling works on the 1.62hectare project a year ago. Opera Square is the largest single commercial property development undertaken outside the capital. The construction programme will see up to 500 people employed at peak output on the site. When fully developed, the site will have the capacity for up to 3,000 employees across a 550,000 sq ft campus accommodation plus carparking and ancillary areas. The programme will take up to six years to complete at an estimated cost of €250m. Philippa King, Coordinator with the Southern Region Waste Management Office - which oversees waste strategies for seven local authorities in Munster as well as Carlow, Kilkenny and Wexford – said that recycling and reuse programme has the potential to be a template for major projects involving large-scale demolition. “Outlets for construction and demolition waste are limited, so we had to explore alternatives to waste creation and did this from the very outset with the Opera pre-demolition audit. The focus has ultimately been about diverting as much from waste as possible and we were not just talking about reuse alone but also repurpose and remanufacturing as well. Our goal was to maximise resource recovery on site as the buildings were demolished and I think we’ve achieved that. A key objective for Limerick today is to embrace international environmental best practice on the circular built environment and what’s happening at Opera is a great example of that.” David Conway, CEO at Limerick Twenty Thirty, said that sustainability is integral to all its projects. “We have already set a new standard in terms of sustainable development with our first project, Gardens International, and we are going to maintain that standard with the Opera Square site and with the Cleeves Riverside Quarter and every single project we work on, big or small. However, what this project shows is that we are not alone going to have an environmentally proofed finished product but every step along the way is going to be as sustainable as possible.”
Apprentices Training
Shane O’Donovan, General Manager – Special Projects with contractors John Sisk & Son said, “Pretty much anything we can reuse on site is staying here. Of the other materials, we’ve managed to recover over 1,000 tonnes. We’re delighted to see it being reused and we’re also very happy that some is being used in training apprentices in the use of stone and stone masonry. The apprentices are cleaning and dressing the stone and preparing it for reuse on projects around the city and county such as wall repairs and graveyards and the like. That’s a really positive output as well.”
PLANT & CIVIL
CONSTRUCTION, QUARRY & RECYCLING MAGAZINE AWARDS2022 SAVE THE DATE THURSDAY 24th NOVEMBER 2022
