
9 minute read
Hyundai Adds to Growing A-Series Excavator Range
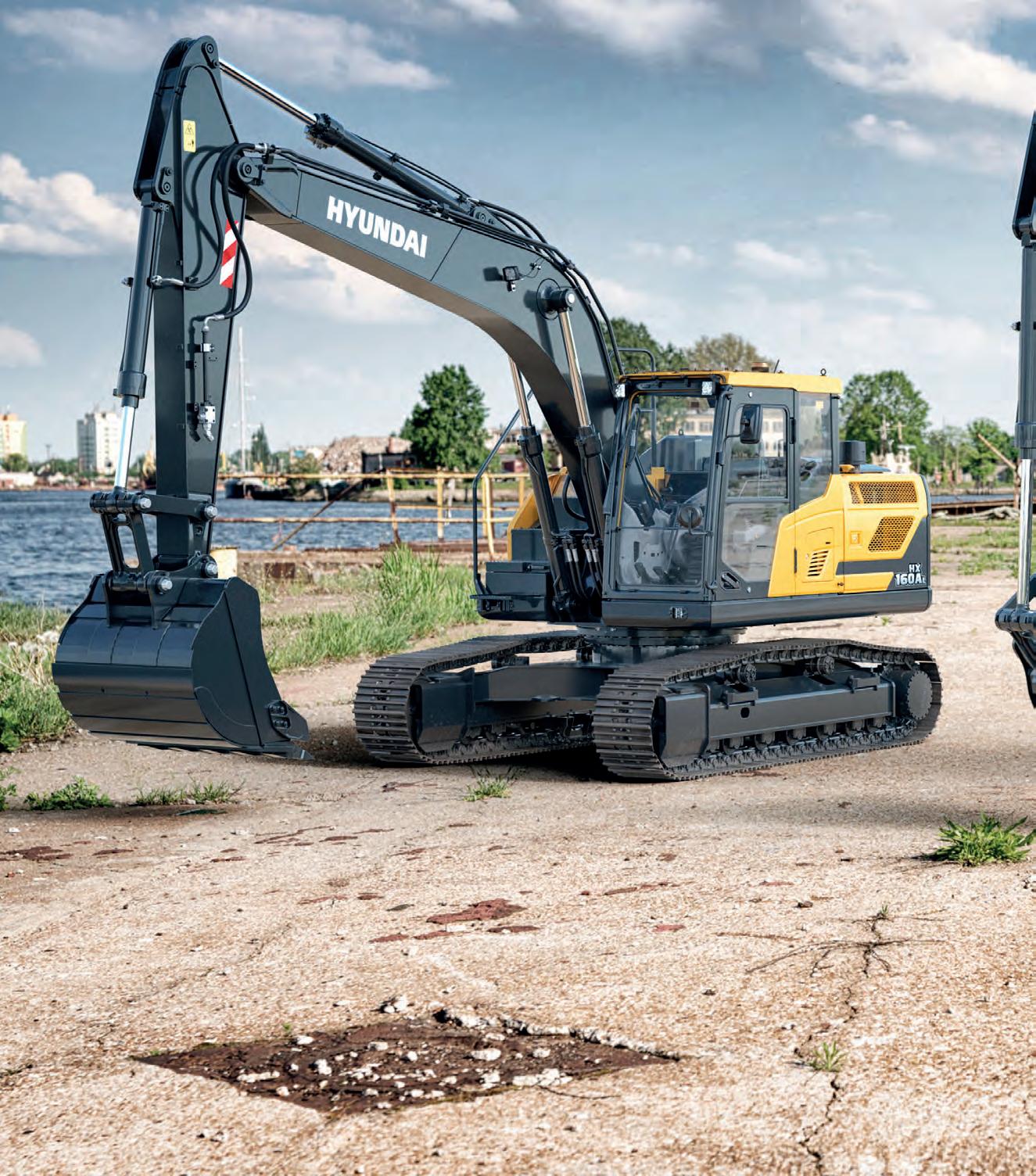
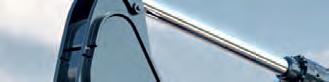
Hyundai Construction Equipment is introducing a further two EU Stage V compliant A-Series crawler excavators, with the launch of the HX160A L and the HX180A L.
These mid-weight machines are powered by the latest Cummins diesel engines, achieving Stage V emissions standards without the need for Exhaust Gas Recirculation (EGR). Offering improved fuel consumption, the 16 and 18-tonne models deliver improved operating speed and performance, with increased visibility and safety. Hyundai’s Electric Pump Independent Control (EPIC) system has been adopted, to make the most of the additional performance provided by the Cummins B4.5 diesel engine. Both excavators benefit from a 115kW (155hp) gross power output, with a robust 712Nm peak torque available at just 1,200rpm. Twin variable displacement hydraulic pumps deliver 160lpm of flow, providing the HX160A L and HX180A L with increased productivity when compared to many competitor machines. Improved control of the engine output and the hydraulic system has resulted in increased fuel efficiency, with the excavators achieving a 5% efficiency gain against the previous HX Series when levelling and truck loading in P Mode. By optimising the design of the main control valve and hydraulic hose routing, Hyundai has also minimised energy losses within the system. A new Lifting Mode improves fine control and lift capability, reducing engine rpm, activating power boost and offering improved pump flow control. The machines are also offered with an optional Fine Swing Control, smoothing the movement of the boom at the start and stop of the swing movement.
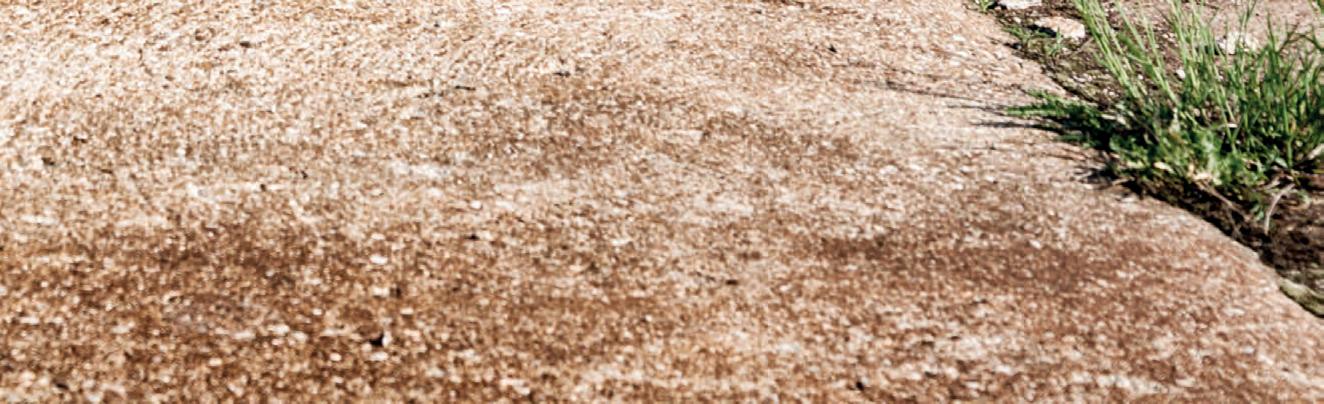
CONTINUES ON NEXT PAGE
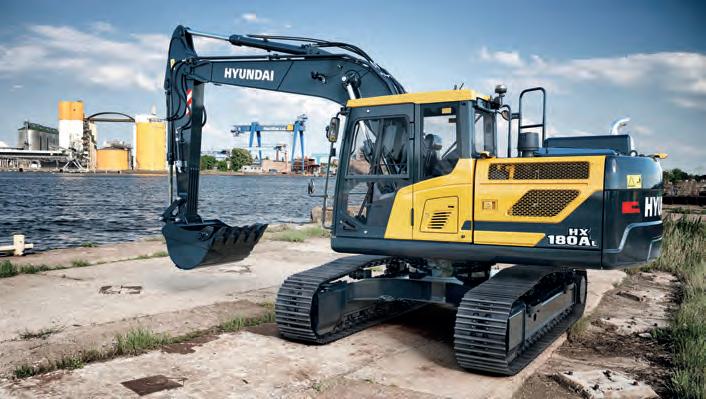
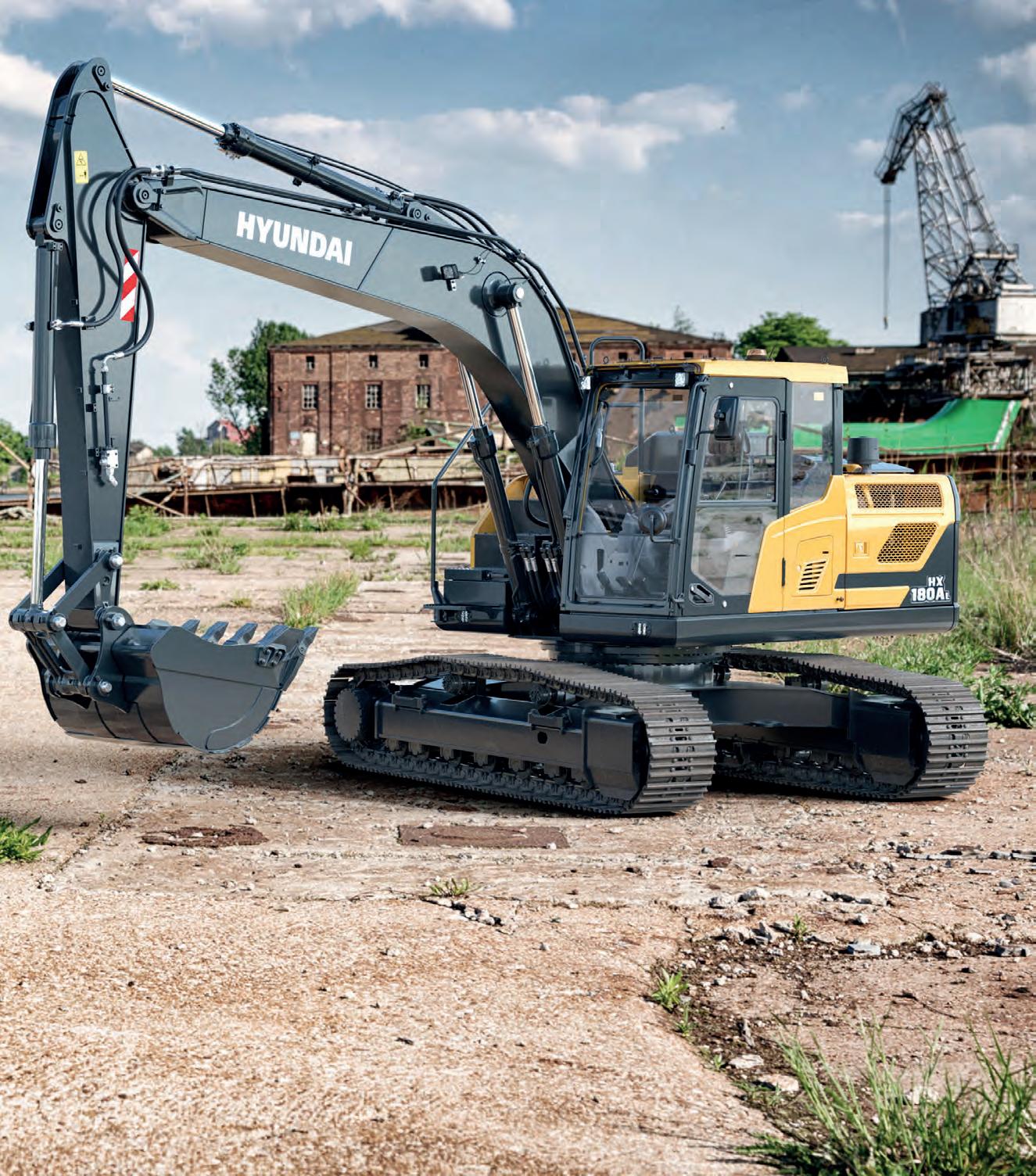
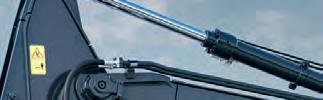
CONTINUED

An Auto Safety Lock is offered as standard, preventing unintended operation of the hydraulic functions of the excavator. The operator can set boom-lift speed compared to swing speed, by activating and deactivating the boom priority function. Dipper arm in speed can also be fine-tuned, by activating and deactivating the arm regeneration function. It is now possible to save machine settings through the new Key On Init work mode, to apply the settings on engine start-up. The machine owner can also restrict operator access to some functions within the menu if required. INDIVIDUAL REQUIREMENTS
The HX160A L has an operating weight of 17,455-19,050kg, while the HX180A L weighs in at 18,140-19,985kg. Both models can be supplied with a range of track pads, from 500mm to 700mm, while the HX180A L can also be equipped with a low ground pressure 800mm wide pad. Customers can choose to equip either model with a full width dozer blade, increasing versatility, while boosting digging and lifting stability. The standard monoboom length is 5,100mm and there are three dipper arms offered, at 2,200mm, 2,600mm and 3,100mm in length. These provide maximum digging reaches of up to 9,450mm and a maximum digging depth of 6,530mm. Alternatively, customers can choose a factory two-piece boom, offering a boom length of 5,100mm with arm lengths of 2,200mm and 2,600mm. Maximum digging reach with the two-piece boom is 9,110mm, while maximum digging depth is 5,690mm. A host of options allows full customisation of the excavators, with buyers able to specify Hyundai’s Advanced Around View Monitoring (AAVM) camera system for maximum visibility and safety on site. Customers can also choose a mirror view camera, helping the operator to cover visual blind spots to the right of the machine. Operators can specify an optional Level 2 Falling Object Guard (FOG) for the cab and there are optional side protectors for the upper structure of the machine for use in tight conditions or within more severe operating conditions. Other options include the provision for a three-way valve, for bucket/ clamshell operation, an engine air intake precleaner and an engine coolant pre-heater. INCREASED PRECISION
The A Series cab provides a 13% increase in internal space for the operator, with an improved grab handle design in the cabin door, making it easier to access the driver’s seat and improving visibility to the side of the machine from the cab. There are also wider, anti-slip steps for easier access to the cab and service areas. The interior has an 8” capacitive-type touchscreen for all major information, which can also be controlled through an automotivestyle jog/dial module. The excavators can be specified with optional proportional auxiliary controls in the Kawasaki joystick lever heads. Single pedal straight travel is also available. Hyundai’s HX A Series excavators benefit from a host of state-of-the-art digital connectivity technologies. This includes the proven standard Hi-MATE remote management system, that delivers the highest level of service connectivity and remote diagnostic ability. The Mobile Fleet App has been updated to allow fleet owners easy access to machine operating data, including economical usage, utilisation and fault code recognition. That Wi-Fi connectivity, using Miracast, allows the operator to use many of the functions of their smartphone, directly through the machine’s 8” infotainment screen. Drivers can operate their phones hands-free, listen to music directly from their smartphone and use a number of internet-based applications through the Miracast system. REDUCED SERVICE COST
The excavators benefit from a revised cooling package layout that contributes to improved serviceability. Engine oil and oil filter change intervals have been extended from 500hrs to 800hrs, while the fuel filter and pre-filter intervals are now double, at 1,000hrs. This contributes to reduced service and maintenance costs and a cut in planned downtime, improving productivity and utilisation for the customer. Optional Engine Connect Diagnostics (ECD), which is an integrated resource between Cummins and Hyundai, allows technicians and dealers to support customers with diagnostic reports and engine performance data. HCE-DT Air also allows the customer to connect wirelessly through a smartphone or laptop on site.
Aggregate Industries Launches UK’s First Ever Commercially Available Biogenic Asphalt
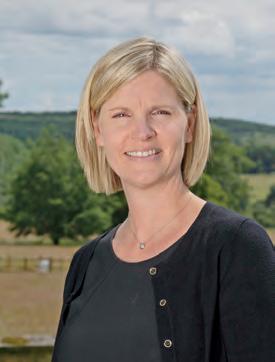
As part of its ongoing commitment to decarbonising the construction industry, leading building materials supplier Aggregate Industries has further developed its SuperLow product range with the launch of the UK’s first commercially available biogenic asphalt.
SuperLow-Carbon asphalt has been developed in partnership with Shell Bitumen as a pioneering product for more sustainable pavement projects. In an industry first, SuperLowCarbon uses Shell’s Low Carbon Bitumen in a unique formula that utilises improved production processes and alternative energy sources to lower its embodied carbon footprint. It also includes a biogenic material that effectively locks CO2 within the asphalt rather than releasing it back into the atmosphere, which creates a ‘carbon sink’ – something that absorbs and stores more carbon from the atmosphere than it releases. SuperLow-Carbon is manufactured at lower temperatures than standard asphalt, which means it requires lower energy to produce than its hot mix equivalent without compromising on performance. Production at a lower temperature also reduces nuisance fuming, odour and steam at the project site, which in turn lowers burn risk, improves visibility and provides better working conditions for operatives. In addition, lower asphalt temperatures during production reduces binder ageing and the product remains highly compactable for longer – allowing more time for full compaction, delivering enhanced performance and durability, and ultimately life-expectancy. It also reaches trafficking temperatures much quicker than hot mix products, allowing for earlier reopening of carriageways to the travelling public; resulting in less disruption and reduced build costs. Vicky Smith, Managing Director – Asphalt at Aggregate Industries, said: “As the UK’s leading building materials supplier, we have a responsibility to ensure we play a central role in the transition to net zero. That is why it is crucial to us to never stand still when it comes to the production of innovative and sustainable building solutions.
Unique Solution
“We are pleased to have worked with Shell Bitumen to bring the UK’s first commercially available biogenic asphalt UK market. With highways agencies under ever-greater pressure to deliver a sustainable strategic road network (SRN), SuperLowCarbon offers a unique solution unlike any other on the market. Containing biogenic materials that lock in CO2 – even when recycled - as opposed to realising it back into the atmosphere, SuperLow-Carbon has the potential to change the way we create pavements. “We’re delighted with the result, which is a hardworking, sustainable and low carbon product that does not compromise on quality, performance or durability.” Ana Alvernhe, General Manager, Shell Construction & Road, said: “This innovation is an excellent example of how both new and existing technologies can be combined to deliver a solution which reduces the embodied carbon of materials, a critical lever for decarbonising construction. “Working with customers on technology development is a priority for Shell, and we are proud to have partnered with Aggregate Industries on this solution using our Shell Bitumen CarbonSink. Wide-ranging collaboration across the value chain such as this will be crucial in accelerating the pathway to a net-zero construction sector.” The launch of SuperLow-Carbon is the latest in a series of steps taken by Aggregate Industries towards the development and use of more sustainable construction materials. In 2020 parent company LafargeHolcim became the first construction company to sign the Net Zero Pledge and since then Aggregate Industries has introduced a host of low-carbon products, including its SuperLow asphalt and ECOPact concrete product ranges.
Vicky Smith, Managing Director - Asphalt at Aggregate Industries.
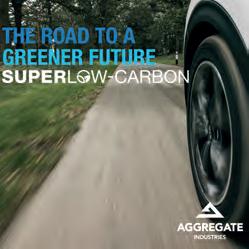
New Research Highlights Commercial Value of Developments with Sustainable Design
A new report, ‘Sustainable by design’, by engineering consultancy Patrick Parsons, based on research with 100 senior executives of UK construction firms, reveals that they are seeing significant commercial benefits from using sustainable design and engineering to build developments with lower carbon footprint and water use, reduce waste and materials used.
Two thirds (66%) said sustainable design is adding value to current developments and 83% said that projects designed with green credentials have given them a competitive advantage. Furthermore,68% expect the value of developments with sustainable design to increase by between 10% and 20%, and 18% expect values to increase by between 20% and 50% over the next three years, demonstrating the significant premium placed on sustainable construction. The research also highlighted that the most important aspect of sustainably designed developments is that they can be adapted to meet future environmental and social challenges. Commenting on the findings of the report, Conor Murphy, Senior Partner, Structural Engineering At Patrick Parsons said: “Reducing the impact of our built environment is no longer an option but an imperative, and sustainable design and engineering has a crucial role in protecting the environment and our communities. This is recognised in our report, which shows that sustainable design and engineering gives construction firms a competitive advantage when it comes to securing new projects and increases the value of developments.”