
37 minute read
Rokbak win two CeeD Industry Awards
ROKBAK WINS TWO CEED INDUSTRY AWARDS
Rhys Dingwall, CeeD Young Person of the Year.
Rokbak employees are celebrating after winning two prestigious industry awards. The company bagged awards in both Marketing and the Young Person of the Year categories of the CeeD Industry Awards 2022.
CeeD is a national body that supports a range of industry sectors in Scotland, bound together by a common aspiration to improve operational efficiency, effectiveness and profit through peer-to-peer knowledge exchange. CeeD’s Industry Awards Dinner, which took place recently at the Glasgow Hilton Hotel, in Scotland, recognised and celebrated the achievements of some of the best established and rising-star businesses and individuals in the country. Rokbak’s entry for the Marketing category focussed on the company’s hugely successful global rebrand campaign. Judges were impressed with the passion shown by the marketing team, who working in unison with other Rokbak teams, to help devise and drive the campaign – which also included direct feedback from both dealers and customers. This ensured Rokbak and its robust RA30 and RA40 haulers received extensive coverage in the national and international trade press, as well as across social media. “Rokbak’s rebrand campaign was of huge importance for our company,” says Paul Douglas, Managing Director, Rokbak. “The campaign had to connect to our dealers and customers, and it did so on so many levels. It really grabbed the attention of the various media streams about the reliable haulers we are manufacturing from our plant in Motherwell. “The campaign was expertly conceived and delivered through incredible Rokbak teamwork. The project touched every area of the business and you could really feel the pride and passion from our team members. It took a significant contribution from all functions in making the rebrand so successful, and that they have now been officially acknowledged by CeeD with this award.” NURTURING TALENT
Rokbak’s evening of success continued as Rhys Dingwall was announced CeeD’s Young Person of the Year. Rhys, 19,joined Rokbak through the company’s partnership with local authority, North Lanarkshire Council and their No Limits Scheme. The initiative is linked to the Supported Employment Scheme, which matches jobseekers who have additional support needs and / or disabilities to recruiting companies. Rhys has proven to be a real asset to the business, especially to the Paint Shop team, taking on every task with enthusiasm and enjoying the challenge of learning new skills. Since coming on board, Rhys has undertaken a range of activities – from washing trucks and valeting cabs to masking and paint finishing. Having joined the business for a fixed term of a year, it is planned that Rhys will be offered full-time employment. “I am thrilled that Rhys has won CeeD’s Young Person of the Year award,” says Paul Tierney, HR Director, Rokbak. “Since joining Rokbak he has proven to be a real talent for the company and I know that his work is greatly appreciated by his colleagues from the Paint Shop team – Rhys has a great future ahead of him.” Sharing Rokbak’s plaudits was also Ross Mitchell, who was shortlisted for the Young Person of the Year category. Ross, 23, joined the company in 2017 and has excelled working with the New Product Introduction teams, helping to implement quality processes and inspection documentation for Rokbak’s new haulers being distributed around the world. Ross also manages the Customer Concerns Database and achieved internal auditor certification in both Quality and Environmental ISO standards. He has joined Rokbak’s Internal Audit team, while also continuing to study for his Engineering degree. “I am delighted that Ross was also recognised by the judges,” concludes Paul Douglas. “Rokbak is committed to nurturing and developing the skills and experience of young people so that they can have great careers.” Rokbak were Headline Platinum Sponsors of the CeeD awards, as well as sponsors of the Women in Industry Award, which Paul presented to Rachel Jones, from SnapDragon Monitoring Ltd on the night.
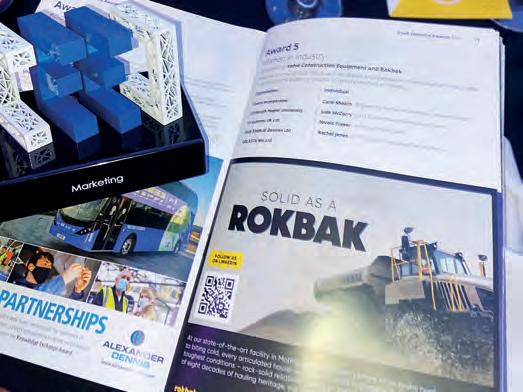
news Construction Will Need More Women to Meet Future Needs, Says CIF
Ireland’s construction industry will need to entice more women into the sector to meet its future needs, the Construction Industry Federation (CIF) has warned.
The CIF made their remarks as new figures revealed that one in four of the construction jobs added in 2021 went to women and the total number of women in the industry has reached its highest point since records began. According to the latest figures available from the Central Statistics Office, on a seasonally adjusted basis the number of women employed in Irish construction reached 14,400 in Q4 2021. This represents 9.1% of the total construction workforce in the country. It is also the highest proportionate level since the CSO started tracking construction employment in 1994. The figures also showed that total construction employment grew by 23,200 over the course of 2021, rising from 135,200 in Q4 2020 to 158,400 in Q4 2021. During that same period the level of female employment in the sector grew from 8,500 to 14,400 – an increase of 5,900. This jump represents 25.4% of the total increase in the Irish construction workforce gained during 2021. With the construction sector continuing to expand and requiring an additional 1,000 workers per month, the CIF believes that the industry will need to make further inroads into improving the ratio of female employees in the industry. The analysis was presented during the CIF’s recent International Women’s Day Event held in Clontarf Castle. Among those to participate in conference were women at various stages of their careers, representing a variety of aspects of the industry. These included Tara Flynn, President of the Master Builders’ and Contractors’ Association (MBCA) and Director with Paul Flynn Construction; Joanne Cluxton, Group HR Manager of Mercury Engineering; Lorraine Brady, Pre-Construction Director with BAM Ireland; Phil Kane, Country Manager with Eaton; Sinead Savage, Association Director of Manning Construction Group; Kate Rooney, Mechanical Engineer with Designer Group as well as Ireland’s first female crane driver Kate Fahey of BKRN Construction. Speaking at the event, CIF Director General Tom Parlon said, “Our industry needs more women – from the building site to the boardroom. It is positive to see that there was a significant increase in the number of women working in Irish construction last year, but our sector will need to build on that momentum. That means addressing any barriers that are preventing women from viewing construction as a viable career pathway in 2022. “Clearly that also involves breaking any biases that remain in the Irish construction sector. There are so many women who are doing this on that on a daily basis. This ranges from high ranking directors in some of Ireland’s premier construction companies, to those who are beginning their careers. Every day these women are showing how much of a contribution they make to Irish construction and highlighting why we need to bring more women into the industry. “Thankfully the construction sector is growing and growing fast. With a major demand for more workers we have to be exploring all avenues for attracting additional talent. Women account for approximately half of the overall labour force in this country, but still less than one in ten of the people working in our sector is female. “ We have to address this gap and it is up to everyone in the industry to do what they can to help encourage more women to consider a career in construction. Growth goes beyond numbers, it also has to include expanding our outlook and appeal. I hope to see further progress made on all of these counts this year and over the coming years.”
Construction Industry Specialist Appointed as New Head of Sitech
SITECH UK & Ireland has appointed a new head of business with thirty years’ experience in the industry. Grant Pearce has held several field-based and customer-facing roles over the last three decades spanning all aspects of the construction industry, giving him a unique insight, and understanding of customer needs and challenges.
Pearce brings authorised Trimble technology dealer SITECH a wealth of knowledge in the construction, aggregates and waste industry having started his career as an engineering apprentice for Finning, exclusive dealer of Cat equipment. After completing a four-year apprenticeship Pearce spent a decade working across the UK as a field service engineer, before taking on a number of customer facing roles for the company. More recently Pearce was head of the parts and service division at Finning, where he oversaw the implementation of a digitisation programme called Parts Direct, giving customers the ability to order parts on-line for direct delivery to site within 24/48 hours to help ensure machine uptime and efficiency. He then spent three years working as head of machine equipment rental services where he established and developed the company’s rental and used equipment sales units – both of which are now a major part of the company’s product and service offering to customers across all industries. His new role will see Pearce overseeing the commercial strategy for SITECH and helping it continue to thrive as it expands. “I’m thrilled to join SITECH at such an exciting time. The industry is gearing up to make construction technology the norm and not just for those operating big machines in the construction and aggregates industries,” explained Pearce. “The team here are passionate and driven, and I’m looking forward to work alongside them to continue to move the SITECH business forward.” Pearce continued: “Last year SITECH introduced a range of new services for customers, including access to newly trained drone operators, and a training facility that is already teaching future machinery operators using augmented reality. As we look forward, I have ambitious plans for SITECH, including plans to significantly expand our technology rental service as well as continuing to build the purchase and aftersales offering. I am confident that alongside this brilliant team, we are going to deliver big things in 2022 and beyond.”

Grant Pearce.
news
Mallon visits A6 Dungiven to Drumahoe scheme to mark significant progress
Infrastructure Minister, Nichola Mallon recently visited the £220 million Flagship A6 Dungiven to Drumahoe Dualling Scheme to mark what she says is ‘the significant progress made on this strategic project.’
The scheme will provide 25.5 kilometres of high standard dual carriageway between Drumahoe and Dungiven, including a bypass of Dungiven with new roundabouts connecting the scheme to the existing road network at either end. Minister Mallon said: “The A6 is a strategically important route as it connects the North West to Belfast and beyond so I am delighted to confirm that huge progress that has been made on this vital scheme. The existing road carries around 15,000 vehicles per day and with traffic levels continuing to grow, the very significant investment of £220million from my Department will help to address regional imbalance,
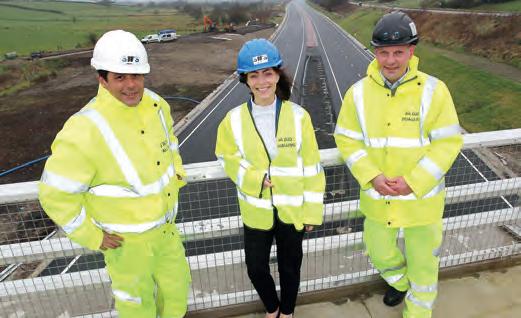
Minister Nichola Mallon is pictured with Juan RodriguezAltonaga Martinez (Contracts Manager) and Michael Troughton (Project Director) representing the Contractor Joint Venture of Sacyr, Wills Bros Ltd and Somague.
contribute to the economic development of the area, and bring long-term benefits to road users and local communities. “Work commenced in September 2018 and I am pleased to say that the project is now very well advanced with the earthworks, drainage and all 22 of the structures along the scheme substantially complete. The pavement construction is also progressing well with more than 30% of the surface course already laid along the main carriageway. “Last year the £189 million A6 Randalstown to Castledawson dual carriageway was opened to traffic, and when the A6 Dungiven to Drumahoe section is completed this year, approximately three quarters of the Belfast to Derry route will be of dual carriageway standard or better. “As well as improving the standard of carriageway along the A6, both schemes also provide enhanced provision for public transport, pedestrians and cyclists. New park and rides sites are now operational at Drumderg (Toome) and Drumahoe, with a further park and ride site currently under construction at Claudy. “My officials and the contractor have worked hard to minimise any inconvenience for the public and I want to thank them for all their efforts. I look forward to the completion of this scheme as it will significantly enhance the connectivity of the north-west, improve journey time reliability, reduce journey times and crucially improve road safety.”
Introducing the most adaptable Tipper on the market DEALERS
From building site waste to construction materials or plant, the Brian James Tipper, freshly updated for 2022, has you covered.
The new Tipper comes with a host of market-leading features, including the all-new ‘Click & Clamp’ system with auto-adjusting posts and locking clamps for easy fit rattle-free sides and battery trickle charge. Available in two widths, four different lengths with a choice of 2700kg or 3500kg gross capacity and twin rams on all 3.6m and longer bed models, the Tipper has a number of health and safety friendly features such as an audible alarm when lowering the bed, a storage box for storing items and multiple anchor points. A visually stunning trailer with a choice of body panel colours and eye catching LED lighting as standard, it is available with a host of options to build the trailer to suit your business demands. Options include a ladder rack, loading ramps, electric winch, rear support stands, side extensions and much, much more. The new Brian James Tipper is available to order from your local Brian James Authorised Retailer now. In Northern Ireland, Eakin Brothers, Co. Londonderry and Trailertek (NI) Limited, Co. Armagh. The Republic of Ireland dealers include AD Test Centre Limited Co. Kilkenny, Barrett Trailers Co. Limerick, BG Motors Co. Kerry, Blue Print Autos Co. Roscommon, DH Farm Machinery Co. Galway, Heneghan Plant Hire Ltd Co. Mayo, Noblewood Co. Cork, SME Group Co. Meath and Trailerstuff (KER Group) Co. Donegal.
THE NEW 2022 TIPPER

FROM BRIAN JAMES TRAILERS
available to order now
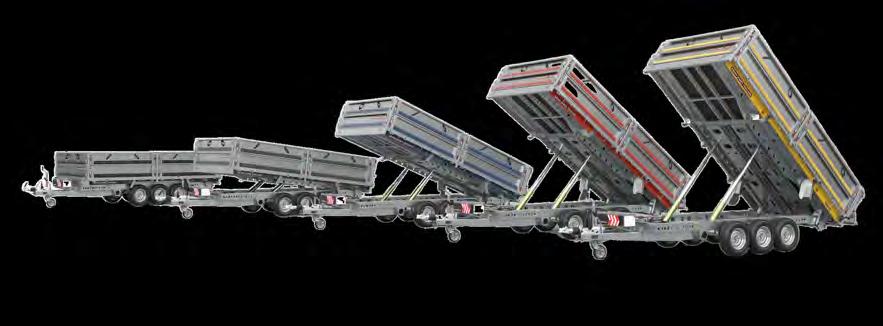
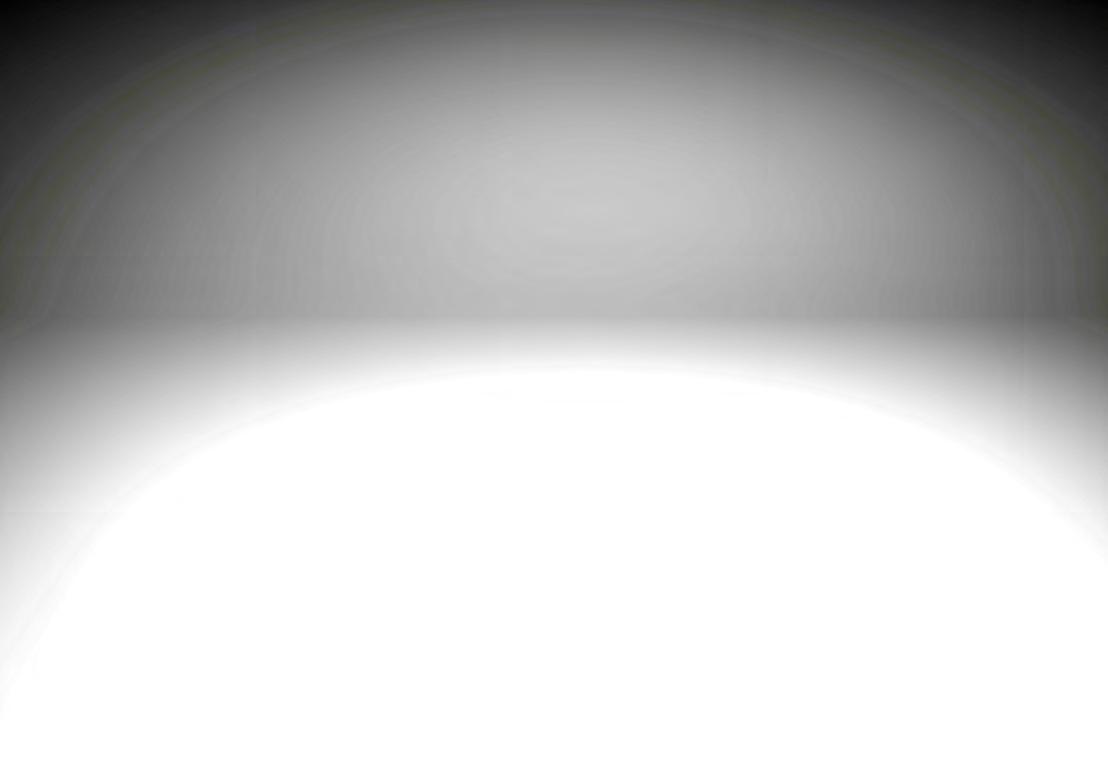
CASE UNVEIL NEW E-SERIES CRAWLER EXCAVATOR RANGE

CASE Construction Equipment has launched its new E-Series Crawler Excavator range; it includes seven new models from 13 to 30-tonne.
Market-leading features include new FPT Industrial (FPT) Stage V engines, enhanced cab design and operator experience, improved hydraulics’ controls and settings, machine structure, undercarriage and new full range of CASE® Service Solutions. As a result, customers benefit from greater controllability, reliability, operator comfort, efficiency, productivity and total cost of ownership (TCO). “Our customers are facing increasing challenges, which is intensifying competition. So, they look to CASE to develop machines that have the highest levels of uptime, efficiency and productivity,” explains Egidio Galano, Director, Construction Equipment Product Management Europe, CNH Industrial. In response, we developed the E-Series, delivering excellence, efficiency and economy.” The new E-Series range has many new features that integrate and work together to deliver market-leading uptime, productivity and profitability for customers. When combined, the new Stage V FPT engines, CASE Intelligent Hydraulic System (CIHS), new work modes, telematics, optimised cab control layout and improved visibility lead to greater controllability and precision. In turn, this results in safer, more productive and more profitable operations. The new E-Series is delivering competitive advantage to customers. CIHS, a leading feature of the previous generation, is now integrated with four new work modes, with additional customisable hydraulic settings to adjust the flow priority for arm, boom or swing movements all controllable by the operator. Efficiency-enhancing Super Power (SP) mode delivers maximum productivity, Power (P) mode provides a surge of power when needed and Lifting (L) mode optimises object handling. When paired with the new FPT engines, the Eco (E) mode delivers remarkable fuel savings of up to 17% on some models. FPT STAGE V ENGINES
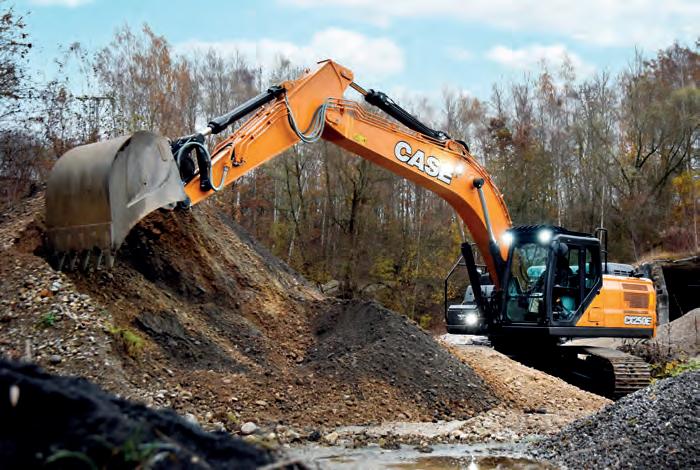
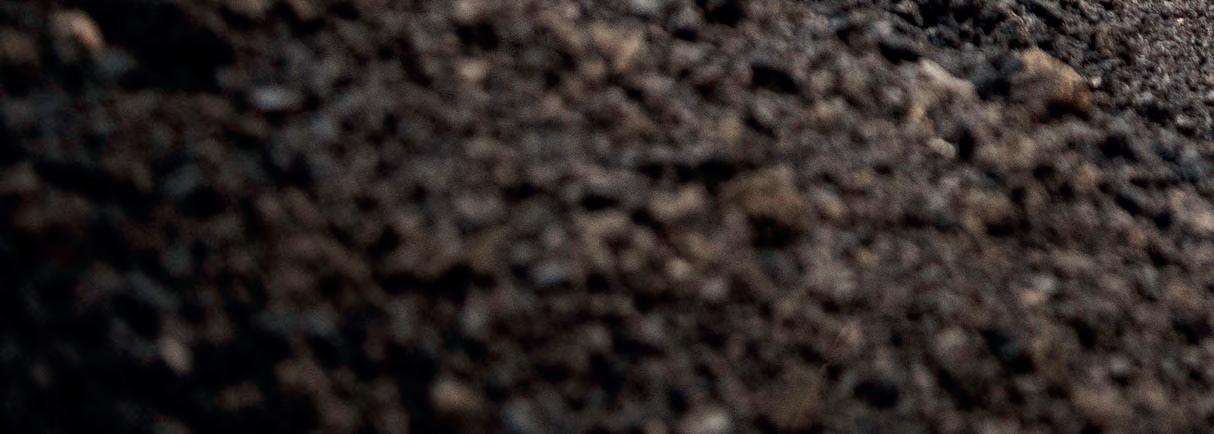
CASE reinforces the long-standing partnership with FPT, with its strengths in construction powertrain design. The E-Series

THE EAGLE HAS LANDED!
CASE’s NEW E-Series excel in everyway.
incorporates more powerful and efficient Stage V engines in all new series models. The 13-18-tonne models feature N45, the 4.5-litre engines from the renowned NEF series, while the N67, from the same engine family, powers the 21-30-tonne models providing 6.7-litre displacement. Describing the beating heart of the new E-Series, Galano highlights the FPT engines’ extensive new features: “CASE has introduced a solution free from exhaust gas recirculation (EGR), ensuring greater efficiency during the fuel combustion. When coupled with selective catalytic reduction (SCR) on filter, the E-Series delivers unprecedented total cost of ownership (TCO) improvements.” The new e-Series is equipped with HI-eSCR2, the patented after-treatment solution by FPT that is completely maintenance free and built for-life. There is no requirement for mechanical cleaning or replacement over the life cycle. CASE has also improved the service experience by doubling the maintenance intervals up to 1,000 hours for engine oil, fuel filters and oil filters. ALTERNATIVE FUELS
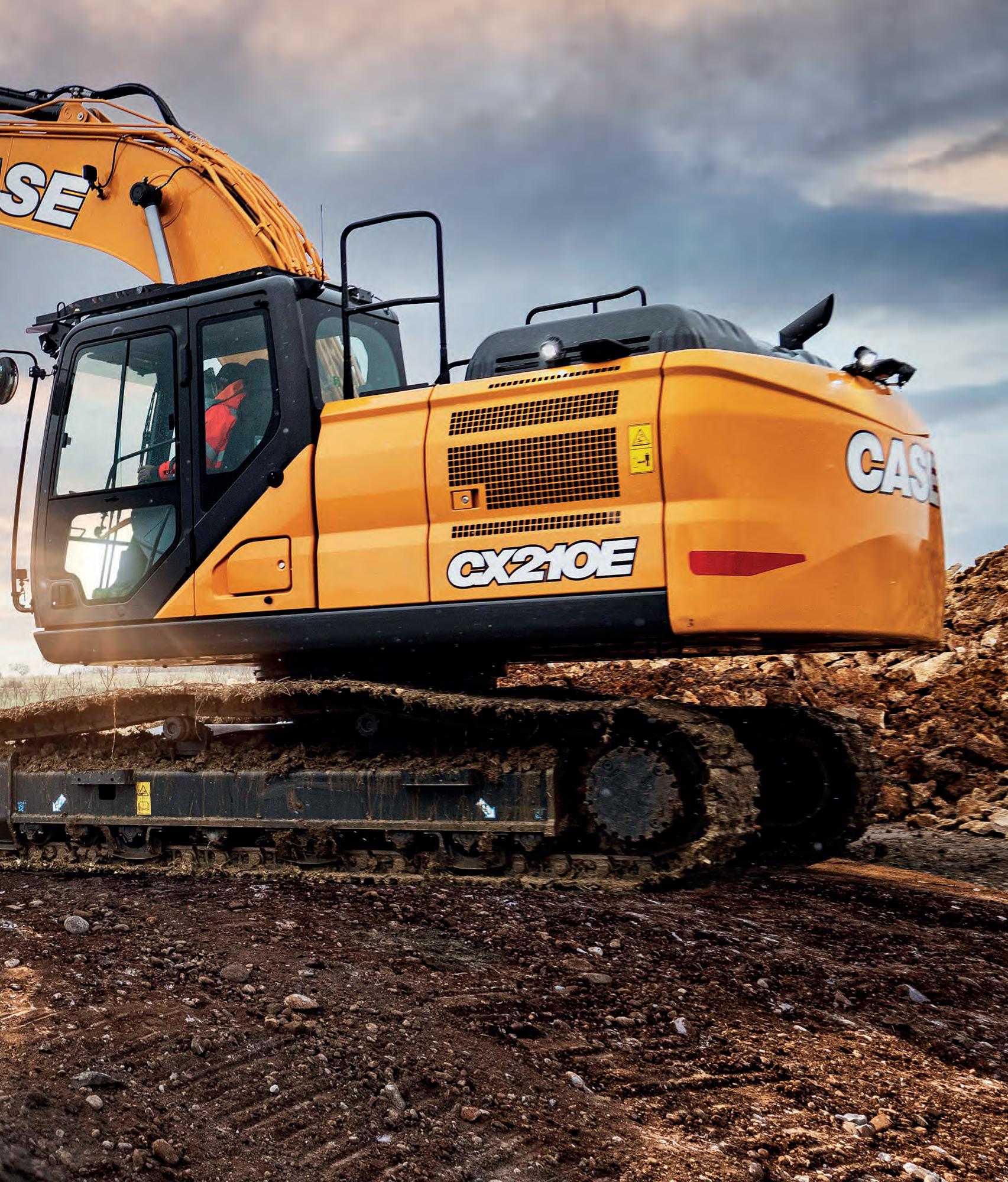
The new FPT Stage V engines are designed to offer flexible fuelling solutions for customers, particularly those operating in jurisdictions with demanding local regulations. All E-Series models can run on regular or alternative fuels, such as increasingly popular HVO (hydrogenated vegetable oils). Building a revolutionary operator experience with extra comfort and safety In addition to the new work modes, the E-Series provides operators with increased levels of comfort and visibility. The cab has many new features that will enhance the overall operating experience. Improved access, a brand-new industry-leading 10-inch LCD monitor with 5 configurable buttons, new control layout, suspended pilot lever console, improved air conditioning system and larger storage compartments. OPERATOR COMFORT
All E-Series models retain the top tier comfort and safety features of the previous generation crawler excavators: spacious and roomy, fully adjustable ergonomic seats, optimised armrest position and joystick control. The right-hand side visibility was good before, and now it is excellent. Operator protection is still a priority, with standard safety features, such as the falling object protective structure (FOPS) level 2, retained. Additional competitive advantage for customers comes from the productivity, profitability and uptime of the new CASE E-Series Crawler Excavator range. CASE Service Solutions is a range of connected and non-connected after sales services that support customer experiences.
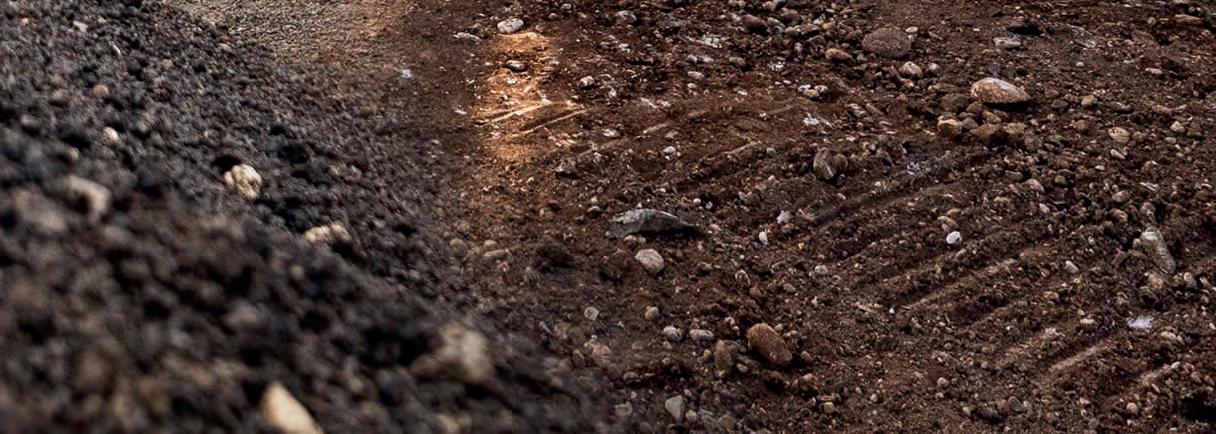
CONTINUED
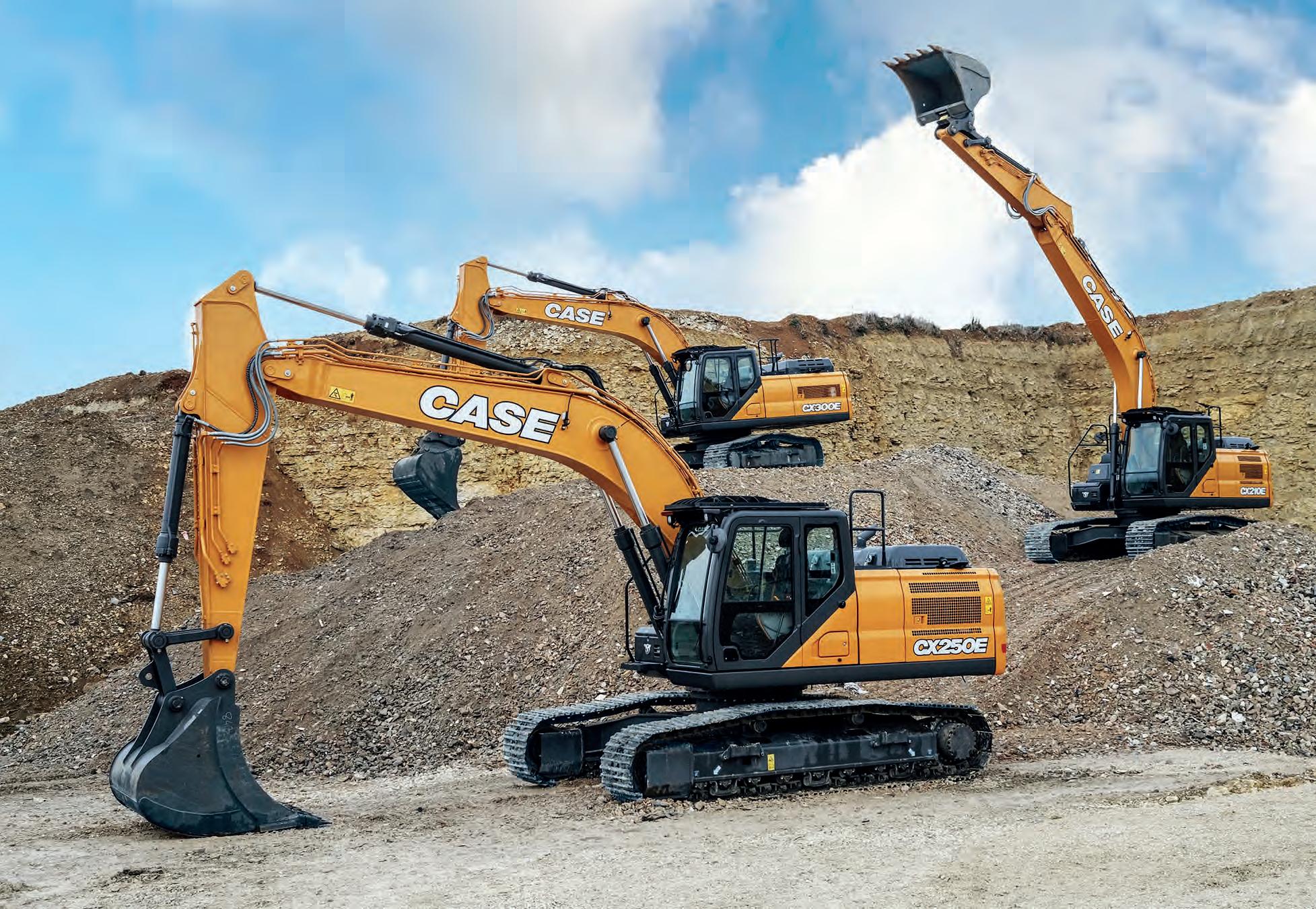
The bidirectional modem enables the use of CASE SiteConnect and CASE SiteWatch, a complete fleet management tool. The solution includes geolocation, fleet security using geo-fences and unauthorised use alerts and flexible reporting. Customisable reports can include key performance indicators (KPIs) such as fuel consumption, utilisation rate, machine hours and idle time, so productivity and profitability can be monitored and optimised. The data is easily accessible via a portal. CASE SiteConnect enhances telemetry data used by CASE’s Uptime Center team to provide dealers with alerts based on machine performance. Fast, corrective action to minimise downtime is possible, as dealers remotely access machine data and take corrective action faster. This enables dealers to be proactive in managing customer machines and boosting uptime. Both SiteWatch and SiteConnect are standard with the new E-Series range. Customers benefit from greater peace of mind with CASE Care, CASE Protect and CASE Fluid Analysis. CASE Care is a standard planned maintenance programme with genuine parts and lubricants. The programme is underpinned by the support, logistics and technical expertise of the wide-reaching CASE dealer network. CASE Protect is an extended warranty programme and CASE Fluid Analysis aims to prevent major failures, optimising the asset reliability and extending operating lifetimes. “CASE Service Solutions is designed to keep customer equipment in top condition with maximum uptime, no unexpected costs and optimised profitability,” concludes Peter Garry, Director, Aftermarket Solutions Europe. “CASE Protect and CASE Fluid Analysis are available for customers throughout Europe. CASE Care is available now in selected markets, with Europe-wide availability soon.” CUSTOMER RESPONSES
Customers drive CASE Construction Equipment’s business, and several have been evaluating the new E-Series in the field. Here is what two of them say: According to 32-year veteran operator Arnaud Bourguet, of SAS Bredillet near Dijon, France, who took a new CX300E on site, the machine is “perfect”, saying: “After the test I concluded that the shovel is very comfortable, fast, flexible and precise. The dashboard is good, especially the CASE Maximum View camera, you can see everything. It's perfect…I can recommend it.” A life-long CASE customer, François Jehae, manager of Belgian contractor Terrassements François Jehae had high expectations of the E-Series before his CX210E test drive. And he was delighted, starting with the new FPT engine which has: “…a lot of power, it purrs like the old generations, very flexible, the machine is precise…” adding “…the cabin is quite comfortable, I was delighted with the new monitor…it's really great.”
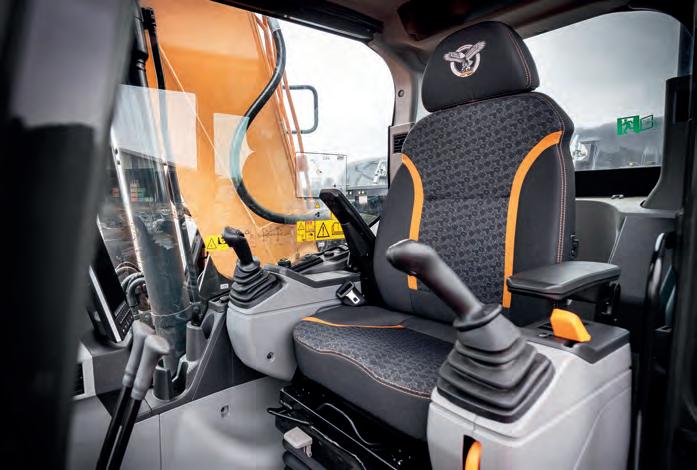
news
IPAF launches targeted safety campaign
A campaign emphasising the importance of working safely to avoid falls from the platform when using Mobile Elevating Work Platforms (MEWPs) to enable temporary work at height has been launched by the International Powered Access Federation (IPAF) at its annual Summit in London.
IPAF’s Don’t Fall For It! safety campaign outlines the possible underlying causes of falls from the platform when using MEWPs, which almost always lead to serious injury or death. It offers operators and managers key advice to mitigate the most common risks and avoid accidents of this type, as identified in IPAF’s ongoing incident reporting and analysis via the www.ipafaccidentreporting.org portal. Peter Douglas, CEO & MD of IPAF, comments: “MEWPs are designed to safely conduct temporary work at height in just about every environment, but every year the most common type of accident we see reported are falls from the platform, which as you can imagine nearly always lead to serious injury or death if they occur while using machines at height. “We are determined that our new Don’t Fall For It! targeted global safety campaign will help to instil safe working practices and remind operators and managers of some fairly basic positive steps they can take to reduce the risk of such incidents occurring. The messaging is really simple – select the correct machine for the job, don’t take risks, don’t cut corners, and wear the correct personal fall protection equipment in boom-type platforms.” Brian Parker, IPAF’s Head of Safety & Technical, says: “Operators can help avoid this type of accident by focusing on the principles we’ve set out as part of this campaign. If they are properly trained and familiarised on the MEWPs being used, then hopefully none of this guidance should be new, but we know that complacency breeds contempt, and that too often corners are being cut or fundamental principles of safe use ignored. “With this safety campaign, IPAF is saying that, if you find yourself tempted to do something different to what you know is the right and proper way to work, or if you are ever asked to do something that you think just isn’t safe by a work colleague or supervisor, then ‘don’t fall for it!’ Far better to think twice and save a life – whether it is a workmate’s or your own!” Key points of guidance in the IPAF Don’t Fall For It! global safety campaign include: • Plan thoroughly – conduct a proper MEWP site survey/assessment, select the correct machine for the work and use professionally trained operator(s) and supervisor(s). • Know your machine – operators should be trained on the machine type they are using and familiarised on the specific model.
Operators should assess that the machine is suitable for the task and conditions, and
adequate in terms of reach, articulation, and load-bearing capacity. Machine knowledge includes whether personal fall protection equipment (PFPE) should be used and, if so, what type to use, and how to attach it. • Clip on – If personal PFPE is required, all occupants of the platform must attach their lanyard to the correct anchor point.
Ensure movement within the platform is possible while attached, and do not move the machine or elevate the platform until and unless all occupants are attached. • Set up and manoeuvre the machine/ platform effectively – occupants should never need to over-reach, unfasten PFPE, step or climb on guardrails or otherwise extend the safe working envelope of the platform. Ensure vertical MEWPs are positioned and repositioned as necessary to allow easy access to the area of work to be undertaken; operators should not overreach or stand on guardrails to access a work area instead of taking the time and effort to correctly reposition the machine. • Stay inside the platform/attached – the guardrails of the platform form the primary fall prevention and define the operational envelope of the machine being used.
Always stay inside the platform. Where there is a requirement for PFPE, you must wear it. Do not exit the platform at height; unclip/exit only on completion of work when safely lowered to the ground. IPAF offers further guidance on using MEWPs that provides more detail on specific risks and advises on safe operating procedures. For more information on all of IPAF’s safety campaigns and links to relevant technical guidance visit www.ipaf.org/safe or see www.ipaf.org/contact to find your nearest IPAF office or representative. Visit www.ipaf.org/training and www.ipaf. org/resources for the full range of IPAF training course and the latest safety and technical guidance materials from IPAF.
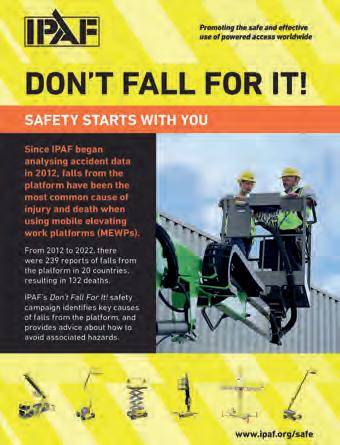
New Construction Industry Report Reveals Main Barrier to Achieving Net Zero
A new report, ‘Sustainable by design’, by engineering consultancy Patrick Parsons, based on research with 100 senior executives of UK construction firms, reveals that despite the majority (85%)believing the industry is doing enough to reach net zero by 2050, there are significant barriers to achieving this target.
Over two thirds (68%) of respondents said that improvements to building material supply chains to reduce carbon would be critical to achieving net zero, followed by 63% who said that existing planning regulations need to change to support the sector if it is to hit this target. Using alternative materials which have a lower carbon footprint is also a significant barrier to overcome for 62% of those questioned, followed by decarbonising existing buildings (59%) and the ability to collect data to measure carbon in buildings (48%). When asked about the impact of the focus on climate change because of COP26, 86% said that they believe it will accelerate positive advances in sustainability in the sector during 2022. Commenting on the findings of the report, Conor Murphy, Senior Partner, Structural Engineering At Patrick Parsons said: “The UK construction industry is committed to reaching net zero by 2050 and is confident that this target will be met. However, this ambition is not without its challenges in terms of the materials used, the need for planning rules to change and the ability to decarbonise legacy buildings to improve their performance. Greater use of sustainable design and engineering in the planning of new developments, will support the pathway to net zero.” Patrick Parsons focusses on helping clients assess, design, and overcome the most complex of engineering challenges across a range of sectors. Operating from four sites – its HQ in Birmingham, London, Wakefield and Ashvale - the business provides a range of connected engineering services including Structural, Civil and Geo-Environmental consulting engineering services, competences the firm has developed over many years, and for which it has built a strong reputation. To read the report in full, visit https://www.patrickparsons.co.uk/ wp-content/uploads/Sustainableby-Design-Report-Web.pdf
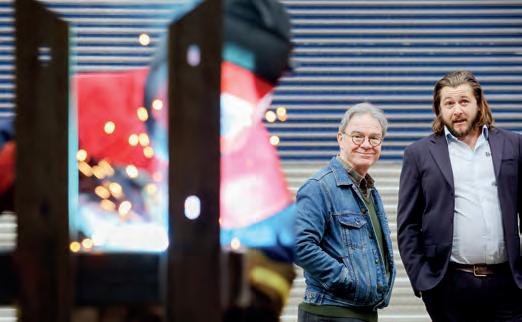
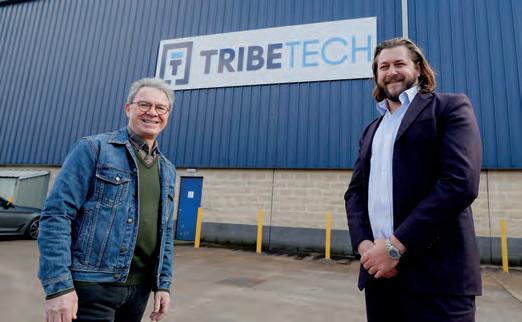
The Ambassador was given a guided tour of Tribe Tech’s manufacturing facility as part of his visit to Northern Ireland. Australia’s Ambassador to Ireland, Hon. Gary Gray, with Tribe Tech’s Managing Director Charlie King outside the company’s production facility in Mallusk.
Tribe Technology Welcomes Australian Ambassador to Mallusk Headquarters
The Australian Ambassador to Ireland has made a special visit to innovative automation focused mining equipment maker Tribe Tech in Belfast to hear about the growth of the company in Northern Ireland and Western Australia.
The Hon. Gary Gray, who is a former Minister for Resources and Energy in Australia and has extensive experience in the mining and minerals industry, met with Tribe Tech’s leadership team and workforce at its headquarters on Enterprise Way. Based in Mallusk, and Perth, Australia, Tribe Tech is led by a team of mechanical, electrical and mechatronic engineers and has developed the world’s first completely autonomous Reverse Circulation (RC) drill rig, which is designed to improve safety and increase efficiency in the mining sector, with a focus initially on iron ore. The first RC drill rigs in production have already attracted an impressive multi-milliondollar order book, with data showing that the automated rig is 100 times safer and 70% more productive than conventional RC drilling rigs. Managing Director Charlie King, who worked in Australia for more than a decade, said it was a fantastic endorsement to have the Ambassador make the trip up from Dublin. “I would like to thank the Australian government, and Gary in particular, for their ongoing support for what we’re building here at Tribe Technology. It was great to be able to show him the progress we’ve made in ramping up production. We’ve built a fantastic team in both Belfast and Perth in Australia and we’re looking forward to expanding into more global mining jurisdictions in future,” he said. Ambassador Gray said: “It’s great to be at Tribe Tech. This is a company that is building safety, it’s building efficiency and it’s building capacity into an activity which has been difficult within the mining industry across the world. Safe practices in drilling are at the heart of the best practices in mining and in exploration. The skill base that’s here in Ireland, the enthusiasm and the talent to build a global business in global supply chains is just magnificent. It’s wonderful to be here.” Tribe Tech moved the company’s headquarters to Mallusk in 2021 in part due to the availability of its highly skilled workforce, Northern Ireland’s strong track record in the manufacturing sector and economies of scale compared to more expensive locations. Plans are in place to grow the workforce to over 120 people in the next four years. Fiona McCartan, Supply Chain Manager at Tribe Tech said: “It is clear from Gary’s visit today that the excitement Tribe Tech is generating reaches far beyond Northern Ireland. We are providing fantastic opportunities for employment and, giving local businesses a chance to be involved in one of Northern Ireland’s most innovative projects and boosting the local economy. “This is why internationally our business is gaining so much traction from world-leading drilling and mining companies. It’s an exciting time for everyone involved and we are so thankful for the Ambassador’s support.”
NEBOSH and HSE to tackle one of the main causes of musculoskeletal disorders
NEBOSH and the Health and Safety Executive (HSE), have partnered to develop a new qualification aimed at preventing one of the main causes of musculoskeletal disorders: manual handling.
Musculoskeletal disorders (MSDs) accounted for 8.9 million lost working days in Great Britain in 2019/20 with manual handling estimated to be the main cause. 0.5 million workers suffered from a work-related musculoskeletal disorder in 2020/21, with a cost to organisations and to the UK economy. This is a global problem; the World Health Organization estimates 1.71 billion people experience musculoskeletal conditions worldwide, three in five workers in Europe report MSD complaints, more than half of US adults experience an MSD and it’s estimated that they cost countries between 0.5-2% of Gross National Product. The new NEBOSH HSE Certificate in Manual Handling Risk Assessment is a one-day qualification which is based on the Health and Safety Executive’s best practice guidance and tools. It focuses on practical solutions to help recognise, assess, and manage manual handling risks. On completion of the course, learners will be required to undertake a manual handling risk assessment, based on a selection of video case studies, to put their new knowledge to the test. Matt Powell-Howard, NEBOSH Head of Product Development, says: “Many organisations jump straight to providing training on manual handling – how to lift etcetera. In developing this qualification we’re encouraging organisations to take a step back and take the time to effectively risk assess their manual handling activities. By doing so they may be able to eliminate or reduce an activity and, if manual handling is required, then they’ll have all the information they need to protect their workers.” The NEBOSH HSE Certificate in Manual Handling Risk Assessment is available to study via NEBOSH’s global network of Learning Partners. For further information visit: www.nebosh.org.uk/manualhandling
DOOSAN COMPLETES DEMOLITION & MATERIAL HANDLER LINES
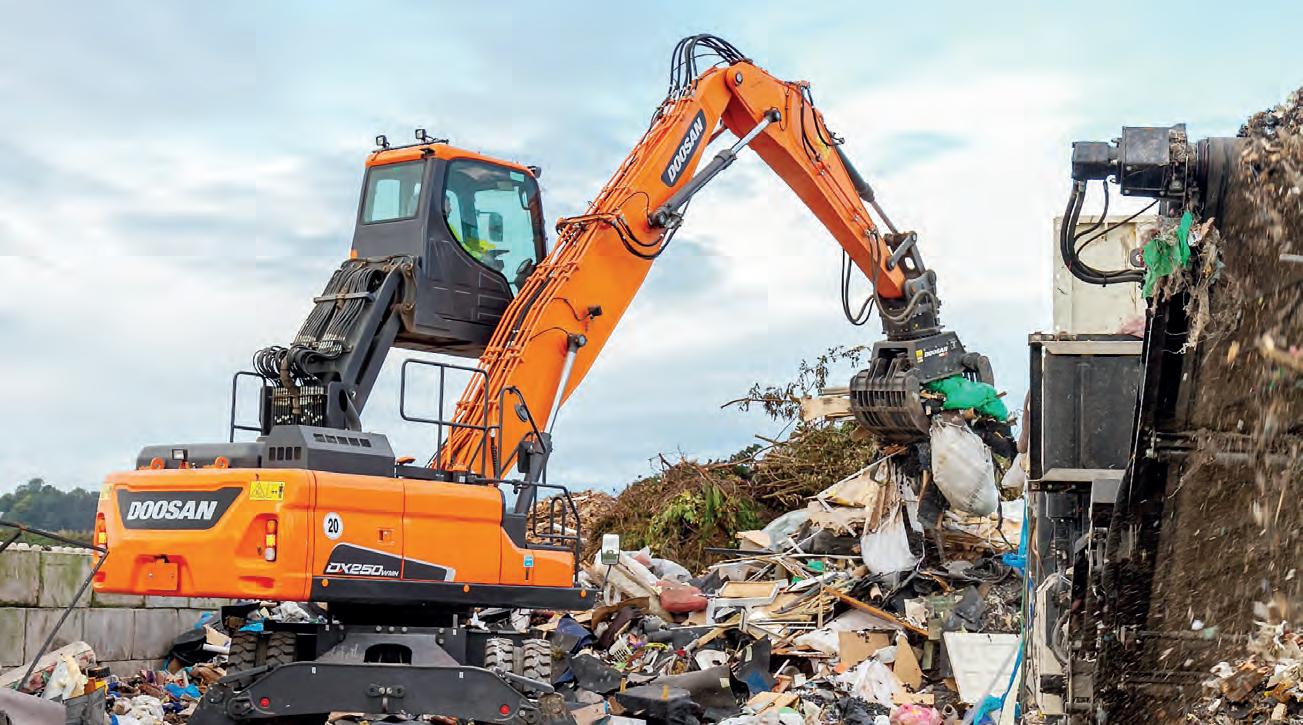
With the arrival of the new DX380DM-7 model, Doosan has completed the company’s range of new High Reach Demolition Excavators. The DX380DM-7 has joined the existing DX235DM-5 and DX530DM-5 demolition models launched in the last two years.
These are complemented by the company’s new range of Material Handler models and together both ranges cover the majority of applications in the demolition, waste and recycling industry. The new Material Handler range now offers three models - the wheeled DX230WMH-5 and DX250WMH-5 and the tracked DX225MH-5 model. In all of Doosan’s demolition excavators, the operator is housed in a high visibility, tiltable cab, providing an excellent environment particularly suited to high reach demolition applications, with a 30 degree tilting angle. All three machines in the High Reach range provide increased flexibility with a modular boom design and hydraulic lock mechanism. This innovative design facilitates an easy change between a demolition boom and an earthmoving boom to accomplish different types of work on the same project, using the same machine. The multi-boom design also allows the earthmoving boom to be mounted in two different ways, which with the demolition boom, provides further flexibility with a total of three different configurations for the same base machine. A special stand is provided to facilitate the boom changing operation, which is based on quick-change hydraulic and mechanical coupler connections. A cylinder-based system is used to push the locking pins into place to help complete the procedure. All three models share a hydraulically adjustable undercarriage, which extends to a maximum width to provide optimum stability when working on demolition sites. The width of the undercarriage can be retracted hydraulically to a narrow width position, for transporting the machines. The adjusting mechanism is based on a permanently lubricated, internal cylinder design which minimises resistance during the movement and helps to prevent damage to the components. On all the Doosan demolition excavators, standard safety features include a FOGS cabin guard, safety valves for the boom, intermediate boom and arm cylinders and a stability warning system. MATERIAL HANDLERS
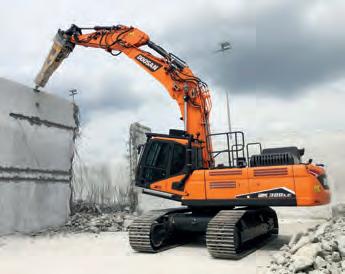
Doosan is now also offering a choice of three different material handler models. The 23 tonne DX230WMH-5 and DX250WMH-5 25 tonne wheeled machines are based on Doosan’s popular DX210W-5 wheeled excavator. The new DX225MH-5 25 tonne crawler model is based on Doosan’s successful DX225LC-5 22 tonne excavator - the crawler type undercarriage is particularly suited for work in difficult ground conditions. All three models have been designed specifically for a wide range of material sorting and handling applications such as those in the scrap metal and other solid waste and recycling industries, as well as demolition, forestry and logging. Designed to carry out the toughest tasks, they are built with front and rear stabilizers, and a boom and arm specifically designed for material handling tasks. A standard feature is the hydraulic cab riser, which gives the operator better all-around visibility of the attachment and work area. When combined with the rearview camera display in the cab, the operator has excellent visibility of the job site.
Berco, a global leader in the manufacturing and supply of undercarriages and components to OEMs, has launched its new Aftermarket Service Line range especially for bulldozers in the construction sector with engine power between 60 kW and 200 kW.
With this new entry, Berco completes its Service Line range designed for the sector, which already includes products for 13, 20 and 30-tonne excavators, introduced at the end of 2020. The construction sector is an increasingly strategic market for Berco, especially since relative expenditure in the industry is forecast to grow by 80% by 2030, driven by a growing world population. This is the context in which the company is playing an increasingly important role in both OE and the Aftermarket, thanks to products which combine high standards of engineering, production and quality control processes along with the financial advantages of low TCO. The Service Line range that Berco is offering for bulldozers includes rollers and lubricated chains designed to cope with intensive use; both products in which the company has extensive expertise. In particular, for 100 kW and 170 kW bulldozer applications – the most widelyused in the construction industry – the chains in the Service Line range have an exclusive, patented link profile design which reduces weight between 6 and 7%, without compromising their wear resistance or structural strength. Production of the Service Line range reflects the high standards of quality in every product from Berco, satisfying customers who are seeking a low TCO to become more competitive – a vital determining factor given that 30% of machinery maintenance costs in the construction sector are attributable to the undercarriage. Every product in the Service Line range provides a lengthy warranty period (up to 2,500 hours under normal operating conditions, in certain geographical regions such as Europe and the Americas), and is highly resistant to abrasion, impact and humidity. Diego Buffoni, Head of Aftermarket at Berco, confirms this point: “I am extremely pleased to see the launch of this new line for bulldozers. It will provide Berco and its dealers with very satisfactory results in terms of new business opportunities, adding to those gained with the launch of our Service Line for excavators. In fact, in the last fiscal year, this contributed to a significant increase in our Aftermarket sales in the construction sector. It demonstrates just how well the Service Line is meeting market demands.” Products from the Service Line range for bulldozers can already be ordered from Berco dealers through the company’s newly launched B2B e-commerce platform: a tool providing advanced product search capabilities and faster order entry. The completion of its Service Line range for the construction sector is a further step forward for Berco in presenting itself as the ‘solution provider’ to its dealers, offering them an increasingly complete product range that will see, in the second half of 2022, the addition of even more new product groups beyond the undercarriage range.

Finning acquires hydraulic services specialist Hydraquip
Finning, authorised dealer of Cat equipment and parts in the UK and Ireland, has acquired Hydraquip, the UK’s largest independent provider of mobile hydraulic services. The move complements the company’s extensive product support offering across key customer industries.
Hydraquip specialises in providing 24/7 nationwide coverage for hose replacement, assembly and fitting, oil replenishment and general hydraulic servicing. With 130 mobile service vans and highly trained technicians, Hydraquip’s rapid response capabilities mean jobs are typically completed within just three hours of the initial customer call - reducing machine downtime and generating significant cost savings and efficiency gains for customers. Tim Ferwerda, Managing Director of Finning UK & Ireland, comments: “The acquisition of Hydraquip demonstrates our commitment to build on and extend our reach to provide exceptional product support and aftermarket services for our customers. The company is a great fit with Finning, in terms of its family-orientated and customer-focused culture, which complements our current product support service perfectly. The Hydraquip brand name will remain in place as we maintain and build upon the high standards of service it is known for. The business has an established footprint with hydraulic hose specialists focused on industries such as construction, transportation, waste management, utilities, manufacturing, and materials handling. With our extensive joint network in the UK and Ireland, customers will find it even easier to reap the benefits of reduced downtime and operating costs. “I’d like to personally welcome all the Hydraquip employees to the Finning family. We’re looking forward to working side by side to ensure our customers benefit from the most responsive and specialist product service support across all our key sectors.” Headquartered in Kent, Hydraquip employs 270 people and serves more than 4,000 customers across a diverse range of industries. Alongside its on-site mobile hose services, the business also sells hydraulic and fluid power products and parts via its website and a network of 27 strategically located branches across the UK. In addition to hydraulic and pneumatic hose products, these branches also carry adjacent inventory of products such as oils and filters. Duncan MacBain, Founder of Hydraquip: “Joining Finning is an extremely exciting move for Hydraquip and will prove a critical step in the continued growth of our offering, enabling Hydraquip to recognise its full potential in the UK and further afield. We can see many cultural similarities as well as tremendous opportunities between the companies to give customers an even stronger proposition. “This is down to the quality and commitment of our team, who will remain focussed on offering our customers the very best service and support levels – now with the added backing of Finning, its network, and broader aftermarket capabilities. Our joint goals and vision remain to continue to build our market share and expand further from being the largest independent provider of mobile hydraulic solutions to the largest provider overall.”
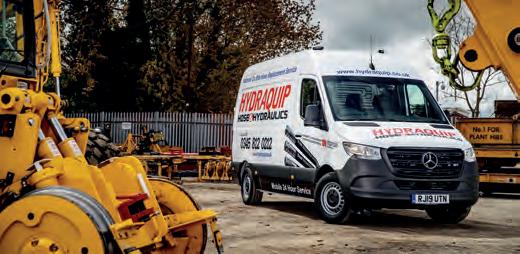
M413 Mobile Track Trommel
MDS INTERNATIONAL ANNOUNCES REBRAND TO BECOME MDS - A TEREX BRAND
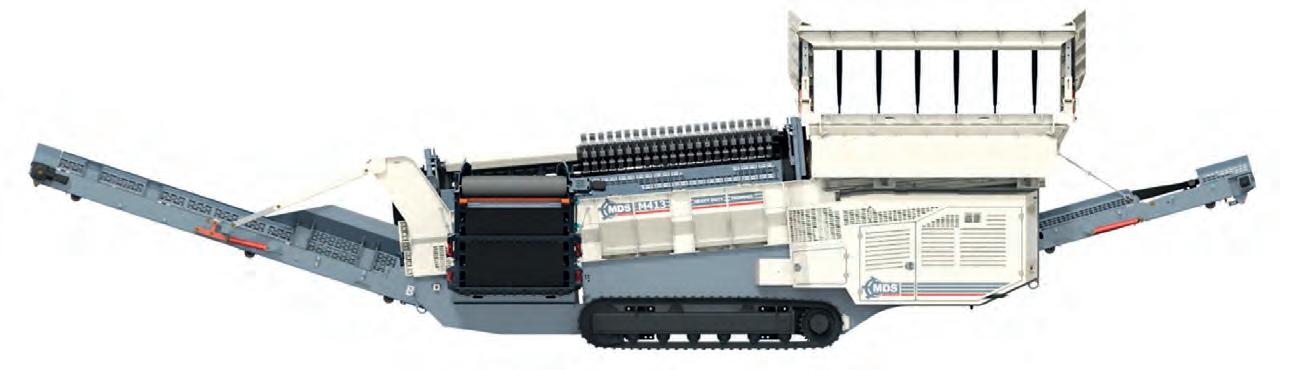
A new look and feel logo will accompany the brands update and is in line with the new direction that the company is going in.
History, as with all Terex Brands, remains a very important part of MDS, the colours used in the new logo represent Terex and the values represented by that part of MDS, but the logo also showcases the MDS heavy duty drums which is the unique feature of MDS products and what we are synonymous with. “MDS is undergoing major positive changes following on from the acquisition by Terex in 2021.We have been making significant investment in our facilities and have added to our team to help us deliver aggressive production growth goals so that we can meet ever growing demand for MDS products. Alongside this, we have been expanding our distribution footprint to help position us for long term growth. “With the positive changes to MDS ongoing, this was the ideal time launch our rebranding. Since the first mobile MDS model was launched in 2015, the branding and livery has remained the same. The new livery will retain the old MDS colour while introducing a Terex grey, giving a modern, two tone effect as well as a consistent look across all our models.” As part of this rebrand, MDS is launching a new website, www. terex.com/mds .This will give users a smoother browsing experience and is consistent with other Terex brands platforms. All of its social handles have also changed to @mds.terex across all its social media channels. “This is an exciting time for MDS and this rebranding allows to continue our upward trajectory. We hope this new look will help strengthen our brand awareness and our unique identity as the leading provider of heavy duty rock trommels.”
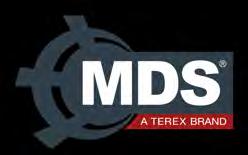
M412 Mobile Track Trommel
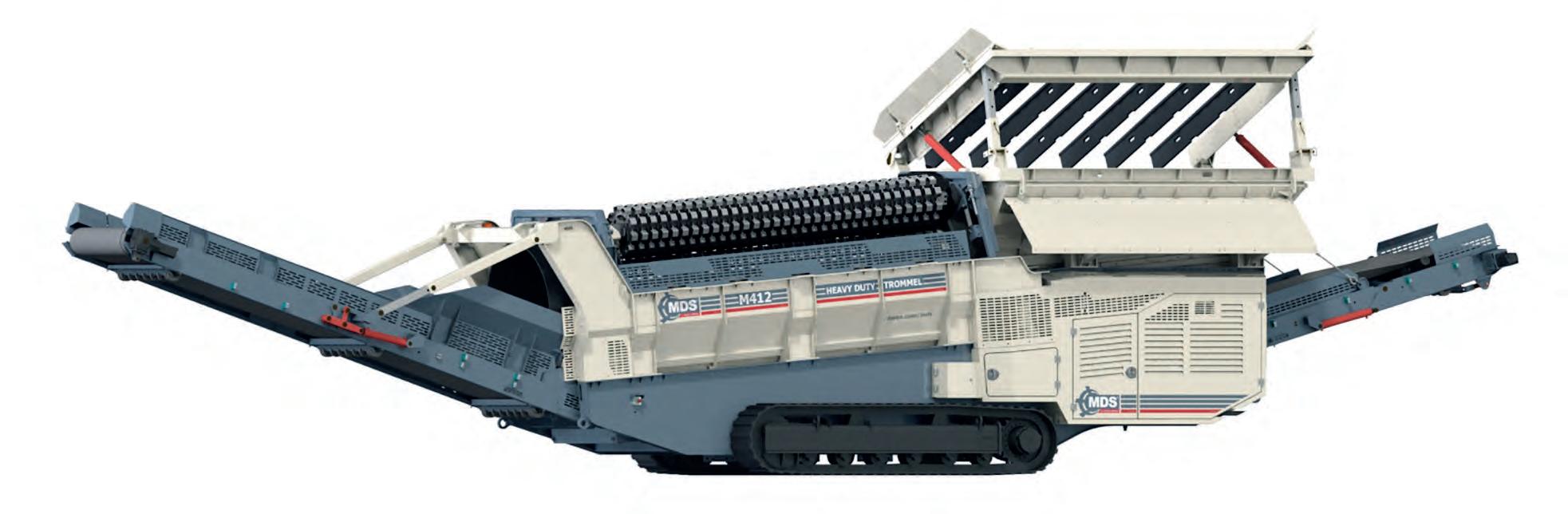