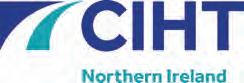
17 minute read
CIHT hold their Annual Gala Dinner
THE CHARTERED INSTITUTION OF HIGHWAYS AND TRANSPORTATION NORTHERN IRELAND BRANCH
ANNUAL DINNER HELD AT THE STORMONT HOTEL, BELFAST

Andrew Murray Former Head DFI, John Hutchinson Institute of Structural Engineers, David Hughes QUB/CIHT, Kaine Lynch CIHT N.I. Chairman, Stephen Orr Institute of Civil Engineers. Collin Barkley Guest Speaker, John McRobert CIHT Past Chairman, Rona McRobert, Deborah Sims CIHT President, Edward Rea Chairman Concrete Society, Kaine Lynch CIHT N.I. Chairman.
Gordon Best MPANI, Lyle Andrew IAT, Edward Rea Chairman Concrete Society, John Hutchinson Institue of Structural Engineers, Kaine Lynch CIHT N.I. Chairman, Micheal Bell CIHT Vice Chairman and Frank Given Engineers Ireland Northern Region.
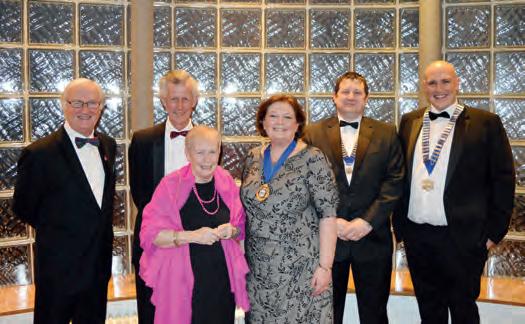

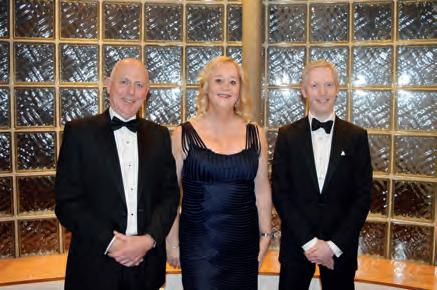
Freddie Patterson CIHT Dinner Secreatry, Kaine Lynch CIHT N.I. Chairman, Bert Bailie CIHT N.I. Council Rep. Andrew Murray Former Head DFI, Karen McShane CIHT, Frank Given Engineers Ireland Northern Region. Duncan McCalister Translink, Louise Doyle Translink and Gordon Best MPANI.
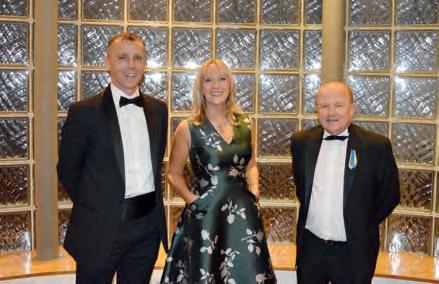
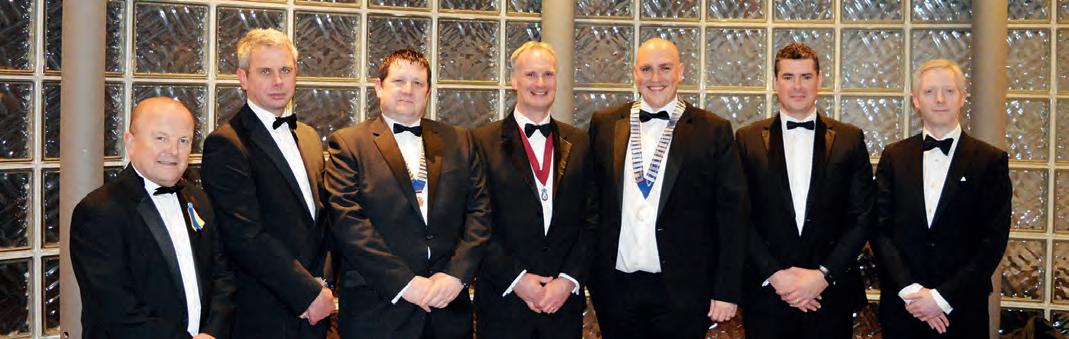

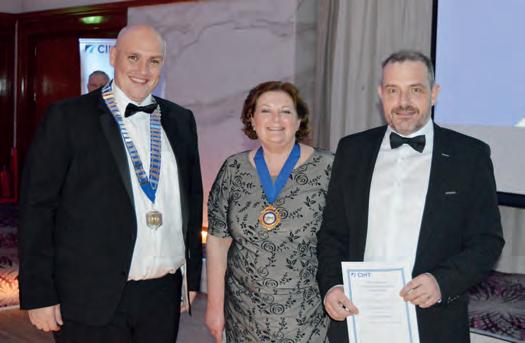
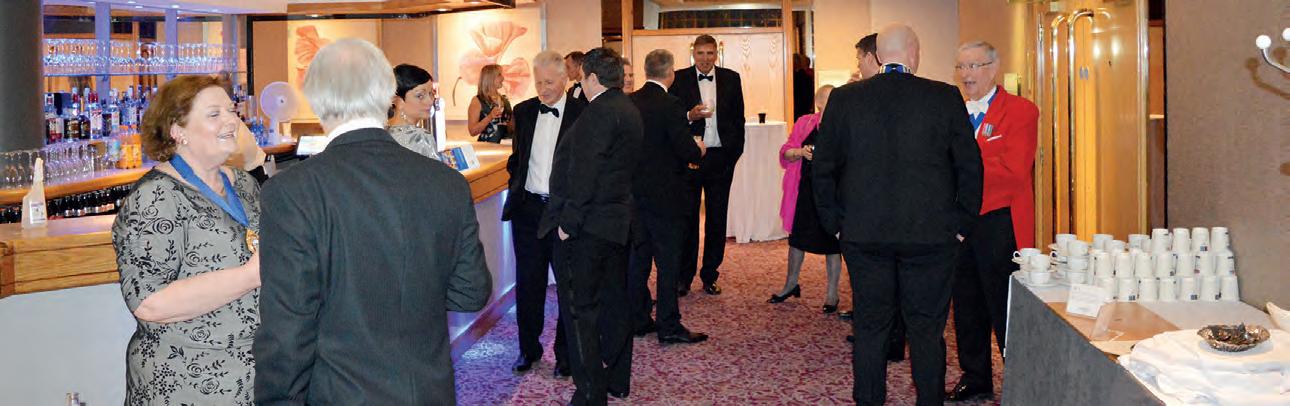
Kaine Lynch CIHT N.I. Chairman, Deborah Sims CIHT President and Dr Andrew Murray CIHT Certificate of Merit Award. Kaine Lynch CIHT N.I. Chairman, Deborah Sims CIHT President and Caldwell CIHT Certificate of Merit Award.

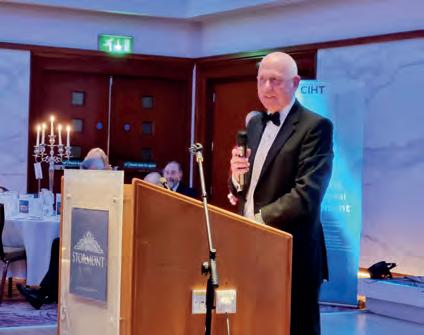
Dr. Andrew Murray speaking at the CIHT Annual dinner. Guest Speaker Collin Barkely entertaining guests at the Annual CIHT Dinner. Deborah Sims, President CIHT speaking at the Annual CIHT dinner at the Stormont Hotel, Belfast.
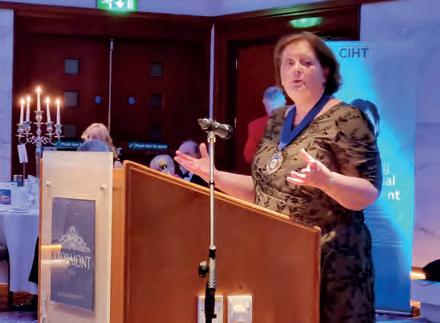
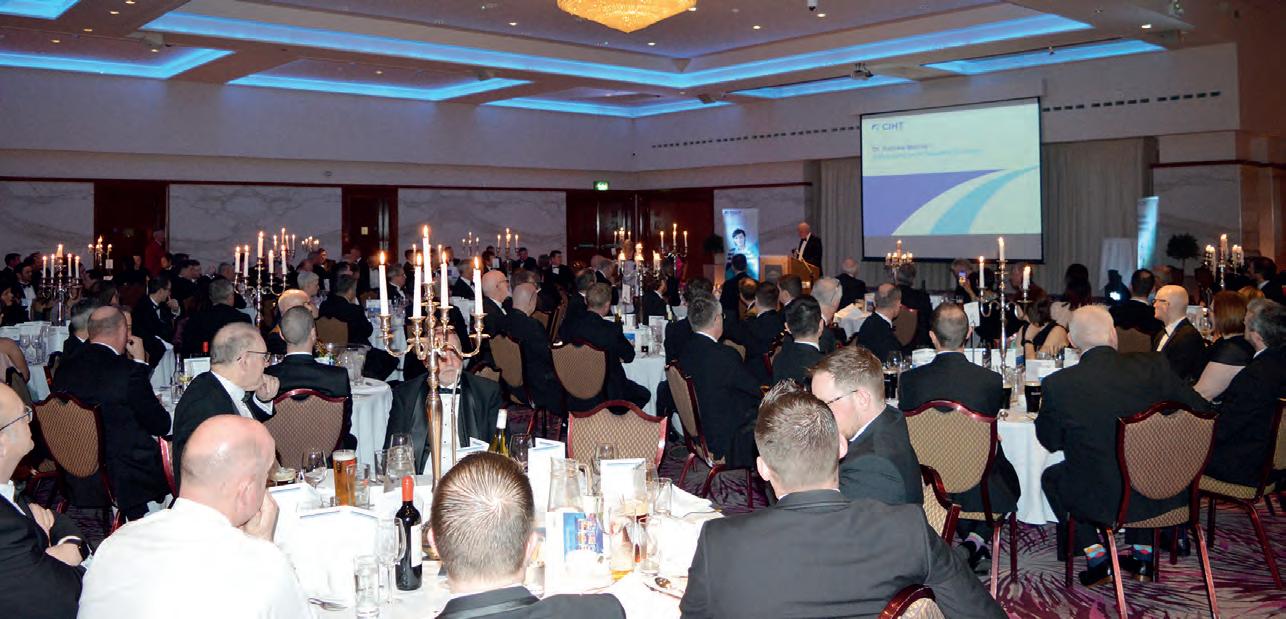
CONTINUED
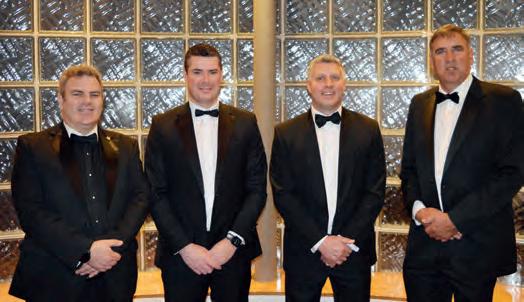
Robert Eadie Ulster University, Michael Bell CIHT, Stephen Bradshaw CIHT and David Hughes QUB/CIHT. Roisin Wilson CIHT N.I. Secretary, Kaine Lynch CIHT N.I. Chairman and Deborah Sims CIHT President.
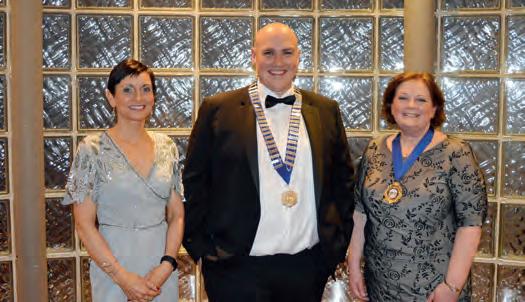
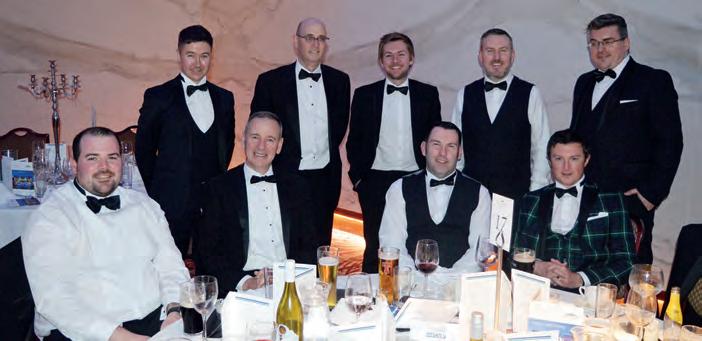

FP McCann Table. Dr. Kaine Lynch Chair, CIHT Northern Ireland speaking at the CIHT Annual Dinner.
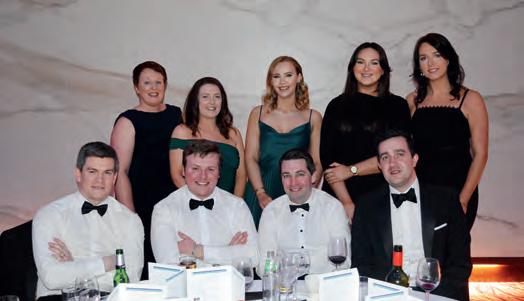
ARUP Table. White Mountian Table.
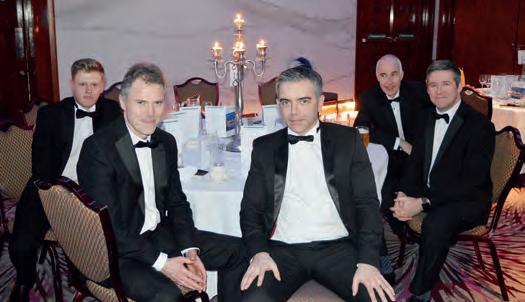
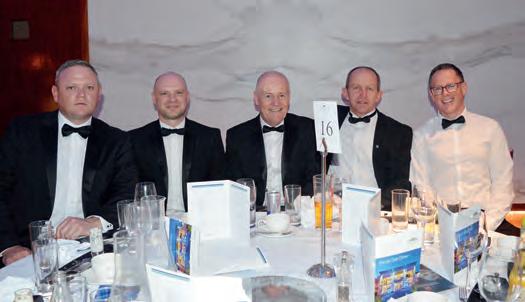
Gibson Brothers Table. Jack Adair Toast Master and Kaine Lynch CIHT N.I. Chairman.
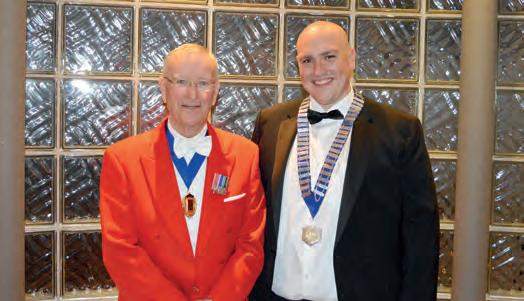
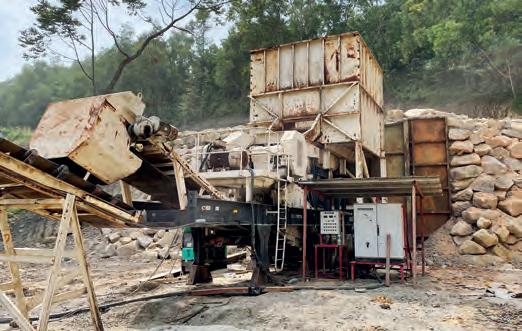
Terex MPS Handles a Large-Scale Relocation Project in Malaysia
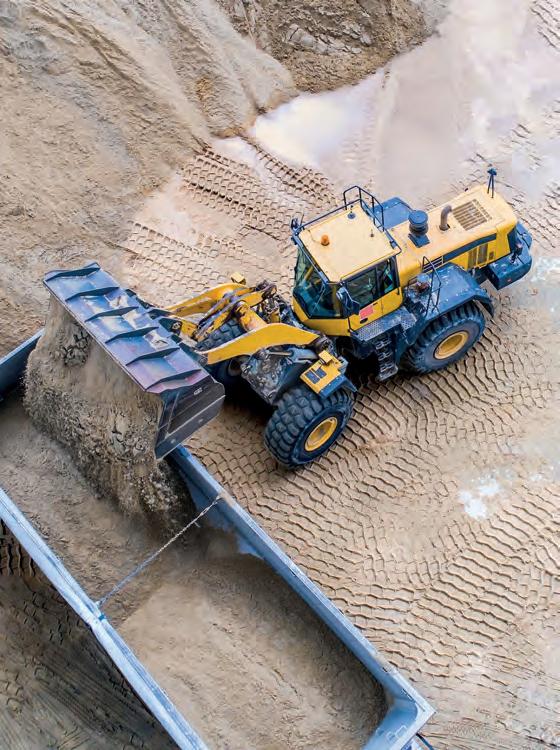
Mount Trusmadi, located in the Trusmadi Forest Reserve, in Sabah, Malaysia, standing at over 2,500 metres above sea level, is the new job site for a Terex MPS crusher along with other Terex equipment.
A recent project for one of its customers involved relocating Terex equipment to this location from over 150km away. The requirement from the customer was that the equipment be moved to this site that needed it post-pandemic. This equipment had been unused for upwards of 2 years. The equipment was the Wheeled Jaw WJ1175, this contained the Primary Jaw Crusher Model Terex JW42, and a Terex Wheeled Cone Model WC1000 containing a Terex TC1000 model Cone Crusher. The machines were relocated successfully, and with ease. The flexibility which is offered with Terex MPS Wheeled Plants was the key factor by which the customer could reuse almost all components from the previous site. This included reusing the 5x14’ IV Decks which were easily attached to the wheeled units in transit. “The versatility of our Wheeled Plant was the main reason that the customer chose Terex originally,” said Benjamin Tong, Regional Sales Manager for Terex MPS. “The IV Decks screen makes it easy for the customer to cope with the market demand for four different aggregate sizes,” he added. The service support provided by the Terex MPS team was also highly appreciated by the customer, which resulted in a quick turnaround of the plant and in turn production. Now sitting at the top of a new site some 150km from the old site, overlooking the beauty and majesty of Mount Trusmadi, the Terex MPS systems are working together as one, once again, after years of sitting idly by. The one-of-a-kind optimisation of the machines, along with their premium quality components has saved the customer time, labour costs and overall relocation costs during a time when the market is at its most challenging.
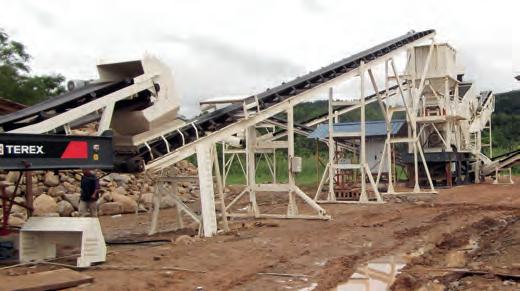
RFID detection system
ZoneSafe uses Radio Frequency Identifi cation (RFID) technology to create detection zones around vehicles and mobile plant.
Vehicle-mounted antennas detect RFID tags which can be worn by workers, or placed on objects or property. When a ZoneSafe tag enters a detection zone, the vehicle operator receives a visual and audible alert. A vibrating tag also warns the detected worker of an approaching vehicle. ZoneSafe RFID technology does not require line-of-sight and tags will be detected regardless of obstructions, blind spots, adverse weather or poor visibility.
01322 420300 brigade-electronics.com
MORE & MORE OPERATORS APPRECIATING MAJOR BENEFITS OF THE HIDROMEK BRAND
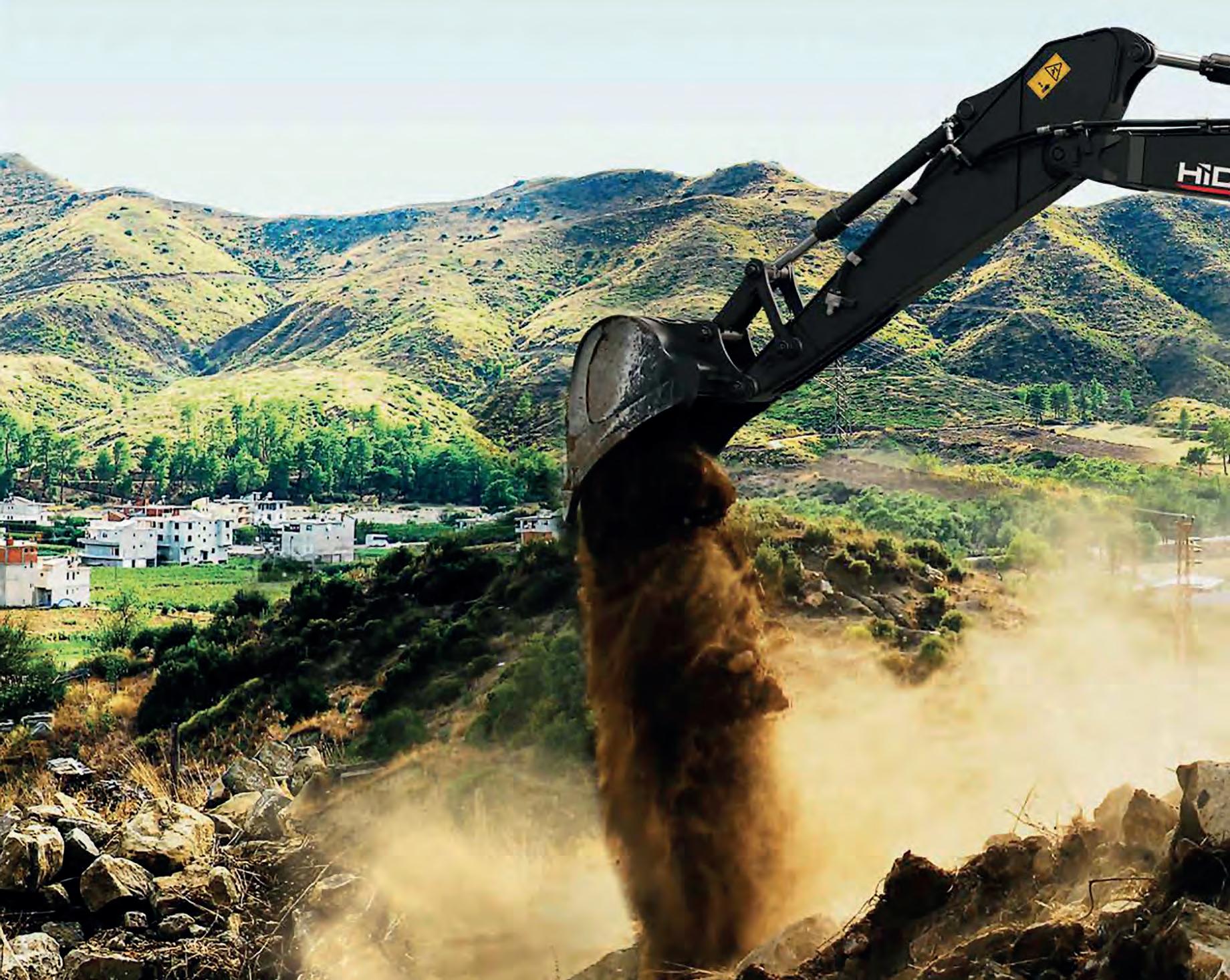
It has been said by some dealers that Hidromek machines ‘sell themselves’ not least because of their excellent build quality, reliability and exceptional fuel economy, with more and more operators across the country discovering major benefits of the brand.
All Hidromek machines feature smooth and efficient hydraulics and spacious and comfortable cabs where all the controls are placed on an operator console integrated into the air suspended heated seat. This console can be moved independently of the seat, allowing the operator to find the best and most comfortable working position - and there’s plenty of space for the operator to store his bits and pieces.
HMK 390LCHD
Take the latest eyecatching heavy duty 42 tonne Hidromek HMK 390LCHD, for example.
It is certainly a big step up in comparison to the earlier 370LC model in the Hidromek range, featuring as it does much smoother and sharper lines and a brand new upgraded, restyled cab that offers an excellent working environment for the operator. This latest generation model also benefits from a relocated switchboard, remodelled travel pedals and levers, high capacity air-conditioning and high-resolution LED backlight colour LCD display. Other features enhancing the operator’s comfort is the versatile and fully adjustable seat designed to enable the operator to work without stress and fatigue for longer hours. The joystick console and seat can move independently so the operator can easily adjust it to the most suitable position for his body structure. The cab is supported by 6 silicon viscose mounts that dampen the effects of noise, shock and vibrations regardless of working conditions of the machine. There’s plenty of storage space, too, for the operator’s bits and pieces, including a cooled storage room, glass holder and a variety of storage pockets. Featuring an Isuzu engine, Kawasaki hydraulic pumps, Nabtesco Japanese slew motor and final drives, all top-quality components, the Hidromek 390LCHD comes with Hidromek’s Opera Control System, an easy to use interface that facilitates communication between the operator and the machine. The operator can easily switch between menus in Opera, change settings, such as hydraulic flow, and check the status of the machine, including pressure, temperature and engine load. The information and warnings on the instrument panel are always easy to see and control, thanks to the positioning of the Opera interface. Other features of the system include automatic powerboost switch-on switch-off, automatic electric power-off and automatic powershift to improve performance – and it also enjoys excellent visibility from the cab, thanks to side and rear cameras, along with the increase in the number of LED headlights, which also significantly improves night vision. Safety is further enhanced with an automatic starting horn, swing warning system and travel warning system.
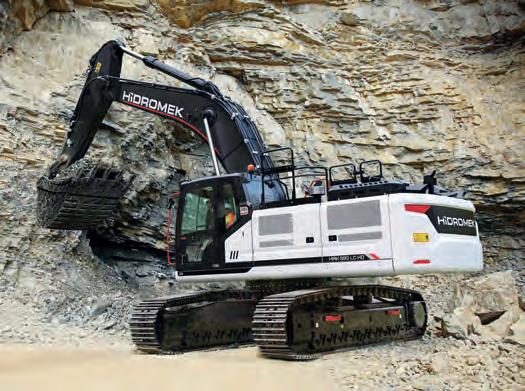
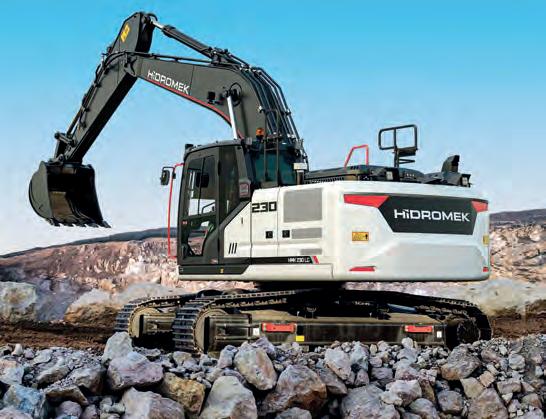
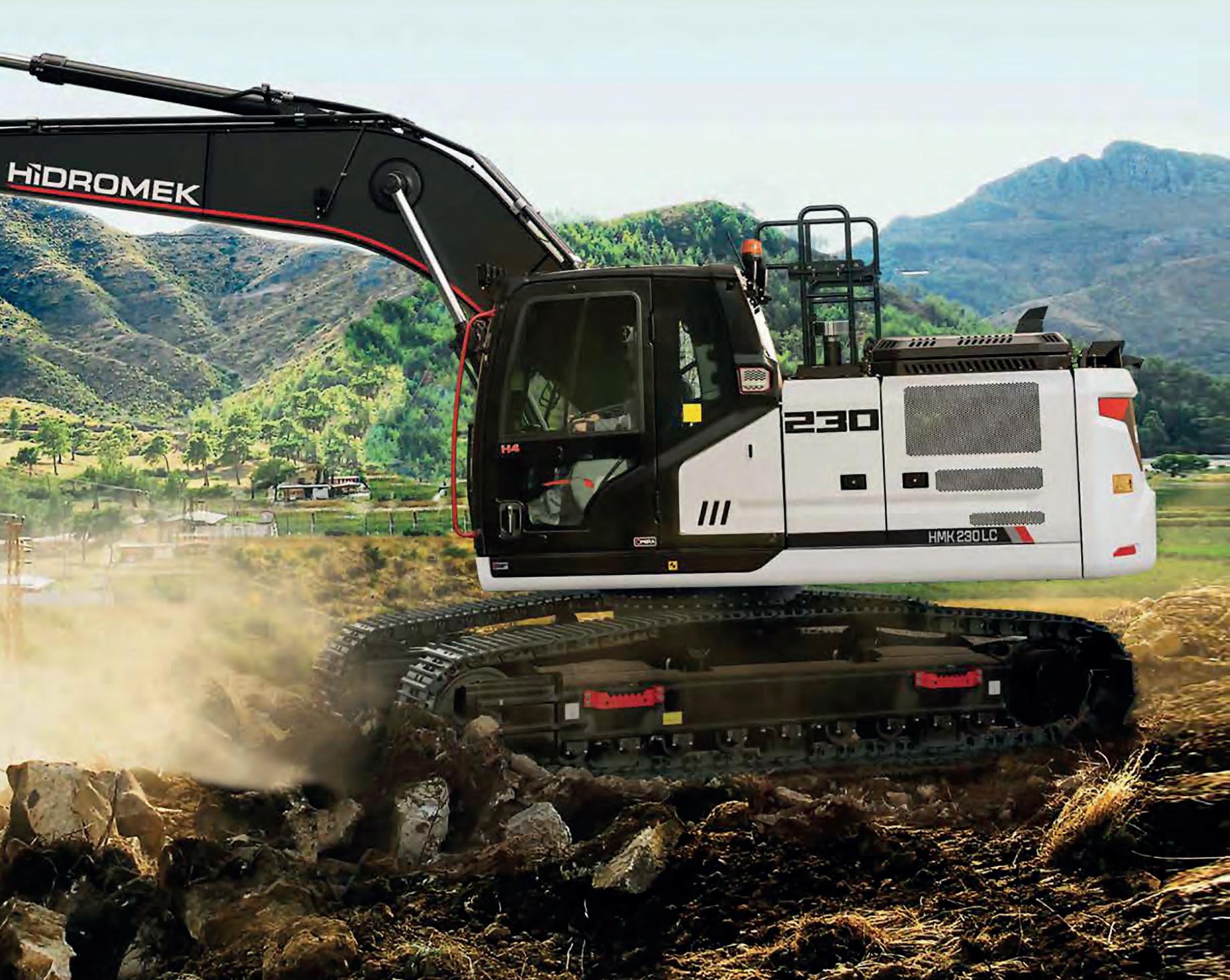
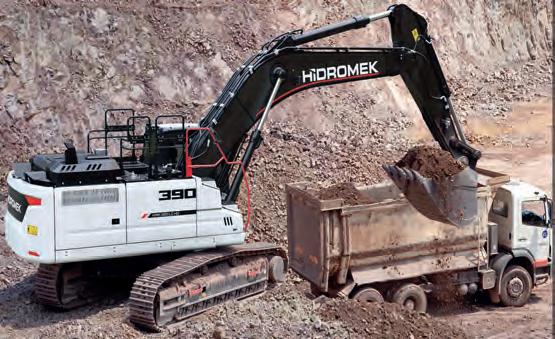
CONTINUES ON NEXT PAGE
HMK 230LC
Meanwhile, the smaller HMK 230 LC crawler excavator at just over 23 tonnes features all the same high quality components, smooth hydraulics and strong build and offers equally outstanding performance by working faster, more productively and more efficiently.
As with all models in the H4 Series, an automatic stop system through configurable idling and stopping times provides fuel saving by stopping the engine after the machine is on idle. The automatic stop system helps to keep operational costs to minimum, and, of course, contributes to saving the environment. Another notable feature is the “safe fuel transfer pump” which stops the pump automatically when the tank is full; this feature gets activated also when the pump does not transfer fuel for 30 seconds, and ensures that the pump stops automatically. The HMK 230LC also has an 8 inch touch control panel which is positioned ergonomically at a point that the operator can easily control the machine’s features. The touch control panel which includes an integrated music system allows the operator to adjust the flow required for the attachment without leaving the cab and save this information for 20 different attachments. It also gives access to information on the average and instant fuel consumption, as well as information on status such as atmospheric pressure, turbo boost pressure, fuel pressure and hydraulic pump pressure. As with the HMK 390LCHD, it is equipped with the Opera Control System enabling the operator to use the machine easily, and feel comfortable and relaxed as if he was in an office environment.
CONTINUED
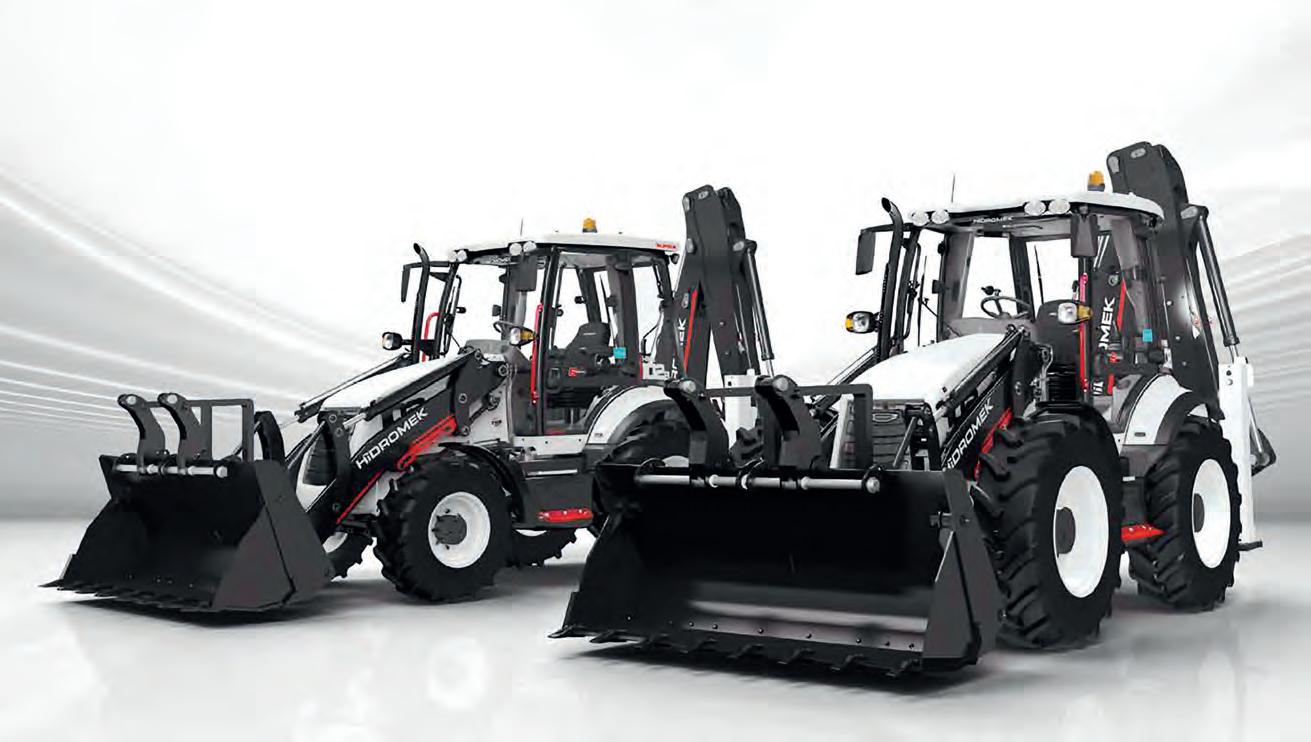
HMK 102B SUPRA
The system is also featured in the HMK 102B SUPRA backhoe loader, powered by a Perkins diesel engine, one of the most economical and durable in its class. The turbocharged engine maintains high torque even at low rpms, while the 6-forward 3-reverse fully automatic transmission used in the SUPRA Series allows smooth driving.
In conventional backhoe loader cabs, while the operator is controlling the machine in the loading and excavation position, he has to turn his head by 90° to the right and left side in order to check the gauges, but in the SUPRA he can easily check these on the LCD screen while he is sitting in the loading and excavation position, without taking his eyes off the driving direction. This working position allows operator to work for longer periods without suffering from neck and back aches. In addition, forward-reverse direction control on the front loader control lever allows the operator to make quicker manoeuvres during the loading process; he can apply both loader and forward-reverse commands from a single point without losing steering wheel handling by using the TIPSHIFT button. The machine’s ROPS/FOPS certified cab is designed for space and operator comfort, and comes equipped with an air suspension seat, cool box, and heating and air-conditioning. www.hidromek.com
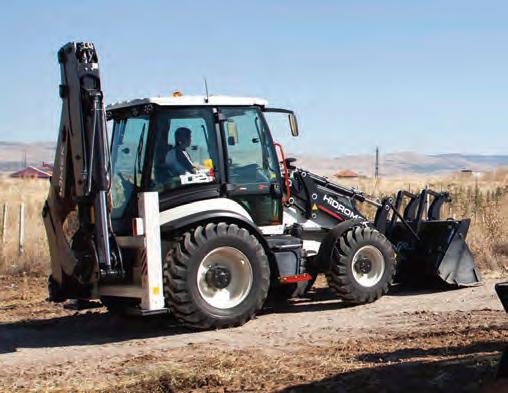

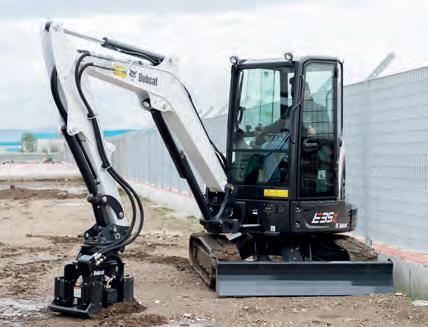
MINI EXCAVATORS UNDERGO REVOLUTION IN DESIGN & APPLICATION
In recent years, mini-excavators have developed into real Tool Carriers. This is thanks to the application of new technology and improved machine stability due to new designs and a better centre of gravity.
As the attachment revolution continues apace, what are some of the new innovations that have come to market in recent years in the excavator attachment space? We’ve been asking Daniele Paciotti, Europe, Middle East and Africa Product Line Director Attachments at Bobcat At Bobcat attachments, we are always working on new solutions to meet the needs of MEX customers. For example, we have recently put more focus on developing our Depth Check and laser system to support the operator in completing trenching works and to make jobs more efficient. As a result, Bobcat is proud to announce the addition of the updated Depth Check System to our portfolio. This system is a solution that uses three sensors placed strategically on the machine to accurately achieve or sustain the desired grade depth, working from the cab. The Depth Check system is fully integrated with the Bobcat panels and display, which offers simple operation and eliminates the need for an add-on Monitor inside the Cab. This simple, durable kit is wired in, so job conditions or the lack of a wireless signal never interfere with digging accuracy, and also remove the inconvenience of lag time with no batteries to replace. The Bobcat Depth Check System is also compatible with the laser receiver, so the operator can ‘bench’ on a laser signal to create slope, or to sustain a grade in multiple locations on a jobsite, which increases flexibility. Bobcat is also offering new Flail Mower and Plate Compactor attachments for MEX. The flail mower has a number of unique features on the market such as the 12 second drum stop after the power is switched off, no need to drain lines as this is integrated in the attachments, a self-levelling system for following the ground surface as a standard feature and the best balanced motor design in order to cut the grass while travelling. The compaction plate attachment is a great tool to maximize compaction, even where workers cannot go with classic compaction plates, thanks to the great reach of the mini-excavator in all these conditions. Bobcat will continue to bring to the market more attachment solutions to make the MiniExcavator even more of a real Tool Carrier.
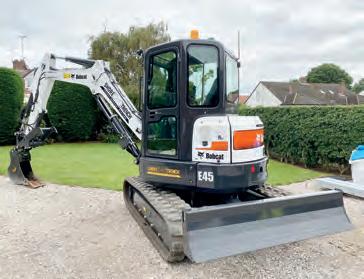
WHAT ARE SOME OF THE MARKET NEEDS ADDRESSED BY THESE ATTACHMENTS?
Compact Excavator customers want to work efficiently, with the same solutions as those on the bigger excavators and with easy to use solutions.
THERE HAVE ALSO BEEN MAJOR ADVANCES IN COUPLING TECHNOLOGY. WHAT ARE SOME OF THE DEVELOPMENTS YOU HAVE SEEN IN THIS SPACE?
The coupling technology is not moving as fast as machine or attachment technology but is concentrated more and more on safety features, to make the jobsite safer and to avoid any kind of potential accident. One development I see expanding in this area is in hydraulic quick solutions, to reduce spending time in connecting hoses every time you change the attachments and to avoid wasting time getting in and out of the cab. WHICH ATTACHMENTS ARE SEEING INCREASED DEMAND IN THE MARKET AT THIS STAGE AND WHY?
The commodity attachments are always the most requested like buckets and couplers or Breakers, probably because the construction and demolition industry is growing thanks to government subsidies but we also see growth in Hydraulic Clamps, flail mowers and augers due to growth in cleaning and landscaping work.
WHAT ARE SOME OF THE INNOVATIONS WE ARE LIKELY TO SEE IN THIS AREA IN THE NEXT FEW YEARS?
Our Attachments team will follow the Market trends and will create solutions to meet these requirements. I’m sure the biggest innovations will come because of three fundamental things: automation, digitalization and recognition. At Bobcat we are working hard on our Long-Range plan to bring the easiest to use and more integrated solutions to the market. Our aim is to make life for the customer as easy and efficient as possible.
news Latest Cat D1 Mulcher features sloped hood styling to improve visibility
Complete with its highperformance powertrain, closed-loop hydraulics and upgraded screening, the new Cat® D1 Mulcher is specially designed to optimize performance when clearing a mix of small- to medium-diameter materials.
Design-matched with the rugged Cat HM518 Mulcher, the D1 Mulcher clears a 188.2 cm (72 in) wide strip on each pass, making it the right machine for right-of-way construction and maintenance, site development, tree management and firebreak clearing. The new mulcher is powered by the 77.6 kW (104 hp) Cat C3.6 Diesel Engine meeting U.S. EPA Tier 4 Final/EU Stage V emission standards. An alternate emissions package for the C3.6 is available to meet Tier 3-equivalent standards. The machine’s lower sloping hood line improves visibility to the mulching head, allowing the operator to better assess the jobsite from the cab. Standard auto reversing fan purges debris from the radiator and enclosures, plus the hinged grill requires no tools to access the radiator for cleaning. Isolating machine vibration from the operator to reduce fatigue, the Cat HM518 Mulcher controls are mounted on the air-suspension seat. Inside the pressurized, heated and airconditioned cab, an intuitive operator interface features a 25.4 cm (10 in) color touchscreen monitor with standard reversing camera display to help improve all-around visibility to the jobsite. An in-cab drum indicator offers quick glance of drum speed and direction to help the operator manage ground speed and mulching productivity. Featuring cladding material in high-wear areas, the new HM518 Mulcher frame offers increased service life. Bolt-on wear plates deliver long wear life and are quickly replaced. Offering a drum speed range of 2,150 to 2,450 rpm, the drum’s 38 fixed teeth feature a single-bolt carbide tooth retention design for simple replacement. Its closed-loop hydraulic circuit includes loadsensing hydraulics to prevent rotor damage when hitting an obstruction. The HM518 Mulcher has a 78.7 cm (31 in) maximum lift height, 36.8 cm (14.5 in) maximum tilt and 25-degree maximum angle to either side. Standard sweeps, screens, windows plus rear guard help to protect both the operator and machine when mulching. With its specially designed tractor platform, the D1 Mulcher is balanced and rugged to increase efficiency when operating in challenging applications. Contractors can choose between the conventional (XL) or low-ground-pressure (LGP) undercarriage design, offering 40.4 cm (16 in) or 63.5 cm (25 in) track shoe widths respectively, to increase flexibility and efficiency for working in soft underfoot conditions, on slopes and in rough terrain. To increase machine versatility, the new D1 Mulcher can be equipped with an optional variable-pitch/angle/ tilt (VPAT) blade in XL, LGP or Intermediate configuration.
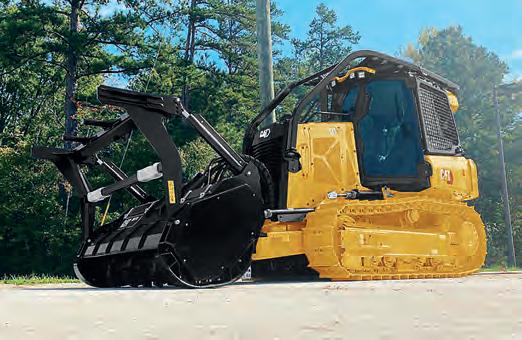
John Deere 8R 410 now available with eAutoPowr
The world’s first electric infinitely variable transmission with electromechanical power split is now an option for the top of the range 8R 410 and is available for all three machine forms – 8R wheeled, 8RT and 8RX.This is a significant step in John Deere’s journey towards electrification which has been developed in partnership with Joskin.
The entirely new transmission concept, inclusive of an e-port for implements, was awarded a gold medal at AGRITECHNICA2019 by the DLG (the German Agricultural Society). After many years of research and development in the space of electrification, John Deere has now found a highly durable solution offering an infinitely variable transmission in the horsepower class above 400hp. Not only does it have increased durability, but it also positively impacts the overall performance. For the new eAutoPowr, John Deere has completely replaced the hydraulic components with an electric power path.The two brushless electric motors are virtually wear-free and powertrain durability exceeds any other concepts previously offered in the industry. Moreover, this simplifies the design of the transmission and allows real time remote technical diagnosis. The electric drive is designed in such a way that it not only supplies the drive, but also provides up to 100kW of electrical power for external implements via 480V variablefrequency three-phase alternating current (AC). A first application has been developed by John Deere together with Joskin. In combination with the Joskin axle drive, two axles of the slurry tanker are driven electrically and thus the weight of the tanker is utilised for traction. This means increased traction, less slippage and precise tracking. The tractor can perform at optimum with less ballast or further increase productivity by having the ability to operate wider implements with the same tractor. With the help of the e-Drive, the electric drive is activated to prevent any wheel slip from occurring. The slip limit can be set by the driver. This allows the system to support the tractor permanently or only in certain situations, for example, when going uphill. In addition to the technical innovations, driving comfort is not neglected. In the already very quiet driver’s cabin, the noise level is reduced even further. The driver also benefits from the fine speed control and improved acceleration. Since speeds of up to 5 km/h are driven completely electrically, a fast and very smooth transition is possible.
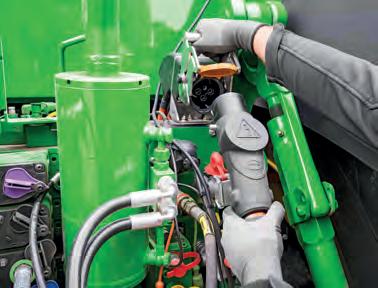