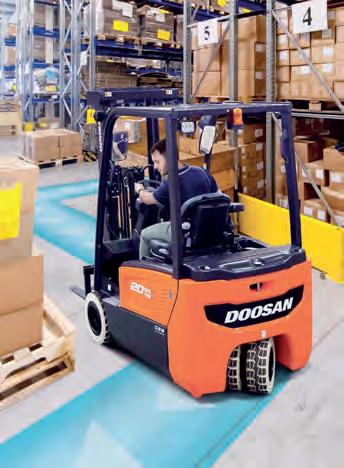
27 minute read
Compact Equipment
DOOSAN UPGRADES ITS POPULAR ELECTRIC BT/BX 7 PLUS SERIES
Designed to deliver simple, powerful performance in even the harshest of operating environments, Doosan’s BT/BX 7 Plus models have now been upgraded, resulting in enhanced braking, reduced noise levels, greater cooling performance, and extra driving comfort.
Further advantages include more efficient ergonomics, new safety features as standard – plus greater choice on options – and improved waterproofing for better all-weather performance and reliability. Safety has been stepped-up a gear with Doosan’s all-round braking system, which includes the Doosan Electric magnetic auto Parking Brake (EPB) and Electric Foot Brake (EFB) systems, together with an unlimited ramp-hold capability. With the EPB system the parking brake automatically activates when the driver leaves the seat, ensuring safety around the vehicle, and with the new EFB system brakes are automatically applied as soon as the operator’s foot lifts off the accelerator pedal. In the cab, clever design features, greater driver comfort and well thought-out ergonomics go hand-in-hand with safer working. The new improved mast design significantly reduces mast oscillation, which allows the operator to safely maneuver when the mast is fully elevated. In addition, Doosan’s optional Guardian Stability System (GSS)ensures safe handling by automatically reducing travel speed as a load is elevated. Further safety improvements include a newly designed overhead guard with angled roof bars for a clearer upward view, a large panoramic mirror for better rear visibility and a new fence-light feature that offers a warning to pedestrians by projecting red lines around the vehicle. In addition, optional front and rear safety lights are available for extra visibility.
Greater comfort
Operator comfort has been significantly upgraded with the introduction of a new Doosan low-vibration, shock-absorbing seat, with full suspension adjustable up to 150 kg and far greater armrest control. Noise levels have been markedly improved too. The combination of a low-noise drive axle and a new sound suppression design has resulted in a 37% reduction in sound intensity compared to the previous model, creating a far more comfortable working environment for both driver and those working close by. In keeping with Doosan’s reputation for rugged design and reliable performance, the latest models have improved waterproofing, offering protection against water and dirt in the harshest of outdoor applications, whatever the weather. All connectors are water protected to IP67, controllers sealed and rated to IP65 and motors and pumps offer full dust and water protection to IP43 rating. Electric motor cooling performance has been improved too, with a new centralised cooling fan. Doosan’s new, improved curve speed control system automatically reduces the vehicle’s travel speed to an optimum level when cornering, reducing the risk of accidents and damage – allowing operators to perform everyday handling tasks with greater confidence. Further efficiency gains can be achieved in battery changing operations, with Side Lift In and Lift Out and Side Roll In and Roll Out design, allowing fast changeover of batteries for multi-shift operations. Helping to reduce valuable warehouse space, a tighter turning radius on the new BT/ BX 7 Plus models offer businesses the potential to move to a more compact racking layout, with narrower aisle widths.
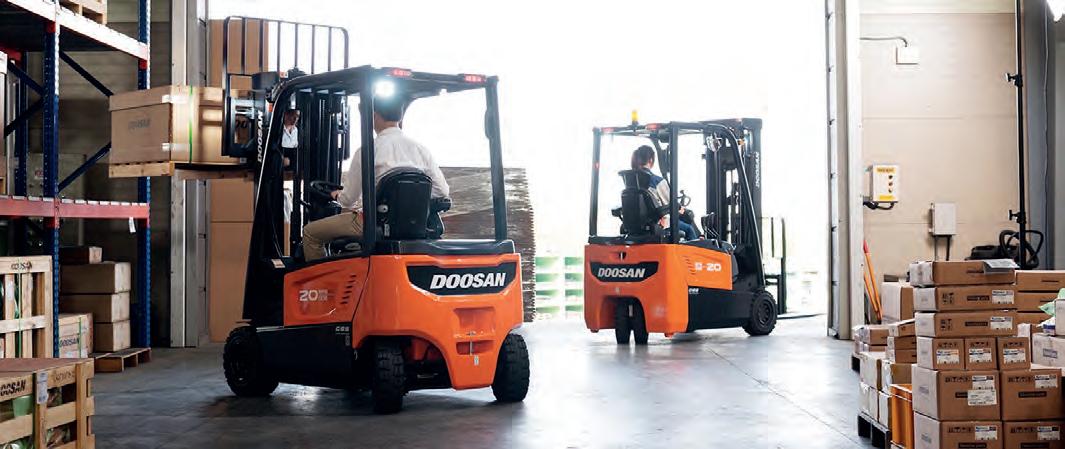
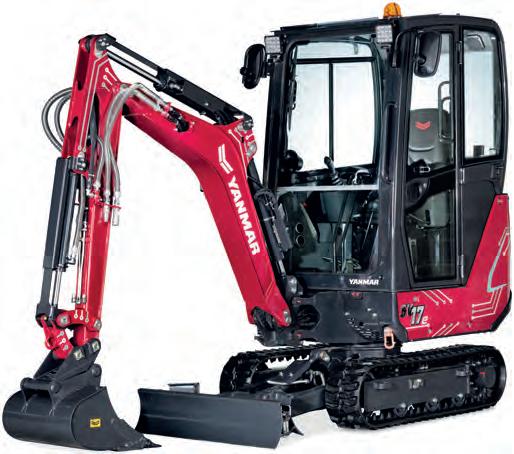
Yanmar Compact Equipment has a long and well-deserved reputation for delivering fuel efficient and sustainable engine technology. Now, the company brings its engine and mini excavator expertise into the field of electrification with its first electric mini excavator prototype: the new SV17e. This innovation represents an important strategic step for Yanmar Compact Equipment.
“Our aim, together with our dealer partners, is to build stronger relationships and create even greater customer value,” said CEO Giuliano Parodi. “Our transformation will embrace our entire business and will encompass new products with alternative fuel technologies. The SV17e prototype is a clear demonstration of our intent to build a sustainable business for our customers and dealer partners.” The SV17e is a mini excavator aimed at customers in the European market and plays in the 1.5 to 2.0 tonnes segment. Powered by efficient electric drive and 48-volt batteries with fast charging capability, it’s a quiet, zero-emissions machine designed to meet the most demanding emissions restrictions. In-line with Yanmar Compact Equipment’s commitment to creating an exceptional customer experience, the appeal of the SV17e goes beyond simply being an electric machine. The design and engineering team have set out to build a machine which offers the highest levels of comfort, ergonomics and operational power, precision, and control. “Our prototype is significant because it demonstrates our capability to bring the quality and reliability of our highly respected conventional engine technology into the arena of electrification,” explained Product Management Director EMEA, Cedric Durand. “But we have gone further. As always, the operator is at the heart of this machine, and we have challenged ourselves to deliver the comfort, power, control and precision which we believe will surpass the expectations of professional operators.” In preparation for its sales start at Bauma 2022, the prototype SV17e is currently undergoing Yanmar’s vigorous product testing regime. These tough field tests are uncompromising in their thoroughness to ensure an uncompromising level of durability and reliability in the design and engineering. According to Director Engineering EMEA, Sota Takami: “We are very pleased with the performance to date – as you would expect, we have a rigorous testing regime which pushes every aspect of the machine to its limit. The machine has performed very well in all these tests. We are particularly pleased with the power, and control of the machine. Of course, this is a quiet, zero emission machine but that, in itself, is not enough. We must create a great feeling for the operator. I am confident that professional operators will be very comfortable in this machine, they will certainly feel the power, control and the precision handling they will need to take on the big jobs as well as the small jobs.” For those who cannot wait until Bauma 2022 to see the new SV17e in action, Yanmar Compact Equipment has prepared a short teaser film. Emphasising the power, control and precision of the new machine, this short film proves that even the smallest jobs deserve Yanmar’s innovation. Video link : https:// youtu.be/zqAxhGZT3Kg
KOMATSU SAYS SHORT TAIL SWING DIGGERS AN IDEA WAITING TO BE INVENTED

Until it first burst upon the scene, the short tail swing excavator was an idea waiting to be invented.
With services and utilities providers now locating an increasing number of pipes, conduits and cables underground, need for equipment that can operate safely in busy urban settings has pushed up demand for these mighty street-size digging machines. This fact is confirmed by Komatsu distributor McHale Plant Sales whose order books show how interest in these attractively designed and cleverly counterbalanced machines has continued to increase. Leading Komatsu model on the market here is the PC138US-11 whose compact swing radius makes it ideal for safe working in confined spaces. Fronting a model series that McHale Plant Sales director, John O’Brien says is “one of Ireland’s best-selling excavators”, the PC138US-11 is powered by a 93.5hp (69.7kW) EU Stage IV emissionscertified and more environmentallyfriendly Komatsu SAA4D95LE engine. Its lower daily operating costs and fuel consumption without loss of performance are two of the beneficial spin-offs when compared to the version it replaces. Operational safety is enhanced thanks to Komatsu’s Komvision system (optional) which gives the operator a 360 degrees bird’s eye view of the jobsite surroundings. Projected on to a standard 7” LCD widescreen monitor within the cabin, it gives the operator notice of possible perils before commencing work – especially useful in urban environments where pedestrian and traffic volumes are high and the risk of accidental injury is ever present.
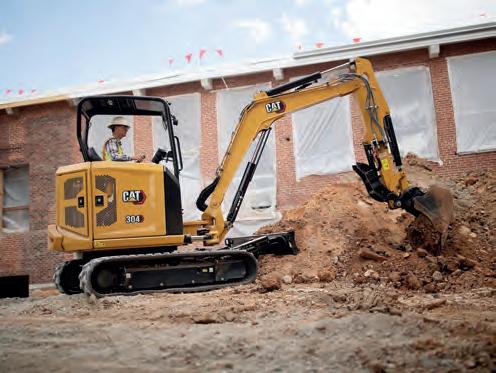

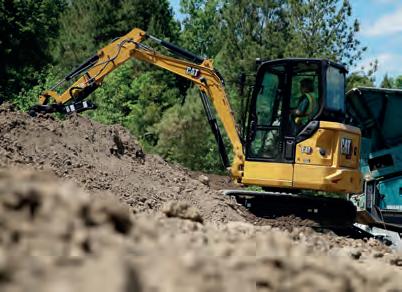
Built to deliver an improved customer experience, the new 4-tonne, Cat 304, and 5-tonne, Cat 305 CR, Next Generation Mini Hydraulic Excavators are said to deliver more power to the pumps, higher bucket breakout forces and deeper standard digging depths to increase performance by up to 20% over their E2 series counterparts.
In addition, their industry-leading grease intervals and extended filter service life, combined with common components throughout the line and flat, easy-toreplace side panels, deliver up to 10% lower owner and operating costs. The new 304 and 305 CR models are the final machines to be reengineered to the Cat next generation mini hydraulic excavator line concept. From the 1.5- to 10-tonne class models, all 17 – 20 Cat mini hydraulic excavators in the range (depending on region) offer common features and consistent controls layout to simplify training and operator adaptation. Built with a new reduced radius design, the 304 features a narrow, 1700-mm (66.9in) track width, 254 mm (10 in) slimmer than the 304 E2, for more versatility and access to confined spaces. While narrower, the new 304 design increases performance, balance and stability of the 4-tonne class model. Its reduced radius allows for greater stability, both 360-degree and when traveling with loads, while its extra counterweight option takes the model to an even higher level of stability.
Compact performance
The new engine on the 5-tonne class Cat 305 CR Excavator delivers nearly 9% greater power to increase machine performance. Hydraulic system improvements provide higher breakout forces – 49.2 kN (11,061 lbf) bucket, 28.3 kN (6,362 lbf) standard stick and 25.2 kN (5,665 lbf) long stick – to improve digging efficiency in hard rock applications. It also offers 140 mm (5.6 in) deeper dig depths than the 305 E2, giving it more application flexibility. Its compact radius swing reduces overhang when working to the side, while its 1980-mm (78in) track width and new extra counterweight option help to optimize stability and lift performance in confined spaces.
Advanced Efficiency
Both excavator models now offer an angle dozer blade option to optimize machine flexibility in backfilling and finish grading applications. In addition to offering ample above- and below-grade travel with standard float function for easy clean-up, the angle blade moves 45 degrees left or right of center. Increasing efficiencies and reducing operator interaction with final grading, angle blade movement is controlled by the right-hand joystick, while the left joystick handles machine drive. Tailoring machine weight to job requirements, interchangeable counterweight packages offer the balance between low ground pressure and lifting

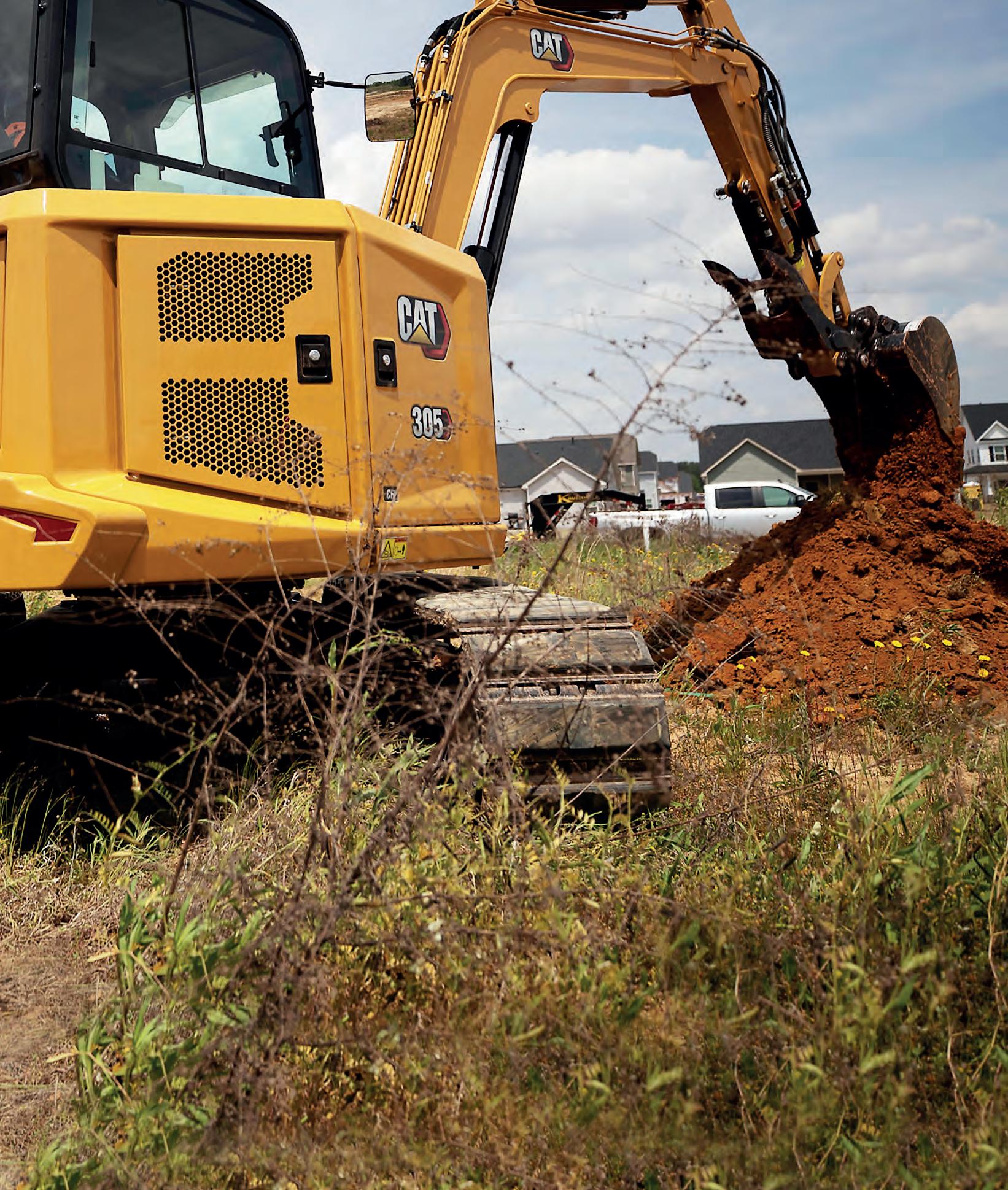
performance. Their industry-exclusive Cat Stick Steer System simplifies machine control by allowing the operator to switch from conventional lever/foot-pedal steering controls to low-effort joystick operation. Two travel speed ranges and standard cruise control facilitate moving around the jobsite with minimum operator interaction. Meeting U.S. EPA Tier 4 Final and EU Stage V emission standards, the turbocharged Cat C1.7 Turbo engine delivers higher power than the previous C2.4 engine. Standard auto idle, auto engine shutdown and efficient load-sensing hydraulics with variable displacement pump help to lower fuel usage at the site for more affordable operation. High main-relief pressures, coupled with flow rates, generates the hydraulic capacity for high digging and lifting forces and more efficient use of a range of attachments. Complete with quick-disconnect lines, the standard auxiliary system provides the choice of one-way, two-way or continuous flow.
Comfort & Savings
Common to most Cat next generation mini hydraulic excavators, the sealed and pressurized cab enclosure is available with heating and/or air conditioning for all-weather climate control. The cab’s large glass areas plus skylight afford all-around visibility. The large display with advanced touchscreen option provides intuitive machine function control and easy monitoring of critical operating parameters. A canopy option is available in some regions. Daily maintenance checks for the 304 and 305 CR are quickly made from ground level through side doors. Expanded use of common parts throughout the line, plus their damage-resistant exterior construction, helps to reduce parts inventory investment and lower repair costs. Increased service intervals mean these excavators spend more time on the job and less time in the shop.

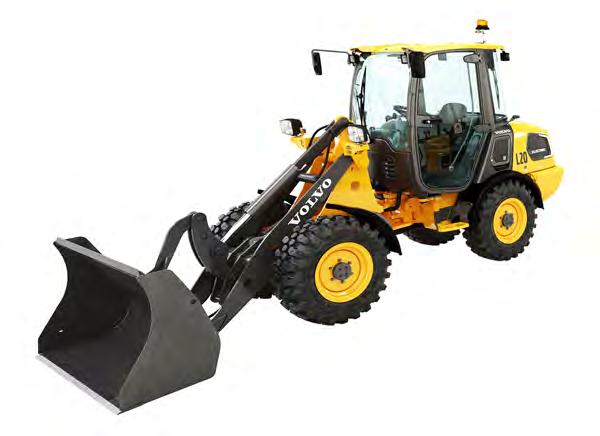
VOLVO CE POWERS A SUSTAINABLE FUTURE WITH LARGEST RANGE OF ELECTRIC MACHINES
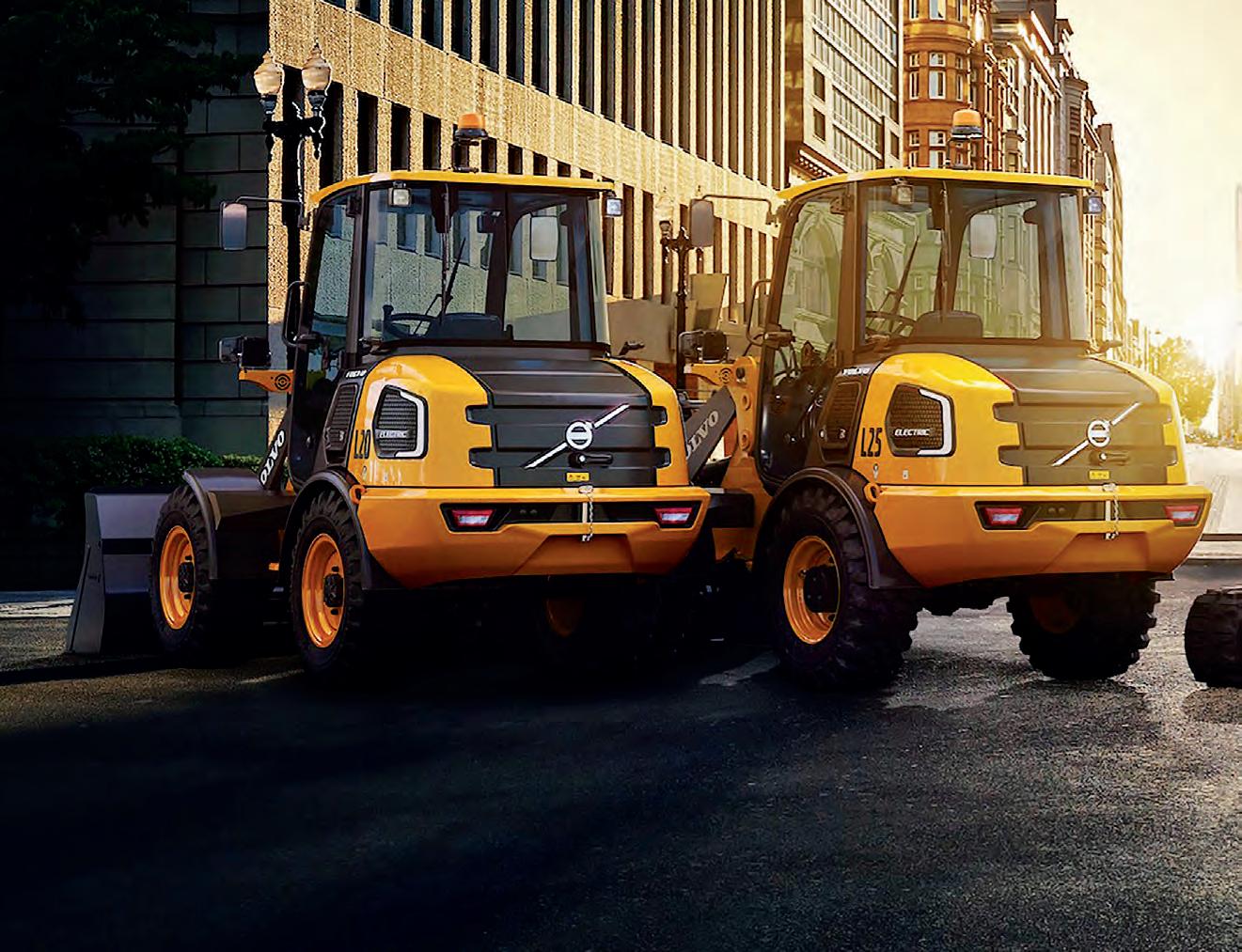
With three new electric compact machines – the L20 Electric, EC18 Electric and ECR18 Electric – now being introduced to the market, Volvo Construction Equipment (Volvo CE) is showcasing its commitment to build the world we want to live in by offering the industry’s largest range of electric machines. In total customers now have five models to choose from.
The three new models are now available to reserve online for delivery in 2022; these latest innovations are the next step forward in Volvo CE’s ambition to reach net zero value chain greenhouse gas emissions by 2040 – alongside development of hydrogen fuel cell solutions and more sustainable internal combustion engine products – and is part of Volvo Group’s target to have at least 35% of its total range of vehicles fully electric by 2030. Melker Jernberg, President of Volvo CE, says: “We are proud to be leading our industry’s fight against climate change as the manufacturer with the world’s largest range of electric machines. Not only are we delivering real-world solutions for a more sustainable way of working but we are adding further power to our customers’ business with the widest possible range of choice to best fit their needs.” The L20 Electric compact wheel loader and EC18 Electric and ECR18 Electric compact excavators join the already launched L25 Electric and ECR25 Electric. The two existing models are already established on the market and are proving to bring power and performance in a more environmentally sensitive package. The three new models represent the latest additions to Volvo CE’s industry-first commitment to move its range of Volvo branded compact wheel loaders
and compact excavators to electric and stop development of new diesel variants. The L20 Electric is a proven concept based on the larger L25 Electric model. It features a 1.8-ton payload and a paralleltype linkage offering great visibility over the attachment being used, outstanding lifting height, as well as 100% parallel movements – making it a perfect fit for fork applications too. Expected to deliver up to six hours of active work per charge, the electric machine comes with a choice of battery pack (33kWh or 40kWh) and reduces maintenance by 30%. As well as the more peaceful working conditions offered by its near-silence, operating comfort is also enhanced thanks to the new automatic park brake with hill-hold functionality and a range of customizable work modes. The short but tough 1.8-ton ECR18 Electric is set to provide the same best-in-class stability and operator experience customers expect from its diesel counterpart but with the benefit of low noise, low vibration and more responsive hydraulics due to the immediate torque. Delivering an anticipated four hours of active work per charge, depending on the environment and task in hand, the ECR18 Electric also benefits from an ultra-short tail radius (perfect for confined spaces). It has been built with durability in mind – from its high profile counterweight to all-round steel panels and hoses routed inside the boom. Easy to operate and transport, the nimble EC18 Electric offers customers a costefficient compact excavator working in 1.8ton applications. Its variable undercarriage retracts to less than 1m and expands up to 1.35m, allowing it to squeeze into the tightest of areas, while the machine’s design ensures the right frame corner, swing post and cylinder stay within the tracks’ width, resulting in maximum visibility and a reduced risk of machine damage when working alongside obstacles. As well as ergonomic controls, a spacious cab and a range of customizable settings, it also offers the option of an enclosed and heated cab.
On-Board Chargers
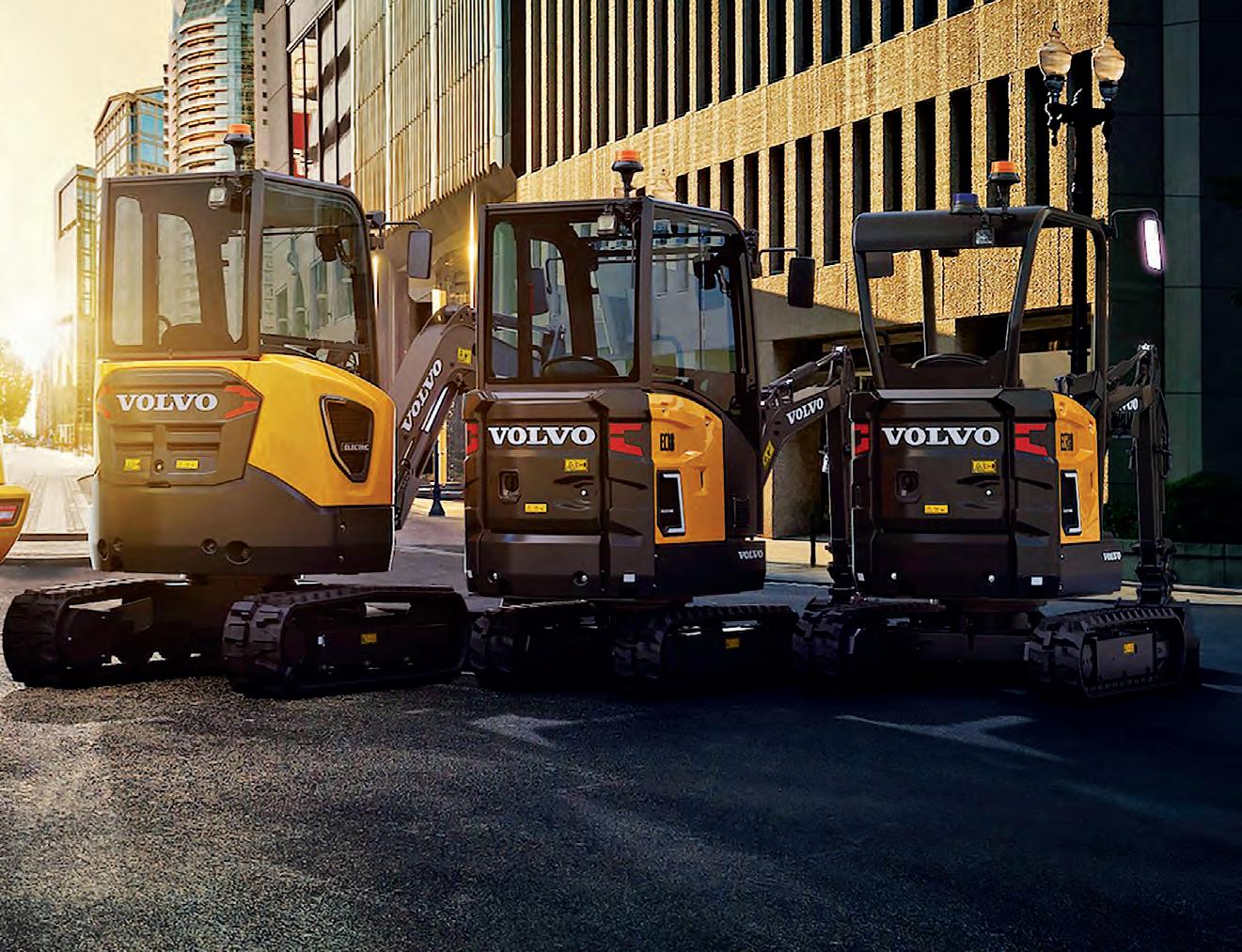
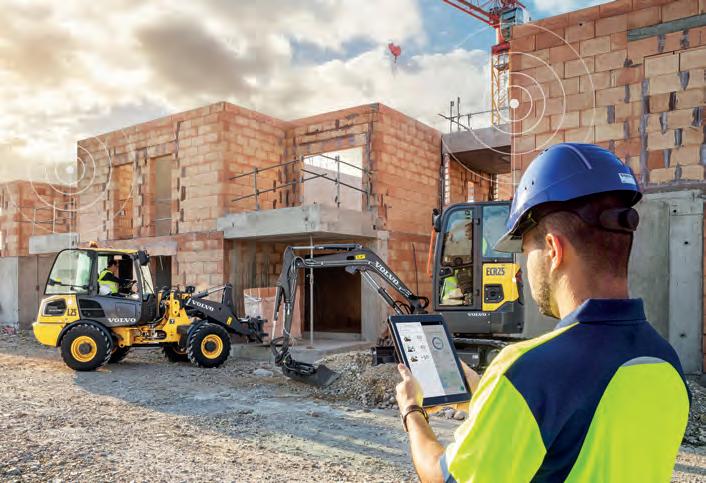
All three machines come with an integrated on-board charger allowing them to charge from 0 to 100% in under six hours. With an optional fast off-board charger, the L20 Electric will fully charge in under just two hours, while the ECR18 Electric and EC18 Electric will charge up to 80% in up to 1.25 hours. For the most accurate picture, Volvo dealers can calculate the expected operating time and optimum charging solution based on customers’ activities. With any of these machines, customers can operate in noise sensitive areas and out of standard hours, as well as lowcarbon projects and indoors, without the need for costly fume extraction systems.
Buying Incentives
As with the first electric models introduced in 2019 and brought to market in 2020, Volvo CE now has available a reservation tool for customers to order one of these three new machines, available across 12 European countries before expanding to other markets. Customers placing an online reservation by December 31 2021 will receive an extra gift – one Volvo bucket free of charge for ordering the L20 Electric and two Volvo buckets free of charge for ordering either the ECR18 Electric or EC18 Electric.
NEW BOBCAT MAXCONTROL BRINGS MACHINE CONTROL OF THE FUTURE
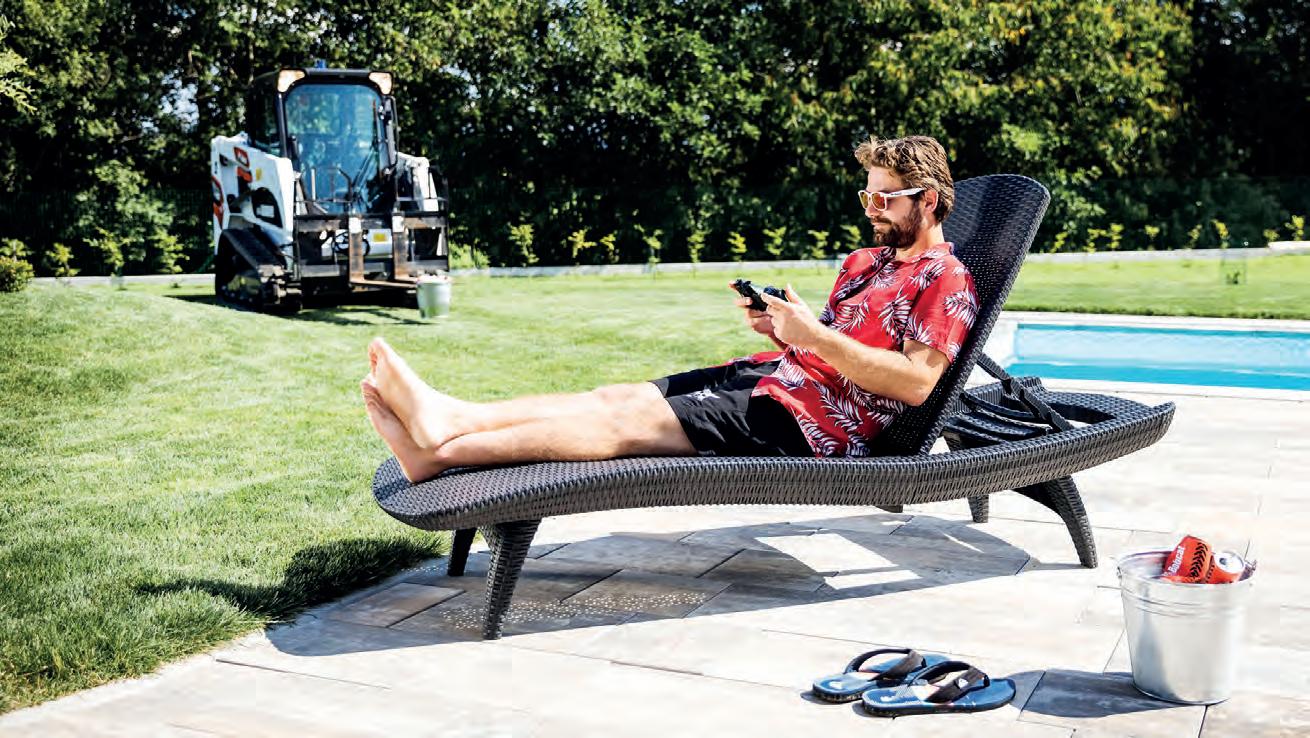
Bobcat has launched the MaxControl Remote Control system, giving us a vision of machine control of the future, by enabling operators to control Bobcat compact loaders remotely via an app, using an iPhone or iPad.
The MaxControl system provides a new remote control solution for applications in many markets, including construction, demolition, agriculture, landscaping, cleaning, recycling and general lifting and handling. With MaxControl, owners of Bobcat loaders do not need the latest machines or costly hardware updates to enjoy remote control. The system is compatible with all Bobcat loaders with Selectable Joystick Controls (SJC) dating as far back as 2004.MaxControl is available now on iOS devices, but an Android version will be available shortly. “The job site of the future is a more connected place and gamification will play a vital role. Changing demographics and consumer preferences are pushing our industry into categories that have been unheard of or have been poorly addressed in the machinery sector. At the same time, the need to address environmental impact, safety and elimination of downtime has become paramount,” says Vijayshekhar Nerva, Head of Innovation and Acceleration for Doosan Bobcat EMEA. “Our Innovation team has delivered a solution that is complex enough to improve productivity on the jobsite and at the same time, packaged to be accessible and simple to use. MaxControl was born out of these ideals and changing preferences to address our ability to not just keep up but keep ahead of competition in both ‘the Iron’ as well as the Digital side of our business,” continues Vijayshekar Nerva. The MaxControl system ensures that remote control capability is always at the operator’s fingertips as they can simply reach for the phone in their pocket and start controlling their Bobcat compact loader remotely within seconds, without having to worry about any extra gadgets. Being based on an app, it is easy to get the newest features the moment they are available. By combining jobs without having to jump in and out of the loader’s cab, the MaxControl system provides the operator with a different view of the job in hand, allowing them to carry out tasks remotely, and to repeat the process with maximum comfort. Being able to operate outside the cab provides a different angle of view, helping new and even less experienced operators in tight areas. When lifting and carrying large loads, the use of MaxControl eliminates blind spots in front of the load and raises awareness of the surrounding environment. Being outside the cab also allows for face-to-face communication with co-workers on site, enabling faster organization of the work. Operators may never know in advance when remote operation will come in handy, but with MaxControl on the phone in their pocket, they are always ready for any challenges that can arise.

news
Kilwaughter Minerals Grows R&D Team by 50% As Part of £3.4m Investment
Mineral processing firm Kilwaughter Minerals Limited has grown its Research and Development team by 50% as part of a long term £3.4m strategic investment in innovation.
This growth includes the recent recruitment of three further PhD scientists, building a foundation on which further investment will be realised over the coming months and years. The new roles follow unprecedented demand for Kilwaughter products, including colour renders, external wall insulation systems and soil health conditioning minerals as the economy rebounds following the coronavirus pandemic and subsequent lockdown. Dr. Ross Savage, Head of R&D at Kilwaughter Minerals said: “Boosting innovation and increasing investment at our R&D centre is core to meeting the sustained demand we are experiencing as well as futureproofing the business to service the evolving needs of our customers. “Having established a strong reputation for engineering high performance products, our focus is now on developing new technologies and using these to drive product excellence and deliver new levels of performance and efficiencies to our industries.” A recent report by the Northern Ireland Statistics and Research Agency (NISRA) estimated R&D investment in Northern Ireland was more than £881.4m last year, an annual increase of 11%, and that is expected to be matched if not exceeded when new figures are released this year. Gary Wilmot, Chief Executive, Kilwaughter Minerals, added: “We have been building our customer insight to allow us to confidently deepen our investment in new technologies and new products. “We are creating a culture that puts high value on ideas and creativity and I’m confident that we have an exciting future ahead of us.” Summarising the key objective of the R&D investment, Ross commented: “For us to remain at the forefront of our market segments we need to be continually enhancing our existing product lines and spearheading the development of next generation solutions. That is exactly what we are going to do.”
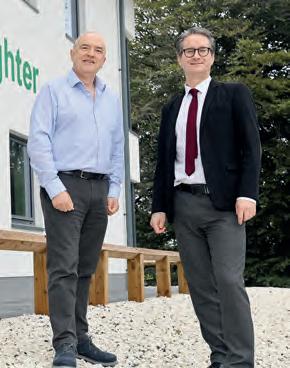
Kilwaughter Minerals Chief Executive Gary Wilmot and Head of R&D Dr. Ross Savage announce team growth of 50%.
‘Idle Non-Tipping Trailers Can Help Combat Supply Shortages’, says Aggregate Industries
With the ongoing shortage of truck drivers, leading construction materials supplier Aggregate Industries is encouraging the sector to overcome supply disruption by adopting widely available NonTipping Trailers (NTTs) which can deliver up to 40% more materials compared to standard trucks.
It comes as the Construction Leadership Council (CLC) recently warned that the availability of hauliers is now a ‘critical nationwide problem’, with the industry having 15,000 fewer drivers due to Brexit. At the same time, almost 30,000 HGV driver tests have been postponed during the pandemic, leading to delays and shortages of materials including bricks, blocks, roof tiles and bagged cement. Having worked throughout the pandemic to provide surety of supply of the materials it offers, Aggregate Industries is advising the construction industry that one of the ways to improve supply is by using NTTs, many which are available and often under-utilised. Aggregate Industries’ NTTs ‘walking floor’ system can raise carrying capacity up to a remarkable 43% per vehicle – essentially reducing the number of vehicles and drivers required. There is also a benefit in the management of logistics on the construction sites; less lorry movements are required due to the larger quantity delivered and the ability to tandem tip. Other key advantages include improved turnaround times due to tandem tipping capability, reduced CO2 emissions as less vehicle manoeuvres are required. NTTs also offer improved health and safety as they can be used in restricted areas such as tunnels or areas with overhead powerlines and on uneven surfaces. Ben Young, Head of Road Logistics, comments: “At a time when the construction sector faces ongoing challenges around the availability of truck drivers, which is exacerbating supply issues, the need to utilise innovative trailers such as NTTs to alleviate the problem cannot be overstated. “The fact that these cutting-edge trucks, considered best practice and with a proven track record on many projects already, can deliver up to 40% more materials compared to standard hauls means they should be a no brainer on all construction projects – especially those suffering from a lack of drivers. “One of the most important benefits of the NNTs is the lower carbon footprint. As a company, we are committed to reducing carbon emissions and by moving just 10% more products via the NTT we can save in excess of 100,000 kg CO2 every year.” Yet, according to Aggregate Industries, despite being introduced in 2013, take up of NTTs remains low due to customer inertia, lack of planning and misconceptions over manoeuvrability, tipping speed, and heat loss. Ben adds: “Hesitancy over NTTs is disappointing and unfounded – they’ve delivered great results on high-profile projects such as the A14, yet they just aren’t utilised as much as they could be. The latest generation of NTTs not only boast a discharge speed of 53 seconds but also have improved inner and outer turning circle (v 8W) in terms of manoeuvrability. “The UK construction sector is considered world-class and with the driver shortage likely to continue in the coming years, remaining competitive and cutting edge in the face of Brexit and a post-pandemic recovery has never been more important. This will depend on how the industry can improve gains in productivity, efficiency and technology and NTTs are a vital part of this.”

BRADDAN PLANT HIRE: FROM MODEST BEGINNINGS TO HARD WON SUCCESS
When Carl Caddick began his working life as an apprentice steel erector at the age of 18, he had little idea that one day he and his two sons, Bradley and Daniel, would be running not just one highly successful business, but two, as Plant & Civil Engineer’s David Stokes has been finding out.
Today, Braddan Plant Hire is one of the largest independent access hire companies in the Tees Valley and surrounding areas in the North East of England; it is part of the wider Braddan Group which includes Braddan Structures, recognised as an industry leader and innovator within the steel construction field. From initially working from a kitchen table at home, the company today operates from three storey, modern and spacious premises that includes offices, workshop facilities, state-of-theart training facility and warehousing. Based in Darlington, Braddan Plant Hire was established just a few years ago after Carl realised the family’s steel business was spending more and more on hiring access equipment to carry out various contracts around the country for an extensive customer base. “It began to make more sense to buy in our own access equipment, which we did,” recalls Carl, “but soon we found ourselves hiring it out to other companies; the first pieces of equipment we invested in were Skyjack and JLG 45ft and 60ft articulated booms.” He adds: “As a steel erecting company, of course, we weren’t set up as a hire outlet, so we brought in experienced help to run that side of the business and began to build up our rental stock, quickly adding 30 access machines of various reaches.” Three years on and Braddan Plant Hire has doubled its fleet of diesel and electric boom lifts and scissor lifts, certainly more so since the arrival of Yvonne Hook, who has more than 20 years of experience in the industry; the company also belongs to the Access Alliance, a collaboration of some of the UK and Ireland’s strongest independently owned regional powered access sales and rental businesses. “We are planning to triple the size of our fleet over the next three to five years, with a goal of building up a stock of around 200 access machines, which will probably mean we will also have to expand our premises or seek a larger site close by,” says Carl. All access hire equipment, of course, is fully serviced before being rented out to customers, with Manager Michael (Tomo) Tomlinson responsible for both maintenance and sales. The equipment can be delivered and collected, depending on the requirements of the customer.
Green Credentials
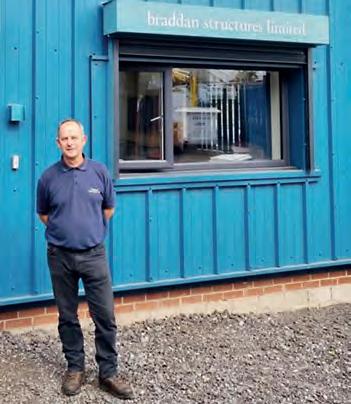
The company carries a variety of brands to satisfy the needs and demands of its customers, including JLG, Skyjack and Niftylift – and it has recently ordered 20 new Genie® Hybrid machines; the Z®-45 and Z®-60 articulated boom lifts feature the latest industry leading hybrid technology. “Our ‘green’ credentials are very important to us and to our customers and the Genie Hybrids tick all the right boxes,” explains Carl. “Not only are they environmentally friendly they are also more efficient and cheaper to run.” Lightweight and easy to transport from site to site., other benefits of the FE machines include zero emissions and low noise, making them ideal for operating in built up areas and indoors. That protecting the environment is close to Carl’s heart is also demonstrated by the company’s investment in making its premises virtually carbon neutral; solar panels, for example, provide much of the building’s electricity needs.
Training Centre
Training and safety also play a big part. “All our access booms come with secondary guards to provide extra safety and we are
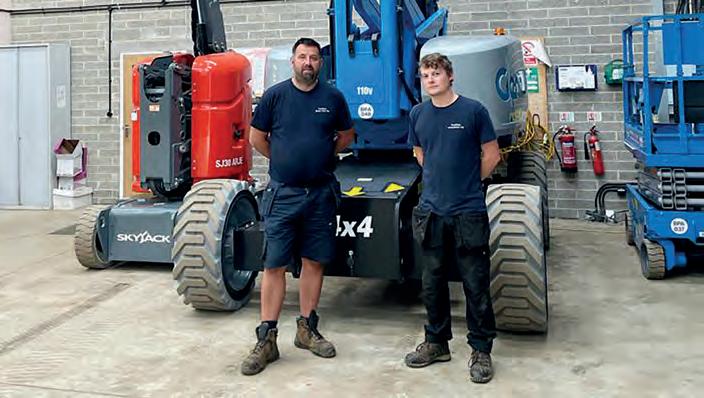
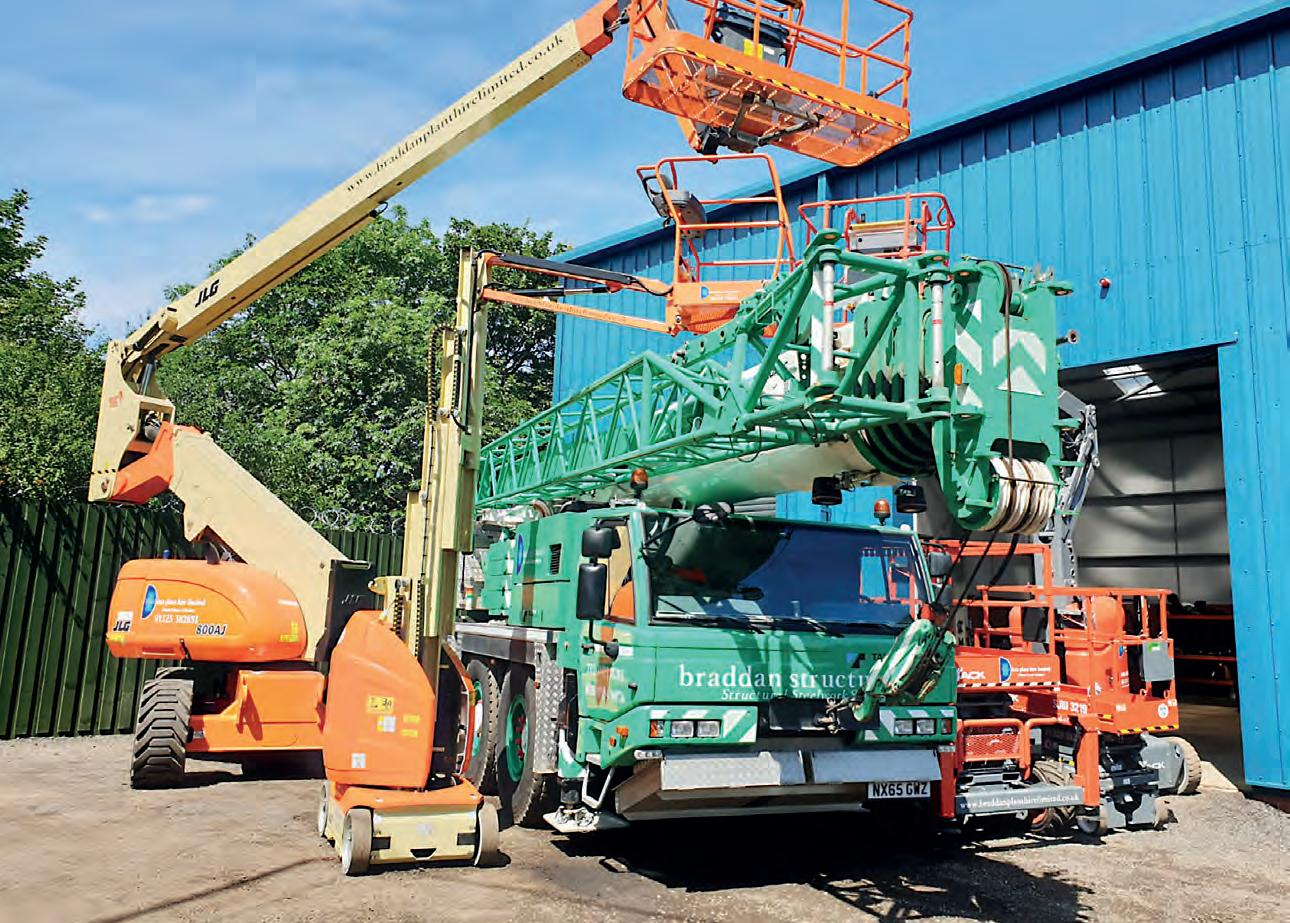
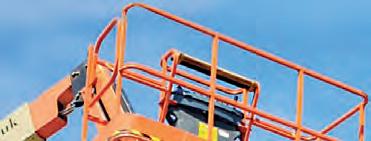
in the process of fitting similar guards to our scissor lifts,” says Carl, whose son Bradley is responsible for access equipment training. With a state-of-the-art indoor training centre and being members of the International Powered Access Federation (IPAF), Braddan Plant Hire provide students with the required knowledge and practical skills to safely operate powered access equipment, running on average five separate courses every month, a mix of theory and practical. “All the courses are well attended; better than we originally anticipated,” says Bradley. “They consist of both classroom and onsite sessions, with the option of IPAF e-learning from home. We also offer the opportunity to undertake the training on a Saturday or Sunday to fit in with our students work commitments.”
Braddan Structures
As we mentioned earlier, Braddan Plant Hire would probably never have been established if it hadn’t been for the growing success of Braddan Structures and its everexpanding needs for access equipment. With around 40 steel erectors on its books, Braddan Structures steel construction work ranges from complicated glazing roof supports to column and beam office developments, portal frames, pre-cast concrete installations for grain stores, retaining walls, stairs and hollow core flooring. Successfully completed contracts include projects at Canary Wharf and Kings Cross in London, and it is currently involved in a major project in Wellington Place, Leeds (2,500 tonnes) another that wraps around the iconic Strawberry Pub opposite St James’ Park in Newcastle. Other high-profile projects in the past include Newcastle City Library (1000 tonnes) Eldon Square phase 3 (4000 tonnes) The Royal Bank of Canada new HQ in St Hellier Jersey (2250 tonnes), Nike and Sony new headquarters in Kings Cross (2,500 tonnes). Due to the nature of the type of work undertaken, great emphasis is placed on the quality of people employed, their training and the provision of modern equipment for the tasks undertaken. The company has invested heavily in both the personnel he employs and the equipment that they use, with the goal of providing a safe, efficient, quality service on time and on budget to all customers across the structural steelwork industry.
Focused on Future
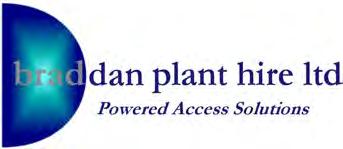
There’s no doubt, this second generation family business group is focused on being the best in its areas of activity, whether it be in the steel structures sector or the access equipment hire industry; it has achieved much since its modest beginnings, having survived a recession and other economic difficulties, not least those caused by the global pandemic. Its success has been hard won, and there’s much more to come in terms of expansion and customer reach. “We have a great team of experienced and dedicated people around us, both in plant hire and steel structures, and with a loyal and growing customer base, we are looking to the future with some confidence,” says Carl.