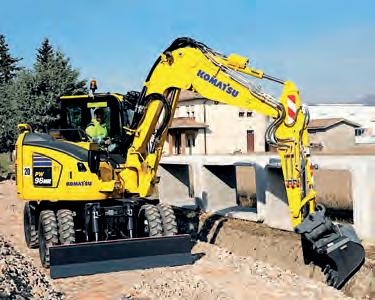
12 minute read
Hire News
news
New Komatsu PW98MR-11 Wheeled Midi Excavator Unveiled
Komatsu has unveiled its latest generation PW98MR-11 tight-tail wheeled midi excavator, first versions of which are now available to order.
Bridging the gap between compact and construction-sized machines, it is aimed firmly at those working in the utilities sector and in confined space applications such as narrow alleys, road construction sites and sewer construction work. Said by Komatsu distributor in Ireland, McHale Plant Sales of Rathcoole and Birdhill, to offer improved efficiency, operator comfort and fuel consumption compared to the ‘Dash 10’ model it replaces, other key features of the 10-tonnes unit are its 0.282 m3 bucket capacity, class leading compact size and what Komatsu calls its ‘unrivalled lifting performance’. A swing boom design makes it attractive for digging parallel to buildings or barriers, while a protected two piece boom cylinder allows for safer truck loading operation. A standard 100% differential lock on both axles provides direct traction and enhanced jobsite mobility when working on slippery and uneven surfaces. With no need for a complex SCR aftertreatment system, and no AdBlue refilling, the PW98MR-11 is a machine which McHale Plant Sales director, John O’Brien says will enable clients to ‘future proof their investment’. With its EU Stage 5 compliant engine, it will appeal to emissions-sensitive customers wishing to demonstrate their environmental credentials when pitching for projects in crowded, built-up urban locations.
Further Enhancements to Mastenbroek’s CT12 Crawler Truck
Mastenbroek recently showcased the latest version of its CT12 crawler truck; the 2022 model features several enhancements designed to make life easier for drainage contractors and operators working on pipeline and renewable energy projects.
Mastenbroek has incorporated a larger, full-width, tipping hopper which reduces spillages when loading. The hopper is fully visible when the operator cabin is raised to its highest position and its variable speed conveyor provides a free flow discharge for aggregates of varying viscosity. As well as allowing the operator to place materials into trenches accurately, the hopper means the CT12 can be used as a dump truck to, for example, haul aggregate along pipeline rights of way. At the front of the CT12, Mastenbroek’s variable height, variable speed, 180-degree swing conveyor makes it easy for the operator to place backfill material directly into a trench or the hopper mounted on the trencher. A critical part of Mastenbroek’s design upgrade is operator and service engineer access to the machine. A new frontmounted ladder provides easy access to radiator levels, with side-mounted wide-opening doors facilitating access to the CT12’s 248hp Volvo Penta D8 eight litre six-cylinder Stage 5 emission engine. Inside the ROPs and FOPs certified cabin, the layout of the operator controls have been improved, and there is now the option to have a 360-degree surround camera view. Mastenbroek has now mounted the hydraulic oil cooler independently to the engine radiator, with both have opening grills for easy access and cleaning. “The CT12 has been popular with agricultural drainage contractors for a long time. Over recent years we have seen more and more construction companies in the pipeline and renewable cable industries adopt the machine,” says Christopher Pett, Mastenbroek’s general manager. “With these latest improvements, which are based on customer feedback and our insights, we are aiming to increase the appeal of the CT12 still further.”

Mid-West Welcome for Government Housing Plan
Leading Mid-West construction equipment distributor – Michael McHale, Chairman of McHale Plant Sales of Birdhill and Rathcoole – has added his voice to that of the Irish Plant Contractors Association, in welcoming the Dublin Government’s €4 billion annual plan to boost house construction over the next five years.
Citing it as a ‘blue print’, from which providers to the sector can make their own plans and projections, proof that it will have a beneficial impact on the plant sector are already evident, Michael McHale said. “The fear expressed by some commentators that skilled manpower shortages might be a constraint in bringing the plan to full fruition within the time period is one that the plant sector can help alleviate by the laboursaving and productivity benefits that latest technology and mechanisation can bring. “This is especially true in the provision of groundworks, site preparation and site services, and in the on-site handling of materials.”
news Enniskillen Recycling Centre benefits from £725,000 investment
Environment Minister Edwin Poots has visited a Household Recycling Centre in Enniskillen to see improvements made following a £725,122 grant from his Department’s Household Waste Recycling Collaborative Change Programme.
The funding was awarded to Fermanagh and Omagh District Council to modernise the Drummee Household Recycling Centre (HRC) in the town and brings the total invested by his Department so far via the Programme to almost £5million. Minister Poots welcomed the environmental and economic benefits the new improved facilities would bring: “I am delighted that Fermanagh and Omagh District Council secured this funding to improve the facilities at Drummee Household Recycling Centre. The former Centre was located on an old site with ageing infrastructure in need of redevelopment and equipment in need of upgrading. The changes are impressive and will no doubt assist the
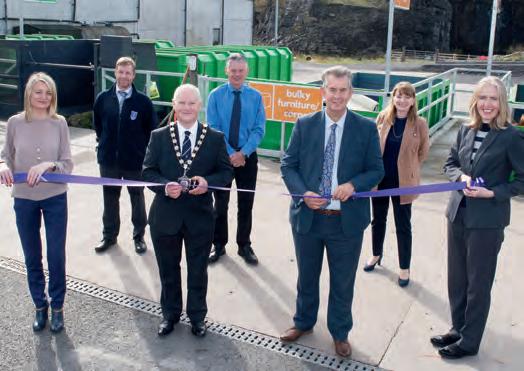
Pictured with the minister at the official reopening of Drummee Recycling Centre are: Front row, (L-R) Anthea Owens, Recycling Education and Grants Officer, Fermanagh and Omagh District Council; Councillor Errol Thompson, Chair, Fermanagh and Omagh District Council, and Alison McCullagh, Chief Executive, Fermanagh and Omagh District Council. Back row (L-R): Brendan Ferguson, Contracts Manager, Fermanagh and Omagh District Council, John McCullagh, Head of Waste and Recycling, Celine McCartan, Director of Corporate Services and Governance.
public to further increase their recycling in a safe and more pleasant environment.” The new facilities will allow for an increase in the quantity and quality of material collected for recycling and reuse. The improved site has separated the recycling facility from the landfill site, removing Council vehicles and contractors from the public areas by creating a separate entrance. There is also an increased number of receptacles to maximise the category and tonnage of material captured for recycling. By the end of the first full year at full operating capacity the Council estimate an additional 590 tonnes of recyclable material, including 115 tonnes of paper, plastics and glass will have been diverted from landfill. This should result in an estimated over 1,600 CO2 tonnage savings per year, equivalent to some £93k in estimated Carbon Savings per year. The Minister concluded: “Over the past few years we have seen an ever increasing positive and responsible public attitude towards recycling and it is important that we continue to collaborate with local councils and stakeholders to ensure this trend continues. By improving our recycling facilities we can ensure that the quality of our recycling improves, thereby reducing our landfill. This benefits both our economy and our environment.”
89% of builders having to delay jobs, says FMB
A shocking 89% of local builders have reported having to delay jobs due to a lack of materials or skilled tradespeople, according to the latest State of Trade Survey from the Federation of Master Builders (FMB).
Adding to the pressure facing the industry, 97% of builders have reported skyrocketing material prices and expect this to continue into the last quarter of 2021, with 78% passing this increased cost on to the consumer. Builders have been forced to hit pause on some jobs, in the face of increasing difficulty to hire tradespeople, such as general labourers and plasterers, with 42% and 37% respectively of builders struggling to get them to a job. Despite a slight easing, near half of FMB members are also facing pressure to find carpenters/joiners and bricklayers. The FMB State of Trade Survey, which is released quarterly, is the only survey of its kind to track the experience of small to medium-sized (SME) construction firms in the UK. It found:
Delays and cancellations
• 82% of builders have delayed jobs due to a lack of materials • 60% have been pressed pause due to a lack of skilled tradespeople • Combined, 89% of builders have faced delays due to either materials or skills shortages • 8% of builders have been forced to cancel jobs due to a lack of materials • 12% have been cancelled due to a lack of skilled tradespeople
Skills shortages
• 42% can’t get hold of general labourers, up 6% on last quarter • 37% can’t hire plasterers, a rise of 6% on last quarter • 47% of builders are struggling to hire carpenters/joiners, down 6% on last quarter • 45% are struggling to hire bricklayers, a fall of 2% on last quarter
Price rises
• 97% of builders are facing material price rises, with 93% expecting this to continue into Q4 • 77% of respondents have been forced to raise their prices in the past quarter Brian Berry, Chief Executive of the FMB, said: “This FMB State of Trade Survey shows a damning situation for the building industry, with 89% of builders facing delays and some cancelling work altogether, due to a lack of materials or skills. “The Government should tackle the growing skills gap. Effective efforts to help the haulage industry ease the supply of materials are also needed. This will help our members get back to building and help the post pandemic economic recovery. “Our data shows the combination of long delays and rising prices mean consumers are also starting to feal the heat. Changing quotes, delays to jobs, and price hikes may lead to some homeowners being pulled in by unscrupulous builders hoping to make a quick buck. A good builder is a busy builder and it is important to be patient when selecting the right person for the job.”
NBS RELEASES FINDINGS FROM ITS ANNUAL DIGITAL CONSTRUCTION SURVEY
NBS, the platform for connected construction information, has revealed its eleventh annual survey, now the Digital Construction Survey, previously the NBS BIM Survey. With over nine hundred respondents, this year’s report provides a more comprehensive picture of the sector’s digital transformation, along with BIM adoption levels, and day-to-day usage of technology.
With approaching three-quarters (71%) of respondents now using BIM, it’s fair to consider this approach now embedded across the sector, with adoption levels consistent for the past couple of years. The construction industry is now on board with technology and confident that it will help solve the challenges facing the sector, as demonstrated by eight in ten stating that digital technologies deliver a better-built environment, with three quarters (75%) saying that tech offers sustainability benefits. The forthcoming Building Safety Bill has forced safety to the forefront of the construction industry, and regulation requires a digital “golden thread” of information. This is an accurate, up-to-date digital record of all data required to maintain and operate a building. This includes how it was designed, built, and any maintenance. This log records all the processes, construction products used, and the decisions made in construction and operation. The golden thread covers information and documents as well as information management processes, all stored as structured digital information. While eight in ten (78%) respondents say they need to be working digitally and 70% say they need to have adopted BIM to make the golden thread a reality, only half (51%) are clear how they will do this. The golden thread process is made much easier with the data available through a digital twin. In addition, having a digital twin enables access to all of the essential information in one place and allows for constant monitoring and maintenance of the asset. While three quarters (74%) of respondents believe that digital technology is helping create a safer built environment, digital twin adoption is still relatively slow, with only 16% having worked on a project that used a digital twin in the past year.
New Tech
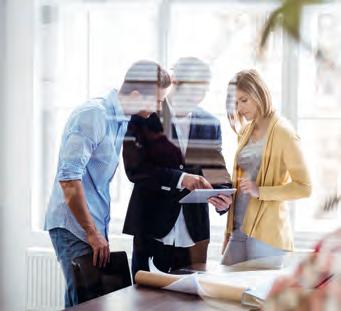
In the past twelve months, half the survey’s respondents have worked on an off-site project, a clear sign that a move to MMC is taking place, yet this figure shows there’s still work to be done if the government is going to embrace MMC on the scale it intends. Over a third (35%) already use immersive techs such as VR/AR, and a half (50%) plan to within five years. These figures could indicate that a switch to digital technologies that can improve data collection and analysis and safety is becoming the norm as construction sites continue to become digital tech ‘hotspots.’ The survey also reveals that over threequarters of the industry (77%) use cloud computing. This result is higher than previous year, compared to 42% in 2020. A clear sign that digital methods are being fully embraced and that steps towards the Golden Thread are now coming into effect, providing a clear digital footprint.
Transformative Tech
The construction industry has traditionally lagged behind others in the adoption of digital capabilities. The Digital Construction Survey asked respondents to rank how various essential technologies or ways of working will transform the sector for the better over the next five years. The top five are as follows, 1) BIM, 2) Cloud computing, 3) Offsite construction, 4) Digital Twins, 5) AR/VR mixed reality. Commenting on the survey’s results, David Bain, NBS’ Research Manager, said, “The adoption of new, digital technologies and ways of working should help to improve outcomes, so it is encouraging that 80% of built environment professionals agree that they are helping to create better buildings and places. Also, 75% say these innovations positively impact environmental sustainability, and 74% see them making a safer built environment. The industry also recognises the key role digital and BIM will play in realising the golden thread of information. “The use of cloud computing and blended working has become commonplace, but BIM has the most significant potential to transform the built environment for the better. BIM is now part of many people’s way of working (71%), with almost twothirds of these recognising it as being about better information management, not just software. However, there remain challenges in taking the benefits of BIM and digital to all parts of the industry.” Over 900 construction professionals took part in this year’s Digital Construction Survey, which included views from architects/engineers and other consultants (66%), contractors (13%), clients (9%), and suppliers (9%) in the UK and beyond.
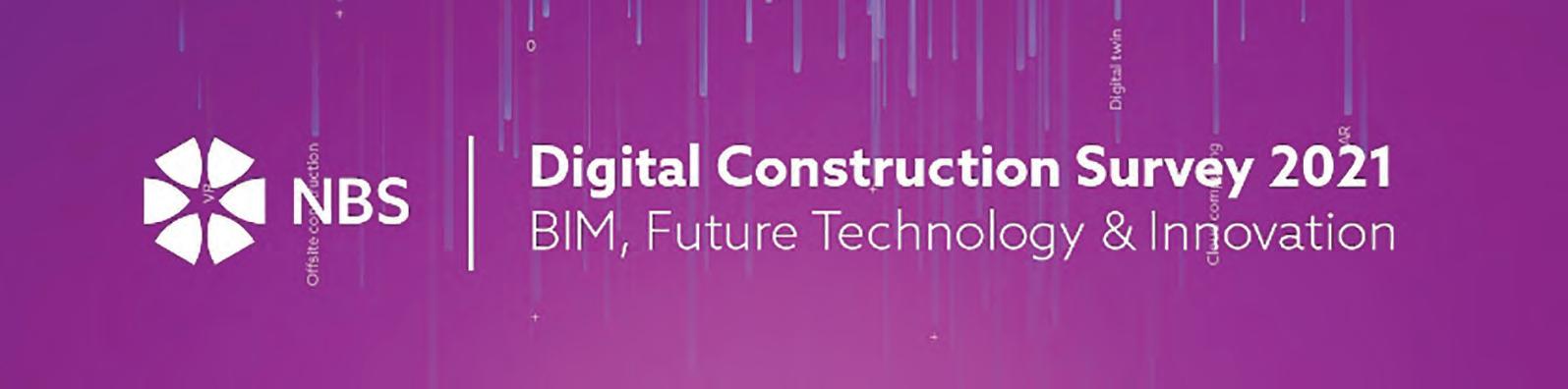