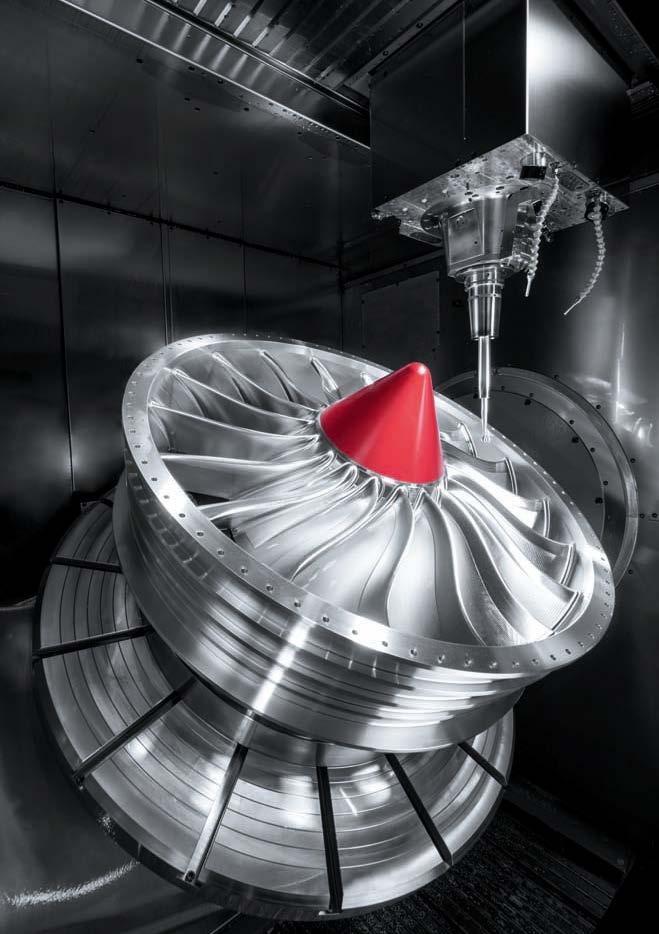
6 minute read
Freesdraai-technologie geeft vliegtuigmotoren boost
De MT-technologie van Hermle maakt het mogelijk om componenten voor vliegtuigmotoren efficiënt te verspanen (foto’s: Hermle)
Door de klimaatagenda is er de laatste jaren een vergrootglas komen te liggen op markten en industrieën die veel CO2, stikstof en fijnstof uitstoten. Zo ook op de luchtvaartindustrie. Er wordt naarstig gezocht naar oplossingen om het brandstofverbruik, de emissies en het geluid van vliegtuigen te reduceren. Naast het verfijnen van de aerodynamica, zullen de vliegtuigmotoren de grootste ontwikkeling door moeten maken om aan deze wensen te kunnen voldoen. Dat betekent dat motoronderdelen complexere geometrieën krijgen en het gebruik van nieuwe exotische, moeilijk te verspanen materialen zal toenemen. Met de draaifreescentra van Hermle richt de machinebouwer zich op de veeleisende productie van rotatiesymmetrische motoronderdelen zoals blisks.
Straalmotoren (turbofan) zijn sinds het midden van de twintigste eeuw de meest gebruikte vliegtuigmotoren. De basis van de meeste straalmotoren is hetzelfde. Lucht wordt ingezogen aan de voorkant en door de compressor samengeperst. Daarna wordt er brandstof toegevoegd en het resulterende mengsel wordt ontstoken, wat resulteert in stuwkracht. Bij turbofans is voor in de motor een grote compressor en een grote fan (soort propeller) geplaatst die de lucht zowel door, als langs de verbrandingskamer blaast. Het gedeelte waar de lucht langs de verbrandingskamer wordt geleid, wordt ook wel de ‘bypass’ genoemd.
Ontwikkelingsdoelen
Een belangrijke factor voor de brandstofefficiëntie en de motorprestaties is de zogenaamde bypassverhouding tussen de luchtmassastromen die om en in de turbine stromen. Terwijl moderne motoren nu een bypass-verhouding van ongeveer 10:1 bereiken, werken oudere motoren nog steeds met waarden van 5:1. Toekomstige aandrijvingen moeten een bypass-verhouding van 15:1 bereiken en dus aanzienlijk zuiniger en stiller zijn. De ACARE (Advisory Council for Aeronautics Research in Europe), een Europees adviesorgaan, heeft specifieke ontwikkelingsdoelen genoemd als onderdeel van haar onderzoeks- en innovatiestrategie: Volgens het ‘Flightpath 2050’, moet in 2050 de CO2-uitstoot met 75% en de NOx-uitstoot met 90% per reizigerskilometer worden verminderd. Tevens pleit ACARE voor 65% reductie van geluidsoverlast. Om deze doelen te behalen, werken de vliegtuig- en motorontwikkelaars aan het verbeteren van de aerodynamica, de massa van het vliegtuig, de brandstof en de motoren. Motorontwikkelaars verhogen de motorefficiëntie door onder andere te werken met hogere drukken en temperaturen van meer dan 2.000 oC. Nieuwe lagedruksystemen helpen om de bypass-stroomverhouding te vergroten en zo meer stuwkracht te genereren met een lager verbruik. Om de geluidsontwikkeling te verminderen, wordt er geëxperimenteerd met de vorm van individuele bladen in de fan en compressor.
Deze titanium impeller van titanium wordt gefreesd op een Hermle C 42 U MT dynamic
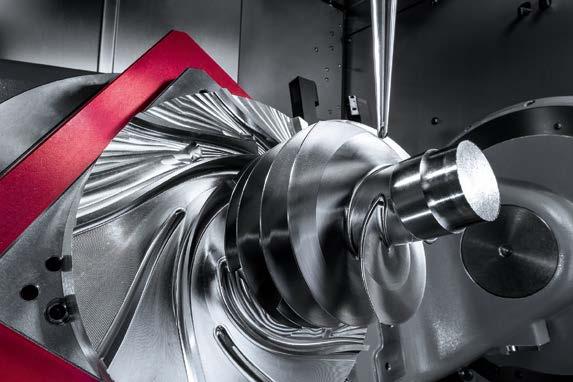
Toenemende belastingen
Complexere geometrieën, hogere drukken en kritische temperaturen - elke toename van de efficiëntie van de motor betekent ook een grotere belasting op de motoronderdelen en dus op de materialen en productieprocessen. Hermle presenteerde in 2010 de eerste MT (Mill-Turn) -machine en legde daarmee hun basis voor de lucht- en ruimtevaartindustrie. Ondanks dat de freesmachines van Hermle ook al voor 2010 werden gebruikt door motorfabrikanten, lag de focus van de machinebouwer toen nog niet speciaal op de luchtvaartindustrie. Met de MTtechnologie breidde Hermle haar gebruikersgroep uit en is de lucht- en ruimtevaartindustrie een belangrijke divisie binnen het bedrijf geworden. Het voordeel van de MT-machines is dat het werkstuk zowel gefreesd als gedraaid kan worden. Door het gelijktijdig zwenken kunnen gebruikers kortere en dus stijvere gereedschappen gebruiken. Bovendien kunnen complexe contouren ook met slechts één gereedschap worden bewerkt. Producenten hebben daardoor minder gereedschappen nodig. De aspecten precisie, stabiliteit en nauwkeurigheid op de lange termijn zijn net zo cruciaal. Een motorserie wordt geproduceerd over een lange periode van wel twintig jaar. Fabrikanten verwachten volgens Hermle dat bewerkingsmachines tot op het laatste onderdeel dezelfde eigenschappen behoudt. Dit is een bijzondere uitdaging, aangezien de machines worden ingezet voor het vijfassig bewerken van moeilijk te verspanen materialen zoals Inconel of zeer speciale hittebestendige in-house ontwikkelingen. Omdat projecten meerdere jaren lopen, kan Hermle op verzoek van de klant garanderen dat elke machine die het bedrijf in deze periode bouwt en levert identiek is. Ongeacht of er in die tijd software- of hardware-updates waren. Hier heeft het standaardconcept van Hermle een voordeel ten opzichte van speciale machines.
Pallet- én werkstukautomatisering
Hermle heeft met het Robotsysteem RS 1 recent een volwaardige combinatiecel geïntroduceerd voor pallet- en werkstukautomatisering. De RS 1 combineert flexibiliteit en productiviteit met een opslagsysteem voor een lange onbemande looptijd, waarbij het wisselen tussen grijper en pallet automatisch verloopt. Het laadstation maakt het mogelijk om pallets en werkstukken parallel aan de productie op te stellen.
Dat maakt de RS 1 voor veel bedrijven een optimale automatiseringsoplossing. De RS 1 kan worden gekoppeld aan één of twee machines voor een maximale output. Het systeem kan op een later moment ook eenvoudig van één naar twee bewerkingscentra worden uitgebreid. Met een vloeroppervlak van slechts 12 m2 biedt de RS 1 altijd vrije toegang tot de werkgebieden van de machines, ongeacht of er één of twee bewerkingscentra zijn gekoppeld. Tevens kan de automatiseringsoplossing worden voorzien van een derde opslagmodule, een wasinstallatie, een meetmachine of een transportsysteem (AGV). Het RS 1-concept werkt met verschillende bewerkingscentra van Hermle, waaronder de C 12, C 22, C 250, C 32, C 400 of C 42. Het maakt niet uit of twee identieke of twee verschillende machines via de RS 1 met elkaar zijn verbonden. Bij een enkele bewerkingsmachine wordt de automatisering aangestuurd met het Hermle Automation Control System (HACS) of met het SOFLEX productiecontrolesysteem. Bij twee machines wordt de RS 1 altijd aangestuurd met SOFLEX. Uiteraard kunnen de bewerkingsmachines ook zelfstandig worden bediend. Het Robotsysteem RS 1 is zowel geschikt voor pallet- als werkstukautomatisering.
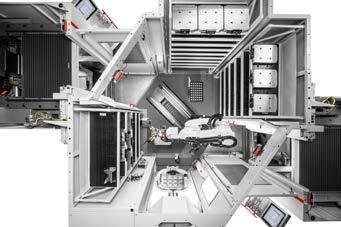
Produceer automatisch meer
De NC-gestuurde spansystemen en grijpers maken een volledig automatische werkstukwissel mogelijk. De NC-grijpers en automatisch instelbare spaninrichtingen passen zich door het grote grijp- en klembereik aan de werkstukken aan, zodat handmatige tussenkomst nagenoeg overbodig is. Drie individueel instelbare opslagmodules bieden ruimte aan een optimale hoeveelheid werkstukken. Of het nu gaat om pallets tot 398 mm x 398 mm of universele matrixopbergplaatsen in vijf varianten voor kubusvormige of cilindrische onbewerkte werkstukken, alles vindt zijn plek in het opslagmagazijn. De RS 1 is volledig in de Hermle-softwarewereld geïntegreerd en daardoor eenvoudig via het touchscreen te bedienen.
Hermle Luchtvaarindustrie
Stabiel verspanen

Hermle biedt momenteel drie high-performance machines aan als MT-versie: de C 42 U, C 52 U en C 62 U. Hiermee maakt de machinefabrikant het gelijktijdig frezen en draaien van werkstukken tot een maximale diameter van 1.200 mm en een hoogte van 900 mm mogelijk. De maximale massa is begrensd op 700 kg (C 42 U MT), 1.000 kg (C 52 U MT) of 1.500 kg (C 62 U MT). De Hermlemachines hebben een starre machineconstructie die van meet af aan essentieel is voor stabiele draaibewerkingen in moeilijk te verspanen materialen. Bij het bewerken van motoronderdelen is procesbewaking ook essentieel. Beschadigingen of andere onvolkomenheden die tijdens het proces optreden kunnen later desastreus zijn. Dit maakt een volledige documentatie van de afzonderlijke productiestappen des te belangrijker. Een voorbeeld hiervan is het monitoren van koelvloeistof. Het bewijst dat er altijd koelvloeistof aanwezig was tijdens een productieproces. Hiervoor zijn in de machines sensoren ingebouwd die de druk en stroming in het interne koelcircuit registreren. De gegevens die door procesbewaking worden gegenereerd, worden vervolgens bij het werkstuk opgeslagen.
De C 42 U, C 52 U en C 62 U bewerkingscentra zijn uitermate goed geschikt voor het gelijktijdig frezen en draaien van complexe werkstukken onder stabiele omstandigheden
Blisks
Veel voorkomende componenten die geproduceerd worden met de machines van Hermle zijn blisks (Blade Integrated Disk). De verwerkingstijd van een blisk kan oplopen tot 20 uur en de blisk kan een waarde vertegenwoordigen van rond de 100.000 euro. Een van de uitdagingen hierbij is de juiste bewerkingsstrategie. De lange bladen mogen tijdens het bewerken niet trillen. Daarnaast is er gereedschapsslijtage. Dit is waar gebruikers profiteren van de geautomatiseerde gereedschapswisselaar. De slijtage is erg hoog bij het verspanen van materialen die moeilijk te bewerken zijn. De onbemande gereedschapswissel betekent vaak een aanzienlijke toename van de efficiëntie. Door de lange bewerkingstijden is een palletwisselaar vaak voldoende voor het automatisch beladen van de bewerkingscentra.