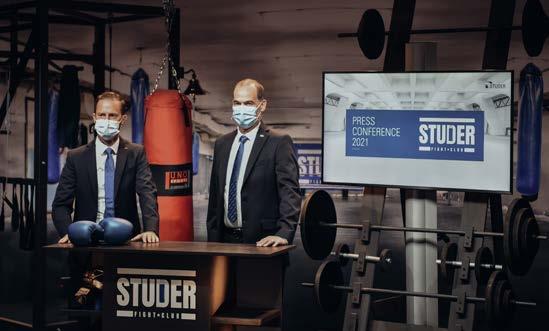
11 minute read
Studer blikt terug op succesvol gevecht met uitdagende tegenstander
Onder het gemeenschappelijke motto ‘Studer Fight Club’, werd dit jaar de Studer persconferentie en de Motion Meeting vanuit de speciaal voor deze conferenties opgezette boks- en trainingsstudio gepresenteerd. Volgens Studer zijn er de afgelopen twaalf maanden genoeg uitdagingen geweest, maar is de machinebouwer overeind gebleven door talrijke projecten op het gebied van digitalisering, service, een breed portfolio en investeringen in nieuwe producten en machines. Met die basis kijkt het bedrijf vol vertrouwen naar de toekomst.
De economische situatie was al aan het verslechteren voordat de wereldeconomie een nieuwe dreiging aan de horizon zag verschijnen: de coronapandemie. “Aanvankelijk was het een kwestie van het personeel en het bedrijf beschermen”, zegt Jens Bleher, CEO van Fritz Studer. Studer reageerde snel en voerde consequent uitgebreide beschermingsmaatregelen in, waardoor besmettingen in de fabriek konden worden voorkomen. “Studer heeft de pandemie en de omzetdaling met succes doorstaan en over het algemeen is de situatie aanzienlijk beter dan tijdens de financiële crisis tien jaar geleden. Zo konden we overall 60% meer orders noteren dan in 2009 en de teruggang in de automobielsector hebben we opgevangen met nieuwe klanten, veelal uit China en Zuid Amerika. Verder hebben we de belangrijkste ontwikkelingen voortgezet en is het productportfolio verder ontwikkeld. Studer investeerde in 2020 en zal dat dit jaar blijven doen", aldus Bleher.
Breed portfolio
Studer noemt het brede portfolio van verschillende universele externe, interne, productie- en conventionele rondslijpmachines als een belangrijke succesfactor in het gevecht tegen de pandemie en de economische uitdagingen. “De in 2019 gelanceerde S33 was
Sandro Bottazzo en Jens Bleher vertellen tijdens de ‘Studer Fight Club’ persconferentie hoe Studer het afgelopen jaar heeft doorlopen. (foto’s: Studer)
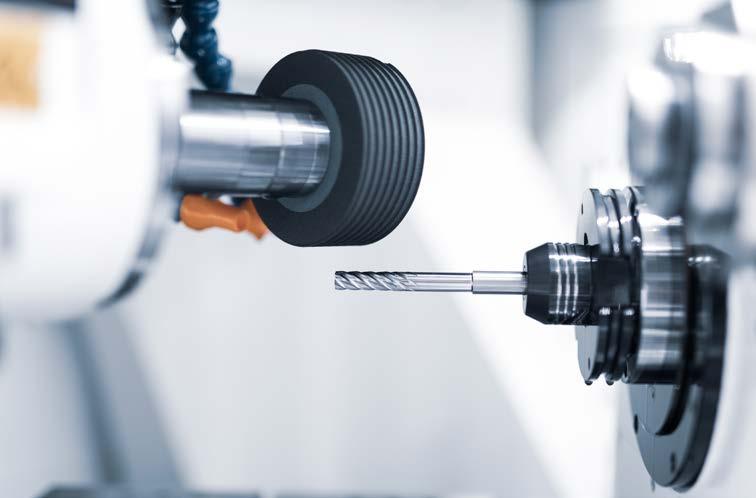
Ontwikkeling heeft tijdens de coronapandemie niet stilgestaan bij Studer. Op de EMO presenteert het bedrijf het resultaat van deze ontwikkelingen.
vorig jaar verreweg de best verkochte rondslijpmachine, gevolgd door de interne slijpmachines, de nieuwe S31 en de nieuwe favorit. De verkoop van de instapslijpmachine, de favoritCNC, heeft zich ook positief ontwikkeld”, vertelt Sandro Bottazzo, CSO bij Fritz Studer. Een andere belangrijke succesfactor van het afgelopen jaar was Studer Customer Care. "Dankzij ons lokale, klantgerichte netwerk van meer dan 130 servicemonteurs wereldwijd, konden we onze klanten ondanks de internationale beperkingen continu ondersteunen tijdens de pandemie. We zijn ervan overtuigd dat blijvend succes alleen mogelijk is als we dicht bij onze klanten staan. Daarom zullen we het servicenetwerk blijven uitbreiden", benadrukt Bottazzo.
Digitalisering voert boventoon
De coronapandemie heeft de ontwikkeling van digitaliseringsoplossingen versneld. Zo heeft de United Grinding Group een roadmap voor digitalisering ontwikkeld, die Studer stap voor stap implementeert. “We gebruiken alle technologieën die we onze klanten aanbieden ook in onze eigen productie. Werkinstructies, testprocessen en checklists zijn grotendeels papierloos en altijd in de laatste versie beschikbaar. Tablets en beeldschermen zijn al onmisbare hulpmiddelen geworden voor onze montagespecialisten”, legt Stephan Stoll, COO van Fritz Studer, uit. De productiemonitor van United Grinding Digital Solutions bijvoorbeeld, geeft op elk moment een overzicht van de bedrijfsstatus van de productiemachines en assemblage-apparatuur van het bedrijf. Het toont in real-time of en welke machines in bedrijf zijn en kan de bijbehorende productiegeschiedenis weergeven. Niet alleen kunnen Studer-machines en andere machines van de United Grinding Group in de productiemonitor worden geïntegreerd, maar via de gestandaardiseerde umati-interface kan ook een grote verscheidenheid aan externe productieapparatuur en fabrikanten worden geïntegreerd. "Het werkstation maakt ook veel gedetailleerde analyses en statusrapporten mogelijk, inclusief informatie over orderstatussen en onderhoudsintervallen", zegt Stoll. Digitalisering is voor Studer een belangrijk thema bij de ontwikkeling van nieuwe technologie. "Nu en in de toekomst hebben we een transparante maar veilige verbinding nodig, zodat procesinformatie gemakkelijk naar externe systemen kan worden overgebracht. Dit zijn precies de voordelen die de OPC-UA-oplossing biedt. In ons Tech Center zijn alle machines via OPC-UA verbonden met onze United Grinding Digital Solutions-toepassingen volgens de universele umati standaard", zegt Daniel Huber, CTO van Fritz Studer.
Nieuwe technologie
Momenteel werkt Studer aan de innovaties voor de EMO 2021 in Milaan. Hoewel het bedrijf nog niet veel wil vertellen over de highlights die het daar zal presenteren, liet het tijdens de persconferentie wel een andere technologische innovatie zien. Studer heeft jarenlange ervaring in het gebruik van machinaal geïntegreerde lasermeettechniek voor het meten van slijpschijven of werkstukken. Op basis van deze kennis, de nieuwste lasermeettechnologie en bestaande gereedschapsbewakingssystemen die in andere industrieën worden gebruikt, heeft Studer een nieuw lasermeetsysteem ontwikkeld. LaserControl, de nieuwste generatie van het lasermeetsysteem, is niet alleen geschikt voor het contactloos meten van snijkanten van gereedschappen, maar ook voor het meten van roterende werkstukken. Door werkstukken te kunnen meten, zonder dat het proces stilgezet hoeft te worden, kan de meettijd aanzienlijk worden verkort. Dankzij de hoogwaardige laseroptiek en de nieuwste evaluatietechnologie kan er snel, nauwkeurig en betrouwbaar worden gemeten. De dynamische en contactloze metingen maken ook kwaliteitsbeoordelingen van zeer nauwkeurige PCD-gereedschappen mogelijk.
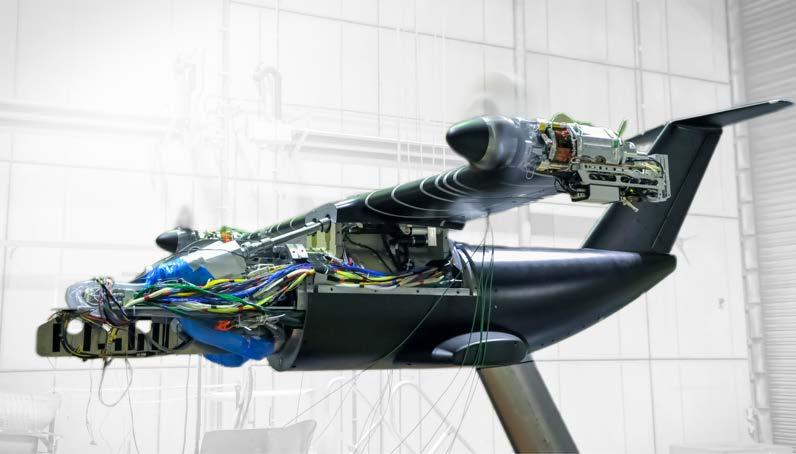
NLR ontwikkelt en produceert complexe testmodellen voor het uitvoeren van onder meer krachtmetingen. (foto’s: Royal NLR en Tim Wentink)
Het Koninklijk Nederlands Lucht- en Ruimtevaartcentrum (NLR) in Marknesse is de verbindende schakel tussen onder andere de luchtvaartindustrie en de wetenschap. Het kennisinstituut bevindt zich daarom in de frontlinie van nieuwe ontwikkelingen en innovaties. Efficiëntere motoren, nieuwe materialen, het gebruik van duurzame brandstoffen zoals waterstof en vergaande aerodynamische verbeteringen, vragen om steeds complexere testmodellen en dus om nieuwe bewerkingstechnologieën. Om aan die vraag te kunnen voldoen heeft NLR geïnvesteerd in een draadvonkmachine van Mitsubishi.
De behoefte aan een klimaatneutrale luchtvaart brengt een versnelling in de ontwikkeling van nieuwe innovaties. NLR streeft samen met de luchtvaartindustrie naar het verminderen van vliegtuigemissies. De netto uitstoot van broeikasgassen zoals CO2 en stikstofoxiden (NOX) zou in 2050 nul moeten zijn. Deze doelstelling is ambitieus maar volgens NLR mogelijk zolang innovatie ruim baan krijgt. “De beweging richting groen vliegen is echt in opmars. Het duurt altijd enkele jaren voordat een nieuwe trend bij ons in de werkplaats zichtbaar is. De eerste ontwikkelingen die zijn geënt op duurzaam vliegen krijgen nu ook daadwerkelijk vorm in de modellen die we maken. Door de coronacrisis en de impact op de luchtvaartindustrie merken we dat sommige vliegtuigbouwers even op de rem hebben getrapt qua innovatie, maar de algemene tendens is dat de komende jaren grote stappen gemaakt zullen worden. Dat heeft veel effect op de modellen die we ontwikkelen en de productietechnologie die daar bij hoort”, vertelt Bert Idserda, teamleider van de productieafdeling binnen NLR.
Krachtmetingen in het model
NLR ontwikkelt aan de hand van een idee en een schil van het vliegtuig een model om krachten en drukken te kunnen testen en meten. Het bedrijf bedenkt en maakt daarbij ook het binnenwerk en de meetsystemen, zodat er met één model een complete krachtmeting gedaan kan worden. Daar zit de expertise van NLR. Modellen zijn er in een grote verscheidenheid aan afmetingen. Zo maken ze bijvoorbeeld raket- en vliegtuigmodellen van 1 x 1 meter oplopend tot modellen van 6 x 6 meter met daarin talloze onderdelen. Idserda: “Vroeger werden er veel meer modellen gemaakt om de krachtmetingen en testen te kunnen doen. Zo maakten we eerst een model voor de windtunnel. Vervolgens maakten we met de data die we verkregen uit de windtunneltest weer een nieuw model waar we de volgende reeks krachtmetingen mee konden doen om uiteindelijk tot de definitieve versie te komen. De rekenmodules van tegenwoordig zijn veel geavanceerder dus is nu één model voldoende om aan te tonen dat het rekenmodel klopt. Het gevolg is dat er meer en meer techniek in een model gebracht moet worden en dit resulteert in complexere modellen en nauwkeurigere onderdelen.”
Exotische materialen
Om alle onderdelen en meetsystemen in het model te kunnen plaatsen, is er ruimte nodig. Om die ruimte te verkrijgen wordt
Onderdelen in modellen worden steeds complexer. Dit vraagt om nieuwe productietechnologieën zoals draadvonken.

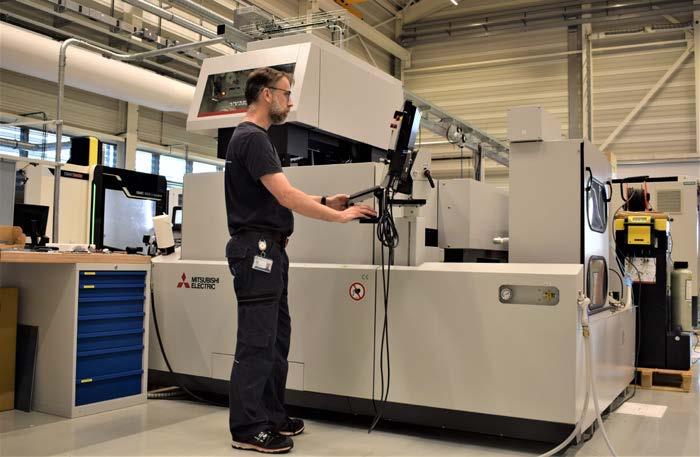
Voor het vonken van complexe onderdelen maakt NLR sinds een jaar gebruik van een Mitsubishi Electric MV2400S Z+ NewGen draadvonkmachine met een grote Z-as.
de wanddikte van het model en de onderdelen steeds dunner en complexer geconstrueerd. Daarnaast zorgt de transitie naar duurzaam vliegen voor langere en slankere vliegtuigconstructies om meer draagkracht en een efficiëntere aerodynamica te realiseren. Dunner, slanker en langer gaan over het algemeen moeilijk samen met hoge krachten. Om toch de krachten kwijt te kunnen in het meetmodel, gebruikt NLR daarom in toenemende mate exotische materialen die bestand zijn tegen hoge krachten. Deze materialen zijn moeilijk te frezen, waardoor NLR steeds meer de focus legt op draadvonken. Om de productie van complexe componenten zoveel mogelijk in eigen huis te houden heeft NLR geïnvesteerd in een Mitsubishi Electric MV2400S Z+ NewGen draadvonkmachine die is geleverd door Dymato uit Veenendaal. “Met frezen liepen we tegen beperkingen aan. Delen van de vleugel bijvoorbeeld, bestaan uit dunne, lange segmenten die moeilijk spanningsvrij zijn te frezen. Met draadvonken kunnen we die delen nu heel efficiënt en met een hoge maat- en oppervlaktenauwkeurigheid bewerken. Bij een ander project hadden we een model waarbij gaten zuiver tegenover elkaar moesten zitten. Met draadvonken hebben we die gaten binnen de toleranties weten te bewerken. Dit was met frezen onhaalbaar. Een bijkomend voordeel van draadvonken is dat je niet het hele blok materiaal hoeft te verspanen om tot het onderdeel te komen. Zo draadvonken we nu titanium bladen die voorheen werden geproduceerd door het hele blok materiaal weg te frezen. Omdat met draadvonken niet al het onnodige materiaal wordt omgezet in spanen, kunnen we de reststukken later hergebruiken om bijvoorbeeld kleinere onderdelen te produceren. Met name bij dure legeringen scheelt dit aanzienlijk in materiaalverbruik en -kosten. Het efficiënter omgaan met materiaal is echt gegroeid sinds de draadvonkmachine er is”, aldus Idserda.
Grote Z-as en eenvoudige besturing
De reden dat NLR heeft geïnvesteerd in een draadvonkmachine van Mitsubishi, heeft onder andere te maken met de bouwwijze die perfect aansluit bij hun wensen. Zo is de MV2400S leverbaar met een Z-as van 310 mm óf, in de Z+-uitvoering, met een bereik van 425 mm. Dat grotere bereik past perfect bij de productafmetingen die NLR met de 3D-metaalprinter kan printen. Zo zet NLR de draadvonkmachine in om 3D-geprinte titanium en magnesium producten van de bouwplaat te verwijderen en na te bewerken. Een belangrijk pluspunt van de Z+-uitvoering is volgens NLR dat ondanks de grotere Z-as dezelfde nauwkeurigheden zijn te behalen als met de korte uitvoering. Het optical drive systeem met het Mitsubishi Tubular Direct Drive aandrijfsysteem en de polymeer glasvezelbekabeling maken die hoge nauwkeurigheid mogelijk. De MV2400S Z+ heeft een bereik van 600 mm x 400 mm x 425 mm (XxYxZ) en kan beladen worden met werkstukken met een massa tot maximaal 1.500 kg. Hierdoor kan NLR de machine inzetten voor de nauwkeurige bewerking van zowel kleine als grote onderdelen. Naast de machine-afmetingen, was de eenvoudige besturing een groot pluspunt voor NLR. Peter Steenhuis, operator bij NLR vertelt: “We maken voornamelijk enkelstuks en omdat we aan de machine programmeren, was een eenvoudige en flexibele besturing essentieel. Dat hebben we bij Mitsubishi gevonden.”
Doorlooptijd verkorten
NLR probeert zoveel mogelijk in eigen huis te produceren. Voorheen werd al het draadvonkwerk uitbesteed. “Omdat draadvonken een relatief niche bewerkingstechniek is, heeft NLR lang gewacht met het investeren in een eigen machine. Nadat twee jaar geleden een nieuwe werknemer de benodigde kennis meebracht, kon NLR de volgende stap zetten. Samen met Dymato hebben we in het voortraject verschillende machines in het veld bezocht en veel relevante kennis opgedaan. Inmiddels volgen er drie werknemers een opleiding bij Mitsubishi om de draadvonktechniek eigen te maken. Ons uiteindelijke doel is om alle complexe componenten zelf te produceren. Op die manier hoef je niet met je ontwikkelingen naar buiten en kunnen we de doorlooptijd verkorten. Zo hebben we vorig
jaar in samenwerking met Universiteit Twente een krachtenbalans ontwikkeld, waarmee de krachten op hun modellen gemeten kunnen worden. In dat project is het model zo ontworpen, dat het volledig in eigen huis geproduceerd kon worden. Hierdoor had het project een hele korte doorlooptijd.”
Draadvonkmogelijkheden passen ontwerp aan
De draadvonkmachine van Mitsubishi is inmiddels een jaar in gebruik. NLR heeft de machine aangekocht in de veronderstelling dat er voor ongeveer 800 uur aan draadvonkwerk per jaar zou zijn. In het eerste jaar werd al ruim 500 uur gevonkt, ondanks dat NLR de machine nog moest leren kennen. Volgens Idserda worden modellen naarmate de kennis van draadvonken toeneemt binnen het team, vaker speciaal ontworpen voor de mogelijkheden van het draadvonken. “Toen vroeger het drieassig en later het vijfassig frezen werd geïmplementeerd, zag je ook een sprong in de ontwikkeling van onderdelen en modellen. Dat zien we nu ook gebeuren met de komst van de draadvonkmachine. Zo hebben we bijvoorbeeld ineens ontwerpen met vierkante gaten en scherpe hoeken. Dat was voorheen ondenkbaar. Onze afdeling is dus sterk ontwikkeld door de draadvonkmachine. In de toekomst zal het draadvonken een alsmaar grotere rol gaan spelen in de productie van modellen en uiteindelijk ook in de stap naar een groene luchtvaart”, concludeert Idserda.

Bert Idserda noemt de eenvoudige en flexibele besturing van Mitsubishi een groot voordeel voor het programmeren van enkelstuks.
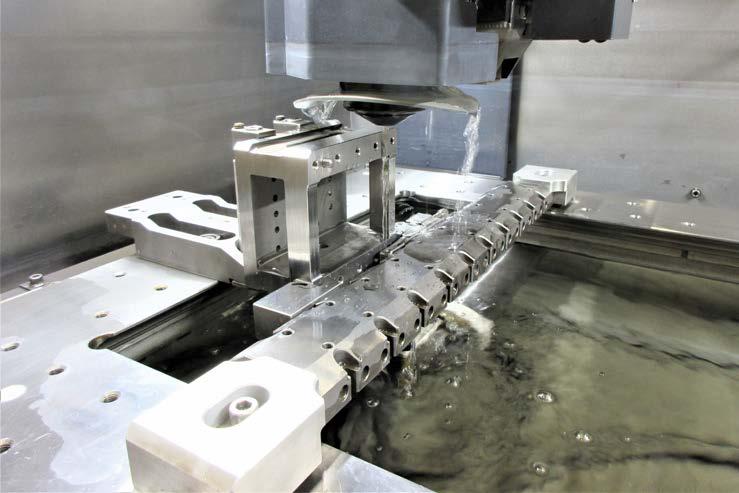