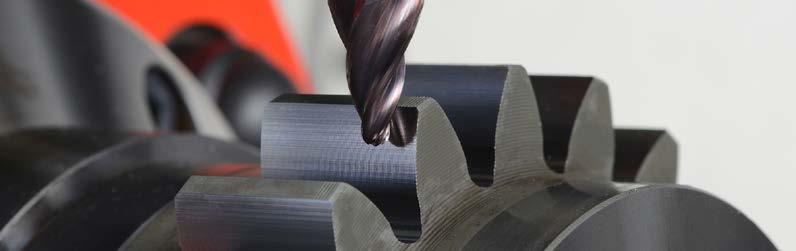
3 minute read
Vliegtuigmotoren profiteren van vijfassig frezen en slijpen
Een onderzoeksteam van het Fraunhofer Instituut voor Productietechnologie IPT in Aken heeft in een consortiumproject een procesketen ontwikkeld waarin dubbele spiraalvormige tandwielen worden vervaardigd met behulp van vijfassig frezen met aansluitend vijfassig slijpen. De tandwielen worden met het nieuwe proces lichter en duurzamer, waardoor ze meer geschikt zijn voor gebruik in moderne vliegtuigmotoren.
Het gebruik van dubbele spiraalvormige tandwielen in vliegtuigmotoren heeft diverse voordelen. Een kenmerk van deze tandwielen is dat de tanden onder een hoek staan ten opzichte van de as waarop het tandwiel is gemonteerd. Omdat de tanden hierdoor langer zijn ten opzichte van de tanden van een recht tandwiel, is het mogelijk om met een kleiner tandwiel dezelfde overbrenging te realiseren. Hierdoor kan er compacter geconstrueerd worden. Daarnaast zorgen de langere tanden voor een hogere belastingsopname dankzij meer contactoppervlak. En zeker niet onbelangrijk, dankzij de langere tanden grijpen de tandwielen geleidelijk in, waardoor een soepele loop ontstaat. Het voordeel: Minder trillingen, schokbelastingen, slijtage en geluid.
Afwikkelfrezen en afwikkelslijpen
Spiraalvormige tandwielgeometrieën worden normaal gesproken bewerkt met productieprocessen, zoals afwikkelfrezen (hobbing) en afwikkelslijpen. Het nadeel hiervan is, is dat de frees- en slijpgereedschappen grote in- en uitloopzones vereisen met als gevolg brede groeven tussen de tandwieldelen. Hierdoor zijn

Uit proeven is gebleken dat het vijfassig slijpen van tandwielen een tamelijk negatief effect heeft op de macrogeometrie van de tandwielen, maar de levensduur ervan aanzienlijk verbetert.
tandwielen relatief zwaar en hebben ze grote afstanden tussen de afzonderlijke tanden - die beide nadelig zijn voor gebruik in vliegtuigmotoren. Met de wereldwijde behoefte naar zuinigere vliegtuigen neemt de vraag naar lichtgewicht onderdelen toe, waardoor conventionele productiemethoden steeds vaker niet meer voldoen.
Vijfassig frezen én slijpen gecombineerd
In het onderzoeksproject ‘Compact gears 4 turbo’ heeft het Fraunhofer IPT samen met vijf industriële partners (ModuleWorks, Werkzeugmaschinenlabor WZL, Aixpath, Rolls-Royce Deutschland en Aerospace Transmission Technologies) nieuwe procesketens ontwikkeld voor de productie van kleine en lichte tandwielen met smalle groeven voor vliegtuigmotoren. De procesketens lopen van het digitaal modelleren van de tandwielen (CAD) en computerondersteund procesontwerp (CAM) tot de fabricage en de daaropvolgende kwaliteitstests. Voor het eerst realiseerden de projectpartners een procesketen voor de fabricage van de tandwielen door middel van vijfassig frezen, gevolgd door vijfassig slijpen. Het slijpen van het oppervlak is van groot belang voor de werking van het onderdeel, aangezien een lagere oppervlakteruwheid de wrijving tussen de tandflanken in het tandwiel vermindert. Zeker bij een spiraalvormig tandwiel ontstaat er veel glijdend contact tussen de tanden, waardoor een lage oppervlakteruwheid essentieel is om warmte-ontwikkeling en slijtage te voorkomen. Een bijzondere uitdaging voor de projectpartners was de integratie van slijpen in de procesketen, omdat volgens Fraunhofer IPT het vijfassig slijpen van tandwielen tot dan toe nog zo goed als onontgonnen gebied was. Het combineren van de twee processen – frezen en slijpen – in zo’n procesketen werd gezien als “pionierswerk”. Om tot geschikte processtrategieën te komen, was in eerste instantie dan ook uitgebreid fundamenteel onderzoek nodig. Vooral het identificeren van de juiste gereedschappen voor het vijfassig slijpen van de tandwielen was een grote klus.
CAM-software
Tijdens het praktijkonderzoek bleek dat het vijfassig frezen bepalend is voor de maximaal haalbare vormnauwkeurigheid van de tandwielen. Uit het onderzoek blijkt ook dat het daaropvolgende vijfassig slijpen geen positief effect op de macro-geometrie van de tandwielen; integendeel, het heeft eerder een nadelig effect. Het slijpproces moest daarom zo worden ontworpen dat de geometrie van het tandwiel slechts in geringe mate zou veranderen, maar dat de ruwheid van het tandwieloppervlak zo veel mogelijk wordt verminderd. Deze en andere bevindingen voor het ontwerp van de nieuwe procesketen werden samengebracht in de ontwikkeling van een CAM-planningssoftwarepakket voor Siemens NX. De software wordt gebruikt voor procesplanning en omvat ook trajectplanning voor het frezen en slijpen van de complexe spiraalvormige tandwielgeometrieën.
Lichter en duurzamer
Uit testen met verschillende tandwielen blijkt dat het vijfassig slijpen de levensduur van de tandwielen aanzienlijk verbetert. Dit is te wijten aan de verminderde oppervlakteruwheid. De nieuwe procesketen maakt het samen met de CAM-planningssoftware mogelijk om duurzamere tandwielen voor lucht- en ruimtevaarttoepassingen compacter en eenvoudiger te vervaardigen. Het Fraunhofer IPT is van plan zijn deskundigheid op dit gebied in vervolgprojecten verder te verdiepen. Het onderzoeksproject "Compact gears 4 turbo” werd gefinancierd door het Duitse federale ministerie voor Economische Zaken en Energie (BMWi).