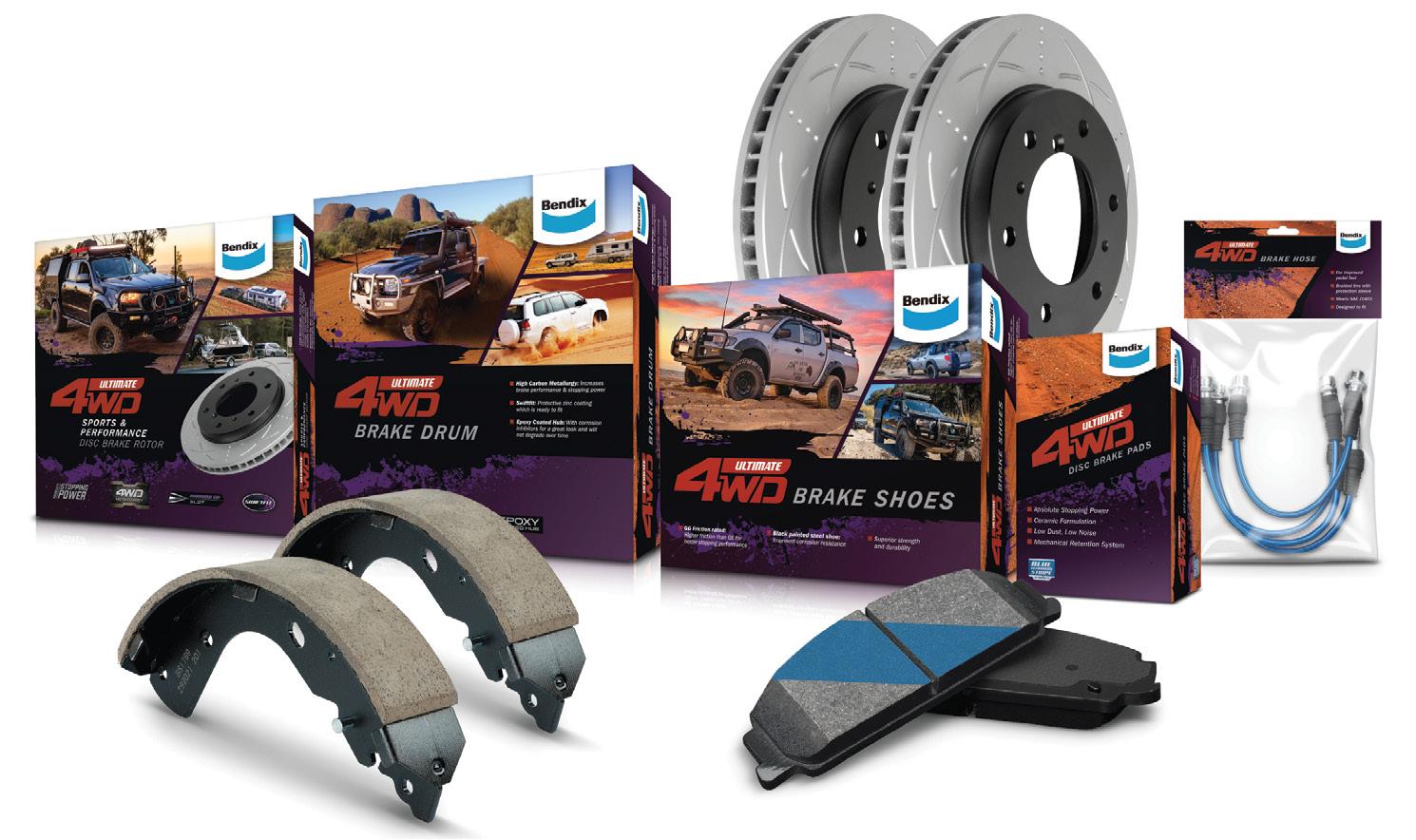
6 minute read
Member Feature: Bendix - Truly Aussie-made
TRULY AUSSIE-MADE
Bendix has been making brake pads in Australia for nearly seven decades
Bendix has been making brake pads in the Victorian regional city of Ballarat for 67 years. The company claims that since the 1950s it has set new standards in driver safety, performance and comfort, and it believes it will be around for many more decades and is already developing automotive products for EVs in an effort to futureproof the business. Founded in 1955, Mintex, as the company was originally known, was established to meet the needs of Australian motorists. “In the early days there weren’t any manufacturers in Australia for brake pads so Bendix was formed to meet the needs of the market, initially Bendix made drum brake linings,” FMP Group Marketing Manager, Ian Bott, says. Initially, it was a modest manufacturing plant initially employing just 30 people; however, a short time later the fledgling company was bought by the US company Bendix Corporation and Bendix Mintex was formed. “Bendix Corporation was a very successful brake manufacturer in the US in the 1960s, it was agreed to use this as leverage for the business in Australia,” Ian says. During the 1970s Bendix Mintex developed new and innovative manufacturing processes for the production of disc brake pads that would see it begin exporting Australian technology overseas. These developments continued as the company began working on new friction materials to further improve the performance and competitive pricing of Australian brake pads. “Bendix had OE programs with the local manufacturers (Ford/Holden/Mitsubishi) and this drove new technologies and flowed into the aftermarket,” Ian says. “Bendix leveraged technology partnerships with international friction businesses bringing those to the Australian market. The business also invested in the R&D facility in Ballarat where products could be developed locally. “Early materials were medium friction but didn’t last long at high temperature or loads, additionally comfort factors such as noise and vibration were not a high consideration in Australia until the ‘90s. Early materials had around eight to 10 ingredients versus today where it is anything from 13 to 15. “Today’s materials are more complex as they need to maintain a stable friction level across a wider range of operating temperatures with additional vehicle weight. Additionally, dust and rotor life are now also a factor. “The growing car parc diversity has made us offer more formulation variants within the segments, for example 4WD covers anything from a RAV4 through to a Landcruiser, these require different materials, so each Bendix Product within the range has different formulations depending on the vehicle type.” Advanced technological development in metal presses resulted in higher quality backing plates to match the new friction materials and in 1993 the company’s dedication to innovation and quality saw Bendix Mintex named Manufacturer of the Year by the Australian Automotive Aftermarket Association. The company’s focus on research and development in the late 1990s coupled with a heavy investment in a state-of- the-art sound analysis laboratory resulted in a strong emphasis on reducing brake pad noise for smoother and quieter braking. In line with the continuing growth of the company within Australia and in overseas markets the company changed its name in 2002 to become FMP Group (Australia) Pty Ltd (Friction Materials Pacific). By 2005 further Bendix advanced developments were launched with General CT plus Heavy Duty brake pads with a revolutionary Titanium Stripe. The new and innovative technology provided instant friction to deliver sure stopping power from the moment the customer first drove out of the workshop. With the superior quality standard within the company, the ultimate level of quality accreditation was achieved in 2006 for OEM supply to the car companies making Bendix one of the key suppliers to the Australian automotive industry. High performance Street-Road-Track brake pads were introduced in 2007 to wide acclaim, meeting the needs of serious drivers with powerful vehicles being driven on the limit. Further recognition was awarded to this impressive Victorian manufacturing company in 2008 when Bendix was inducted into the prestigious Victorian Manufacturing Hall of Fame. Innovation continued with the launch of premium quality Bendix brake shoes in 2009, the 2010 release of the revolutionary ‘STEALTH Advanced Technology’ brake pads – which set new standards in smooth, quiet braking – and 2011
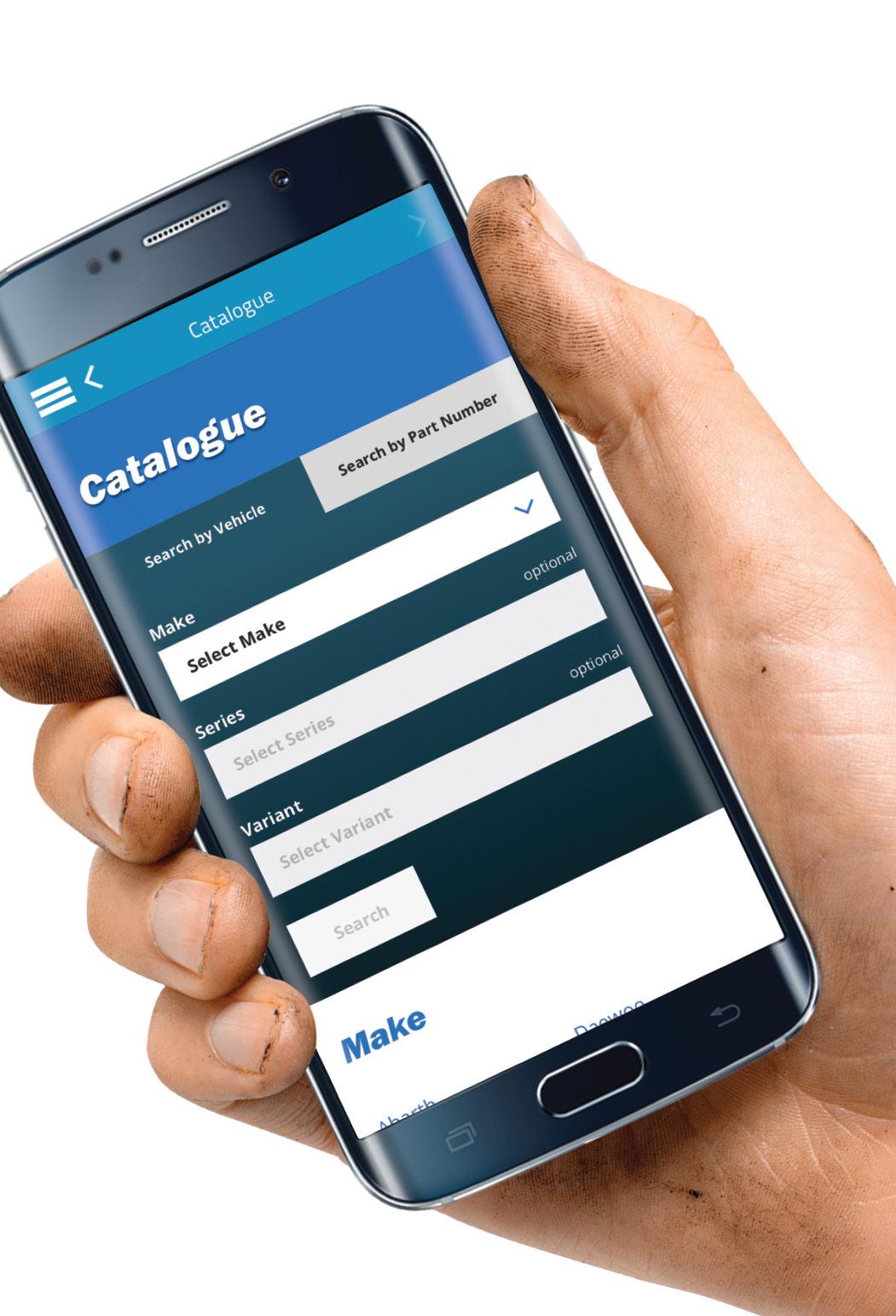
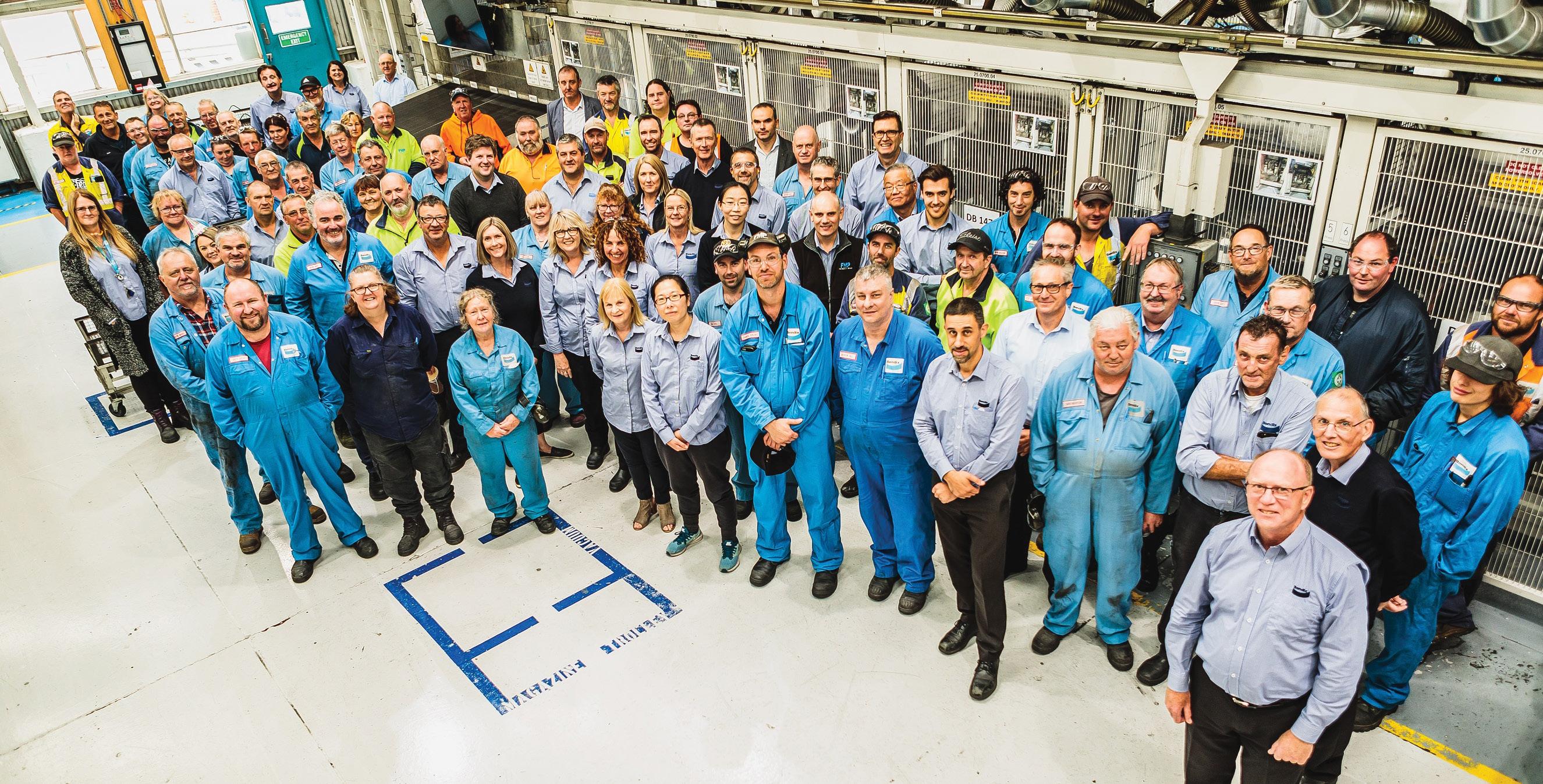
brought the beginnings of a very successful and ever-expanding ancillary range of brake products such as brake lube, brake fluids, brake wear sensors. The Blue Titanium Stripe, Hybrid Fusion Technology and the Euro+ range all followed, giving workshops access to an extensive offering of high-performance brake solutions that reduced fitting time and improved braking performance for customers. Workshops have directly benefitted from Bendix innovation with the development of a unique marketing tool in the award-winning Bendix Brake Identifier App – a mobile tool for the mechanic’s phone that reduces the time in finding the correct replacement part whilst a job is underway. Investment in the plant at Ballarat has been significant with the latest being the commissioning of a $3.5 million IAG moulding press as part of an $8.8 million upgrade of the manufacturing facilities to deliver world-class high-tech products for the Asia Pacific region. As well as R&D, Bendix spends significant resources on testing for both performance and safety. “Bendix key test areas focus on performance, wear and noise, we dyno test in the lab for most work – both development and confirmation testing and finish with vehicle testing, where we focus on noise and durability,” Ian explains. “Testing is continuous for us to ensure we offer a competitive product in an ever-changing market.” So what does the future hold for brake pad manufacturers? Like many components in Internal Combustion Engine (ICE) vehicle’s, companies producing EVs have transformed braking systems. Many have adopted and developed highly sophisticated regenerative braking systems, which redirect energy back into the vehicles batteries. Where does this leave the humble brake pad? “We see friction as a relevant component in the future. Our firm belief is friction will play a role whether its EV or Hybrid,” Ian says. “With the electrification of vehicles, the brake pad is still required to pick up where the regeneration system stops and in emergency situations. EVs use friction braking and pads play a dual role in slowing the vehicle. Friction formulations will continue to be developed in the future to meet the system needs. Bendix will develop formulations to meet future vehicles.” Ian believes the EV braking systems of the future will still require servicing, but specialists’ tools will be required, making it difficult for DIYers. “The greater integration of electronics will mean vehicle specific scan tools need to be used, which is happening now,” he said. “Manufacturers are designing cars that require specific tools to service the vehicles. This can be anything from scan tools to specific hand tools.” Bendix is currently manufacturing over one million sets (including exports) of brake pads every year, all of which are designed and tested in Australia, and the company claims that it is not going to slow down any time soon. For more information, visit www.bendix.com.au
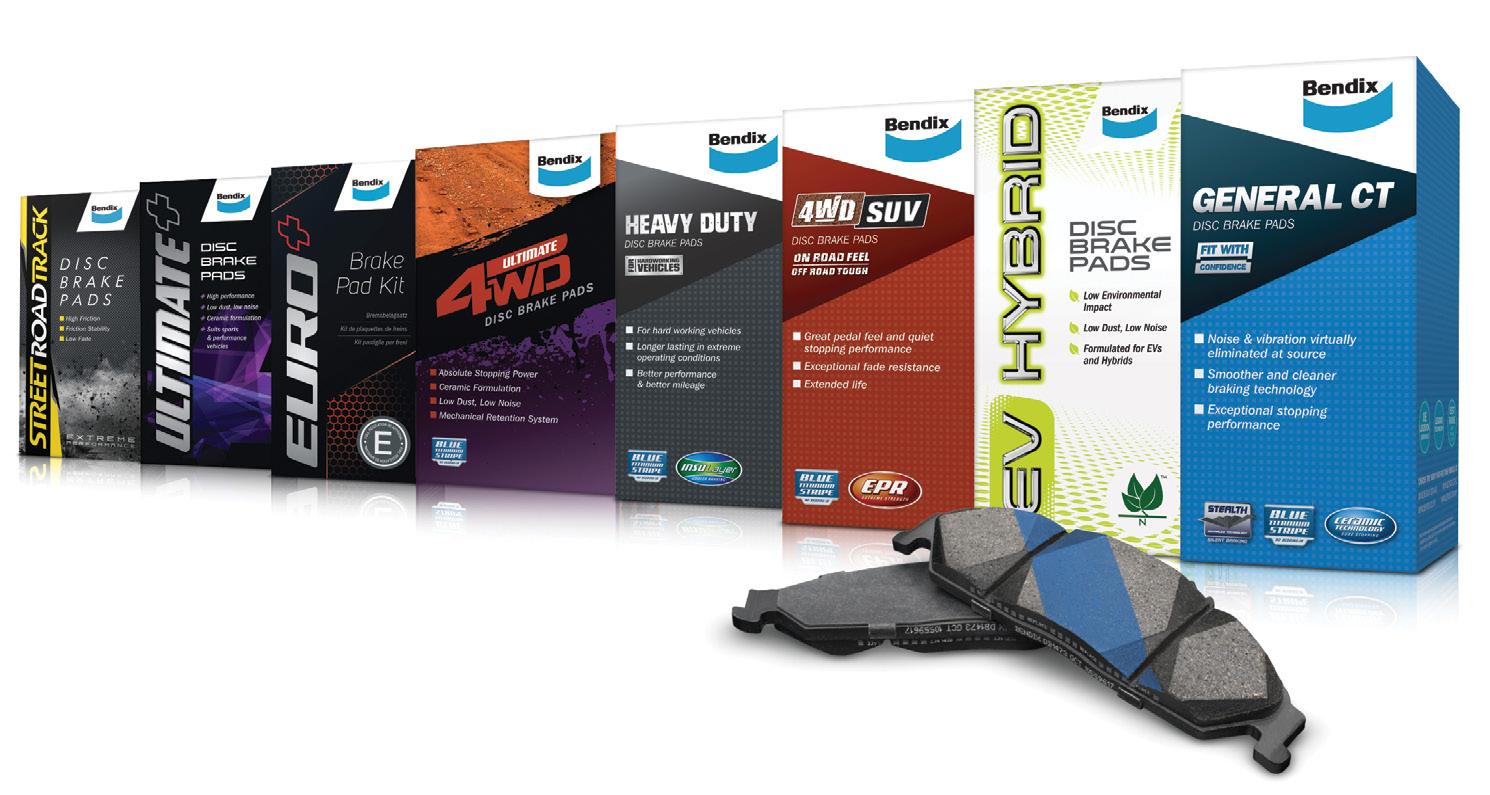