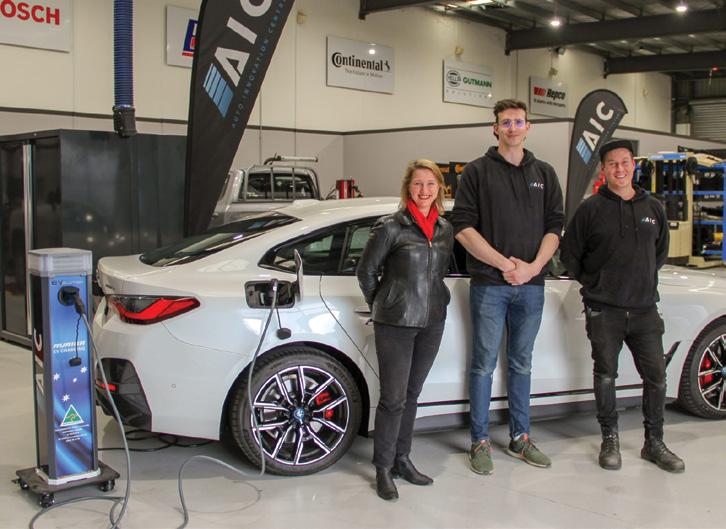
4 minute read
AIC awarded Victorian Government ZLEV Grant
The Auto Innovation Centre is a centre of excellence for the automotive industry
The Auto Innovation Centre (AIC) will become a new Zero and Low Emission Vehicle (ZLEV) hub, supporting the vehicle evolution within the aftermarket manufacturing, service, repair and modification sectors. The AIC was awarded a grant by the Victorian Government as part of its Zero Emission Vehicles Commercial Sector Innovation Fund. Working closely with the Australian Automotive Aftermarket Association (AAAA), the grant will allow the AIC to break down barriers for aftermarket product manufacturers to ensure modified ZLEVs remain fit for purpose, and provide automotive technicians with opportunities to be upskilled on ZLEV technology. Both initiatives are designed to support consumers to access safe, reliable and affordable ZLEV aftermarket parts, servicing and repair. The AIC enables aftermarket companies to fast-track product development through vehicle and product level testing and 3D scanning and owns a fleet of vehicles and a modern, wellequipped workshop and training facility. “The AIC is uniquely placed to support the automotive industry’s uptake of Zero Emission Vehicles given our existing role supporting the aftermarket with testing services, and our facility built with automotive training and development in mind,” AIC Managing Director, Luke Truskinger, said. “The AIC will be investing in ZLEVs, charging infrastructure and specialised ZLEV tools and equipment to be at the forefront of this important evolution for the automotive industry. “The AIC will become a hub for aftermarket companies wishing to develop new products for these vehicles, and become a key training facility for technicians to gain the specialist knowledge required to repair and maintain ZLEVs.” The AAAA is the independent national body responsible for the aftermarket industry, which includes vehicle service and repairers, as well as product manufacturers. ZLEVs are becoming an area of increased focus for the association and the aftermarket industry, which comprises over 50,000 businesses and contributes $25 Billion to the economy annually. “The AAAA actively monitors ZLEV take-up rates and barriers to ensure as an industry we are able to respond to the challenges of this emerging sector,” AAAA Chief Executive Officer, Stuart Charity, said. “It is our role to support our sector to develop and fulfill important new industry responsibilities in relation to the growing segment of ZLEVs within the automotive industry.” The Auto Innovation Centre’s new ZLEV capability will come online in early 2023. The AAAA says it will work closely with the AIC to develop and facilitate education and training programs to fast-track the support of this vehicle evolution for the automotive industry. The AIC a cutting-edge facility for the automotive aftermarket. The centre of excellence is increasing capability of automotive companies and aiding in new product development for local and export markets. Utilising the latest technology and equipment and providing crucial data and testing services, the AIC is transforming the automotive aftermarket industry. For more information about the AIC, visit www.autoic.com.au
MEYLE ATTENDS UN CONFERENCE
The manufacturer focused on sustainability and conserving plastics
The UN Climate Change Conference was recently held in Egypt and Hamburg manufacturer Meyle was there to input new ideas with its own sustainability endeavours. Climate change, the energy transition, the scarcity of resources, increased sustainability awareness and alternative drives – for manufacturers in the independent aftermarket, the need to act has never been as great as it is today. Meyle says it has now achieved an important milestone – the company is conserving 15 tonnes of plastic a year by eliminating plastic caps from Meyle axial rods, control arms, ball joints and tie rods. For some time now, Meyle says it has been doing without the protective caps it previously used in the packaging for its axial rods. And now, control arms, ball joints and tie rods will likewise be delivered in optimised packaging that makes the plastic caps superfluous. Meyle is additionally saving four tonnes of plastic a year by reducing its use of stretch wrap and thanks to its 2018/2019 transition to paper-based adhesive tape and shipping envelopes. Meyle is therefore now saving around 19 tonnes of plastic a year. Meyle says it continuously works with its partners on increasing efficiency throughout the value chain and on doing business more sustainably. The manufacturer explains it has been working to improve its carbon footprint since 2018 and recently presented the first climate-neutral product line in the independent aftermarket – the carbon emissions of Meyle HD steering and suspension parts are offset in cooperation with ClimatePartner. “The impacts of climate change and the consequences of environmental destruction do not lie in the future,” Meyle AG Executive Board Member, Marc Siemssen, said. “We must question our consumption and our conduct regarding resources today. Meyle has therefore taken a close look at its use of plastics as one of many topics and we are consciously eliminating them from more and more parts. “In addition, the concept behind Meyle HD has
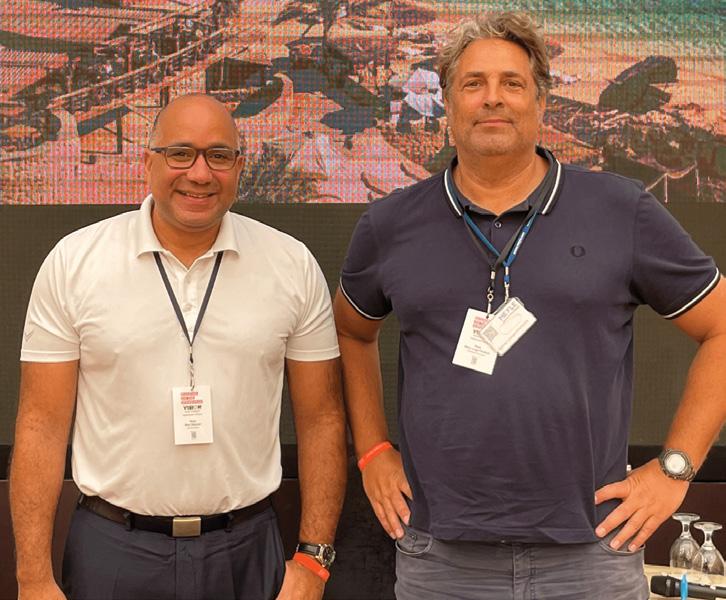
On site at the UN Climate Change Conference: Marc Siemssen, Member of the MEYLE AG Executive Board and Rainer Lange-Hitzbleck, Vice President Marketing and Communication.
been sustainable from the beginning – rather than buying a new part, which involves heavy resource usage, precedence is given to repairs performed using a spare part which is more durable than the original.” Meyle states that it signed up to the UN Global Compact in 2021 to systematically accelerate and steadily expand its sustainability activities. Its current Report on Progress regarding human rights and the environment is available at www.meyle.com