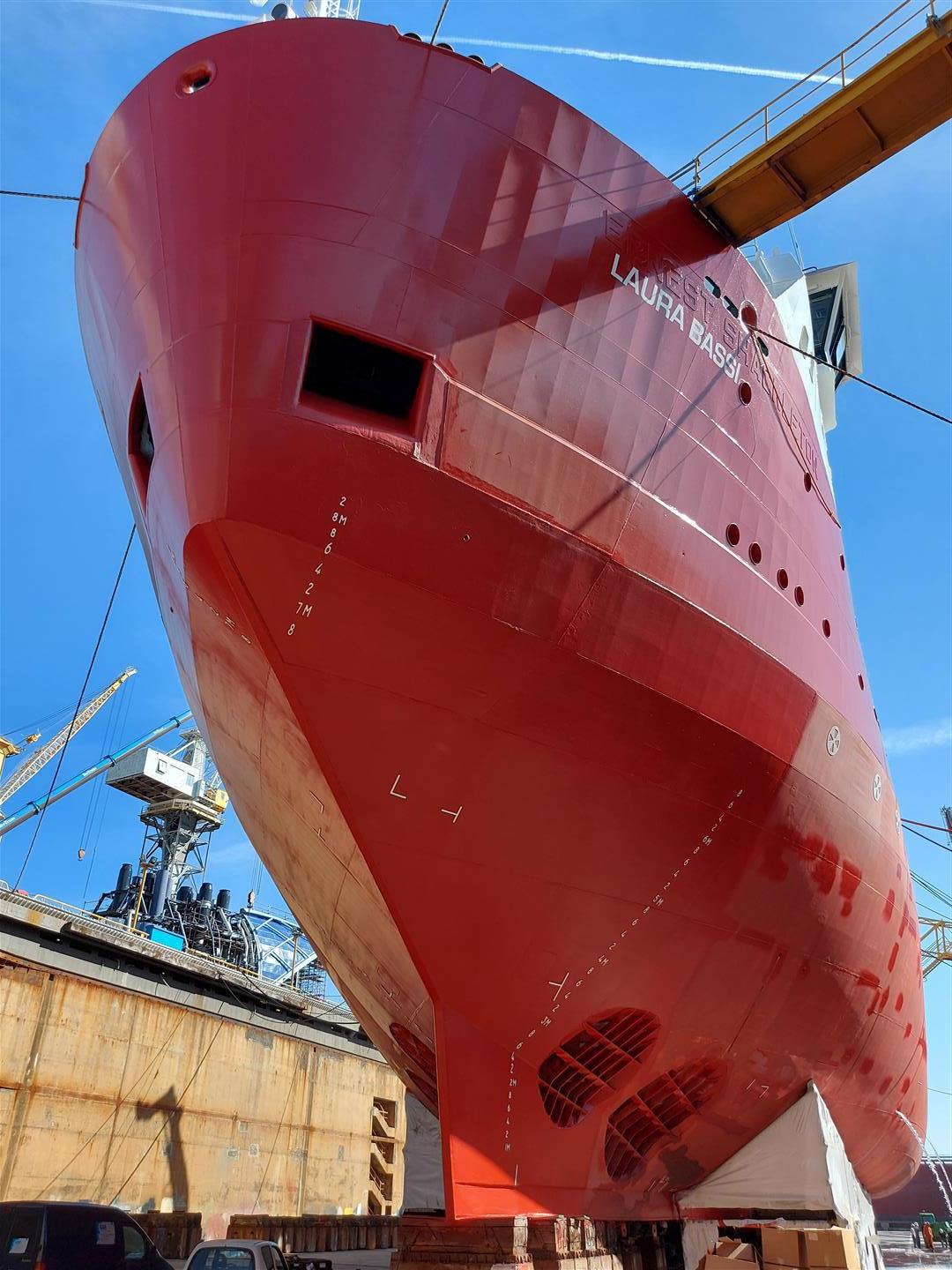
11 minute read
Paints & Coatings
Activities at Subsea Industries
In the last few months a large number of vessels belonging to seven different owners received Ecoshield protection for their rudders, bow thruster tunnels, nozzles and Mewis Ducts. The applications were carried out in China, Singapore, Turkey, Bulgaria, Dubai and the U.S.A. on a wide range of vessels. These included several containerships, tankers, tugs and general cargo vessels. The running gear of these ships will be protected against cavitation and corrosion damage for the rest of their service lives.
Advertisement
A growing number of shipowners have Ecoshield applied on the running gear of their fleet. This coating ensures lasting protection against corrosion and erosion damage. Rudders, thrusters, nozzles and other underwater running gear are exceptionally prone to corrosion and cavitation damage. Cavitation is caused by the spinning of propeller blades. If running gear is not given the proper protection against this the damage can be severe.
This leads to expensive and time-consuming repairs in drydock at least or malfunctioning of the running gear at worst. A rudder has been found missing in its entirety on more than a few occasions with substantial financial consequences for a shipowner.
Ecoshield was designed to protect all running gear for the lifetime of the vessel. This coating system is applied only once. No repaint will be needed during future drydocking. Only small touch-ups to repair mechanical damage will be required.
Applying Ecoshield is a fast and easy to learn process. As a result an application is very flexible and can easily be scheduled around the planning of the yard. Only two layers are required. The minimum overcoating time between these layers is only three hours. This means that most running gear can be coated in a single day.
Newbuild ships benefit the most from Ecoshield. Applying the coating during building means a vessel’s running gear will be protected from the moment the ship leaves the shipyard until the end of its service life. A shipowner will not have to worry about repainting during any of the scheduled dockings.
An existing ship can also be protected with Ecoshield. If for instance a rudder has already suffered corrosion damage, the coating can prevent any further damage from occurring. In such case Ecoshield can be used in combination with another product in the Subsea Industries family - Ecofix.
Ecofix is a superior, tested and proven filler that restores the steel to its original shape with a smooth surface prior to recoating. Because it uses the same basic resin, Ecoshield can be applied just one hour after the filler. Slot welds can also be filled with Ecofix on a newbuild rudder prior to Ecoshield application.
When the icebreaking research vessel Laura Bassi drydocked in Italy earlier this year, only touch-ups were applied to the underwater hull coating. Even though the hull was originally coated with Ecospeed some 12 years ago, there was no need for a full repaint. A truly remarkable result that further reinforces Ecospeed’s ability to withstand the harshest ice conditions for years on end.
OGS (Istituto Nazionale di Oceanografia e di Geofisica Sperimentale) acquired Ernest Shackleton in 2019. The company renamed her Laura Bassi. After her first Antarctic mission for OGS the ship is still protected by the Ecospeed coating as it has been for the last 12 years. Rosario Martino, Naval Architect & Marine Engineer for the vessel’s ship managers, Argo SRL. said, “It was impressive to see the Ecospeed paint in an excellent condition even after so many years of service. We have performed only touch-ups in the bow area affected by the impacts with the ice layer.
The Laura Bassi in drydock
“When Laura Bassi returned from her first Arctic campaign, during which she encountered quite a few icy areas, it was clear that the Ecospeed paint did its job impeccably.”
The number one consideration in a hull coating for ice-going vessels and icebreakers is the ability of the coating to protect the hull in the harshest marine environment there is. Ecospeed will hold up and will not be damaged in the ice and so will remain smooth for the life of the vessel. Even if minor repairs are needed in drydock, the original quality of the coating remains intact. The Laura Bassi is a great example of this.
Metaline’s protective coating for long service lives
In terms of protection against wear caused by the destructive energy of cavitation, erosion and abrasion, there are still two physical schemes available - Energy reflection through very hard surfaces, such as those achievable through plasma treatment, manganese steel, HardoxTM, tungsten carbide and similar alloys. And energy absorption by elastic substrates that absorb, store and release the energy when the energetic impact ends.
Since 1960 on the market as a manufacturer of epoxy ceramic repair materials, MetaLine Surface Protection GmbH introduced in the 1990 a range of elastomeric repair and protective coatings and opted for energy absorption.
Peter Schramm, MetaLine’s Managing Director said, “Some 30 years ago we began developing a material incorporates the primary technical characteristics of completely different materials. The application process is as straightforward as with an epoxy-ceramic composite, but the compound itself functions like rubber, and finally possesses erosion qualities equal or greater than Duplex Steel (AISI316). The result is a hydrodynamic-resistant castable and sprayable protective coating that provides unparalleled erosion/cavitation resistance.”
This fundamental step was based on experience and knowledge from the epoxy ceramics business - epoxy ceramic materials try to fight wear with a low hardness of about 90 to 95 Shore D - which is far less than ordinary mild steel! The epoxy binder is by far not hard enough to become wear resistant by energy deflection and not soft enough for energy absorption. The ceramic content in these products cannot overtake that role, as composites always fail with their weakest element - which is the epoxy binder. The most important maritime applications of epoxy ceramics are quick repairs as an emergency solution until a spare part can be used.
The market demands more wear-resistant materials for professional applications with long service lives. The ongoing development of ultrawear-resistant elastomeric protective coatings has led to today’s MetaLine Series 700 supplied in three different degrees of hardness: • MetaLine 760 (60 Shore A) serves to repair soft rubber linings and worn fenders as well as optimising the performance of hatchcover seals. • MetaLine 785 (85 Shore A) is the first choice for the protection of components subjected to erosion, cavitation, corrosion and wear - rudder blades and horns, kort nozzles, seawater-/
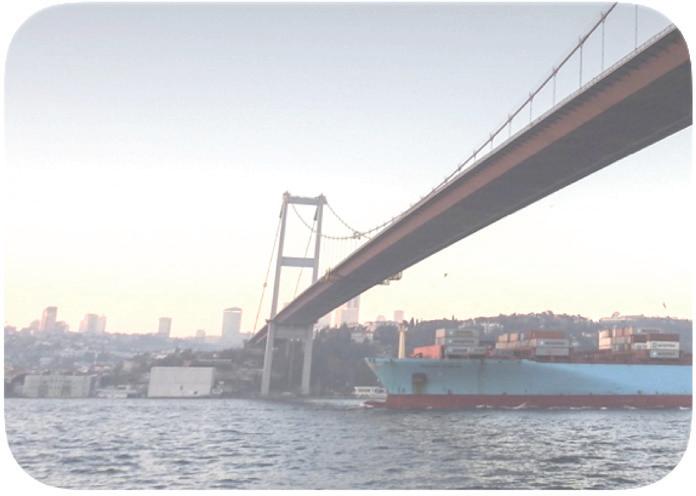
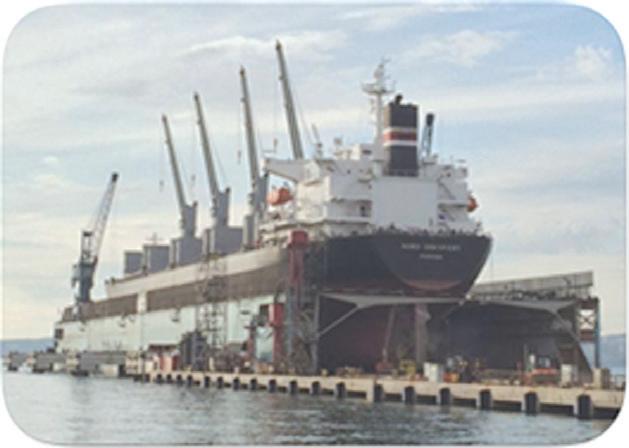
Tugs work hard. The high-revving propeller carries a huge flow of water, which leaves cavitation and erosion marks, especially on the suction-side edge and on the supports of the nozzle
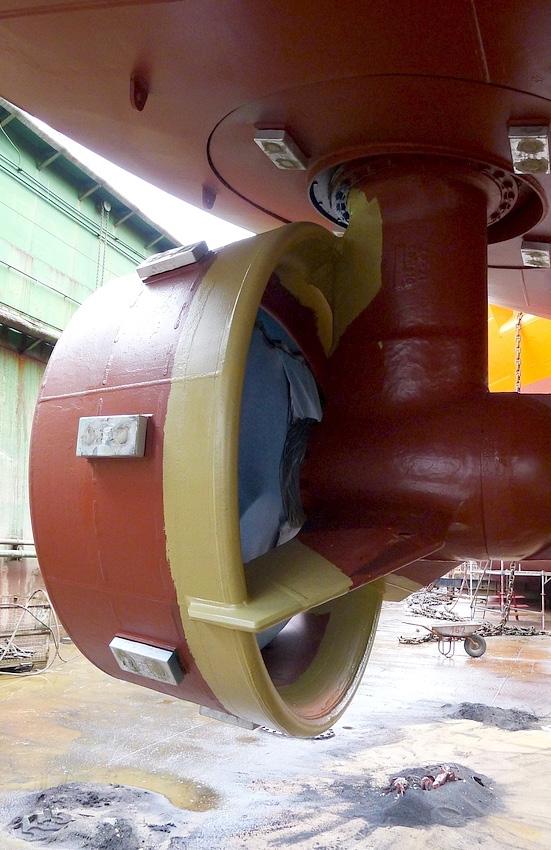
scrubber pipes, strainers, BWM reactors and installations, heat exchangers, pump impellers and casings, thrusters, jet propulsion drives, ropes, fenders, floating hoses etc. • MetaLine 795 (95 Shore A) develops nonstick properties. It offers an ultra-low coefficient of static friction improving material and fouling release. Applications - cargo gates, off-loading chutes, hopper and bunker installations.
The use of highly functional coatings requires competent surface preparation. The surfaces to be coated shall be dry, clean, free of grease and salt and need to have a rough blasted surface profile.
Metal substrates are coated with MetaLine 924. This electro-chemically active corrosion protection prevents borderline penetration on coating edges and protects damaged areas from rusting. After drying, a double coat of MetaLine 900 Universal Primer on solid surfaces or MetaLine 910 on rubber surfaces is applied. Finally, MetaLine Series 700 protective coating with required film thickness and colour is sprayed on. For the purpose of visual wear control indication, the coating can be executed with colour changes during application. MetaLine Series 700 can be recoated and repaired at any time.
MetaLine Series 700 adheres to various substrates including steel, alloys, aluminium, rubber, concrete, wood and different plastics. The coating thickness ranges between 1 mm and 20 mm and can be achieved on vertical surfaces without material sagging. It can be used in many climatic conditions (as in zones with extremely high humidity).
The solvent-free, two-component elastomer can be applied by spraying, injecting or casting by a low-pressure cartridge applicator (about 5 bar). After 5 mins the coating is dry to touch and most parts can go back in service after 24 hours (at 20 °C). The temperature resistance is between -50 °C and +120 °C, depending on the relevant application.
The coating cures without any shrinkage or swelling. In addition to its chemical bonding process, a mechanical memory effect is developed. This permanently ties the coating to the substrate, thus counteracting any separation tendency that is normally associated with conventional rubber sheets. With strict adherence to all processing steps an adhesion/ bond strength of at least 15 N/mm2 is achieved. The low-pressure spray mode creates an extraordinary smooth surface improving any fluid-flow dynamic. Efficiency increases of up to 3.5 % have been proven.
The MetaLine technology allows seamless coating of the most complicated surface shapes. This is a clear advantage compared to rubber linings. While straight pipes are rubbercoated with a pulled-in hose and subsequent pigging, rubber-coating of branched pipes and pipe bends is not practical. Here, with or without vulcanisation on site, rubber would be always installed as a trimmed sheet by gluing and vulcanising. Seams and edges are a current challenge and source of functional problems. On curved parts, due to the bending of the plates, a certain surface tension builds up automatically. On the inner radius it is compressed, on the outer radius – tensile.
MetaLine Series 700 polymerises, is therefore free of any tension and applicable to geometries impossible to reach by conventional rubber lining. A kind of skin covers the part and forms at higher layer thicknesses a selfsupporting shape - for example as a pipe-inpipe. With a density of just 1.05 g/cm3, it is the most lightweight duroplastic wear protection available. The material has practically no influence on the dynamic behaviour of moving parts. The dynamic abrasion of 55 mm3 according to DIN ISO 4649 represents the lowest value among competing protective coatings. Other features listed by the manufacturer: • Non-toxic, safe to use and assessed by US & EU authorities as drug and food-safe according to FDA standards and relevant EEC regulations • Lloyd´s Register and ABS confirm (letters of non-objective / white paper) that No Class Approval is required for MetaLine • Certified for rudders on ultra-fast operating defence vessels • Free of any metal impurities and absolutely non-corroding • Approved up to 700 meter of diving depth in saltwater • Structural born noise / sound reduction of up to 5 dB(A) • 55% vibration damping at a coating thickness of 4 mm • Hydraulic and pneumatic pressure resistant up to 70 bars • Capable to handle up to 60% of solids in slurry applications
MetaLine Series 700 has been used in civil and military shipping since 2012. A wide variety of marine equipment has been repaired or protected using MetaLine´s elastomer materials on more than 500 ships.
Peter Schramm added, “Based on our experience in application and in co-operation with customers, we can confidently claim that we have a proven product range for maritime applications. For on-board repairs, the MetaLine On-Board Surface Protection Kit is available. We offer technical support through all communication channels. And most importantly - we have staff and partners experienced in application and in drydock work, ready to contribute to the safety of the vessels in almost any place in the world.”
Hospital ship coating by I-Tech
Sweden’s I-Tech, has announced the performance of its barnacle-repelling active ingredient, Selektope after an eight-month period in outfitting of the world’s largest civilian hospital ship, Global Mercy.
In May 2021, the Global Mercy completed its sea trial with good results. After extended static period during outfitting, exposed to high risk of fouling, I-Tech found that the vessel showed some signs of fouling on the propellers, however, the vessel’s hull was completely free from barnacle growth.
Built by Xingang shipyard in Tianjin, China,
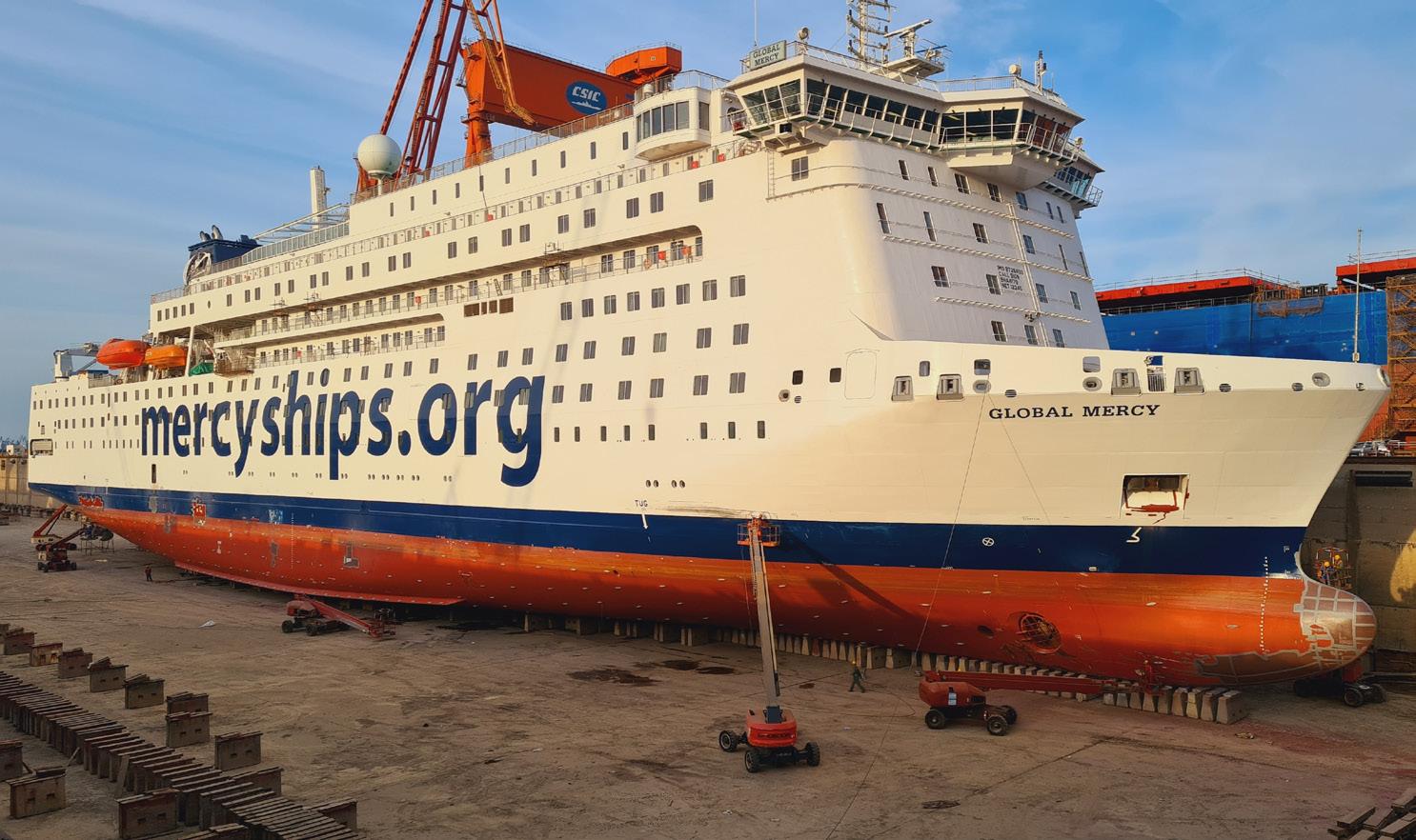
The Global Mercy in drydock
with Stena RoRo appointed by Mercy Ships as the project manager, Global Mercy’s hull was coated with two layers of Jotun’s Seaquantum Pro Ace containing Selektope – an organic, non-lethal, metal-free active agent that is added to marine anti-fouling paints to prevent barnacles from settling on coated surfaces by temporarily activating the swimming behaviour of barnacle larvae. The bio-repellent effect makes Selektope the only type of technology of its kind available to marine paint manufacturers today. During construction, I-Tech worked with leading innovators of the ro/ro cargo and passenger concepts, Stena RoRo, to identify Selektope as the most suitable, innovative technology to ensure that the hull of the new hospital ship would not suffer from the negative effects of barnacle fouling – even during long periods of idling in high-risk areas.
Excess amounts of marine fouling can lead to increased drag, resulting in reduced overall engine efficiency affecting speed, power, performance, and fuel consumption, in addition to costs associated with drydocking the ship to mechanically remove hard fouling, if required.
Embarking on its first mission in early 2022 to the west coast of Africa, the nature of the voluntary aid Global Mercy will provide means that the hospital ship is expected to be stationary in warm water ports for long periods of time, up to as long as 10 months. These extended periods at anchor can put vessels at a heightened risk of barnacle colonisation, according to I-Tech’s recent idling study released earlier this year, which found that ships located in medium or warm waters were at a higher exposure to marine growth.
SORJ
TURN UNCERTAINTY
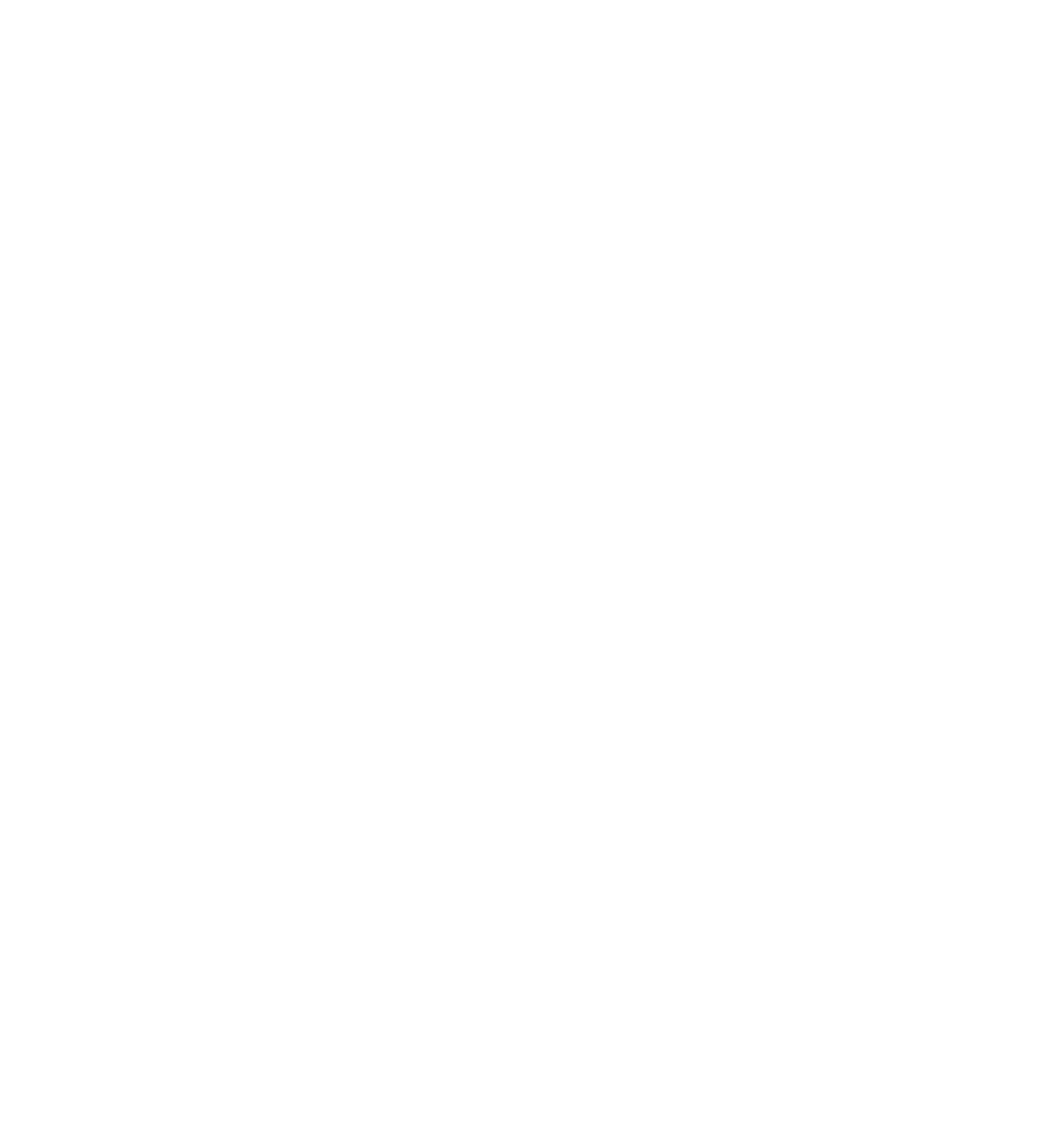
The pressure is on shipping to reduce GHG emissions – but to find the right pathway, you need the right partner. From regulatory compliance, next generation fuels, vessel and operational optimization, to in-depth advice and insight, explore DNV’s decarbonization solutions. And find out how together we can realize a greener future. Learn more: dnv.com/maritime
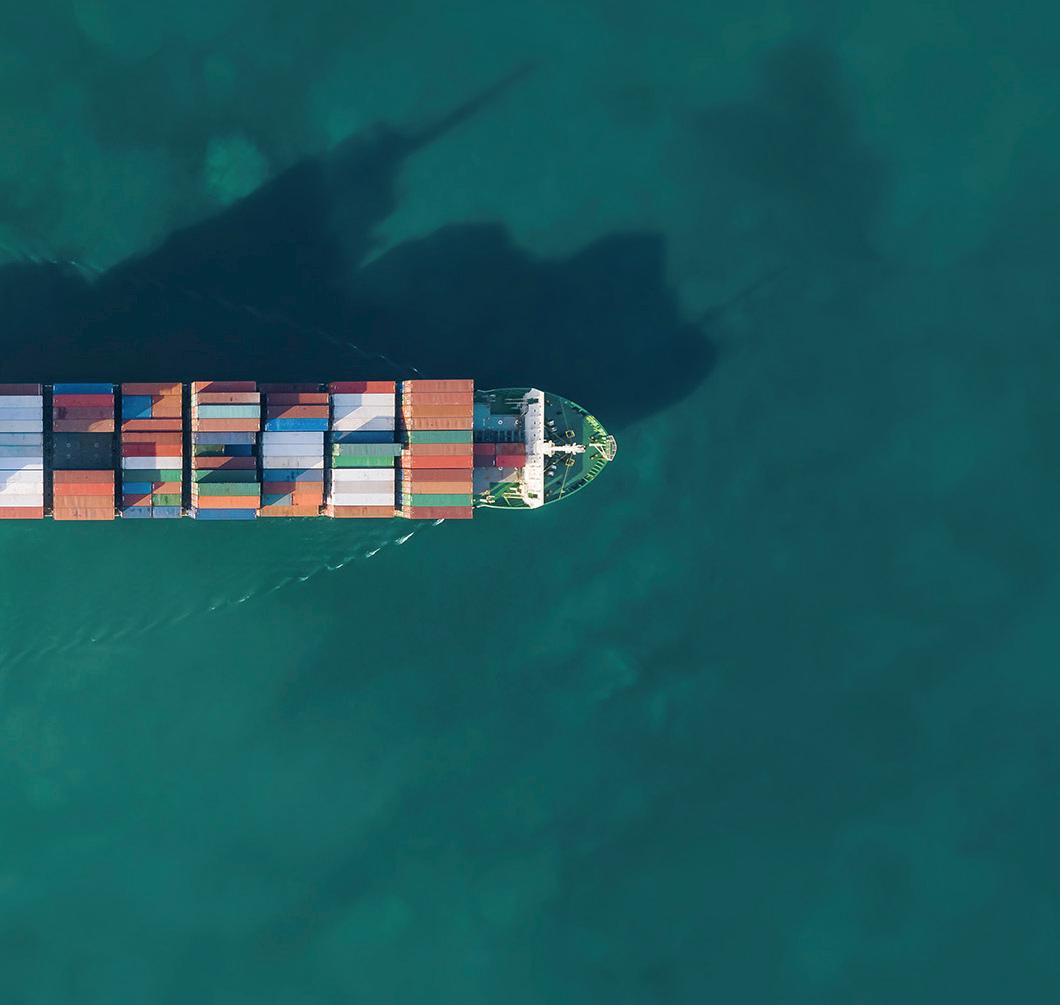