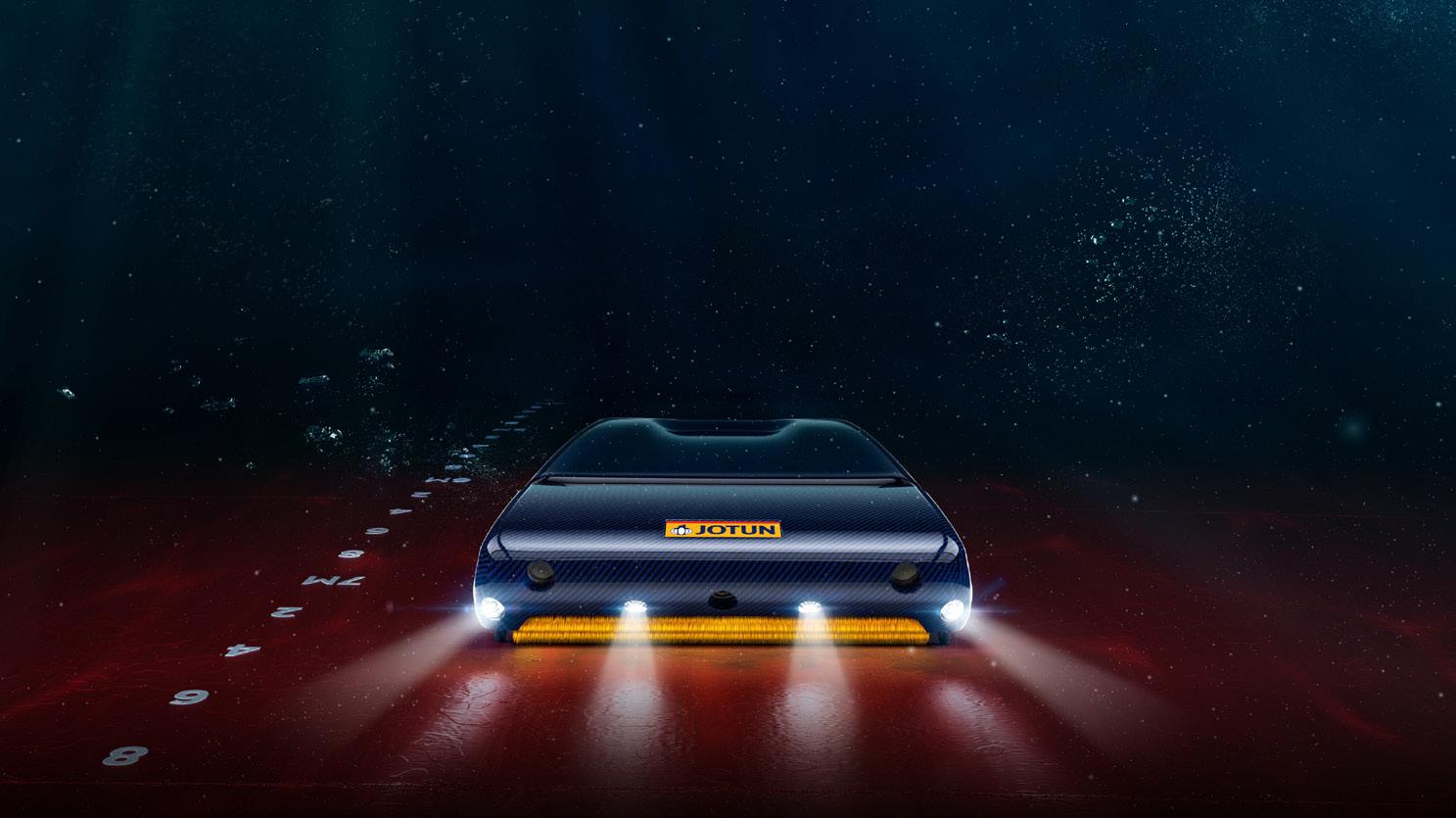
14 minute read
Paints & Coatings
Jotun’s Hull Skating Solutions system
Advertisement
Norway’s Jotun AS, Sandefjord, has unveiled a new digital service, Hull Skating Solutions (HSS), which uses robotics, condition monitoring, smart alogorithms and a high performance coating to prevent hull fouling build-up, reduce fuel consumption, cut emissions and improve ship efficiency. Developed over several years, the practical system is supported by technical back-up including a dedicated project manager attending an installation docking, paint application, robot commissioning and continuing after-sales service. Jotun said that the digital system will tailor hull condition monitoring services to specific vessels, enabling the accurate prediction of fouling rates and proposing suitable cleaning schedules. The system has been developed with a range of partners including DNV GL, Kongsberg, Semcon, a robotics design and manufacturing digital specialist, and Norwegian communications company Telenor. Meanwhile it has been tested over recent months by three shipowning groups – Berge Bulk, Maersk and Wallenius Wilhelmsen – in several ports. Central to the system is an underwater robotic system, the Jotun HullSkater, which is attached to a ship’s hull through the force of its magnetic wheels and is equipped with electric motors for propulsion and steering. The device also has cameras and sensors to provide the operator with data for navigation and as well as the condition of the hull. A motorised brush keeps the hull free from fouling without causing erosion or damage to the coating, Jotun said. The robot is connected to the operator’s control unit via an umbilical and can be operated remotely on vessels in any location with 4G coverage. The system is installed during a docking and remotely operated by a Jotun Skate Operator. This device works in tandem with the company’s SeaQuantum Skate, and anti-fouling which has been designed and thoroughly tested, the company said. Jotun claims that the HSS system can clean an underwater hull in a period ranging from two to eight hours, depending on size and condition, keeps hulls clean ‘proactively’. This contrasts with typical hull cleaning systems which remove fouling organisms from ships’ hulls when they have accumulated and are already affecting resistance, speed and performance. Geir Axel Oftedahl is the coatings company’s Business Development Director. “Biofouling is a big challenge for the shipping industry,” he explained. “It increases frictional resistance leading to speed loss and greater fuel consumption, while at the same time increasing the risk of the transfer of aquatic invasive species. It is a burden to the industry, and our planet, and demands decisive action.” Jotun has estimated that if all ships “in challenging operations” converted to HSS, there would be a total reduction in carbon dioxide emissions from ships of at least 40m tonnes annually. “We believe this is a landmark development for shipowners world-wide,” Oftedahl continued. “Vessels are often faced with unpredictable operations, with erratic idling periods and varied operational profiles that make the selection of anti-fouling problematic, even for the best coatings. And once fouling grows, the impacts are immediate and damaging, with poor hull and propeller performance accounting for around one tenth of the world fleet’s energy consumption. This can make a massive impact on any owner’s bottom line.” Jotun said that the final verification stage is now in progress and the coatings company is recruiting selected owners to adopt the new technology.
Nippon Paints sign NCL contract
Japan’s Nippon Paint Marine has signed a longterm supply contract with Norwegian Cruise Line (NCL) to provide anti-fouling systems to 13 cruise ships operating under the NCL, Oceania Cruises, and Regent Seven Seas Cruises brands. The agreement will see the coatings specialist apply its market-leading low-friction SPC antifouling, A-LF-Sea, to six Oceania vessels, five Regent Seven Seas Cruises vessels and NCL ships Norwegian Epic and Norwegian Dawn. A-LF Sea has already been applied in 11 drydocks while three vessels, Marina, Nautica and Norwegian Epic will be coated with the hull coating during scheduled drydockings later this year. The fleet-wide contract follows the performance success of the low-friction selfpolishing copolymer applied to vessels under individual agreements. “Due to the impressive performance of A-LF-Sea in the past, we decided to broaden the scope of supply to half the Norwegian fleet with a more formal, long-term agreement,” said Carlo Paiella, Vice-President, Technical Operations for NCL. Praising the reliability and performance of the coating technology, he added, “Nippon’s technical service and world-wide supply capabilities complement the excellent fuel-saving performance we have seen from this low-friction paint. “As leaders in the cruise ship sector, we believe it is vitally important to do all we can
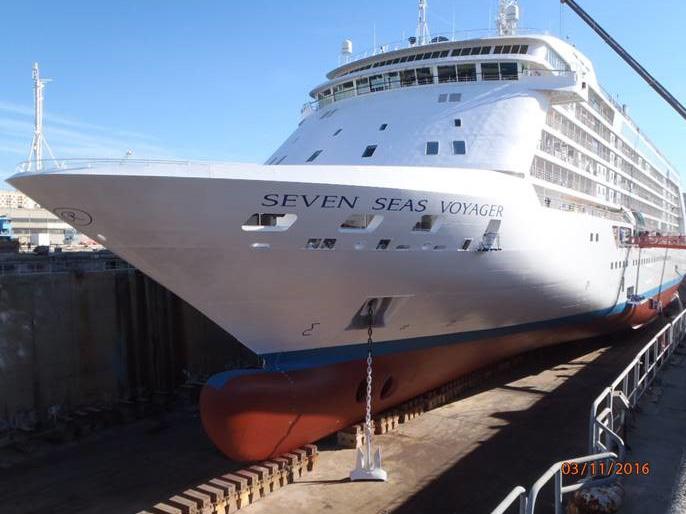
to mitigate against any operations that may influence global climate change. The use of A-LF-Sea has helped towards our ships meeting the very stringent emissions reduction targets we have set.” In December 2019, the company’s lowfriction hull coating system LF-Sea won the 2020 Japanese Government Award for Global Warming Prevention Activity. The judging panel found use of the coating contributed to reduced drag, consequently resulting in lower fuel consumption and reduced CO 2 emissions from those vessels that have applied the hull coating. NCL operates a fleet of 28 cruise ships. The 13 vessels to which A-LF-Sea have or will be applied are Oceania Cruises’ Insignia, Marina, Nautica, Regatta, Riviera, and Sirena - Seven Seas Explorer, Seven Seas Mariner, Seven Seas Navigator, Seven Seas Splendor, and Seven Seas Voyager, and NCL’s Norwegian Epic and Norwegian Dawn. Nippon Paint Marine is also working with NCL in the verification testing and performance monitoring of its unique biocide-free hull coating Aquaterras. A test patch has been applied to an undisclosed cruise ship and results are being benchmarked against a conventional biocide-coating.
Jotun – hull performance is linked with fuel economy
While owners have long recognised the link between clean hulls and lower fuel costs, lack of reliable data has slowed investments in optimising hull performance. But with improved sensor technologies and data analysis tools, hull performance is getting a second look. Owners seeking to lower fuel costs and comply with pending regulations on emissions and invasive species often look to equipment manufacturers to meet their needs. From new efficient engine designs to alternative fuels, scrubbers to ballast water treatments systems, owners face some expensive decisions. But with more vessels now equipped with on-board sensors and standardised tools to measure speed loss due to hull fouling, owners and fleet managers now have access to reliable data measuring the impact of hull and propeller performance over time. The link between hull performance and vessel efficiency is much stronger than previously thought. According to Jotun Marine Analyst Manager A Jotun Marine application
Manolis Levantis, Norway’s Jotun Marine has collected data on hull performance from different types of vessels on different trades for more than decade. “Jotun’s Hull Performance Solutions requires participating vessels to install sensors to enable performance monitoring based on standardised principles (ISO 19030) for the measurement of changes in hull and propeller performance. Since then, the company has amassed one of the industry’s most comprehensive data sets on hull performance.” Levantis says that hull and propeller performance have a much larger impact on vessel efficiency than previously thought. “We estimate that the average yearly speed loss for all vessel types and trades, regardless of what anti-fouling is used, is about six percent,” he says. “For a typical bulk carrier, compensating for this speed loss would require an increase of power of up to 18%, resulting in higher fuel costs and GHG emissions.” Levantis is careful to note that Jotun’s data is taken from owners and fleet managers who are committed to improving hull performance. “When you consider that low freight rates over the past five years have discouraged many owners from investing in premium anti-foulings or sensor technologies, the market speed loss average may exceed 6%.” While Jotun does not usually share customer data, the company worked in co-operation with Gearbulk in 2016 to measure hull performance. GearBulk, which operates the world’s largest fleet of open hatch gantry and semi-open jib craned vessels, shared historical performance data from the cargo ship Penguin Arrow dating from January 2000, allowing for a full comparative analysis. After installing sensors and applying Jotun’s
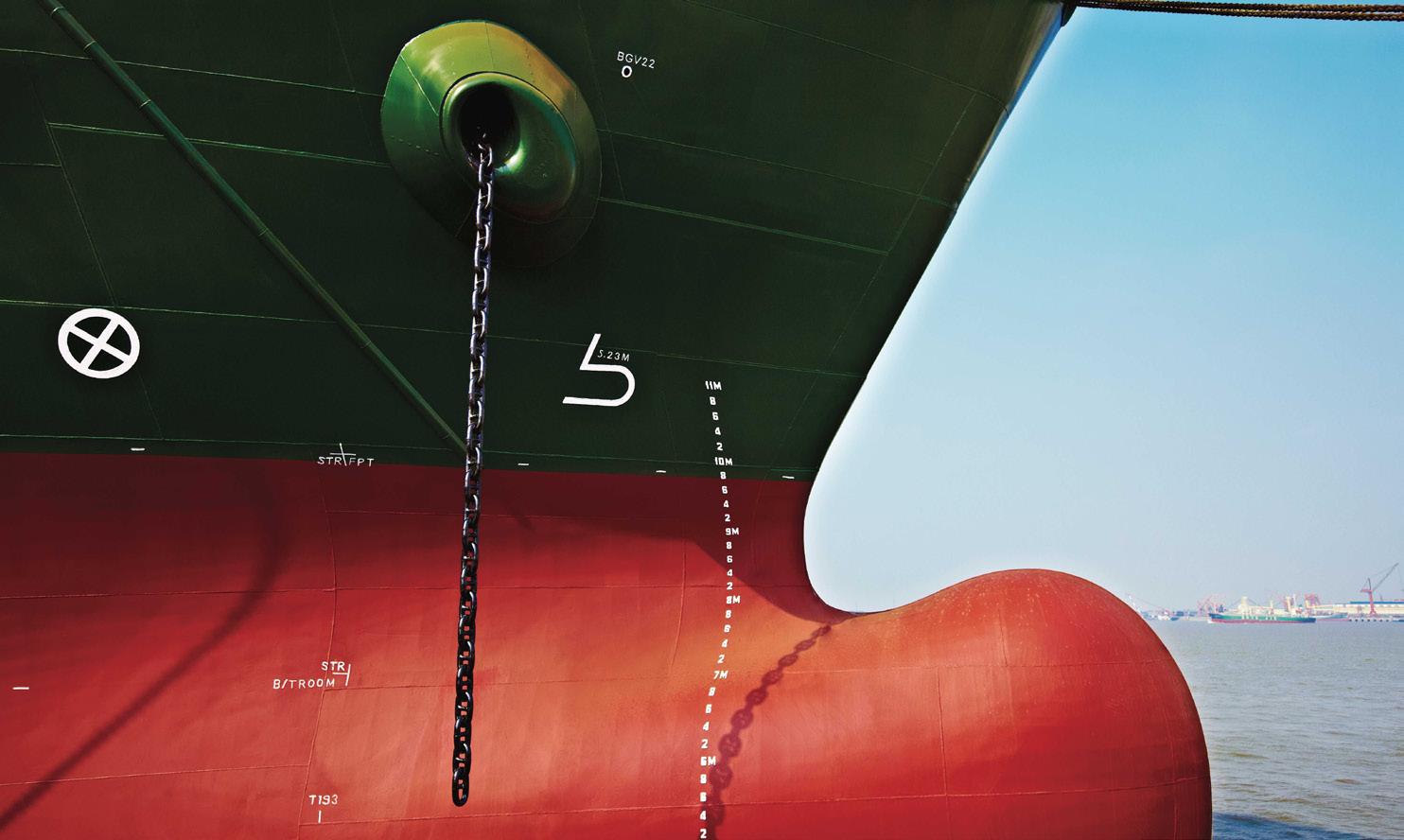
premium anti-fouling, (SeaQuantum x 200), Jotun was able to monitor speed loss over a 60-month period. The results indicated a speed loss of just 0.5%, resulting in an estimated fuel savings of US$1.5m and a corresponding reduction of CO 2 emissions of 12,055 tonnes. “Our data conclusively proves the link between hull performance and fuel efficiency,” says Levantis. “And with IMO’s pledged to reduce the total annual GHG emissions by at least 50% by 2050 compared to 2008, we believe hull performance will play a greater role in helping owners and fleet managers comply with pending regulations.” According to the Clean Shipping Coalition, the only international environmental organisation that focuses exclusively on shipping issues, poor hull and propeller performance accounts for around 10% of the world fleet’s energy consumption, translating to about $30bn in additional fuel costs for the world fleet, every year. Burning this fuel adds 0.3% to shipping’s total greenhouse gas output, which, according to IMO, is about 2.2% of the world’s total – about the same output as Germany. Failure to prioritise hull performance not only result in additional fuel costs, but also may expose owners to claims related to charter party agreements or additional costs for periodic underwater hull cleanings. At the same time, port authorities in Australia, New Zealand, California and the EU have become increasingly sensitive to bio-fouling risk, placing new requirements on owners. While new anti-fouling technologies have drastically reduced speed loss between drydockings and more ports are offering advanced ROV hull cleaning services, pending regulations on emissions and invasive species
will require a more pro-active approach to hull maintenance. Increasingly, owners are seeking solutions to manage hull performance more effectively between dry dockings, when fouling occurs. After all, removing slime before marine organisms can attach to the hull would not only improve vessel efficiency and lower GHG emissions, but also help control the spread of invasive species.
Bellona – links between bio-fouling and the environment should not be underestimated
The risks posed to both the environment and the sustainability of commercial shipping by bio-fouling should not be underestimated, according to leading Norwegian environmental pressure group Bellona. The issue, which has yet to be tackled by any meaningful international legislation, apparently poses a serious threat ‘triumvirate’. However, as Bellona points out, by tackling it head on, especially through ‘proactive solutions’, a three-fold set of benefits can be realised by forward-thinking shipowners. Bio-fouling occurs when aquatic organisms accumulate on vessel hulls. Their growth creates hydrodynamic frictional drag that leads to vessel inefficiency. More fuel has to be burned to maintain operations, increasing both shipowner OPEX and emissions to air. In fact, according to IMO, world fleet fuel consumption (and corresponding emissions) could fall by as much as 10% with better hull and propeller management. “In addition,” explains Sigurd Enge, Head of Shipping and Arctic, Bellona, “bio-fouling is the main culprit in the spread of marine invasive species, which can devastate ecosystems and drive local species extinction. That is compounded by climate change, which allows for greater species introduction, through new shipping lanes, while enabling invaders to survive at higher latitudes, such as in the Arctic, due to increased water temperature. That creates a snowball effect that we must arrest… before it’s too late.” Although IMO and world shipping is tackling invasive species through regulations regarding BWM, bio-fouling has yet to receive the same attention (despite evidence suggesting it’s a far greater problem – a study from New Zealand attributed over 70% of invasive species to biofouling, with only 3% originating from ballast water). Enge says this is beginning to change, but not quickly enough. “New Zealand, Australia and California have initiated their own requirements and that shows the beginning of a ‘trend’, with these frontrunners leading the way for the rest of the industry,” he states. “However, collective action is necessary to create one standard that all must adhere to, and that has to come from IMO… soon. This is a regulatory loophole that must be closed. Our world needs that, and society, driven by increased environmental awareness, will demand it.” “But”, he adds, “Shipowners shouldn’t see this as a burden, more of a ‘huge opportunity’. Effectively dealing with bio-fouling is a win-win-win. Clean hulls mean optimised fuel efficiency and that greatly reduces operational cost. That in turn means lower emissions to air and a better environmental profile. Then, of course, there’s no invasive species spread, and that is essential for the well-being of our marine ecosystems. It is, quite simply, a ‘no brainer’.” However, better in-water hull cleaning solutions are needed to tackle the challenge effectively, with some current practices arguably exacerbating the problem they’re meant to
A rudder with Ecoshield applied Utimately the best way to prevent potential invasive species contamination is ensuring ships sail with clean hulls at all times.
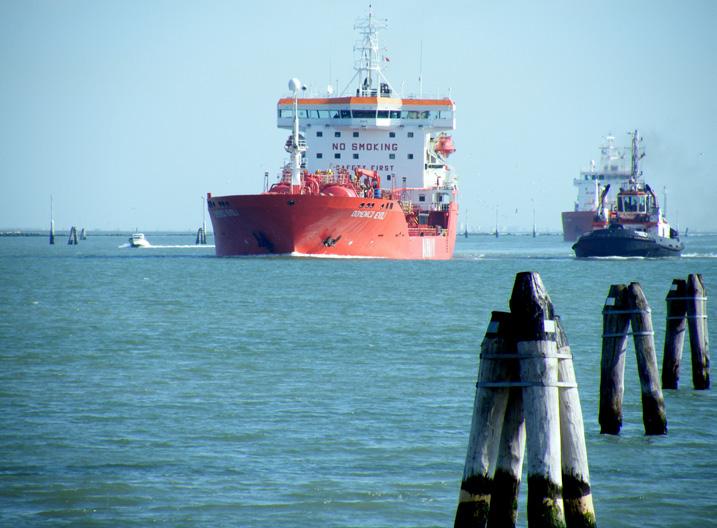
address. For example, Enge says, manual diving teams and remotely operated machinery that scrub hulls often simply dislodge bio-fouling into the water, effectively facilitating invasive species spread. The process can also damage a vessel’s anti-fouling coating, releasing potentially toxic biocides into the water. Because of this, cleaning with capture or offshore is certainly preferable, he imparts, but for the optimal solution, the industry needs to be ‘proactive’.
The use of Ecofix
Ecofix is a filler product which is used in combination with the award-winning Ecoshield hard coat system. Ecofix is specifically
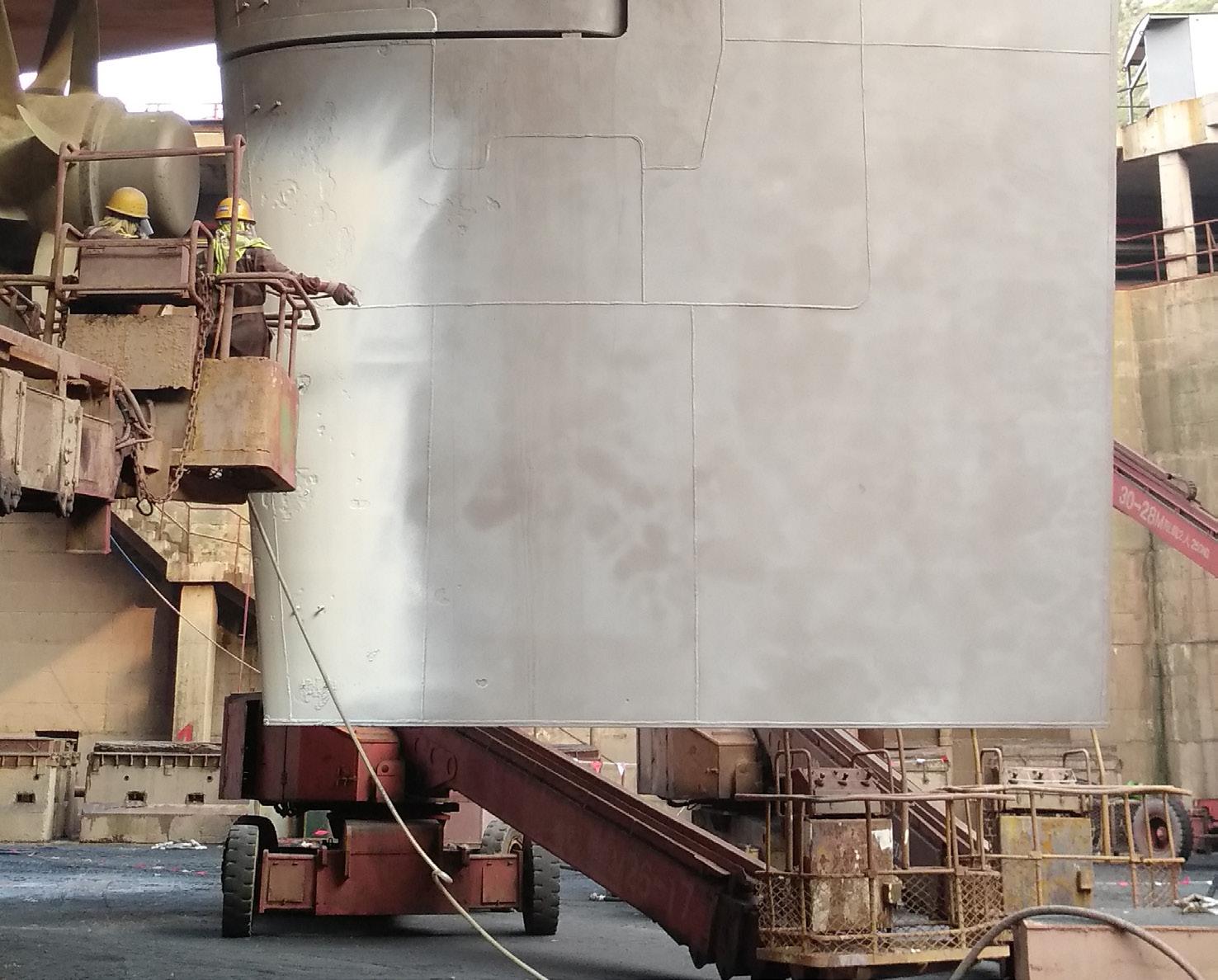
developed to provide ship owners and Original Equipment Manufacturers with a cost-effective solution for the repair of corroded or pitted steel surfaces. The rudder of a LPG tanker was given the full treatment in Setubal, Portugal. First Ecofix was applied to restore the surface of the damaged rudder back to its original condition. Next it was coated with Ecoshield. This will protect the rudder from ever suffering corrosion and cavitation damage again. Ecoshield and Ecofix are also suitable for stabilizer fins, thrusters, nozzles and other underwater ship gear which needs special protection from corrosion. Now these items can also be repaired prior to recoating when other, less effective coatings have permitted corrosion and cavitation damage to occur. For this reason the corrosion damage on the rudder as well as in the thruster tunnel of a container vessel was repaired in Rotterdam with before Ecoshield was applied. We offer the full package -Ecofix restores the surface of the rudder or other underwater gear and Ecoshield will protect the area from ever suffering corrosion and cavitation damage again. Over the last few months the rudders and running gear of different types of vessels were given an Ecoshield protective coating at yards in the Netherlands, Canada, Turkey, Finland and China. These ships include container vessels, tugboats, vehicle carriers, a reefer and a tanker. Most of the ships belonged to different owners. Some of them were new customers, others returning ones. The returning customers had seen first-hand that Ecoshield solved the problem on their other rudders and wanted the same protection for the rest of their fleet. The new ones saw the excellent result obtained by other owners and chose Ecoshield to prevent corrosion and cavitation damage from reoccurring. In the last couple of years sister company Hydrex has noted a substantial increase in the number of enquiries for underwater rudder repairs. This clearly shows the need for a cost saving and lasting solution. A great deal of effort goes into the design and manufacture of rudders because they are such an important
MARINE SERVICES
part of a vessel. If a rudder is not given the proper protection against cavitation and the resulting erosion and corrosion damage, the financial consequences can be substantial for the owner. Ecoshield puts an end to this. By removing the existing paint layers and applying the coating system on running gear we can break the never-ending cycle of painting, suffering damage, having to perform extensive repairs in drydock followed by a full repainting, again and again. Ecoshield gives a very thorough and lasting defence for a ship’s entire service life. No repaint will be required during drydocking. At most minor touch-ups will be needed. With time at a premium in drydock, the speed of application of Ecoshield is a further advantage. Ecoshield’s flexibility makes it easy to adapt the application schedule to the rest of the activities at the shipyard or drydock in a way which does not interfere with them. Overcoating time can be as short as three hours. With the right planning grit blasting and application of the two required layers can be performed in just one day. Suitable for all running gear. SORJ
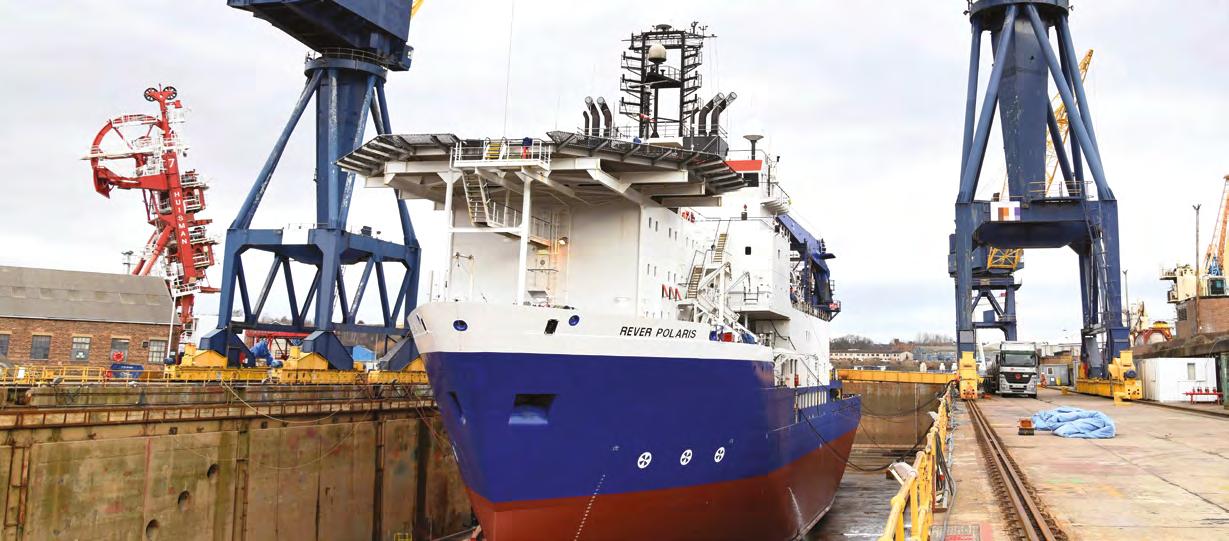
• SHIP REPAIR & REFIT • REACTIVATION & CONVERSION • MOBILSATIONS & DEMOBILSATIONS • EMERGENCY REPAIRS
A&P TYNE | Wagonway Road, Hebburn, Tyne & Wear, NE31 1SP | T. +44 (0) 191 430 8600 A&P FALMOUTH | The Docks, Falmouth, Cornwall, TR11 4NR | T. +44 (0) 1326 212 100 A&P TEES | Teesport Commerce Park, Dockside Road, Middlesbrough, TS6 6UZ | T. +44 (0) 1642 464 024