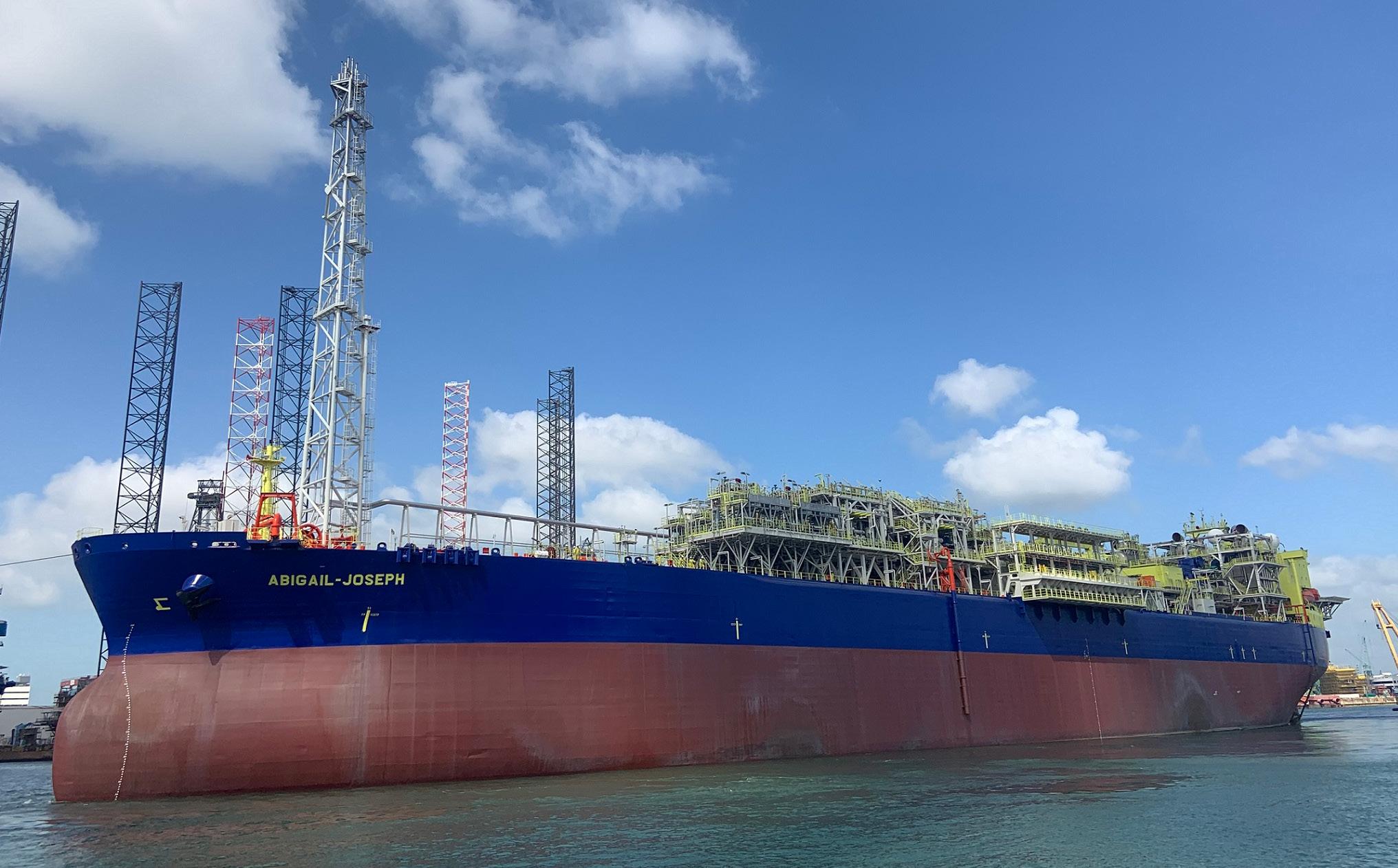
11 minute read
Offshore
The FPSO Abigail Joseph
Keppel delivers latest FPSO project
Advertisement
Singapore’s Keppel Offshore & Marine, through its wholly-owned subsidiary Keppel Shipyard, has delivered the world’s fastest FPSO modification and upgrading project safely and on time. The FPSO Abigail-Joseph was delivered to Yinson Nepeta Production, a wholly-owned subsidiary of Yinson Holdings Berhad. Chris Ong, CEO of Keppel O&M said, “This is our 134 th floating production vessel, and we are pleased to be able to fast-track the project and upgrade it in less than seven months. This achievement reflects Keppel’s track record of reliability and quality, anchored in our strong engineering and project management capabilities, which enable us to offer value adding solutions for customers.” Keppel’s scope in this project includes refurbishment and life extension work, engineering and procurement, fabrication and installation of new structures including the heli-deck and riser balcony, as well as the installation, integration and completion of topside modules. Lim Chern Yuan, Group CEO of Yinson Holdings, added, “This is our third FPSO conversion project with Keppel since 2012, and our close partnership has grown from strength to strength. Leveraging our FPSO expertise and Keppel’s experience in vessel conversions, we are able to achieve this significant industry milestone and bring FPSO Abigail-Joseph to market quickly, maximising its operational uptime.” Chartered by First Exploration and Petroleum Development Company on a firm seven-year
contract with options to extend, FPSO AbigailJoseph will be deployed in Block OML 83/85 in the Anyala-Madu field, Niger State, Nigeria. FPSO Abigail-Joseph has a processing capacity of 50,000 bbls of oil/day and 60,000 bbls of liquid/day. It also has a gas compression capacity of 34m standard cubic feet/day (mmscfd) and a storage capacity of not less than 550,000 bbls of oil. It is designed for 15 years of operations without drydocking.
Sulzer completes pump repair offshore Australia
Not many service providers can deliver complex service solutions to all types of rotating equipment regardless of the OEM. When a FPSO unit off the coast of Australia required engineering support, Sulzer stepped in to provide the solution. FPSOs are critical in the oil & gas industry for the production and processing of hydrocarbons as well as the storage of oil. When such vessels have production capacities of over 90,000 bbls of oil/day, there is little room for ill-performing equipment on-board. Where subpar performing pumps and motors are identified, service experts need to be called in for peace of mind. After over a decade in operation, three API BB3 water injection pumps were subject to a number of seal failures, which were outside the routine maintenance schedules. The failures were caused by an increase in the seal chamber pressure - an issue that resulted in the owners contacting Sulzer for expert analysis and support. Field service teams provided on-site inspection and a review that revealed a reduction in pump head and performance as well as wear caused by sand particle impingement. The high amount of sand passover, coupled with incomplete regular cleaning of auxiliary equipment, lead to the pumps operating at a reduced efficiency, having a detrimental impact upon production output. Having gained the necessary information to understand the root causes of the problem, the engineering team based in the Suzhou factory began designing the solution. Specialist engineers proposed a multi-faceted solution to combat the wear and seal issues. This included modifying internal geometries, ensuring a smoother flow and allowing particles to follow the fluid streamline more closely, resulting in reduced turbulence and thus reducing erosion. A tungsten carbide-based coating SUME, specially developed for sand abrasion within pumps on water injection duties, was used for coating of the impellers and wear parts due to its high wear resistance and anti-galling properties. Finally, the wear rings were upgraded in material to a ceramic type providing further wear and abrasion resistance. The proposed solutions were approved by the customer and executed according to the customer’s outage plans. One of the pumps was upgraded, while the FPSO vessel was in dry dock, at Sulzer’s Singapore Service Centre and the subsequent pumps were upgraded within Sulzer’s Perth Service Centre once the vessel was back in operation in Australia. This allowed the customer the flexibility of completing the job within their project schedules. Furthermore, having the service sites nearby gave the customer piece of mind, with the equipment being repaired to the highest level of quality and offering excellent support during the project. In addition to the support with the mechanical rotating equipment, Sulzer was also able to deliver maintenance and repair work for the electrical equipment. This time, the FPSO vessel required support on the removal of an old 2 MW, 11 kV Siemens motor while simultaneously installing and commissioning a brand-new identical piece of machinery. The original motor was removed from the vessel and sent to the Perth Airport Service Centre for a full inspection, repair and testing. Specialists assessed the condition of the unit and replaced a number of components including stator leads, rotating seals and grease lines as well as remanufacturing a new terminal box to better suit the application on site.
Sulzer - Partially assembled pump after improving the components
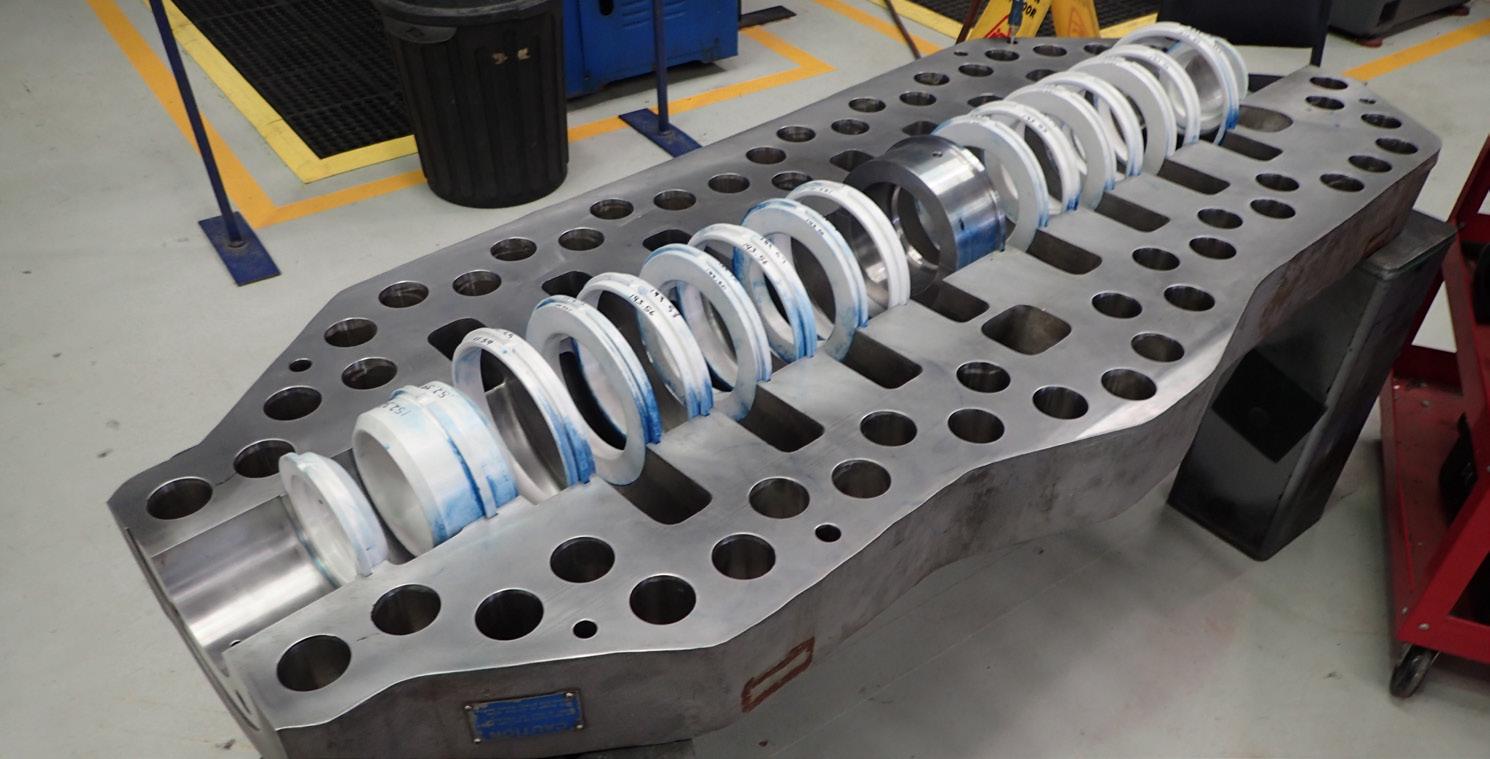
The windings were cleaned, dried and the motor was tested at rated voltage 6.6 kV. The entire overhaul process was completed over a fivemonth period with the motor remaining at the service centre for preservation until it is required again.
Royston completes FPSO power system repair
UK’s Royston has completed the overhaul of a critical power system on-board another Bluewater Services operated FPSO. A team of engineers from the North East-based diesel on the MAN 32/40 STX diesel generator B onboard the 88,000 dwt Aoka Mizu, as part of a planned refurbishment and refit of essential power systems. Work on the vessel, which is currently on contract to Hurricane Energy for the early production system (EPS) on the Lancaster field, west of Shetland, saw engineers dismantle the generator to complete maintenance and repair work on con rod bearings, pistons and cylinder heads. Engine components were refurbished onboard and new OEM spares fitted as necessary. This is the latest work Royston has completed
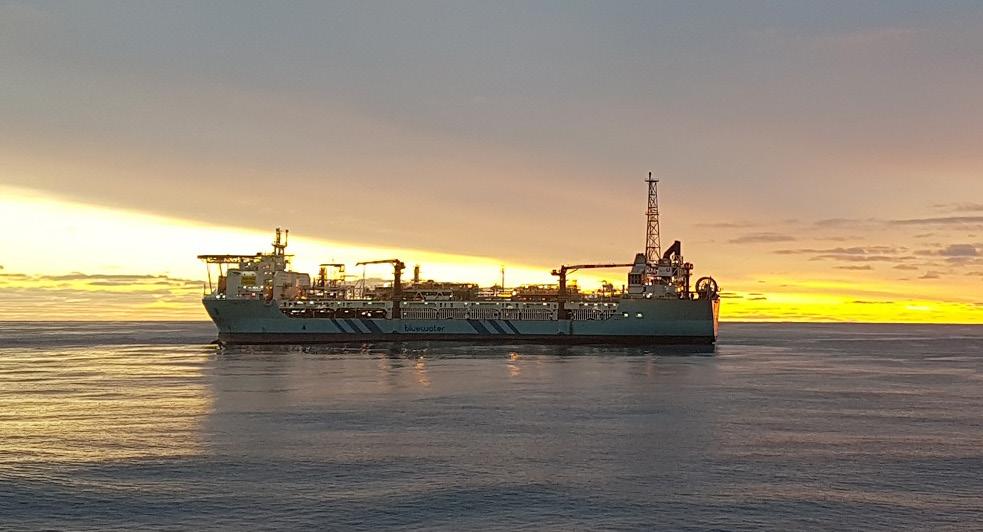
The FPSO Aoka Mizu on Bluewater Services’ vessels – it has previously carried out extensive work on the FPSO Haewene Brim as part of a series of planned engine overhauls. The Aoka Mizu is part of a five-strong fleet of FPSO vessels owned by Bluewater Services, with the Aoka Mizu and Haewene Brim being
power specialist undertook the 6,000-hr service operated from Aberdeen. They are all designed to a high specification and to operate in the harshest environmental conditions, under the most stringent regulatory regimes.
Wärtsilä introduces power solution for NUIs
Finland’s Wärtsilä has introduced an agreementbased Power Solution for new normally unattended offshore installations (NUIs). The solution provides the asset with up to six months of operating time without planned maintenance activity on-board, thus enabling significant cost savings. It is a holistic power solution that can be tailored according to the requirements of each individual installation and is supplied together with a power system, including high-efficiency Wärtsilä DF (dual-fuel) engines, generators, and auxiliary systems. The Wärtsilä Power Solution has been developed to allow all scheduled maintenance activities for NUIs to be performed efficiently using ‘walk to work’ support vessels, thereby eliminating the need for on-site accommodation facilities. The solution can be extended to include the maintenance of power management, automation and auxiliary equipment. Whereas conventional offshore power solutions require monitoring and regular inspections with maintenance being carried out depending on the number of running hours of the engine, the Wärtsilä Power Solution requires no such activities. The interval between maintenance campaigns can typically be extended by up to six months, and in the meantime the condition of the equipment and its performance are constantly monitored and evaluated remotely from a Wärtsilä Expertise Centre. This remote detection and diagnosis defines the actions to be taken during the next maintenance campaign, or immediately if required. Wärtsilä has extensive experience with remote operated unmanned power generation installations utilising highly reliable and efficient dual-fuel engines. Operations are supported by digital enablers and expert analysis of condition monitoring data.
The Wärtsilä Power Solution relieves cost pressure for the offshore sector by eliminating the need for permanent on-site maintenance crew and permanent facilities for them
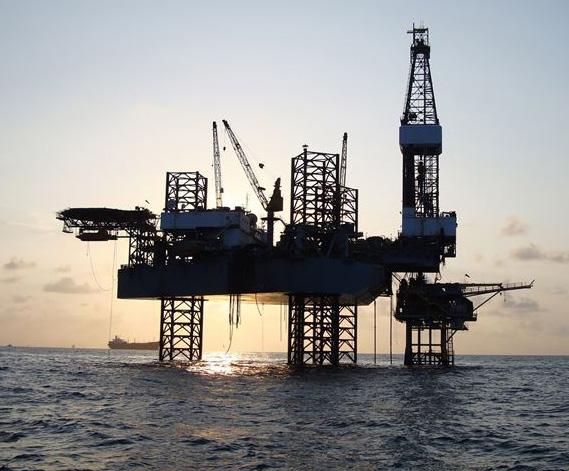
LR wins TenneT contract
Following a competitive tender process, Lloyd’s Register’s (LR) Inspection Services team has secured a significant contract win with TenneT, a leading European electricity transmission system operator. Headquartered in the Netherlands, TenneT provides a reliable and uninterrupted supply of electricity to over 41m people. The five-year contract covers inspection and assurance services during the erection and commissioning phases of three North Sea converter platforms, with construction sites based among other in Spain, Norway and Turkey. The contract includes services on the TenneT FAST project (Framework Agreement for Site Supervision at Yards for TenneT) such as
The DP3 vessel Pride
detailed site supervision and vendor assurance and performance during the construction and commissioning of the platforms. Led by Dr Hendrik Lau, Director Corporate Accounts North Europe, and Massimo Alvaro, Global Head of Assurance, Inspection Services at LR, the team was selected by TenneT in a European Union tender process. Previous work completed by LR includes 2 nd and 3 rd party assessments, yard assessments, risk assessments and certification of various platforms, design appraisal and certification of offshore converter platforms for offshore wind farms.
Osbit awarded FTAI Ocean contract
UK’s Osbit Ltd, Broomhaugh, has been awarded a contract by FTAI Ocean, a subsidiary of Fortress Transportation and Infrastructure Investors LLC (FTAI), to design and construct an innovative new well intervention tower system. Osbit’s Smart Tower System facilitates integrated riserless and riser-based well intervention operations, in water depths up to 1,500 m, and is to be installed on FTAI’s 14,203 gt flagship DP3 vessel Pride. The Smart Tower System combines elements of modular technology from Osbit’s experience in well intervention and offshore handling, with a series of innovations to improve operational safety, flexibility and accessibility. The tower’s vertical Completion Workover Riser (CWOR) racking system improves deck safety by reducing the need to access the intervention floor and to handle CWOR joints, while its small footprint optimises deck space, for more effective equipment storage. The Smart Tower System integrates the existing vessel crane into the full deployment system - with up to 250 tonne active heave
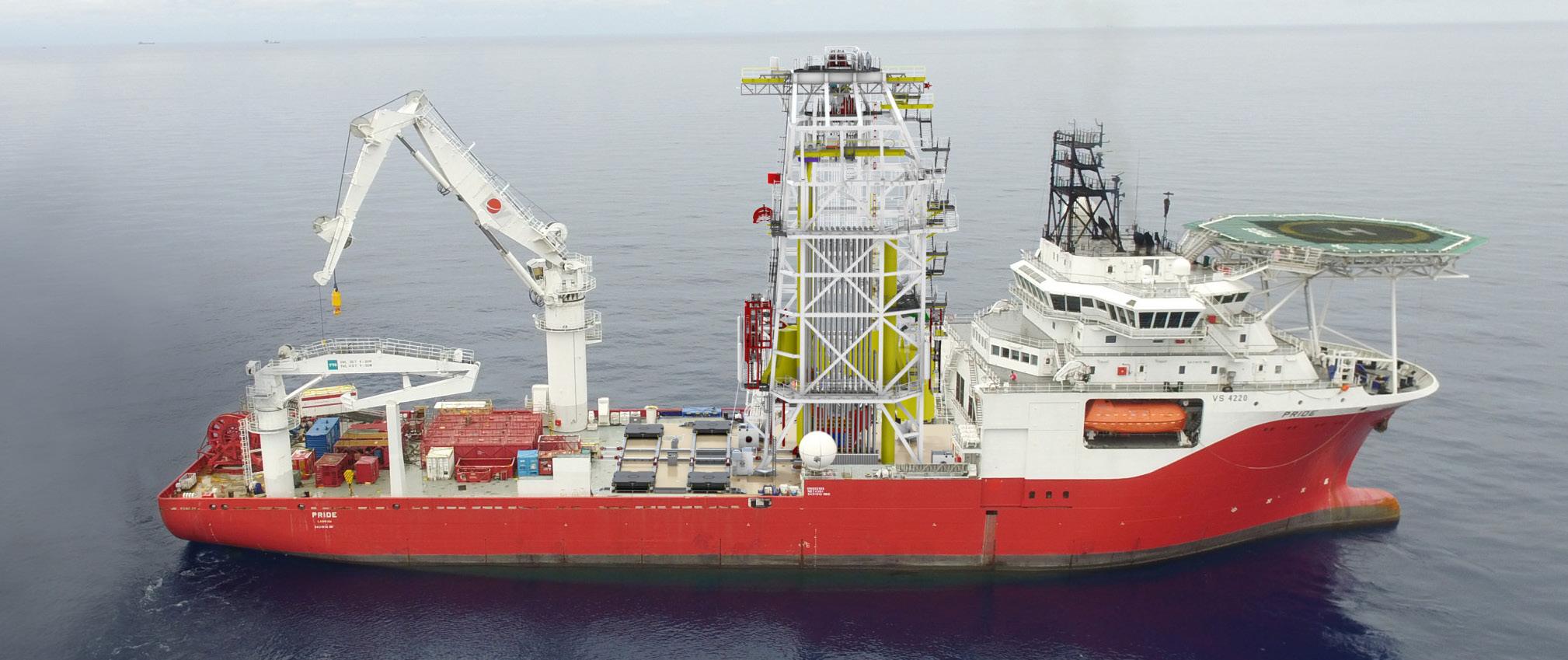
compensated capacity. Additionally, the system offers a universal platform for surface pressure equipment, active heave compensated slickline and e-line operations and for the building, operation and recovery of CWOR and intervention systems. The Smart Tower System is fitted with multiple guide wire systems and an extensive deck skidding system, which minimises the need for crane lifts, increases operating windows and enables equipment to be directly loaded into the well centre. The Smart Tower System will also feature Osbit’s Integrated Logistics Support (OILS) control system technology, which the company has already integrated across a range of offshore assets. The software package will deliver unrivalled data insight and performance analysis, while its market-leading control cabin is highly ergonomic, and will interface with the vessel’s safety systems, crane and CCTV.
DNV GL reveals optimism in the offshore market
New research published by DNV GL reveals that optimism for growth in the oil and gas industry has weakened for this year. This comes amid uncertainty around the oil price and global economic conditions – the top barriers to growth reported by the industry. While two thirds (66%) of senior oil and gas professionals are confident of industry growth in 2020, this is down 10% from the 76% recorded in 2019 – the peak of a surge in confidence from a low of only 32% in 2017. Under half (46%) of respondents think that more large, capital-intensive projects will be approved this year compared to 2019, down from two thirds (67%) last year. New Directions, Complex Choices - The outlook for the oil and gas industry in 2020 is based on a survey of more than 1,000 senior oil and gas professionals and in-depth interviews with industry executives. Now in its 10 th year, DNV GL’s research assesses industry sentiment, confidence, and priorities, and provides expert analysis of the key challenges and opportunities for the year ahead. Meanwhile, a new standard for site investigation, engineering, planning and execution of pipeline installation through horizontal directional drilling (HDD), has been published by DNV GL, the technical advisor to the oil and gas industry. The new standard, DNVGL-ST-F121, was created through a joint industry project (JIP) and provides a series of minimum requirements and best practice for all phases, from site investigation, engineering and planning to execution of pipeline installation to reduce the risk associated to HDD crossings. HDD is a construction method in the trenchless industry which provides significant improvements over traditional open cut methods for installing pipelines beneath obstructions such as rivers, highways and railroads. These include preservation of the ground surface of the construction site, minimal requirement for site preparation and reinstatement, and secure depth of cover. The use of HDD installation techniques has grown significantly over the last decades. A recent HDD survey estimated in 2019 that contractors expected HDD to be applied to nearly half (47%) of their projects. However, HDD crossings are complex in nature and always very challenging. It is not uncommon to face problems during execution with significant impact on cost and schedule. The best way to overcome this is to ensure a proper investigation, engineering, planning and execution of all drilling-related activities. Additionally, there are currently no methods for in situ repair of damaged pipelines installed by HDD, which makes it even more important to ensure the quality of pipeline design, construction and installation. The earlier potential risks and problems are identified in an HDD project, the better for the delivery of the project. All these challenges led to a joint industry project to consolidate the knowledge and experience of HDD. Operators, EPC companies and drilling contractors were brought together for the first time, addressing not only the borehole stability and the drilling activities perspective but also the aspects related to the pipeline integrity as well. SORJ