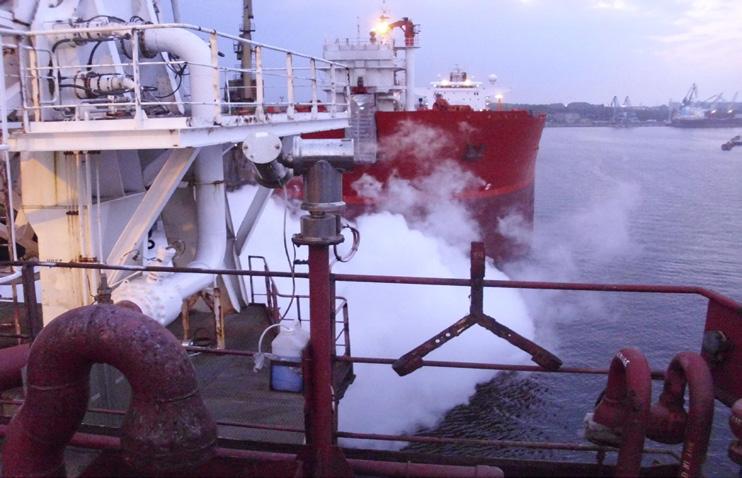
14 minute read
Services
Fire-fighting training - essential
UK’s Survitec is advising the maritime industry to ensure fixed fire-fighting systems are commissioned by their original equipment manufacturers and that crews undergo basic system configuration training, following a spate of incidents where ship fires have been exacerbated through incorrect use or installation of CO2-based extinguishing systems.
Advertisement
While IMO’s FSS Code provides engineering and design standards for all types of fire extinguishing systems, there are no mandatory regulations governing their installation and commissioning, only recommendations. Standards on operation and maintenance have improved over the last years but in many cases, they are still seen as guidelines. Survitec said that although these guidelines should be followed, there have been several incidents in recent times where fixed fire extinguishing systems have failed.
“While it is difficult to put a number on all the fire related incidents where incorrect installation, operation or maintenance of a fixed fire-fighting system has resulted in system failure, injury or death, the subsequent accident investigations offer a different perspective on the effectiveness of the current regulations and guidelines,” said Mats Hestmann, Survitec Group QHSE Manager.
“Fire safety systems are inherently designed to protect and save lives. However, if these systems are incorrectly used, installed or insufficiently inspected and maintained, the consequences can be severe,” said Hestmann.
Hestmann believes that it would be beneficial for MSC.1/CIRC 1318 to become even more structured as is the case with MSC 1432, clearly defining what should be inspected. Once the majority of flag states have adopted an MSC circular, it then becomes a resolution making it mandatory.
As the market leader and a champion of maritime safety initiatives, Survitec is fostering greater fire safety and systems awareness across the industry. It has already issued advice notices and is raising wider awareness of the need to ensure fire-fighting systems are correctly installed, regularly maintained, serviced and that crew operating the systems are trained and understand how to use the specific system.
“We want to ensure that operators and crews have a much better understanding of how fixed fire-fighting systems operate and the importance of regular, properly carried-out maintenance. With greater knowledge, they will be able to overcome many of the operational challenges they face and prevent system failure when it is required in an emergency,” said Hestmann
Meanwhile, Survitec has introduced a new service aimed at ensuring CO2 low pressure (LP) fire-fighting systems are correctly deactivated when ships enter lay-up. The turn-key CO2 LP lay-up service, developed in collaboration with a leading European-based shipowner, was introduced two-months-ago following market demand for a solution capable of simplifying decommissioning and recommissioning procedures.
Survitec has already seen an upswing in demand for the service following a surge in the number of ships temporarily suspending services and deactivating ships due to the lack of trade.
A CO2 LP system, typically used in a vessel’s fixed-fire extinguishing arrangement, can only be decommissioned and recommissioned by a specially trained service provider once the Classification Society has granted approval for the system to be deactivated and the tank emptied. Survitec has Z17 approvals as service suppliers – from various classification societies allowing the company to service maintain a vessel’s multi-branded fire-extinguishing systems, including CO2 LP systems.
With shipowners unprepared for the rapid and extended economic crisis the on-going pandemic has created, the shortfall in trade volumes is resulting in a need to protect revenues and scale back operations. For many, a cold lay-up is the best way of reducing overheads. Survitec is currently creating CO2 LP cold lay-up and re-activation procedures for some 10 vessels in a prominent ro/ro and PCTC fleet.
Seaspan’s experience with Ecoshield
Over the past 10 years the rudders of 55 containerships owned by Canada’s Seaspan have been coated with Ecoshield. A number of vessels also had their thruster tunnels and twisted fins given the same treatment. One of these ships recently docked in Indonesia ten years after application. Only small touch-ups were needed on its rudder, much to the satisfaction of the owner.
After the recent drydocking of the Seaspan New York its superintendent Chandrashekhar Singh commented, “In my 10 years of experience as superintendent I have never seen a rudder in such a good condition as when Ecoshield paint is applied. With this good experience, we have applied Ecoshield paint on the draft and load line marks and bow thruster tunnel as well.”
A low-pressure CO2 system can only be decommissioned/recommissioned by a specially trained service provider
Ecospeed being applied
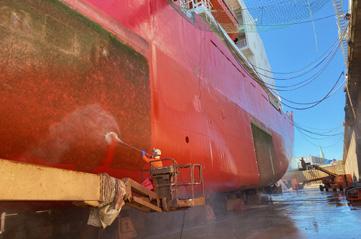
A great deal of effort goes into the design and manufacture of rudders because they are such an important part of a vessel. If a rudder is not given the proper protection against cavitation and the resulting erosion and corrosion damage, the financial and operational consequences can be substantial for the owner.
Mithun Vasudevan superintendent of Seaspan’s CSCL Sydney said that “Ecoshield has definitely been a success and most of our ships have and are in the process of using it. This in itself is a testimonial to the quality of the product.”
Three years ago, Ecospeed was applied on-board the shallow draught anchor-handler Antarctic, owned by Ark Shipping Company. The success of this application led the owner of the boat to order the same protection for his next two shallow draught anchor-handlers - Polar and Polus. Building of these vessels will start in 2021 and will again take place at the Atlas Shipyard in Kocaeli, Turkey.
Ark Shipping Company is a large Russian business structure performing river and sea transportation. The organisation has been successfully operating in the transport and logistics market since 1992. The key cargo transportation routes run through the basins of the Neva, Volga, Oka, Don rivers, the Caspian, Black, and Azov seas, as well as the Gulf of Finland and the seas of the Arctic Ocean.
Orkun Çomuo lu who is the managing
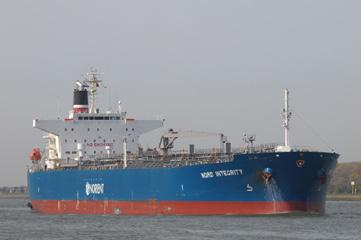
The Nord Integrity
director at Amat Engineering, Subsea Industries’ agent in Turkey said, “These are super ice-class vessels that require extensive hull protection for the operations they (will) undertake. The positive experience with the Antarctic made the choice for the next two vessels much easier for the owner.”
Synergy Group in JV with Norden
UK’s Synergy Group and Denmark’s D.S. Norden have formed a new joint venture (JV) to handle the technical management of Norden’s owned tanker vessels. Norden Synergy Ship Management (NSSM) is a 50/50 joint venture between Norden and Synergy and will be headed by Henrik Christensen who previously managed Norden’s Technical Department.
The formation of NSSM further cements the partnership between Synergy Group, one of the world’s leading ship managers with a fleet of over 300 vessels, and Norden, the globally renowned independent shipping company founded in 1871 and listed on the Nasdaq Copenhagen exchange.
Last year, Norden appointed Synergy Group to manage its fleet of owned bulk carriers, with management services provided from Synergy’s head office in Singapore and its technical office in Chennai, India.
NSSM will manage Norden’s current fleet of Medium Range (MR) and handysize product carriers from its headquarters in Copenhagen, Denmark, with additional technical support provided by a 100%-owned subsidiary based in India.
Seafarers currently employed directly by Norden will be transferred to the joint venture where they will continue their employment on Norden-owned vessels under the same terms and conditions as before. All other seafarers will be offered new contracts through Synergy.
New welding unit from ESAB
For those who need enhanced multi-process welding capabilities and portability in harsh industrial environments, ESAB Welding & Cutting Products has introduced its Aristo 500ix inverter-based welding power source and ESAB design the Aristo 500ix inverter and Robust Feed Pulse/U6 wire feeders for advanced performance and reliability in extreme environments
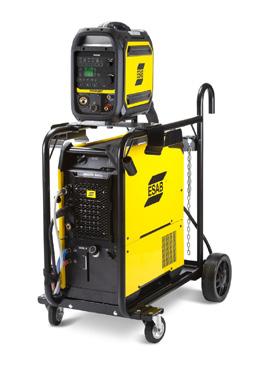
Robust Feed Pulse and Robust Feed U6 wire feed systems.
The Aristo 500ix provides outputs for MIG/ MAG, flux cored, MMA and TIG welding, offering maximum output of 500A/39V at 60% duty cycle and a 100% duty cycle rating at 400A/39V. When paired with Robust Feed Pulse or U6, users can weld with solid wire up to 2.0 mm and cored wire up to 2.4 mm. These feeders offer a 50 mm dinse terminal on the back for connecting an MMA electrode holder, while the Robust Feed U6 also enables gouging from the wire feeder.
Housed in a weather-protected IP23-rated case, the Aristo 500ix has a cooling design that isolates electronics from dust, oil, metal shavings and other airborne contaminants. Thick, double bent metal side panels provide impact protection, yet the design enables easy access for service and maintenance. Its ergonomic handles are crane rated. The optional trolley also features dedicated crane lifting points, as well as a torch holder and large cable holders for better organisation.
Robust Feed Pulse and Robust Feed U6 feature the industry’s only IP44 rating to protect the unit against dirt, mud, splashes and even heavy rain. The primary power cable secures to the rear of the unit with a twist lock connection that eliminates stress on the positive power terminal and gas connections inside the case. There is no strain or risk from shearing off a cable or hose connection if an operator drags the feeder by the cables between the feeder and power source.
A heat kit inside Robust Feed wards off condensation and keeps the wire dry, while a cooling fan manages heat in operating conditions up to 55o C without the need for cooling vents. Robust Feed also offers best-inclass ergonomics, crane-rated lifting options and an optional wheel that affixes to either the bottom or side of the unit to provide a very stable wheeled solution. The digital display can be rotated 90o for a vertical or horizontal orientation so operators can read parameters without straining.
Robust Feed Pulse/U6 accept wire spools up to 300 mm, measure 595 mm x 250 mm x 430 mm and weigh 18.3 kg. The precisely crafted 4-roll drive stand accommodates 38 mm drive rolls and feeds wire at speeds of 0.8–25.0 m/min. The design improves accuracy at lower speeds, has the power to feed cored wires and the high speeds necessary for smaller diameter hard wires. These feeders offer all the benefits of a premium workshop wire feeder for controlling MIG/MAG functions, including synergic pulse, amperage target setting, 2/4-stroke trigger control, creep start, hot start, crater filling, adjustable burn-back time, gas pre- and post-flow time, gas purge/wire inching and more.
Robust Feed Pulse control functions are easy to find, set and fine-tune, while the Robust Feed U6 offers the ultimate combination durability and advanced functionality, including parameter limits and parameter lock for better repeatability. Both panels feature QSet, which automatically optimises the short circuit arc for the gas/wire combination installed and then adapts welding parameters to match an operator’s individual welding style.
Icons, push buttons and digital displays simplify use and eliminate language barriers. To begin pulsed welding, operators simply
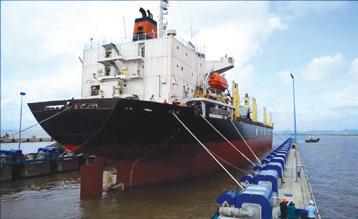
The 4BZFM brakes are specialised for marine and offshore applications and are seawater-proof thanks to an IP67 ingress protection rating select the synergic line. The system then provides optimum dynamic arc control to maintain consistent penetration and weld bead appearance, automatically adjusting for variations in arc length and wire feed speed. Robust Feed Pulse offers 93 synergic lines and Robust Feed U6 offers 92 synergic lines to address a wide variety of steel, aluminium, stainless steel and high alloy solid and cored wires.
Shiplift system winches from Stromberg
Since the dawn of large-scale shipbuilding and repair, a principle challenge has been moving ships from sea to land and vice versa - making shiplifts a crucial part of any modern shipyard. Working under huge loads, it’s important that key assemblies such as brakes are up to the task.
An Italian winch and gearbox manufacturer providing assemblies for a shiplift system approached Stromag to provide 4BZFM brakes that could deliver reliable stopping power for the system’s hoists.
As of 2018, the global shipbuilding market was worth a staggering US$114.3bn with 281 active shipyards operating world-wide. Over 50,000 merchant ships form the spine of the international trade network while the world’s 10 largest navies have an estimated 4,185 vessels in active service. What both merchant and naval fleets share in common is the need for expansion and repairs. Consequently, shipyards are important facilities.
Most modern shipyards utilise immensely powerful shiplifts, which can raise and lower huge vessels in a controlled manner. A shiplift works by positioning a platform underneath the ship, which is then raised or lowered by multiple hoists in synchronicity. This allows horizontal or angled (if ballast is a factor) lifting of the ship, ideal for launching or drydocking vessels.
Consequently, the vessel can be released out to sea or moved to an onshore transfer system for maintenance work in a highly streamlined manner. This contributes to a reduced time for repair, which benefits the shipyard in terms of efficiency and reputation.
Lifting a load as large as a ship requires a mix of precision, power and reliability. Any loss of synchronicity risks the ship tipping, so power transmission equipment must move the huge load in a highly controlled manner. Furthermore, in conditions such as a loss of power, the hoists must be able to brake effectively to hold the vessel in place. Added to this, are the inherent corrosion risks of a salty application environment, which can damage poorly specified equipment.
Considering this balance between power, precision and reliability, a leading Italian winch and gearbox manufacturer approached Stromag, a leading brand of Altra Industrial Motion Corp., to provide a reliable and robust braking solution to be incorporated into shiplift hoists. The shiplift systems were destined for a shipyard which was aiming to improve its launch and dry-docking efficiency.
The 4BZFM Series electromagnetic, springapplied, double-face brakes were specified, which are specialised for marine and offshore applications. Supplied in size 16/13, each provided a static braking torque of 130 Nm. Installed on the winch’s gearbox, the brakes provide stopping and parking functionality in the case of power loss. Each unit was modified to incorporate a special mounting flange and radial cable.
The 4BZFM is seawater-proof thanks to an IP67 ingress protection rating. Furthermore, all steel components feature special nitrocarburated and postoxidated surfaces to provide a high level of durability and corrosion protection.
Chevron agreement for ABS
ABS and Chevron Shipping Company have taken the first step in a pioneering digital fleet management journey with ABS Smart notations for vessels. The 155,374 dwt Suezmax lightering vessel Pegasus Voyager is the first vessel in Chevron’s fleet to receive the ABS maintenance optimisation notation SMARTMHM (Machinery Health Monitoring), with the Polaris Voyager on course to receive the notation soon with more vessels expected to follow.
The Pegasus Voyager is the first ABS-classed vessel to qualify for the SMART-MHM notation. It is just the beginning of ABS and Chevron’s journey to condition-based maintenance for the company’s fleet of 28 vessels. Chevron’s Asset Integrity team and the ABS Digital Solutions team are working closely on digital
strategies to drive enhanced risk management, streamline the class interface and increase asset availability. “Together, ABS and Chevron are shaping the next generation of maintenance methodologies, delivering future class services and driving the evolution of maritime safety in a digital world. As a leader in maritime digital technologies, ABS is proud to be working with industry leaders such as Chevron to challenge traditional approaches and develop advanced services for the benefit of our clients and members,” said Kash Mahmood, ABS Senior Vice President, Digital Solutions.
“We value the opportunity to partner with ABS and further utilise the investment Chevron Shipping has made with predictive maintenance tools. The ABS Smart Function approved technology provided by the DEI Group is installed on twenty of Chevron’s vessels and clearly demonstrating value. The system provides visibility into equipment health that is unavailable with any other monitoring systems allowing us to quickly identify and act
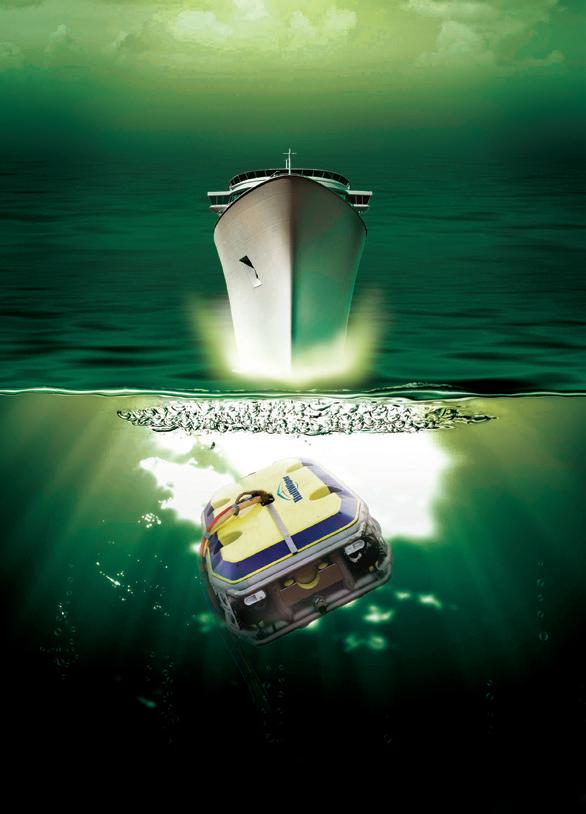
on degrading conditions. Not only do these tools make our vessels more reliable, but they also reduce our costs by avoiding expensive equipment failures,” said Steve Brady, Asset Integrity Manager, Chevron Shipping.
Chevron has long been a leader in proactive maintenance, acquiring the PMP (Preventative Maintenance) notations for its fleet and utilising a range of ABS remote survey services. The ABS SMART-MHM notation leverages Chevron’s investment in fleet sensor technologies to support remote analytics, utilising machinery data for Class crediting. The notation allows ABS and Chevron to align maintenance strategies for the Pegasus Voyager and Polaris Voyager to specific condition-based survey approaches.
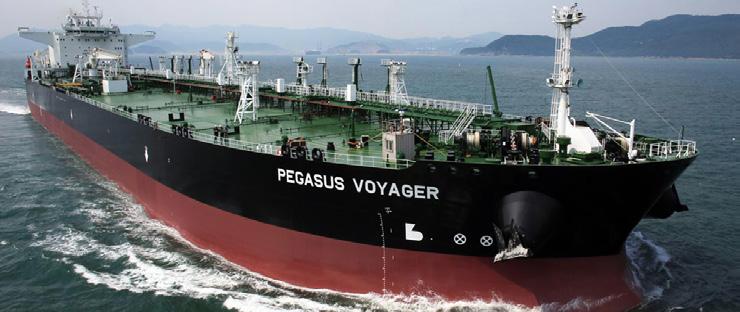
Chevron’s Pegasus Voyager
