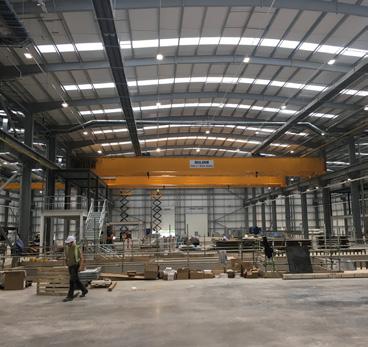
19 minute read
Machinery Repairs
New service centre for Sulzer
Work on Sulzer’s new state-of-the-art service centre in Birmingham, UK, is continuing to schedule. As planned, the building is now watertight, and attention is turning to the internal construction of the workshop area and the offices. Customers can expect the new facility to be open towards the end of autumn 2020, and in the meantime, the existing service centre will continue to work at full capacity.
Advertisement
Located in the prestigious Birmingham Business Park, Sulzer’s new service centre is rapidly taking shape with the main building shell in place and sealed. While the construction continues, plans for moving all the staff and their tools and equipment are being finalised so as to avoid any interruption in service to customers.
Warren Bell, Project Manager for Sulzer, commented, “Now that it is watertight, we can really make some progress inside this fantastic building. The office floors are in and soon we will have a massive concrete pour for the workshop floor. Once this is complete, we will really start to see the various business areas take shape.”
A great deal of planning has gone into developing the most efficient work flows for each area of the service centre. Together, they will deliver a wide range of capabilities, all using lean manufacturing techniques, to ensure all maintenance and repair projects are optimised. A specialist logistics company will be relocating all of the machinery and equipment over a two-month period with a seamless move that will ensure that every customer has a smooth transition to the new site. In addition to the
The new Sulzer service centre in Birmingham, UK existing equipment such as the copper rolling mill, winding machines and the high voltage test-bed, Sulzer is also investing in additional equipment, such as new ovens and paint booths.
Chris Powles, Head of Electro Mechanical Services – EMEA, added, “This new facility will be an engineering centre of excellence using lean manufacturing principles to ensure an enhanced customer experience. The improved working environment and more efficient processes will benefit our employees as well as our customers, who will have uninterrupted, high-level service throughout the transition to the new site.”
Dredger repair by Thordon Bearings
The 7,800 kW cutter suction dredger (CSD) Umm Al Anber, operated by Abu Dhabi’s National Marine Dredging Company (NMDC), has completed the refurbishment of its cutterhead shaft bearings as part of an extensive refit at Dubai Maritime City (DMC).
Thordon Bearings’ Dubai-based distributor for the Middle East, Ocean Power International (OPI), replaced the cutterhead and intermediate line shaft bearings like-for-like with Thordon’s water-lubricated Composite system. The turnkey project included shaft dismantlement, laser alignment, in-situ line boring, calibration, installation and commissioning.
Mohammed Fawzy Khalifa, Fleet Manager, NMDC, said, “We have been using Thordon’s grease-free elastomeric polymer bearings since the 1990s. Compared to traditional rubber cutterhead bearings, we find that Thordon Composite reduces vessel operating costs substantially. The bearing requires no lubricating grease and extends bearing wear life fourfold, which is very impressive given the type of environments in which these dredgers operate.”
The 1995-built Umm Al Anber has an 800 mm diameter suction pipe and can dredge to depths of 16 m. Rafid Qureshi and Ayman Saad, Managing Partners, Ocean Power International LLC, added, “Together, OPI and Thordon Bearings have been optimising the performance of NMDC’s cutterhead dredgers for more than two decades. Thordon Composite bearings are the preferred choice for NMDC dredgers.”
NMDC has converted all of its dredgers except two to the Thordon system. However, The composite cutterhead bearing installed on the Umm Al Anber
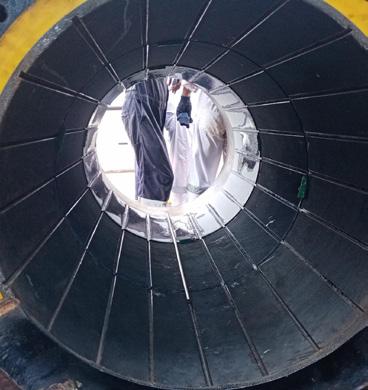
Qureshi revealed OPI is in discussions to convert the rubber bearings on-board these final two vessels.
“We are also in talks to convert the intermediate line shaft bearing to Composite. Replacing worn out rubber bearings with Thordon’s ever-lasting material offers NDMC excellent wear rates, high performance in harsh, abrasive environments, and reduced OPEX,” he said.
George Morrison, Thordon Bearings’ Regional Manager, commented, NMDC has established a strong reputation for delivering high quality projects and services. It is nice to think that Thordon’s water lubricated Composite cutterhead shaft and intermediate bearings have played an important role in that success.”
Late last year, OPI and Thordon replaced the rubber cutterhead shaft bearings on the CSD Al Khatem and the IHC beaver dredgers Embarka 2, Embarka 5 and Embarka 6. The projects followed the success of similar conversions to the Al Sadr,Al Mirfa, Al Hamra, Umm Al Zemoul and the IHC beaver Dredge 2 .
After 100,000 operating hours dredging up silt, sand, rocks and stones in some of the toughest marine environments the Thordon Composite bearing installed on the Al Mirfa’sdredge cutterhead shaft “did not need replacing and was still in perfect working condition,” said Morrison.
“This is due to the bearing’s black homogeneous material, GM2401, which is fused to a stiff, high strength (yellow) polymer sleeve to provide unprecedented performance and environmental safety. Thordon Composite bearings are available for a wide range of shaft diameters in both tube and stave configuration.”
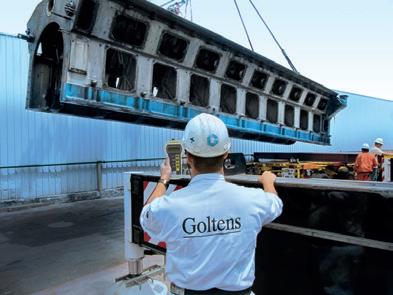
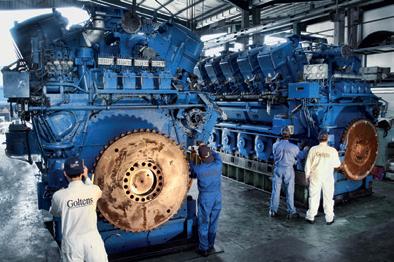

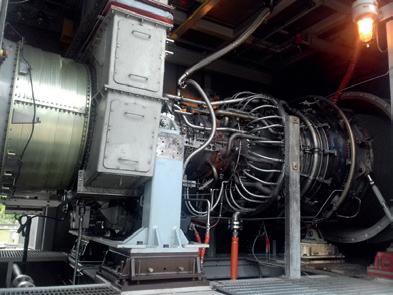
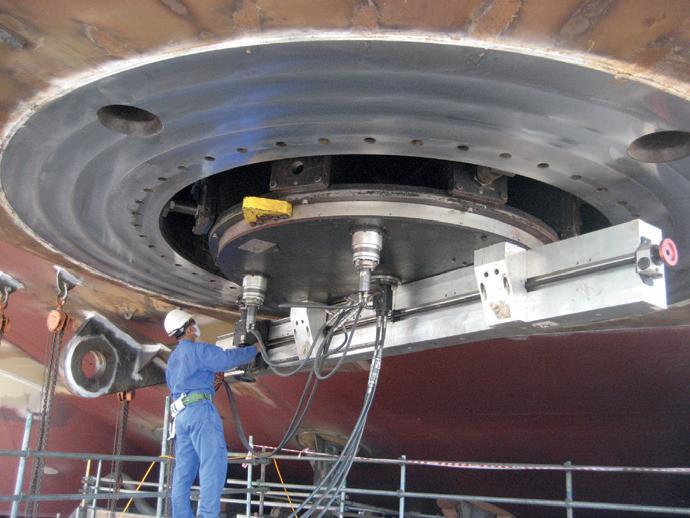
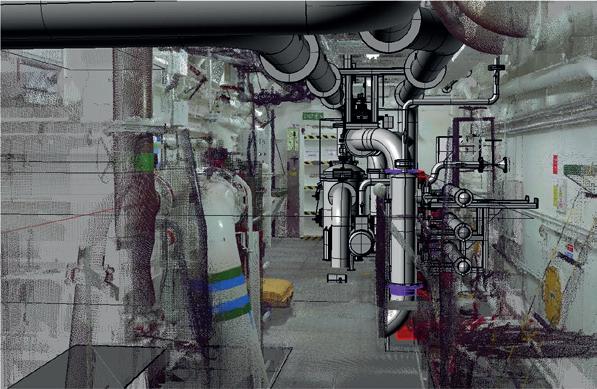
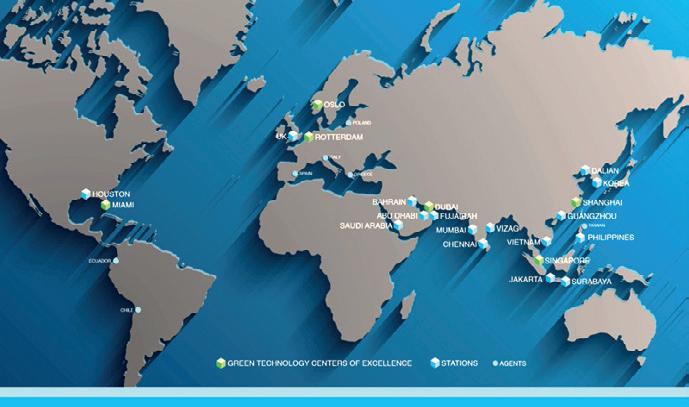
Norwegian hybrid ferries equipped by SCHOTTEL
The first of a total of four SCHOTTEL-equipped hybrid ferries for Norwegian ferry operator Norled – the Festøya, has recently entered operation. Each of the four double-ended ro/ pax ferries built at Remontowa Shipyard in Poland features two SCHOTTEL EcoPellers type SRE 340. These are powered by an innovative diesel-electric hybrid system, and operated by green battery power during transit.
This move further strengthens SCHOTTEL’s position in the Norwegian ferry market. The main propulsion for the LMG 120-DEH design vessels consists of electrically driven SCHOTTEL EcoPellers type SRE 340 with 2.1 m diameter fixed-pitch propellers. These thrusters allow economical operation of the newly built vessels at a service speed of 10 knots and a free running speed of 12.5 knots.
The propulsion units are designed to provide full thrust in the required direction, even with strong side winds. Thanks to the SRE’s outstanding overall propulsion efficiency and course-keeping stability, it is characterised by low operating costs and low fuel consumption, resulting in low emissions.
In operating mode, the required power is supplied by two rechargeable battery packs installed on-board. A shore charging system, which also includes an automatic mooring system, recharges these batteries from the mains when the vessels are docked. The vessels only use generators, run on 100% biodiesel, in an emergency.
Two of the 114.4 m long and 17.7 m wide Norled ferries will service the Festøya-Solavågen route and are capable of taking on-board up to 120 cars and 296 passengers. The other two vessels will operate the Mannheller-Fodnes route and are certified to carry more, with a maximum of 395 passengers. The series is set to be completed during this year.
Meanwhile, according to its Latin American service strategy, Schottel do Brasil will soon be able to offer more services for existing and new marine customers in a new service centre located in Itajaí, Santa Catarina. After German propulsion specialist Schottel enabled its Brazilian subsidiary to acquire land in 2019, the construction work has been making progress.
The 10,500 m² sized plot will be home to a spacious administration, repair and warehouse
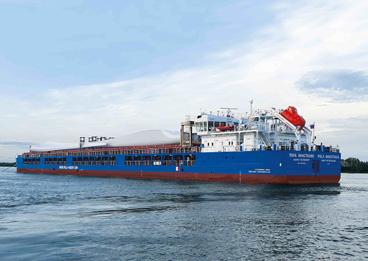
The Russian market is important to Schottel
location. It is expected to be opened in 2021.
The future facility’s services will correspond to local content requirements and will serve customers across Latin America that are building and operating their fleets with the state-of-art Schottel thrusters. According to generations of thrusters which represent a large installed base, with the new location Schottel do Brasil will be prepared for an increased future demand to repair, assemble and maintain Schottel thrusters of all kinds and sizes. Plus, it will ensure an even more extensive customer support.
Schottel do Brasil will merge the administrative offices and the warehouse facilities, which are currently spread out regionally, to the new location, which will offer more logistical advantages, as well as quicker in-house communication.
In Russia, a new service centre is planned for Saint Petersburg to further strengthen OOO SCHOTTEL’s sound market position in this country. In fact, the Board of Management of the German propulsion specialist has already approved the acquisition of a 3,000 m2 plot of land. An administration building with repair workshop and warehouse site is to be planned and constructed on the purchased property within the next two years.
OOO SCHOTTEL has established a strong market position by equipping a large number of inland waterways vessels with propulsion systems, especially in the cargo and passenger transport segments. The decision for a new service centre addresses the customer’s requirements in terms of thruster maintenance.
Scandlines’ ferry fitted with wind sails
The end of May saw the key installation of a new Norsepower Rotor Sail on the Copenhagen, operating on the Rostock-Gedser route between Germany and Denmark. The installation was undertaken as part of the EU funded Wind Assisted Ship Propulsion (WASP) project that was launched in late 2019` with the aim to install five wind assisted propulsion units on to a series of different vessels operating in the North Sea and Baltic Sea to test, validate and help facilitate the uptake off wind-assisted propulsion technologies. These systems are expected to deliver between 4 – 5% fuel savings - corresponding to the same amount of CO2 – in average, and more than 20% in optimal wind conditions.
A couple of months of daily operations on the Copenhagen have been completed since this wind-assisted system was installed and initial impressions of the technology from the crew, the captain and the passengers are already in. The necessary steel foundation (21 tonnes) for the Rotor Sail (42 tonnes) was put in place during an ordinary yard stay back in November 2019. The installation of the Norsepower supplied Rotor Sail itself, the 30 m rotor was installed on the vessel during an overnight stay in the port of Rostock.
This is key as the senior captain of the Copenhagen Alan Bach explains, “We were able to complete almost everything within the limited time of just a few hours. This was key as we are operating on a 24/7 basis, every loss of service or revenue is naturally critical for ferry operations.”
Another key part of the WASP project is the monitoring and validation of the equipment and performance itself. The German environmental association NABU (Nature and Biodiversity Conservation Union), has a long-term partnership with Scandlines focussing on the improvement of the company’s environmental footprint, and is very satisfied with the steps taken.
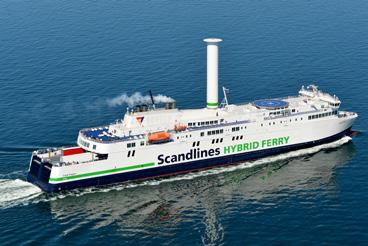
The Copenhagen with a Norsepower rotor sail
What makes this installation particularly interesting and important for the region is that it is installed on a ferry, one of the few places that shipping connects or interfaces with the wider public, and it is at this nexus point that a whole different conversation takes place: What is this cylinder used for? How does it work? Why is it here?
NCL award for Brookes Bell
UK’s Brookes Bell has been contracted by Norwegian Cruise Line (NCL) to deliver its innovative software solution SRtP Onboard across its Breakaway Plus class of vessels. Brookes Bell was engaged directly by the Meyer Werft shipyard for these tasks whose close collaboration greatly enhanced the final output to NCL Holdings.
The software was installed on the newly launched NCL ship, Norwegian Encore in December 2019 including the delivery of training to all crew involved. The software will be rolled out across other vessels including Norwegian Escape, Norwegian Bliss and Norwegian Joy by 2020.
The SRtP Onboard software assists with the management of the response to casualties by providing crew with relevant guidance to support each situation and restore system functionality. The software monitors the response in real time and simplifies a complex logistics process by assigning tasks to groups, either through Wi-Fi connected devices or in paper format, with the required details needed to complete the actions.
Following the introduction of the Safe Return to Port regulations in July 2010, the responsibility to show continuous compliance across a vessel’s lifetime, post build, lies with the operator. SRtP Onboard supports demonstration of compliance to Flag by recording all SRtP drills and also complies with the specific requirements of the Bahamas Authority Marine Notice 03. The system is designed to provide an on-board knowledge base which can be improved after every drill, continuously increasing the efficiency of the SRtP casualty response process.
Giovanni Canu, Vice President Special Projects and Operational Support at Norwegian Cruise Line, added, “In order to ensure our fleet is ready for the operational requirements of Safe Return to Port regulations, we selected The Norwegian Encore in Meyer Werft
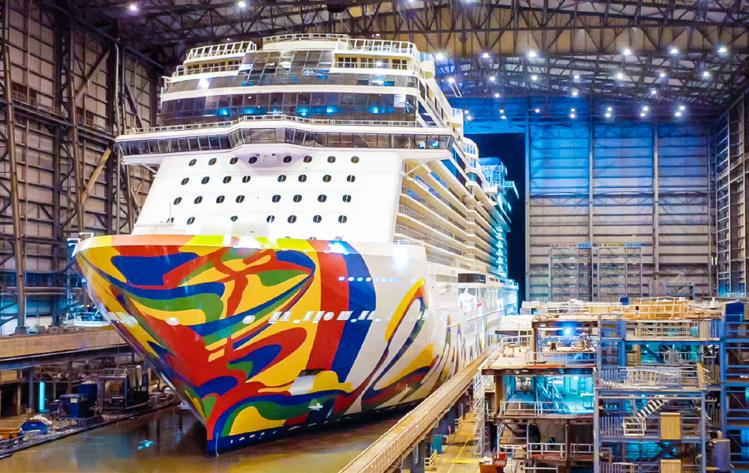
Brookes Bell’s SRtP Onboard software. This offers an efficient and informative solution that has already successfully been installed on Norwegian Encore and will be installed on the rest of our Breakaway Plus class vessels. We also expect to extend this solution to Norwegian Breakaway and Norwegian Getaway.”
Engine diagnostic system from ABB Turbocharger
ABB Turbochargers is to install its state-of-theOne of the Ming Wah fleet art engine diagnostics software ABB Ability Tekomar XPERT on 12 bulk carriers operated by Shanghai Ming Wah Shipping. The fleet-wide deployment follows a trial on two ships which started in February 2019 and an initial order covering four vessels in June 2019. The order for the remaining eight vessels was received in July this year.
Under the initial order, ABB Ability Tekomar XPERT helped Shang Ming Wah save 0.62 tons of fuel/day on each of the four ships. One vessel, with a MAN B&W 6S42MC main engine, recorded a fuel saving of 4.3 g/kWhr,
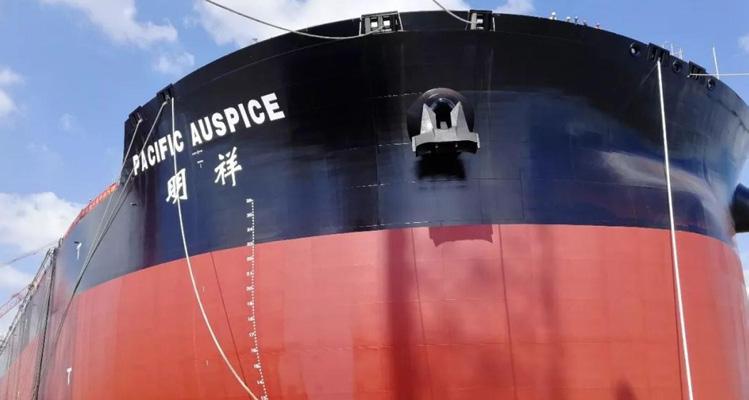
highlighting the significant fuel consumption
advantages the software can bring to highpowered engines in particular. The lower fuel use will lead to a dramatic improvement in environmental performance, reducing fleetwide CO2 emissions by an anticipated 5,800 tonnes a year.
Chen Qiuhua, General Manager, Shanghai Ming Wah Ship Management Centre, said, “With changing market conditions, Shanghai Ming Wah is embracing digital technologies while improving management efficiency, which will enable us to retain our full strength and market competitiveness. ABB is our trusted partner and the Tekomar XPERT digital solution helps our fleet optimise operations while creating a better experience for our customers.”
Tekomar XPERT analyses turbocharger and engine performance to provide pre-emptive warnings and recommendations which can prevent engine failures. In one notable example, Tekomar XPERT helped Shanghai Ming Wah detect high cylinder pressure in one engine. High pressures increase the mechanical load on cylinder components and can lead to operational hazards.
Tekomar XPERT empowers ship owners and operators with key engine indicators provided via intuitive dashboards, allowing them to monitor, optimise and benchmark engine performance while preventing engine problems. It runs on any engine, regardless of type or age and is built on ABB’s Ability platform with the highest standards of cyber security.
PSV installation for NES
The PSV Sjoborg, currently on a five-year charter with Equinor, operates in the North Sea with base in Florø on the North-West coast of Norway. The vessel is equipped with a diesel electric propulsion system, in addition to automation system and Bridge design from Norwegian Electric Systems (NES).
During 2018 the vessel was retrofitted with a Quest Energy Storage system with a 565 kw/ hr battery pack and a 1,500 kW micro-grid connection to the existing AC MSB, in order to
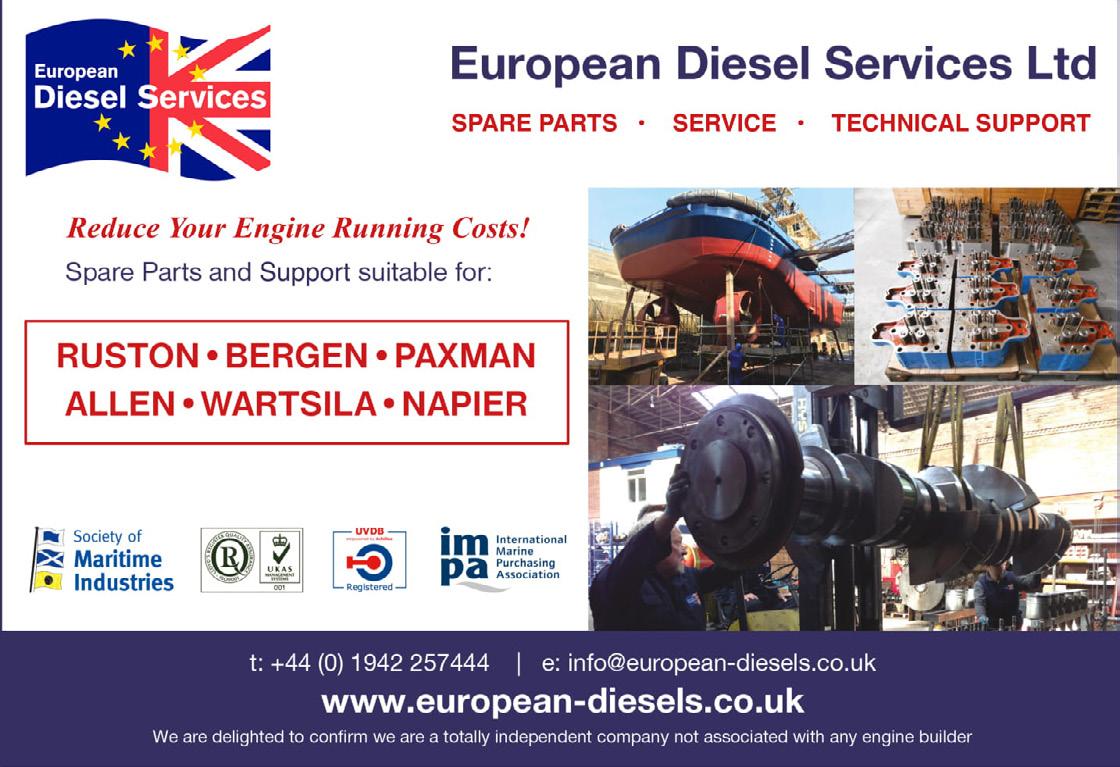
meet requirements from the Tender issued by Equinor - obtaining Battery Power notation from Class.
NES was responsible for system integration and delivery off the Battery container in addition to other necessary integration and software update on IAS/PMS and switchboards. The PSV operates as much as 30% in DP mode supporting the offshore platforms with goods and other support. In this mode the vessel has most advantages with the use of the battery system, with approximately 20% reduction in fuel consumption.
Operating the switchboard with a close bus tie, and reducing the number of engines running the battery system ensures reduced emissions but also reduced cost for the charterer. The size of the battery system is dimensioned with a safety aspect ensuring that the vessel can abort a DP-operation and move into a safe zone outside the platform within 15 minutes. During calm weather conditions, while the vessel is in standby mode, the use of the battery-system also reduces the fuel
The PSV Sjoborg
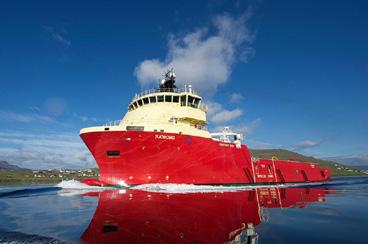
consumption, due to only one required diesel generator running. In addition the Battery system can be used when the vessel is in harbour, either self-supplied or in combination with shore power if available.
As an example Sjoborg used 2.2 – 2.4 m3/ day in fuel before the retrofit. After the retrofit with batteries, the consumption is 1.6 – 1.8 m3/ day, says the Johan Sigurd Fjallsá the technical Manager at Skansi Offshore
An important aspect for the Owner is the reduced maintenance cost for rotating machinery. It is anticipated that the Owner will save as much as 15,000 – 20,000 a year, and the regular yearly maintenance work can be postponed due to decreased running hours.
Skansi Offshore anticipates about 15,000 – 20,000 reduced running hours over a 10 year period.
Making the system optimal for the vessel, through feedback from Owner, understanding the operational profiles and optimising the software has been important for NES. The dialogue between Owner and NES during the past two years has been excellent and both partners enjoy to see the new technology implemented, “contributing to the reduced emission and increased knowledge about hybrid solutions,” says General Manager Sales at NES, Svein Ove Farstad.
CCG order for Wärtsilä
Finland’s Wärtsilä has won a contract for the delivery and integration engineering of two Retractable Thrusters and a Dynamic Positioning (DP) system for the CCGS Amundsen, a Canadian Coast Guard (CCG) Icebreaker. The Wärtsilä equipment is scheduled for delivery in September 2021.
Wärtsilä was able to meet the CCG’s challenging requirements for build quality and fitting the equipment in the existing space of the 98 m long Arctic Class 3 Medium Icebreaker, the only vessel in its class to be fitted with Retractable Thrusters and DP. The new Thrusters will be integrated with the existing Bow Thruster, which is also a Wärtsilä product.
“The Platinum DP system will exceed the functionality desired by the CCG, and will enhance the DP capacity of the vessel to perform sailing and manoeuvring operations. By offering the most intuitive user interface on the market, Platinum DP also reduces the training requirements for successful system operation. The user interface plays a critical role in helping operators make the most of the system in the trying conditions found in Canada’s Arctic waters,” states Mike Ford, Sales Manager for Americas & DP at Wärtsilä Voyage.
“We continue to work closely with the CCG to ensure that we fully understand and successfully meet their requirements for specification writing, documentation and project management. Supplying the products is only part of the picture, since they need to be engineered for complete integration with the CCGS Amundsen’s existing machinery, and for this we have outstanding capabilities,” says Ian Brouwer, Senior Sales Manager, Wärtsilä Marine Power.
Höegh Autoliners contract for KD/MAN
Norway’s Kongsberg Digital (KD) and leading engine manufacturer MAN Energy Solutions are entering into a strategic digitalisation partnership, formalising the MoU signed by the two companies in October 2019. The first project undertaken by the partnership will be to deliver joint digital infrastructure to Norway’s Höegh Autoliners, marking the first step in their stated aim to work together in accelerating the rate of digitalisation in the maritime industry and securing greater value for customers on both sides.
The agreement to collaborate in developing digitalisation solutions for the maritime sector came about as the two companies realised that their separate efforts in this space were complementary. KD’s recently launched Vessel Insight – a new, cost efficient data infrastructure solution for the maritime market – is a natural match with MAN Energy Solutions’ PrimeServ Assist digital solution for optimisation of engine use and maintenance.
Vessel Insight captures contextualised data from vessels and fleets for use in value generating applications for ship owners and operators, so by integrating the data from PrimeServ Assist will be able to provide a more holistic picture for the majority of vessels with MAN Energy Solutions’ two-stroke engines on-board. With two major maritime vendors collaborating on a common data infrastructure, customers will benefit from interfacing with one system instead of many, automated data integration, and a larger selection of digital solutions. This will make the digital transformation faster and more cost efficient for customers in the maritime sector.
“The engine is the most critical component
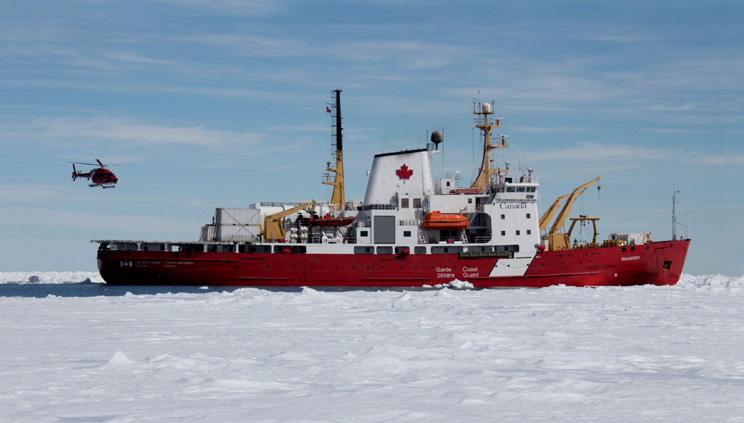
The CCGS Amundsen will be the only vessel in its class to be fitted with retractable thrusters and a DP system
on-board a vessel, and this strategic collaboration will ensure optimal operation and maintenance of the engine,” says Hege Skryseth, President, KD. “This will generate significant value for our customers. We look forward to working together with MAN Energy Solutions and our customers to ensure that they get the digital solutions that fit their capabilities and needs.”
The maritime industry is in a transformational phase and is still learning new ways to extract additional value from digitalisation, and with two major vendors now working together to further develop a powerful, safe and open infrastructure, this transformation will accelerate. For vendors of digital solutions and services, developing value adding applications and software for customers will be easier and more cost efficient, which in turn leads to a broader selection of available solutions. This will speed up the ability to digitalise and gives ship owners and operators a quicker return on their digital investment.
The inaugural project with Höegh Autoliners One of the Höegh Autoliners’ fleet
is currently in a testing and validation phase, with a goal to enable real time engine monitoring and digital assistance for optimisation, while reducing digital equipment on-board. Kongsberg Digital will provide its data infrastructure solution, Vessel Insight, for real time data transfer while MAN Energy Solutions will deploy PrimeServ Assist for engine
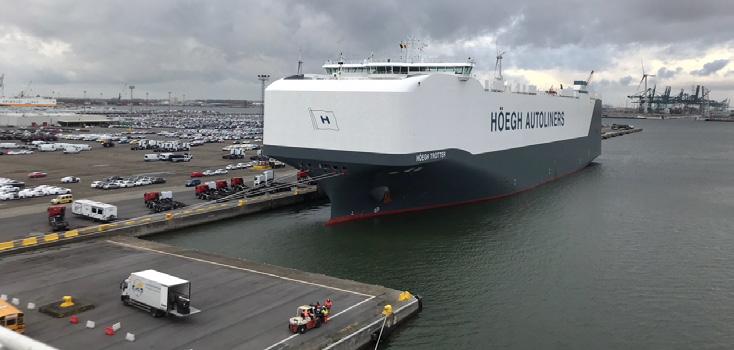
data analysis.
Geir Frode Abelsen, Head of Technical Operations in Höegh Autoliners said, “For us at Höegh Autoliners, this collaboration is an important step towards the utilisation of digital solutions in optimising the running and maintenance of our engines in a safe and effective way.”
LINK marine and offshore instrumentation, automation and controls Dubai [Singapore – Philippines – Thailand]

Your preferred service centre for all automation, electrical, electronic and calibration works for the Marine Industry. MOU with MAN Diesel and Turbo Middle East LLC
Over 900 main engine pneumatic remote control systems overhauled c/w supply of original repair kits Agents for:
NABTESCO
Marine Propulsion Bridge Maneuvering Systems
EVOQUA [Electrocatalytic]
Chloropac®MGPS, CAPAC®ICCP, BWTS SeaCure
BRANNSTROM
ODME, OWS 15ppm, MasterTrack (white box)
NORIS
Alarm Monitoring and Control Systems
MacGREGOR (Ex-INTERSCHALT)
Voyage Data Recorder
BMT SMART
Engine performance and Hull stress monitoring