CLEAN METHOD FOR EMPTYING LARGE BULK BAGS
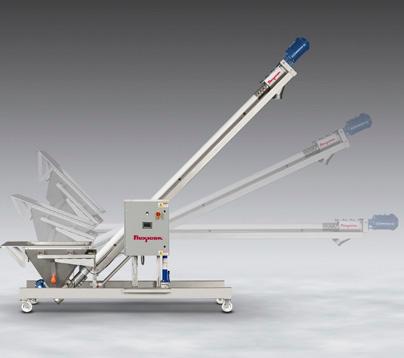
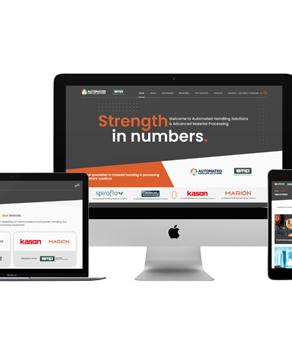
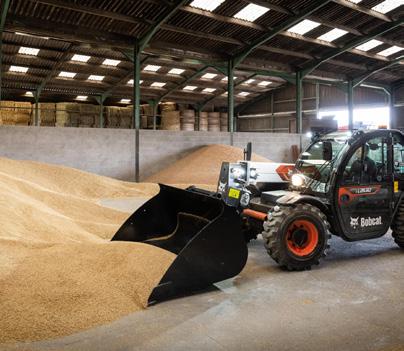

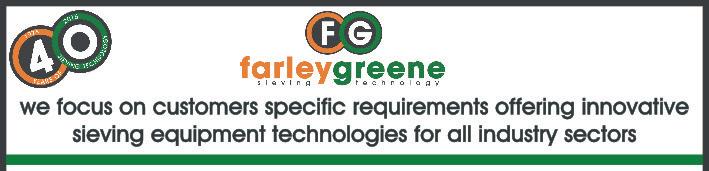
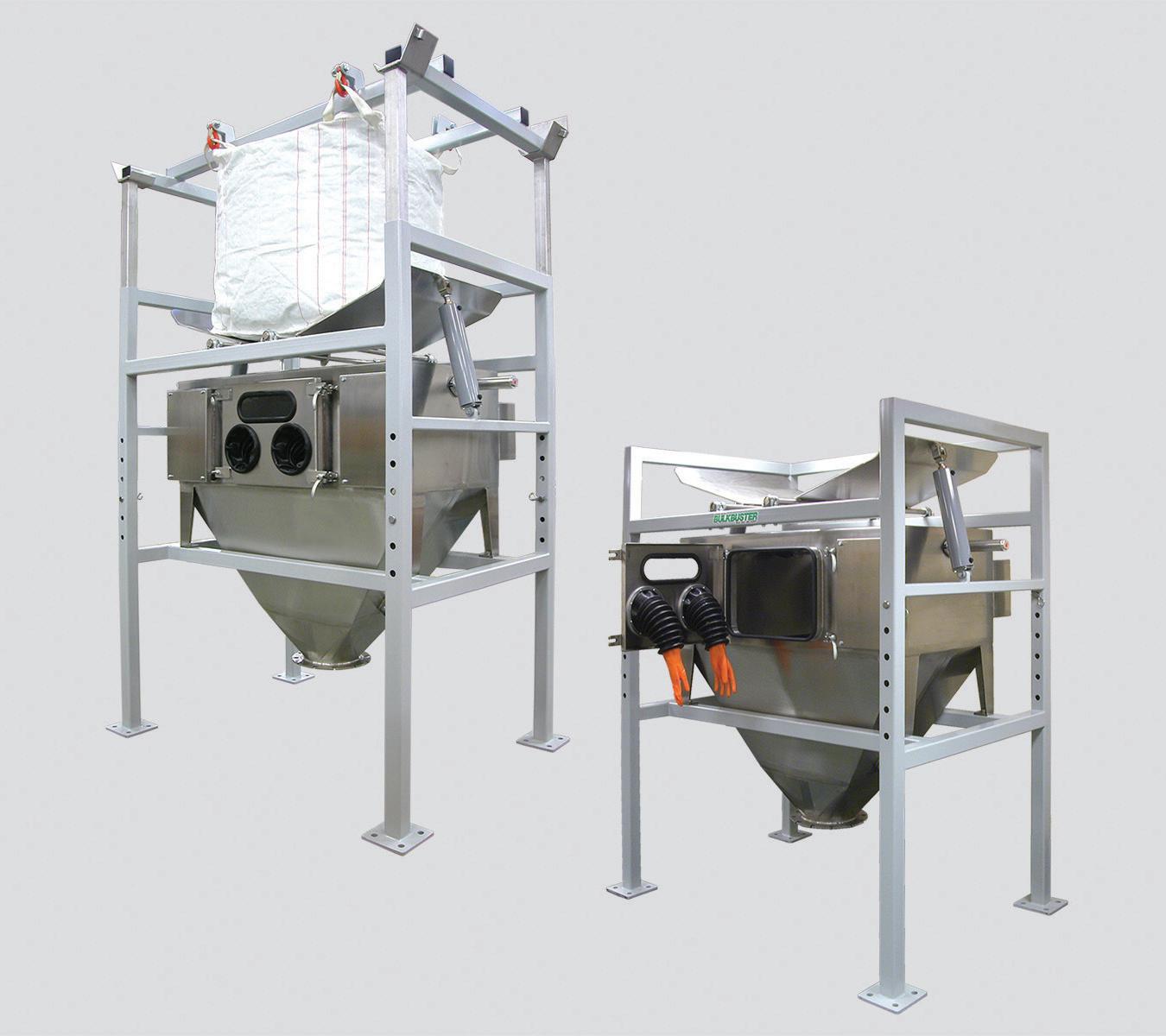
CLEAN METHOD FOR EMPTYING LARGE BULK BAGS
From micron sized powders to large pellets and everying in between, Dynamic Air can move your dry granular materials gently, reliably and with significant reductions in product degradation and/or system wear.
Dynamic Air dense phase pneumatic conveying systems have been proven in over 15,000 installations worldwide. They handle a wide range of materials and bulk densities at rates from less than a hundred kilograms per hour to 400 tonnes per hour, over distances exceeding 1500 metres.
Each Dynamic Air system is custom designed from one of our sixteen different conveying concepts. So you get a conveying solution that fits your process perfectly, without compromises.
Our high material-to-air ratios reduce energy and compressed air requirements. Our low conveying velocities provide significant process savings in both operation and maintenance.
Issue
Sales Director: James Scrivens
Production: Sarah Daviner
Accounts Manager: Avery Hudson
Office Manager: Katie Brehm
BULK SOLIDS TODAY is published 6 times a year by Abbey Publishing Ltd
ADVERTISING & EDITORIAL
Please contact us at:
Tel: 01933 316931
Email: editorial@bulksolidstoday.co.uk advertising@bulksolidstoday. co.uk
Web: www.bulksolidstoday.co.uk
Twitter: www.twitter.com/
BulkSolidsToday
CIRCULATION
To receive a copy free of charge, please send your details to subs@bulksolidstoday.co.uk
No part of this publication may be reproduced by any means without prior permission from the publishers. The publishers do not accept any responsibility for, or necessarily agree with, any views expressed in articles, letters or supplied advertisements.
ISSN: 1365/7119
Automated Handling Solutions (AHS) and Advanced Material Processing (AMP), the combined material handling and processing platforms consisting of Spiroflow and Cablevey Conveyors for AHS, and Kason Corporation and Marion Process Solutions for AMP, have recently released an impactful new group website.
The launch follows the formation of AHS and AMP by Chicago-based private equity firm, May River Capital, both created to offer a differentiated and comprehensive suite of material handling equipment and industrial automation solutions.
The site provides top-tier introductions for each brandSpiroflow, a global manufacturer of material handling equipment and provider of control systems integration, and Cablevey, a global speciality conveyor manufacturer that designs, engineers, assembles and services tubular drag cable and disc conveyor systems - together with Marion, a leading producer of industrial mixing, drying and integrated material handling solutions, and Kason creating sifting, sorting, drying, cooling, and particle reduction solutions.
Featuring a fresh, modern design for a worldwide audience, the website has been created
with the user experience in mind. Providing a clear insight into this unique collaboration, the site explains how each of the four brands unifies their expertise and capabilities to deliver integrated core competencies and marketleading product portfolios to customers globally.
Key features include contentrich sections giving access to each brand’s product portfolios, as well as a range of industries, including food & beverage, pharmaceutical, chemicals, pet foods, minerals and more, where each brand has extensive knowledge and expertise. The site showcases the group’s extensive testing centres, where feasibility studies can be conducted in small quantities prior to scalability testing of larger batches of materials. The site, which includes full language options, also provides the user with every opportunity to ‘Talk to an expert’ -
Bulk Solids Today is the bi-monthly digital journal covering the storage, processing and handling of materials ranging from fine powders to the heaviest raw materials.
To subscribe to Bulk Solids Today magazine or for more information, please feel free to visit www.bulksolidstoday.co.uk
a repeated call to action designed to encourage conversations and progress material handling and processing enquiries.
Commenting on the site, May River Executive Resource Group member, acting CEO of Cablevey and Executive Chairman of AHS designate, Brad Sterner, said: “In showcasing the significant expertise of each brand in providing unrivalled product offerings and specialisms, the website has fully achieved its aim. The content provides visitors with access to significant resources across the combined product ranges, enabling them to solve their material handling or processing queries. Through its launch, we look forward to continuing to increase market share in our served global, highgrowth end markets.”
For more information visit www.amp-ahs.com.
Solids handling equipment manufacturer, Ajax Equipment, has supplied one of the UK’s leading providers of resource management with an ash conditioner, including wear resistant mixing paddles and clean-in-place features, for the processing of Air Pollution Control Residues (APCr).
APCr is treated to convert it into a non-hazardous state suitable for storage. Effectively treating APCr requires thorough mixing of the ash with acidic liquor to ensure the materials are combined to homogeneity. Ajax achieves this by basing the design of its ash conditioners on its twin screwed continuous mixer, using spray bars to deliver a controlled supply of liquor directly where the mixing action is greatest.
As a result of the ash’s abrasive nature and Ajax’s experience, it was recommended that the paddles be produced from a wear resistant steel to ensure the performance of the conditioner. The fitting of the paddles also makes them easy to remove, minimising downtime should they need replacing.
“Ashes such as APCr require careful handling due to the hazardous nature of the material but also because if left it is likely to set in the conditioner, affecting its performance. To prevent material setting and minimise operator exposure the customer requested a clean in place system for the conditioner. Swivelling spray bars with profiled spray nozzles provide good cleaning coverage while the conditioner’s counterbalanced covers allow
easy inspection internally,” says Eddie McGee, managing director, Ajax Equipment. For more information on Ajax Equipment solids handling and processing equipment, call +44 (0)1204 386723, email sales@ ajax.co.uk and visit www.ajax. co.uk.
The Pump & Motor Division Europe of Parker Hannifin, the global leader in motion and control technologies, has announced the launch of its new disengageable twin flow truck pump, the F4 series, as an innovation for the mobile hydraulics market.
The new F4 hydraulic pump merges technology from the successful F2 twin flow pump and F3 axial piston fixed pump series, resulting in a simple and flexible solution for any vehicle requiring separate flows of differing capacities. This will have multiple applications in vehicles such as salt spreaders, hook loaders, forestry cranes, sewage trucks, snow ploughs and many others.
The patented clutch function lets the user engage and disengage the pump from the diesel engine on the move, without turning the engine off, by pressing a switch on the dashboard. This enables substantial fuel savings and a significant reduction in CO2 emissions.
If, for example, a truck (with a hook loader and a detachable snow plough) that utilizes the new F4 series pump runs for 260 hours in its first month using power take-off (PTO) for just 56 of those hours, around 1.2 kW per hour less power is required when the pump is disconnected. This equates to about 50 liters less fuel needed in that month alone, and in a year, the possible savings could exceed 600 liters (especially where the snow plough is in use only for a few of those months). The CO2 emissions are therefore also reduced by around 1.8 tonnes.
In addition, the clutch feature reduces wear and tear on the pump and minimises the risk of costly downtime and standstills,
while also reducing the noise emission levels.
“The ability to disengage a twin flow pump is a huge money saver in terms of fuel savings and less wear on the pump. In the situation of a hydraulic hose failure, users also would be able drive to the workshop instead of the truck being towed, resulting in less downtime,” stated Anders Larsson, Product Leader at Pump & Motor Division Europe.
Learn more about the F4 pump series at: https:// ph.parker.com/ gb/en/axialpiston-fixed-pumpsseries-f4
Unlike other valves that seal with friction, Posi-flate’s unique butterfly valve uses an inflatable seat to seal with air pressure. Thus it requires less torque and a smaller actuator, resulting in lower cost. Plus, the seat automatically compensates for wear, providing longer life. Some users have reported over six million cycles and the valves are still going strong.
• Less friction
• Low torque
• Low maintenance
• Lower actuator costs
• Longer valve life
• More reliable
The robust OMRON TM20 improves cycle times and comes with a two-year warranty after registration
OMRON, a leading provider of industrial automation solutions, has announced the launch of its new OMRON TM20 cobot with a payload of 20 kg. The new cobot is ideal for tasks such as palletizing, machine tending and material handling. Whilst managing heavy payloads, the OMRON TM20 has a small footprint and a reach of 1,3 meters.
The OMRON TM20 is the latest addition to the OMRON family of TM cobots, which are known for their ease of use, reliability, and safety. It is designed to work seamlessly with other OMRON products, including sensors, controllers, and software, to provide a comprehensive automation solution for industrial customers.
One of the key features of the OMRON TM20 is its lightweight
design, weighing in at just 33 kg. This makes it easy to integrate with mobile robots, providing greater flexibility and efficiency in industrial environments. The robot also comes equipped with special joint covers to protect it from cutting oil and other hazardous materials, making it suitable for use in machine tending applications.
“We are excited to launch the OMRON TM20, which expands the capabilities of our cobot family and gives customers the ability to automate heavy payload applications,” Fernando Vaquerizo, Fixed and Cobots Product Marketing Manager at OMRON Europe. “The OMRON TM20 is designed to be easy to use, reliable and safe. It relieves operators from tasks that involve heavy lifting, while working safely side by side with people.”
OMRON’s ROI calculator supports companies in the process of evaluating an
investment in collaborative robots, including easy and affordable leasing opportunities. In addition, OMRON offers a wide range of support services, including installation, training, and maintenance, to ensure customers get the most out of their investment.
Key features and benefits:
• 20 kg payload capacity for handling heavier parts and materials
• Reach of 1300mm ideal for palletizing applications
• Cycle improvements thanks to faster joints
• 24 months warranty after registration
The OMRON TM20 collaborative robot is available for pre-orders now. For more information on the OMRON TM20 and other OMRON cobots, please visit the company’s website at http:// industrial.omron.eu/cobots
If you would like to subscribe to receive a regular copy of the digital edition of Bulk Solids Today magazine, you can subscribe on our website - www.bulksolidstoday.co.uk
If you are interested in advertising within Bulk Solids Today magazine or supplying editorial content, please feel free to get in touch using the details on our website or below.
Bulk Solids Today is sent to our digital readership of over 9,000 Chief Engineers, Operations Managers and Technical Managers from within sectors including Chemicals, Food & Drink, Mining, Quarrying, Transport/Distribution, Recycling & Waste Management and more.
www.bulksolidstoday.co.uk
Automated Handling Solutions (AHS) and Advanced Material Processing (AMP), materials handling and processing platform companies consisting of Spiroflow and Cablevey Conveyors from AHS, and Kason Corporation with Marion Process Solutions from AMP, will be exhibiting on Stand D23-5 in Hall 15 at Interpack 2023 on 04-10 May at the Düsseldorf Trade Fair Centre.
Alongside impressive materials handling and processing equipment displays, senior representatives from both AHS and AMP will be on hand to show how the four brands combine their industry-leading product portfolios, to provide exceptional turnkey solutions to solve the most challenging applications. The show will also provide an opportunity for AHS and AMP to promote their new Germany-based European Test Centre, which opened on 1 April. In addition, they will be introducing Maschinen Wagner on stand as a packing machines partner.
At the event and on behalf of AHS, Spiroflow will be showcasing its reputable Flexible Screw Conveyor (FSC) together with an Aero Mechanical Conveyor (AMC), while Cablevey will be demonstrating its enclosed tubular drag conveyor - ideal for moving materials in a safe, clean and efficient manner. Both the FSC, AMC and Cablevey conveyor will
be running continuously throughout the show using various products.
For AMP, Kason will have their centrifugal sifter, the CENTRI-SIFTER™, on display. Engineered to sift, scalp, de-lump, and de-water virtually any bulk solid or slurry, the CENTRI-SIFTER™ is available in many configurations designed to solve specialised problems and continuously deliver high performance. Kason will also have its industryleading circular vibratory screener and separator, the VIBROSCREEN®, with a multi-deck version on stand, while Marion will be displaying its Horizontal Paddle Mixer.
Antoine Lecomte, vice president of sales and business development Europe for AHS and AMP, said: “As a solution provider for multiple industries, being at Interpack provides a unique opportunity to showcase our know-how to visitors and to the industry in general. It is also an excellent opportunity to continue showcasing our latest innovations, as well as our new European capabilities when it comes to testing customers’ products in actual industrial scale equipment.”
For more information on AHS-AMP visit https:// amp-ahs.com/.
If you would like to subscribe to receive a regular copy of the digital edition of Bulk Solids Today magazine, you can subscribe on our websitewww.bulksolidstoday.co.uk
If you are interested in advertising within Bulk Solids Today magazine or supplying editorial content, please feel free to get in touch using the details on our website or below.
Bulk Solids Today is sent to our digital readership of over 9,000 Chief Engineers, Operations Managers and Technical Managers from within sectors including Chemicals, Food & Drink, Mining, Quarrying, Transport/ Distribution, Recycling & Waste Management and more.
www.bulksolidstoday.co.uk
bst@abbeypublishing.co.uk
Tuf-Lok ring grip pipe and tube couplings are rugged, heavy duty, self-aligning and self-grounded couplings with a high end pull. They can be used for almost any application where pipe or tube ends need to be connected. The Tuf-Lok self-aligning couplings install quickly and easily with little effort. Features
• Self-aligning
• Self-grounding
• High pressure rated
• Full vacuum rated
• Stainless or mild steel
• Usable on thin or thick wall pipe or tube
• Low cost
• Reusable
• Absorbs vibration
• Externally leakproof
Dynamic Air BulkBuster bulk bag unloaders provide the solution for effectively emptying large bulk bags and getting the material where you want it in your process. Safety is always a primary concern when handling and maneuvering extremely heavy and cumbersome bulk bags. The Series 422 Model 1900 BulkBuster bulk bag unloader offers a continuous cleaning method of discharging bulk bags because it includes internal dust collection for containing all fugitive dust. Features include easily removable bayonet mounted cartridge filters for recycling the fugitive dust by discharging it back into the process hopper below. Also included is a bag closing device, sight glass and work gloves to allow the bulk bags to be untied and emptied without
contacting any of the process material being discharged. One unique but standard feature is a set of air operated bulk bag jostlers for massaging the bulk bags for faster discharging of difficult to handle materials. An optional bag closing mechanism is also available to allow partial bulk bag unloading.
https://www.dynamicair.com/products/ bagunloaders.html
Dynamic Air Ltd.
Milton Keynes, United Kingdom
+ 44 1908 622344
E-mail: sales@dynamicair.co.uk
www.dynamicair.com
Solids handling equipment manufacturer, Ajax Equipment, has supplied one of the UK’s leading providers of resource management with an ash conditioner, including wear resistant mixing paddles and clean-in-place features, for the processing of Air Pollution Control Residues (APCr).
APCr is treated to convert it into a nonhazardous state suitable for storage. Effectively treating APCr requires thorough mixing of the ash with acidic liquor to ensure the materials are combined to homogeneity. Ajax achieves this by basing the design of its ash conditioners on its twin screwed continuous mixer, using spray bars to deliver a controlled supply of liquor directly where the mixing action is greatest.
As a result of the ash’s abrasive nature and Ajax’s experience, it was recommended that the paddles be produced from a wear resistant steel to ensure the performance of the conditioner. The fitting of the paddles also makes them easy to remove, minimising downtime should they need replacing.
“Ashes such as APCr require careful handling due to the hazardous nature of the material but also because if left it is likely to set in the conditioner, affecting its performance. To prevent material setting and minimise operator exposure
the customer requested a clean in place system for the conditioner. Swivelling spray bars with profiled spray nozzles provide good cleaning coverage while the conditioner’s counterbalanced covers allow easy inspection internally,” says Eddie McGee, managing director, Ajax Equipment. For more information on Ajax Equipment solids handling and processing equipment, call +44 (0)1204 386723, email sales@ajax.co.uk and visit www.ajax.co.uk.
Bobcat has launched the new TL25.60 AGRI Super Compact telehandler. This new addition extends Bobcat’s telehandler range for the agricultural market to eight models, offering rated capacities up to 4.3 tonne and lifting heights up to 7.5 m. The TL25.60 AGRI is powered by the D24 Stage V diesel engine providing 56 kW (75 HP) of power, has a rated operating capacity of 2500 kg, maximum lift height of 5.9 m and a fully extended reach of 3.3 m.
Florian Hilbert, Product Manager Telehandlers at Bobcat EMEA, said: “The innovative design of the TL25.60 AGRI is based on intensive analysis of customer and application requirements in agriculture. This ensures the new telehandler is simple to use, offers excellent stability and provides optimum comfort and productivity in any type of work on the farm.”
The arrival of the new TL25.60 AGRI follows on from the successful launch of its counterpart model for construction, rental and associated industries in late 2022. Like the construction machine, the TL25.60 AGRI is compact and agile for optimum manoeuvrability on the farm. Whilst there are similarities, the TL25.60 AGRI offers many more features specifically for agricultural customers, including:
• Front auxiliary with hydraulic flow of 80l/ min
• Boom cushion retract as standard
• Three AGRI finishing levels to choose from
• Large variety of tyre choice
• Air suspended seat
• Cab+ AGRI option containing all required AGRI features within the cab
• Electric mirror with de-icing
• Hand throttle
The TL25.60 AGRI offers superior comfort, with a roomy cab which offers easy stepless access via the large entry door with ergonomic handholds. Inside the cab there is a tilting steering column as standard and telescopic as an option, which can be adjusted for the convenience of the operator.
Florian Hilbert added: “The TL25.60’s cab is identical to that of some of Bobcat’s larger models, making it the most spacious compact telehandler on the market today. The intuitive operating system on the TL25.60 AGRI allows operators to quickly master the controls and joystick layout - ideal for both experienced and novice operators. The machine also provides excellent visibility and ease of use, so that all workers can use the machine on the farm.”
Users of the TL25.60 AGRI have industry-
leading expertise at their fingertips, enhancing their work with the innovative smart technology found throughout the machine. This includes unique Bobcat features such as maximum lifting angle and return-to-ground functions, boom suspension, boom float and the automatic fan inverter system on the machine.
This is combined with the high productivity provided by the impressive loading capacity and fast cycle times thanks to the flow-sharing function as standard on the TL25.60 AGRI. The smooth hydrostatic transmission and flow sharing ensure precise control at any height.
Using the same main valve as the larger models from the Bobcat range, the TL25.60 AGRI has the best cycle times on the market. The high pushing and breakout force on the TL25.60 AGRI give operators all the power they need with dependable torque and hydraulics, supported by the robust build of this machine.
The high performance of the TL25.60 AGRI is matched by the maximum uptime that results from the straightforward maintenance requirements, including direct access to all major components around the engine. In addition, the large bonnet and no-tool design of the maintenance cover allow operators to easily perform regular maintenance tasks themselves.
The robust build and high protection for machine components provided by the box-welded frame is
part of the high standard for quality and toughness found on all Bobcat machines including the TL25.60 AGRI. The protected critical components mean the machine can be operated in even the most demanding applications.
The versatility built into the design of the TL25.60 AGRI allows the operator to choose from a wide range of available attachments and different carriage systems. The Bob-Tach carriage allows users to connect even the most advanced attachments – which handle everything that can be thrown at them – and tackle any jobs on the farm with ease.
Florian Hilbert commented: “The TL25.60 AGRI is a machine that can be trusted in any situation on any farm. The superior stability, balance and visibility offers unrivalled peace of mind. The machine enables operators to work day and night, aided by the large mirrors, rear-view camera and powerful LED lights.”
Bobcat TL25.60 AGRI in action
https://youtu.be/COykUk9NNO4
Bobcat TL25.60 AGRI Customer’s first impressions at mussel farm
https://youtu.be/hg9n8n5YJps
Bobcat TL25.60 AGRI Customer’s first impressions at dairy farm
https://youtu.be/JOj-c4193sk
For more information about Bobcat and Bobcat products, visit the website www.bobcat.com
DEVELON, formerly known as Doosan Construction Equipment, will be exhibiting for the first time in the UK on Stand B-EB2 & B-EB1 at the Plantworx 2023 Exhibition at the East of England Arena outside Peterborough in Cambridgeshire from 13-15 June 2023. Several of the products on display are being seen for the first time in the UK. These include the new DX63-7 6 tonne and DX85R-7 8 tonne miniexcavators in the Static section of the stand and the new DX250WMH-7 material handler in the Demonstration area.
Together with the DX62R-7, the DX63-7 is one of two new 6 tonne mini-excavators from DEVELON, completing the roll out of the next generation of machines from the company, with a new shared global styling design. Both models are powered by the D24 Stage V compliant diesel engine providing 44.3 kW (59.4 HP) of power. Despite offering an 8% increased torque of 26.5 kgm/rpm, the D24 engine still provides
a 7% decrease in engine fuel consumption.
Alongside the DX63-7, DEVELON is showing the new DX85R-7 8 tonne mini-excavator for the first time in the UK at Plantworx 2023. The DX85R-7 reduced tail swing (RTS) excavator utilises a newly improved upper structure platform offering increased durability and robustness and a different boom swing cylinder layout resulting in an increased boom swing angle of 60o. The bucket digging force of the DX85R-7 is 6.7 tonne and this is combined with a traction force of 6.6 tonne, whilst travel speeds are a mobile 2.9 km/h in the low range and 4.8 km/h in the high range.
Like all of DEVELON’s new generation mini-excavators, the DX63-7 and DX85R-7 are designed to offer maximum performance, optimum stability, increased versatility, enhanced operator comfort, controllability, durability, ease of maintenance and serviceability.
Joining the DX63-7 and DX85R-7 in the Static area of the DEVELON stand are the DX27Z-7
mini-excavator, the DX100W-7 wheeled excavator, the DL80TL-7 compact wheel loader, the DX140LCR-7 15.6 tonne crawler excavator and the DL280-7 wheel loader.
Equipped with an MG22 Sorting Grapple, the new DX250WMH-7 25 tonne Stage V compliant material handler is being demonstrated by DEVELON for the first time in the UK, for use in the solid waste, recycling, demolition and forestry industries. Designed to carry out the toughest tasks, the DX250WMH-7 is built with front and rear stabilizers, and a boom and arm specifically designed for material handling tasks.
A standard feature is the hydraulic cab riser, which gives the operator better all-around visibility of the attachment and work area. When combined with the rear view camera display in the cab, the operator has excellent visibility of the job site.
The DX250WMH-7 material handler is easy to operate with ergonomic joysticks and a steering wheel. The machine comes equipped with twoway auxiliary and rotate circuit hydraulics to improve efficiency. The operator can use buttons on the joysticks or an optional foot pedal to control auxiliary attachments.
The new DX250WMH-7 material handler is powered by the 6-cylinder, turbocharged Develon DL06V water-cooled diesel engine, providing an output (SAE J1995) of 141 kW (189 HP) at 1900 RPM.
Joining the DX250WMH-7 in the Demonstration area of the DEVELON stand is the DL80-7 compact wheel loader, the DX55R-7 5.7 tonne mini-excavator, the DL380-7 wheel loader and the DX225LC-7 23 tonne crawler excavator.
For more on DEVELON, please visit the website: https://eu.develon-ce.com/en/
Coperion K-Tron announces the expansion of the original ProRate™ PLUS feeder portfolio with more solutions for feeding powders. A ProRate PLUS-MT twin screw feeder will be added to the product line that will be available end of April 2023. Together with the recently introduced ProFlow™ bulk solids activator the new twin screw feeder is an efficient solution for feeding powder additives in plastics applications. Last year Coperion K-Tron developed a completely new feeder line built on 100 years of feeding experience to provide a robust and reliable feeder for simple feeding applications in the plastics industry. The ProRate PLUS continuous gravimetric feeder line is an economical solution and offers a quick return on investment due to its good price-performance ratio and fast delivery times. The original product line featured three single screw feeders that are ideal for the feeding of pellets, granules and other free-flowing bulk materials in secondary plastics applications.
For more difficult to handle materials Coperion K-Tron is expanding the ProRate PLUS product line with a new twin screw feeder, the PLUS-MT. This gravimetric feeder with its horizontal agitator ensures
that the two screws are always optimally filled with material. The twin screw technology also has the advantage of reducing pulsations and the screws have a self-cleaning effect. Twin screw feeders are ideal for difficult to handle powder additives such as talc, calcium carbonate or carbon black. The steep design of the hopper walls allows poorly flowing bulk solids to be fed reliably without an additional vertical agitator. Should material bridging or ratholes still occur, one or more ProFlow bulk solids activators can be mounted on the hopper to promote material flow.
The new ProRate PLUS-MT twin screw feeder can handle throughputs from 40 up to 1800 dm3/h [1.4 to 63.6 ft3/h], depending on bulk material characteristics. With individual bulk solids tests in our test centers, we can determine more precisely what the exact feeding range is for a specific bulk material.
Together with the new ProFlow™ solution, the scope of the original ProRate PLUS single screw feeders has been expanded to include moderate flowing powders and flakes. The solution is available for all four models (PLUS-S, PLUS-M, PLUS-L, PLUS-MT) and can be installed on new equipment or as a “mounting kit” on
existing feeders.
The ProFlow bulk solid activator consists of an electromagnetic vibrating device, which activates the feed hopper to keep bulk materials moving. The device operates at an optimized frequency and amplitude to ensure minimal energy consumption and maximum product flow. Thanks to its smart electronic control, ProFlow only uses 3.6 Watts of electricity. Tests with a wide range of bulk materials have shown that ProFlow is an ideal solution for a variety of bulk materials. ProFlow has no wear parts and since it is mounted outside of the product contact area, there is no additional cleaning effort needed.
For the smaller PLUS-S model, the ProFlow activator is implemented in conjunction with specially developed overflight screws. Overflight screws have wings that help move the bulk material into the throat of the feeder and positively promote improved screw fill.
The ProRate PLUS feeder line features a spacesaving trapezoidal shape which allows up to six feeders to be easily grouped around an extruder inlet within a 1.5 meter [5 ft] radius. The four feeder models PLUS-S, PLUS-M, PLUS-L and PLUS-MT cover a wide range of throughputs. The ProRate PLUS feeders are capable of handling feed rates from 3.3 up to 4800 dm3/h [0.12 up to 400 ft3/h], depending on the material. Theoretically, a feeding system with six ProRate PLUS-L feeders can feed up to 28.8 m3/h [1017 ft3/h] on a footprint of only 7 m2 [75 ft2].
ProRate feeders are highly standardized and include a variety of design features to optimize performance and ease of use. Simple access for cleaning and maintenance, even within a cluster, is provided thanks to a patent-pending rail system called “ProClean™ Rail”. ProClean Rail makes it possible to retract the base unit toward the rear of the feeder and rotate it for access to the feeding section and screw element while keeping the feeder in position. In addition, the bellows and screws use the latest magnet technology for simple but robust mounting. The magnet connections allow these parts to be released without tools while at the same time providing the required holding force for optimal and safe operation.
Thanks to the high level of standardization of the feeders, the number of spare parts required for an emergency stock is minimal. Many parts are identical for all three models and can be used as exchange parts for all devices.
All ProRate PLUS feeders are equipped with P-SFT load cells, featuring reliable Smart Force Transducer single wire weighing technology. Each feeder also comes equipped with its own pre-wired and pretested ProRate PLUS PCM control module. The PCM is mounted to the feeder stand, with adjustable height positioning. Most feeders only need a basic motor control unit (PCM-MD) while one feeder per group of eight is equipped with an advanced version
featuring an integrated user interface and line control functionality (PCM-KD).
ProRate PLUS feeders and the ProFlow bulk solids activator are suitable for use in hazardous locations rated NEC Class II, Div. 2, Group F & G and ATEX 3D/3D (outside/inside).
Preconfigured pneumatic refill solutions are available for each feeder size. Each feeder can be outfitted with either a filterless vacuum receiver for pellet applications or a vacuum receiver with a cartridge filter for applications where there may be dust that must be kept out of the air only line of the vacuum conveying system. Refill solutions include a compact support stand, level indicators, butterfly valves and electrical terminal boxes as well as one or more vacuum blowers as needed. The Series 4 MPC controller is ideal for up to 24 vacuum receivers on one blower with one back-up blower.
Coperion (www.coperion.com) is a global industry and technology leader in compounding and extrusion systems, sorting, size reduction and washing systems, feeding systems, bulk material handling and services. Coperion develops, produces, and services plants, machinery, and components for the plastics and plastics recycling industry as well as the chemical, batteries, food, pharmaceutical and minerals industries. Coperion employs 4,000 people in its three divisions, Polymer, Food, Health & Nutrition, and Aftermarket Sales & Service, and in its 40 sales and service companies worldwide. Coperion is an Operating Company of Hillenbrand (NYSE: HI), a global industrial company that provides highly-engineered, mission-critical processing equipment and solutions to customers serving a wide variety of industries around the world. www.hillenbrand.com
A new Mobile Tilt-down Flexible Screw Conveyor fits restrictive processing situations, and offers a low centre of gravity and full accessibility from standing height.
Positioning of the support boom against and parallel to the conveyor tube minimises the height needed to manoeuvre the system under doorways and mezzanines, and to fit the conveyor’s discharge between process equipment inlets and overhead obstructions. A low centre of gravity maximises stability during operation and when rolling the unit between multiple processing tasks and wash down stations.
When fully lowered, the tilt-down mechanism positions the clean-out cap of the conveyor tube higher off the plant floor, and the conveyor’s discharge closer to the floor, allowing removal and re-insertion of the flexible screw from standing height during cleaning and inspection.
The screw is the only moving part contacting material, and is driven beyond the discharge point, preventing material contact with bearings or seals. It self-centres as it rotates, providing ample clearance between itself and the tube wall to eliminate or minimise grinding, while creating a gentle rolling action that prevents segregation of the most disparate blends.
Constructed of #316 stainless steel finished to
sanitary standards, the mobile system is equipped with a low profile hopper with bag support tray; quick-release clean-out cap; quick-disconnect discharge access cover; and stainless control panel, conduit and liquid-tight compression fittings, allowing wash down and/or conveying of corrosive materials.
Ready to plug in and run, it includes HMI controls for manual or automatic start/stop and speed adjustment, and a manual hydraulic jack to raise and lower the support boom and conveyor assembly.
A broad range of screws with specialised geometries is available to handle free- and nonfree-flowing materials, including products that pack, cake or smear.
Flexicon also manufacture other configurations of mobile and stationary flexible screw conveyors, as well as tubular cable conveyors, pneumatic conveying systems, bulk bag dischargers, bulk bag conditioners, bulk bag fillers, bag dump stations, drum/box/container tippers, drum fillers, weigh batching and blending systems, and engineered plant-wide bulk handling systems with automated controls.
For information contact Flexicon Europe Ltd, +44 (0)1227 374710, sales@flexicon.co.uk, www. flexicon.co.uk
Solids handling equipment maker, Ajax Equipment, has supplied leading black masterbatch producer, Hubron International, with an inclined screw feeder to transfer difficult raw materials. Ajax has previously supplied Hubron International with a range of solids handling equipment including screw feeders, hoppers and three FIBC big bag dischargers over multiple investment projects.
The new screw feeder features Ajax’s LynFlow™ ribbon blades in Abrazo, a wear resistant steel, to ensure excellent auger service life in a demanding application. The auger’s variable pitch design ensures the poor flowing material is effectively driven up the feeder’s incline.
Commenting, Craig Hodgkinson, operations director at Hubron International said, “As usual Ajax provided us with a new unit in a professional and timely manner, having experienced great service life from the previously installed screw feeder.”
“Developing collaborative working relationships with our customers has been one the keys to Ajax’s success over the past 50 years. Working with Hubron again and again enables us to draw upon the company’s feedback as well as the valuable design insight gained from previously
conducted powder testing,” says Eddie McGee, managing director, Ajax Equipment.
For more information on Ajax Equipment screw feeders, call +44 (0)1204 386723, email sales@ ajax.co.uk and visit www.ajax.co.uk.
Posi-flate 585/586 butterfly valves feature seats and discs for application pressures up to 10 bar. The design improves on existing 485/486 seats to provide the same incredible valve life at even higher pressures. The 585/586 valves are designed to fit PN 10 flanges, and come in sizes 80mm to 600 mm.”
The Posi-flate Series 585/586 butterfly valves are designed for the most severe of applications. They are ideally suited for very abrasive materials which can reduce valve life. The inflatable seat design provides a better seal by utilizing air pressure to expand the seat against the disc, providing more sealing area and an even pressure distribution against the disc every time. The seat automatically compensates for wear when it inflates against the disc, extending valve life considerably.
Because the Posi-flate disc only makes casual contact with the seat during opening and closing, torque requirements are substantially lower. This ease of movement also allows the disc to come to a perfect 90-degree position every time. Additionally, the smooth profile of the disc helps material flow easier and reduces build-up. For unique fail-safe monitoring, a pressure switch can be utilized to verify a perfect seal.
The Posi-flate 585/586 butterfly valves are available in a wide variety of construction materials including stainless steel and lightweight aluminum.
https://www.posiflate.com/ products/585.html
Posi-flate
Milton Keynes, United Kingdom + 44 1908 622366
E-mail: sales@posiflate.co.uk
www.posiflate.com
It is with great pleasure we are able to announce that 30 years after joining the Gericke group of companies, and adding its world leading rotary valves as an integral product to the group’s portfolio of innovative powder handling solutions, UK based Rota Val Ltd. are now continuing the journey of integration by changing the name to Gericke Rotaval Ltd.
Part of a truly global network
The Gericke group of companies gives Gericke RotaVal worldwide reach in providing customers with tailored solutions and product support. As well as the ability to drive improvement in our product portfolio for all our customers by working and learning from the system solutions and expertise the Gericke group provides.
Our world leading rotary valves play an integral part in the efficiency and safety of a powder handling process. Thanks to their highly modular design, Gericke RotaVal valves can be adapted for virtually all types of product characteristics and applications, from heavy duty to highest hygienic standards. With our own development and production, we can react
quickly to new needs, and the well-known quality can be guaranteed throughout.
Gericke Knows Powder Handling
Gericke is not only a rotary valve manufacturer. Gericke is a technology leading supplier of powder processing machines and systems, used in many food, chemical, pharmaceutical and raw material industries.
The Swiss Gericke Group has been designing and manufacturing equipment and systems for modern bulk material processes, as well as providing design and consultation services, for more than 125 years. Gericke bulk materials processing technology can be found throughout the world in many sectors including the food, chemical, pharmaceutical, plastics and construction material industries.
Gericke’s fully owned group companies employ more than 300 experienced professionals and are located in Switzerland, Germany, Great Britain, The Netherlands, France, USA, Brazil, Singapore, Indonesia, Malaysia, Thailand and China.
Magnetic separators, metal detectors and x-ray foreign body detectors to identify and remove metal and other contamination prior to and after packing are the focus for Bunting at Interpack 2023 (4-10 May, Düsseldorf, Germany). On stand D66 in hall 11, Bunting will exhibit working metal separators such as high-strength rare earth Drawer Filters Magnets; conveyor-mounted high-sensitivity tunnel-type Metal Detectors; and, for the very first time, the easySCOPE foreign body detector.
Bunting is one of the world’s leading designers and manufacturers of magnetic separators and metal detectors. The Bunting European manufacturing facilities are in Redditch, just outside Birmingham, and Berkhamsted, both in the United Kingdom.
The global packaging industry converges on the biennial Interpack exhibition to see the latest industry innovations. The focus is on packaging materials, packaging machines and related process technology for the food, beverage, confectionery, bakery, pharmaceutical, cosmetics, non-food and industrial goods sectors.
Bunting is exhibiting at Interpack for the first time in 2023. For over 60 years Bunting has built a reputation as a globally-leading designer and supplier of metal separation equipment to companies processing and handling foodstuffs, chemicals, and pharmaceuticals.
Metal contaminated products damage a company’s reputation and are costly with product recalls. In the UK, the Food Standards Agency issued ten alerts regarding metal-contaminated food products that had reached the public in 2022. Metal contamination occurs in many forms, commonly occurring due to the wear and tear of
processing plant such as pumps and screens. The optimum combination of magnetic separators and metal detectors in the manufacturing and packaging process ensure that finished packed goods are metal-free.
On Bunting’s stand D66 in hall 11 at Interpack are examples of magnetic separators, metal detectors, and foreign body detectors successfully installed in processing plants around the world.
The diverse range of magnetic separators on show at Interpack includes a Bullet Magnet, Inline Magnet (PIM), Torpedo Inline Magnet (TIM), FF Drawer Filter Magnets, Grate Magnet, and Plate Magnet. All the magnetic separators are available in a range of magnetic strengths, with high-powered rare earth being the most popular. Ferrous and magnetically-susceptible metal is attracted to the surface of the magnet and then securely held until manually cleaned. The different designs suit installation at various stages in a process.
The Bunting range of metal detectors includes designs for free-fall, pneumatically-conveyed, and final packaged product checking. The pTRON metal detector identifies and removes metal contamination from products transported in pneumatic pipelines. The quickTRON 07RH metal separator detects
free and encapsulated metal in free-falling bulk materials, whilst fulfilling the most stringent hygiene requirements. For ultra-high-sensitivity detection of metal, Bunting is displaying the conveyor mounted meTRON 07 CI tunnel metal detector. This metal detector brings a new performance benchmark, with imagePHASE visualising the product for highly accurate metal detection at maximum reliability.
Bunting is exhibiting the easySCOPE 400 foreign body detector for the first time in Europe. The advanced X-ray technology detects contamination in packed goods and provides that final check to ensure maximum product quality. The easySCOPE detects a wide range of contamination including metal, glass, stone and plastic.
“The nature of manufacturing means that foodstuffs and other processing materials are at risk of being contaminated by metal and other materials,” explained Bradley Greenwood, Bunting’s European Sales Manager. “Our job is to provide equipment that identifies and removes any contamination before packed goods leave site. Interpack provides us with the ideal platform to help companies solve or prevent such a contamination problem caused by metal or any other materials.”
For further information, please contact us on press@buntingmagnetics.com or visit our website: Bunting-Redditch – www.bunting-redditch.com