
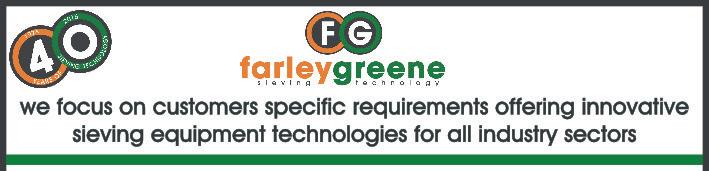

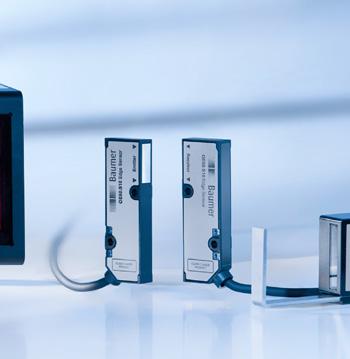


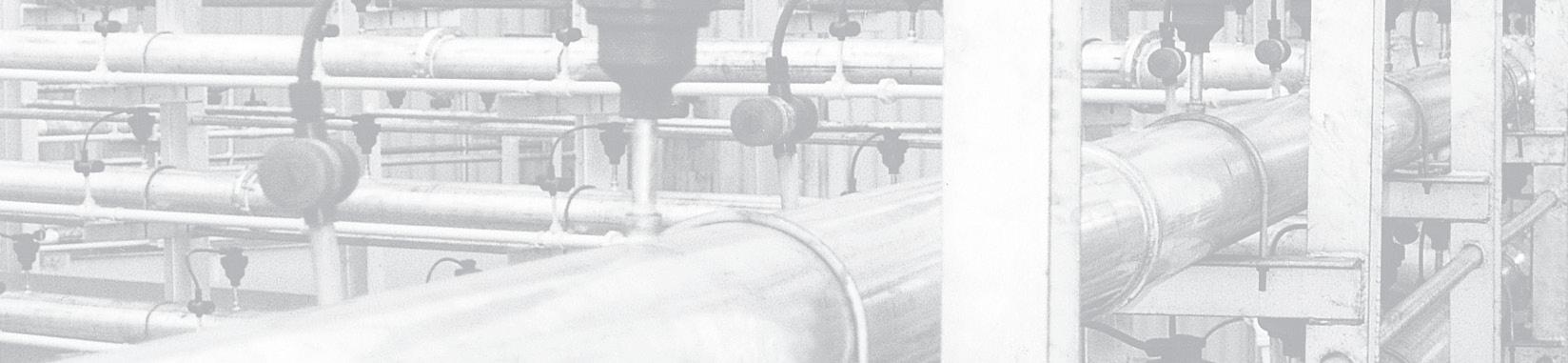
We are a leading provider of custom solutions for the handling of bulk materials for processing businesses across various industries. Dynamic Air has over five decades of expertise in designing and manufacturing pneumatic conveying systems and equipment for handling dry bulk solids.
At Dynamic Air, we set the standard for excellence in bulk solids handling. With a relentless focus on quality, reliability, and customer satisfaction, we deliver reliable, high-quality pneumatic conveying systems, equipment, and custom solutions that exceed expectations. BULKBUSTERTM
We never take a cookie-cutter approach just to cut costs up front; we know that the right solution will save you money in the many years to come. Our tailored solutions involve thoughtful planning, meticulous engineering and precise manufacturing that optimize efficiency and productivity.
Sales Director: James Scrivens
Production: Sarah Daviner
Accounts Manager: Avery Hudson
Office Manager: Katie Brehm
BULK SOLIDS TODAY is published 6 times a year by Abbey Publishing Ltd
ADVERTISING & EDITORIAL
Please contact us at:
Tel: 01933 316931
Email: editorial@bulksolidstoday.co.uk advertising@bulksolidstoday. co.uk
Web: www.bulksolidstoday.co.uk
Twitter: www.twitter.com/ BulkSolidsToday
CIRCULATION
To receive a copy free of charge, please send your details to subs@bulksolidstoday.co.uk
No part of this publication may be reproduced by any means without prior permission from the publishers. The publishers do not accept any responsibility for, or necessarily agree with, any views expressed in articles, letters or supplied advertisements.
ISSN: 1365/7119
The “TalkingTons” vodcast will see CDE experts sharing industry insights and knowledge
CDE, a leading provider of wet processing solutions for the natural and waste recycling sectors, has launched a vodcast series designed to share insights on latest industry trends.
Today, Tuesday 4th March, sees the release of the first “TalkingTons” vodcast episode, part of a series which will shine a light on topics such as waste recycling, industrial sands and water management.
Hosted by CDE’s senior marketing manager Lauren McMaster, there will be new episodes every month which will feature CDE’s experts from across its five strategic regions talking about industry issues and opportunities.
Lauren McMaster commented: “At CDE, we share
a common purpose to create our best world a ton at a time. We have over 30 years of experience, and unmatched expertise in the industry and with that we are passionate about not only delivering pioneering technology but sharing our expertise to support the creation of a circular economy.
“We certainly do have tons to talk about, and the launch of the vodcast today signifies our dedication to equipping our team, customers, and the wider industry with the knowledge to drive meaningful change across the sectors we operate in.”
The first episode sees Lauren joined by three of CDE’s regional experts, Eunan Kelly who oversees Europe, Regis
Marty who focuses on the French, Belgian and Swiss markets, and Garry Stewart who manages Ireland.
In the episode, the team discusses quarry waste, and how the industry has evolved in its view of overburden, scalpings and crushed rock fines and that quarry operators are now seeking to process this material to reduce the volume of quarry byproduct that is being stockpiled.
The conversation also explores the opportunities that the industry has to extend the life of a quarry, and the environmental benefits of processing this material in moving products up the value chain and reducing carbon emissions.
To register to listen to the TalkingTons vodcast please visit CDEGroup.com/talkingtons
Sensor experts BAUMER continue to expand their extensive ‘Toolbox’ range of high-performing sensors following the introduction of new edge sensors, the OE60 and OE40.
The combination of these new sensors with their established smart 2D OX series of profile sensors provides users with ultra-reliable and flexible edge measurement options to suit different precision levels and available space conditions across a wide range of applications.
Key features and benefits include; Edge detection with up to 1µm precision with repeat accuracy at a distance of up to 100mm, flexible design to suit different functional principles, compact and easy to integrate along with connectivity options including IO-Link, EtherCAT and Modbus RTU.
The portfolio includes the high-performance OE60 and OE60C providing bestin-class precision up to 1µm across a measuring range up to 10mm, the OE40 which delivers measuring precision up to 24mm, detection of transparent edges along
with plug-and-play ability thanks to a reflection bracket. Completing the edge sensing ‘portfolio’ are the OXS smart profile sensors for measurement of multiple edges and step heights, providing resolution up to 30µm in X-direction and up to 5µm in Z-direction.
The high-precision OE60 sensors are claimed to be the only ones in their class that can be deployed as stand-alone devices without the need for a controller unit, because the sensor heads are designed to directly integrate into the control via the standardized Modbus RTU protocol. This eliminates the need for an additional device and therefore reduces overall costs.
Examples of applications where these sensors will be especially beneficial include battery cell production, where edge measurements must be extremely precise as the individual layer positioning (anode, cathode and separator foil) in the winding process defines service life, capacity and even battery safety.
Reliable detection of the individual tracks, even at high speeds, is crucial in battery
production and the OE60 succeeds thanks to the very short response time combined with outstanding precision of 1µm which is achieved without the need for any filtering. Another potential application is web edge control in the packaging industry where edge detection of transparent films with optical sensors is a major challenge. The OE40 plays to its strengths with its reflector bracket reliably and precisely measuring edge positions on thin transparent films where optical sensors would reach their limits.
Finally, in the wood processing industry the smart 2D profile sensor can check floor planks to identify any non-compliance of tongue and groove. By measuring the edge position the sensor identifies depth or width of tongue and groove with the measured results delivered straight to the system so that issues such as tool wear can be detected early by any change in the height profile.
Discover more about BAUMER’s smart toolbox at: https://www.baumer.com/ gb/en/product-overview/
Bunting has developed a new Electromagnetic Dry Filter to remove free fine iron from powders. The high-intensity magnetic separator generates ultra-strong magnetic fields to capture ferrous particles present in difficult-to-process fine materials. The new technology enhances magnetic separation in a diverse range of applications found in mineral
processing, chemical and pharmaceutical production, ceramics, and recycling.
The Electromagnetic Dry Filter features a centrallylocated vibrating canister inside a specially designed electromagnetic coil. The coil generates between 3,500 and 5,000 gauss in the canister, which is then concentrated on the points of the matrix to reach
peaks of up to 12,000 gauss. In operation, fine powder flows under gravity through the vibrating canister which is packed with magnetic stainlesssteel matrix. Magnetic particles are attracted to the magnetically induced matrix and held until the batch feed is stopped. The electromagnet is then turned off, releasing the magnetic particles into a
separate waste collection area, before processing is resumed.
The ultra-high magnetic fields and multiple magnetic capture points on the matrix enable enhanced separation of magnetically susceptible particles. The separation efficiency is far higher than permanent magnetic separators utilising permanent neodymium rare earth tube magnets. Many rare earth magnetic separators experience difficulties with bridging, ratholing and poor flowability due to particle size and shape, electrostatic charges, and environmental factors such as humidity.
The Electromagnetic Dry Filter is particularly suited for the magnetic particle purification of high-value fine powders, especially when processed and produced in controlled batches.
The process times and integration of the Electromagnetic Dry Filter into a production line is conducted through a separate control featuring a Siemens S7-1200 PLC and Human Machine Interface (HMI) control. To simplify maintenance and reduce production downtime, the Electromagnetic Dry Filter is fitted with a built-in jig crane to remove the centrally located matrix canister for inspection or cleaning.
“The development of the Electromagnetic Dry Filter has been customer driven,” explained Adrian Coleman, Bunting’s Technical Director. “Processing powders is often challenging due to the way in which the materials behave. Our design engineers considered these
challenges when designing the Electromagnetic Dry Filter, focusing on good powder flow, whilst maximising magnetic separation.”
Bunting is one of the world’s leading designers and manufacturers of magnetic separators, eddy current separators, metal detectors and electrostatic separators, with globally located manufacturing facilities.
For further information, please contact us on press@buntingmagnetics.com or visit our website: www.bunting-redditch.com
valves that
with friction, Posi-flate’s
butterfly valve uses an inflatable seat to seal with air pressure. Thus it requires less torque and a smaller actuator, resulting in lower cost. Plus, the seat automatically compensates for wear, providing longer life. Some users have reported over six million cycles and the valves are still going strong.
• Less friction
• Low torque
• Low maintenance
• Lower actuator costs
• Longer valve life
• More reliable
A new deep water bulk berth has been opened at the Port of Liverpool which will give a major boost to the port’s cargo handling operations.
The first deep water bulk berth to be opened at the port in 40 years is located at Peel Ports Group’s Alexandra Complex, and represents an investment of £2 million by Peel Ports as part of its ongoing development of the Alexandra Complex.
The berth welcomed its inaugural vessel on Friday – the Andesborg – and will accommodate vessels up to handymax sizes.
Combined with the existing N3 Alex berth, the new addition will increase the vessel handling capacity of both the Alexandra Complex and the Port of Liverpool as a whole.
The 534,000 sq. ft. complex, where a £28 million state-of-the-art warehouse was also recently developed, is designed to provide a
full, efficient solution for customers’ bulk storage and handling requirements.
Phill Hall, Mersey Port Director, Peel Ports Group, said: “This is a significant moment for the Port of Liverpool. The addition of the new deep water bulk berth will not only allow us to accommodate larger vessels, it will also improve the port’s overall ability to manage bulk cargo, providing more efficient cargo operations and helping us to keep supply chains moving.
“Not only does this project show our dedication to investing in infrastructure, when combined with our modern storage facilities the new berth ensures we can handle a diverse range of commodities and support customers with their needs.”
Warehousing space is currently available at the Alexandra Dock Complex and interested parties should contact Peel Ports for more information.
If you would like to subscribe to receive a regular copy of the digital edition of Bulk Solids Today magazine, you can subscribe on our website - www.bulksolidstoday.co.uk
If you are interested in advertising within Bulk Solids Today magazine or supplying editorial content, please feel free to get in touch using the details on our website or below.
Bulk Solids Today is sent to our digital readership of over 9,000 Chief Engineers, Operations Managers and Technical Managers from within sectors including Chemicals, Food & Drink, Mining, Quarrying, Transport/Distribution, Recycling & Waste Management and more.
www.bulksolidstoday.co.uk
Permanent lubrication system reduces maintenance costs
A large beverage producer in Mexico invested in an automated system for packing and unpacking bottles from crates. They ordered their system from KHS, one of the world’s leading manufacturers of filling and packaging systems. In contrast to the more usual case, reusable cartons, which are much more stable, are used to transport the bottles instead of plastic crates. To enable the automated packers and unpackers to remove and insert the bottles gently and precisely, the Dortmund-based system supplier faced the challenge of finding a guide system that could travel very small radii (R=100) and right/left curves without play due to the limited installation space.
KHS therefore co-operated with PGM Motion and used their W-Line guideways. They integrated the rail systems with specially developed guide carriages as part of the prototype construction, which enable their systems to negotiate tight curves without any play.
PGM Motion has developed special drive chains to drive the carriages.
“Most people in the world of beverage bottling in this country think of robust plastic crates that transport bottles safely from A to B,” says Joachim Öchsner, Managing Director at PGM Motion GmbH. But the reality is not the same everywhere: for example, reusable bottles were transported in cartons at a well-known drinks manufacturer in Mexico. These containers are less stable, which can cause difficulties during tightly synchronised transport automation. And that was also the case with the system that was to run on site at the bottler: “Cardboard boxes are much more unstable than plastic crates and so are already quite worn by the time they reach our production process. The difficulty now was to ‘divide’ these cartons in a way that was gentle on
the product so that our packing system could insert or remove the bottles,” reports Stefan Habermann, Head of Design – Product Centre Palletizing Technology at KHS. “It is essential for the individual cartons to be positioned correctly on the pack conveyor so that the containers do not break and the conveyor belts rarely need readjustment.”
Carriages using traditional roller guideways have to be individually adjusted to the rails using eccentric bolts, and they are not able to travel on small radii with right and left curves without play or load resistance. The transitions at the joints of the guide rails also often have to be reground with an
oil stone, which is very time-consuming. These systems were therefore not feasible in this application.
KHS turned to the drive specialists at PGM Motion to ensure nothing was left to chance.
Following intensive dialogue, PGM developed a solution specially designed for this application, based on a new design for the guide carriages and rail elements.
Special trolley enables play-free transport
“The crucial advantage of this solution lies in the introduction of a spring package that permanently presses the carriages onto the rail using pre-tension,” explains Öchsner. In contrast to conventional systems, where the play increases over time and the carriages start to wobble, the movement of the PGM solution remains stable in the long term. The guide carriage rollers are in permanent contact with the rail, both in straight sections and in changing curve radii. There is no need to set eccentric bolts, the carriages are immediately ready for operation and can be replaced.
The cartons must be positioned precisely so that the packer and unpacker can lift and lower the bottles. The drive chain was therefore also adapted. A spring system enables the chain to elongate in the spring links, yet it remains robust enough not to be damaged by glass or shards.
A keyway is integrated at the ends of the guide rails to ensure precise transitions between the rail elements, eliminating the need for manual reworking. Individual rail segments can be replaced as required.
Permanent lubrication system replaces tedious manual maintenance
A permanent lubrication system is designed to prevent the carriages from wearing out over time. It ensures that grease is continuously delivered to the carriages. “The limited installation space made it impossible for the operator to reach all the necessary lubrication points. The PGM system takes over this task, making a reliable contribution to longevity and customer satisfaction,” explains Habermann.
Overall, PGM Motion’s solution not only successfully overcame the specific challenges of
the project, but demonstrated that other system series can also be easily customised. The high manufacturing precision of the guide rails and the integrated keyway enable quick and easy installation, as the rail elements fit together precisely. Since being commissioned in October 2022, the system has been running smoothly at the user in Mexico and no major challenges or failures have been reported. “We received excellent support at all times during this prototype development. We always felt that we were not just another customer, but that PGM Motion was just as invested in our success as we were,” summarises Habermann.
Further information is available online at www. pgmmotion.com
Parker Hannifin, a global leader in motion and control technologies, announces its involvement in the Integrated Hydrogen-Argon Power Cycle (iHAPC) project, a collaborative research initiative to advance cleaner and more energyefficient engine technologies.
Led by the University of Vaasa and supported by Wärtsilä under the WISE (Wide and Intelligent Sustainable Energy) program, the project will develop and test a prototype engine that uses hydrogen and argon to achieve a significant efficiency boost.
The initiative unites Finnish research institutions, technical experts, and industry partners, including Wärtsilä Finland Oy, VTT Technical Research Centre of Finland, University of Oulu, Vahterus Oy, Vaisala Oyj, and TotalEnergies.
Parker Hannifin Manufacturing Finland Oy, located in Urjala, plays a key role by designing an advanced filtration system to ensure the closed-loop reuse of argon.
Argon, a key component of the hydrogenargon power cycle, is recaptured after combustion, and Parker’s system removes residual water and other contaminants, ensuring clean argon for reuse.
“At Parker, we’re proud to contribute our engineering expertise to innovations that drive cleaner and more sustainable technologies,” says Mikko Merikoski, Senior Technology Engineer at Parker’s Manufacturing Facility in Finland. “The hydrogen-argon power cycle represents a major step forward in improving the efficiency of hydrogen power generation.”
Hydrogen-Argon Power Cycle: A step towards efficiency
The iHAPC project which kicks off in January 2025 replaces conventional air intake with a mix of argon and oxygen during combustion. Argon’s superior heat capacity ratio enables the engine to produce the same power output with significantly less fuel, potentially increasing combustion engine efficiency up to 20%.
In this closed-loop process, hydrogen, oxygen, and argon are the inputs, producing only water and recycled argon as byproducts. Most water is removed via a condenser built by Vahterus Oy,
while Parker’s filtration technology eliminates any remaining moisture and impurities.
Balancing engines are critical for stabilizing power supply alongside intermittent renewable sources like wind and solar. Today’s most efficient engines run on gas but are ready to transition to sustainable fuels such as hydrogen. By 2030, sustainable fuel production is expected to reach 38 million tonnes—exceeding current demand by one-third and accelerating the shift towards renewable energy systems.
Rasmus Teir, Director of Sustainability & Future Plant Concepts at Wärtsilä Energy, commented: “We have the technologies required to achieve a 100% renewable energy future. Our goal is to continually innovate solutions that improve both affordability and sustainability. The argon power cycle is a significant technological breakthrough with the potential to positively impact these goals.”
Professor Maciej Mikulski from the University of Vaasa, the project leader, said: “The argon power cycle allows for the complete valorization of green hydrogen with exceptional power generation efficiency. This could represent a major breakthrough for the energy sector. The University of Vaasa is dedicated to advancing innovative energy solutions with a strong focus on sustainability. Our expertise in fuel analytics, modeling and simulation, powertrain testing, and control development equips us well to lead this project.”
For more information about Parker’s hydrogen industry technologies and sustainability initiatives, please visit: https://www.parker.com/fi/en/ solutions/hydrogen.html
If you would like to subscribe to receive a regular copy of the digital edition of Bulk Solids Today magazine, you can subscribe on our websitewww.bulksolidstoday.co.uk
If you are interested in advertising within Bulk Solids Today magazine or supplying editorial content, please feel free to get in touch using the details on our website or below.
Bulk Solids Today is sent to our digital readership of over 9,000 Chief Engineers, Operations Managers and Technical Managers from within sectors including Chemicals, Food & Drink, Mining, Quarrying, Transport/ Distribution, Recycling & Waste Management and more.
www.bulksolidstoday.co.uk bst@abbeypublishing.co.uk
Tuf-Lok ring grip pipe and tube couplings are rugged, heavy duty, self-aligning and self-grounded couplings with a high end pull. They can be used for almost any application where pipe or tube ends need to be connected. The Tuf-Lok self-aligning couplings install quickly and easily with little effort.
Features
• Self-aligning
• Self-grounding
• High pressure rated
• Full vacuum rated
• Stainless or mild steel
• Usable on thin or thick wall pipe or tube
• Low cost
• Reusable
• Absorbs vibration
• Externally leakproof
Danfoss Power Solutions will exhibit products and solutions that pave the way to more sustainable construction at bauma 2025, April 7-13, in Munich, Germany. At its booth — Hall A3, Stand 125 — Danfoss will highlight its capabilities in hydraulics, eHydraulics, electrification, digitalization, autonomy, and software, emphasizing the company’s innovation and application know-how.
The Danfoss booth will feature more than 60 of the company’s products, organized by the subsystems common to construction and mining machinery: propel, steering, work function, and controls. Additional stations will be dedicated to electrification and eHydraulics as well as Danfoss’ PLUS+1® Platform. The company will demonstrate how its scalable, modular solutions can be tailored to specific customer requirements and seamlessly integrated into a wide range of applications and machine sizes.
Danfoss will launch several new products during
the event, including the X1P family of open-circuit piston pumps built on the all-new X1 platform, additions to the Thorx™ line of cam lobe motors, and a thermoplastic hose for material handling applications. In addition, key solutions and recently launched products will be showcased throughout the booth, including the Digital Displacement pump and controller, the Editron ED3 onboard charger and ePTO, electrohydraulic steering subsystem solutions, and an industrial cam lobe motor for large stationary machinery.
eHydraulics, or electrified hydraulics, and electrification will be particular focus areas. Ondřej Aulich, a subsystem engineer with the company’s Controls division, will present during the bauma Forum on the impact of electrification on work hydraulics. His lecture — Monday, April 7, at 10 am in Hall B0 — will cover the technological advancements required to improve efficiency while maintaining high functionality and reliability in electrified mobile machines. Markus Plassmann,
Head of Growth and Sales Operations with the Editron division, will join Carraro’s Enrico Tracanzan, Group R&D Director, for a presentation on the companies’ two-speed driveline solution. Their lecture — Wednesday, April 9, at 3:30 pm in Hall B0 — will detail how the solution enables OEMs to switch between hydrostatic and electric propel systems without chassis modifications, streamlining vehicle design. The electric propel system will be on display in the Danfoss booth, along with the Danfoss eHydraulic Power Module, highlighting the advantages of packaged solutions.
“The theme of our booth is ‘Set your vision in motion. From idea to reality.’ This reflects our aspiration to help our customers solve their
greatest machine challenges and achieve their vision,” said Steen Rohleder, Vice President, EMEA Sales, Danfoss Power Solutions. “Danfoss has the technologies and the know-how to transform construction machinery. Our solutions improve productivity and precision, enhance safety, increase efficiency, and reduce or eliminate emissions, paving the way to more sustainable construction. We look forward to sharing these solutions with visitors at our booth.”
For more information on Danfoss solutions for construction and mining, visit the company at bauma in Hall A3, Stand 125, or online at Danfoss.com/bauma25. To
The company starts using SSAB Zero™, made of recycled steel and produced with fossil-free electricity and biogas, resulting in steels with significantly lower fossil carbon emissions
Toyota Material Handling Europe and SSAB enter a fossil-free partnership, and the cooperation makes the company the first material handling equipment manufacturer using SSAB Zero™. The company secured the delivery of SSAB Zero™steels, which it will use to produce the forks and frames for hand pallet trucks this spring. The quality and properties of SSAB Zero™ steel are the same as those of SSAB´s conventional steel.
“We aim to be a leader in the sustainable transformation of our value chain and are building a resilient supply chain together with our suppliers,” says Giorgio Polonio, VP Purchasing, Supply at Toyota Material Handling Europe.
“We are happy to work with Toyota in producing the next generation of material handling equipment with a lower carbon footprint. Toyota Material Handling Europe has been our customer via our subsidiary, Tibnor, for over 20 years, and we are ramping up our collaboration based on our mutual trust and common goal of a fossil-free future,” says Tony Harris, Head of SSAB Europe.
In early 2024, SBTi validated Toyota Material Handling Europe’s near- and long-term sciencebased targets, aimed at reaching net-zero by no later than at the end of 2041. The Science Based Targets initiative (SBTi) provides a clearly defined pathway for companies to reduce greenhouse gas emissions to prevent the worst effects of climate change, and supports ambitions to limit global warming to 1.5°C.
As part of its net zero efforts, the company will be ramping up our use of recycled steel produced with fossil-free electricity and biogas, which will reduce the carbon footprint of raw materials used
in our trucks. Toyota Material Handling Europe aims at making low-carbon steel the standard for their products, starting with the most popular models of our hand pallet truck range.
Cooperation with SSAB ensures Toyota Material Handling Europe can reduce the carbon footprint of the raw materials used in their products. Toyota Material Handling Europe is the first in the industry to include low carbon recycled steel as standard in a product family, starting with the most popular models of hand pallet trucks.
The material in the forks and frame of the highvolume product LHM230 are to be replaced by SSAB Zero™ which has a77% reduction of CO2 compared to iron-ore based steel, considering the entire value chain. This initiative is an important step to reduce material emissions and contributes towards Toyota Material Handling Europe’s net zero targets by fiscal year 2041.
For more information, please visit: https://tinyurl.com/teezu2aj
The mixing of powders is a central process in the chemical, pharmaceutical and food industries. Short mixing time, excellent homogeneity and gentle product handling are of crucial importance. The precise dosing of ingredients in minimal concentrations in particular requires automated solutions and the careful selection of the right mixer
Individual recipes and allergens pose special requirements in order to prevent crosscontamination, guarantee product purity and ensure compliance with labelling regulations.
The mixer should therefore process even the smallest quantities of ingredients in the per mille range homogeneously and gently within a short time and minimise downtime for cleaning when recipe changes are required.
In the Gericke GMS Multiflux® mixer, 2 counter-rotating mixing rotors form a fluidised bed. The particles circulate freely in the fluidised bed without the application of force. This explains the short mixing time and the gentle mixing of particles. An increase in bulk density is therefore minimised.
In most cases, cleaning is carried out dry. With the GMS ECD, the entire drive unit and mixing
shafts can be easily removed from the housing. This means that the entire interior is extremely well accessible and can be cleaned within a short time.
Another approach to simplify the cleaning process is Gericke’s AirCIP system. Automated cleaning with air nozzles. Air pulses first remove product residues from the housing. A targeted air flow then transports the powder out of the mixer via the outlet flaps. The system also cleans the paddles and the inner walls of the mixer so that virtually no residue remains. The AirCIP system can be customised for different products and applications and does not affect the homogeneity or quality of the mix.
The AirCIP system offers several advantages: It reduces product loss, prevents cross-contamination and eliminates the need for manual cleaning between product changeovers. This significantly reduces labour costs in the cleaning process.
The system is compatible with Gericke’s horizontal shaft mixers, such as the GMS Multiflux® and the GBM Gericke batch mixer, and can also be retrofitted to existing mixers.
The Blendcon® air blender by Dynamic Air is a fast, efficient blender for mixing batches from 5 cubic feet to over 4000 cubic feet of dry bulk materials. The blender is unique in that it lacks moving parts required to displace the material in the mixing process. Instead of shafts, paddles, or agitators, compressed air is pulsed into the material in an upward circular pattern to lift, turn, and tumble dry materials. This makes the Blendcon air blender especially effective for abrasive blends such as glass batch, tile grout, and concrete mixes. Since the process area is a conebottomed vessel, the Blendcon air blender empties nearly 100%, making cleanup easy. Plus, the Blendcon air blender’s blending method is so effective, the ratio of horsepower to blended material is very low, resulting in high energy efficiency.
https://www.dynamicair.com/product/blendcon-airblender/
The Series 486 inflatable seated butterfly valve from Posi-flate is suitable for many applications, such as food, chemical and pharmaceutical. The stainless steel valve features a fully machined 316L stainless steel housing and a single piece disc and shaft that is available in a number of materials including 316L stainless steel and Hastelloy. The disc may be polished to a mirror finish or coated with PTFE, nylon or other high-performance coating. The Posi-flate Series 486 butterfly valve is ideal for powders, granules, slurries and liquids and is available in sizes 2” (50mm) to 20” (500mm). Typical applications include loading and unloading of process material, sterile air control, and outlet valves for storage containers or hoppers.
The inflatable seat design of the Posi-flate butterfly valve provides a better seal by utilizing air pressure to expand the seat against the disc, providing more sealing area and an even pressure distribution against the disc every time. The seat automatically compensates for wear when it inflates against the disc, extending valve life considerably. Because the Posi-flate disc only makes casual contact with the seat during opening and closing, torque requirements are substantially lower. This ease of movement also allows the disc to come to a perfect 90-degree position every time. Additionally, the smooth profile of the disc helps material flow easier and reduces build-up. For unique fail-safe monitoring, a pressure switch can be utilized to verify a perfect seal.
Posi-flate
Milton Keynes, United Kingdom +44-1908-622366
E-mail: sales@posiflate.co.uk https://www.posiflate.com
Bedfordshire-based ECL Civil Engineering Ltd. has completed a deal for 20 new Kobelco excavators. This latest deal builds upon over five years of successful collaboration between ECL and Molson Group, the UK distributor for Kobelco Construction Machinery. ECL has consistently chosen Kobelco excavators throughout this partnership for their advanced technology, exceptional fuel efficiency, and proven reliability.
ECL Managing Director Sean Hoare commented on the expansion: “Our ongoing investment in Kobelco excavators reflects our positive experience of running these machines, along with a very high standard standard specification on the Kobelco product aligns perfectly with our sustainability goals, our
commitment to delivering highquality services and our drive to invest in the best products for our teams on site.”
Molson Sales Director Stuart Butler added: “This deal reflects the strong relationship we have built over the last five years with Sean and his team. Over this time, we have built trust by delivering on our promises. Whether that is around the lived experience of the actual running costs of the machines or delivering a reliable and reactive after-sales support, through to understanding their business and having the flexibility to structure a deal that works for them.”
The new excavators added to the ECL fleet join a range of machines from the Japanese manufacturer’s portfolio. The new excavators are aimed at the core
of the ECL fleet and comprise of SK85MSR-7, SK130LC-11 and SK210LC-11E models fitted with a selection of Geith and Strickland quick hitches. Supplied in the traditional blue Kobelco paint scheme, the machines will be working on sites for some of the UK’s largest developers, housebuilders and local authorities, who make up much of the repeat customer base.
Hoare commented, “We need to ensure we can deliver our clients an industry-leading service that can be relied on to produce not only a quality finish at the right price but also one that meets our and their demands for lowering environmental impact. The purchase of these new excavators is a step forward in offering both that reliability, quality, and fuel savings we demand.”
- “I usually move the fork or shovel on the machine myself,” says Sister Terezka, who operates the equipment during the construction of the convent in Draste -
In Draste in the Czech Republic, the transformation of a former farm into a convent is becoming a dream come true - the nuns of the Barefoot Carmelite Sisters and many supporters have done a tremendous amount of work on the project. And this year, the consecration ceremony of the new convent church of St Teresa of Avila could even take place.
The campus, which the sisters chose to replace their previous headquarters in a building on Hradčanské náměstí in Prague in 2018, has changed beyond recognition. In addition to the work of individuals, construction machinery has also played a role in this. Out of necessity, the nuns at the convent began to operate machines such as a legendary Bobcat 773 skid-steer loader, which has now been joined by a new state-of-the-art Bobcat L85 compact wheel loader.
We talked to Sister Terezka (Markéta Paterová) at the convent about how the nuns learned to use construction machines and other topics related to the construction of the new convent.
During the renovation works, you learned to drive a number of construction machines. Which type was easiest for you and what do you appreciate about the
machines as a user and what are the important aspects for you?
Easiest, it’s hard to say, each of the machines I’ve used had advantages and disadvantages. It was nice working with the Bobcat L85 compact wheel loader. It is a powerful machine and has a modern design - the L85 worked reliably and was a good choice for the job we wanted it to do - stacking pallets of paving from trucks.
User-wise, I like the reversing camera on the machines when it’s well positioned in the field of view. And then good access to the fuel tank is also important to me. We buy diesel in cans, and not all machines are easy to fill from a can, so then I gratefully use willing and strong helpers. In the past, you have worked with a Bobcat skid-steer loader and now the larger L85 compact wheel loader. What are your observations and comparisons between the two machines, which one did you find was better?
They are very different machines, each with a different purpose. A skid-steer loader has the big advantage of being small, so it can work in places where there is not much space, it can get into harder to reach places, narrow passages and it can even turn on the spot. It’s also short, so I can, for example, handle pallets in places where there’s not much room behind me.
There’s a flip side to this coin: by being skidsteerable, it does a lot of rutting on unpaved surfaces, so even a slight turn leaves ruts. Gradually, once we had some parts of the property (the park and the garden) finished, this proved to be a problem and I couldn’t operate it there anymore.
In the course of the renovation of the whole area, we did a lot of landscaping, levelling the land or delivering gravel on our own. This would have been unthinkable without the skid-steer loader. It was a great help for transporting dirt, sand, gravel, also stone, sorting rubble or even handling in the garden, we also used it for transporting wood and tools.
We needed a bigger wheel loader when the load capacity of the small skid-steer was no longer sufficient. In our case it was mainly for paving. The L85 machine we had rented was an excellent powerful machine for which the pallet of paving was no problem at all, both when stacking the truck and when handling it in the area, even on uneven ground and lifting it up. I also appreciated the wider wheels and articulated turning, which again made it no problem to drive over flattened ground, established grass if necessary and not do too much damage.
What made you decide to get a compact wheel loader? Is it worth it? Will you take care of the machine or is it provided by the dealer?
We bought the new wheel loader thanks to our benefactors, just for the paving. We have to pave the whole area, which is a very large area. Already the loader has certainly put down more than 70 truck loads of paving and other materials, and we still have to handle all of it within the site during the construction work and the paving of the yard.
With this amount, I cannot imagine how we would have managed this organisationally if we had to get an external person with a loader for every truck arrival. The fact that the machine is here and available at any time is a huge advantage. That’s where the loader definitely pays off for us.
We bought the machine new, so it’s still under warranty. We can handle basic routine maintenance with our technician and the dealer is handling the service for now. We bought it with the idea that one day when we don’t need it here, we can resell it again and get some of our money back. But that’s not on the agenda yet. There’s still plenty of work to do here for a few years.
Construction machines are often referred to as attachment carriers. This is because their basic function depends on the attachments. Whether it is pallet forks, a bucket or a hammer, it is the attachment that gives them their specific capability. What attachments have you had the opportunity to try out and do you manage to switch between them yourself?
I have worked with several, including pallet forks and buckets. I usually switch them myself. I’m sure it depends on the machine here, too. If it has a quick release, it’s a matter of moments, you don’t even
have to get off the machine. With a skid-steer loader, where the attachments are secured by hand with levers, it was sometimes, shall we say, more physically challenging - the levers are not always easy to manipulate, but I’ve learned to be independent about it.
I also briefly used a clamshell bucket - it took longer there as the hydraulics have to be connected and disconnected as well. We didn’t make much use of the flapper function here, so after trying it we stuck with just a regular bucket, which is much easier to just switch with.
Work with construction machines is usually done by men, less by women and even less by nuns. Operating the ‘Bobcat’ and other loaders yourself was a choice of necessity, or were you drawn in that direction and discovered a hidden talent?
I have to say that I never thought I would ever work with construction machinery like this. It was more of a challenge the first time when it was a borrowed machine, but the person who was supposed to drive it got sick. And following encouragement from a friend of mine that it’s easy, let me learn with it, I can do it. And I soon found out he was right, it just takes a little practice. And the more practice the better.
There are more than enough opportunities here. Of course, it probably also has to be a person who has a positive attitude towards operating machines and who isn’t afraid of it. It’s a job that I enjoy and that makes me happy and that has helped us a lot. We do what we can here on our own, and the machines have already saved us a lot of money.
Finally, I will ask you how you manage the demanding work and if you have anyone helping you?
I would like to add that it is not only about the machines, but also about the people who move around them. That is also a very important part. Some of the machines we have here or have had on loan from our supporters. Without them, it couldn’t work the way it does here now. With a bought machine, on the other hand, it helps a lot to have good service, a helpful person who understands their job and is able to give basic advice even over the phone. And for me here, as I am changing between different machines and learning how to use them, our technician, a close associate, is also very important, showing me around, guiding me so that the work with the machines is safe and efficient.
If you would like to contribute to this good cause, please visit: https://donio.cz/ dlazbaprodrasty
For more information about Bobcat products, attachments and services, visit www.bobcat.com
Let us introduce you to the smallest product in the British Rema Process Equipment Range; the Aerosplit 100 Classifier.
This compact forced vortex air classifier is designed for use in the ceramic, chemical, metal powders and pharmaceutical sectors when low volume powder production is required. It is particularly suitable for Research & Development departments when trialling and researching new products or new powder mixes. An all-in-one solution with feeder, classifier, collector and integrated control panel it is encased in a mobile, castor mounted cabinet providing a nimble solution in tight spaces.
With all contact parts manufactured from stainless steel, the plug and play system simply connects to power, LEV & compressed air sources. The system is up and running quickly and efficiently for the costeffective separation of smaller material volumes.
One small unit, multiple benefits:
• Very sharp cuts up to 1 micron
• Feed rate of 1 to 75 kgs/hr
• Control of mean particle size within 0.5 microns
• Precise on-stream control of cut-point by variation of rotor speed
• Adjustable secondary air system for optimisation of classification efficiency
• Optional screw or vibrating tray feeders
• Feed and product bin capacities to suit customer requirements
• Inbuilt control system allows ‘on the fly’ changes to process parameters via the touchscreen HMI control panel
• ‘Recipe save’ function enables machine parameters to be stored for replication of specific PSDs ensuring efficiency and ease of operation
OPTIMUM VERSATILITY
The Minisplit can be supplied with interchangeable components for easy conversion to a Fluid Bed Jet Mill for the particle size reduction of a wide variety of materials. The simple conversion requires the substitution of the classifier coarse discharge cyclone with the Fluid bed jet mill chamber.
The Bella dryer/cooler offers thermal efficiencies to 80 percent or better because air flows around material while it is suspended in the weightless zone. The result is a more consistent material.
The global leader in belt conveyor accessories and bulk flow technology is expanding its operations in Australia to offer solutions to more customers nationwide.
Martin Engineering first entered the Australian market in 1978 and has since grown to become the country’s top bulk-handling service and solutions provider, improving production, safety, and efficiency for the mining, quarry, cement, and port sectors. By building a new manufacturing facility in Yatala on the East Coast and opening a fully staffed office in Perth on the West Coast, Martin is investing in and adding jobs to the Australian economy. Using a “factory direct” sales, service, and equipment model, customers receive reliable product fulfillment, faster response times, and hands-on service from local experts.
Martin Engineering Australia in Yatala.
“Our purpose-built space has been designed to enhance our customer service, operational capabilities, and provide a better working environment for our team,” said Bo Hu, Australia Manager, Martin Engineering. “This expansion ensures we continue delivering industry-leading
solutions to our customers. We will now have full production capabilities in Australia of a wider range of products beyond our already established polyurethane parts production for cleaners and other wear parts.”
The newly built facility in Yatala will house Martin Engineering Australia’s headquarters in addition to 13 sales, production, and service team employees, allowing them a central hub to offer the best solutions and technical service to the market. Although the Yatala facility will be Australia’s primary manufacturing site, Perth will also have partial production capabilities.
Historically, Australian equipment production at Martin Engineering focused on polyurethane belt conveyor cleaner blades to ensure fresh products for a longer equipment life. The new Yatala facility expands the manufacturing capability to include a wide variety of patented equipment, all designed and engineered by Martin Engineering at the company’s Center for Innovation in Neponset, Illinois, USA.
“Our new manufacturing facility will produce bulk flow equipment and conveyor accessories,” said Mr. Hu. “These include air cannons, customized conveyor transfer points, impact cradles that protect the belt during loading, belt support cradles and idlers that ensure a smooth belt path, skirting to mitigate dust and spillage in the transition, and innovative belt alignment devices.”
Martin Engineering orientation and safety training takes staff through the company’s rigorous standards of service and safety.
The Yatala service and manufacturing personnel have all completed Martin Engineering’s popular Foundations™ training on conveyor maintenance and safety. In addition to online tutorial tools and hands-on training, Martin® Service Technicians (MSTs) who visit customer sites are updated on the latest bulk handling technology and methods. The training ensures that any MST who enters a customer site utilizes servicing best practices and consistently complies with WorkSafe Australia standards.
Since 2020, Western Australia and its largest city, Perth, have seen double the economic growth
rate compared to the rest of the country. The region is quickly emerging as an economic powerhouse for raw materials and trade. Martin Engineering is prepared to support that growth through shorter equipment lead times, a faster service response than competitors, and a greater understanding of local challenges.
Martin’s fleet is ready to move, serving a wide array of industries in some distant locations.
With a 14-person trained staff, a targeted manufacturing capability, and a large warehouse, the Perth branch focuses on service, maintenance, and solutions to new and existing customers. The MSTs specialize in bulk material flow on belt conveyors through belt cleaning, dust-/spillage-free conveyor transfers, belt alignment, and mitigating hopper/chute clogging using efficient air cannon designs.
Martin® Service Technicians (MSTs) enthusiastically receive some hands-on training.
Mr. Bo Hu serves as the Financial Controller of Martin Engineering’s Australian Business Unit, overseeing operations with support from Oleksiy Yakovlenko. Martin CEO, Robert Nogaj and Mr. Yakovlenko will jointly manage the operations of the Western location’s commercial department. Jorge Enriquez leads the engineering team. Sales for both branches are cooperatively managed by Mr. Yakovlenko and Marcelo Silvestre, who also oversees the East Coast Sales Department and the New Zealand territory. Additionally, Mr. Silvestre assumes responsibility
for all marketing activities within the Australian territory.
Martin Engineering Australia proudly brings its innovation and safety messages across the country.
“After years of experience in the Australian market, Martin Engineering understands the everyday challenges for bulk handlers and mining operators in the varying climates and extreme environments the country has to offer,” concluded Mr. Hu. “With these new spaces, Martin Engineering Australia is excited to embark on the next chapter of delivering excellence and innovation. Stay tuned as we continue to grow and invest in Australia’s mining landscape.”