
4 minute read
Protolabs hjälper Michelin ta fram steriliserbara skärmar
Protolabs hjälper Micherotolabs hjälper Michel ansiktsskärmar fönsiktsskärmar för
Det tog bara Michelin en månad att förse två av Frankrikes största sjukhus med 10 000 steriliserbara och återanvändningsbara ansiktsskärmar. Skärmarna är helt tillverkade i polykarbonat, och det gällde för Protolabs, att på bara några dagar välja och få fram rätt material, och tillverka komponenterna. Idag erbjuder Michelin gjutformarna, som är tillverkade av Protolabs, till andra producenter.
Advertisement
Ansiktsskärmen, som består av ett genomskinligt visir i plast med ett huvudband, används av sjukvårdspersonal tillsammans med munskydd och skyddsglasögon, och ger ett skydd mot stänk med smittsamma kroppsvätskor.
Den här typen av skärmar behövs på alla sjukvårdsavdelningar. Covid-avdelningar så klart, men också vanliga vårdavdelningar. Trots många initiativ från mindre innovativa leverantörer, är efterfrågan fortfarande större än tillgången.
När två av Frankrikes största universitetssjukhus bad Frédéric Pialot, Senior Fellow Processer på Michelin, om hjälp, släppte han allt, för att försöka lösa det akuta problemet. Sjukhusen hade ett akut behov av 10 000 enheter, och inom 48 timmar hade Frédéric valt en open source-modell, förbättrat den och hittat leverantörer för de olika komponenterna. En vecka senare levererades de första skyddsskärmarna och inom en månad hade samtliga 10 000 levererats. I samråd med de berörda sjukhusen valde Michelin en open source-lösning vanlig i Tjeckien. Modellen, som är enkel att montera och behaglig att använda, förbättrades dessutom avsevärt av Michelin:
”Det är ingen bra idé att använda PLA-tråd och plast (ofta PET) vid 3D-tillverkning av skyddsutrustning som ska användas inom vården. Eftersom PLA och PET inte kan steriliseras och även har dålig motståndskraft mot alkohol, fungerar de i realiteten som engångsmaterial. Det är däremot viktigt att påpeka att sjukvårdspersonal fortfarande måste desinfi cera utrustningen mellan patienterna” förklarar Frédéric Pialot.
”Om vi ska komma tillrätta med på bristen på skyddsutrustning måste vi kunna erbjuda återanvändningsbar utrustning. Vi valde därför att tillverka alla delar i polykarbonat, som klarar sterilisering vid höga temperaturer och som även klarar rengöring med IPA (isoproylalkohol). Vi gjorde också visiret tjockare, 1 mm, så att det klarar montering bättre, och vi valde att använda resårband av hög kvalitet."
Nästa steg för Michelin var att hitta partners som kunde leverera de olika komponenterna.
– Jag ringde femtio företag innan jag hittade ett som hade tillräckligt med polykarbonat i lager, berättar Frédéric Pialot. Till slut hittade jag ett företag i Belfortain som kunde tillverka visiren och resårbanden är specialtillverkade i Haute-Loire.
Michelin kontaktade därefter fl era 3D-printspecialister för tillverkning av huvudbandet och förstärkningsdelen i den nedre delen av skärmen.
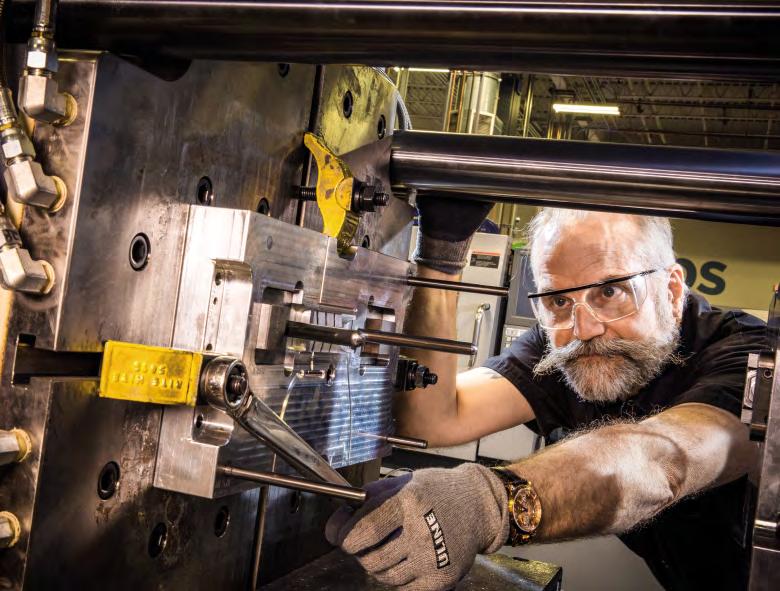

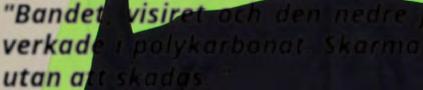
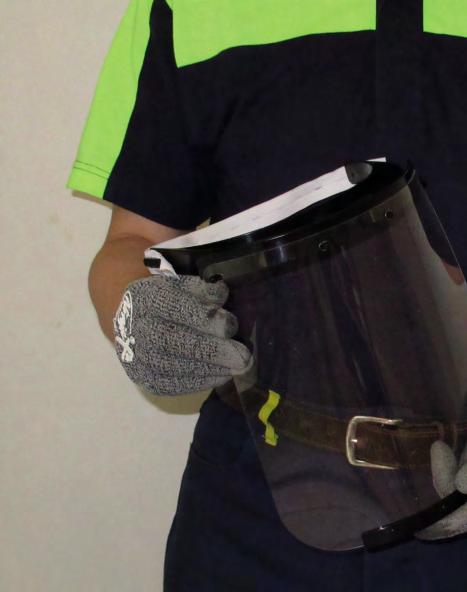
in ta fram steriliserbaral n ta fram steriliserbara sjukvårdspersonalr sjukvårdspersonal
En av dem var Protolabs, som Michelin tidigare samarbetat med för att ta fram prototyper.
Den första förfrågan kom in 29 mars 2020 och gällde tillverkning av fl era hundra delar i polyamid med så kallad Multi Jet Fusion. Så snart fi lerna laddats in i programvaran Protoquote ® startade tillverkningen, som var genomförd inom 24 timmar.
Samtidigt kontaktade Denis Ferra från Protolabs försäljningsteam och Thibaut Jeannerot från det tekniska supportteamet, Frédéric Pialot för att så snabbt som möjligt ändra produktionen till formsprutning, vilket var enda möjligheten för att kunna använda polykarbonat och producera 20 000 delar på bara några dagar.
Tillverkningsanalysen (DFM), som Protolabs hade färdig efter bara några timmar, identifi erade två mindre justeringar av delarna som ledde till att kostnaden för gjutformarna kunde kapas betydligt. Ändringarna implementerades 1 maj och tillverkningen av gjutformarna inleddes omedelbart. De första formsprutade delarna kom ut ur gjutformarna mindre än 48 timmar senare, bara fyra dagar efter att Michelin kontaktade Protolabs.
Tack vare digitala projektledningsverktyg, Protolabs produktionskapacitet och att 3D-printning och formsprutning är ett kompletterande sätt att tillverka delar, kunde alla 20 000 delar som behövdes för att montera och leverera ansiktsskärmarna på bara 11 dagar. "Det är verkligen glädjande att vi lyckades bidra i kampen mot coronaviruset. Vi är vana vid att arbeta mot tuffa deadlines eftersom vi är specialiserade på snabb turnaround, men vi vill gärna försöka överträffa oss själva när det gäller just Covid-19-projekt. Vi prioriterar dessa ordrar och tar inte extra betalt för snabb tillverkning." sägerDenis Ferra.
Resultatet är att de beställda 10 000 steriliserbara och återanvändningsbara skyddsvisiren kommer att levereras till de två sjukhusen innan slutet av april.
Michelin vill nu lämna över till andra tillverkare: ”Jag har redan kontaktats av fl era företag och har erbjudit dem att använda våra gjutformar och satt dem i kontakt med företag som kan leverera skärmarna och resårbanden,” berättar Frédéric Pialot. "Andra industriföretag som vill delta I insatsen är välkomna att kontakta oss. Det enda vi begär är att hållas informerade och att de två sjukhus som tog kontakt med oss från början fortsätter att få leveranser. För egen del kommer jag att kasta mig in i nya projekt eftersom det inte bara råder brist på skyddsutrustning. Vi har till exempel också ont om tourniqueter för blodprovstagning."
Protolabs är en av världens snabbaste digitala tillverkare av skräddarsydda prototyper och tillverkning av delar i små volymer. Det teknologistödda företaget använder 3D-printning, CNC-bearbetning och formsprutningsteknik för att tillverka delar på bara några dagar, ovärderligt för designers och ingenjörer som snabbt vill få ut sina produkter på marknaden. www.protolabs.se
förstärkningen är alla tillrna kan därför steriliseras
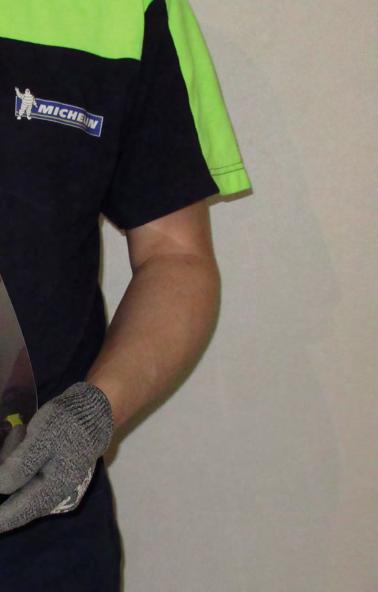
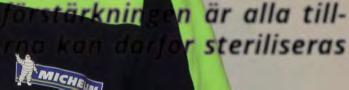

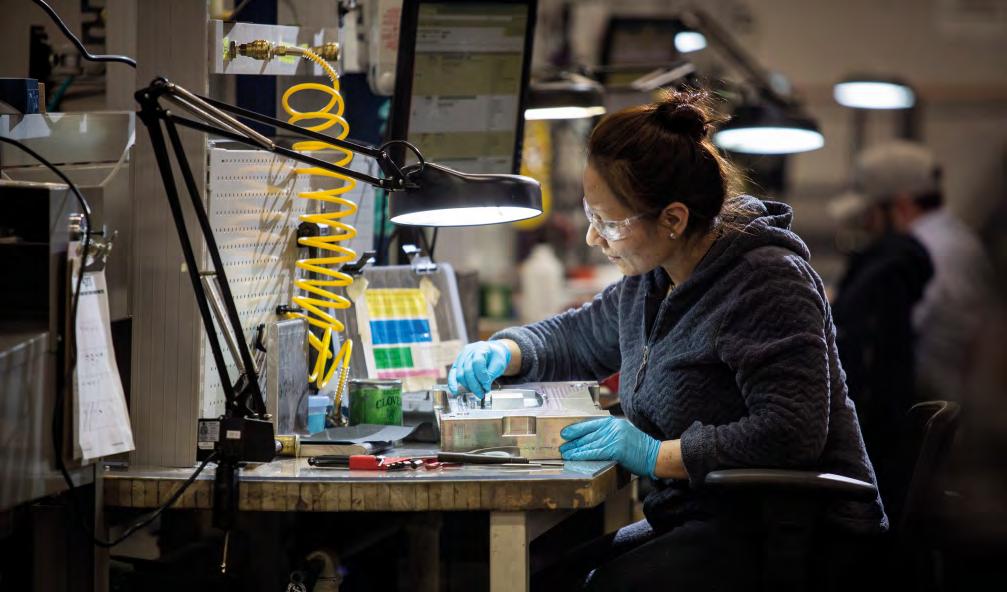