
3 minute read
Fabrication is Necessary for Navigation
from America's Engineers: The People, Programs, and Projects of the U.S. Army Corps of Engineers '24-'25
BY KELCY HANSON
Repairs and maintenance work on locks and dams is not your typical construction job. It requires detailed engineering and specialized tools for various tasks. Replacement parts are usually not available at local hardware stores.
The aging infrastructure, with over 80 years of wear and tear, needs parts specifically tailored to each component. The fabrication workshop at the Mississippi Project Office in Pleasant Valley, Iowa, is crucial for building the tools and parts required for these repairs.
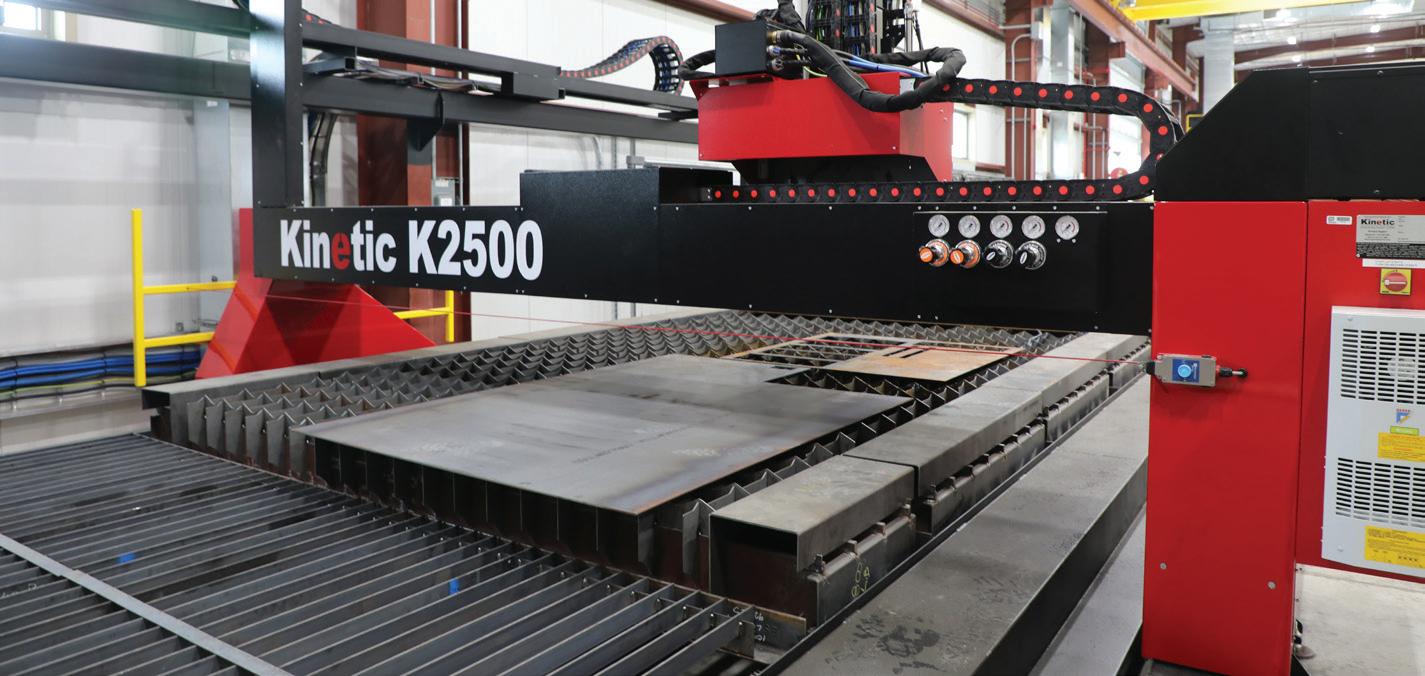
The recently added maintenance building features various mills, lathes, and a new plasma cutter, providing the Rock Island District with state-of-the-art equipment. This equipment also assists other districts with their fabrication needs.
The new plasma cutter has an 8-by 20-foot cutting bed, capable of cutting beveled edges and etching logos and designs into metal. The maintenance shop includes an overhead crane system that allows workers to safely transport heavy materials from trucks to the cutting bed.
advertisement
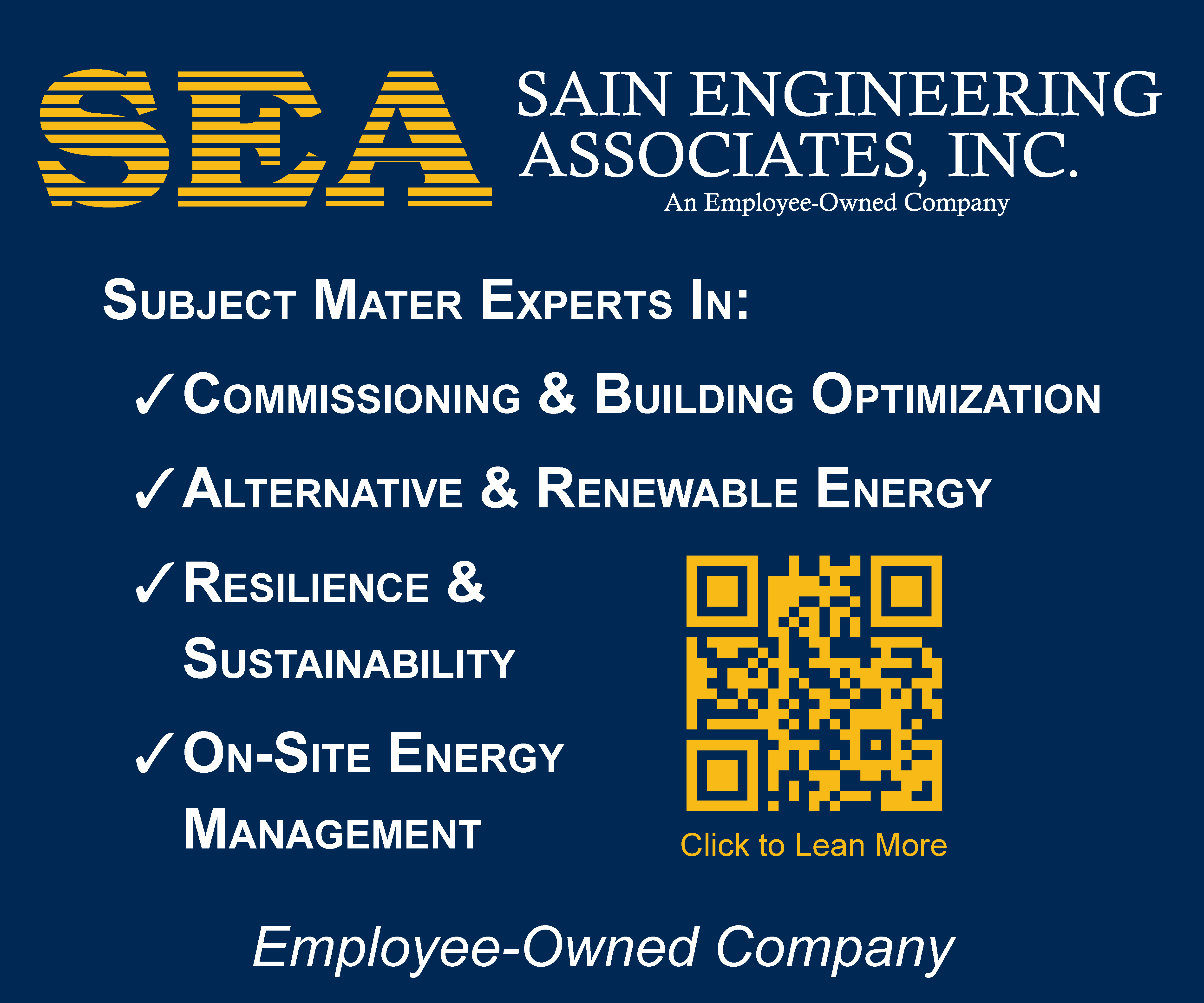
Two large machining lathes and a large vertical mill are also located in the maintenance shop. These machines are used to create round and flat tools and parts. Over the past few years, all the miter gate anchors have been replaced with newly designed “lollipops” made from 4-inch steel plates, custom cut on the machining equipment. Other parts created include anchorage pins, shafts, gear pins, large bolts, and more.
“Having our fabrication capability ensures … reliable navigation on the Upper Mississippi River,” said Matt Thurman, operations maintenance chief for the Mississippi River Project Office.
The maintenance team, consisting of 21 workers, handles all fabrication work for the Rock Island District. Additionally, they have assisted with projects in other districts. The team fabricates for the St. Paul District and has completed projects for the St. Louis, Nashville, and Little Rock districts.
One of the main benefits of having an inhouse fabrication workshop is the time saved in making and building parts. Ideally, all maintenance would be scheduled with ample time for planning and execution, but urgent repairs are sometimes necessary due to navigation accidents and routine inspections.
“Parts and fabrication items can be made quicker by self-performing the work compared to other alternatives,” said Thurman. “Now, we can adjust our priorities based on needs and fabricate on the fly.” AE
Visit www.Americas-Engineers.com to sign up for a free print edition of our annual publication and to join our weekly newsletter.