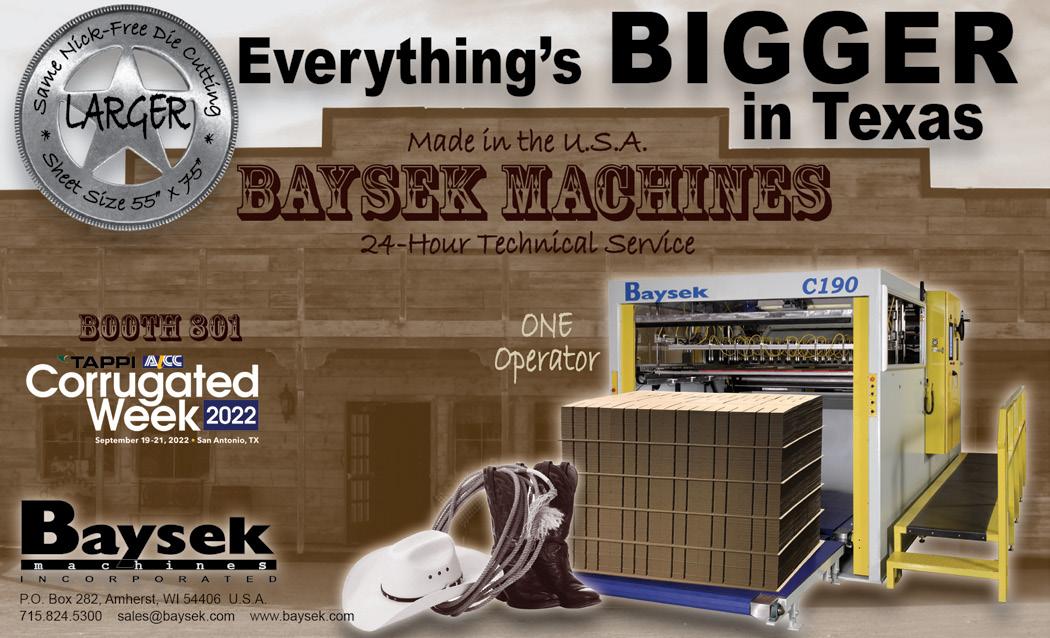
7 minute read
DESIGN SPACE
The agenda may be as simple as assigning a member to lead discussion on a key topic such as safety, production measurement, conflict management, or waste reduction. This can be as easy as sourcing information to address a recent challenge. In the discussion, all are encouraged to participate and to recommend topics to address specific needs. While a seasoned superintendent may be able to comfortably facilitate a group, a rookie will need assistance to prepare and encouragement to overcome the nerves involved in public speaking, even on this scale. In this situation, the courses at Packaging U are a perfect match. Whether the topic is waste reduction, delegation, or production code accuracy, there is a course to inform and prepare the discussion leader. At some point, there may be worth in sending one or more members to outside training (e.g., Dale Carnegie, SuperCorr, or the Science of Paper course), with the expectation that they return with practical ideas for improvement to explain and then work with the group to apply.
As the club proves the value of the time investment, local experts may be invited in. Field trips to supplier and customer facilities are invaluable perspective enhancers. The group might utilize group problem-solving tools to address real-time issues. This adds immediate value and models the use of the tools so that members may put them to use in their own areas of responsibility.
Advertisement
What is the ROI of a strategy like this? The investment is significant in terms of effort, time, and perhaps even lost production opportunity. The return will be engagement of the willing and self-selection out of the leadership ranks for the unwilling. In meetings like these, perspectives are changed, skills are modeled and developed, and ultimately, a culture is changed. Yes, it is one more thing to add to your to-do list, but developing leadership is always worth it.
And, oh, by the way, had you not heard? There’s no crying in manufacturing.
Scott Ellis, Ed.D.,
delivers training, coaching, and resources that develop the ability to eliminate obstacles and sustain more effective and profitable results. He recently published Dammit: Learning Judgment Through Experience. His books and process improvement resources are available at workingwell.bz. AICC members enjoy a 20% discount with code AICC21.
Reframing Your Approach
BY SHABAN AL-REFAI
AICC Emerging Leader Contribution
How did you get into the boxmaking industry? Everyone’s always curious, but not everyone sees it as their calling. Growing up, I loved Tetris and origami. Over time, graphic design and technology worked their way into my daily life. Naturally, it makes sense that I would end up working as a designer with a foot in both structure and graphics, and I love every day. Puzzles and problem-solving are my dessert.
In addition to working in packaging for more than seven years, I also teach packaging at night at a local university. Being allowed and encouraged by my management to teach at the University of Texas at Arlington (UTA) has allowed me to give back to the community while keeping myself sharp. Every semester, I run into new students who have no idea about our industry, and I get to reinforce my own foundations with every class.
Because the class I teach is part of the art department at UTA, it doesn’t follow the traditional packaging science teaching methodologies. Instead, there is a strong focus on fl uid intelligence, creativity, and the ability to multitask with what’s expected in the industry. Th ey learn about ArtiosCAD, Adobe, the corrugated industry, and how to design both the structure and art for boxes and displays. Each semester, students are assigned three projects for which they must create the structure and art. Over the course of their projects, they work on both elements simultaneously and have progress checkpoints for each. Rather than getting burnt out on one or the other, switching back and forth lets them process new information at a slower pace and retain it better. Remember, this is all new to them, so in some cases, it’s like taking two classes at once. Th eir foundations in creativity, art, and the 3D form help them approach design situations in uncommon and unique ways because they aren’t restricted by all the science and manufacturing limitations. People can be taught manufacturing or how to use a program because those are concrete or hard skills, but creativity falls into a weird gap. It’s a soft skill that can be honed over time, like public speaking, and a mindset or viewpoint of a nonlinear approach that’s intrinsic to the individual, like a personal quality.
Th ose familiar with graphic design coursework know that projects involve the development of 30–50 thumbnails followed by refi ned sketches. Sketches rarely only have simple linework, though. Th e students always end up doodling and sketching smaller details into the designs as they visualize their solutions. Th ey begin to work out the details of how it all links together during these brainstorming stages. If each class and each project follow the same requirement of 30–50 thumbnails, the students become extremely profi cient at brainstorming and problem-solving, which increases their fl uid intelligence over time.
Fluid intelligence is the capacity to think from diff erent points of view quickly to problem-solve without relying on past experiences and accumulated knowledge. It allows us to take independent information and create relationships between the points of reference. Th is is how abstract problem-solving is performed. Crystallized intelligence, though, is based on your past experiences and knowledge. Th is type of intelligence increases with age—“Oh, I worked on something like this in the past. I have a solution for you.” When you run into a problem that can’t be solved with the information available to you or based on past experiences, fl uid intelligence helps you take that leap. Th e purpose of 30–50 sketches during the brainstorming phase isn’t to torture the students but to exhaust their initial gut reactions and
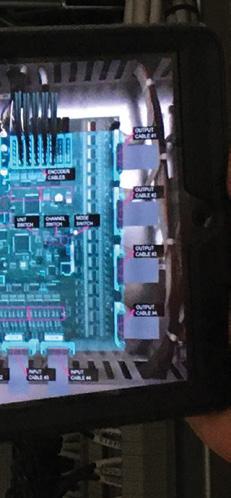
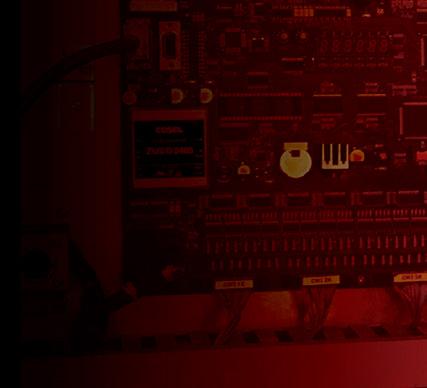


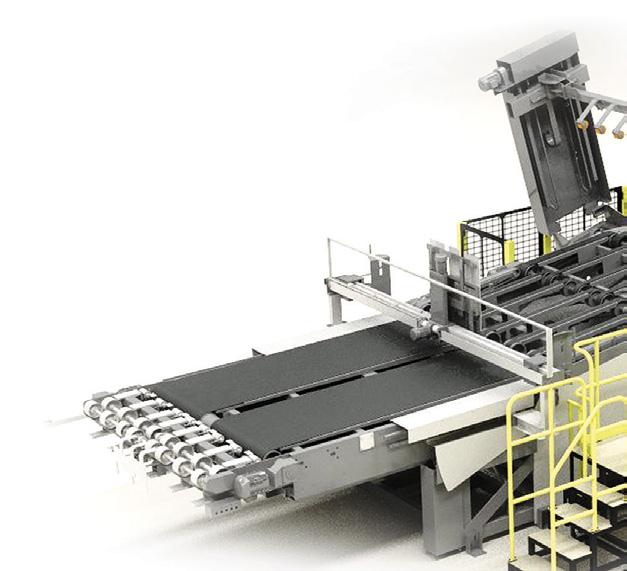
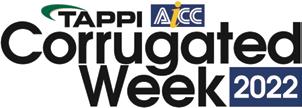
The Perfect Combo

Get Peak Performance From Your Equipment with Matched Component Sets
Nothing’s more rewarding than a couple made for each other. That’s why the engineers at ARC International have focused their skills and talents on crafting perfect matches between the components that must work in tandem on your exo folder gluers and die-cutters:
• Anilox Rollers and Ink Chambers • Anilox and Wiper Rollers • Feed and Pull Rollers • Glue and Meter Rollers
You can achieve the press speeds and print quality you need to ll your most demanding orders by pairing your team with
The ARChitects of Flexo.
Contact ARC today to learn how these engineered matches of exo folder gluer and die-cutter components (new or reconditioned) can help you achieve a more perfect union of production and pro ts.
BRONZE SPONSOR
Meet us in Booth#518
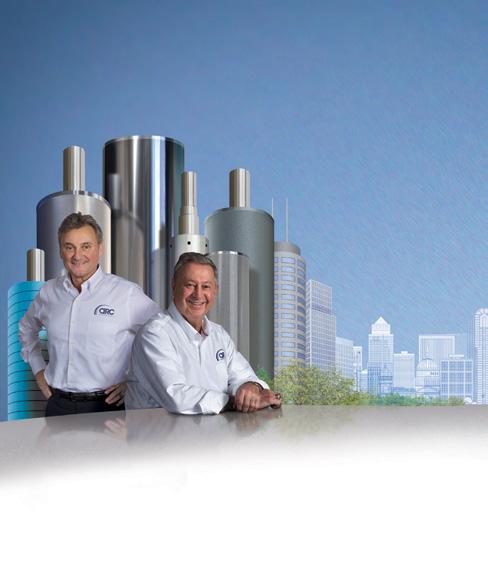
The ARChitects of exo
ARCInternational.com 800-526-4569
thoughts about a solution so that they must tap into their creative muscles and grow. Fluid intelligence is thought to decrease as we become adults, but research suggests that this happens only when we stop challenging and allowing ourselves to get creative. Being an effi cient multitasker only enhances these skills, because you don’t need to actively sit and think about the solutions. A designer can mentally work on solutions for projects that require more eff ort while working on more mundane projects that don’t require any eff ort. Everyone does this to some degree in their day-to-day life, like washing dishes or prepping dinner.
As the industry becomes more diverse, there needs to be a shift in the desired skill sets and aspirations of incoming future designers to include fl uid intelligence, creativity, and an ability to multitask. In the fi eld, I run across designers who know only graphics or structure, with no desire to learn the other side, because they feel as if they aren’t creative enough to connect the bridge; I believe this is holding back the industry. By being open to learning a new skill or taking on a project that’s outside of their scope, they can gain insights that will help them in the future. I came from a creative background in which being multifaceted was necessary, and it has only helped me excel. I love being handed the oddball projects that others don’t look forward to and creating a solution where one wasn’t apparent. In the meantime, encourage your team to engage in activities or projects that fl ex their creative muscles and increase fl uid intelligence. It helps make the day-to-day become more exciting, because creativity isn’t just a one-trick pony.
Shaban Al-Refai is a designer in structure and graphics at Harris Packaging Corp. He can be reached at shabana@ harrispackaging.com.