VAI
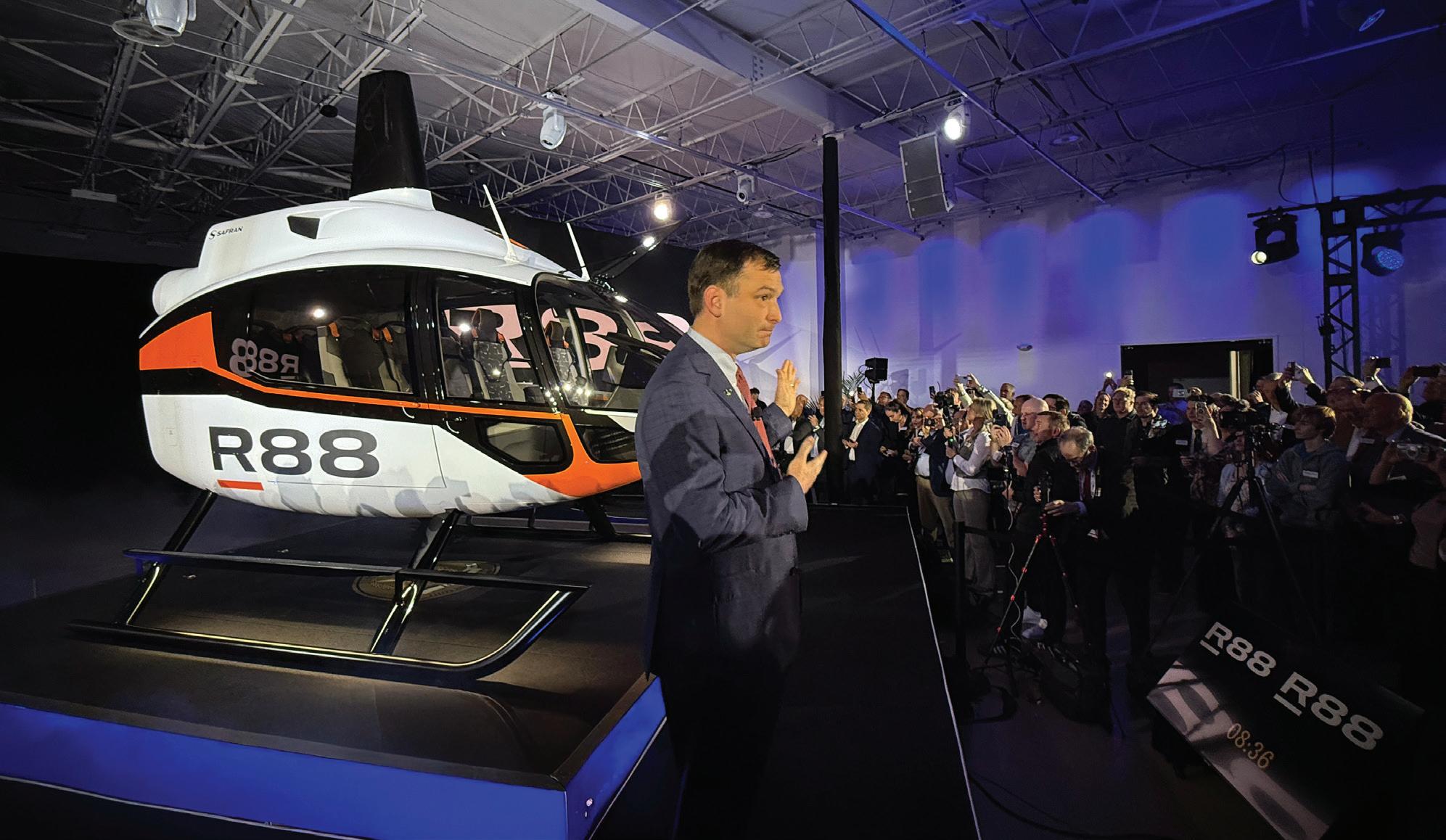
David Smith, president and CEO of Robinson Helicopter, took the wraps off the larger R88 on the eve of Verticon 2025.
David Smith, president and CEO of Robinson Helicopter, took the wraps off the larger R88 on the eve of Verticon 2025.
By Matt Thurber
In a departure from its light-helicopter roots, Robinson Helicopter has introduced the next helicopter in its product line: the 10-place single-engine turbine R88, a clean-sheet design with a new type certificate. First flight could come as early as this year, with certification and service entry to follow later this decade. The company is already booking orders for the $3.3 million R88. With a 275-cu-ft cabin capable of carrying up to eight passengers or 1,800 pounds of payload with full fuel, R88 missions will include aerial firefighting, air medical transport, utility work, and passenger transport and the cabin will be reconfigurable for various mission types.
Until the R88 enters service, the Torrance, California company’s largest helicopter is the five-seat R66, powered by a 300-shp Rolls-Royce turboshaft. The R88’s engine is a Safran Helicopter Engines Arriel 2W capable of producing 1,000 shp.
“We like to surprise the market,” Robinson Helicopter president and CEO David Smith told AIN. “It’s quite a large aircraft and is everything that Part 27 can offer in a singleengine package, with cabin capacity and performance consistent with many twins.
“This opens a lot of doors, and it’s more than the next class above the R66. I feel like we hit a sweet spot, [in terms of] economics, it’ll run at an affordable rate and can be acquired at an affordable rate and missionized at an affordable rate. It’s larger than a seven-seat aircraft and in the same range of cabin and payload as you get with twins.”
Engineers have been heavily working on the R88 for the past two years, and developing the helicopter was one of the objectives for Smith when he took over leadership of the company from Kurt Robinson in February 2024. “We talked to a lot of customers,” he said, “and asked what they needed. It’s been a big part of our engineering focus.” continues on page 22
NEW TECHNOLOGY
PioneerLab flies on Airbus’ next-gen team is working on achieveing hybrid-electric helo flight in 2027 | 16
SAF lands at Verticon
Most of the helicopters on static display flew in using greener fuel | 6
AVIONICS
Autopilot for H130 Garmin working on FAA STC approval for GFC 600H system in the Airbus helicopter | 18
EXIT INTERVIEW
Viola on VAI Association chief reflects on his tenure before he departs to head up GAMA | 20
By Curt Epstein
It was more than a decade ago when Sikorsky began developing a solution to counter the possibility of loss of main gearbox lubricating oil pressure on its large-cabin S-92 helicopter. The impetus behind the project was the 2009 crash of an S-92 about 50 miles off the Canadian Atlantic Coast after mounting studs on the helicopter’s oil filter failed in flight, causing a complete loss of gearbox lubrication.
While the OEM swiftly remedied that particular situation, it self-initiated a system-wide redesign process for future S-92s. After an investment of more than $100 million, that aspiration has been met with the unveiling of the Phase IV main gearbox, the central feature of the airframer’s new S-92A+ evolution. An independent, auxiliary oil lubrication system has its own three-gallon reservoir that will kick in if the oil pressure in the primary system fails.
“It’s not very likely; it doesn’t happen very often, but it basically lets you fly the aircraft without having any concern with respect to the gearbox and land anywhere you need to,” explained Leon Silva, the Connecticut-based airframer’s v-p of global commercial and military systems. “You don’t need to land in the water; you don’t have a 30-minute restriction.”
Thus far, the company has assembled four of the Phase IV gearboxes. As part of the program testing, Sikorsky twice ran the upgraded gearbox via the auxiliary system in a test stand for 7.5 hours—a span that far outlasts the endurance of an S-92.
“We could have kept going from what
we saw in the data,” said Kevin Wittke, a lead engineer on the program, during a preVerticon media briefing at Sikorsky’s Stratford headquarters. “By all means, the gearbox is still operational; we didn’t see any significant degradation to the internal parts.”
Overall, the company has reached 800 hours of testing, including 200 flight hours on the Phase IV gearbox that has been installed in one of its test S-92s.“We’re projecting finishing [certification] this year, and we’re taking orders,” said Silva. “We’ve done the demonstrations; the rest of it is mostly paperwork.”
Considerations are still being weighed for pricing of the Phase IV, which—in addition to becoming standard equipment on all new-build S-92s going forward—will also be available as part of a retrofit package for existing S-92As. Part of the value equation could include allowances for taking the old Phase III gearboxes as trade-ins, according to Silva.
The Phase IV gearbox was designed to be a drop-in replacement for the earlier Phase III version. Thus, the conversion process can be done right at the customer’s facility, Silva said.
In addition to the safety benefits, the move to the Phase IV gearbox carries other benefits, starting with its construction. “One of the significant changes we made is it will actually be made out of aluminum versus magnesium,” Silva said, noting that magnesium is a harder material to work with. “When we start making the Phase IV in aluminum, we anticipate that it will be easier to do.”
While heavier, aluminum has a higher strength capacity than magnesium and there are more
suppliers who work with it, thereby expanding the potential suppliers. Given that aluminum is easier to work with, the company expects the acceptable part yield to also increase. That, according to Sikorsky, will foster shorter lead times and make the units more affordable.
Another part of the A+ package benefits is a 1,200-pound increase in the helicopter’s capability, which will translate to extra fuel capacity, extended range, and/or extra load weight. In addition, Sikorsky’s engineers anticipate a higher TBO than the previous Phase III gearbox.
“We expect that the Phase IV will stay on-wing longer, and we have some projections for that, but we want to finish the certification before we publish that,” explained Silva. “The objective is that the overhaul interval and the replacement interval on a lot of these components, especially the big one being the main housing, is to be substantially longer.”
The S-92 entered service in 2004, and there are presently 276 in service in 28 countries in roles ranging from offshore oil and gas support to search-and-rescue to head-of-state transport. Notably, the fleet has accumulated more than 2.4 million flight hours, adding approximately 13,000 hours every month.
“Even if we didn’t introduce any more S-92s, the current fleet is not even halfway through its usage,” said Silva, adding that helicopters such as this tend to last up to 30 years. He pointed to the major investment in the gearbox as proof of Sikorsky’s commitment to the airframe. “Why would we be doing this if we didn’t have plans for the long term?” z
By Hanneke Weitering
CHC Helicopter and its MRO subsidiary HeliOne are working with eVTOL developer Supernal to establish and scale advanced air mobility (AAM) networks in the U.S. and abroad, the companies announced yesterday at Verticon.
Supernal is developing a four-passenger eVTOL aircraft slated for certificaton in 2028. The California-based Hyundai subsidiary has also been working with Blade Air Mobility and FBO chain Clay Lacy to figure out a plan for introducing commercial air-taxi operations.
“In partnering with CHC and Heli-One, we are confident we will devise new ways to meet customer needs through [AAM],” said David Rottblatt, senior director of strategy and commercialization at Supernal. “Matching CHC’s global experience and Heli-One’s support services with Supernal’s scaled eVTOL vehicle manufacturing will expand seamless operations as the industry matures.”
CHC Helicopter is a global helicopter services provider that primarily serves the offshore oil and gas industry while also
conducting search-and-rescue missions and emergency medical evacuations. The company operates around 300 helicopters in 30 countries. Through the partnership CHC hopes to understand how eVTOLs can integrate with its existing helicopter operations.
Heli-One would provide MRO services for CHC, as well as other Supernal eVTOL operators. According to Supernal, Heli-One is “positioned to provide MRO services to Supernal vehicles in markets where the eVTOL OEM does not initially open facilities.” z
Helicopter leasing company Milestone Aviation Group has signed leases with three operators covering 17 helicopters, most of which are in the super-medium category. Milestone’s fleet has reached more than 320 helicopters worth more than $3.5 billion, and the company is planning to redeploy some aircraft into new missions because the energy market’s needs remain steady with about 300 helicopters serving oil and gas producers (OGP).
The market for large helicopters is shifting to more super-medium types such as the Airbus H175 and Leonardo AW189, it noted. “The
major opportunity is replacement demand as aircraft age out,” said CEO Pat Sheedy.
Generally, helicopters such as the Sikorsky S-92 will serve about 20 years in their primary mission then another 10 to 14 years before retiring. Typically, this might mean a first life in OGP missions then switching to firefighting.
Because few new S-92s are being manufactured, those OGP roles are shifting to super-medium helicopters. “We’re forecasting replacement demand,” Sheedy said, “and not any major expansion.”
Some recent transactions that Milestone has concluded include Omni Helicopters In-
ternational for seven helicopters: two Airbus H145s, one H135, one H160, and one H175. The H160 and H175 are new helicopters, and the H160 is Milestone’s first placement in Brazil and will be operated by Petrobras. Omni Helicopters also extended leases for two Sikorsky S-92s. Delivery of the seven helicopters begins now and will be completed in the second quarter.
Milestone also signed an agreement to deliver four additional helicopters to Offshore Helicopter Services UK, to include two new Leonardo AW139s, one new H175, and one S-92. Deliveries are scheduled this year and in 2026. Offshore Helicopter Services also extended leases with Milestone for an S-92 and three H175s. Plans call for the H175 and S-92s to be configured for oil and gas missions by Offshore Helicopter Services in the UK.
CHC Helicopter and Milestone signed longterm leases for two new Leonardo AW189s to be delivered in the second and fourth quarters. Aker BP will fly the two helicopters in support of offshore operations in Norway. M.T.
Offshore missions demand exceptional capability: the AW189 sets the benchmark. In a rapidly evolving energy market comprising fossils and renewable energies, it enables operators to tackle challenging long-range, day/night, and deep water missions in all weather conditions.
With a class-leading cabin capable of carrying up to 16 passengers fully IOGP compliant, the AW189 meets or exceeds all current sa ety standards and is the frst helicopter certifed with HTAWS o shore mode, stren thenin operational sa ety. CO2 emissions are minimised versus payload available and usa e o Sustainable Aviation Fuels is approved ensurin maximum environmental benefts.
Visit us at VERTICON, Hall F, Stand 7750
By Curt Epstein
Many of the helicopters that flew to the Kay Bailey Hutchinson Convention Center in Dallas this weekend for display at Verticon did so on sustainable aviation fuel (SAF). The 30% SAF blend was provided by Avfuel and paid for by Airbus Helicopters.
SAF is viewed as the best near-term solution for aviation to reduce its carbon emissions footprint. While currently only approved for use in blends of up to 50% with conventional jet-A, in its neat, unblended form SAF can provide up to an 80% reduction of lifecycle greenhouse gas emissions.
The initiative underscores VAI’s commitment to sustainability in aviation and lessening the rotorcraft industry’s environmental impact. Through the use of SAF at its annual rotorcraft showcase, the organization aims to support operators’ adoption of cleaner,
renewable energy solutions, promote industrywide sustainability efforts, and demonstrate SAF’s viability in rotorcraft operations.
“The future of vertical aviation depends on our ability to innovate and adopt sustainable solutions,” said VAI president and CEO James Viola. “By using SAF at Verticon, we are taking a meaningful step toward reducing aviation’s carbon footprint and fostering a cleaner, more sustainable future for helicopter operations.” z
International helicopter brokerage Blueberry Aviation reported this week at Verticon in Dallas that it reached a milestone in rotor -
craft transactions last year. The company— with 25 sta ers based at o ces in Monaco, Dublin, New York, Mumbai, and Singapore—
acquired helicopters worth $113.65 million in 2024.
Those assets are expected to meet the needs of global clients in various platforms and market segments and signal the company’s ability to invest in high-value helicopters.
As of last year, Blueberry—established in 2003—had completed more than 540 helicopter transactions valued at more than $1.88 billion.
“Our 2024 performance demonstrates the strength of our company, our ability to invest for the benefit of our clients to provide solutions whenever they need it,” said Blueberry founder and CEO Francois Gautier. “This level of investment in very sought-after models such as [the] AW139 and AW 169 positions us well for sustained growth, as we continue to o er premium products and services that set industry standards.”
C.E.
By Charles Alcock
Propulsion pioneer MagniX is developing a new family of electric engines specifically designed for helicopters. This week, the U.S. company is going public with its response to demand for faster rotor speed motors with between 6,000 and 7,000 rpm, compared to 1,900- to 2,500-rpm powertrains it is already developing for other applications.
MagniX is working on the Heli Stormbranded motors, which it announced yesterday at Verticon 2025, with a view to be ready to start tests next year. It is aiming to have hardware, which will be integrated with the company’s Samson batteries with an energy density of up to 300 Watt hours per kilogram, delivered to early customers in 2026.
According to MagniX chief technology officer Riona Armesmith, several rotorcraft manufacturers have approached the company seeking a fresh approach to electric and/or hybrid-electric propulsion. MagniX’s engineering team is working on configurations for direct drive applications with no gearbox, and also for the motor to be combined with a turbogenerator, which in some instances might be used to produce power for non-propulsive purposes on aircraft.
While MagniX has yet to announce an initial rotorcraft application for the Helistorm engines, Robinson Helicopters has already shown interest. “MagniX has a proven track record when it comes to powering our R44 with their electric motors,” said the manufacturer’s CEO, David Smith. “Robinson is supportive of MagniX’s HeliStorm electric engine range and we look forward to continuing our collaborative efforts to deliver market leading sustainable helicopters.”
The power rating for the new engines would be no higher than the 350- to 650-kilowatt
Magni350 and Magni650 electric propulsion units (EPUs) now in development for other applications. Armesmith said her team would leverage the company’s experience of integrating motors with five different aircraft that have flown to deliver increased rotor speed.
Fundamentally, the architecture of the new engine will be fairly similar to what MagniX has already produced, but they will be smaller and lighter. The first powertrain in the range is expected to deliver peak power of 330 kilowatts and weigh just 165 pounds.
“Getting higher speeds is mainly a mechanical challenge,” Armesmith told AIN. “For what we have today [for converting airplanes] there is a large cone at the front of the engine to take the load off of the propeller. We can take this off and won’t have a propeller governor so we can skinny it down.”
Asked whether the higher speed motors would have increased wear and heat issues, MagniX CEO Reed Macdonald said the company will deliver new motors that can match the maintenance intervals of established helicopter engines. The Seattle-based company has been developing electric propulsion for the past 19 years and has produced motors for converted Caravan and Beaver utility airplanes, as well as for new airframes such as the Alice fixed-wing model being developed by Clermont Group sister company Eviation.
According to Macdonald, the path to market for an electric helicopter will be more straightforward than it is proving to be for eVTOLs.
Acknowledging that European rivals such as Safran and Pipistrel have already achieved certification for electric propulsion with EASA, he indicated that MagniX feels it is in a good
position to be the first to get to this point in the U.S. with the FAA, which agreed to Part 33 special conditions with the company in 2021.
“The helicopter market represents a tremendous opportunity for MagniX,” Macdonald commented. “Helistorm engines expand upon our existing world leading capabilities and deliver a step change in performance, reliability, and value for our customers.”
In June 2022, an electric Robinson R44 helicopter developed by Tier 1 Engineering for prospective customer United Therapeutics flew for the first time at the Los Alamitos Army Airfield in California. MagniX provided the electric motor for the planned conversion program, for which Tier 1 was seeking a supplemental type certificate.
In August 2024, Unither Bioelectronics announced a partnership with Robinson Helicopter to develope hydrogen-electric powered versions of the R44 and R66 rotorcraft. MagniX is partnered with Unither to develop the fuel cell-based propulsion system for this program.
MagniX is also working with NASA to test the Magni650 EPUs with the agency’s Electric Aircraft Testbed laboratory. This simulated flight conditions at 30,000 feet with a maximum continuous power output of 700 kilowatts. z
By Charlotte Bailey
The FAA has certified Airbus’ H125 helicopter to operate with single-pilot IFR capability.
Announced on Monday, the approval clears the way for deliveries of the IFR single-engine model to begin from the manufacturer’s U.S. assembly line in Columbus, Mississippi.
Developed in collaboration with Moog’s Genesys Aerosystems, the extended capability is based on an upgraded cockpit and new autopilot, along with redundant hydraulic and electrical systems. According to Airbus Helicopters, this combination supports advanced situational awareness and reduced pilot workload.
The FAA certification process started in March 2023, and Airbus had aimed to complete it during the second half of 2024. However, describing the capability as an “incremental innovation which brings value to the market,” Airbus Helicopters CEO Bruno Even said that the approval will reinvigorate demand for the single-engine rotorcraft.
“I don’t see the end of the H125 tomorrow,” he told journalists at a media briefing in
Airbus’ H125 is now FAA approved for single-pilot IFR operations and features Moog’s Genesys autopilot.
Germany last week. “When you are at almost 80% market share [for intermediate singleengine helicopters], I don’t have the feeling we are lagging behind, [and] we benefit from the maturity, the reliability of the product.”
According to Jérôme Ronssin, head of the light helicopters unit at Airbus, the IFR feature will expand the H125’s mission capabilities across public service, emergency medical support, and law enforcement applications. He described these market segments as being
“in high demand worldwide, and particularly in North America.”
The aircraft is produced at three final assembly lines across France, the U.S., and Brazil, while an upcoming fourth line in India, earmarked for civilian aircraft, is “progressing well,” according to Airbus. To date, more than 4,300 H125 helicopters have been delivered worldwide, with the wide Ecureuil family of aircraft having logged more than 40 million flight hours in the 50 years since its first flight. z
Van Horn Aviation has received an FAA supplemental type certificate and parts manufacturer approval for its retrofit Airbus Helicopters AS350 tail rotor. The tail rotor replaces the AS350’s spar-and-paddle style with two composite tail rotor blades attached to a steel hub with self-lubricating spherical bearings.
According to Van Horn, its tail rotor solves maintenance issues associated with the elastomeric half-bearings in the standard AS350 tail rotor and eliminates the associated inspections and replacements. Van Horn’s replacement tail rotor serves as an alternate means of compliance for four airworthiness directives.
The company claims that operators can save at least 25% in lifetime maintenance costs by replacing their AS350 tail rotors. Van Horn’s tail rotor also has a service life of 4,800 hours, which is 800 hours more than the OEM’s design.
Swept-tip composite blades and spherical bearings are features of the Van Horn STC.
“When we first tackled the AS350 tail rotor design, our main goal was to solve the maintenance problem posed by the elastomeric bearings,” said Van Horn CEO Dean Rosenlof. “Through four years of research and redesign, we’ve not only solved that issue but also produced a system that no -
ticeably enhances tail rotor performance on the venerable AS350.”
The AS350 tail rotor with individual components and installation tools, is on display at Van Horn’s Verticon booth. Components of Van Horn’s tail rotor include two swepttip composite blades, interchangeable pitch horns, a steel hub with a teeter axis for reduced pitch link loads, the spherical bearings, and a drive shaft extension with a teeter stop.
“Our AS350 tail rotor introduces several major improvements over the OEM system, from allowing operators to replace a single damaged blade to eliminating the time and expense of frequently replacing elastomeric bearings,” explained Van Horn flight operations manager Terry Tyner. “In addition, they are great blades to fly. They’re very responsive.”
H.W.
By Curt Epstein
Bell Textron is showing off a fresh slate of luxury interiors for its light single 407GXi this week at Verticon. Inspired by customer feedback, the interiors constitute a new entry in the OEM’s designer series catalog, which debuted at then-HAI Heli-Expo in 2022 with the Bel l 429.
The upgraded options for the 407 include leathers and color coordinated schemes
featuring Black Kydex panels, headliner, trim, and custom-stitched seats, along with leather wrapped, color-matched armrests and headliner inserts with embroidered Bell logos.
Among the interior color scheme combinations now available are charcoal and jet black; snow and jet black; arctic grey and charcoal; sand and jet black; and crimson and jet black. The elevated style is completed with premium flooring options.
This snow and jet black color scheme is one of five new premium Designer Series combinations offered by Bell for the 407GXi light single multi-mission helicopter.
Bell noted it has already received several orders for these interiors from corporate operators. “The release of these Bell 407 Designer Series truly sets a new standard for Bell interiors,” said Danny Maldonado, the rotorcraft manufacturer’s chief commercial officer. “We provide our customers the highest quality of materials and finishings for their aircraft and continue to introduce fresh concepts and selections to enhance their experiences.” z
By Matt Thurber
Moog’s Genesys three-axis rotorcraft autopilot for the Sikorsky UH-60A Black Hawk helicopter will soon get a fourth axis that incorporates full control of the collective. This safety enhancement, expected to get an FAA nod as soon as May, would build on the Genesys GRC autopilot supplemental type certificate (STC) issued in October for the helicopter.
Moog partnered with XP Services, a specialty helicopter modification company based in Tullahoma, Tennessee, on the Black Hawk GRC-4000 four-axis autopilot STC, which Moog will own. The modified Black Hawk with a full Genesys IDU-680 avionics suite and autopilot can be seen this week at the company’s Verticon static display.
Two- and three-axis autopilots or automatic flight control systems are common in the helicopter world and are generally a minimum requirement for flying IFR, helping pilots manage pitch, roll, and—with the third axis—yaw. Adding the collective as the fourth axis brings new layers of capability to helicopters and, to make a simple comparison, is like having autothrottles in an airplane.
A helicopter’s collective control is essentially a thrust control, enabling the pilot (or
autopilot) to adjust vertical velocity. This means climbing or descending or speeding up and slowing down, depending on which way the helicopter is oriented.
With the fourth axis, the Genesys autopilot adds more hover modes, envelope protection features, and a level button to recover the helicopter to straight-and-level flight in case of imminent loss of control. This is especially useful for inadvertent entry into instrument meteorological conditions (IMC) situations.
An automatic leveling function in the threeaxis system is enabled by engaging the stability augmentation system (SAS) with the SAS button on the HeliSAS control panel (HCP) or pressing the force-trim release (FTR) button on the cyclic for 1.25 seconds. The four-axis system adds a level button on the collective, and this accomplishes the same leveling function while also engaging the collective servo, which provides friction to keep the collective in the position that the pilot selected.
In addition to the three-axis autopilot modes, which include altitude hold, heading hold, navigation signal tracking, speed hold, and approach guidance, adding collective control as the fourth axis enhances those capabilities by
adding hover modes. These include roll/pitch geo-position, yaw heading hold, and collective above-ground height hold. The yaw damper adds turn coordination in forward-flight mode. With collective control, the four-axis autopilot can also fly terrain-avoidance maneuvers and bring the helicopter to hover at a point in space after flying an RNAV or other instrument approaches. The three- and four-axis autopilots include search-and-rescue patterns that can be programmed into the IDU-680’s integral FMS.
Sikorsky’s S-92 was one of the earlier helicopters demonstrating the benefits of fouraxis autopilots in civil rotorcraft, and they are now slowly but surely moving into more civil helicopters such as Black Hawks and lighter machines. Garmin’s GFC 600H is available in four-axis configuration and is approved on the Leonardo A109 Trekker.
Thales and StandardAero have developed a four-axis autopilot for the Airbus H125. Genesys HeliSAS and autopilots have been installed on more than 1,000 helicopters, including the Airbus H120, H125, and H130; Bell 206B/L, 407, and 505; Robinson R44 and R66; and UH-60. Along with Metro Aviation, Moog is developing a fouraxis autopilot for the Airbus EC145.
Legacy UH-60A and L Black Hawks come equipped with a SAS and a flight path stabilization computer, and the Genesys autopilot retains the original SAS but adds its own SAS, which flies on top of and in parallel with the original SAS. The SAS always stays on during flight and is never shut down, even for training purposes.
Because the original SAS is an analog system, Genesys provides a digital interface between the SAS and the GRC-4000’s flight control computer. UH-60M models have a Collins autopilot and aren’t covered by the Genesys STC.
Replacing all the old electromechanical instruments and gyros (some are fiber-optic) and wiring and installing the Genesys avionics suite with autopilot results in 80 pounds less weight in the nose of the Black Hawk. If the customer’s helicopter is equipped with radar or other nose-mounted sensor systems, the weight and balance work, but if not, stainless steel ballast plates may need to be installed. Besides being more capable, the modern avionics are more reliable and repairable; the older
instruments and gyros are almost impossible to repair, although companies such as XP Services do make removed and working equipment available to operators that still need those products.
In the demo Black Hawk, the Genesys avionics include four eight-by-six-inch IDU-680 displays, dual GPS/SBAS, dual ADAHRS, dual digital radios (navcom), a dual-channel data acquisition unit, an integrated engine and crew alerting system with system synoptic pages, and an L-3 ESI-500 standby instrument. Each IDU680 is interchangeable and includes synthetic vision system, integral FMS, TAWS, and TCAS. Two of the IFDs are isolated and can run off the helicopter’s battery in case of a complete power failure, plus the ESI-500 has its own internal battery.
The full Genesys IDU avionics suite and four-axis autopilot will cost less than $3 million. XP Services is modifying a second Black Hawk with the avionics and autopilot as well as putting together a VIP version for a customer. It also has several contracts for the avionics and four-axis autopilot as well as interest from operators of the civil Black Hawk, the S-70. z
PS Engineering is highlighting new control heads for its HUB50 audio management system optimized for HEMS and law enforcement operations this week at Verticon. The HUB50 enables users to adjust more than 270 parameters using a smartphone app.
For HEMS operators, the CTL-E has dual control heads for the pilot and flight nurse, “allowing for independent functionality during critical medical flight missions,” according to PS Engineering. CTL-E features include Doppler heartbeat monitoring audio; five passenger/patient intercom stations; patient intercom isolation with music input; nurse call button; three transmit seats for medical sta ; and copilot training configuration for non-mission flights.
The HUB50 audio unit is optimized for HEMS.
The CTL-J system is available in up to four control heads for law enforcement pilot and tactical flight o cer (TFO) positions. Capable of simulcasting simultaneous transmissions on any com port, the CTL-J’s transmit relay feature can link any two com radios for ground-to-ground communication.
Audio output is customizable, including TFO CVR audio for FLIR recordings. Additional features include artificial sidetone and microphone bias voltage for police-band radios.
Noting the versatility of the HUB50, PS Engineering CEO Greg Ledbetter said, “This unique approach has been extremely well receivedi [for] its ease of use.” M.T.
Skid-mounted sensors enable the autopilot to see and recognize obstacles and chart a safe path.
By Charlotte Bailey
Airbus Helicopters’ PioneerLab team is set to make its first hybrid-electric powered flight in 2027. During a pre-Verticon media briefing at its Donauwörth facility in Germany, the company announced the target date and said the project is on track to confirm a preliminary design later this year.
Unveiled in September 2023 with the intention of testing technologies specifically dedicated to twin-engine helicopters, the PioneerLab concept is based on the H145 platform. The test aircraft will be powered by a hybrid-electric propulsion system developed and refined in-house in an attempt to lower fuel consumption and carbon dioxide emissions by up to 30%.
This target was set based on initial studies of different propulsion systems. The H145’s existing Safran Helicopter Engines Arriel 2E turboshafts will be replaced by a hybrid-electric system, combining a single Pratt & Whitney Canada PW210S engine with a pair of Collins Aerospace 250-kW electric motors and controllers.
Drawing on lessons learned from the 100kW electric motor employed on an earlier autorotation-focused trial with the smaller H125, project manager Dominik Strobel said, “This system is not only a backup function,
it’s a full hybrid twin-engine.” He noted that the location of the batteries, provided from an undisclosed supplier, is still being finalized.
Propulsion questions still to be resolved by the PioneerLab team include which phases of flight are most suited to electric power integration and which will best benefit from thermal power. Johannes Plaum, head of research and technology at Airbus Helicopters Germany, acknowledged the limited capacities offered by today’s lithium-ion batteries. Further, the addition of an electrical element will require further collaboration between all parties to develop the required Fadec capability.
With the preliminary design review planned to be completed by year-end, unspecified aerodynamic modifications to the aircraft, which are expected to account for around 10% of the total efficiency gains, will commence later this year. “We will focus more in the aft sector than the front,” revealed Plaum, who added that adaptations will focus not only on forward flight but also embrace “the more difficult part” of efficiencies in the hover.
The first flights of these drag-reducing modifications are scheduled for 2026, and some elements could later be incorporated into
wider H145 design refinements, described by Plaum as “a hot topic for this helicopter in the future.” Installation of the hybrid powertrain is estimated to take up to a year.
In the meantime, the PioneerLab has plenty to keep busy with pending powertrain design decisions to be finalized for other applications. With the team also tasked with advancing the integration of digital technology and other environmental initiatives, flight testing of an automatic takeoff/touchdown system commenced a few weeks ago.
Sensors located on bars above the skids and fuselage-mounted cameras allow the autopilot to see and recognize obstacles and chart a safe path while providing a fully automated touchdown with the click of a button. Augmented by a third centrally-mounted camera, an upcoming fourth camera also aims to provide 360-degree coverage.
The potential integration of bio-based or recycled material into the nose section is also an area of ongoing attention. The PioneeerLab is partially funded through BMWK, the Federal German Ministry for Economic Affairs and Climate Actions through German national research project LuFo. Funding calls are made every other year, with the average funding period lasting for three years. z
By Matt Thurber
Leonardo helicopters have gained significant market share in the offshore services market, not only for oil and gas exploration but also renewable energy exploitation. This has driven demand for “modern, capable, and safe rotorcraft technologies,” according to the company.
Energy support operations are expected to continue growing during the next five years, with key drivers being wind farm support, harbor pilot shuttle flights, and search-and-rescue. In offshore service, nearly 500 Leonardo helicopters are flying, achieving 60% market share for deliveries from 2014 to 2024. Meanwhile, the global Leonardo fleet has flown nearly 3 million hours.
Of the global fleet of Leonardo helicopters, 14% are operated in the offshore energy market but they log nearly one-third of the total annual flight hours. Compared to 2019, Leonardo helicopter numbers have grown 16 percent and flight hours rose 25%.
In addition to the best-selling AW139, the AW189 is “the most successful super-medium type today,” according to the company. z
The National EMS Pilots Association (NEMSPA) is inviting Verticon visitors interested in air medical transport to participate in its Medical Pilot Career Launch activities. This week at Verticon, NEMSPA is o ering current and aspiring EMS pilots “a unique opportunity to learn from industry leaders, network with professionals, and gain valuable insights into the dynamic world of air medical transport.”
Over the show’s three days, Career Launch participants will meet EMS pilots, medical crew, and industry leaders and have access to hiring managers, chief pilots, and directors of operations from EMS operators. Career Launch training sessions will cover air medical transport technology and techniques and career paths, industry trends, and best practices. NEMSPA is also o ering free professional headshot photos during the career fair today from 10:30 a.m. to 5:00 p.m. M.T.
The Garmin GFC 600H autopilot for the Airbus H130 includes a night-visiongoggle-compatible mode controller.
By Jessica Reed
FAA supplemental type certificate (STC) approval is pending for Garmin’s GFC 600H Helicopter Flight Control System in Airbus H130 helicopters. Expected to be available in the second quarter, the retrofit autopilot will provide H130 operators with enhanced safety features and reduce pilot workload.
The system incorporates a hover assist mode that automatically detects hover conditions and helps maintain position over the ground. Garmin’s helicopter electronic stability and protection (H-ESP) technology is also featured in the system, helping pilots maintain a safe flight envelope even when hand-flying.
“We are very excited to bring the highly capable GFC 600H to Airbus H130 owners and operators. This flight control system can significantly reduce in-flight workload while also providing many advanced and safety-minded capabilities to better assist pilots in conducting their missions,” said Carl Wolf, Garmin v-p of aviation sales and marketing.
Included in the hardware configuration is a console-mounted mode controller with push-button interface and night-vision-goggle
compatibility. Integrated smart servos manage pitch and roll inputs, and a collective sensor provides smoother flight control adjustments.
When paired with Garmin’s G500H TXi and GTN Xi avionics, the system enables fully automated approach capabilities, en-route navigation guidance, and coupled missed approach procedures, including automated holds and search-and-rescue patterns.
Jérôme Ronssin, head of the light helicopters program at Airbus Helicopters, noted, “This innovative autopilot further extends the outstanding operational capabilities of the H130, offering advanced stability and precise control for safer, more efficient, and more productive missions.”
Among its safety-oriented features, the GFC 600H includes a dedicated return-to-level button that can help pilots avoid spatial disorientation in degraded visual environments, along with low-altitude protection that provides alerts and automatic pitch adjustments. Beyond retrofit applications for existing H130 and EC130T2 helicopters, Garmin indicated that the GFC 600H will also be available as a factory-installed option in new-production Airbus H130 helicopters. z
Airwolf Aerospace has received approval from Brazil’s ANAC for the installation of True Blue Power’s TB20 lithium-ion battery in Airbus AS350/H125 and AS355 helicopters.
The company also holds STCs for TB17 installations in the Airbus EC120 and EC130/H130, Bell 206A/B and 206L through L4, Enstrom 480B, MD 369/500, and Hiller UH-12E, with approvals from the FAA, EASA, Transport Canada, and ANAC. The TB20 battery is also approved by the FAA and Transport Canada in the AS350/H125 and AS355.
The TSO-certified True Blue Power batteries are up to 63% lighter than comparable lead-acid or nicad batteries, adding more useful load to the helicopter. Engine starts are also much faster and cooler with the higher voltage from the lithium-ion batteries, which take just four to 10 minutes to replenish after start.
Maintenance of the True Blue Power TB17 is required only every two years and is on-condition for the TB20, with average battery life of eight years. During cold weather, the battery’s automatic built-in heater warms up the battery before engine start.
Airwolf is also developing additional STCs for helicopters and airplanes. M.T.
True Blue Power’s lithium-ion main ship
installed in the Airbus AStar.
By Hanneke Weitering
As preowned twin-engine helicopter prices steadily increased in 2024, a drop in the number of deals and the growing supply of aircraft for sale could signal “a possible cooling trend,” according to market analysts at Aero Asset. The helicopter trading and market intelligence firm released its “2024 Annual Heli Market Trends: Twin-Engine Edition” report yesterday at Verticon.
“Our research shows a slowdown in 2024 deal volume and a growing supply for sale,” said Valerie Pereira, v-p of market research at Aero Asset. “However, the resilience in transaction prices—an 11% year-over-year increase—highlights the continued demand for quality preowned twin-engine helicopters, despite supply fluctuations.”
rose to 16 months of supply at current trade levels.
Supply of light twin-engine helicopters on the preowned market swelled by 33% YOY, while medium-twin supply dropped by
twin-engine helicopters rose by 11% last year, with the light twin segment skyrocketing to a five-year high of about $4 million. Medium and heavy twin prices both increased by 8%, according to Aero Asset.
The number of preowned twin-engine helicopter sales declined by 8% year over year (YOY) in 2024, whereas the supply of aircraft for sale increased by 14%. Average absorption rates for the market segment
15%. Although sales of preowned light twins remained steady year-over-year, medium-twin models saw a 22% decline in sales. Meanwhile, sales of heavy-twin helicopters hit a five-year low as the supply for sale increased by 13%.
Average transaction prices for all preowned
According to Aero Asset, the deal pipeline slowed toward the end of 2024. In the fourth quarter of 2024, there were about half as many pending deals as the same period in 2023. The number of twin-engine transactions still pending at year-end also hit a three-year low.
North America and Europe combined accounted for more than two-thirds of the total transactions in 2024. Sales in Europe surged 29% year-over-year, while North America saw a modest increase of 6%.
The top-performing preowned twin-engine model in 2024 was the Airbus Helicopters H145, while the Airbus H135 and Leonardo AW109S/SP were also top contenders. Ranked at the bottom with the weakestperforming markets were the Sikorsky S76D and Airbus H225. z
The FAA and EASA have granted supplemental type certificate (STC) approval for installation of Hartzell Propeller’s Tanis helicopter preheat systems on the Airbus H135, including EC135T1/ T2/T2+/T3 models and the EC635T2+. The preheat systems are available in two voltages: 115 VAC for the U.S. and 230 VAC for Europe.
Tanis preheat systems help operators perform protected engine starts in cold weather on both piston- and turbine-powered aircraft, contributing to aircraft longevity, reliability, and safety, according to Hartzell.
The Tanis silicone pad heating elements can provide heat to engines, gearboxes, hydraulics, avionics, and batteries to extend the lifetime of critical driveline components,
reduce torque oscillations, and maximize battery and starter life. Verticon visitors can see the Tanis products at the Hartzell exhibit.
“These Hartzell Propeller STCs for our Tanisbrand preheat systems expand coverage for Airbus H135 helicopters,” said Hartzell president J.J. Frigge. “The entire Tanis team truly cares about enhancing the reliability, safety, and utility of your aircraft, despite the cold weather.”
M.T.
By Kerry Lynch
As Vertical Aviation International (VAI) returns to the newly minted Verticon convention and exhibition this week, the seeand-avoid safety topic comes back into focus. VAI president and CEO James Viola pointed to the recent midair collision of a U.S. Army Black Hawk and the PSA (dba American Airlines) CRJ-700 regional airliner that claimed the lives of all 67 aboard both aircraft at Washington Reagan National Airport (KDCA).
While it will be some time before the NTSB delivers its probable cause, Viola believes that an accident such as this highlights an ongoing effort to focus on seeand-avoid skills and that the issue will be addressed during the expo. He noted that focus is important not only as a lesson learned from accidents that have occurred but also as advanced air mobility vehicles begin to enter the market, potentially sharing airspace an d airports.
“We really have to use the technology available to deconflict,” he said. “The eyeball’s been a terrible deconfliction technique for many years. We continue to have midairs.”
Technology is developing to help in these areas, Viola said, citing as an example Skyryse’s flight envelope protection system.
Part of the difficulties with advancing technology stems from the varied helicopter types and missions. “I like to think about a helicopter as a tool for work, and we’ve got 44 different missions that helicopters do,” he said, citing varied activities from tour operators to power lines and firefighting.
“You can’t put the same equipment on all the helicopters like you do with aircraft or airlines. You have to look at really the mission set that you’re trying to enhance the safety on,” Viola said. For example, he noted that some equipment adds weight, which can cut the safety margins.
“The equipment that can go on those aircraft [such as offshore operations] to make them safer are not the same ones that need to
go on ones that are doing power line patrol or moving Christmas trees up in the Northeast for the holidays,” Viola added.
Part 135 operators could more closely align with fixed-wing commercial requirements, he added, however. Viola further pointed to technologies developed for remote-piloted beyond-the-line-of-sight operations that provide deconfliction capabilities. “That same technology could be on manned aircraft as well.”
Moving toward such efforts is imperative, he said. “It’s not just even about risk; it’s about risk to your whole livelihood.”
Efforts to embrace the technology and the proper tools for the mission are paying dividends, he said, adding helicopter operators largely are on board. Referencing Skyryse again, he cited an exhibit the company did last year at the Experimental Aircraft Association’s AirVenture show in Oshkosh, Wisconsin. “I was very impressed,” he said. Several helicopter operators put down money on a technology still in development.
“I was really happy to see that industry is leaning forward with the technology with the promise that it will make flying safer because it eliminates some of the human error,” he added.
Viola is preparing to leave VAI to transition into his new role as president and CEO of the General Aviation Manufacturers Association immediately after Verticon closes. In a sad and unfortunate coincidence, Viola is departing VAI as another high-profile accident confronts the rotorcraft industry—just as it did when he came aboard to what was then Helicopter Association International (HAI) in 2020.
Joining the association in early 2020, Viola immediately faced his first crisis with the high-profile crash of a Sikorsky S-76B in Calabasas, California, that killed nine people, including basketball star Kobe Bryant
“I’m actually sad because there’s time, there’s the lessons to be learned, and there are things where there’s no quick fix like with Kobe Bryant’s accident—having an operator trying to fly in bad weather visually with their eyes again instead of just being on the
machine. And it was a fully capable machine,” he said. “Helicopters can fly low. We don’t have to be up as high as airplanes, but we do have the capability to fly in the clouds. We have the technology to do that.
“The loss of life that day was certainly not the outcome that anybody wanted,” Viola continued. “Now we just had the accident in the river, and we go back to the eyeball again. Both times you’ll see where the human failed in the eye. It was all based on visual.”
He stressed the need for the industry to get to the point where it has the technology installed and “actually use the technology for separation, by space, by altitude.”
Viola, who joined the association with a strong safety background formerly as FAA director of general aviation safety assurance, had an ambitious agenda when joining HAI. This included expanding its reach, including into new frontiers such as advanced air mobility. This all led to a new identity for the association and its hallmark annual convention.
But this goes beyond the helicopter community into the international safety stage, where VAI was able to formalize its activities with the International Civil Aviation Organization. VAI formerly did this through an umbrella organization, the International Federation of Helicopter Associations. But that organization wasn’t as recognizable.
developed helicopter communities start to look at helicopters as dangerous and move to prevent their operations locally. “There’s going to be a lot of negative ramifications just because of the involvement of the helicopter,” he acknowledged.
notion that eVTOL aircraft would replace helicopters. “We got rid of the ‘helicopters are going away,’ and the way we did that was trying to show people they have 44 missions out there,” he said.
But at the same time, helicopters are evolving with options of hydrogen and electric on the horizon. “The thing that inspires me for the future is the sustainability of the helicopters that are currently in production as we welcome the new into the future,” he said.
“As other organizations all use their same names, we this year also have transitioned to VAI at ICAO so that everybody understands that we’re the global organization collaborating around the globe,” Viola explained. “We’ve been doing that since 1986, but nobody really realized it because we used kind of an alias. We hope that transitioning to VAI will help with that.”
This is important, he explained, as accidents such as the one at KDCA reverberate around the globe and countries with less
Viola pointed to the “great work” done by helicopters such as the firefighting in California but said access to those assets isn’t as available in some locations because there aren’t global regulations for them. He also pointed to the myriad safety programs that VAI has developed or formed partnerships on such as for safety management systems—”anything we can do on the partnerships to help reduce the cost for the members as well as lessons learned and shared.”
As VAI expanded its reach, it also has worked under Viola’s tenure to dispel the
As he prepares to leave the association, Viola is enthusiastic about it remaining in good hands, praising the staff. “The pace at which VAI operates for 35 folks is amazing,” he said. “When members call, they don’t just pass on the information. They actually take on the problem, try to solve it, and then make sure others learn from it.”
As far as his transition to his new role at GAMA, he noted it is somewhat of a return for him. “When I was at the FAA, I was in charge of general aviation dealing with both airplanes and helicopters,” he noted. Coming over to VAI enabled him to focus on helicopters, “but my passion truly is aviation safety and still seeing the work that’s out there that needs to be done in both areas.”
He noted how he’s worked with the GAMA staff and leadership for well more than a decade, going back to his days at the FAA.
“They are very committed to safety. It’s a bigger, broader field. I will spread my wings a little going back to all of general aviation,” Viola said.
The outgoing VAI leader also pointed to the membership overlap with the helicopter manufacturers but particularly noted his relationship with current GAMA president and CEO Pete Bunce, who is retiring next month after a transition period with Viola. “I think that is key, and I hope to have that same relationship with whoever the board decides will take VAI after me,” he concluded. z
The R88 carries on Robinson’s two-blade teetering main rotor system with bonded metal blades but with a slightly higher disc loading, Smith said. “This is a fresh look at our two-blade architecture.”
Its blades maximize the benefits of new components, tip shapes, and noise treatment to deliver additional performance and a lower noise footprint. The tail rotor will continue company founder Frank Robinson’s specialty of high margins in all sorts of wind conditions. “That’s what customers expect from us,” Smith said.
One Robinson characteristic that is common to the R22, R44, and R66—the teeter bar single-post cyclic control—will not appear on the R88. The R88’s cyclics will be traditional dual controls, mounted like most helicopters on the floor in front of each pilot.
“It’s a huge deal,” Smith said of the departure from the teeter bar design. “The reason why is the physics of the aircraft. It is a very wide aircraft, so to get a teeter bar to work in the geometry, it just didn’t work. It was too large and the height was too high, so it didn’t make sense.”
Smith said engineers explored variations of a single-post dual control, but “pretty quickly we settled in that this was going to need a dual cyclic setup [because] of physics, not out of preference.” A benefit is that each front seat’s controls can be removed for passenger carriage.
The R88 shares the structural architecture of its siblings, with a welded steel frame, aluminum skin, and few titanium parts. The R88 will employ more use of carbon-fiber composites because those parts will be thick enough where carbon-fiber is justified compared to fiberglass. Flight controls will feature dual hydraulics for pitch and roll control.
Eighty percent of buyers select stronger windshields on the R66, so impact-resistant windshields certified to Part 29 transport helicopter requirements will be standard on the R88. “The thinking is that if we give people that as a standard feature, then no one has to choose [between] weight or safety or cost or safety,” he said.
While the Safran Arriel engine for the R88 will require certification, this is an update to an existing model, mostly involving Fadec software. Power will be derated to leave some margin, he said, “so we aren’t living at the redline.”
The R88 has three rows of seating that can accommodate a pilot and up to nine passengers.
At the aft end of the R88 fuselage, a folddown rear entry door will make it easier to load medevac patients on stretchers. Rear doors will be sliding units.
IFR capability will be an available option, according to Smith. Cruise speed isn’t yet revealed but will be “plenty fast for this market,” he said. “It isn’t a critical parameter.”
As for maximum weight, he said, “We’re not talking about gross weights directly right now, but the big picture of this aircraft is you’ll have the option for a 3,000-pound external load hook, and that’ll be a human external cargo-rated hook. And so that gives you a sense of how much it can lift, just by itself. It’s going to be a massive aircraft that’s above an [Airbus] AStar and in the range of a [Bell] 429-, [Airbus] H135-category performance.”
Range is projected at more than 350 nm and endurance will be more than 3.5 hours. Other options include a utility basket, wire-strike protection kit, and pop-out floats. Buyers can opt for high skids for increased ground clearance and firefighting water tank compatibility.
Maintenance for the R88 will replicate the typical Robinson periodic overhaul system, where the helicopter goes back to the factory or qualified service centers for heavy work.
The first R88 flight test article is under construction. “We are working hard to fly as soon as possible,” Smith said. “If it flies this year, that will be a real success for the team. But I think the more reasonable approach is maybe
a little bit beyond that.” Some pacing items include the first time Robinson is working with Safran on an engine and the fully integrated Garmin avionics suite.
“It’s an engine that we know very well from the industry. It’s a unique variant for us but it is a very stable core engine to work from,” he said. A service program from Safran is included with each R88, covering unscheduled removals for five years or 2,000 flying hours (whichever comes first), premium health monitoring, and advanced digital services.
The Garmin suite features touchscreen G500H TXi displays that include a crew alerting system, GTN navcoms, and a standard four-axis Garmin autopilot. The autopilot includes level mode, hover assist, limit cueing, and low-/high-speed protection.
A health usage monitoring system and data recording with datalink are also standard. “We’re not asking Garmin to do anything super out of the ordinary,” Smith said, “so we’re hoping that these things have de-risked the schedule and we can fly very quickly.”
“Certification for us is a relatively fast process,” he said. After the first flight, certification takes 2.5 to four years for a typical Robinson program. “The R66 was a fairly quick turnaround, roughly three years to get to certification from the initial flight. In [the R88], we intentionally chose design features that kept the risk level low from a certification standpoint.”
We train you to stay sharp, fine tune, and always be prepared—for whatever the next flight throws at you. This kind of training is more than fulfilling a requirement. It is an achievement. And it’s reserved for the sky’s most elite. FSI. Nothing short of excellence.