
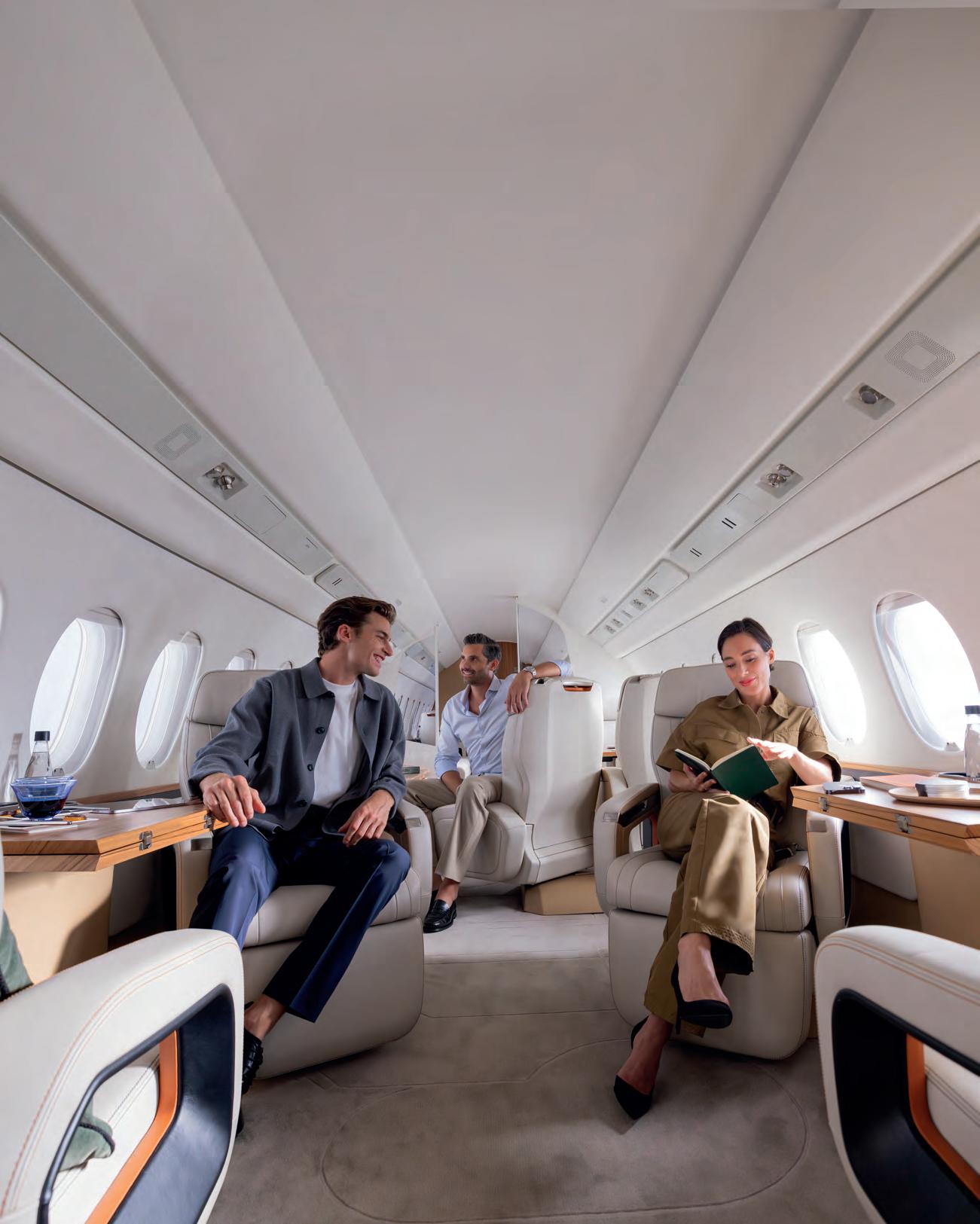
PILOT REPORT: MORE PERFORMANCE FOR THE PC-24
TECHNOLOGY: THE PROMISE OF THE DIGITAL TWIN
EXPERT OPINION: PREPPING FOR ICING
Photo of the Week: Best from AINalerts
PILOT REPORT: MORE PERFORMANCE FOR THE PC-24
TECHNOLOGY: THE PROMISE OF THE DIGITAL TWIN
EXPERT OPINION: PREPPING FOR ICING
Photo of the Week: Best from AINalerts
GE's Catalyst is among a slew of engines under development for next-generation aircraft
Scan the QR code to see the mission
17 Special Report: Engine manufacturers bet on hydrogen combustion
4 VAI’s James Viola to succeed Pete Bunce at GAMA helm
6 Gulfstream G800 makes first flight for cabin testing
8 Bombardier speeds to 200 Global 7500 deliveries
10 GAMA: Bizjet and rotorcraft deliveries, billings up in 2024
12 Special Report: New-generation engines drive the future of aircraft 20 Special Report: French start-up Beyond Aero wins backing for hydrogen bizjet
Special Report: Pipistrel advances hydrogen, hybrid, and electric power
Best of AINalerts photos of the week 26 Pilot Report: The Pilatus PC-24 refresh
42 Expert Opinion: Knowing the known in icing conditions
BY KERRY LYNCH
The General Aviation Manufacturers Association (GAMA) has selected James Viola, currently president and CEO of Vertical Aviation International (VAI), to succeed Pete Bunce at the helm of the association.
As part of a transition plan, Viola will step into his new role as GAMA president and CEO in March after the conclusion of VAI’s biggest event of the year, Verticon, while Bunce will retire in April after leading the association for nearly 20 years. In the interim, both will work closely together.
“GAMA has an outstanding reputation as a leader across the international aerospace ecosystem and I am honored and excited to work with GAMA’s members and team to further advance the critical interests and contributions of the aviation industry,” Viola said.
He joins just a handful of presidents who have steered GAMA over its 55-year history. Bunce was the second-longest serving, only behind founding member Ed Stimpson.
“I would like to extend our deepest gratitude to Pete who has done a tremendous job over the last 20 years growing GAMA’s membership, broadening its policy and regulatory reach, honoring our nation’s veterans, and being a staunch advocate for the industry,” said Eric Hinson, GAMA immediate past chair and president and CEO of Simcom International.
Bunce joined GAMA in April 2005 after retiring from a 26-year career with the U.S. Air Force. While with GAMA, Bunce expanded the association with rotorcraft membership and the growth of the advanced air mobility sector and built up its office in Brussels, tying GAMA more closely with international leaders. A fierce advocate for the general and business aviation communities, Bunce played an integral role in the fight against user fees and privatization, as well as obtaining resources for the industry during the Covid pandemic and seeking key certification reforms within the FAA.
Bunce’s plans to retire have been widely known in Washington circles. The GAMA board formed a selection committee that spent months searching for a successor.
Viola is an experienced helicopter pilot with strong regulatory expertise as a former director of general aviation safety assurance at the FAA. Joining VAI in 2020, he undertook a broad agenda to elevate the association’s international reach as well as its presence before global regulatory authorities. Perhaps among the most notable efforts in his relatively short tenure was the broadening of VAI’s reach into advanced air mobility, which resulted in the rebranding of the association. z
Gogo completed the acquisition of Satcom Direct for $375 million in cash and issuance of five million shares of Gogo stock to SD. The sellers could realize an additional $225 million “tied to realizing performance thresholds over the next four years,” according to Gogo. The acquisition expands Gogo’s airborne connectivity o erings, making the Colorado company “the only multi-orbit, multi-band, in-flight connectivity provider serving the needs of every segment of the global business aviation and military/government mobility markets.”
Two environmental protesters who spraypainted a Cessna Citation CJ1+ at Sylt Airport in northern Germany in June 2023 have been jailed by a district court judge. According to a December 8 report in Die Welt newspaper, an unnamed 24-year-old woman was sentenced to seven months in prison for joint damage and trespassing, along with a 22-year-old woman who received a six-month sentence. Fines were imposed on another pair of protesters from the Letzte Generation (Last Generation) group.
Gulfstream Aerospace has manufactured its 1,000th aircraft wing after moving production to Savannah, Georgia in 2012. All wings for Gulfstream large-cabin business jets—the G400/500/600, G650ER, and G700/800—are produced at the company’s headquarters in Savannah. The 1,000th wing shipset will be installed on a G600. Triumph originally shifted its Gulfstream G650 wing box and wing completion work to Gulfstream’s plant in 2018 and has continued to shift more of its wing work to Gulfstream to divest non-core operations.
BY AMY WILDER
Gulfstream Aerospace’s G800 test aircraft dedicated to cabin interior testing successfully completed its first flight on November 27. The aircraft took off from Savannah/Hilton Head International Airport (KSAV) in Georgia on a 1 hour 41 minute flight, during which it reached an altitude of 46,000 feet and a top speed of Mach 0.91. This marks a milestone in G800 testing focused on cabin performance and passenger experience.
The G800 will undergo a series of tests, including evaluations of its systems operations during multiple flight phases, such as hot and cold weather, turbulence, and overnight missions. This inaugural flight is part of the broader certification program for the G800, which Gulfstream heralds as exceptionally comfortable for long-haul flights.
As the longest-range Gulfstream, the G800 can fly up to 8,000 nm at Mach 0.85 or 7,000 nm at Mach 0.90.
“The G800 flight test program is making great progress, reaffirming our confidence in the flexibility, durability, and reliability this aircraft will provide,” said Gulfstream president Mark Burns. “With its vast range of innovative customization options, the ultra-long-range G800 is a true testament
to our industry-leading completions and interior and industrial design teams and their commitment to bespoke artistry.”
The G800 boasts several features designed to enhance the passenger experience, including an “ultra-galley.” The aircraft can be configured with four living areas, accommodating up to 19 passengers and sleeping 10. The G800 features a 100% fresh air system, a quiet cabin, and large panoramic windows.
It is also equipped with the Gulfstream Symmetry Flight Deck, which features active control sidesticks and touchscreen technology, as well as the Combined Vision System on a dual head-up display for enhanced safety.
Meanwhile, Gulfstream’s G700—the recently certified larger sibling of the G800—continues to amass city-pair records, with the tally now topping 65.
Most recent record flights included a 4,090-nm journey from Savannah, Georgia, to Honolulu in 8 hours 52 minutes using a blend of sustainable aviation fuel and averaging a speed of Mach 0.90. The aircraft also flew 6,507 nm from Los Angeles to Sydney in 14 hours and 26 minutes. z
FAA Administrator Michael Whitaker will step down from his role leading the agency on January 20, coinciding with the inauguration of President-elect Trump, he informed employees in a letter last month. Whitaker’s decision to depart the agency comes a little more than a year after he was confirmed to the post for a five-year tenure.
In addition to Whitaker’s departure, Deputy Administrator Katie Thomson is leaving the agency on January 10. Mark House, assistant administrator for finance and management and a 20-year FAA veteran, will become acting deputy administrator at that time.
A fixture at Seattle King County International Airport-Boeing Field (KBFI) for nearly a century, Galvin Flying quietly and suddenly closed its doors for the last time in late November. Having sold its FBO in 2014 to Landmark Aviation (now part of Signature Aviation), the company continued to provide flight training, aircraft charter, and Part 145 maintenance. The 94-year-old company announced the cessation of business in a note on its website without citing a specific reason.
The ultra-longrange Gulfstream G800’s cabin can be configured with up to four living areas, accommodating up to 19 passengers and sleeping 10, and features large panoramic windows.
Three years after Honda announced plans to produce an eVTOL aircraft for intercity travel, the Japanese carmaker is preparing to fly its first prototype. While Honda has kept its eVTOL program under wraps, FAA records indicate it recently granted an exemption to Honda Research Institute permitting the company to fly a subscale prototype experimentally for research and development. The FAA’s letter of exemption refers to the prototype as the “R&D subscale model test vehicle N241RX” weighing at least 55 pounds (25 kilograms).
BY KERRY LYNCH
The
Bombardier’s 7,700-nm Global 7500 has reached a new plateau: the 200th delivery to a customer, the airframer announced last month.
Since its 2018 entry into service, the Global 7500 fleet has amassed 200,000 hours and logged a dispatch reliability of more than 99.8%. As the fleet has grown, so have the speed records for the Mach 0.925, four-zone model.
The Canadian manufacturer noted the aircraft has accrued some 75 city-pair records. More are coming, according to David Strassburg, Bombardier demonstration pilot and safety manager for demo flight operations.
These include an 8,225-nm flight in 2019 from Sydney, Australia, to Detroit, Michigan—the longest flight ever recorded in business aviation, the company maintained. More recent missions included Miami to São Paulo, Tokyo to Los Angeles, Jeddah to London, and Los Angeles to Auckland.
However, most of these records were established in roughly the past 18 months, once Bombardier had fully ramped up production on the model, according to Strassburg.
“There was an early phase where there were a couple of records that were set, and then a lot of the focus was really on producing the aircraft, trying to support them, and making sure that we got them out there to customers,” he noted.
While the aircraft was flying at record performance, “there was a rather large gap of several years where we really weren’t taking the time to document that and show that we had the performance for the aircraft,” he said. Now, “we got the paperwork dialed in and understand what’s involved.”
In fact, all but three of the records occurred in the past year and a half. Strassburg stressed that these records were obtained during the aircraft’s normal course of business. “These are not experimental aircraft that are just available to fly around. We have customers that want to see them. We have salesmen that want to see them. So, the records are dictated by the needs of the aircraft,” he said.
Many of them were done on demo flights from one city to another, providing the ability to demonstrate speed and the quality of the flight in the aircraft to potential buyers. z
In what it is calling “the great M&A unwind,” Je eries Equities Research has outlined amounts its analysts believe Boeing could generate with the sale of some prime Boeing Global Services assets, including Jeppesen and ForeFlight. Je eries analysts believe Boeing may be planning to sell the digital services companies and that Jeppesen is worth $7 billion and ForeFlight $1 billion. Boeing is conducting a portfolio review but has not indicated what it might sell.
Embraer has implemented a program to leverage its digital evolution to help better manage its supply chain. Coming as supply-chain issues have continued to nag manufacturers, ONEChain is designed to produce greater transparency, increased collaboration, and more agility through an integrated digital platform. The result, Embraer said, is a simplified approach to supply-chain operations and one that the manufacturer believes will benefit its suppliers as well by standardizing its processes.
International Finance Corporation (IFC) is providing up to $35 million in longterm capital financing to help establish Pakistan’s first sustainable aviation fuel (SAF) plant in Sheikhupura, Punjab. Construction of the SAFCO Venture Holdings project is expected to begin this month, with an anticipated start of SAF production in September 2026. Pakistan generates more than a million tons of used oils, fats, and greases annually, and the plant—the first of its kind in South Asia—is expected to convert 250,000 tons of it as feedstock to produce 200,000 tons of SAF a year via the HEFA production pathway.
BY CURT EPSTEIN
Business jet deliveries in the first nine months increased 10.1% year over year (YOY) while turboprops saw a slight decline, according to the third-quarter 2024 aircraft delivery report released by the General Aviation Manufacturers Association (GAMA). Overall airplane billings climbed by 20.5%, to $17.3 billion.
All of the major business jet OEMs saw improvement, led by Embraer, which ramped up its production by 30% YOY over the nine-month period with 86 units delivered. The Brazilian aircraft manufacturer normally stacks its deliveries towards the fourth quarter but is taking steps to more evenly distribute its production throughout the year.
While Embraer handed over seven more light Phenom 300s this year than it did in 2023, deliveries of its midsize Praetor 500s and super-midsize Praetor 600s exceeded the previous year’s by 11 units.
Gulfstream groups all of its large-cabin aircraft (G500, G600, G650ER, G700) into one category, and it delivered 19 more of them through the first nine months of this year than it did a year ago, against two
fewer super-midsize G280s, for a more than 23% increase overall with 89 shipments. Rival Bombardier improved on the number of Challengers (3500, 650) it handed over this year by six aircraft, and tacked on one of its Global family, giving it an 8.5% rise compared with third-quarter 2023 for a total of 99 deliveries.
Textron Aviation and Cirrus Aircraft were virtually static, each with one more delivery in the first nine months of 2024 than a year ago for a total of 119 Citations and 62 Vision Jets, respectively.
Handing over 31 of its light PC-24s in the first three quarters of the year put Pilatus Aircraft just one unit off the pace it set last year, while Honda Aircraft—with nine Honda Jets to date this year—had a 25% decline from the dozen it delivered through the same period in 2023.
Dassault only reports its deliveries at mid-year and year-end. At the end of the second quarter, it had added 12 Falcon jets to the worldwide fleet.
Though it had two deliveries last year, Eclipse Aerospace did not have any through the first three quarters of 2024.
The UAE’s General Civil Aviation Authority (GCAA) is simplifying its processes and making it easier to communicate with GCAA o cials, it announced during MEBAA. Under the e ort, GCAA is encouraging business aviation companies and those wishing to open shop in Dubai to engage with its o cials. It also established a new Business Aviation Advisory Council to foster open communications. The initiative is called the “Golden Package for Registering and Operating Private and Business Aircraft.”
France-based global energy conglomerate
TotalEnergies has signed a joint development and cost-sharing agreement with Saudi government-owned petroleum producer Aramco and Saudi Investment Recycling Company to assess the development of a sustainable aviation fuel (SAF) production facility in Saudi Arabia. The three participating companies will use their expertise to establish a production unit that will create SAF from locally sourced residue feedstocks including animal fats and used cooking oil.
Abu Dhabi-based Royal Jet is diversifying its charter fleet with a firm order for three Airbus ACJ320neo VVIP jets plus options for six more. The deal is worth anywhere from $330 million to nearly $1 billion, depending on options exercised. The company has long operated Boeing aircraft, but the ACJ order is the culmination of 10 years of negotiation with Airbus Corporate Jets, said Royal Jet CEO Shafiul Syed. Royal Jet plans to take delivery of the aircraft in 2026 and is seeking bids for their design and completion.
In the bizliner segment, Airbus had no AC J deliveries through the first nine months of 2023 but this year it reported two. Boeing, with two BB Js handed over, doubled its tally from last year.
While turboprops overall experienced a nearly 1% decline from a year ago, the high-end pressurized segment had four more deliveries this year than it did for the first three quarters of 2023, equating to a better-than-2% increase.
Epic Aircraft saw an epic rise through the first nine months of 2024, with the 18 single-engine E1000 GXs it handed over representing an 80% jump from a year ago.
With Piper Aircraft’s new top-of-the-line M700 Fury receiving FAA certification this past March, it replaced the M600 in the company’s lineup, accounting for 24 deliveries in the first nine months of 2024 versus 27 for the M600 in the same period last year. The Florida OEM delivered 36 turboprop singles, two more than last year.
Textron remained virtually static in its King Air line, handing over just one fewer of the twin-engine aircraft through the first nine months of this year than in 2023.
With 58 PC-12s delivered in the first three quarters of 2024, Pilatus Aircraft was off by eight units from its YOY tally, a decline of 12%.
Piaggio—which continues to operate in receivership as it awaits a new buyer— delivered two of its twin-pusher P.180 Avanti Evo aircraft through September of this year, one more than it did in the same period last year.
Piston aircraft deliveries rose 7.5% compared with the first nine months of 2023.
Total helicopter billings increased from $2.69 billion to $2.71 billion YOY as shipments this year were slightly above those in the first three quarters of 2023, buoyed by the turbine-powered segment, which saw a nearly 2% increase. continues on page 56
Turbofan and turboprop/turboshaft engines for business aircraft of all sizes have made great strides over the last two decades in terms of improved efficiency and lower emissions in models including the GE Honda HF120, Pratt & Whitney PW800 and PW545D, Honeywell HTF7000 series, GE Passport, and Rolls-Royce Pearl. These new engines reduce fuel burn by up to 20% compared with legacy technology and feature innovative designs, materials, and production techniques.
The efficiency gains come largely in the form of engines that deliver more thrust— and therefore faster times to climb and overall ranges—with nearly the same amount of fuel.
Unlike next-generation engines developed for airliners, which can gain efficiency by increasing fan size, new business jet engines rely on operating at higher temperatures and greater thermal efficiency with redesigned low-pressure turbines, exhaust nozzles, and shaped fan blades made together in a single forging called a blisk to save weight and reduce maintenance. Greater use of composites and additive manufacturing also saves weight and parts counts.
While long-established aircraft OEMs typically work closely with legacy engine manufacturers, a new crop of supersonic fixed-wing and at least one helicopter manufacturer have decided to develop their own engines, attempting to achieve new levels of performance and reduced costs.
Despite the daunting challenges associated with choosing this path, several of these companies are reporting significant progress, as is at least one company that is
BY MARK HUBER
developing a novel-design diesel engine as a replacement option for a variety of legacy aircraft as the industry continues to confront the myriad of technical challenges accompanying the adoption of unleaded fuel as a substitute for 100LL.
AIN looked at the latest business and general aviation aircraft engine developments at the start of 2025 and their prospects for future applications.
Rolls-Royce spent the bulk of 2024 flight-testing its new Pearl 10X turbofan slated for installation on the new Dassault Falcon 10X ultra-long-range business jet. Those test flights, conducted on a Boeing 747-200 testbed aircraft, have been completed after logging 36,000 nm and 2,300 hours at speeds up to 0.9 Mach at altitudes up to 45,000 feet. Initial deliveries to Dassault are expected next year, and the 10X is slated for customer deliveries in 2027.
Exact thrust rating for the 10X engine has yet to be determined. The Pearl 700,
which will power the G800 and is currently flying on the recently certified Gulfstream G700, has a thrust rating of 18,250 pounds. A scaled version of the engine, the Pearl 15, also is used on the Bombardier Global 5500/6500 series. On the Gulfstreams, the Pearl delivers a 12% better thrust-to-weight ratio and a 5% better efficiency compared with Rolls-Royce’s BR700 series engines.
The Pearl is built around Rolls-Royce’s Advance2 engine core and low-emissions ALM combustor.
The design features a 24-blade titanium fan blisk, 10-stage HP compressor with six titanium blisks and 24:1 pressure ratio, shroudless two-stage high-pressure turbine with shroudless blade design with enhanced aerodynamics and blade cooling; and four-stage low-pressure turbine with higher fan power for more thrust with 3D airfoil geometry and 360-degree low eight cast stators. Composites are used extensively in a drive to reduce weight. The “slim-line” nacelle includes target
door thrust reversers that are aerodynamically optimized. Other composite applications include bypass ducts, maintenance doors, fan track liners, spinners, and cable bushings. Enhanced acoustic treatment improves noise reduction.
Rolls-Royce also is proposing Pearl technology for the uncrewed remote carrier system for the future combat air system being developed jointly by France, Germany, and Spain.
The GE Aerospace Passport engine currently powers the Bombardier Global 7500 and will also be on the upcoming Global 8000. FAA-certified in 2016, the twinspool design features a 52-inch, 18-blade titanium blisk fan, a 5.6:1 bypass ratio, and a 45:1 overall pressure ratio. It is GE’s first integrated powerplant design that builds the core and nacelle as an integrated unit.
The design borrows extensively from the CFM LEAP engines developed for Airbus’ narrow-bodied “neo” variants and includes a 10-stage HP compressor with both titanium blisks and nickel alloy blades.
The cowling, exhaust cone, and mixer make extensive use of advanced composites and ceramics, and the nacelle, developed with Safran, reduces weight and drag. GE claims the engine has an 8% lower specific fuel consumption compared with the Rolls-Royce BR725 on the Gulfstream G650.
An upgrade to the engine on the Global 8000, also available via STC on the Global 7500, will enable those aircraft to achieve an industry-leading top speed of Mach 0.94. Jennifer Ratica, president of Passport and CFE for GE Aerospace, told AIN that the update does not involve “turbomachinery” changes but rather software alterations. She said those changes, which require FAA approval, “are going to unlock some potential that we had already designed into our engine.”
Melvyn Heard, GE’s general manager for business aviation, told AIN that as
of October, the Passport was powering a Global 7500 fleet approaching 200 aircraft. “Overall, the operators are very happy,” he said. Heard said the health usage and monitoring system (HUMS) on the engine is streaming “terabytes” of data “that allows us to get a lot smarter on how we understand aircraft operations,” identify trends across the fleet, and quickly take any required actions.
GE is using the Passport as the demonstration platform in collaboration with NASA on the agency’s Hybrid Thermally E ffi cient Core (HyTEC) program aimed at driving further fuel efficiencies in commercial jet engines for 2030 and beyond. Part of that strategy involves using the engine core to drive substantially more electric systems on aircraft via electric motors embedded with the main engines. (Pratt & Whitney also is working with NASA on the program.)
HyTEC also will focus on the development of advanced high-pressure compressors and turbine aerodynamics and enhanced combustor materials.
Meanwhile, GE’s 1,300 shp Catalyst turboprop engine for the Beechcraft Denali was nearing the completion of its lengthy certification program as of press time. The engine, the first new significant competition to Pratt & Whitney’s venerable PT6 line in a long time, features single-lever
power control with Fadec, a three-stage power turbine, a reverse-flow combustor with advanced fuel nozzles, and a fourstage axial single centrifugal compressor that yields a 16:1 pressure ratio.
Advanced technology incorporated into the design includes a variable-geometry turbine with stator vanes that turn in flight, enabling increased pressure and temperature inside the engine. The package produces 20% fewer CO2 emissions, 18% better specific fuel consumption, and 10% more thrust compared to comparable engines, according to GE. An international team of 400 engineers and technicians worked on the program from GE facilities in the Czech Republic, Italy, Germany, and Poland.
The Honeywell HTF7000 series currently powers the Bombardier Challenger 300, 350, and 3500 series; Gulfstream G280; Embraer Legacy 450/500 and Praetors; and Cessna Citation Longitude, providing takeoff thrust between 6,944 and 7,665 pounds.
Approximately 3,000 engines are currently in service, and the list of aircraft it flies on could be growing. In early December, Honeywell signed a $17 billion agreement with Bombardier for avionics and other upgrades to the installed fleet as well as “focus on evolutions of power, reliability, and maintainability, led by the
next-generation model of Honeywell’s HTF7000 engine,” according to the company, fueling rumors that Bombardier is looking at a new entry in the super-midsize business jet category.
Compared with the company’s ubiquitous 3,000- to 5,000-pounds-of-thrust TFE731 geared engine series that began powering business jets in the 1970s, the HTF7000 series is a direct drive model that offers substantially more thrust with a new core capable of variants that can generate up to 12,000 pounds of thrust and incorporates advanced materials and designs including a high-efficiency, low-emission combustor.
Dave Marinick, president of engines and power systems for Honeywell Aerospace Technologies, told AIN that the company is continuing to pursue HTF7000 engine upgrades, in part, to stay “well ahead of emissions standards” including noise. Marinick also said the company is “very interested in hybrid” engine technologies and that the HTF7000 “has an opportunity to be configured for hybrid.”
Overall, he said the company is preparing for an era of “more electric aircraft” with technologies that include hydrogen fuel cells, noting that the company “first burned hydrogen in our APUs (auxiliary power units) more than 20 years ago” and that Honeywell is currently working on a “1-megawatt class proton exchange membrane fuel cell that we believe can also find a subscription in a future aircraft architecture.”
However, of more immediate customer interest, Honeywell unveiled its Ensemble health usage and monitoring system in October that monitors more than 50,000 engine parameters and automatically downloads and transmits information after each flight.
Ensemble allows customers and Honeywell to approach maintenance more proactively and reduce administrative burdens,
particularly for customers already enrolled in a Honeywell maintenance program because it eliminates the need to access a portal and log data as the system runs continuously in the background.
The PW545D is the latest variant in the engine maker’s series of PW500 turbofans and will power the new Cessna Citation Ascend midsize business jet that is expected to enter service in 2025. The PW545D received Transport Canada certification in May 2024, quickly followed by FAA validation. Features include Fadec with integrated autothrottle, an advanced mixer, and compressor efficiencies that will reduce fuel burn and noise.
More than 4,600 PW500 series engines are in service powering a range of Cessna Citation and Embraer jets. The PW545D supports the company’s flight, acquisition, storage, and transmission (FAST) health usage and monitoring system, and customers with FAST enrolled in the OEM’s Eagle Service Plan (ESP) can take advantage of a 6,000-hour TBO option.
The larger PW800 series turbofans currently provide power in the 10,000- to
20,000-pounds-of-thrust class and are flying aboard Gulfstream’s G500 and G600 and the recently certified Dassault Falcon 6X. Compared with legacy engines in the class, the PW800 is more fuel efficient and requires 40% less maintenance and 20% fewer scheduled inspections, according to the company. The engine shares a common core with the PW1000G developed for airline applications.
Engine maker Williams has been selected to power Honda’s new light jet entry, the Echelon. Williams already powers most of the light jet market with its FJ44 and FJ33 series engines on aircraft including Cessna Citation CJs, Cirrus Vision Jet, Premier, and Pilatus PC-24. Overall, more than 8,000 light jet engines are enrolled in the company’s TAP Blue product support program. Williams’ engines feature innovations including blisk fans and rotating fuel nozzles.
For some aircraft OEMs, either technical or price point barriers—and sometimes both—force them to chart a new path, either building onto an existing engine or designing anew from scratch. The path to doing so is often lengthy and complex.
CEO and founder Jason Hill said the price point of off-the-shelf OEM engines made developing its 500-shp single-stage gas turbine in-house an imperative. “Producing a next-generation turbine engine is a very big deal, not because it’s difficult, but because it is absolutely crucial to being able to deliver next-generation light aircraft at commercially viable prices,” he said.
Hill maintains that he can get unit costs under $100,000, based on an annual run rate of 500. And that’s important when you are marketing a new-design, five-seat kit helicopter, the HX50, for under $1 million.
Hill is attacking the problem with a design with a heavy dose of 3D printing (aka additive manufacturing) and a modular design that is “simpler, more efficient, lighter, and easier to manufacture” with “an extremely low parts count” and that is “easy to maintain.”
“Our fuel nozzles are actually removable from the outside of the engine, so they can be changed and checked and modified,” Hill said. “The fuel manifolds can be accessed from the outside as well.”
The engine also uses air-blast atomized fuel injectors for better efficiency and fewer emissions. Hill has refined a new annular combustor that will run on both conventional and synthetic biofuels. The company has reached the final stages of completing the aerodynamic optimization and is developing bearings, turbine blisks, gears, transmissions, and fabricated metal components. It plans to have a completed engine running by the end of June 2025.
The FAA-industry collaboration to eliminate the use of leaded avgas in general aviation aircraft by 2030 with unleaded (UL) fuels continues to face technical and supply challenges. Meanwhile, piston engines capable of running on jet-A are seen as one possible solution.
DeltaHawk is developing a family of fuel-efficient general aviation diesel engines as a replacement and original power for piston-engine aircraft. The company’s jet-A-fueled 180-hp DHK180
engine received FAA certification in 2023. This year, the company announced agreements with OEMs Piper Aircraft and Vulcanair Aircraft to power models of those companies’ aircraft, including Piper’s
ELEVATING EXPECTATIONS FOR 60 YEARS.
PLEASE VOTE PENTASTAR IN THE ANNUAL SURVEY TO KEEP US YOUR #1 FBO IN THE AMERICAS!
PA-44 Seminole twin. Piper and DeltaHawk are jointly developing a related STC for the Seminole.
DeltaHawk is working on variants up to 235 hp. The clean-sheet design features an inverted-V engine block, turbocharging and supercharging, mechanical fuel injection, liquid cooling, direct drive, and 40% fewer moving parts than other engines in its category. The engine is controlled via mechanical linkages, has a limited number of sensors, and is designed for most components to be externally accessed.
Working with key suppliers including StandardAero and ATI, Boom Supersonic is developing its own 35,000-pounds-thrust, twin-spool, medium-bypass turbofan Symphony engine for its Overture supersonic passenger aircraft (55 seats in airline configuration). The engine is designed to power the Overture to supersonic speeds without employing afterburners.
It incorporates a traditional turbofan design with an axisymmetric supersonic intake, variable geometry exhaust nozzle, and a cooled high-pressure turbine. The hollow-core blades are mated to a 72-inch main fan. The engine is designed to run on 100% sustainable aviation fuel and meet ICAO Chapter 14 noise restrictions.
The first 3D-printed parts have been produced for Symphony, including fuel nozzles and turbine center frames. The purpose-built engine already has run 30 engine hardware rig tests for key engine components including fans, nozzles, and combustors.
Fully operational engine core tests that will analyze the performance of the compressor, combustor, and turbine section are slated for late 2025. Forging of the engine’s superalloys for the compressor and turbine began in November.
ATI is providing the high-temperature materials and components for Symphony’s high-pressure compressor integrated blade and disk stages and for its turbine assembly including nickel-based superalloys.
StandardAero will assemble, test, and support the engine from its San Antonio, Texas facility, where it will have the capacity to assemble up to 330 engines annually.
Boom is aiming to have the aircraft certified and into production by 2030 from its factory in Greensboro, North Carolina.
Hermeus is developing the Chimera II, a turbine-based combined cycle engine capable of transitioning from turbojet to ramjet modes and powering aircraft to Mach 5 hypersonic
speeds. For Chimera II, the company will modify a commercially available, off-theshelf Pratt & Whitney F100 engine (29,160 pounds of thrust) with its proprietary inlet, precooler, ram burner, and bypass system derived, in part, from 3D printing. The F100 propels the aircraft to Mach 2.8 and then the ramjet system kicks in to do the rest. The F100 originally was developed for military aircraft including F-16 and F-15 fighters.
Chimera II is slated to fly on the Hermeus Darkhorse uncrewed aircraft and build on the work of the company’s Chimera engine program, which uses GE’s smaller 5,000-poundsof-thrust J85 engine as its core.
Darkhorse is expected to provide the technological foundation for Hermeus’s Halcyon Mach 5 passenger aircraft. z
Over the last few years, much of the hubbub about hydrogen in the advanced air mobility sector has revolved around hydrogen fuel cells, which could power eVTOL aircraft and small regional airplanes without producing harmful emissions. But hydrogen combustion technology has been picking up steam, too, with several companies preparing test campaigns with hydrogen-burning engines in 2025.
Manufacturers of traditional fossil fuel-burning engines—including RollsRoyce, Pratt & Whitney, and Safran— are betting on liquid hydrogen as the most effective means of powering large passenger-carrying airliners more sustainably and helping the industry achieve netzero carbon emissions by 2050.
Although hydrogen burns cleaner than jet fuel, hydrogen engines are not totally emissions-free. However, they could enable longer flights with larger aircraft than those that use hydrogen fuel cells, thanks to the high energy density and compact nature of liquid hydrogen.
Stored in a cryogenic tank onboard an aircraft, liquid hydrogen can fuel traditional turbine engines with some modifications. It’s compatible with existing technologies. On the other hand, hydrogen fuel cells present a more complex engineering challenge. They use hydrogen to generate electricity that powers electric motors. Hydrogen fuel cell powertrains also have a lower power-to-weight ratio due to the weight of the system’s components, so it doesn’t scale well for large aircraft.
Airbus, which wants to introduce a hydrogen-powered passenger airliner by 2035, is mulling over several configurations
BY HANNEKE WEITERING
Airbus is mulling over several configurations for hydrogen propulsion systems and airframes.
for the propulsion system and airframe, including both hydrogen fuel cells and hydrogen combustion engines. The first jet engine Airbus plans to test with hydrogen fuel will be a GE Passport on an A380, which is slated for a first flight in 2026.
Meanwhile, Safran is also developing hydrogen-powered turbine engines for light aircraft in the general aviation sector. In January 2024, Safran and its partner Turbotech completed the first successful ground test of a hydrogen-fueled gas turbine engine for France’s BeautHyFuel project. Those tests used gaseous hydrogen in TurboTech’s small TP-R90 engine. “Hydrogen is easier to handle in this form, especially on a small engine,” explained Adrien Cahuzac, a system architect for Safran’s energy and propulsion division.
Whereas hydrogen gas can power both combustion engines and fuel cells, storing it requires large, heavy pressurized tanks. Cryogenic liquid hydrogen has a higher energy density and is less bulky to
store, making it more suitable for aviation applications, although keeping the hydrogen cold enough to remain in a liquid state presents another challenge.
Using hydrogen gas, Safran was able to test engine parameters such as flow regulation strategies and engine shutdown limits, Cahuzac explained. “On the long term, the goal is therefore to store hydrogen in liquid form to carry larger quantities and fly long distances.”
This year, Pratt & Whitney Canada is preparing to demonstrate hydrogen combustion technology on a PW127XT turboprop engine—also starting with gaseous hydrogen—for a Canadian government-backed project called Hydrogen Advanced Design Engine Study (HyADES).
Canada’s Initiative for Sustainable Aviation Technology (INSAT) has already awarded funding for the first phase of the
HyADES project, which will involve ground tests of the engine’s fuel nozzle and combustor rig running on gaseous hydrogen, the engine manufacturer announced.
“This collaborative project with INSAT enables us to develop key technologies for future hydrogen-powered aircraft and complements our wider efforts to advance aviation sustainability through a range of pathways,” said Edward Hoskin, vice president of engineering at P&WC.
P&WC originally introduced the PW127XT engine in 2021 for ATR 42 and ATR 72 regional turboprops. Deutsche Aircraft has also opted to use the engines for its D328eco, a derivative of the Dornier D328 turboprop that could someday fly on hydrogen power—although initially will run on sustainable aviation fuel (SAF).
Deutsche Aircraft began building the first D328eco test aircraft in mid-2024, and the company is targeting 2027 for service entry of the SAF-powered model.
It has yet to announce a timeline for the hydrogen-powered variant, but it has already begun developing the concept in partnership with Univeral Hydrogen and H2Fly, a German company specializing in hydrogen propulsion technologies.
Joby Aviation, which owns H2Fly, has also been experimenting with the
integration of a hydrogen fuel cell powertrain in its four-passenger eVTOL aircraft. In July, Joby and H2Fly flew an eVTOL prototype with a hydrogen fuel cell powertrain. According to Joby, the hydrogen-electric demonstrator aircraft flew 523 miles— more than five times the range of its standard battery-powered JAS4-1 aircraft.
Rolls-Royce is also making inroads with hydrogen-powered business aircraft engines amid the shutdown of its electric propulsion business unit, which the company officially confirmed in November.
In September, the engine manufacturer broke ground on a new test stand at NASA’s Stennis Space Center in southern Mississippi, where the company plans to test full-scale gas turbine engines on hydrogen power.
It will use this test rig to demonstrate 100% hydrogen propulsion in ground tests with a modified Pearl 15 turbofan engine, which powers Bombardier Global 5500s/6500s.
Rolls-Royce has run a Pearl 700 turbofan engine (which powers the Gulfstream G700 and G800) on pure hydrogen gas, achieving maximum takeoff thrust during
ground testing in 2023. This followed earlier ground tests in 2022 with a Rolls-Royce AE 2100 turboprop running on “green” hydrogen, sustainably produced by splitting water molecules via electrolysis.
These efforts are all part of longer-term work Rolls-Royce is conducting in partnership with EasyJet to introduce a liquid hydrogen combustion engine for narrowbody airliners in the mid-2030s.
Rolls-Royce and EasyJet are also part of the Hydrogen in Aviation Alliance, a consortium of U.K.-based companies working to accelerate the adoption of hydrogen.
GKN Aerospace, another member of the U.K. consortium and an EasyJet partner, is advancing both hydrogen combustion and fuel cell technologies with its H2Jet and H2Gear programs, respectively. The company is also working on a cryogenic hydrogen storage system that it says could apply to either form of propulsion.
On the hydrogen fuel cell front, several companies are already integrating hydrogen- electric powertrains in eVTOL and other small electric aircraft.
In California, Joby and Alaka’i Technologies are experimenting with hydrogen in their respective eVTOL aircraft. Meanwhile, London-based Lyte Aviation is trying to use hydrogen fuel cells to power a 40-seat VTOL aircraft.
ZeroAvia, which is developing hydrogenelectric powertrain conversion kits for aircraft retrofits, expects to receive its first supplemental type certificate for the 600-kilowatt ZA600 motor in 2025.
The ZA600 is intended for regional commuter airplanes and has been tested on a Dornier 228. ZeroAvia also is working on a 2-megawatt powerplant that could power a larger aircraft carrying up to 80 or 90 passengers.
Even helicopters could soon be flying on hydrogen fuel cells, with plans underway to introduce hydrogen-powered variants of Robinson’s R44 and R66 helicopters. z
While various hydrogen propulsion options are under development for next-generation airliners, French start-up Beyond Aero for now appears to be the only company actively working to bring a hydrogen-powered business jet to market. The Toulouse-based company recently announced the completion of a $20 million Series A funding round taking its total funding to date to $44 million as it advances plans for a six- to eight-seat aircraft that could enter service in 2030.
So far, Beyond Aero faces no declared competition from any of the major business aviation manufacturers, none of which have yet confirmed plans to incorporate hydrogen propulsion into future aircraft.
However, according to co-founder and COO Hugo Tarlé, the company’s main motivation for focusing on this sector is that, with an expected maximum takeoff weight below 8.6 tonnes (about 19,000 pounds), its aircraft can be certified under EASA’s CS-23 rules, as opposed to the more complex CS-25 requirements for larger commercial aircraft.
For an aircraft that currently goes by the simple name One, Beyond Aero expects to be able to repurpose already mature propulsion technology being used for trucks, buses, and trains. “Our job is to take existing subsystems and adapt them to meet the certification requirements, filling any gaps to integrate the subsystems with the aircraft,” Tarlé explained.
Beyond Aero expects to deliver an aircraft with a four-passenger range of 800 nm, which it says matches the needs of 80% of business aviation flights. Tarlé said many of the start-up investors who have
BY CHARLES ALCOCK
backed the company’s efforts travel in business aircraft, making it easier for them to identify with the company’s core addressable market.
Earlier this year, Beyond Aero appointed Luiz Oliveira as its chief engineer. In the span of a 44-year career with Brazilian aerospace group Embraer, he was involved in that company’s Energia project, which includes plans for hydrogenpowered aircraft.
The 50-strong engineering team’s most immediate objective is to prepare to start ground testing for a 600-kilowatt subscale propulsion system that can be scaled up to a megawatt-class powertrain. Beyond Aero is investing around $12 million in a laboratory and test center in Toulouse, where Airbus is working on its ZeroE hydrogen airliner program, and it is also developing the design office it needs to secure design organization approval from EASA.
After unveiling its ambitious plans at the Paris Air Show in June 2023, Beyond Aero
had a subscale version of its hydrogenelectric powertrain flying in February 2024. It converted a G1 SPYL-XL ultralight aircraft with an 85-kilowatt propulsion system running on a mix of gaseous hydrogen and batteries. The aircraft, which the company named Blériot in honor of the French aviation pioneer, completed 10 sorties from the Gap-Tallard airfield in southern France to validate the powertrain architecture.
According to Beyond Aero, it already holds letters of intent for 108 of the planned hydrogen business jet.
These commitments are valued at $914 million, and the company said the projected unit price will be between $9 million and $10 million. That is roughly comparable to the current price for a new Textron Cessna Citation CJ4+ jet.
Beyond Aero opted for a hydrogenhybrid powertrain because the fuel cells used to produce electric power do not generate nitrogen oxide emissions, which do occur when hydrogen is directly combusted
by an engine. “It was a big technology choice and we have decided to use gaseous hydrogen because this is a realistic operational possibility for 2030, which is not the case for liquid hydrogen,” Tarlé explained.
In his view, existing business aircraft manufacturers have to focus on generating more revenues from existing programs. In this respect, he argued that a start-up like Beyond Aero is—for now—better placed to push the boundaries of new technology.
“But private aviation needs to switch to hydrogen,” he stated. “Because if you take the carbon dioxide emissions per passenger [on a business jet flight], you have a factor of 10 between the airlines and business aviation, so there is now an emergency need to decarbonize.”
In December 2022, following consultation with an advisory group of operators, Embraer said it would tighten the focus of its Energia future aircraft program to explore the possible use of hybrid-electric and hydrogen-electric powertrains. At the time, the Brazilian airframer said its primary focus would be on 19- and 30-seat regional airliners with a view to hybrid-electric options reaching “technology readiness” in the early 2030s, followed by a hydrogen fuel cell-powered application in 2035.
“Embraer sees the use of hydrogen as part of the multiple alternatives that are being explored to achieve the industry’s goal of net-zero emissions by 2050,” a company spokesman told AIN.
It is now 15 years since Bombardier launched its EcoJet project aimed at reducing emissions from business jets by 50%. The main focus of the work is on a possible blended-wing-body design, for which it has been flight testing a subscale technology demonstrator since 2022. The Canadian manufacturer has consistently said it remains “propulsion agnostic” over plans for next-generation aircraft.
Gulfstream Aerospace is keeping an open mind about future propulsion plans as it evaluates a range of technology options. “Our research and development teams continue to monitor new technologies in propulsion and electrification as they in turn continue to evolve. There are some hurdles and uncertainties to resolve before this becomes a reality for our industry,” Smitha Hariharan, vice president and chief sustainability o ffi cer, told AIN “In the near term, as we further our own decarbonization efforts and enable our customers’ decarbonization pathways, using sustainable aviation fuel blends is one of the most tangible means of doing so.”
Through its eAviation business, Textron Aviation has been actively involved in projects focused on all-electric, hybridelectric, and hydrogen propulsion. The work, mainly conducted by its Europebased subsidiary Pipistrel, is in the context
of possible new regional airliners, but that in theory could be applied to business aircraft. The most active new aircraft program is the Nexus eVTOL vehicle being jointly developed with Textron’s Bell helicopter business unit.
Pilatus told AIN that it does not comment on future technological developments. “However, we can confirm that we are actively monitoring advancements in technology,” a spokesman said. “In line with this commitment, we are participating in various initiatives, including a partnership with Swiss Synhelion to advance the development of synthetic fuels.”
Dassault Aviation did not respond to AIN ’s questions about possible plans to use new propulsion systems for future members of the Falcon family. Like other manufacturers, boosting the use of SAF has been the main focus of the French company’s decarbonization initiatives. z
Identify
When Textron acquired family-owned Slovenian sustainable aviation pioneer Pipistrel in 2022, the U.S. group significantly expanded involvement in new propulsion technology and laid the foundation for its eAviation business unit. Pipistrel’s enterprising engineering team is now contributing to all sorts of projects, ranging from Textron’s in-development Nexus eVTOL aircraft to European Union-backed work to develop a megawatt-class electric propulsion system for new airliners.
In September 2023, Pipistrel provided a repurposed example of its Taurus 4G aircraft to serve as a flying testbed for a liquid hydrogen powertrain developed by German start-up H2Fly. The flight in Slovenia was part of the EU’s Project Heaven work to assess the feasibility of hydrogen-powered airlines in achieving a quantum leap towards decarbonizing air transport. Joby, which owns H2Fly, has indicated that it may integrate a hydrogen-electric powertrain into its four-passenger eVTOL vehicle at some later date.
Through its involvement in other Europe-based projects Newborn and Hypotrade, Pipistrel has worked alongside partners including Honeywell on hydrogen fuel cell-based powertrains. The Hypotrade program calls for ground tests to start in 2026, followed by flight testing in 2030, with Pipistrel planning to provide a technology demonstrator aircraft modeled on its Miniliner concept for a 19-seat regional airliner being advanced through the Unifier 19 project.
In the near term, Pipistrel’s focus is on completing type certification of its Panthera four-seat piston single that will run
BY CHARLES ALCOCK
Pipistrel expects to fly the first of a planned family of cargo drones this year.
on avgas or unleaded fuels. Pipistrel’s president, Gabriel Massey, told AIN that it still has ambitions to introduce a hybridelectric version of the aircraft.
“We’ve flown hybrid [propulsion systems] and the technology is there, but the regulatory side is a challenge,” he explained. “People are curious about a hybrid version of a higher-performance four-seat aircraft like this, but it’s a balance between [development] resources and demand.”
Meanwhile, Pipistrel’s Velis Electro all-electric two-seat training aircraft is gaining traction on both sides of the Atlantic. Having been certified by Europe’s EASA in 2020, it subsequently earned an FAA
airworthiness exemption allowing it to be operated in the light-sport aircraft category for pilot training in the U.S.
“Flight schools are proving that it is a better option in terms of cost, noise, simplicity, and maintenance, but there is also curiosity about demonstrating [environmental] sustainability too,” Massey said.
Making use of the same electric motor and batteries as those on the Velis Electro, Pipistrel is getting closer to starting test flights with the first member of its Nuuva family of cargo drones. The V300 prototype is being assembled now and is expected to take to the air in early 2025 at the company’s facility in northern Italy. The drone is projected to deliver a range of almost 165 nm and a payload of around 660 pounds. z
Throughout the year, our AIN alerts newsletter readers have submitted many interesting and eye-catching pictures for the Friday Photo of the Week feature. Here’s a sampling of the ones we’ve published. Our thanks to everyone who has contributed photos. Keep them coming!
2 GOING OUT FOR A SPIN WITH SEAN
4 DOG DAYS OF SUMMER
We couldn’t pass up using this cute dog photo from Laura Davies on behalf of Luxaviation UK. This good boy is Buddy, a 17-month-old Bernedoodle (cross between Bernese Mountain Dog and Poodle).
1 SOMEWHERE UNDER THE RAINBOW
Chris Cook, a senior pilot for the ProOwnership team at Textron Aviation, captured this double rainbow behind a Cessna Citation CJ3+ at Blue Grass Airport (KLEX) in Lexington, Kentucky, before a large storm sytem moved through the area.
Aviation photographer Alan Staats sent in this photo of the legendary Sean Tucker in his Randolph Sunglass-sponsored Pitts S2S Skydancer, flying in fairly close formation over Chandler, Arizona, to get this incredible shot.
3 TAILING A COMET
Je ery Cullen snapped this photo from a Thrive Aviation-operated Cessna Citation Sovereign+ as they chased the ATLAS comet at FL450 from Wyoming’s Jackson Hole Airport (KJAC) to McNary Field (KSLE) in Salem, Oregon.
5 HOW LOW CAN YOU GO?
Brian Ha eman at air charter operator Latitude 33 Aviation sent in this photo from a trip to Terrance B. Lettsome International Airport (TUPJ) in Tortola, British Virgin Islands.
AIN contributing photographer Barry Ambrose captured this stunning photo of a VistaJet Global 5000 passing the Mandalay Bay Hotel on departure from Harry Reid International Airport.
The night airshow at EAA AirVenture in Oshkosh, Wisconsin in July—captured by AIN editor-in-chief Matt Thurber—thrilled crowds with stunning fireworks display.
Ian Thomson was able to capture this spectacular show of the Northern lights one early morning as he was flying from Anchorage to Kotzebue, Alaska, on a Boeing 737-400.
This Cessna Citation Longitude stays safely on the ground ahead of an approaching storm at Chester County Airport in Coatesville, Pennsylvania. Photo by Richard Bertoli, a ProOwnership pilot.
Patrick Shaver, multimedia manager at aircraft MRO C&L Aviation Group, sent this photo of a Dash 8-Q200 that came into the company’s Bangor, Maine shop for heavy checks.
If you’d like to submit an entry for Photo of the Week, email a high-resolution horizontal image (at least 2000 x 1200 pixels), along with your name, contact information, social media names, and info about it (including brief description, location, etc.) to photos@ainonline.com. Tail numbers can be removed upon request. Those submitting photos give AIN implied consent to publish them in its publications and social media channels.
BY MATT THURBER
The Pilatus PC-24 has captured a unique niche of the light jet market since it was certified in 2017. Able to operate from unpaved landing strips and match the performance of its light jet competitors, the more than 500 PC-24s delivered thus far are flown in charter operations, for single-pilot business transport, and in remote areas such as Australia where they serve patients of the Royal Flying Doctor Service. While AIN contributing writer Rich Pickett flew the earlier version of the PC-24 and reported about it in 2021, we were eager to fly the updated model and experience the changes that help make the PC-24 a top choice among light jet buyers.
For many years in the early 2000s, rumors swirled that Pilatus Aircraft was working on a special project behind closed
doors at its Stans, Switzerland headquarters. While the occasional hint spread through the business aviation industry, it wasn’t until 2013 that we finally learned about the top-secret project, and it was well worth the wait for what we now know as the PC-24—or, as Pilatus calls it, the “Super Versatile Jet.”
The genesis of the PC-24 came from discussions with customers who liked the PC-12 single-engine turboprop but hoped for a faster airplane from Pilatus. They wanted to retain the PC-12’s signature large cargo door, but designing a twinjet with such a door hadn’t been done before and it was a challenge, according to Tom Aniello, the company’s v-p of marketing.
Engine intakes have to be protected from foreign object debris, so engine position is critical. Pilatus designers also aimed to make the PC-24 capable of landing on unpaved runways including dirt strips, and that imposed further design constraints.
The ideal configuration would allow a forklift to drive up to load bulky material into the PC-24’s cargo compartment, so the trailing edge of the swept wing had to be straight instead of tapered. The double- slotted Fowler flaps needed to act like mudguards on truck tires to protect the engines. The nose landing gear is fitted with a removable fairing to protect the underbody from gravel damage during unprepared-surface operations.
Last year, Pilatus announced the first major upgrade to the PC-24, leaning into its rugged design and providing more range and payload capabilities. This included structural changes that resulted in a 600-pound payload increase to 3,100 pounds and range with six passengers growing to 2,000 nm.
However, in designing the PC-24 Pilatus didn’t stop with features that are unique in the light jet market. For example, the jet’s right engine is set up to run in Quiet Power Mode (QPM). This allows the engine to operate in a special “sub-idle” mode on the ground to cool or heat the cabin and power other systems, eliminating the need to make room for an auxiliary power unit and saving its weight.
Because the right engine runs in QPM, raising the cargo door doesn’t a ffect that engine. Although there is no limit on how long the engine can run in QPM, that running time doesn’t add to the engine’s official running time towards maintenance intervals, nor does it add an extra start cycle. QPM is especially useful in remote operations where external ground power units are unavailable.
Both engines are the same, 3,600-poundthrust Williams International FJ44-4As, but the right engine’s software enables QPM with no hardware changes. The engines normally are limited to 3,420 pounds of thrust, but an automatic power reserve mode enables the full 3,600-pound thrust capability when extra power is needed.
The PC-24’s flight controls are sophisticated for a light jet, incorporating multifunction spoilers to improve control at slow speeds and help reduce landing distance. The large Fowler flaps help slow the PC-24 down for an approach reference speed (Vref) in the low 90s. After touchdown, the weight-on-wheels switch activates the outboard spoilers, then the inboard spoilers for lift dump, and enables anti-skid braking. At slow speeds in the air, the outboard spoilers aid in roll control when the flaps are set to 8 degrees or more. The outboard spoilers also double as
airbrakes, which can be used at any speed except during a steep approach.
To keep systems simpler, the PC-24’s flight controls are actuated via pushrods and cables, while the multifunction spoilers and stabilizer trim are electrically actuated, as well as the landing gear and flaps, saving more weight and the complexity of a hydraulic system. For emergency extension, the landing gear freefalls to the down position, aided by springs and air loads.
In keeping with the Pilatus philosophy of simple, robust design and making its airplanes optimized for single-pilot operations, the PC-24 is equipped with a utility management system (UMS) that monitors and controls 28 subsystems. Developed by avionics specialist Innovative Solutions & Support, the UMS reduces pilot workload by controlling systems through the PC-24’s Honeywell avionics. Some functions are automatic, such as de-icing.
The electrical system is supported by two True Blue Power TB40 lithium-ion main-ship batteries, one aft of the right wing for engine starting and one in the PC-24’s nose for systems. Both TB40s are standard and reduce empty weight by 84 pounds compared to the previous batteries.
Pilots and passengers will appreciate the PC-24’s externally serviceable lavatory and
its freshwater storage tank, which is good for about 12 flushes. Single-point fueling is another convenience factor. The vaporcycle air conditioning uses an electrically driven compressor and can be run using ground power or the QPM engine.
Pilatus chose Honeywell’s Primus Epic 2.0 avionics for the PC-24’s Advanced Cockpit Environment (ACE) flight deck. This wasn’t a surprise, given the PC-12’s adoption of a similar Honeywell suite and realizing that many PC-24 pilots come to the jet with experience in the PC-12. For pilots who grew up on Garmin avionics, the Honeywell system takes a little getting used to but it is a fully capable, powerful integrated avionics suite.
In the PC-24, there are four 12-inch displays, a primary flight display (PFD) in front of each pilot, and two multifunction displays (MFDs) in the center. There are a lot of buttons in this cockpit because these aren’t touchscreen displays. However, there is a touchscreen controller (TSC) below the lower MFD, and here pilots can select active displays, tune radios and set transponder codes, access datalink communications, swap MFDs, and record events.
The TSC was adopted from its first implementation in the PC-12 NGX. Two dual-concentric knobs on the TSC generally mirror each other, and they are used for various tasks, depending on what is displayed on the TSC, such as display unit scrolling, radio tuning, and radar controls. The TSC also hosts a pop-up keyboard, which activates when the cursor hovers over a field where data entry is available. Moving the cursor is done with the cursor control device (CCD), but this isn’t a separate piece of hardware that takes up a bunch of console space; the CCD uses the TSC screen as a touchpad, activated by touching the display.
Like any modern business jet, the Honeywell ACE suite has all the modern features including LPV approaches, SmartView synthetic vision system, Honeywell Laseref IV inertial reference system-based flight path guidance, coupled VNAV, visual approaches, envelope protection, CAS-linked checklists, and Honeywell’s SmartRunway and SmartLanding, the latest version of its Runway Awareness and Advisory System. Avionics options include ADS-B In for cockpit display of traffic information, 2D airport moving maps, Honeywell RDR 7000 digital radar, satellite weather, and en route controller-pilot datalink communications.
Pilots can update PC-24 nav databases and send ForeFlight flight plans and weight and balance information directly to the PC-24 from iPads via an Aspen Avionics gateway installed in the airplane. With the upgrade, Pilatus added connected features so that after landing, the airplane sends fault history to Pilatus for AOG support. This is retrofittable to older PC-24s and will enable Pilatus to analyze the data to inform its predictive maintenance program.
When Pilatus finally introduced the PC-24 in 2013, some may have wondered whether there was a large enough market for another light jet, but initial and subsequent sales have clearly answered that question. Since its introduction, one of the PC-24’s competitors—the Learjet 70/75—has ceased production, and its remaining rivals are the Citation CJ4 and Embraer Phenom 300E.
Performance-wise, the PC-24 doesn’t seem to stand out, but it more than keeps up with a much larger cabin than its competitors and a 4-foot 1-inch-wide and 4-foot 3-inch-high cargo door, which none of the others have. The PC-24’s cabin volume is 501 cubic feet, not including the cargo area, which is essentially part of the cabin and fully accessible in flight. This is significantly larger than the Phenom 300E at 314 cubic feet and the CJ4 at 293 cubic feet, but what that extra space does is provide not only more legroom between seats but also more flexibility in the cabin layout. The PC-24 is the only jet among these three that has a flat-floor cabin. The PC-24 cabin is also taller (5 feet 1 inch) and wider
(5 feet 7 inches) than the 300E (4 feet 11 inches and 5 feet 1 inch) or CJ4 (4 feet 9 inches and 4 feet 10 inches).
The second row of executive seats can swivel 180 degrees so, even in flight, passengers can easily switch from a club to a forward-facing configuration. The typical interior layout selected by buyers is the sixseat executive, and this is easily expanded to eight by adding two commuter-style seats, which are categorized as loose equipment for easy swapping in and out.
The cargo area shrinks and expands with the number of seats. In the six-seat layout, the cargo volume is 90 cubic feet, and that drops to 51 cubic feet with eight or 10 seats installed.
Opposite the entry door is a sink, and underneath is a stowable vacuum-flushing toilet that is externally serviceable. Privacy is provided by hard doors forward and aft. The big benefit of the forward lav is that it doesn’t take up any cargo space, leaving room for up to pallet-size payloads to be loaded via forklift.
All three jets are not far off in speed capability: the PC-24’s high-speed cruise is 440 knots, although the competitors are faster. The CJ4 cruises at 451 knots and the Phenom 300 at 464 knots. Now, with the upgrade, range is just over 2,000 nm for all the three jets, and they share the same FL450 maximum altitude.
Current retail pricing for the PC-24 is $12,150,000 at base level or $13,510,000 typically equipped.
Like other business aircraft OEMs, Pilatus is highly vertically integrated, manufacturing most of the airframe at its Stans, Switzerland headquarters and employing a team of skilled craftspeople to make interior components and paint the airplanes at both Stans and at its U.S. Pilatus Business Aircraft base at Rocky Mountain Metropolitan Airport (KBJC) in Broomfield, Colorado.
Seat work for all PC-24s is done in Broomfield. A huge Zünd Systemtechnik
leather-cutting machine cuts the 82 to 84 pieces that make up a PC-24 seat in an optimal pattern that maximizes the output from a hide of leather. Before the cutting, a Pilatus expert marks up the leather with a special pen to identify any defects on the hide, and the Zünd eliminates these from its output. Defects might include barbedwire scars on U.S. leather or mosquito bites on European leather (barbed wire isn’t used in Europe). Once cut, the pieces go to skilled craftspeople at the sewing and stitching station, then they are placed on the seat frame.
Cabinetry comes as part of a kit from F/List in Austria, simplifying the interiors completion process.
Pilatus opened a paint shop at KBJC in 2022, which greatly sped up completions. The PC-24 comes either coated in primer green or with a base coat from Stans. The paint shop’s seven bays run seven days a week to keep up with demand.
As for the upgrade, there were more than 700 structural changes to the airframe, some as small as shaving off a few grams, and 1,000 total changes to achieve an empty weight 160 pounds lower and an increase in mtow of 440 pounds. Some of these include modifying wing spars and ribs, changing how the nose landing gear
is machined, and switching the spoilers to carbon fiber from aluminum.
A new in-flight entertainment system from Lufthansa Technik is now standard, with a 10-inch touchscreen display and 3D moving map, four cabin speakers, mood lighting, more USB ports, and dedicated media storage. A three-seat divan that is 6 feet 6 inches long and can convert to a bed is a new option. Drawers under the divan can store pillows and blankets.
Deliveries of the upgraded PC-24 began in 2024.
My flight in the PC-24 was in serial number 503 with Pilatus Business Aircraft chief pilot Gerard Lambe. This PC-24 had all the latest enhancements introduced in 2023 but not the optional divan. We started with a walkaround where he pointed out the PC-24’s aforementioned features.
Both True Blue Power lithium-ion batteries are used to start the Williams FJ44-4A engines. The electrical system is managed and protected by four electrical power distribution units, which provide secondary power distribution, utility management via two data concentration and processing units, over-current protection, and automatic load-shedding to
reduce pilot workload during a generator failure.
Lambe explained that the PC-24 has a rudder bias system that senses an engine spooling down and applies rudder using autopilot servos to mitigate the resulting yaw. After the large yaw caused by an engine out on takeoff, the automatic yaw trim system takes over and maintains coordinated flight.
Contributing to the PC-24’s takeoff performance is another unique feature: passive thrust vectoring. The FJ44-4A engines’ exhaust nozzles have a curved ramp on the top section, which creates a Coanda effect that keeps exhaust airflow attached to the nozzle and flowing slightly (3 degrees) upward at slow speeds such as during takeoff. The result is a thrust component that pushes the tail down and helps the PC-24 rotate. At higher speeds, the exhaust flow straightens and there is no drag penalty.
We planned an IFR flight to Telluride, Colorado, with five occupants and carrying 3,220 pounds of fuel and 50 pounds of cargo for a takeoff weight of 16,136 pounds, 2,604 pounds below mtow.
To prepare for engine start, we ran the electronic checklists using a dedicated button on the yoke. Where applicable, a synoptic page opens to show system status related to the checklist item. For starting, we needed to verify that the state of charge indicator was green because voltage is not a good indication of the charge on the lithium-ion batteries, Lambe explained.
After starting the right engine, Lambe showed me the QPM. Fuel flow was 118 pph with power at 19.7 N1; this contrasts with the normal idle of 25.1 N1 and 146 pph. There is a noticeable difference in noise in QPM, and it is much quieter than idle power. With flaps set to 8 degrees, V1 was 96 knots and rotation speed 97 knots. The PC-24 automatically compensates for configuration changes, so I could see the trim adjust as the flaps extended.
Taxiing the PC-24 in tight spots is easier with the free castoring mode, which is engaged by pushing the inboard rudder pedal and brake and adding power to the outboard engine. It’s important, however, to keep moving when transitioning out of free castoring, then apply opposite rudder, brake, and power to get back to direct steering mode.
We selected the initial altitude of 8,000 feet and checked the FMS speed setting. The final step was to push the takeoff/ go-around button on the left throttle.
After lining up on KBJC’s Runway 30L, I advanced the throttles. Lambe had advised me to give the yoke a fairly strong pull at rotation speed, and when I did, the PC-24 lifted promptly off the runway. After retracting the landing gear and flaps, I followed the flight director’s guidance and turned to the north while climbing to avoid terrain to the west.
After briefly leveling off at 8,000 feet, we continued climbing with the autopilot on, eventually leveling o ff at the PC-24’s maximum altitude of FL450 where cabin
altitude was 8,000 feet. During the climb, we watched the RDR 7000 weather radar automatically scan for weather forward and to the side and display some buildups that were forming.
Level at FL450, I kept the power set to max continuous, and the PC-24 accelerated toward the Mach .73 Mmo barber pole on the airspeed tape. At the speed limit, the auto speed protection (ASP) system kicked on and instructed the autothrottles to reduce power to prevent overspeeding. ASP will also help prevent low-speed problems by adding power, and it works whether or not the autothrottles are switched on.
I flew two sets of left then right steep turns, and the PC-24 pirouetted smoothly with zero buffet at that high altitude. I did have to add a good dose of back pressure to stay level in the turns. Lambe showed me the PC-24’s bank limit protection feature, which adds a tactile feedback force to lateral control when the bank angle approaches or exceeds 51 degrees at low roll rates or 49 degrees at high rates of roll, pushing the
angle back to 31 degrees before deactivating. If ASP is active, bank limit protection is 20 degrees lower, activating at 31 degrees and deactivating at 11 degrees. The tactile feedback can be overridden using the touch control steering button on the yoke.
At ISA +5 and with autothrottles and autopilot on, the PC-24 settled at Mach .719 and a true airspeed of 416 knots burning a total of 924 pph.
Descending toward Telluride, we set up a VNAV-direct to Cones VOR for the RNAV Y approach to Runway 09. The moving map and vertical situation display clearly depicted the high terrain around the airport as we crossed the VOR at 13,000 feet and followed the 3.69-degree glide path from the final approach fix. The synthetic vision showed the runway centerline extending from the runway outline well before we could see the runway perched on a mesa visually, and the autothrottles smoothly followed the speed schedule down to 135 knots as we crossed the final approach fix to 105 knots on the glide path then to the 94-knot Vref as we neared the runway.
I switched off the autopilot but kept the autothrottles on until short final, then eased the power off as the PC-24 floated over the numbers for a smooth touchdown. Lambe recommended maximum braking, and the PC-24 stopped with 3,500 feet of runway remaining. The multi-purpose spoilers deployed in their scheduled sequence for lift dump; to retract them I moved the throttles out of the idle position.
We added more fuel, and weight for this leg was 16,173 pounds, about 500 pounds more than the previous flight. On the way back to KBJC, we paid a visit to Colorado Springs (KCOS) for some touch-and-goes.
Terrain dictates taking off to the west on Telluride’s Runway 27 and climbing to cross Cones VOR before turning east. The PC-24 easily outpaced the terrain after
takeoff, then we climbed to FL330.
While descending, I tried out the airbrakes by switching off the autothrottles and reducing power to idle. With airbrakes at the half position, I could feel no rumble, and at full there was an almost imperceptible vibration. The airbrakes retracted automatically when I pushed the power levers back to max continuous power.
Lambe wanted to demonstrate a single-engine go-around, so we continued south to Pueblo, Colorado (KPUB) and flew the RNAV Runway 17 approach. As we neared the airport, he set the flaps to 15 degrees, lowered the landing gear, and retarded the right power lever. I could feel the automatic trim adjusting the rudder to compensate for the thrust differential.
After the go-around, he demonstrated a slow-speed recovery, allowing the airspeed to bleed off until the autothrottle engaged to add power as the PC-24 slowed to 112 knots.
Back to normal, we proceeded to KCOS and Runway 17, where winds were gusting to 17 knots and a rainshower slowly passed over the airport. We slowed down to line up with other traffic that was waiting for the rainshower to move on, then did another single-engine go-around, this time with the left engine at idle. The autothrottle smoothly advanced the power on
the right engine as the PC-24 overflew the airport.
I enjoyed some good gusty wind practice during two touch-and-goes at KCOS; the PC-24 handled precisely in the squirrely conditions, and touching down smoothly proved no problem. We used just 15 degrees of flaps to make the touch-andgoes simpler and safer.
Returning to KBJC, the passengers had to endure some bouncing around as we stayed low and maneuvered between the Rocky Mountains and rain showers. The wind was blowing straight along Runway 30L and gusting to 33 knots. With full flaps, on short final it looked like the PC-24 was pointing down steeply and the nosewheel would hit first, but that wasn’t the case.
I just had to give the yoke a small tug to pull the nose up slightly as we neared the runway, and the PC-24 touched gently on the main wheels and then the nosewheel. Thanks to the strong wind and the spoilers, I hardly had to use any braking.
The PC-24 was one of the few jets I had never flown, and I’m glad I waited so I could see the new features and get a better perspective on how it compares to the competition. It’s no surprise that Pilatus Aircraft has sold so many PC-24s, and if ordering one today, a buyer would have to wait about two years for delivery. z
BY AMY WILDER
Virtual twins enable more e cient product development, manufacturing, and maintenance processes.
Dassault Systèmes is forging ahead with a virtual twin technology that it believes can transform how aircraft are designed, manufactured, and maintained. Through virtual twins—digital replicas of physical objects, environments, or systems—engineers can simulate, test, and optimize aircraft using data points before physically making them. Known for 3D and product life cycle management design, Dassault Systèmes can create a digital model that simulates an aircraft’s real-world behavior and forces of flight. This digital counterpart can replicate an aircraft’s structural components and aerodynamic performance. Dassault
can also create twins of manufacturing facilities to head off potential production issues before any physical materials are committed to a build.
The U.S. Air Force, through its “ECreate Before You Aviate” initiative, is challenging aircraft manufacturers to prove the capabilities of new aircraft designs through simulations and digital models before physically building and flying them. This marks a shift where private companies and government agencies prioritize “proof-ofconcept” testing upfront.
“We are really [developing models] across the board from commercial aviation to space to defense to supply chains and airlines,” said David Ziegler, v-p of aerospace and defense at Dassault Systèmes. “And the challenges are a little bit different, whether you focus on the defense world or whether you focus on commercialization. In defense, the name of the game is to ramp up production and to manage the growing complexity of the products. You’ve seen the shift and the transfer from fighter aircraft with platform to platforms and systems to systems, it’s more and more complex. It’s how to manage that
complexity while, at the same time, [managing] the production and distribution.
“There is another paradigm shift in the short term: How do I increase my production and my supply chain? How do I manage my supply chain and the supply chain issues the world needs because everybody wants to travel? And at the same time, how do I manage decarbonization, which is something absolutely not related to defense?”
Virtual and digital twins have been used for decades to answer such questions and have been called by various names. NASA used a form of this modeling during the Apollo missions, but the concept wasn’t named as such until the late ’90s— initially in reference to infrastructure and urban planning.
In healthcare, virtual twins of human organs aid medical research, drug development, and treatment plans. Digital twins in the automotive industry simulate driving conditions, optimize vehicle performance, and develop autonomous driving systems.
DAVID ZIEGLER V-P OF AEROSPACE AND DEFENSE AT DASSAULT SYSTÈMES
... if we want to transition to net-zero, it’s not building an aircraft, but building an aircraft that will consume much less fuel, or that is going to be transitioning to a new form of energy ...
In aviation, manufacturers can improve airframe designs and fuel efficiency and anticipate maintenance needs by replicating an aircraft’s performance under various stressors.
“The first advantage is to be able to move faster and to design, test, and find the most appropriate technology,” Ziegler said. “Because if we want to transition to netzero, it’s not building an aircraft, but building an aircraft that will consume much less fuel or that is going to be transitioning to a new form of energy. For this, we need new types of materials—more advanced composites. We need new types of flight
controls [and] new shapes of aircraft. So there is a lot of new technology that we need to embed.”
Dassault has developed what it calls the “3DExperience” platform to integrate data from various sources, including CAD models, simulation results, and real-world sensor data.
This platform (and others like it) generates highly accurate digital replicas and allows for prototyping without using finite resources. It also speeds up the process as the timeline between ideation and testing shortens in the digital world. The company’s goal is to create a seamless “digital thread” throughout an aircraft’s life cycle that allows designers, engineers, and operators to collaborate and make datadriven decisions.
Virtual twins contribute to safer and more reliable aircraft by identifying potential risks and failures before they emerge in physical reality, Dassault believes. As technology advances, the potential applications of digital twin technology are expanding.
Dassault envisions a future where virtual and physical worlds converge. Using artificial intelligence, machine learning, and the Internet of Things, businesses can create intelligent, self-optimizing products and systems—and potentially save significant funds in the development, manufacturing, and maintenance of aircraft, which is important as the demand for sustainability increases. z
BY MATT THURBER
Tony Kern, for 28 years the influential speaker on the first day of Bombardier Safety Standdown and founding partner and CEO of Convergent Performance, challenged this year’s Standdown audience on the event theme of “Elevate Your Influence.”
“I want you to think about reversing this theme a little bit and ask yourself, what influences you? Who influences you?”
Tying together the influence theme and how business aviation professionals can help each other with safety issues related to preparedness, Kern illustrated his points with Venn diagrams showing the intersection between unexpected events and lack of vigilance, complacency, and apathy.
“There’s a lot of shade in that Venn diagram,” he said. “What if we could replace that? What if we could influence ourselves? What if we could influence others and replace that apathy and complacency?
No one is apathetic or complacent overall; it goes up and down. Sometimes we’re apathetic, sometimes we’re bored, sometimes we’re complacent, and other times we’re hypervigilant.”
What Kern was trying to point out is that bolstering vigilance can help prevent accidents or prepare pilots to handle the unexpected, “moving that spectrum a little bit and recognizing when we begin to drift. Now we get that unexpected event, but it’s not so unexpected. [Shift] to we’ve touched the switches [with our eyes closed], we know where the [emergency] door handle is, and we can keep [accidents or issues] at bay.”
An important factor to understand, Kern emphasized, “is that the risk is not where you think it is.” He illustrated this point by
showing videos of heroic sports plays—for example, New York Mets baseball infielder Luis Guillorme’s famous midair catch of a bat inadvertently let loose by the batter.
Risk in aviation is primarily due to the human factor, whether it’s pilots, mechanics, or engineers. Yet, he added, “Not only is aviation incredibly safe, but we are.” We must avoid lying to ourselves about safety and assuming that just because we say aviation is safe, no more work needs to be done.
“We have to understand that there are accidents lurking inside of us, waiting for
the holes in the Swiss cheese to line up to where we’re the last piece that can prevent it,” Kern said. “We have to understand it can happen to us, and to some extent, we have to believe that it will happen to us. We have to attack this idea of how incredibly safe aviation is inside our own noggins.”
But if that’s the case, little useful learning is happening. “There’s so much we can learn from every single flight, every single pre-brief and debrief, everything, and we have to [do that],” he said.
“One of the things that influences us is this idea that we’re pretty good, right?
Which is good, confidence is good. But we are never good enough. Are you tough enough to take a hit, professionally, personally, physically, and keep moving? Are you tough enough to not let your feelings get in the way when you don’t get a job or somebody gets promoted ahead of you, or something else happens in your organization or your life? Are you tough enough to realize what I just said is true, that you can never be prepared enough because you don’t know what level the challenge is at? And have the courage to offer constructive, honest, objective criticism to others, but also when you look in the mirror?”
This was Kern’s “most important lesson” of the day: “Things that have never happened before to you or to people happen all the time. These black swan events that we never think can happen to us—that the odds are astronomical, won’t happen to us—they happen all the time to somebody, and we have to be able to evaluate this concept.
“We get our type ratings, we go through training, we meet the minimum standards, and we fly for thousands of hours and years, and nothing bad happens...We begin to get this idea that we’re good enough. Every once in a while, something like this comes up that reminds us we might not be, and things can turn in a minute. I don’t know how many of you ever had a serious emergency. When you do, you’re going to realize that your brain doesn’t work the same, but when you’ve got something to fall back on…I trained with fog goggles. I know where the switches are. I know where the hatch is. I’m going to survive this. You’ve got somewhere to go.”
What this means is being prepared, he explained. “Preparation is getting ready for something you may or may not ever encounter, and then you’ve
got to couple that with the state of mind that says it could happen right now. So preparation, plus that vigilance that says I’m going to be here now, I’m ready for it, equals some level of what I want to call readiness. But the most important thing to understand is that readiness can only be determined after the challenge arises, and it may or may not be the one that we train for in the simulator. It may not be the one that has happened enough times to create a trend in our safety management systems. It may be something completely odd and strange, so the best thing we can do is to constantly look at the levels of preparedness that we have.
of being abnormally alert. To Kern, hypervigilance means being “normally alert for abnormal things to occur.”
...These black swan events that we never think can happen to us—that the odds are astronomical, won’t happen to us—they happen all the time to somebody, and we have to be able to evaluate this concept...
— Tony Kern CEO, Convergent Performance
“And there’s a lot of elements to that. It’s aircraft knowledge and systems knowledge. It’s empathy with your team, being able to understand the tone of voice, whether that air traffic controller is getting stressed out and might do something silly. All of those things come to play into our level of preparedness.”
There is more to this, however, and Kern believes not just in vigilance but hypervigilance. He doesn’t agree with the Merriam-Webster Dictionary definition: the state
The seemingly normal act of aviating remains inherently risky. “Our field of play has always been dangerous,” he said, “even when we’re sitting around hangars and flying airplanes. Never forget what an airplane is. It’s an aluminum eggshell that has highly combustible materials in it with all kinds of kinetic energy and fire happening right beside us, right underneath us, and we take it up to altitudes where the time of useful consciousness can be measured in seconds. We navigate around thunderstorms, where lightning is as hot as the surface of the sun. And then we come down, we land on little, tiny strips of concrete, and we call it normal. Yeah, that’s not normal. That’s a high-risk environment.” Kern asked, “So how do we get this hypervigilance?” People who exhibit this trait “see deeper, and they’re able to attach meaning to the things that they see. That’s a conscious process. It’s not going to be intuitive when you see something new that you’re going to figure out how to process what to do with it. That requires you to think. That’s a conscious act of diving deeper.
“We can always learn. We can always get better. What prevents us is the expert’s curse of reading the press clippings that say we’re safe enough or resting on our laurels because we’re really good at what we do. You don’t self-select to a safety conference unless you care about getting better. So I know I’m kind of preaching to the choir here, but can you take that same exuberance for learning, applying, and sharing back and demonstrate it for others? Expert readiness doesn’t happen by accident. You’ve got to have this burning desire to get better.” z
NTSB board member Michael Graham addressed attendees of Bombardier’s 28th Safety Standdown on how influence shapes safety and what we can learn from recent close calls. His presentation, “Impacts of Influence,” examined the ways people can influence aviation culture in sometimes surprising ways. To make his point, he delved into two case studies of runway incursions, at New York’s John F. Kennedy International Airport and in Austin, Texas, over the past two years.
Graham, referencing the overarching Safety Standdown theme of “Elevate Your Influence,” opened by reflecting on the pervasive influence of advertising, government, and social media on buying habits and behaviors. He noted that sometimes simple actions can have a significant influence, which could be either positive or negative.
He played a 90-second 2012 Dollar Shave Club ad, which he said cost about $4,500 to produce and load to YouTube,
BY AMY WILDER
and led to a 12,000-person membership increase within two days. “Four years later…they sold the company for $1 billion,” Graham said. “Do you think that when he posted that, he thought it was going to have that much influence? Sometimes it’s the real simple things that make a big difference out there.”
Growing up in Albuquerque, New Mexico, Graham was inspired to become an aviator by watching airplanes flying over his home. His parents and teachers helped shape his values and career aspirations. A commanding officer in his first fleet squadron impacted his leadership and career development. Graham drew a line from these critical early influences to the importance of developing younger, inexperienced members of the aviation community and stressed the importance of setting a good example, even when not being watched.
“I think it’s really important that the most influential people in my life are
“You’ve always got to be vigilant out there,” cautioned NTSB Member Michael Graham.
probably not even aware of the things they’ve taught me,” he said. “And each one of you can be that out there. I’m going to try to influence you today.
“I hope you read our accident reports like I did, and learn from them, and apply the lessons learned there, because that’s the most important stuff. It’s not what happened, but understanding how and why, so we can prevent future accidents like that from happening again. I’m going to talk to you about a couple of near misses here— and the FAA would call them ‘close calls.’”
Looking at the history of runway incursions, Graham noted that audience members might look at statistics and see a steady state with no recent fatalities domestically. “That doesn’t mean that the potential is not there,” he cautioned.
Recent data shows an uptick in runway incursions, particularly in Alpha and Bravo airports. “We actually have 11 incursions that we’re investigating right now,” Graham said.
He outlined a runway incursion incident at JFK Airport that occurred nearly two years ago, which was impacted by pilot task saturation, changed clearances, and lack of standard operating procedures (SOPs) for verifying which runway the crew was crossing after being cleared to cross. Action by ATC alerted one of the crews to abort its takeoff in time to avoid a collision.
“One of the things that we recommended out of this was for [Part] 91K, 135, and 121 operators that you incorporate into your SOP, a better procedural cross-check if you don’t have this already, by verbalizing the runway that you’re crossing, so others can
be tied in, especially if they’re doing other tasks at the time, and that should be based on runway signs,” Graham said. “Now, I know some of you have the technology out there that tells you where you’re at, so use that. You’ve always got to be vigilant out there.”
The NTSB has also asked that airlines investigate their data to look for surface navigational errors caused by crew performing other tasks at the time, and if so, to work to mitigate it. In addition, “For 24 years now, since 2000, there are two things we’ve been asking for: surface detection equipment in the towers and detection equipment in the cockpit that will visually and orally alert flight crews of traffic on the runway or taxiway, approaching to land, or taking off,” Graham said.
He went on to detail an incident between a Southwest Airlines Boeing 737 and a FedEx Boeing 767 in Austin, Texas. The Southwest airplane was given takeoff clearance while on the taxiway and advised of another aircraft on approach; it subsequently taxied onto the runway and then paused for an engine run-up, reducing
Now, I know some of you have the technology out there that tells you where you’re at, so use that. You’ve always got to be vigilant out there.
— Michael Graham NTSB board member
separation with the approaching FedEx airplane. There were low-visibility conditions, and the air traffic controller could not see aircraft from the tower, on the surface, or on approach. The FedEx airplane, on a low-visibility approach, called for a missed approach just in time.
The incident highlights the importance of pilots informing ATC of additional time needed on the runway for runups or similar procedures—particularly in conditions in which the tower has no visual contact with
aircraft. Graham reiterated the call for the installation of surface detection equipment and said the CVR recording had been lost due to the two-hour recording limit. He also emphasized there is a continued need for vigilance among aviation professionals and clear communication between pilots and ATC.
“Anybody who’s heard me speak in the last couple of years, or anybody from the NTSB for that case, is probably aware that we were really hounding the FAA on requiring 25-hour CVRs,” Graham said. “In 2023, all the incursions that we investigated out of all that, and the one collision we had down at Houston Hobby between the Hawker and the Citation Mustang— you know how many CVR readouts we got from all those? Zero. We got zero.
“The two-hour CVR is old and dated. There’s no reason why we can’t have 25-hour CVRs. They’re doing them in Europe on new aircraft. Congress got involved with the reauthorization of the FAA and said, ‘Hey, FAA, guess what, you’re required now to have these within one year on new aircraft and within six years retrofitted.’ So hopefully that will help.” z
Contract pilot Kevin Van Splunder took the Bombardier Safety Standdown stage to share his experience during an extremely hard landing and subsequent fire in a Cessna Citation X+ on August 5 in Jamestown, New York.
Details about what caused the failures in the airplane aren’t yet available, but Van Splunder said of the experience of the short seven-minute flight: “I’ve learned, I’ve applied—and you’ll understand why—and now I’m here to share it,” he told the audience.
BY MATT THURBER
Climbing through 5,000 feet, he smelled smoke and pointed that out to the captain, who said he didn’t smell the smoke. But Van Splunder commented, “Well, that’s interesting, maybe we should do something.”
At 10,000 feet, the jet began to level off and accelerate, and then it started descending, uncommanded. “All of a sudden, we saw ourselves in a descent at 494 knots and 6,700 feet per minute. It’s about 73 seconds to impact.”
As a young pilot, he recalled the training he received from “old codgers” who taught him to close his eyes and learn how to touch every switch in the cockpit. “Know what the different switches feel like,” he said. “We don’t get that information from CAE and FlightSafety, as much as I think we need it. You need to do that in the aircraft.”
In a previous job as director of operations, Van Splunder brought that training to his fellow pilots. He would have them
wear smoke goggles covered by duct tape and put them in a dark cockpit, then simulate an emergency landing. “Go ahead and get out, open up the emergency exit door in your hangar. Have your chief pilots and your safety personnel set up a day that you can get in the plane and you can open up that door and make sure that you can do it without sight.”
Returning to the ill-fated flight, he remembered a strong feeling of confidence that he knew that he would be walking away from the “really bad landing.” At 10,000 feet, he said, “the stabilizer trim ran full nose down to keep us accelerating, and then everything started to fail. The autopilot failed. The primary stab trim failed. I knew the checklist without even having to pull it out. I activated the secondary stab trim, and that also failed.
“Now with all the other CAS [crew alerting system] messages that were on the CAS list, we didn’t have any time to pull out checklists and start reading and seeing what the systems were [doing]. It’s the knowledge that you learn that you have to apply. What are you going to do? What speed do you have to be at? The only way we could stop our descent was to continue our accelerated speed.”
One of the first captains that Van Splunder flew with “was adamant to always have 121.5 [the emergency frequency] on your second comm [radio],” he said. “That’s what saved us. I was able to talk to the air tra!c controller. They told us where the airport was because we had smoke in the cockpit. And even though oxygen masks can be worn, you’re not going to see much past that.”
The Citation impacted the ground 200 feet before the runway threshold and bounced into the air, then onto the runway before sliding onto the grass, bouncing back into the air and spinning around, and finally coming to a stop in a total of just 2,020 feet.
“We didn’t have much time,” he said, “and if I was in that cabin probably 10 seconds longer, we wouldn’t be here. I knew I had to get out. We both agreed I was the first to exit because of my training: I knew exactly how many feet, how many steps it was going to take for me to get to the emergency exit door.
“When I passed the main entrance door, it was so engulfed in flames that I couldn’t even reach to get the handle. I made it back to the emergency exit door and ripped it out. I can’t tell you that I lifted the thing and released the cover and pulled the
handle up like they tell you to do nice and easy, because, trust me, you’re not thinking nice and easy. I ripped it out of the wall, threw it outside, and then I looked down.
“The wing had separated from the fuselage, and fuel was boiling out like it was lava. I yelled back to the captain and said, ‘We’re not going out this way!’ At that point, he came back to me and said, ‘The main door is open.’ I came down like a freight train. He’s a lot bigger than I, and I almost ran straight over the top of him, but we got out of the airplane. I had a few burns and a few cuts. He unfortunately suffered some second-degree burns and some fractured vertebrae. But we’re both doing well, and we’re both flying.
“But I go back and say that [it’s] because of the training I had from the old people. I can tell you that when I was younger, [I thought] I don’t need to know that, it’s never going to happen. Well, guess what?
It happened. And I was able to, without thought, apply that, and with that application of my knowledge, I was able to get out of the aircraft, get the captain out of the aircraft, and we walked away.
“I at no point thought that I wasn’t going to make it. I knew I was going to walk away,” he concluded. z
A Part 135 operator case study serves as a cautionary “could have gone terribly wrong” tale for aircraft operators to develop better internal communications, documentation, and operating procedures, Aviation Safety Solutions CEO Amanda Ferraro said at Bombardier’s Safety Standdown during her “Into the Danger Zone” presentation.
Kenny Loggins’ “Danger Zone” played during a drone light show and faded as Ferraro took the stage. “We all love the song,” she said. “I don’t know what pilot, what aviator, what mechanic doesn’t like that song. But when it comes to safety, the danger zone is a place that we don’t want to be.”
Ferraro pointed to the close call illustrated in a Part 135 operator/aircraft management case study and lessons that could be gleaned from the experience.
The unnamed operator failed to document in writing a maintenance light issue on a smoke detector system for an airplane newly managed by the company, leading to eight subsequent flights with inoperative equipment.
The maintenance team determined that the smoke detector was operative, but the maintenance light continued to light up, which made it difficult for flight crews to determine if there was or was not an immediate problem. There was no minimum equipment list (MEL) approved for the aircraft to defer the maintenance temporarily. Multiple flight crews at the company flew the airplane with the maintenance light illuminated.
Ferraro was called in to help investigate the issue when FAA scrutiny heated up. “When we got on the call with the
BY AMY WILDER
FAA, who do you think they were holding responsible for this event?” she asked the audience. “The PIC, the pilot in command, is responsible to ensure the airworthiness of the aircraft, is he not or she not? So, the FAA was squarely looking down the railroad track at the pilot in command, and they wanted answers. They said, ‘You guys have an SMS [safety management system], don’t you?’ And the operator goes, ‘Well, yeah, we have an SMS.’ ‘We want a full-fledged investigation. In this event, we want this completely run through the SMS, and we want you to report back a full investigation report to us.’
“I helped them through this process, but…I think the most interesting part of the story, in talking to the pilot in command…this individual didn’t want to take any responsibility...and didn’t believe that he did anything wrong...and placed the blame on the maintenance vendor.”
The FAA interviewed the maintenance vendor, flight crew, chief inspector,
contractor, and chief pilot of the operating certificate. The maintenance vendor indicated that the crew had a habit of dropping off airplanes without providing written documentation of discrepancies.
The investigation further revealed systemic issues, including a culture of verbal reports of discrepancies and a lack of proper documentation. Rather than take a punitive approach, the agency asked the operator to update its training and policies to prevent similar situations in the future. Mitigations included strengthening MEL training, updating procedures, and ensuring written discrepancies. The case underscored the importance of SMS and continuous improvement, and the operator began using it for annual training.
As for the PIC, Ferraro said, “The accountability executive decided to...provide counseling...in a strict manner and remedial training, and ensure that it was very clear that” the company’s expectations included adhering to its SOPs. z
Let the Good Times Fly… Navigating Tomorrow, Today! The 2025 NBAA Schedulers & Dispatchers Conference (SDC2025) is where your journey towards success takes flight. Elevate your logistical planning and explore the latest in dispatch technologies and innovative equipment designed to propel your flight department operations to new heights. In the spirit of New Orleans, where timeless charm meets innovation, start planning today to ensure you’re part of this exceptional event you won’t want to miss!
Icing’s specter looms over a wide swath of our flying lives. During the winter, we’re particularly attuned to its presence, but those conditions that constitute “icing” can occur any time of year, no matter where we fly.
As a pilot, you’re tasked to know when icing conditions are likely to exist, and whether your airplane has the approval and equipment to enter those known icing conditions. The certainty implied by the term “known” eludes most of us, however. Still, the burden is on those operating under Part 91 to weigh the risk as well as any airframe limitations on launching a flight into these conditions. If you fly under Part 135, Part 91 Subpart K, or other approval regimes, you’ll reference your operations specifications for guidance on what makes for a “no go” in times of known icing.
However, nailing down the FAA on what constitutes “known icing” is a bit, well, slippery. David St. George, executive director of the Society of Aviation and Flight Educators and an active corporate pilot, summed it up: “If the composite information indicates to a reasonable and prudent pilot that he or she will encounter visible moisture at freezing or near-freezing temperatures and that ice will adhere to the aircraft along the proposed route and altitude of flight, then known icing conditions likely exist.”
You can expect icing when flying in visible moisture—that’s rain, snow, fog, or clouds—if the temperature of the airframe is below freezing. True, not every “cold cloud” produces ice of significance on the airplane. But to launch up into them without due regard runs you afoul of FAR 91.13, with a “careless and reckless operations” charge possible if anything happens.
Fortunately, technologies have evolved in both anti- and de-icing equipment, and they’re now available on a broad range of business aircraft, including turboprops
BY JULIE BOATMAN AIN CONTRIBUTING WRITER
and the single-engine Cirrus Vision Jet. For engines that produce enough hot bleed air, thermal anti- and de-icing systems are the gold standard, providing the ability in some installations to heat the accumulation to an evaporation point, preventing run-back.
Electro-thermal anti-ice systems use a graphite foil electrically heated to prevent leading-edge buildup. Electro-mechanical expusition de-icing system break ice off and are frequently found on horizontal stabilizers. Inflatable rubber “boots,” found on most turboprops and some jets, work only after accumulation has begun. Weeping wing systems, such as TKS, use perforated distribution foils to seep antifreeze fluid onto the leading edges in flight they have brought flight into known icing (FIKI) to single-engine airplanes.
Though there are light icing conditions that may lull us into thinking they are benign, any icing can degrade performance. You never know when you might need that percentage of capability in flight, on takeoff, during landing, or when going around. Even in aircraft certificated for FIKI, it is nearly impossible—and you cannot presume—that the test aircraft encountered all types of icing in its program for certification. These unexplored realms
may include: freezing rain, freezing drizzle, mixed conditions combining rime and clear ice, and any conditions termed “severe.” In these regimes, you put yourself in the role of test pilot.
A proper preflight includes understanding the current icing levels, both reported and forecast. Once in it, you should look at one of two ways to exit the icing:
a. Get out of the area of visible moisture laterally.
b. Get to an altitude where the temperature is above freezing. The warmer altitude is not always the one below you, particularly in the event of a temperature inversion.
Report icing to ATC and request a new route or altitude as needed, without hesitation. Keep in mind the axiom: “Change altitude, change course, or continue into the clear.”
While few of us call an actual briefer these days, the depth of the self-brief—taking advantage of the astounding visual and data-rich tools available with a briefing query via ForeFlight or another planner— has outstripped most concerns about its thoroughness. This is one area where the technology has evolved tremendously, yet it still relies upon reporting to validate complex models.
Yes, an IFR brief when icing is in the picture is only as good as the reporting. You can click on visual representations of pilot reports—as long as the pilots are already up there making them. If you can, give a quick update to ATC and do your fellow pilots on the ground a solid. Your position report turns into a dot on the map laid next to a course line—and that is gold.
Check the Aviation Winter Weather Dashboard (https://aviationweather.gov/ winterboard) for a wide-scale assessment. Convective forecast products for areas of convection—and thus, icing—run throughout the winter months.
If you’re in a hold and ice begins to accrete beyond a touch of light rime, understand that everyone stacked up with you is probably experiencing the same— albeit at different rates at different altitudes and positions on the approach. If the accumulation gives you pause, look at diversion promptly, especially if the conga line ahead of you extends beyond an airplane or two. If there’s widespread icing potential around a major terminal area, consider delaying the flight for better conditions if you can. Unless you have a rocksolid plan B, C, and D.
And that’s the key. Corporate pilot Wayman Luy has ferried many single-engine turboprops across the North Atlantic—and he remains cautious regarding ice. He points to a recent trip he took repositioning a Daher TBM 960 from Buffalo, New York (KBUF), to Fort Lauderdale, Florida (KFLL), as an exercise in flight planning and preflight risk mitigation. “Looking at the route on ForeFlight, I stay away from forecast moderate conditions and pick a route around that ice.” Be flexible with your departure schedule to mitigate. And be ready to fly the airlines. “I
sit it out,” he said. “If you need to de-ice, it’s the wrong decision to go” in light business aircraft. If he finds himself in it unexpectedly, he has a couple of tips. “Keep your speed up,” he said. “And I like to warm up the propeller and windshield early on.”
That reminds me of an adage I learned flying around with a former colleague from the Aircraft Owners and Pilots Association. When I asked about turning on the pitot heat on the Beech A36 Bonanza we were flying as we were about to depart into the soup—on a summer day—he answered: “Use it. All the time. It’s free.”
The hazard induced by not having the pitot tube warmed up before encountering any ice outweighs any possible cost of drawing those amps or wearing out the heating element.
Another part of your preflight brief includes conditions at the departure, destination, and alternate airports. As part of the FAA’s Takeoff and Landing Performance Assessment initiative, airports began using the current Runway Assessment and Condition Reporting system in October 2016, which assigns values to both coverage and braking action of runway and taxiway surfaces.
The Field Conditions Notices to Air Missions outlines the reported information, to help mitigate the need to call the airport directly for conditions.
A cold-soaked airplane needs careful consideration and handling, and this includes the wings, nacelles/inlets, empennage, braking and landing gear systems, and other protrusions on the exterior. Interior fittings, appliances (the lav), and avionics can also lose utility in cold weather, and the total airplane must be safely brought up to operating temperatures before passengers arrive. Remove fluids that can freeze from the cabin and water system—and also any cold-sensitive items from onboard medical kits—after you arrive to mitigate this hazard. Also, be prepared in case of holding time or overnight snowfall that it doesn’t induce enough weight on the empennage or horizontal tail surfaces to put the aircraft on its tail.
The pilot and crew must observe icing holdover times to ensure that deicing and anti-icing procedures and fluid application have the desired effect. The FAA publishes Holdover Tables for each winter season based on what’s available. Type I and Type 4 are the most common deicing and antiicing fluids available.
Common mistakes of pilots? Not recognizing that slowing airspeed is a key indicator of ice accumulation. Not getting out quickly enough. And not removing completely any frost or ice accumulation before departure. According to the AOPA Air Safety Institute, nearly one-quarter of icing accidents were caused by failure to ensure clean surfaces before takeoff—and two-thirds of all fatal icing accidents are the result of ice buildup in flight. Ice is deadly either way.
My sense has been that if you grow too confident in your jousts with ice, it will find a way to smack you and shellack you— on the wings, stabs, filters, and probes. z
The opinions expressed in this column are those of the author and not necessarily endorsed by AIN Media Group.
BY CHARLES ALCOCK
Vertiport Simulations is adding its design for vertiports to flight simulation software to provide realistic scenery for eVTOL aircraft operations.
Flight simulators developed by the gaming industry are set to play a role in training the large numbers of pilots needed to fly new eVTOL aircraft. What’s more, software like the latest versions of Microsoft’s Flight Simulator and Laminar Research’s X-Plane are also being deployed by companies developing the broader advanced air mobility (AAM) ecosystem, including vertiports.
Florida-based Vertiport Simulations was established earlier this year to design heliports and vertiports. It soon found it could expedite changes and client approval by giving clients the opportunity to preview designs through virtual reality.
This capability prompted the company to offer imagery of eVTOL aircraft ground infrastructure to serve as scenery in the newly released 2024 edition of Flight Simulator and X-Plane 12. Its designers are adding key details, such as the electric charging units developed by eVTOL aircraft manufacturer Beta Technologies and Electro.Aero.
One of Vertiport Simulations’ first clients is Helo Holdings, Inc. (HHI), which is redeveloping its New Jersey heliport at Kearny, close to Manhattan, for use by eVTOL companies, including Joby Aviation. HHI has plans to develop another vertiport at an undisclosed U.S. location. Vertiport Simulations, founded by AAM entrepreneur Joe Mattern, is also working with a heliport operator in Dubai.
Mattern told AIN that regulators still have plenty of work ahead of them to finalize standards for AAM infrastructure such as vertiports. “[Regulation of] aircraft is ahead of infrastructure, and the industry needs common standards,” he commented.
Meanwhile, the professional edition of X-Plane is set to be among the options for an eVTOL industry facing the challenge of needing to recruit and train thousands
of new pilots. Though originally developed for hobbyists, X-Plane 12 is already FAA-certified for some use in flight training. Mattern said he hopes this will be extended to cover eVTOL aircraft, too.
Beta Technologies confirmed that its engineers had used X-Plane to conduct some initial physics validations for its Alia aircraft, which was the first eVTOL aircraft to be featured on the platform. Founder and CEO Kyle Clark also used it to learn how to fly the aircraft.
The new version of Microsoft Flight Simulator already features the fourpassenger eVTOL aircraft being developed by Joby and its competitor Archer Aviation. X-Plane 12 includes Beta’s Alia aircraft and Cirrus used the software to develop its SR20, SR22, and Vision Jet aircraft. z
This article is courtesy of AIN Media Group’s FutureFlight. To read more, please visit ainonline.com/futureflight.
Colorado’s Pitkin County has issued final approval for the renewal of Atlantic Aviation as the sole source provider at Aspen/Pitkin County Airport (KASE), capping a process that has lasted more than a year and a half since the FBO megachain was selected as the winner of the airport’s RFP process.
During that span, there was heated discussion from the local community about what direction the airport should take, but the matter was settled after the conclusion of a public comment period on the decision and a final vote by the county board of commissioners.
As a result, Atlantic was awarded a 30-year lease on the FBO with the provision of $136.5 million in capital improvements over that span, in addition to an estimated $880 million in rent, fees, and charges paid to the county, bringing the total commitment of the deal to a projected $1.15 billion. Included among the final lease points was a 25% discount from the fuel retail price for locallybased aircraft operators and those on the waitlist.
Illinois’ Mount Vernon Outland Airport (KMVN) Authority will return to the FBO business for the first time in nearly 20 years after its purchase of SRT Aviation, the lone service provider on the field. On December 1, the facility was renamed SRT Flightline in honor of the last time the airport operated the FBO. Shawn Sayle—the “S” in SRT—will stay on to manage the location’s Part 145 repair station.
The airport authority and the FBO have shared aircraft fueling responsibilities on the field since 2008, with the FBO handling the physical operations. “It’s all about retention and control,” said KMVN director Chris Collins. “The airport operator controls the pricing, pricing drives aircraft
operations, and aircraft operations dictate FAA grant funding.”
The Titan Fuels-branded, CAA-preferred FBO offers 32,000 sq ft of heated hangar space and 10 acres of ramp. It also has a recently renovated 4,100-sq-ft terminal available 24/7 with passenger and pilot lounges, eight-seat conference room, and refreshment bar.
Commercial real estate investment firm SomeraRoad has launched a new investment platform SR Aviation Infrastructure (SRAI) with the purchase of the Quail Air Center complex at Las Vegas Harry Reid International Airport (KLAS).
Established in 1985, the 23-acre facility features 268,000 sq ft of hangar space that can accommodate bizliners and 32,000 sq ft of offices. It acts as a private FBO, providing fueling and ground handling services for hangar-owner tenants.
SomeraRoad sees aviation infrastructure as “one of the most compelling opportunities in real estate today,” fueled by the increase in private air travel and limited new airport development, particularly in the general aviation sector.
Clay Lacy Aviation has broken ground on its $100 million FBO complex at California’s John Wayne Airport (KSNA) in Orange County. The Los Angeles-based service provider was awarded a 35-year lease on the field in 2020 as part of the airport’s general aviation restructuring plan.
The 14-acre facility will offer 41,800 sq ft of passenger terminal and office space, along with four hangars totaling 145,000 sq ft of space and 6.7 acres of ramp. It will also feature a purpose-built home for the Orange County Sheriff ’s Department air support unit. Phase One is expected to be operational by mid-2026.
Atlantic Aviation has had a presence at Nashville International Airport (KBNA) since 2007, when it acquired the location as part of the blockbuster 24-FBO purchase of Mercury Air Centers. Earlier this year, it relocated from the 1970s vintage 8,600-sq-ft terminal to a brand-new 12,000-sq-ft terminal, part of a major reconstruction of the chain’s complex.
For general manager Aaron Wood, the old facility had outlived its usefulness. “For the activity that we were seeing at the location, the facilities weren’t big enough,” he told AIN. “It was great for its time, but it was time to make the move.”
To make room for the construction of the new terminal, an old 26,000-sq-ft hangar with a low door height was demolished next door to the existing terminal. This past May, the facility was completed.
“We were conducting business in the old one, and at 7 o’clock the next morning, we flipped the switch and were operating out of the new one,” said Wood. “We ended up leveling the old terminal within weeks after moving into the new terminal.”
That lot was paved over to extend the FBO’s ramp to 12 acres and improve the ramp flow, according to Wood. “The efficiency for our customers and parking on the ramp has just been so much better from a service perspective as well as a safety one.”
The single-level terminal features an airy lobby with a soaring 30-foot-high ceiling and a fireplace, a business center, dishwashing service in the galley, refreshment bar, onsite car rental, pilot lounge with bathroom and shower facilities, and two snooze rooms (or “studios,” as they are locally referred to in Music City). It has a pair of conference rooms, seating 10 and 12 respectively, each equipped with wet bars and built-in refrigerators. At the landside entrance is a large porte cochère to protect arriving customers from the elements.
A unique feature is the facility’s large VIP suite featuring direct ramp access, a wet bar, and ensuite bathrooms and showers. “When we have opportunities to elevate our service for certain groups that would maybe prefer to have a little more private environment, we utilize that space,” said Wood, adding that the suite is used more and more as time goes on. “We’re doing things in that space right now that people probably never envisioned to be done in an FBO in an airport.”
Among the more unusual activities that have taken place there: bridal party fittings. “Nashville is the bachelorette party capital of the world, apparently,” said Wood, “so there’s a lot of women who show up to do things like trying on wedding dresses.”
To replace the hangar that was displaced by the new terminal, Atlantic built the 30,000sq-ft Hangar 19, which can shelter the latest planned ultra-long-range business jets. The hangar was also designed to function as a dedicated charter terminal with its ramp rated to handle aircraft up to a Boeing 757.
It has a 1,500-sq-ft lobby that can accommodate large charter groups such as collegiate and professional sports teams or touring entertainers. Using Hangar 19, they don’t need to visit the terminal and can load directly into buses to depart the FBO.
The complex, with 76,500 sq ft of heated hangar space, is home to 15 turbine-powered business aircraft ranging from a Gulfstream G550 to a Beechcraft King Air C-90. U.S. Customs clearance is available with advance notice on the Atlantic ramp, and the facility can handle international trash disposal.
Another part of the project was the construction of a new fuel farm holding 60,000 gallons of jet-A and 10,000 gallons of avgas. It is served by the facility’s trio of 5,000-gallon jet fuel tankers and a 750-gallon 100LL truck that transmit fuel tickets directly to the CSR desk.
The facility is open 24/7 and has a sta of 30 who have undergone Atlantic’s in-house training. To illustrate his sta 's dedication, Wood noted a recent instance where a passenger landed after a late-night flight. Once they met their ground transportation, they decided to use the terminal restroom and, unaware, left a backpack filled with important documents behind in the lobby.
A CSR noticed it, found identification within, and began contacting the recently arrived flight crew members to find out who flew the passenger in and what hotel they were using. Armed with that information, she then drove the backpack there and hand-delivered it to the hotel concierge. It was reunited with the grateful passenger the following morning. C.E.
Las Vegas-based flight training provider and hangarkeeper All In Aviation has acquired Lone Mountain Aviation, its long-time maintenance provider. Founded in 1982, Lone Mountain is an FAA-approved Part 145 certified repair station and warranty center for Cirrus, Cessna, Piper, Beechcraft, and Epic Aircraft, along with engine makers Williams, Pratt & Whitney Canada, Continental, and Lycoming.
The two companies jointly built a multi-use aviation complex at Henderson Executive Airport (KHND) that debuted in 2020. With the acquisition, All In will gain 23,000 sq ft of aircraft maintenance space at KHND, as well as an 18,000sq-ft repair facility at North Las Vegas Airport (KVGT).
Operators of Sikorsky S-92 helicopters can reduce operating costs and boost availability with longer scheduled inspection intervals introduced by the OEM.
The new intervals extend the intervals for scheduled inspections to 500 hours from 375 hours and 1,000 hours from 750 hours. According to Sikorsky, this will eliminate up to 30 inspections over the 30,000-hour S-92 lifespan, reducing maintenance downtime over that period by a year.
ExecuJet Haite Aviation Services, a China-based franchisee of ExecuJet MRO Services, has completed three simultaneous 96-month inspections on Embraer Legacy 650s at its Binhai International Airport facility in Tianjin.
The work on the trio of super-midsize business jets took place over a four-month span. According to ExecuJet
Haite, the 96-month inspection is the most extensive on the Legacy airframe, requiring more than 3,000 labor hours. It necessitates the complete removal of the aircraft cabin interior, down to the fuselage frame, for structural inspection.
Founded in 2010, ExecuJet Haite also offers base and line maintenance at Beijing Daxing International Airport and has a line station at Beijing Capital International Airport.
Parts manufacturer for legacy aircraft and MRO provider Ontic will expand into Florida with the opening of a new facility early next year. The Miramar location will be a dedicated MRO center of excellence focused on supporting customers of the company’s manufactured parts and systems.
With the opening of the site, Ontic will transfer its North Carolina MRO operations to Florida to allow the expansion of its manufacturing capabilities at the former location.
The company is not planning staff reductions due to the relocation and will offer its maintenance workers in North Carolina the opportunity to move to the Florida facility or transition into manufacturing roles at their current site.
Jets MRO has moved into a 40,000-sq-ft hangar at Dallas Executive Airport (KRBD, formerly Redbird Airport) and simultaneously welcomed its 100th aircraft serviced since launching operations in May.
The new maintenance hangar was developed under a partnership with Jet Access, which in late 2022 broke ground on 60,000 sq ft of additional hangar space with 8,000 sq ft of offices, as well as an 8,000-sq-ft FBO terminal.
While Texas-based Haven Aviation Services Group has been in operation only since 2017, it already has outgrown its city-leased 10,000sq-ft facility at Rick Husband Amarillo International Airport (KAMA). In March, the company moved into its current 40,000-sq-ft location on the field, part of the Signature Aviation FBO.
Haven Aviation focuses on scheduled maintenance for light and midsize business jets and turboprops. “Our specialty lies in the legacy Citations and CJs and some of the more offthe-path jets like Premiers and Beechjets,” said CEO Travis Lamance. “We do a lot of those and then the whole King Air line and anything [Pratt & Whitney Canada] PT6-powered.”
With its sta of 20 technicians, the location usually has around 15 aircraft in the KAMA shop at one time. But with a backlog of scheduled maintenance extending through April, Haven expects to add four more mechanics and move to a second shift by March.
The company holds avionics dealer authorization from Garmin and Collins and is about to secure approval from Honeywell. On the airframe modification side, it holds authorizations from Blackhawk, Raisbeck, and BLR.
As an A&P mechanic himself, Lamance is familiar with the labor perspective and is more sympathetic to them than many other business owners might be. “I’ve structured the company and our values, systems, and processes to be very mechanic-friendly,” he said. “We have very low turnover, and we do that through the company culture and environment that lends itself to them sticking around.”
That background also provides Lamance with a built-in stress reliever. “When o ce life is getting to me, dealing with all the woes of running a business, one of my favorite things to do is to go down on the floor and take on a project and spend a day or two working,” he explained.
This year the company marked its first expansion with the acquisition of Private Jet Maintenance, a service provider at New York’s Bu alo Niagara International Airport (KBUF). While the location is 1,500 miles from Haven’s Amarillo flagship location, that separation is part of the company’s plan to reach new customers, according to Lamance.
“We have a lot of maintenance customers that come in to see us in Amarillo from all over the Midwest and the Western U.S., so [Buffalo] was a good geographic location for us,” he said. “The New York City area is super dense with aircraft, and a fair amount of support network, but it’s increasingly hard to get in with those [maintenance providers], and it’s increasingly expensive.
The Bu alo facility—which just completed its relocation into a 24,000-sq-ft hangar, also part of the Signature complex on the field— possesses an FAA Part 145 repair station certificate. Despite it being smaller than the Amarillo facility, Haven expects to soon have its Texas headquarters location listed as a satellite facility under that Part 145 certificate.
Both locations have AOG repair teams that serve their respective areas. “From our
perspective, as long as they want us to pay for travel time, we’ll go wherever they need us to,” said Lamance.
His staff is dedicated to helping their clients any way they can, as evidenced by one recent situation where an owner-pilot noticed oil leaking from the cowling after landing in Amarillo for a fuel stop on a cross-country flight. Haven’s technicians discovered a leaky prop seal but as the aircraft was not one they typically worked on, they did not have the spare parts on hand.
The distraught pilot explained he was rushing to Nashville where his daughter was about to give birth to his first grandchild. One of the Haven sta volunteered to drive four hours to Oklahoma City—the closest location for the parts—and back. The technicians then gathered in the wee hours to conduct the repairs and checks overnight, leaving the pilot clear to make an early-morning departure.
“I thought that was fun how our team went above and beyond to get him up and running,” said Lamance. “All of [them] wanted to make sure we did everything we could to make sure he didn’t miss the birth.” C.E.
BY DAVID JACK KENNY
Beech C99, Oct. 7, 2024, Norfolk, Nebraska
The solo pilot was killed and the majority of the aircraft consumed by the post-crash fire when the Part 135 cargo flight went down immediately after takeoff. Airport surveillance footage showed the airplane taking off from Runway 20 of the Norfolk Regional Airport, banking left, and descending into the ground. It struck about 640 yards southeast of the runway’s departure end and came to rest 24 yards further east in a flat, near wings-level attitude.
The flaps were found retracted and the landing gear extended. Flight control continuity appeared to have been continuous prior to impact. Fire damage prevented reading the cockpit instruments, and no non-volatile memory devices were found in the wreckage. Prevailing weather included clear skies with 10 miles visibility and sixknot winds from 160 degrees.
Daher TBM 700, Oct. 29, 2024, Pinedale, Wyoming
One passenger was seriously injured when the single-engine turboprop crashed departing after a fuel stop. The pilot and the other five passengers escaped with minor injuries. A witness on the field reported that heavy snow was falling while 40 gallons of fuel were added to each tank and the six passengers boarded. The pilot “cleared the snow off the airplane with a brush,” and the snowfall was described as “light” during its taxi and takeoff roll.
Shortly after it lifted off from Runway 29, the airplane’s left wing dropped and struck the ground. It came to rest in a snow drift
adjacent to the runway with “substantial” damage to the left wing and fuselage. Weather conditions recorded 10 minutes before the accident included four miles visibility under 600-foot scattered and 3,200foot broken cloud layers with a temperature of -1 and dew point of -2 Celsius. Prevailing winds were not reported.
Kaman Aerospace K-1200, Oct. 4, 2021, Killam Bay, British Columbia, Canada
Debris recovered from the accident site, including pieces of all four blades, indicated that the helicopter’s main rotor system broke up in flight. The solo pilot conducting external load operations from a logging site to an offshore pen was killed when the helicopter fell nose-first into the pen eight seconds after releasing its load. Search-andrescue efforts were initiated as soon as the operator lost radio contact with the pilot, but it took eight days to locate the underwater wreckage using sonar.
The Kaman K-1200 is an unusual design that uses two counterrotating main rotors with two blades each, thus eliminating torque reaction and the need for a tail rotor. The planes of their rotation intersect; a 12.5-degree outward tilt in each rotor pylon and a 90-degree offset in blade positions allows them to intermesh. Flight-control inputs are transmitted via control rods to 35-inch servo flaps located along each blade’s trailing edge. Deflection of the servo flap imposes torsional loads that twist the blade’s 50-inch elastic working section, changing its angle of attack.
Extensive analysis led the Transportation Safety Board to conclude that a fracture of
an internal bond joint in one of the left rotor’s servo flaps caused fatigue cracking of the flap’s skin, resulting in the departure of the aft (trailing edge) two-thirds of the flap’s structure. This in turn “created an out-of-track condition that caused a cyclic imbalance and a sudden vibration of the left main rotor system, the flutter of the three other rotor blades, and the failure of the left pylon structure. This led to the collision between a blade on the left rotor and a blade on the right rotor that resulted in the in-flight breakup of the rotor system.”
Two fatal U.S. accidents also involved collisions between the K-1200’s main rotor blades; the second, in August 2020, was specifically attributed to a servo flap failure. The manufacturer has also received three field service reports of servo flap failures in which the pilots landed safely. On June 1, 2023, Kaman revised the K-1200 maintenance manual with instructions for repairing chordwise paint cracks in the servo flaps that require removing the flap from service if the crack extends beyond the paint layer.
Eclipse Aerospace EA500, Nov. 3, 2022, Mesa, Arizona
An excessively fast approach, a misaligned wheel speed transducer (WST), and a missed step in the emergency procedures combined to render the right brake inoperative and send the very light jet off the left side of a 5,100-foot runway. The pilot and copilot were not injured, but the airplane sustained damage to the nose, both flaps, and all three legs of the landing gear after coming to rest in a six-foot-deep drainage culvert.
The accident occurred on the jet’s first flight after maintenance, including its 24-month/300-hour airframe inspection, had been performed at the Henderson
(Nevada) Executive Airport. Both pilots recalled normal braking before takeoff, though while taxiing slowly due to rain. The flight was uneventful.
Running the before-landing checklist, the pilot confirmed that the anti-lock braking system (ABS) was armed and pressed the ALL INTERRUPT switch to verify that the yaw damper was disengaged. He reported landing just beyond the 1,000-foot markings on Falcon Field’s Runway 22L, but when he applied the brakes the airplane drifted left without slowing. The copilot called for him to activate the ALL INTERRUPT switch; the pilot replied that he already had.
Full right rudder failed to correct the turn. The jet exited the left side of the runway, crossed two taxiways and dropped into the culvert.
ADS-B and onboard recorded data showed that the approach and landing were flown about 20 knots faster than the appropriate reference speed. The runway slopes down 0.6 degrees, and the four-knot tailwind reported earlier had increased to 10 knots. The lift provided by the additional speed limited braking effectiveness; the weight-on-wheels sensors did not activate until 2,490 feet down the runway.
Investigators subsequently found that the right WST had not been correctly aligned with the hubcap after maintenance, leading the ABS to erroneously detect a locked right wheel and release pressure to that brake. Holding down the ALL INTERRUPT switch would have disabled the ABS and restored braking function, but the recorded onboard data showed that it had only been depressed briefly once, during approach.
Cessna Citation 525A CJ2, Oct. 28, 2023, Paris-Le Bourget Airport, France
After the crew made a successful emergency landing, investigators found that the reason the nose gear had neither retracted
nor extended was that maintenance personnel failed to reconnect the actuators to the gear doors during a routine inspection of the gear well. The connecting hardware was found in a plastic bag taped to the left door actuating rod.
The jet departed Le Bourget for Farnborough Airport in the U.K. at 21:23 local time with one passenger on board. It was its first flight after several days of scheduled maintenance.
Extended discussions with air traffic control followed the crew’s unsuccessful attempt to use the standby gear extension system. Because the Citation is not equipped to dump fuel, they burned off excess fuel in nearly three hours of lowaltitude flight following vectors from ATC. After much additional discussion the airport decided not to foam the runway, and the jet landed safely on Le Bourget’s Runway 25.
Maintenance staff interviewed by investigators described a confusing organizational structure, with no clear lines of responsibility for specific tasks. The initial landing gear inspection was conducted by the least experienced member of the six-person team, a 19-year-old who’d joined the company two months earlier.
After inspecting the nose gear well, he asked whether he should reinstall the door actuator hardware and was told not to do so before a more senior technician inspected the work. The doors were subsequently held closed with aluminum tape while the airplane was towed out of the hangar for an engine run-up; fragments of the tape were found on the bottoms of the doors after the accident. A red flag attached to the gear doors was removed by the same senior technician on the mistaken assumption that he had already performed that inspection. z
BY GORDON GILBERT
Jan. 17, 2025
The FAA proposes to amend requirements applicable to meteorological towers and permanent wind energy systems. This rule would require any entity that owns a proposed, altered, or existing meteorological tower to file notice with the FAA if the highest point of the structure is at least 50 feet agl up to and including 200 feet agl. The agency is also proposing marking requirements for such structures and making such information available to the public on the FAA’s o cial database. In addition, this proposed rule would also add additional requirements addressing permanent wind energy systems. The FAA expects these changes to lower the collision risk for aircraft during low-altitude operations. Moreover, these requirements would partially address two statutory mandates and two NTSB recommendations based on three accidents between 2003 and 2011. Comments are due by Jan. 17, 2025.
Jan. 8, 2025
The UK is rolling out an electronic travel authorization (ETA) digital permission scheme to travel to the country that is being implemented in phases, with different countries being added to the requirement at different times. The U.S. is included in the group of countries from which certain travelers must comply with ETA requirements starting on Jan. 8, 2025. Applications will start being accepted after Nov. 27, 2024. By April 2025 most international visitors who don’t require a visa will need an ETA to enter the UK. An ETA costs 10 UK pounds and will be valid for two years.
Jan. 15, 2025
The UK Civil Aviation Authority (CAA) is proposing increased charges scheduled to take effect April 1, 2025. Proposals will see a “below-inflation increase in the cost of likefor-like activity with a general price increase of 1.6%.” New charges also cover cutting-edge technologies including eVTOLs and vertiports. The proposals are intended to “respond to the ever-increasing consumer demand for capacity and reliability,” said the agency. “The changes also reflect
rapid technological advancement, with a greater drive towards decarbonization, digitization, and continued demand within UK airspace.” The CAA’s proposed fees are expected to represent an estimated 0.4% of UK aerospace turnover. Comments on the proposal are due by Jan. 15, 2025.
Jan. 21, 2025
New rules adopt permanent amendments and establish a special federal aviation regulation (SFAR) for 10 years to: facilitate the certification of powered-lift pilots and flight instructors, clarify operating rules applicable to operations involving powered-lift, and finalize other amendments that are necessary to integrate powered-lift into the national airspace system. In this final action, the FAA provides alternate frameworks to facilitate the certification of pilots seeking qualifications in a powered-lift aircraft with single functioning flight controls and a single pilot station. In response to commenters, the FAA clarifies certain operating rules and adopts a performance-based approach to operating rules to enable powered-lift operations. The rules also change practical tests in aircraft that require type ratings, rotorcraft training centers, and rotorcraft
instructor eligibility, training and testing requirements. This final rule is effective Jan. 21, 2025, except for some Part 135 automatic pilot instrument proficiency check requirements, which are effective July 21, 2025.
Jan. 22, 2025
The UK government will impose a 50% hike to air passenger duty (APD) taxes for most business aircraft charter flights beginning April 1, 2026, according to plans in the country’s new annual budget statement. The government also launched a proposal on how the duty applies to what it categorizes as private jets. The consultation will consider whether the private aircraft APD, first introduced in April 2013, might be extended to models not now within the scope of the charges. Currently, duties apply to aircraft with a mtow of more than 44,000 pounds with 18 or fewer passenger seats. Comments on the proposal are due by Jan. 22, 2025.
Feb. 3, 2025
The FAA is inviting comments on the possible expansion of its delegation program to include new certification tasks that might
be accomplished by individual designees or Organization Designation Authorization (ODA) holders. The expanded tasks being considered involve certification of all commuter and on-demand operator types, excluding airplanes with 10 or more passenger seat operations. The effort may require the FAA to initiate rulemaking corresponding with additional certification tasks for individual designees and a revision to policy for additional ODA-authorized functions. Comments are due by Feb. 3, 2025.
Feb. 1, 2025
Australia has adopted the Global Reporting Format (GRF) for flight crews and airport air traffic controllers to report runway conditions. The GRF started being required in Australia on Aug. 1, 2024, for all airports serving Part 121 air carriers and will start on Feb. 1, 2025, for all remaining certified airports. In November 2021, ICAO developed the GRF as an international system for assessing and reporting runway surface conditions and recommended that countries implement the format when able. It is intended to provide better information for pilots to help assess takeoff and landing performance and to help reduce the risk of runway excursions.
April 10, 2025
Brazil plans to reinstate visa requirements for Australian, Canadian, and U.S. citizens (including flight crews) starting April 10, 2025. According to business aircraft flight planning service Universal Weather and Aviation, travelers should apply online at least 15 days before their intended arrival to account for the five-day processing period. At last check, the visa fee is $80.90 with a 10-year validity.
For the most current compliance status, see: ainonline.com/compliance
This newly refurbished Gulfstream is a show piece that emulates the creativity and craftsmanship of Duncan Aviation. Some of the details include two-tone leather seats with a fabric insert, porthole window surrounds, vinyl-wrapped sidewalls, carbon fiber table boxes, and a stone look used throughout that really makes it a one-of-a-kind show piece.
WATCH NOW www.DuncanAviation.aero/videos/GV-show-piece
BY JESSICA REED
President-elect Donald Trump selected Sean Duffy, a former Republican congressman from Wisconsin and Fox Business show host, to serve as the next secretary of transportation. A former district attorney for Ashland County, Wisconsin, he brings little transportation background to his new role but is known in Washington, having served in the U.S. House of Representatives from Jan. 3, 2011, until his resignation on Sept. 23, 2019.
CAE president and CEO Marc Parent will step down in August 2025 as part of an ongoing succession plan. A 20-year veteran of the company, Parent has been at CAE’s helm for the past 15 years. In the meantime, he will continue to lead CAE in his role as CEO and as a member of the board of directors while the board searches for his replacement. NBAA announced key changes to its leadership team, including expanded roles for two senior executives and the planned departure of another leader. Jo Damato has been appointed senior v-p of events and professional engagement, while Andrew Broom assumed the position of chief revenue officer. These changes followed the departure of Laurie Lutz, who concluded her tenure as senior v-p of events earlier in November. In her expanded role, Damato will oversee the strategic direction of NBAABACE, as well as the association’s conferences, forums, and professional development initiatives. Broom’s new responsibilities include leading exhibit sales for events while continuing to oversee membership, marketing, and sponsorship initiatives.
Chapman Freeborn appointed Bernardo Nunes as COO. Nunes previously served as director of transformation and analytics for the company in 2021 and 2022.
Fabrice Kunzi was named president of Avidyne, while Dan Schwinn will remain CEO and CTO of the company. Kunzi’s previous experience includes working at SkyGrid, Aurora Flight Sciences, and General Atomics Aeronautical Systems.
The Aerospace Industries Association (AIA) promoted Alison Lynn to senior v-p of external affairs. Lynn previously held the title of v-p of communications for AIA since 2019.
The Air Charter Safety Foundation (ACSF) appointed Kent Stauffer, v-p of safety for Flexjet, as its new chairman, and Michael Wootton, director of operations for Advanced Air, as vice chairman. Both begin their new positions in January. Stauffer is an aircraft pilot, UAS pilot, and A&P mechanic. Wootton has an ATP certificate with multiple business jet type ratings.
Traci Fremin was hired as v-p of customer experience at Modern Aviation , bringing more than three decades of experience in the FBO industry. Fremin previously served as director of key accounts at Atlantic Aviation.
The National Air Transportation Association promoted Shannon Chambers to senior v-p of communications and association affairs. Chambers has worked for NATA for the past 17 years and previously was employed at the National Aeronautic Association.
Patrick Enz joined ACASS as senior v-p of aircraft management and charter sales. His prior experience includes working as a consultant, as well as holding executive positions at Jet Aviation, Rizon Jet, and Hawker Pacific Asia.
Wheels Up Experience hired Jill Greer as executive v-p of investor relations and sustainability. Greer was previously employed at Delta Air Lines for 21 years and more recently served as v-p of investor relations at Travel + Leisure Co.
Hunt & Palmer Group recently unveiled leadership changes. Its new executive management team will include existing senior managers Julie Black (director of subsidiary Premier Aviation in the UK) and Jamie Peters (director of Hunt & Palmer Cargo Charters), as well as main board directors Simon Edwards and Mark Jenkinson. Peter Hunt and Jeremy Palmer will transition away from day-to-day management of the
company but will continue as main board directors of the group, along with Neil Harvey Richard Krawczun and Andy Reed were reelected to the Naples Airport Authority’s Noise Compatibility Committee (NCC) for the 2024–2025 term. Krawczun continues in the role of chair and Reed continues as vice-chair.
GAMA added Carsten Hoyt and Andy Phillips to its team. Hoyt, who previously served as an airworthiness regulatory, national security, and international law attorney for the FAA Office of Chief Counsel, takes on the position of general counsel and director of regulatory affairs at GAMA. Phillips, formerly aerospace policy adviser at ADS Group, is now GAMA’s manager of airworthiness and regulatory affairs.
LifeFlight has appointed Jeremy Ovens as head of flight operations. Ovens spent five years working as an instructor for the Dubai Police Airwing. Delray Dobbins was hired by Engine Assurance Program (EAP) as its director of global strategy. Dobbins’ prior experience includes leading sales and global strategy for Pratt & Whitney Canada’s Eagle Service Plan.
West Star Aviation promoted Craig Kuntz to project manager for Embraer at its facility in East Alton, Illinois. Kuntz has worked for West Star since 2020, when he was hired as an aircraft maintenance technician. West Star Aviation also promoted Lee Smieja to Gulfstream program manager at its Chattanooga, Tennessee facility. Smieja’s 22-plus years of experience in aviation include working for Gulfstream. At the same facility, West Star promoted Brent Ventosa to Embraer program manager. Ventosa’s maintenance career started with working on avionics for U.S. Air Force F-15s, and he came to West Star from Embraer Executive Jets. At West Star’s facility in East Alton, Dan Sies was promoted to Falcon program manager. Sies has been with the company since 2000.
Marc McKenzie joined Aircraft Specialties as regional sales manager for the company’s Midwest region. McKenzie previously worked as an F-16 aircraft technician and maintenance instructor for the U.S. Air Force, as well as at Duncan
Several business aviation companies were recognized in the annual Excellence Awards event organized by the Air Charter Association (ACA). Ten awards were handed out during a gala dinner attended by 500 industry professionals in Brighton, UK, on November 21. As part of the ACA’s ongoing work to promote opportunities for a new generation of charter industry professionals, judges chose Saxon Air’s Rachel Harvey as the group’s NextGen Young Person of the Year.
William Bush was recognized among the 2024 cohort of ACA interns for a project he conducted during the program.
John Goglia, president of the Aerospace Maintenance Council and former NTSB member, will be one of six inducted into the National Aviation Hall of Fame’s class of 2025. Goglia was the first NTSB member to hold an FAA mechanic certificate with airframe and powerplant ratings.
The National Air Transportation Association recognized several recipients with its 2024 Industry Excellence Awards. Stan McDu e, director of operations and flight instructor at SunEx Aviation, received NATA’s Excellence in Pilot Training Award. McDu e is an Air Force veteran who was recognized for helping U.S.-allied Afghan military pilots earn their civilian pilot certificates. Myrthe Simons, Clay Lacy Aviation’s director of commercial operations, received the Future Leader Award. NATA’s General Aviation Service Technician Award was presented to John Malecha, a technician at Stevens Aerospace and Defense Systems Hanna Mulugeta, line service ramp agent at Million Air Dallas, received the NATA Safety 1st Certified Line Service Professional Award. Mulugeta was nominated for her 22 years of dedication to the company and her e orts to cultivate relationships with clients. NATA’s FBO Customer Service Representative Award was presented to Isadora Pena, customer support manager at Banyan Air Service in Fort Lauderdale, Florida.
A member of the team at Banyan since 2011, Pena was recognized for her e orts to raise awareness of business aviation and to mentor the next generation of customer service representatives.
Franklin Carson, founder and president of Carson Helicopters, passed away on October 25. He started the company in 1958 and, after decades of modifying aircraft and developing new use cases for helicopters, received the Sikorsky Pioneer Award in 1998.
Bell noted an 18% increase YOY delivering 94 helicopters in the first nine months. The OEM added 18 light single-engine 505s to its total from the first three quarters of 2023.
Airbus Helicopters remained fairly static, with 184 deliveries through the first three quarters of 2024, just four o ff the pace it set last year.
Italian airframer Leonardo saw an 8% decrease from a year ago, with the decline most noticeable in its light-single AW119 family, which was 14 units off from its total through the third quarter of 2023.
Robinson Helicopter ramped up production of its light-turbine R66, with 95 deliveries through the end of September representing a 19% increase from the same period a year ago.
After handing over five civil helicopters—including three medium-twin S76s—during the first three quarters of 2023, Sikorsky Aircraft had no deliveries to the civilian market through the first nine months of this year.
PETE
“The health of our industry remains stable, which allows our companies to invest in technology and innovation that drives improved safety and sustainability for all civil aviation sectors,” said GAMA president and CEO Pete Bunce. “With new sessions and assemblies of governments set to convene shortly in both the U.S. and Europe, GAMA will continue to make the case to government leaders about the essential nature of the general and business aviation industry.” z
JAMES HOLAHAN (1921-2015), FOUNDING EDITOR, WILSON S. LEACH, FOUNDER & CHAIR EMERITUS
EDITOR-IN-CHIEF – Matt Thurber
MANAGING EDITOR – Charles Alcock
DIGITAL EDITOR – Chad Trautvetter
EDITOR AIN MONTHLY MAGAZINE – Kerry Lynch
SENIOR EDITORS – Curt Epstein, Hanneke Weitering – Technology Editor
COPY EDITOR – Jessica Reed
NEWS REPORTERS – Sarah Rose, Amy Wilder
CONTRIBUTORS – Cathy Buyck – Europe, David Donald – U.K., Mark Huber – Rotorcraft, Jennifer Leach English, David Jack Kenny – Safety, Gordon Gilbert , Jennifer Meszaros – Southeast Asia, Dale Smith, Richard Pedicini, James Wynbrandt
PRODUCTION MANAGER – Martha Jercinovich
GRAPHIC DESIGNER – Grzegorz Rzekos
DIRECTOR OF VIDEO – Ian Whelan
SENIOR DEVELOPER – Cameron MacPherson
FRONT END DEVELOPER – David Lohmeyer
EXECUTIVE CHAIR – Dave Leach
PRESIDENT – Ruben Kempeneer
HEAD OF PEOPLE & BRAND – Jennifer Leach English
SENIOR DIRECTOR, INDUSTRY AFFAIRS AND EVENTS – Nancy O’Brien
ADVERTISING SALES
DIRECTOR OF SALES - Henry Specht
Victoria Tod – Northeastern U.S./Eastern Canada/United Kingdom, +1 (203) 733-4184
Michelle James – Western U.S./Western Canada, +1 (520) 343-0236
Susan Joyce – Midwestern U.S., Southeastern U.S./Caribbean/Brazil, +1 (303) 641-5505
Diana Scogna – Europe/Middle East, +33 6 62 52 25 47
DIRECTOR OF MARKETING AND CLIENT SERVICES – Lisa Valladares
AUDIENCE DEVELOPMENT DIRECTOR – Eileen Silberfeld
MARKETING SPECIALIST – Alyssa Barry
SOCIAL MEDIA MARKETING – Zach O’Brien
SALES ADMINISTRATOR – Cindy Nesline
MANAGER OF FINANCE & HUMAN RESOURCES – Tracy Britton
ACCOUNTS PAYABLE – Mary Avella
ACCOUNTS RECEIVABLE – Bobbie Bing
U.S. HEADQUARTERS
214 Franklin Ave., Midland Park, NJ 07432, +1 (201) 444-5075
Advertising Inquiries: +1 (201) 345-0085, adsales@ainonline.com
Circulation Inquiries: +1 (201) 345-0085, subscriptions@ainonline.com
WASHINGTON, D.C. EDITORIAL OFFICE: Kerry Lynch: klynch@ainonline.com, Tel: +1 (703) 969-9195
EUROPEAN EDITORIAL OFFICE: Charles Alcock: calcock@ainonline.com, Tel: +44 7799 907595
Aviation International News (ISSN 0887-9877) is published twelve times per year (monthly). Periodicals postage paid at Midland Park, N.J., and additional mailing o ces. Postmaster: Send address changes to AIN Media Group, 214 Franklin Ave., Midland Park, NJ 07432. Allow at least eight weeks for processing. Include old address as well as new, and an address label from a recent issue if possible.
Subscription inquiries: +1 (201) 345-0085 or email: subscriptions@ainonline.com.
Aviation International News is a publication of AIN Media Group, 214 Franklin Ave., Midland Park, NJ 07432; Tel.: +1 (201) 444-5075.
Copyright © 2024 All rights reserved. Reproduction in whole or in part without permission of AIN Media Group is strictly prohibited. AIN Media Group publishes Aviation International News, AINalerts, AINonline, Business Jet Traveler, BJTwaypoints, ABACE Convention News, Dubai Airshow News, EBACE Convention News, Farnborough Airshow News, FutureFlight.aero, VAI Convention News, LABACE Convention News, MEBAA Convention News, NBAA Convention News, Paris Airshow News, Singapore Airshow News, Mobile Apps: Aviation International News; AINonline. PUBLICATION MAIL AGREEMENT NO. 40649046 RETURN UNDELIVERABLE CANADIAN ADDRESSES TO: PITNEY BOWES INTERNATIONAL MAIL, STATION A, P.O. BOX 54, WINDSOR, ON, N9A 6J5, returns il@imex.pb.com.
For feedback, letters to the editor, or other editorial needs, please contact AIN’s Editors at ainedit@ainonline.com
April 9 – 12, 2025
Friedrichshafen | Germany
More than 85,000 engines in service—and we’re just getting started. From the peerless PT6 to the legendary F135 to the groundbreaking GTF, we continue to take powered ight to new heights—increasing efficiency, developing the latest hybrid electric technology and creating a future that is smarter, cleaner and greener.
Learn more at prattwhitney.com
AIN Media Group is excited to announce our inaugural
March 27, 2025 | The National WWII Museum | New Orleans, LA
Join us for AIN’s FBO Dinner & Awards Gala, a prestigious event dedicated to celebrating excellence in the business aviation industry, as we announce the top performers from our survey.
The event will take place on Thursday, March 27th, 2025, from 6 pm to 9 pm in the U.S. Freedom Pavilion at The National WWII Museum in New Orleans. This exclusive evening will feature a formal dinner and an awards ceremony.
This event promises to be an unforgettable night of networking, recognition, and celebration among the leaders in aviation.
More than 85,000 engines in service—and we’re just getting started. From the peerless PT6 to the legendary F135 to the groundbreaking GTF, we continue to take powered ight to new heights—increasing efficiency, developing the latest hybrid electric technology and creating a future that is smarter, cleaner and greener.
Learn more at prattwhitney.com