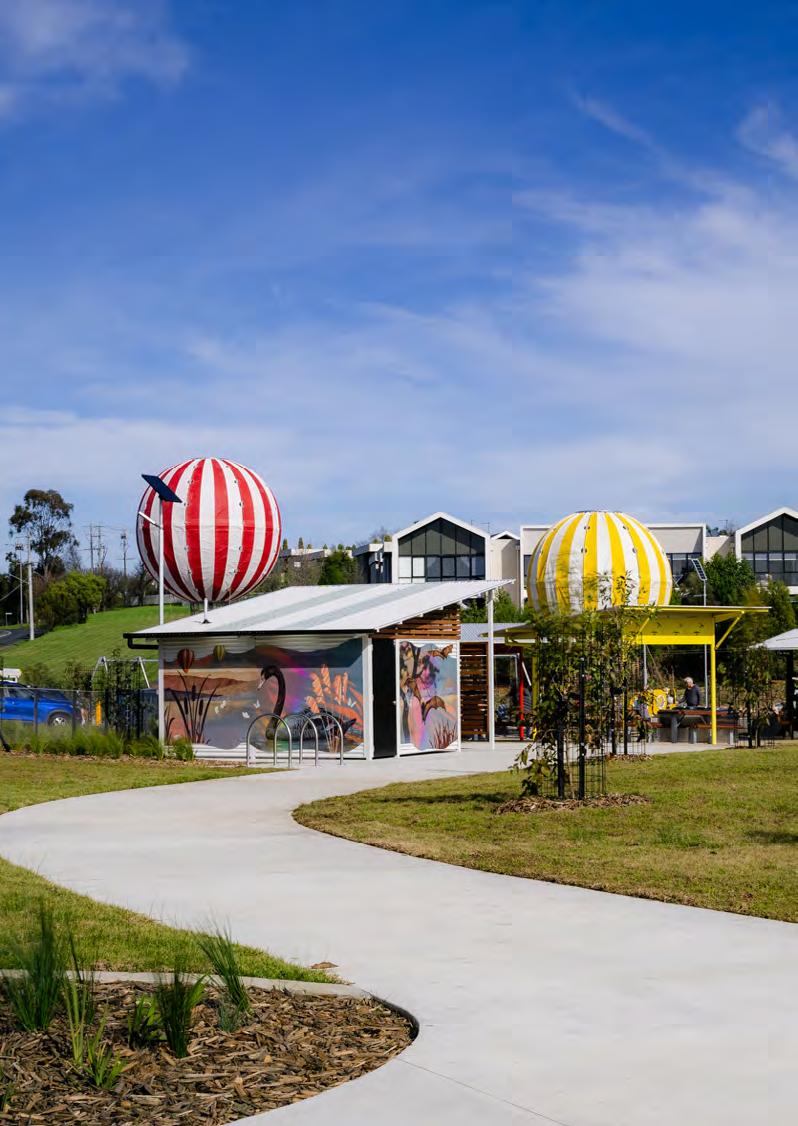

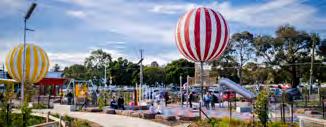
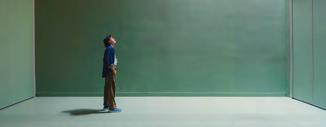
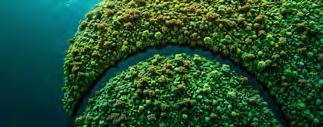
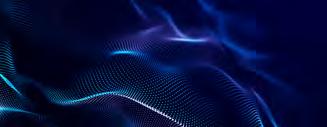

The recent ABC exposé on the lack of transparency and unethical behaviour of many strata management companies highlights the requirement for increased scrutiny and regulations to support the provision of independent, impartial and expert advice on which owners corporations can make informed decisions. As a consequence, the NSW State Government is undertaking an independent review which will look at business structures, processes and systems, professional practices, fees and charges, commissions and incentives, and third-party relationships.
Here, the Certified Quantity Surveyor has a key role in providing independent, impartial and expert services relating to the strata capital works fund (also known as sinking funds or capital replacement funds), annual administrative fund, replacement cost assessments (for insurance purposes), and tax depreciation schedules.
Owners corporations should have clarity and transparency around all professional services, especially those with any financial impact.
To support this, AIQS has developed guidelines on replacement cost assessments (for insurance purposes) and residential tax depreciation, which are freely available on the AIQS website.
The Strata Schemes Management Acts (or similar) in most states and territories in Australia require an owners corporation to establish and determine the funding required for a 10-year capital works program, an administrative fund, and building insurance.
All owners should have direct access to independent capital works fund reports as well as insurance reports.
A deficiency with many capital works funds is that they are often not based on independent, impartial, and expert information with respect to the lifespan of common area assets. This often leads to many strata buildings having inadequate funds for major capital works. Any subsequent purchasers will be caught with higher capital works fund levies to make up the shortfall not paid by original owners.
Unfortunately, the legislation does not prescribe that the capital works plan should be based on independent, expert advice. Consequently, many capital works plans and funds are understated, either deliberately or through lack of engagement of a Certified Quantity Surveyor to provide independent whole-of-life and capital works costs, accounting for any escalation. The levies paid are subsequently found to be insufficient to cover the costs of future capital works. While a tribunal may order an original owner to pay compensation for inadequate levy payments, any application to the tribunal must be made within 3-years after the original owner sold their unit entitlements.
Owners corporations should be aware that not all strata buildings are the same and the capital works fund and administrative fund calculations will vary due to factors such as geographic location, environmental aspects (weather, proximity to the sea, etc.), construction material, age of the building, heritage issues, accessibility, and local construction costs.
A Certified Quantity Surveyor can establish whole-of-life costings for the building and its various asset components, and the contributions required to ensure any repairs, maintenance, and capital works are adequately funded.
AIQS will be engaging with owners corporations to assist in developing guidelines on the establishment of capital works funds, administrative funds, and replacement cost assessments for insurance purpose.
GRANT WARNER
CEO
The Australian Institute of Quantity Surveyors
IRENA KUZMAN FAIQS, CQS Director, REN Project Controls
Across my twenty-two years in this profession, I have had many visions for the future: from diversity and inclusion to disruption by digitisation. However, there is one vision that I find myself returning to: collaboration.
It is no secret that the modern quantity surveyor is a different breed of consultant. No longer do we dwell in the shadows crunching numbers, we are now at the forefront of many developments within the construction industry. The most recent being the changes to Development Applications where CIVs have been replace by a more robust and comprehensive process of EDCs. This was achieved through the successful collaboration of our two major governing bodies: AIQS and RICS, as well as through their extensive community engagement with quantity surveying thought leaders such as my mentor, Bob Richardson.
There are also the awesome, yet terrifying, forces of artificial intelligence (AI) and automation. The exponential speed at which AI is achieving world domination in all spheres has the potential to disrupt the quantity surveying profession detrimentally. But all is not lost when you realise that AI is a large language model that requires data input from past and present producers. This is where collaboration and development within our own community can mitigate any adverse impacts of AI. Through banding together to secure the protection and integrity of our data and locking down exclusive knowledge sharing via our governing bodies, quantity surveying can work in tandem with advances in AI.
In recent years, I have been privileged to witness some excellent examples of collaboration through my work on life
science projects in the STEM space. One that comes to mind is Co-Labs; the brainchild of two Melbourne-based scientists; Samuel Wines and Andrew Grady, who have created a science and technology space for co-location, cross-pollination, and collaboration. This project was brought to life through the collaborative efforts of Co-Labs and the specialist life-science design and construct firm; Amicus Labline, which entrusted me with their cost management. Collaboration in STEM environments is a normal part of work and life, and the openness with which each professional operates results in a net positive for all. QSs are the cost engineers and data scientists of the building industry, and collaboration will only strengthen our future.
The recent unveiling of Chirnside Urban Park by Minister Sonya Kilkenny represents a landmark achievement in community development. Nestled adjacent to the Chirnside Park Shopping Centre, this newly opened park is designed to be a vibrant, inclusive play space catering to all age groups. The park features a variety of attractions, including two climbable balloons of this design in the southern hemisphere, a flying fox, music play areas, swings, shelters, and more, making it a dynamic hub for leisure and recreation.
The development of Chirnside Urban Park is the culmination of extensive community consultations that began in late 2019. This participatory approach by Fitzgerald Frisby Landscape Architecture and Yarra Ranges Council ensured that the park would address local needs, prioritising accessibility, safety, and green space. As a result, the park now stands as a testament to community-driven planning and execution.
Councillor Richard Higgins of Yarra Ranges Council emphasised the park’s potential to serve as a central gathering place for the town, offering a flexible environment for social, recreational, and community activities.
The park boasts a regional playground, walking paths, trampolines, an urban forest, and a custom-designed play area, establishing it as a model of integrated community infrastructure.
Melbourne Quantity Surveyors played a crucial role in the successful realisation of this project. Our team was integral in delivering the park by providing expert cost We undertook comprehensive quantification and value management, meticulously analysing tenders and contracts to determine the most suitable contractor. Our involvement extended throughout the project lifecycle through facilitating effective contract administration, which resulted in a project delivered ahead of the program and under budget while upholding the high standards expected by the community and stakeholders.
The successful transformation of Chirnside Urban Park was made possible through the collaborative efforts of Yarra Ranges Council and the Victorian Government’s Growing Suburbs Fund. These contributions have helped create a space that not only meets but also exceeds the community’s vision, promoting health and wellbeing for all residents.
DESIGNERS: FITZGERALD FRISBY LANDSCAPE ARCHITECTURE
CONTRACTOR: WARRANDALE INDUSTRIES PTY. LTD.
PHOTOGRAPHER: COLCHEEDAS PHOTOGRAPHY
By Andrew Loh AAIQS
Currently in Melbourne, there are a number of major infrastructure projects showing potential signs of budget blowouts. The cost overruns can be attributed to a myriad of factors including complexities in project scope, design changes, inadequate risk management, poor decision-making processes, ineffective project oversight, supply chain disruptions, labour shortages, and regulatory changes.
Value engineering might have mitigated these budget blowouts without compromising successful project delivery. Why wasn’t value engineering considered?
There are many reasons why value engineering is not applied or even considered more often in Australia. Chiefly, value engineering is not well understood or appreciated with many project stakeholders having a limited awareness of value engineering principles, methodologies, and best practices, leading to misconceptions or scepticism about its effectiveness in delivering successful infrastructure projects.
Indeed, more often than not, value engineering is interpreted to mean cost-cutting. It’s not.
Value engineering is a systematic and organised approach to improving the value of a project by examining its requirements and reducing unnecessary costs without sacrificing quality, performance, or customer satisfaction. The primary goal of value engineering is to identify opportunities for cost reduction while maintaining or improving functionality and quality.
Value engineering involves engaging stakeholders, including designers, engineers, contractors, suppliers, and project owners, in collaborative decision-making processes. By fostering open communication and collaboration, project teams can leverage diverse expertise and
perspectives to identify cost-saving opportunities and address potential challenges effectively. This collaborative approach ensures alignment with project goals and enhances the likelihood of successful cost management throughout the project lifecycle.
Despite these challenges, there is growing recognition of the importance of value engineering in optimising infrastructure projects’ cost, quality, and performance. Efforts to promote awareness, education, and collaboration among project stakeholders, along with improvements in contractual and procurement practices, are helping to overcome barriers and encourage the consideration and adoption of value engineering when designing and delivering infrastructure projects.
Despite the potential to maximise taxpayer dollars and improve project outcomes, risk-adverse governments have generally been less inclined to consider value engineering. While on the one hand, governments prioritise cost savings and efficiency, politics, the economic climate, bureaucratic processes, and public scrutiny influence government decision-making.
design methods... Often prioritise low upfront costs and fast project delivery over value optimisation. ...PPPs facilitate the implementation of value engineering principles aimed at optimising costs and enhancing project outcomes.
Traditional procurement methods, such as lump-sum contracts or design-bidbuild approaches, often prioritise low upfront costs and fast project delivery over value optimisation. Additionally, risk allocation and contractual arrangements may not adequately incentivise collaboration and innovation among project stakeholders.
Moreover, traditional design and delivery methods may be deeply ingrained. Many project stakeholders, including designers, engineers, contractors, and government clients, may be more accustomed to conventional approaches and therefore hesitant to adopt new methodologies.
Significantly, Australian infrastructure projects are increasingly being delivered via public-private partnerships (PPPs) and this model provides a conducive environment for value engineering. By leveraging the expertise and resources of both the public and private sectors, PPPs facilitate the implementation of value engineering principles aimed at optimising costs and enhancing project outcomes.
Private sector partners bring specialised knowledge in design, construction, and financing, contributing innovative solutions to improve project efficiency, quality, and sustainability. Meanwhile, the public sector ensures regulatory compliance, funding, and strategic direction, aligning projects with broader societal objectives.
Through performance-based contracts and risk-sharing mechanisms, the PPP model incentivises stakeholders to prioritise cost-effective design choices, streamline construction processes, and minimise lifecycle costs. This collaborative approach fosters creativity, innovation, and efficiency, driving continuous improvement across infrastructure projects and maximising returns on investment.
Ultimately, the PPP model supports the application of value engineering, promoting collaboration, innovation, and success in delivering essential public assets.
Implementing value engineering typically involves a systematic approach to identify opportunities for cost reduction and quality improvement while maintaining or enhancing functionality. Here are five steps to implement value engineering effectively:
1. Research – Analyse the functions, requirements, and performance metrics of the project, and the needs of stakeholders, to understand its purpose and identify areas where improvements can be made.
2. Speculation – Assemble a crossfunctional team to challenge assumptions, explore innovative solutions, and brainstorm creative ways to improve the value of the project.
3. Evaluation – Evaluate the ideas generated based on criteria such as feasibility, cost-effectiveness, and potential impact on performance, quality, and customer satisfaction. Prioritise the most promising ideas that offer the greatest potential for value improvement while considering potential risks and trade-offs.
4. Development and implementation – Incorporate the most promising ideas into the design or delivery process. This may involve redesigning processes, modifying materials, or leveraging new technologies.
5. Continuous improvement – Review the outcomes to assess their effectiveness in achieving the desired objectives and measure KPIs to evaluate the impact on cost savings, quality improvement, and customer satisfaction. Continuously seek opportunities for further optimisation and innovation to drive ongoing improvements.
For value engineering to be sufficiently impactful, it must be considered in the early stages of an infrastructure project – from the initiation and design phases through to early in the delivery phase. As you move through construction, the impact is diluted.
By integrating value engineering principles into the initiation and design stages of large infrastructure projects, project teams can proactively analyse cost-related risks associated with design choices, construction methods, supply chain issues, or external factors such as regulatory changes or market fluctuations.
This allows them to develop strategies to mitigate these risks early in the project lifecycle. This proactive risk management approach helps ensure that infrastructure projects are delivered on time and within budget while meeting quality and performance requirements.
Implementing value engineering requires an upfront investment of time, resources, and expertise...
Additionally, as value engineering considers the entire lifecycle of the infrastructure project, including construction, operation, maintenance, and eventual decommissioning, project teams can evaluate the long-term cost implications of design decisions and identify opportunities to optimise costs over the project’s lifespan including by minimising ongoing operational and maintenance expenses.
Time is the principal reason value engineering is not the default approach when designing and delivering infrastructure projects.
Implementing value engineering requires an upfront investment of time, resources, and expertise to analyse design options, conduct cost-benefit analyses, and develop alternative solutions.
Some project stakeholders may perceive these additional upfront costs and time commitments as barriers to adopting value engineering, especially if they prioritise short-term budget constraints over long-term value optimisation.
Deciding whether to adopt a value engineering approach on an infrastructure project requires careful consideration and evaluation by stakeholders. Here are the steps stakeholders can take to make an informed decision:
1. Assess the project’s objectives, requirements, constraints, and priorities.
Consider factors such as budget, schedule, quality standards, performance criteria, and stakeholder expectations. Determine whether cost optimisation, quality improvement, and innovation are critical goals for the project.
2. Evaluate the potential benefits of value engineering for the project. Consider how value engineering can help achieve project objectives, such as reducing costs, enhancing quality, improving functionality, mitigating risks, and maximising value for stakeholders. Assess the potential impact of value engineering on project outcomes, lifecycle costs, and long-term sustainability.
3. Consider the risks and tradeoffs associated with adopting a value engineering approach. Assess the potential challenges, uncertainties, and limitations of value engineering, such as upfront costs, time investment, changes to project scope, impacts on project schedule, and potential resistance from stakeholders. Evaluate whether the benefits outweigh the risks and whether stakeholders are willing to accept the trade-offs.
4. Engage relevant stakeholders, including project owners, designers, engineers, contractors, and suppliers in discussions about value engineering. Seek input and expertise from individuals with experience in value engineering and cost optimisation. Collaborate with multidisciplinary teams to explore alternative design solutions, assess cost-saving opportunities, and develop innovative ideas.
5. Conduct a cost-benefit analysis to quantify the potential savings, benefits, and returns on investment associated with value engineering.
Compare the estimated costs of implementing value engineering measures with the expected benefits, such as reduced construction costs, operational savings, increased asset value, and improved project performance. Consider both shortterm and long-term implications to make an informed decision.
6. Evaluate regulatory requirements, contractual obligations, and procurement practices that may impact the adoption of value engineering. Determine whether existing regulations, standards, or contractual provisions facilitate or hinder value engineering initiatives. Consider how to align project goals with regulatory compliance and contractual requirements while optimising value.
Many high-profile infrastructure projects have been delivered using a value engineering approach. The Golden Gate Bridge and the Panama Canal are two examples.
Completed in 1937, the construction of San Francisco’s iconic Golden Gate Bridge utilised value engineering principles to optimise costs and enhance structural integrity.
Engineers implemented innovative design solutions, such as the use of lightweight aluminium for the bridge’s towers and suspension cables, to reduce material costs without compromising strength or safety. The project also employed advanced construction techniques, including the use of pneumatic caissons (watertight structures to create a dry working environment below the water level) to anchor the bridge’s foundations, resulting in significant cost savings and accelerated construction timelines.
Effective value engineering requires a balanced approach that considers all aspects of a project’s lifecycle...
The expansion of the Panama Canal, completed in 2016, involved the construction of new locks to accommodate larger vessels and increase the canal’s capacity. Value engineering played a crucial role in optimising the design and construction of the locks, minimising costs, and maximising efficiency.
Engineers implemented innovative solutions, such as the use of prefabricated steel gates and advanced concrete mix designs, to reduce construction time and costs while ensuring durability and reliability.
Of course, when value engineering is wrongly applied to construction projects – meaning, when safety, quality, and long-term durability are not prioritised over short-term cost savings – the results can be catastrophic.
The 2017 Grenfell Tower fire in London is a highly reported contemporary example.
The fire, which claimed the lives of 72 people, raised serious questions about the adequacy of value engineering practices in the construction and refurbishment of high-rise buildings. The tragedy exposed flaws in the building’s design and construction, including the use of combustible cladding materials and inadequate and value engineering decisions may have compromised fire safety standards and contributed to the rapid spread of the fire.
While cost optimisation is an essential aspect of value engineering, it cannot come at the expense of structural integrity, safety, or regulatory compliance. Effective value engineering requires a balanced approach that considers all aspects of a project’s lifecycle and prioritises the wellbeing of its users and the surrounding community.
• Cost optimisation, quality improvement, and innovation are critical project goals
• It will have a positive impact on the project outcomes
• The benefits outweigh the risks and stakeholders are willing to accept the trade-offs
• Relevant stakeholders, including project owners, designers, engineers, contractors, suppliers, and end-users, have an appetite for exploring alternative design solutions, assessing cost-saving opportunities, and developing innovative ideas
• Cost-benefit analysis quantifies the potential short- and long-term savings, benefits, and returns on investment
• Existing regulations, standards, and contractual provisions facilitate (don’t hinder) value engineering initiatives – project goals can be aligned with regulatory compliance and contractual requirements while optimising value.
Contract Administrator, McConnell Dowell
Quite often the final revision of construction drawings is delayed, with the construction program usually still requiring the subcontractor to start on-site as per the original program. As a result, the timeframe required to complete tendering, bid evaluation, and contract negotiation is extremely tight. Errors and ambiguity often appear in a contract if it is completed under pressure. In such situations, we need to remind ourselves of the importance of not rushing into anything. Calmly review every document and clarify all terms and conditions to avoid taking unnecessary commercial risks.
Many reasons may result in scope gaps in a contract. Generally, they are due to contradictory information in the scope of work, drawings, and specifications; not considering subcontractors’ exclusions or making assumptions that it is included in the scope. Closing the scope gap requires good communication with the project construction team and subcontractors to have a comprehensive understanding of the responsibilities of the work package.
Contractual entitlement to adjust price was very common in the past but has become a trend recently. Due to increasing inflation and a competitive job market, more and more subcontractors, especially the provision of labour and plant hire (wet), have a price review clause in the contract to allow them to adjust rates on a yearly basis. As contract administrators, we need to take caution when reviewing updated rates to make sure the increase aligns with the general CPI movement. Furthermore, it is necessary to make efforts to negotiate a lower increase amount and be prepared to seek alternative service providers to keep the cost under budget.
Administrator, Xenia Constructions
As a contracts administrator, I face several key challenges that are critical to the successful management of contracts.
The most significant challenge is risk and opportunity management With the growing use of Design and Construct (D&C) contracts, the level of detail during the design or tender stages is often insufficient, leaving gaps that can lead to unforeseen risks. It’s essential to thoroughly identify and understand these risks to develop effective mitigation strategies. Conversely, recognising and capitalising on opportunities within a project is equally crucial. If there is an opportunity, the team explore ways to maximise its benefits, ensuring that the project can achieve the best possible outcomes.
Another major challenge is variation management. During the execution of a contract, project requirements often evolve, leading to changes in scope – whether additions, deletions, or modifications. These changes necessitate careful and flexible management to avoid compromising the contract’s objectives or the interests of the involved parties. This aspect of contract administration requires constant vigilance and adaptability to ensure that adjustments are made smoothly and that the project continues to meet its goals.
Lastly, dispute resolution is an unavoidable challenge. Contracts, once executed, can give rise to disputes or disagreements. As a contracts administrator, it is my responsibility to handle these disputes effectively.
This involves protecting the company’s interests while also maintaining strong relationships with contracting partners. Effective dispute resolution demands quick decision-making, a thorough understanding of the contract, and strong negotiation skills to reach outcomes that are fair and beneficial to all parties involved.
These challenges – risk and opportunity management, variation management, and dispute resolution – are central to my role, requiring a balance of strategic thinking, adaptability, and interpersonal skills.
By Paul McArd FAIQS, CQS
Project teams are often told to keep daily or even hourly records of on-site events if a claim for additional time and cost arises. These records are known as contemporaneous records in that they are ‘recorded’ when the event occurs.
In the age of technology, there have been advancements in carbon copy daily diaries with handwritten notes accompanied by date-stamped photographs taken on a digital camera. Examples such as live feed web cameras, real-time digital diaries, and electronic sign-in and out systems and programming software are many ways that can, in some respects, automatically capture or demonstrate ‘contemporaneous records’.
What has not changed from the days of carbon-copy daily diaries and blurry digital photographs is the requirement for the event the records relate to be described in a manner that clearly articulates:
• What happened
• Why the event is a change
• If the event is a cost change, what is the quantum of the cost change, and how further records support this
• If the event is a time change, what is the quantum of time (effect) and why has the event caused a delay to the critical path?
The previous is easily articulated as a written notice or letter that refers to/ appends the other contemporaneous records, such as site diaries, photographs, etc.
A picture may tell a thousand words, but pictures alone do not always demonstrate the cause and effect or tell the full story. The same goes for impacted programs, if there is no narrative explaining the impact, the program alone may be misunderstood.
Project teams need to review and collate all the records related to the event and create a further contemporaneous record in the form of a formal notice that, as a minimum, includes the four points above. The notice then becomes the primary piece of contemporaneous record which in effect tells the story of the event by using the supporting records mentioned previously.
The initial notice does not need to be legalese or overly complex. Instead, the notice should allow a third party to inform themselves of what the situation entails even though they have no experience with the project or matter.
This third party should also be able to be satisfied that what is stated in the notice is fully correct by referring to the site diaries and photographs, etc.
Another benefit of sending a notice immediately after an event occurs, along with all the associated records, is that you create a separate head of claim, demonstrating the cause and effect.
If contemporaneous records are well organised and articulated with notices, the likelihood of contentious claims may be reduced. However, no matter how good your records are, your client may disagree with your position.
If you face a dispute, you may need expert advice and support; however, if you have organised your records in the manner detailed above, then the task may not be as difficult for your advisors.
Disclaimer: This paper does not in any way constitute any type of legal or professional advice whatsoever and in no way should it be relied upon by any party in any jurisdiction.
This article was written by Paul McArd FAIQS, CQS from Accura Consulting.
Written and first published by Slattery
Every building has an embodied carbon footprint. As Australia’s development industry begins to measure embodied carbon emissions, the scales are tipping in favour of retrofits. Slattery, with Australia’s first carbon planning service, is releasing our data and knowledge so the industry can move further and faster together.
A building’s upfront embodied carbon emissions are locked in before a light switch is flicked, an air conditioner is turned on or a single occupant walks through the front door.
Until very recently, the built environment sector was focused on driving down operational emissions, which make up 28% of the world’s greenhouse gas emissions footprint, according to the World Green Building Council.
But the built environment’s embodied emissions are responsible for another 11% of the world’s carbon footprint. Most of these emissions are generated ‘upfront’, during the design and construction phases of buildings. This means the opportunity to reduce these emissions can only happen upfront.
Slattery released our first upfront embodied carbon benchmarking paper in May 2022. Since then, we have expanded the breadth and depth of our upfront embodied carbon benchmarking database and have data on a wide range of sectors, including commercial office, industrial, tertiary, healthcare, aged care, arts and cultural, and justice.
In this report, we share breakdowns of upfront embodied carbon for four new sectors. We also offer an overview of the most recent developments influencing the direction of the property industry.
Upfront embodied carbon emissions must be tackled with urgency if Australia is to set its trajectory to net zero. In this report, we provide some new analysis that compares current upfront embodied carbon data, based on our benchmarks, against Australia’s targets. By breaking the task down by building typology, we reveal the enormity of the task ahead and the need for accelerated action.
In section three of this report, we examine a case study of Hines’ office development, 600 Collins in Melbourne. This project demonstrates how smart design decisions can deliver significant embodied carbon savings. The upfront embodied carbon conversation, we believe, is so vital to the future of Australia’s property and construction industry, that we’ve put this information ‘up front’.
Our latest benchmarking data reconfirms the findings from our July 2023 report and provides some additional insights. The headline findings are:
• Australia’s construction industry must reduce upfront embodied carbon emissions by 31-36% by 2030 to adhere to the Science Based Target initiative (SBTi) and limit global temperature increase to 1.5°C above pre-industrial levels.
• We now have upfront embodied carbon benchmarks for four new sectors including industrial, justice, arts and culture and commercial base building refurbishments.
• On average, new commercial office buildings generate 4.5 times more upfront embodied carbon emissions than commercial office refurbishments, emphasising the importance of refurbishment over rebuilding.
• 82-91% of the upfront embodied carbon in typical new builds comes from the cold shell scope.
We find that upfront embodied carbon savings of around 20% are achievable through design decisions that do not carry a significant cost impost. Our data reconfirms that extending the life of existing buildings through retrofitting and reuse is the most effective strategy to minimise upfront embodied carbon emissions and meet sustainability targets.
Australia, as a signatory to the Paris Agreement , has agreed to “hold the increase in the global average temperature to well below 2°C above pre-industrial levels” and to “pursue efforts to limit the temperature increase to 1.5°C above pre-industrial levels.”
New Slattery analysis suggests that the required reduction in upfront embodied carbon (GWP/m2 or kgCO2eq/m2) to maintain the 1.5°C trajectory is very ambitious.
We assessed the average upfront embodied carbon (kgCO2eq/m2) across the Slattery benchmarking dataset against the Science-Based Targets initiative (SBTi) required to maintain a 1.5°C pathway. The reductions in upfront carbon required are shown in Exhibit 1, measured in units of kgCO2eq/m2
For example, for the commercial office sector, the average new-build upfront embodied carbon intensity (kgCO2eq/ m2) in 2024/25 is 740 kgCO2eq/m2 in 2050.
Exhibit 1: Australian upfront embodied greenhouse gas emission intensity (kgCO2eq/m2 of Gross Floor Area) targets to limit global temperature increase to 1.5°C above pre-industrial levels. Source: Slattery.
To achieve SBTi-aligned targets and limit global temperature increase to 1.5°C above pre-industrial levels, Australia’s construction industry must reduce the upfront embodied carbon emissions by:
• 31-36% by 2030
• 55-63% by 2035
• 76-80% by 2040
• 87-89% by 2045
• 98% by 2050.
These targets can appear overwhelming and unachievable when we consider that upfront embodied carbon must be almost entirely eliminated by 2050.
But applying a shorter-focus lens reveals the immense challenge for Australia’s construction industry right now.
Building projects in the early design phase today will be in construction in 2030 and must, therefore, be designed
to reduce upfront embodied carbon by a third on today’s business-as-usual.
The 31-36% reduction by 2030 is the average across all buildings. Given that embodied carbon is not yet measured on most projects, the industry’s leaders must step up quickly to make up for the laggards.
To determine these figures, we expanded on the work of 2050-Materials co-founder and CEO, Phanos Hadjikyriakou, who broke down upfront embodied carbon targets of residential buildings in the United Kingdom into their key components. To do this, he combined two datasets:
• Embodied carbon data from LETI (London Energy Transformation Initiative) and
• Data from the Science Based Targets initiative (SBTi) report a 1.5°C pathway for the global buildings sector’s embodied emissions
From this work, Phanos has questioned whether the current Science Based Targets are achievable for the UK’s residential sector.
Slattery completed a similar exercise by combining our benchmarking data averages for new builds with the SBTi upfront embodied carbon reduction targets and percentage reductions required to align with the 1.5°C climate change trajectory.
The
31-36% reduction by 2030 is the average across all buildings. Given embodied carbon is not yet measured on most projects, the industry’s leaders must step up quickly to make up for the laggards.
Slattery’s
modelling
suggests Australia must encourage more than just market leaders to meet Green Star upfront embodied carbon targets. We need every project to be thinking about embodied carbon footprint.
We know, in some cases and depending on the building type, we can make upfront embodied carbon savings of up to 20% without imposing a cost premium.
Any project team seeking a Green Star Buildings rating from the Green Building Council of Australia must reduce upfront carbon by at least 10%. Higher ratings require a 20% reduction as a minimum expectation, and the GBCA has indicated this will increase to 40% over time to encourage market leading practices.
In section three of this report, we examine a case study of Hines’ office development, 600 Collins, in Melbourne. Hines’ work with Slattery illustrates how a 44% reduction in upfront embodied carbon could be achieved with a relatively small cost impost.
However, this case study also demonstrates the challenge for Australia’s construction industry. This outcome was driven by a motivated team with ambitions for a world-leading building.
Slattery’s modelling suggests Australia must encourage more than just market leaders to meet Green Star upfront embodied carbon targets. We need every project to be thinking about embodied carbon upfront.
To meet Australia’s 2030 targets and maintain 1.5°C trajectory will require a step change in design, procurement and construction.
How can we proceed? Addressing upfront embodied carbon in the built environment will require collaboration across the entire supply chain. We have explored some of the opportunities in Retrofitting Reimagined, the previous issue of our embodied carbon series. Ultimately, Australia will not meet its targets if we don’t measure the upfront embodied carbon component of every building. Only then can we make informed and cost-effective decisions about design, make choices that incentivise innovation in product manufacturing, and expand the market for low-carbon materials.
Slattery continues to expand the breadth and depth of our upfront embodied carbon benchmarking database. We now have benchmarks for the following sectors:
• Commercial office new build
• Commercial base building refurbishment
• Fitout
• Industrial
• Education (both tertiary and schools)
• Healthcare
• Aged care
• Residential
• Justice
• Arts and cultural.
We have not recorded significant shifts in the range of results across most sectors since publishing our embodied carbon benchmarking report in July 2023. However, the number of benchmarked projects within these ranges has significantly increased, which enhances the quality of our data.
The major changes since July 2023 include:
• Commercial fitout and tertiary fitout have now been combined into one sector within the dataset
• Schools sector data range has widened from 700-860 kgCO2/m2 to 466-910 kgCO2eq/m2
• Aged care upper range has increased to 730 kgCO2/m2 from 580 kgCO2/m2
. Detailed information on the percentage breakdown of upfront embodied carbon for commercial new builds is available in our July 2023 report. And we provide a detailed comparison of commercial new builds and retrofits in our March 2024 paper, Retrofitting Reimagined.
In this report, we share fresh insights into four new sectors. Our main takeaway from our detailed analysis to date is that “a building is not just ‘a building’”. The quantum of carbon in each building type can vary significantly, which means a bespoke project-by-project and sector-by-sector approach will be the key to unlocking carbon savings in design, procurement and construction.
This new sector includes museums, art galleries, cultural and community centres, and visitor centres.
Arts and cultural buildings tend to prioritise bespoke designs, visual appeal and open, expansive space. The specific architectural features, with large load and span requirements, can make arts and cultural buildings carbon-intensive structures.
The key carbon indicators are the substructure, external walls, upper floors and roof. The substructure and superstructure (columns, upper floors, stairs, roof, external walls, internal walls and doors) contribute, on average, 88% of the typical building’s upfront embodied carbon. This means reuse and re-purposing existing buildings are a smart strategy.
The range of results for arts and culture benchmarks is 655-856 kgCO2eq/m2
We have isolated commercial refurbishment because it is an important sub-sector of Australia’s commercial property market. Our data includes projects with base-building cold shell refurbishment work. The work completed on these projects is mostly internal; therefore, the key carbon-intensive elements are finishes, services, internal walls, upper floors, and fitments.
The project type and scope will dictate which building elements are addressed and the focus areas. More information about the opportunities for upfront embodied carbon savings on commercial refurbishment can be found in our Retrofitting Reimagined thought leadership paper, published in March 2024.
The range of results for commercial refurbishment benchmarks is 24-394 kgCO2eq/m2
This sector includes law courts, prisons and correction centres. Justice buildings have significant security requirements which can mean in-situ or precast concrete walls, additional corridors for access or privacy, and additional steel for security.
Therefore, the upfront embodied carbon emission intensity for the justice sector is high. The key carbon indicator elements of this sector include internal walls, external walls and upper floors.
The range of results for justice benchmarks is 1203-1436 kgCO2eq/m2 .
This new sector’s benchmarks are predominantly storage facility projects. These projects generally have high loading requirements and therefore require a heavy structure and substructure. As a result, the substructure (32%) and upper floors (22%) are the largest contributors to upfront embodied carbon emissions.
As this sector expands to larger singlestorey sheds, as well as multi-storey warehouses, the building elemental percentages for upper floors are likely to change.
Our work with industrial developers reveals a significant barrier in the current delivery method. In most cases, a builder designs and constructs based on the developer’s brief. This is a costeffective delivery method, but means the developer has little control during the design process or in the selection of materials. Unravelling the upfront embodied carbon challenge in the industrial sector may need innovation in delivery models.
The range of results for industrial benchmarks is 432-645 kgCO2eq/m2 .
“Addressing embodied carbon in construction is a crucial step towards a sustainable future for Australia’s built environment. At Hines, we’ve been actively reducing embodied carbon across the assets we own, manage, and develop. Through innovative materials, design choices, and construction practices, we’re helping to advance Australia’s low-carbon future.”
David Warneford, Senior Managing Director, Hines
Smart design decisions can deliver significant embodied carbon savings.
Hines acquired 600 Collins Street in 2020 with plans to develop a Premium grade office tower with a strong focus on sustainability, amenity, wellness and tenant experience.
Standing 180 metres tall with an articulated curved façade, 600 Collins is targeting a 6 Star Green Star and 6 star NABERS Energy rating, as well as a Platinum WELL Certification for shell and core.
Hines’ team was determined to design a low-carbon asset and engaged Slattery to undertake cost and carbon planning.
Our initial measure of the upfront embodied carbon of the schematic design resulted in an upfront embodied carbon of 757 kgCO2eq/m2 of GFA.
Slattery compared this measure to other similar commercial office benchmarks.
We highlighted specific design efficiencies that could reduce upfront carbon. Following a collaborative process with Hines’ project team, the design of the structure was altered to reduce the amount of concrete required without impacting the net lettable area. Consequently, upfront carbon at the 70% design development phase was lowered to 680 kgCO2eq/m2
Slattery also provided a pathway for further upfront embodied carbon reductions with multiple lower carbon material specification options. These could be specified with a cost uplift of less than 1% on the total build cost.
Taking this pathway would achieve an upfront embodied carbon measure of 424 kgCO2eq/m2 , equivalent to a 44% reduction when compared to the schematic design measure.
Carefully controlling the cost and carbon budgets throughout design, measuring multiple iterations of the design and providing robust data to guide informed design decisionmaking, have delivered an achievable pathway to deliver a high-quality, lower upfront embodied carbon building.
Slattery’s team is finding efficiencies in designs that drive cost and carbon outcomes on projects around Australia.
We are working with many of the market leaders, including Hines, and with engaged and innovative project teams who understand the imperative, value and opportunity of lower upfront embodied carbon buildings.
With upfront embodied carbon a hot conversation topic across Australia’s construction industry, the library of research reports, policy papers and thought leadership positions continues to grow. Since reporting on this in July 2023, the five biggest shifts we’ve observed for Australia’s built environment are:
1. NSW mandates to measure embodied carbon: The NSW Sustainable Buildings State Environmental Planning Policy (SEPP) came into force on 1 October 2023, mandating that certain large and state-significant projects must measure upfront embodied carbon emissions at the Development Application phase and then again at the construction certificate stage. This policy is a clear signal to the market, and similar policies from other state governments can be expected.
2. Federal government guidelines for low-carbon procurement: Introduced in April 2024, the Australian Government’s Environmentally Sustainable Procurement (ESP) policy guides federal government departments and agencies across three areas: climate, the environment and circularity. Businesses bidding for government construction projects above $7.5 million must meet certain sustainability outcomes from 1 July 2024. While the policy
doesn’t specifically mention upfront embodied carbon, it signals that the Australian Government will use its significant purchasing power to accelerate the market for low-carbon materials.
3. Growth of EPDs: As more project teams specify lowcarbon products, suppliers and manufacturers are scrutinising their Scope 1, 2 and 3 emissions to remain competitive. A record 108 Environment Product Declarations were published in 2023, according to EPD Australasia. In total, 274 EPDs have been independently verified and registered with EPD Australasia, building valuable and comparable data about the lifecycle environmental impact of products. EPDs are currently competitive differentiators for product manufacturers, but as more EPDs become available over time, we expect the competitive advantage to be in the carbon impact delivered.
4. New reporting standards cover Scope 3 emissions: In October 2023, the Australian Accounting Standards Board released an exposure draft for disclosure of climate-related financial information, aligned with the International Sustainability Standards Board’s new standards. This proposal, applying to annual reporting from 1 January 2025, would require companies to prepare a ‘sustainability report’ that includes Scope 3 disclosures. This is expected to bring an uplift in data expectations around embodied carbon reporting, as even smaller companies not required to report will be approached by their clients and customers for Scope 3 emissions data.
5. NABERS embodied carbon tool: NABERS undertook public consultation of 10 proposals in 2023.
After assessing feedback, NABERS has settled on a development pathway for a framework to measure, benchmark and certify embodied carbon of building materials and construction. Currently slated for release in late 2024, the framework should align and fast-track benchmarking efforts so the industry can set robust upfront embodied carbon reduction targets. The NSW Government has noted the NSW Sustainable Buildings SEPP will use the NABERS embodied carbon framework, upon its release. The GBCA has also flagged its intention to align Green Star’s upfront carbon calculation methodology with the NABERS framework. NABERS is currently testing the draft framework on pilot projects.
As Slattery’s database of real-world project upfront embodied carbon benchmarks expands, we will continue to publish our data. As leading carbon planners, we are committed to sharing information and educating industry participants about how they can begin to address upfront embodied carbon now.
There are choices we can make on building projects today that can enhance their value while uplifting industry capability, incentivising innovation and helping us to meet net zero targets tomorrow.
This article was first published by Slattery, a property and construction advisory firm operating across Australia. The report and other publications in this series are available at slattery.com.au/kaizenpapers.
Citation: Dean, T., Mortensen, J. and Wijesuriya, S. (2024), Let’s be upfront about upfront carbon: Upfront embodied carbon benchmarking, Slattery.
By Matt Stevens PhD & John Smolders AM
A construction project’s success is determined by safely meeting its estimated cost, schedule, and quality per the owner’s contract. In particular, the financial result is critical to a construction firm due to its funding improvement initiatives. For the project owner, the initial budget is enough for the structure envisioned. The builder and their client must have effective tools for cost budgeting before the contract agreement stage. Additionally, this plays an important role in both parties’ portfolio management. An incorrect cost forecast for either stakeholder can quickly turn an estimated profit into a loss across multiple projects. This cost change prediction becomes critical as a contract clause to protect the project owner (if costs decrease) and construction organisation (if costs increase).
Cost escalation, especially in construction, has been a significant factor since the dawn of the COVID-19 pandemic. The most prevalent effects are housing affordability and increased bankruptcies. These effects have made cost increases a root cause of several societal ills.
For the past few decades, Rise and Fall (R&F) adjustments linked to the CPI have taken a backward step due to stable working conditions in the industry. Since the COVID pandemic, however, that stability has dramatically changed, as evidenced by the escalation of company liquidations and incomplete projects dotted across the country. The Master Builders Association introduced R&F clauses in the 1930s due to unstable working conditions resulting from WW1.
It was reintroduced in the 70s and 80s due to overseas conflicts that impacted Australia’s supply chain and labour availability. Standard contracts maintain an R&F clause, such as in AS4000-1997 and AS4902-2000. Bespoke clauses are usually included on larger projects such as infrastructure. Data used to calculate R&F come from differing sources. The Australia Bureau of Statistics (ABS) publishes its quarterly Producer Price Indexes (PPI), one of which is Input to the House Construction Industry, which construction magazines widely publicise. The PPI is historical and is not predictive. This paper demonstrates a well-founded indicator that can be adapted to calculate cost fluctuations today and in the future; however, our formula and process are starting points. Our research aimed to use historical data to identify significant correlations that predict price changes within a range. This, of course, would benefit construction contractors, property developers, and other stakeholders. We captured market pricing of products and services over two decades.
Data science was the main tool of this project. Our process was to turn historical data into a credible predictive model. We engaged research teams from North Dakota State University and Western Sydney University to create a residential cost prediction process, inputs, and equation. The work presented here is a starting point. Selected data is from the Australian Bureau of Statistics and the Reserve Bank of Australia.
Prediction is a hazardous business. Any capitalistic market is chaotic, and construction appears to be more so. The probability of error is high.
Constructing work involves many uncontrollable factors that affect core dynamics, such as government funding impacts, i.e., significant subsidies have been correlated historically to inflation. From industry experience, some inputs may seem to have a statistical effect but, upon statistical testing, do not. The most famous examples are the correlation between ice cream consumption, hot weather, and police arrests. They are positively correlated but logically flawed.
We do not claim Intellectual Property but ask that you provide proper attribution to us and our university due to its support of this research.
All predictive models overlook one or more statistical problems. Often, these issues are structural or conditional and require disclosure of their nature and severity.
1. Low signal/noise ratio: The “rule” asserts that a minimum 15x events ratio is required for a low signal/ noise ratio. This is not possible.
2. Intercept: one needs 96 observations to accurately estimate the intercept so that the overall predicted risk is within a ±0.1 margin of error of the true risk with 0.95 confidence. This was not possible.
…About onethird of contractor bankruptcies would have been eliminated if this algorithm had been included in contracts.
3. Static Assumptions: Another issue is that this model must assume that asset returns and volatilities remain stable over time. In reality, market conditions change, affecting returns and risk levels. For example, the changing nature of contracting, such as the increased use of services (less direct labour), “smarter” equipment, innovative materials, and modernising methods.
4. Single-Period Analysis: Our design captures a single period (two decades). In reality, the built environment horizons vary, and longterm dynamics may differ from shortterm trends. Also, there is a timing issue, i.e., when does a factor have its most significant impact on cost, such as immediately or a year later?
5. Market Frictions: The model doesn’t consider changing market frictions, such as liquidity constraints, changing consumer preferences, or regulatory creep.
6. Data Reliance: Historical data drives the model’s outputs. Due to changing economic conditions and unforeseen events, future price changes may not mirror the past.
We have derived the model equation as: Y = -201.485 + (4.2463*E) + (0.0596*C) + (-1.122e-01*M) + (0.5008*H) + 2.8178e-11*B)
Correlations of Each Factor:
E = The Australian Employment Rate is +.7181
C = The International Commodity Price Index is +.8043
M = International Base Metals is +.6771
H = Australian Housing Credit is -.8294
B = The Australian Broad Money Supply is +.9842
Key statistical test outputs include R-squared is 0.971, and F-statistic is 115.4.
Reviewing the difference in cost escalation over the past two decades, our algorithm delivers cost savings to the owner, and contract increases to the builder depending on the year. It is important to note that these are reimbursements of expenses with no profit or overhead – very fair. Analysing COVID-era inflation and resulting insolvencies, we estimate that about one-third of contractor bankruptcies would have been eliminated if this algorithm had been included in contracts.
A comparison of the Consumer Price Index and Housing Index Cost demonstrates the hazard and opportunity of including an R&F clause in residential contracts. The period 2020 to 2022 shows the devastating increases that bankrupted many builders.
This algorithm provides a prediction and should not be used solely to make costs forecasts. Other factors should be considered but are not quantifiable, such as legislative activity and man-made disasters. Additionally, the housing market is chaotic, and economic “animal spirits” make consistently accurate forecasting a challenging vocation. However, when markets are calm, not chaotic, less destruction occurs. For example, consumers receive credits when costs decrease, and contractors receive reimbursement when costs increase. Everyone receives mostly what they bargained for at the beginning of the project.
As an analogy, the stock market is notoriously irrational. However, if four reputable share advisors unanimously recommend ‘buy’ or ‘sell’, following their advice has a high probability of benefit.
The same applies here – more independent predictions outside of ours should be reviewed to make this significant economic decision, that is, to construct or not.
We predict our continuing research will become more holistic and complete. In the coming decade, Australia may experience novel conditions such as war, currency devaluation, and severe legislative activity that have not been part of our two-decade data capture. Upon re-analysis, this will refine the equation. Additionally, the construction process will change as it has always.
A publicly disclosed cost forecasting algorithm is part of value-based practitioner-academic research outputs. Our team’s work provides a starting point that furnishes equitable protection for residential stakeholders. In all, future cost chaos in the built environment can be lessened.
By Sepani
The construction industry is one of the largest industries contributing to the global economy. Being the largest contributor to many countries’ economies, there is no surprise that the construction industry consumes most resources and raw materials from nature and is one of the most resourceintensive industries. In percentage terms, this consumption accounts for about 50% of total global raw material use and 36% of total global energy use. On the other hand, the construction industry generates millions of tonnes of solid waste and has high embodied energy requirements, which results in substantial CO2 emissions all over the world. According to the Australian National Waste Report (NWR) 2020, 27 million tonnes of Construction and Demolition (C&D) waste are produced in Australia annually along with 25% of the total yearly carbon emissions. These facts have made it urgent for the construction industry worldwide to find more sustainable alternatives.
The main problem with the construction industry is its ‘take, make, dispose’ approach, where materials are used to build structures and then thrown away when they are no longer needed, even though they could be reused in another project. Transforming into a circular economy model would be ideal to become more sustainable, where resources are circulated at their highest economic value. Therefore, a circular economy model will minimise impacts on the economy, society and the environment.
The Ellen MacArthur Foundation (EMF), one of the pioneer organisations of the concept has defined the circular economy (CE) as, “An industrial system that is restorative or regenerative by intention and design”. Furthermore, EMF has expanded the concept by adding three main principles for CE namely, 1) eliminate waste and pollution; 2) circulate products and materials at their highest economic value;
and 3) regenerate nature. Although various definitions of the concept of CE have developed over time, the three principles outlined here remain commonly used.
...There would be a high contribution to the Australian GDP growth and job market through circular economy initiatives.
CE has been implemented gradually across many industrial sectors at different levels since its introduction in the late 90s. However, the construction industry is still in the early stages of adopting CE despite the vast benefits it can generate within the industry. Currently, a growing level of awareness can be seen within Australia for a circular construction industry.
Numerous state-level initiatives have been implemented that encourage the transformation to CE in the construction industry. For example, the South Australian government has developed different initiatives and policies about recovering and recycling C&D waste. The New South Wales government also published a CE design guideline for the construction industry in 2023.
The construction industry is showing greater awareness of CE benefits. Built’s report on ‘Demystifying the Circular Economy’ in 2022 identifies Green Building Council Australia (GBCA), Planet Ark, Circular Australia and RMIT’s Circular Economy Hub as the main organisations in Australia that pursue many initiatives related to a circular construction industry. According to an analysis done by PwC Australia in 2021, moving towards circular construction will generate $1,860 billion of direct economic benefits over twenty years and save 165 million tonnes of CO2 per year by 2040.
Similarly, according to KPMG, there would be a high contribution to the Australian GDP growth and job market through circular economy initiatives in the construction industry. Thus, it is high time for the Australian construction industry to step into a circular construction industry.
The transition towards a circular construction industry necessitates alterations in the current construction practices.
...CE would mitigate many negative impacts on the environment including climate change, ozone layer depletion and acidification via reduced waste generation and carbon emissions.
It further requires a thorough understanding of the whole construction process and a focus on applying circular economy practices at each stage of a construction project. Figure 1 shows some of the prevalent CE practices that can be adopted throughout the construction lifecycle based on the ongoing research of the authors.
Successful implementation of these CE practices within a construction project would have many impacts on the economy, society and environment, which are majorly considered to be positive.
Some major economic effects of CE include cost savings, revenue generation, reduced raw material purchasing costs, and reduced operational costs. CE transition will inevitably have social consequences such as new employment opportunities and improved community well-being.
Furthermore, CE would mitigate many negative impacts on the environment including climate change, ozone layer depletion and acidification via reduced waste generation and carbon emissions.
Assessing and monitoring transitions toward CE is crucial, as without an evaluation framework, CE initiatives are not sustained. Successful CE assessments should combine a circular flow assessment and an impact assessment of CE practices.
Circular flow assessment measures the circularity of the practice itself and the impact assessment measures the effect of the practice on the economy, society and environment. Determining the impacts that each CE practice would create in the economy, society and environment is pivotal in project execution. Often, CE practices are not utilised in construction projects as stakeholders may not be aware of its benefits for the economy, society and the environment. Sometimes, CE practices may not create equal benefits for all aspects.
For example, the material recycling process is sometimes more expensive than traditional material manufacturing even though it is considered an environmentally friendly practice.
mdpi.com/2075-5309/14/3/653
Furthermore, end-of-life dismantling requires a lot of labour, whereas traditional demolition can be done with less labour involvement. This will create costs for the client but benefit the community through job creation.
Thus, project stakeholders would benefit from proper impact (costbenefit) analysis, when it comes to implementing CE practices in a construction project.
Several assessment mechanisms of CE have been developed across many industries aligning with CE principles, level of implementation, and sustainability aspects. Circularity indicators play a vital role in assessing CE implementation as analytical tools.
However, these indicators are less capable of comprehensively assessing the impacts of CE practices, thus separate impact assessment methodologies are required to measure the impacts of applying CE practices in a particular context.
Often, the environmental, social and economic impacts of CE are measured using Life Cycle Assessment (LCA), Life Cycle Cost (LCC), and Social Life Cycle Assessment (S-LCA) respectively. In addition, methods like Life Cycle Sustainability Assessment (LCSA) and Cost Benefit Analysis (CBA) are used to collectively measure economic, social and environmental impacts.
A quantitative analysis method thus provides objective and influencing results for environmental impacts.
A simple, frequently used method that uses readily available data to assess the economic impacts.
Uses a wide range of social indicators to evaluate the social impacts.
An integrated method of LCA, LCC and SLCA, which provides a full assessment of all impact categories.
Assess both positive and negative economic, social, and environmental impact (costs and benefits) using a single unit of measurement (monetary terms).
These methodologies have their own strengths and weaknesses as shown in Table 1.
A construction project is widely recognised as a complex environment with involvement from different stakeholders at different life cycle stages. It is paramount to improve coordination and participation of all stakeholders to successfully implement CE in the construction industry.
The gearing stage would be the design stage of the project since many
Lifecycle Assessment (LCA)
Lifecycle Cost (LCC)
Social Lifecycle Assessment (S-LCA)
Lifecycle Sustainability Assessment (LCSA)
Cost Benefit Analysis (CBA)
Uses different units of measurement thus, less harmonisation in the result. Focus on negative impacts.
Less competent in providing a full assessment of environmental and social impacts. Only focus on costs.
Requires different data types (qualitative, quantitative) and no common unit for assessment.
The process is complex as it integrates three different methods and needs to use alternative mechanisms to convert the results into a single unit.
Difficult to assess certain impacts in monetary terms.
later activities are dependent on the decisions taken at the design stage. Finalising the design incorporating different CE initiatives, establishing their budget requirements, and assessing the impacts created through these initiatives are vital activities in the design stage.
In particular, the architects, engineers, quantity surveyors and sustainability consultants, should be involved in these activities and make decisions on the best initiatives to be applied in the considered project. Quantity surveyors perform the role of cost management throughout the life cycle of a construction project from the concept stage through acquisition and operation and finally to disposal.
In accordance with the competency guidelines established by many professional bodies, the professional quantity surveyor is competent in all activities related to cost estimating, cost planning, cost control, procurement management, contract management, feasibility studies, and financial execution of projects.
During the initial design stages, quantity surveyors play a vital role in supporting decision-making by comparing different design options, preparing cost plans, carrying out feasibility studies and assisting in determining the kind and quality of materials.
Correspondingly, in the CE context, the impacts that different CE initiatives would create on the economy, society and environment can be assessed by quantity surveyors to support overall decision-making.
The AIQS competencies that can be mostly related to the quantity surveyor’s involvement in assessing the impacts of CE initiatives in a construction project can be identified in Figure 2.
Source:
A considerable number of AIQS core and support competencies are aligned with the assessment of the impacts of CE implementation, which makes a quantity surveyor the ideal professional in the consultancy team to carry out such assessments. Methods like CBA and LCC are frequently used by quantity surveyors during the feasibility assessment stage.
Further, the quantity surveyor needs to be knowledgeable about other assessment methods such as environmental LCA and social LCA to perform a complete CE impact assessment in a project.
for Quantity Surveyors and Construction Economists
Being in the consultancy team from the beginning, the quantity surveyor can build relationships with all other professionals involved in the project, ultimately resulting in the effective implementation of CE in construction projects. Clients may be unaware of the extent to which implementing CE can benefit their projects, thus, quantity surveyors have a major role in advising these benefits.
Like any other professional, quantity surveyors are also responsible for contributing to achieving the United Nations Sustainable Development Goals (UNSDGs) and moving away from traditional financial cost comparisons to include environmental and social costs/benefits of various project options.
As the specialists responsible for construction costs and quantities, the quantity surveyor’s role in implementing the circular economy can be extended to other areas such as circular flow assessment of material and energy, among others in the future.
This article was written by Sepani Senaratne MAIQS, CQS, Associate Professor, Iresha Gamage, Doctoral researcher, and Srinath Perera MAIQS, Professor, from the Centre for Smart Modern Construction (c4SMC) Western Sydney University.
By Payapps
In the pursuit of progress and profit, the construction industry, like any other, seeks ways to enhance efficiency, reduce errors, and make the best use of its resources. However, Payapps’ findings show that a sizeable portion of the sector continues to rely on outdated manual tools such as spreadsheets for managing progress claims, resulting in several notable drawbacks.
Spreadsheets have long been a trusted tool for quantity surveyors tasked with administering construction projects and managing progress claims. However, as the pace and complexity of projects continue to increase, builders are finding traditional approaches no longer support the modern demands of the industry.
According to Payapps’ “Building the Future: Navigating Challenges and Opportunities for Quantity Surveyors and Contract Administrators” report , a startling 26% of quantity surveyors still rely on manual processes for critical functions like progress claims. Yet these traditional methods introduce significant inefficiencies that impact construction schedules and budgets. A recent Payapps webinar on leveraging specialised construction technology also highlighted that reliance on manual workflows is a major hurdle that can be easily overcome with innovative solutions already available and accessible now to construction professionals.
46% of quantity surveyors spend six or more hours per week on manual administrative tasks ranging from tracking progress claims to administering contracts.
Managing projects with manual processes like spreadsheets is labourintensive and prone to errors
This leads to wasted time reconciling paperwork instead of focusing on high-value tasks. Additionally, manual workflows limit real-time visibility across project teams, causing delays and misunderstandings that can derail projects.
Scott Lockwood, Head of Customer Success at Payapps, highlights these limitations: “While spreadsheets are excellent for data analysis, they are not designed for collaborative project management. They create silos of information and can lead to significant delays and disputes.” This inefficiency is not uncommon – over 64% of construction projects in Australia regularly experience overbilling due to manual data entry errors.
Compliance is crucial in construction, ensuring that every phase of a project meets regulatory standards and contractual obligations. For quantity surveyors, this involves numerous compliance-related tasks that are both time-consuming and complex.
Around 24% of construction professionals spend over six hours per week managing compliance within their progress claim processes.
These tasks consume valuable time that could be better spent on strategic project management. The ever-evolving regulatory landscape only adds to the challenge, requiring continuous learning and adaptation from project teams.
In a sector already strained by labour shortages, the burden of compliance can escalate project costs and lead to penalties for non-compliance.
Time-saving automation tools like Payapps can alleviate this burden. Joanna Rivers, CFO of ATG Projects, shares her experience: “Switching to Payapps has been a game-changer for us. The real-time visibility and automation have significantly reduced errors and improved our subcontractor collaboration. Compliance is no longer a concern, allowing us to focus on delivering quality projects on time.”
24% of quantity surveyors spend 6+ hrs chasing subcontractors on compliance documentation.
One of the standout features of Payapps is its ability to integrate seamlessly with leading construction ERPs and accounting software. This integration ensures consistency and accuracy across all financial and administrative functions. With 22% of quantity surveyors seeking greater technology integration with existing systems, and 34% desiring automated workflows, Payapps addresses these growing needs effectively. Additionally, Payapps also includes comprehensive reporting tools, such as retention ageing reports, which are crucial for maintaining transparency and compliance.
According to the Payapps “Building the Future” report, 72% of construction professionals acknowledge the substantial benefits of integrating digital tools into their workflow. This highlights a strong desire for built-forpurpose tools that offer automation, enhanced collaboration, and standardised processes – needs that Payapps is designed to meet.
Payapps streamlines construction workflows by consolidating all progress claim data across multiple platforms, ensuring everyone is working on the same page, reducing misunderstandings, and fostering more effective communication.
Toni Hall, Group Commercial Business Systems Manager at Buildcorp highlighted Payapps integration capabilities: “The seamless integration of Payapps with Jobpac is crucial for Buildcorp’s operations. We don’t have siloed systems for safety, quality, financial, and commercial functions – you can’t implement a system in isolation from the rest of the business. For Buildcorp, there’s a lot of teamwork and collaboration involved.”
61% experience a positive impact when adopting specialised digital tools to manage their construction projects
The advantages of adopting specialised construction solutions extend far beyond time savings. Standardised progress claim processes facilitated by a digital tool such as Payapps help mitigate financial risks by ensuring all parties work from a single truth source. Progress claims can be simply submitted, reviewed, and approved through an auditable digital workflow, reducing errors and disputes that often lead to cost overruns and project delays.
Functional reporting features within Payapps easily generate audit-ready documentation, from payment schedules and compliance requirements to evidence documents. These can be conveniently produced with a click to substantiate adherence to state-based legislation.
This provides reassurance for both internal operations and external audits, protecting businesses from costly noncompliance penalties. Scott Lockwood sums up why adopting tools like Payapps significantly enhances project outcomes: “Embracing technology is not just about staying current; it’s about paving the way for a more efficient and collaborative future in construction.”
The clear benefits of leveraging adaptive progress claims technology such as Payapps are not just theoretical; they are backed by realworld success stories from firms that have adopted simplified solutions to address complex challenges within the construction project lifecycle. For instance, ADCO, one of Australia’s oldest and most established construction companies, experienced an outstanding 50% improvement in their progress claims processing times This big leap in efficiency allowed the rapidly expanding company to grow from three initial projects to 50 projects nationwide within just one year of rolling out Payapps, an impressive change management feat by any standard.
69% of construction professionals are open to new technologies to help them do their jobs more efficiently.
For quantity surveyors, moving away from spreadsheets and manual workflows is not just a trend but a necessity.
Specialised construction technology like Payapps offers a clear path to overcoming the inefficiencies and risks associated with traditional methods. By embracing a digital tool such as Payapps, quantity surveyors can enhance their productivity, improve collaboration with subcontractors, reduce financial risks, and contribute to the successful delivery of construction projects.
For a deeper understanding of how Payapps can help you build better together, head to our web page Payapps for Quantity Surveyors (payapps.com/quantity-surveyor)
Ditch the spreadsheets and embrace greater productivity and collaboration with your team and subcontractors. Discover Payapps for Quantity Surveyors now.
payapps.com/quantity-surveyor/
By EAP Assist
A positive workplace environment is where individuals are respected and valued. There is a clear allocation of roles, expectations are transparent, and everyone has an equal opportunity to contribute and be recognised for their work. It can also involve mentorship programs that help employees develop skills or grow in their careers. A positive workplace environment, by definition, is beneficial to healthy work-life balance and productivity.
In addition, workplaces with healthy environments have policies and procedures in place to address employee complaints promptly and effectively. And finally, team events that focus on enhancing employee engagement promote camaraderie among co-workers instead of competition. By creating a solid foundation from the ground up, organisations build a healthier workplace environment where workers enjoy coming to work each day.
A positive workplace environment is built on the foundation of trust. With mutual trust in the core, the other elements of positivity follow. In addition, a positive work environment is characterized by a culture of transparency, communication, and mutual respect across all levels. Employees know what is expected of them, and feel free to communicate with their managers about any questions or concerns they may have. Furthermore, as trust is key to building a positive culture, every employee is willing to act according to company values and standards without question.
A positive workplace environment has cooperation among its foundations. Cooperation leads to creativity, initiative, and teamwork – characteristics essential to work success. Employees work together as a team to achieve common goals, and they value collaboration over competition. This cooperative environment encourages employees to give maximum effort in their job duties, which leads to improved productivity and greater success for the team.
A positive workplace environment reinforces proper behaviour from everyone. Employees comply with company values and standards. Furthermore, they have to treat others with respect, regardless of their position or status within the company. This type of environment fosters an ethical work culture where employees take pride in working hard and doing what is right, not just for themselves but also their team members. The managers and leaders themselves establish the proper behavioural standards that incorporate accountability and loyalty.
A healthy workplace environment always values communication. Communication is critical to building trust and cooperation, as well as removing conflicts. Employees can communicate effectively with their managers and fellow employees to work harmoniously in healthy workplace cultures. Open communication channels allow for effective coordination of tasks and improved employee morale.
A positive workplace culture aids the growth of the whole team. With each employee striving to improve their skills and knowledge, a positive work environment nurtures creative ideas and innovation. Employee growth continues to be an essential part of a positive company culture, as it helps employees feel appreciated and valued. Moreover, it helps them personally and professionally, ensuring that they do not remain limited to the completion of routine tasks day after day. In addition, continuous learning allows employees to keep up with trends, which leads to increased productivity and better results for the organisation. An environment that inherently values everyone and pushes them towards improvement is a great asset for any team.
An essential feature of a positive workplace environment is that everyone builds it together. While the managers can outline core values and ensure that they behave appropriately, workplace culture comes together only when everyone actively builds it together. The management does not enforce a healthy workplace culture alone. Instead, the team members understand and live those values to make the space positive for everyone. It requires extensive participation –from developing the ideas to practising carrying them out and resolving issues.
By Imogen Lyons
To ensure a sustainable built environment and progress towards a net zero future, every sector must transform. Innovation and new technologies continue to improve how buildings operate, bringing productivity, efficiencies and greater user comfort – but the industry is still finding its feet in reducing built-form emissions. In the race to meet global agreements and targets for emissions reduction, we need to work together to leave a lighter footprint.
Reducing embodied carbon needn’t be viewed solely through an environmental lens.
Expectations and requirements for greener construction materials, processes and activities are pushing the envelope. While we can retrofit and continually update technologies as they become available to reduce operational carbon, upfront embodied carbon is locked in before the building opens and is often heavily defined by the very early stages of design.
Reducing embodied carbon needn’t be viewed solely through an environmental lens. Greener buildings can attract lower lending costs and achieve premiums with investors, purchasers and tenants. Shrinking a project’s emissions is likely to pay off in the long term, especially as sustainability standards, certifying bodies and governments become more stringent, stronger requirements and penalties emerge, and carbon offsetting becomes less acceptable, more expensive, and harder to achieve.
Across the world, we are seeing carbon measurement and reduction targets embedded into permitting processes, government policies, frameworks and legislation. In Australia, New South Wales has committed funding to ensure transformation and, naturally, Victoria will follow. In New Zealand, it is already mandated. We also see evolving requirements in Asia for certifications such as Green Building and LEED, with local and international investors driving the need to measure and report on embodied carbon.
Focusing early on the building skeleton… will ensure that the heaviest emitters are considered.
Let’s start building experience now, sharing our learnings and moving to minimise our industry’s steep-capped footprint while we house, teach, care for, entertain and transport our evergrowing population. There will be a price tag, but we can work together to limit it before action on emissions becomes mandatory.
Every developer will have different objectives, priorities and targets for their carbon budget – whether it’s pursuing GBCA or NABERS accreditations, meeting internal stakeholder targets or complying with government requirements. Reputable advice and support will help clarify goals and map pathways to achieve them.
Quantity surveying goes hand in hand with measuring upfront embodied carbon. As a design progresses and is costed for currency, it can be costed or rated for carbon too.
Seeking
guidance, exploring the industry and trying new lowercarbon opportunities adds value and can
be managed for cost.
Choose an advisor experienced in your project type and one who understands your priorities. As with value engineering, options to reduce embodied carbon and cost must be weighed against a building’s function, purpose and brand. Cost-benefit analysis needn’t be limited to capital expenditure.
The greatest opportunity to reduce embodied carbon is from day one –when it is still possible to identify where all priorities lie, optimise design, explore alternatives, and consider low-carbon, recycled or reused materials. Time pressures associated with redesign make it inefficient to revisit a concept design and trying to adjust for carbon later can increase costs.
Focusing early on the building skeleton (structure and façade) while also provisioning for a range of mechanical and electrical solutions will ensure that the heaviest emitters are considered. As the building design evolves, additional elements can be weighed for carbon cost benefit, ensuring the full project team is alert to the greatest impacts and applies learnings to future projects.
Simply applying a benchmark cost percentage to a reduction target may not be appropriate… …What gets measured gets managed.
Materials engineering is moving fast, with a constant stream of innovative new products. Seeking guidance, exploring the industry and trying new lower-carbon opportunities adds value and can be managed for cost.
The evolving landscape of options and standards brings some uncertainty. Simply applying a benchmark cost percentage to a reduction target may not be appropriate given the number of projects available to be referenced, the ever-expanding market for green materials, and often unstandardised approaches. Every project and certification option is unique, so engage with consultants who can look at the project in detail, determine the likely pathway to realise objectives, and price it appropriately.
Ideally, your consultant should have access to rich, current, sector-specific data to inform their calculations and recommendations – and the ability to collaborate with a broader team with on-the-ground experience across the lifecycle of your project type. Generic references have limitations in representing how each development will be operated and managed over its life. The ability to draw on a pool of information will refine the cost-benefit analysis, drawing on experience rather than templates.
Whether or not your construction project has specific reduction targets, consider incorporating policy and legislative changes into contractual agreements to protect you throughout the often lengthy duration. It’s a good idea to clearly define carbon reduction parameters, identify levers and triggers for change, and determine how to deal with variations, extensions of time, latent conditions and the like. These aspects may not affect the materiality of the building but can affect site operations – and, in turn, the carbon footprint.
It’s often said that what gets measured gets managed. Whether or not you’re targeting accreditation or certification, there’s no doubt that transparent and credible costing and tracking of embodied carbon will drive our sector to use less, recycle more, build smarter, and learn. It will certainly add value and may save money too.
Despite challenges and uncertainties, reducing embodied carbon is a rich opportunity to create sustainable and resilient built environments.
By John Corry and Syidah Arnold MAIQS, CQS
We have recently learned that generative AI, or GenAI, can build an entire website from a hand-drawn diagram, troubleshoot for technicians in the field, and win ‘Where’s Wally?’ in seconds.
The use cases for GenAI are evolving so rapidly that what is fresh today will be yesterday’s news by the time you read this.
We have entered a new epoch – our own Cambrian explosion. But this time the proliferation is not of new species, but of innovative applications that spark new ideas.
McKinsey¹, which hailed 2023 as GenAI’s “breakout year”, estimates that the technology could add US$4.4 trillion annually to the global economy. IDC forecasts² that enterprise spending on GenAI services, software and infrastructure will grow from US$16 billion in 2023 to $143 billion in 2027.
A year on from ChatGPT’s launch, there are now thousands of tools available. Many workers are using GenAI for research, to generate or iterate ideas and write emails, and Deloitte estimates that daily users of GenAI³ are saving around 5.3 hours each week.
Dozens of ‘business-ready’ Gen AI⁴ use-cases already apply to
construction: site plan optimisation, material design review, virtual field assistance, cost analysis and more. And 55% of businesses, globally, are either piloting or producing GenAI solutions, according to Gartner⁵.
Large-Language-Models (LLMs) like ChatGPT, Luminous and Llama, put the power of GenAI into everyone’s hands. We are experimenting in the AI playground with various LLMs, using our treasure trove of data to run queries and extract fresh insights to age-old problems.
We have developed our digital system well ahead of the curve and have been innovating with data for many years now. Our team is focused on GenAI initiatives that support innovation and unearth value that has, until now, been hidden or out of reach. We are investigating data warehouse options to aggregate disparate sources of anonymised data – from cost estimates to building information models – into one accessible and digestible repository. This processed data can be fed into an LLM and quantity surveyors will be able to ask a chatbot questions. This will catalyse our own Cambrian explosion.
1 McKinsey 2023, ‘Gen AI and the future of work’, Five Fifty, <https://www.mckinsey.com/ quarterly/the-five-fifty/five-fifty-gen-ai-and-the-future-of-work>.
2 Afshar, V. 2023, ‘How AI reshapes the IT industry will be ‘fast and dramatic’’, ZDNET, 31 October, <https://www.zdnet.com/article/rote-automation-is-so-last-year-ai-pushes-moreintelligence-into-software-development/#google_vignette>.
3 Rumbens, D. 2023, ‘Generation AI: Ready or not, here we come!’, Deloitte, 6 September, <https://www.deloitte.com/au/en/services/economics/blogs/generation-ai-here-we-come. html>.
4 Deloitte AI Institute 2023, The Generative AI Dossier, available at <https://www2.deloitte. com/content/dam/Deloitte/us/Documents/consulting/us-ai-institute-gen-ai-use-cases. pdf>.
5 Gartner, Inc. 2023, Gartner Poll Finds 55% of Organizations are in Piloting or Production Mode with Generative AI, 3 October, <https://www.gartner.com/en/newsroom/pressreleases/2023-10-03-gartner-poll-finds-55-percent-of-organizations-are-in-piloting-orproduction-mode-with-generative-ai>.
We are also using machine learning (ML) – statistical models that can infer patterns or trends to make predictions – that allow us to ask a multitude of ‘what if?’ questions. After the ML model determines the pattern, an LLM provides a human-centric way to query the results. Essentially, the quantity surveyor chats to the LLM that has ingested the ML’s results. The quantity surveyor can then better monitor and mitigate potential risks, such as cost or time overruns.
It sounds obvious, but when GenAI can tell us exactly how many hinges are required for each of the doors in a 50-storey tower, quantity surveyors can have extra time to spend value-adding.
Importantly, we will still be required to review and verify data, identify inconsistencies and find efficiencies. But ahead of us lies the promise of greater efficiency and the possibility of more time to spend on high-value tasks that only thinking and feeling human beings can execute.
Working with GenAI does come with risks, although eight in 10 business leaders⁶ believe that the positives outweigh the pitfalls. Hallucinations –when LLMs generate convincing but inaccurate information – are a new challenge and a type of information error we haven’t encountered before.
LLMs are designed to please the person asking the question, even if the answer is wrong, but we are learning that these hallucinations are usually the result of dataset deficiencies.
Another obvious area of concern is data privacy. LLMs are only powerful because they’ve been trained on the creative output of human beings; a recent analysis⁷ found 170,000 pirated and copyrighted books were the source of one tech titan’s dataset. Employees are also uploading confidential information into ChatGPT without considering how that data may be used.
No job role will be untouched by GenAI, and Goldman Sachs analysts⁸ have predicted that more than 300 million of today’s jobs will be automated. But technology has traditionally created more jobs than it has displaced. According to the World Economic Forum’s Future of Jobs Report 2023⁹, the impact over the next five years will be net positive.
GenAI will also require all of us to rethink the way we think. One illuminating research project undertaken by Boston Consulting Group¹⁰ found a 40% improvement in performance when skilled professionals used GenAI for creative ideation. But when the same skilled professionals were asked to undertake business
problem solving – a capability outside GenAI’s current frontier but well within their own remit – it led to a 23% decrease in performance.
What this tells us is that GenAI can identify unexpected, and sometimes even counter-intuitive patterns and correlations that can spark new ideas. But human intelligence determines how we use these ideas.
Today’s quantity surveyor requires a different set of skills to those we have relied on in the past. Our role is no longer limited to preparing cost estimates, but to harnessing data and unlocking insights that create new value for clients. As we do this, quantity surveyors will move up the value curve.
When ChatGPT launched to the public in November 2022 it was like watching Roger Bannister break the four-minute mile barrier. Now we know it can be done. We understand that GenAI will change everything – we just don’t know how yet. But just as the Cambrian Explosion transformed the earth’s biodiversity, GenAI is reshaping the digital ecosystem and ushering in a new era of boundless possibilities.
6 Gartner, Inc. 2023, Gartner Poll Finds 55% of Organizations are in Piloting or Production Mode with Generative AI, 3 October, <https://www. gartner.com/en/newsroom/press-releases/2023-10-03-gartner-poll-finds-55-percent-of-organizations-are-in-piloting-or-production-modewith-generative-ai>.
7 Reisner, A. 2023, ‘Revealed: the authors whose pirated books are powering generative AI’, The Atlantic, 19 August, <https://www.theatlantic. com/technology/archive/2023/08/books3-ai-meta-llama-pirated-books/675063/>.
⁸ Briggs, J. & Kodnani, D. 2023, ‘The potentially large effects of artificial intelligence on economic growth’, Goldman Sachs, 26 March, <https://www.gspublishing.com/content/research/en/reports/2023/03/27/d64e052b-0f6e-45d7-967b-d7be35fabd16.html>.
⁹ World Economic Forum 2023, Future of Jobs Report 2023, available at <https://www3.weforum.org/docs/WEF_Future_of_Jobs_2023.pdf>. ¹⁰ Candelon, F., Krayer, L., Rajendran, S. & Martinez, D.Z. 2023, ‘How people can create – and destroy – value with generative AI’, BCG, 21 September, <https://www.bcg.com/publications/2023/how-people-create-and-destroy-value-with-gen-ai>.
By Kevin Windross FAIQS (Ret.)
Anyone who’s been embroiled in a contractual claim for loss and expense will know the value of well-kept records, accuracy, and overall purpose, either from the contracting entity’s position or the client’s organisation.
Gone are the days when the supervisor’s incomplete diary notes thrown into a drawer in the site shed constitute good records. However, that is not to say they are of no value. The primary position we should take is that any records are better than no records, but superior records are built around certain guiding principles, one of which is factuality.
Adequate records should as a minimum contain resources used, plant, weather conditions, listings of documents provided on a particular day, delays, progress achieved, and the like. There is a wealth of information contained in records that is eminently usable by the claim’s consultant and conversely, usable by the client’s consultant, tasked with defending claims when they raise their ugly head.
This glamorous word is used to describe most construction records these days. What is a contemporaneous record? Many on construction sites wouldn’t know what this means as they go about their daily and hectic routines.
But the word contemporaneous (adjective) means existing, occurring, or beginning at the same time or during the same period as something else.
In the case of committing the records to paper (or hard drive), this means they should be made within, in my opinion, no longer than a day or at most 2 days after the event (read day).
Records should not be created based on hearsay and should be created by a person present or nearby to all items worthy of recording.
For example – during a concrete pour on a high-rise block, the concrete pump malfunctions and is stood idle for four hours.
For example, the record might say: “Foreman advised concrete pour cancelled for the day. Supply issues.”
However, it should say something like: “Concrete pump broke down at 9am and repairs finished by 1pm. Balance of pour cancelled concrete poured 10 cum. Targeted 50 cum.”
If the client was supplying the concretefree issue to the contractor, there would be a preference for the second record to be lodged in the system.
Arbitrators, mediators and adjudicators will, in my view, prefer the latter entry, when the claim for delay inevitably follows.
Records made need to be non-emotive and matter of fact. In life, personalities will clash in everything we do, and the fact that one party does not necessarily see eye to eye with the other does not need recording.
By Jim Doyle
In the fast-paced world of construction, quantity surveyors play a crucial role in managing project costs and ensuring financial transparency. However, the challenge of securing timely payment for services can disrupt not only cash flow but also operational efficiency. This article provides a roadmap, using the Security of Payments Act (NSW) as a reference, to help quantity surveyors across Australia understand how to leverage this legislation for the effective recovery of fees and to assist other stakeholders in using the process to resolve issues and promote project efficiency.
The Security of Payments Act in NSW (SOPA) is designed to ensure that anyone who carries out construction work or supplies related goods and services can recover their payments promptly and fairly. For quantity surveyors, this Act serves as a crucial tool to enforce their right to timely payment.
Quantity surveyors are entitled to progress payments for their services under the Act, as it applies to professional work linked to construction projects.
• Fast-Track Payment Process: The Act facilitates a rapid adjudication process to resolve payment disputes.
“A construction contract means a contract or other arrangement under which one party undertakes to carry out construction work, or to supply related goods and services, for another party.”
The SOPA is engineered to ensure swift payment to parties undertaking construction work or providing related services, including professional services such as quantity surveying. Specifically, the Act covers individuals providing, “architectural, design, surveying, or quantity surveying services in relation to construction work”, under construction contracts (Section 6(1)(b)(ii)).
– Section 4
• Right to payment: Ensures quantity surveyors are paid for their services according to the agreed terms, or, in the absence of such terms, within a statutory timeframe.
“A person who, under a construction contract, has undertaken to carry out construction work or to supply related goods and services is entitled to receive a progress payment.”
– Section 8
As a quantity surveyor, issuing a payment claim under the Act involves a series of strategic steps:
1. Preparing the Claim: Ensure that all services are documented. Payment claims must clearly state the amount due, reference the work completed during the payment period, and clarify the position in respect of each contested element of the claim.
2. Submission Timeline: Payment claims must be submitted according to the timelines stipulated in the contract. For principal to head contractor payments, the due date is 15 business days after a claim is made unless an earlier date is agreed upon. For subcontractors, this extends to 20 business days (Section 11(1A), (1B))
11 Due date for payment
(1A) A progress payment to be made by a principal to a head contractor under a construction contract (other than an exempt residential construction contract) becomes due and payable on – (a) the date occurring 15 business days after a payment claim is made under Part 3 in relation to the payment, except to the extent paragraph (b) applies, or (b) an earlier date as provided in accordance with the terms of the contract.
(1B) A progress payment to be made to a subcontractor under a construction contract (other than an exempt residential construction contract) becomes due and payable on – (a) the date occurring 20 business days after a payment claim is made under Part 3 in relation to the payment, except to the extent paragraph (b) applies, or (b) an earlier date as provided in accordance with the terms of the contract.
3. Payment Schedule Response: The client must respond with a payment schedule stating the amount they intended to pay within 10 business days. If no payment schedule is provided within this time, the full amount claimed becomes due on the due date for the payment (Section 14).
(2) A payment schedule:
(a) must identify the payment claim to which it relates, and
(b) must indicate the amount of the payment (if any) that the respondent proposes to make (the scheduled amount).
(3) If the scheduled amount is less than the claimed amount, the schedule must indicate why the scheduled amount is less and (if it is less because the respondent is withholding payment for any reason) the respondent’s reasons for withholding payment.
(4) If:
(b) the respondent does not provide a payment schedule to the claimant:
(ii) within 10 business days after the payment claim is served, whichever time expires earlier, the respondent becomes liable to pay the claimed amount.
If a dispute arises, either due to nonpayment or disagreement on the payment amount, quantity surveyors can initiate an adjudication process:
1. Application for Adjudication: This must be made shortly after receiving the payment schedule or the due date for payment, whichever is sooner (Section 17).
2. Adjudication Decision: An independent adjudicator will assess submissions from both parties and make a decision, usually within 10 business days (Section 22).
3. Enforcement: Decisions under the Act are binding and can be enforced through the court system if necessary.
• Clear Contracts: Define clear payment terms within contracts to avoid ambiguities
• Proactive Management: Regularly communicate with clients about project statuses and upcoming payment milestones
• Documentation: Maintain detailed records of all work done and correspondence related to payment claims and schedules.
The Security of Payments Act offers a framework for quantity surveyors to secure their fees, minimising financial risks and enhancing business sustainability. By understanding and effectively navigating this legislative environment, quantity surveyors can safeguard their interests and focus more on their core professional activities and assist other stakeholders to resolve payment issues expeditiously.
Quantity surveyors should ensure that their invoices are issued under the Act, correctly identifying the work involved, the project, and the contract under which they’re working as often the impetus the Act gives results in negotiations and agreements which assist project success.
1 Jeffrey, D. 2024, ‘‘No danger’ to residents of Sydney apartment buildings with hundreds of homes ‘at risk of collapse’’, 9 News, 17 Jan, <9news. com.au/national/apartment-complex-northern-sydney-macquarie-park-risk-collapse/00bde588-6f4b-44be-9339-bc967bc82b1b>. ² Fair Trading 2024, ‘Register of Building Work Orders’, NSW Government, <fairtrading.nsw.gov.au/help-centre/online-tools/rab-act-ordersregister>.
THE BUILDING COST INDEX IS PUBLISHED IN THE PRINT VERSION OF THE BUILT ENVIRONMENT ECONOMIST.
IT CONTAINS DATA THAT CAN BE USED AS A PREDICTOR FOR THE ESTIMATED TIMES FOR DESIGN AND CONSTRUCTION AND INCLUDES A SUMMARY OF THE PAST, PRESENT AND ESTIMATED FUTURE CONSTRUCTION COSTS.