


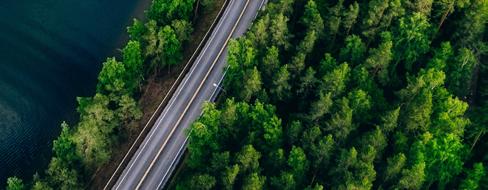
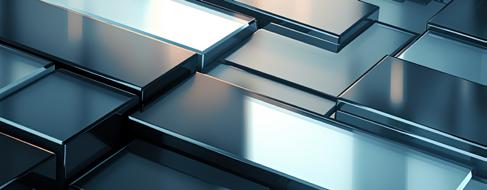

The theme of International Women’s Day on Friday 8 March 2024 was Inspire Inclusion. This theme facilitated an ideal opportunity to highlight why quantity surveying is an excellent profession for women.
While women currently make up just 19% of the total membership of The Australian Institute of Quantity Surveyors (AIQS), we are seeing a trend showing an increasing number of women joining AIQS in the younger demographics. With a lack of any formal historical data on the number of women engaged in the quantity surveying profession over time, the AIQS membership data does reflect good news.
As illustrated in Figure 1, the percentage of AIQS members who are women has increased from 2% of those born prior to 1959 to 34% of members born between 1990 and 1999.
Should this trend continue, we could expect to see gender parity in new members joining AIQS sometime between 2030 and 2040.
This increase represents the number of women becoming quantity surveying professionals, which appears to be driven by a number of factors including:
• schools pushing STEM subjects,
• AIQS continuous presence at Career Expos,
• increased awareness of employment opportunities across the broader quantity surveying profession,
• women in the quantity surveying profession acting as role models and promoting quantity surveying as a viable profession, and
• increased awareness of the profession amongst Career Advisors and parents.
A 2023 Department of Industry, Science and Resources study found that:
• the number of women enrolling in university STEM courses increased by 21% between 2015 and 2021,
• the number completing these courses grew by 15% from 2020 to 2021, and
• the number of women in STEMqualified occupations increased by 68% from 2012 to 2022.
While this is positive, women still make up only 37% of enrolments in university STEM courses.
AIQS has been offering university scholarships for over 10 years, and over that time applications from women have totalled only 26.5%. Which begs the question, why aren’t we seeing more scholarship applications from women?
Interviews with women in the quantity surveying profession in recent years have highlighted several issues impacting their career decisions. For many, a career in construction or quantity surveying either wasn’t on the radar, was never mentioned by Career Advisors or parents, or construction was thought of as an undesirable, maledominated industry.
In addition, more needs to be done to address the problem of women leaving the profession after having children.
As Nicole Trumbull MAIQS, CQS (National Director, WT Partnership), has previously stated, “The biggest challenge many women face in not reaching senior roles is an uneven division of labour at home.”
Nicole also sees the many positive aspects of the quantity surveying profession:
“We work on ten to fifteen jobs at one time, while other roles in construction can be one job for two years.
That keeps it interesting. One of the key parts of our role is advising consultants and developers on construction costs and the way their projects are progressing.”
For those women with a particular interest in technology, the quantity surveying profession offers a career utilising Building Information Modelling (or Digital Engineering),
which according to AIQS Vice President Fiona Doherty FAIQS, CQS, “allows designers to create an integrated multidisciplinary model of the built form. In addition, adopting the technology and embracing the role of quantity surveyor as a technical and financial expert will help attract more women into future quantity surveying roles.”
Here technology enables quantity surveying professionals a flexible approach, being able to perform numerous functions without being tied to the office or set hours.
Given the increase in women joining the profession I found this quote by Ziqi Chen MAIQS, CQS, as a positive note for women contemplating their careers:
“I like that quantity surveying has many facets. Every project is unique in itself and there are also a range of services to quantity surveying that many might not realise but we do deliver as part of our profession.
It also gives a sense of achievement seeing the project you are involved with being developed from hand-drawn blocks and lines to considering every detail and then seeing it built.”
The field of quantity surveying is not immune to the impacts of technological advancements, changing industry dynamics, or global trends. Artificial intelligence-assisted measurement software has been released in the market. Although the technology is still in its infancy, it is designed to simplify the quantification process and make the process more efficient.
According to software developers, their software allows users to measure common objects identified by artificial intelligence with just one click. This software will soon have AI documentation management features that enable users to effortlessly view an object on a floor plan, navigate to any sectional drawing containing that object, and then access the associated specifications or schedules.
This feature saves the user time that would otherwise have been spent sifting through potentially hundreds of pages manually.
Separate from this technology, voicebased operations are increasingly being used in addition to keyboards and mice to operate technology. In the future, we might be able to converse with our measurement software as if we were talking to a co-worker. Artificial Intelligence should be capable of understanding the quantities you require, searching through various websites to locate a supply price, or informing you of the obscure acronym that the engineer mentioned, along with a helpful link to a five minute webinar.
As with any technology, artificial intelligence needs to prove to the industry that it is reliable and technologically secure.
When this is achieved, it will be an indispensable tool to complement our core competencies and professional services. That being said, the importance of adopting proper measurement methods when preparing cost plans cannot be understated.
Professional judgement should always prevail and supplement artificial intelligence’s limitations of conceptual comprehension and non-quantifiable costing. Artificial intelligence should be seen as a tool to enhance correct measurement methods, not dictate them.
The future of quantity surveying is set to navigate through a transformative era – by morphing into more sophisticated management consultancies offering more than cost management, we must have agility in hybrid working models and an unprecedented level of flexibility. The profession is poised to break away from traditional bounds, stepping into a more respected and appreciated role within the consultant team.
Quantity surveyors have historically faced challenges in demonstrating their full potential, often relegated to roles that react to the decisions of others and constrained by pressures to lower fees. However, a visionary outlook suggests a revival and resurgence of the profession, by enlightening clients on the substantial value that a competent quantity surveyor brings from the project’s inception through its entire lifecycle.
The digital landscape and the effects of the COVID-19 pandemic have expedited a shift towards remote consulting and a hybrid work model, presenting quantity surveyors with opportunities to redefine their roles and services. Embracing technologies such as Building Information Modelling (BIM) and digital tools allows for a more integrated and efficient approach to cost management, asset management, and value engineering.
This shift not only facilitates better collaboration and flexibility but also enhances the profession’s ability to manage projects proactively, emphasising smart solutions to costrelated problems and contributing to high-quality modelling that benefits all stakeholders.
Moreover, the future will see quantity surveyors taking ownership of innovation and sustainability in project management, highlighting their critical role in ensuring value and efficiency. By attracting new talent and promoting continuous and cross-skill development, the profession seeks to elevate its standards and adapt to the evolving demands of the industry. The transition towards a more collaborative, technology-driven, and clientfocused approach will surely cement the quantity surveying profession’s significance, making it an esteemed career choice and an essential facet of the consulting industry in the forthcoming years.
COST MANAGEMENT
PROJECT COST MANAGEMENT GROUP (PCMG)
CLIENT OVERNEWTON ANGLICAN COMMUNITY COLLEGE
BUILDER IRELAND BROWN
ARCHITECT LAW ARCHITECTS
SECTOR EDUCATIONAL
LOCATION KEILOR, VICTORIA
PHOTOGRAPHER DIANNA SNAPE
Overnewton Anglican Community College (OACC) is located on the land of the Wurundjeri, Woi Wurrung People of the Kulin Nation. OACC has offered coeducational independent education on a dual Campus for Prep to Year 12 students for over 30 years in Melbourne’s North-West. As part of a strategic masterplan developed in 2017, the College engaged the Architect and Project Team to transform their two school sites into a separate Junior campus at Taylors Lakes and a Middle/ Senior Campus at Keilor. The new Middle School (Years 5–8) building became Stage 1 of the Yirramboi (Keilor) Campus.
The building sits nestled into a steep hill adjacent to the existing learning building and reimagines the offerings for middle years students into a healthy habitat promoting a sense of belonging and connectedness. The design is focused on flexible learning environments that are connected to each other and the surrounding environment. The building materials and finishes reference the natural environment and colours of the earth.
Comprising fifteen learning areas arranged around a tiered ‘Central Commons’, the precinct is consolidated by a canteen, external (undercover) auditorium and concourses. Pedagogical flexibility is paramount, resulting in a diverse range of learning areas, nooks and informal gathering spaces. Meanwhile, all fifteen learning areas have direct access to generous external covered spaces. The building layout and surrounding landscape design strategically link to previously disparate existing buildings across the school site to create a more unified and cohesive learning environment for the whole campus.
“This project demonstrates the benefits of significant consultation with the school community that resulted in a well-considered and robust brief allowing Law Architects to successfully develop a design to create rich, contemporary learning environments. The site, though challenging, presented opportunities to engage seamlessly with the natural environment. The building is imaginative, creating unusual shapes and spaces that work well on the sloping site. A sense of calm and connectedness is provided through the extensive use of glass to frame vistas of the landscape. All learning areas have direct access to generous external learning spaces that promote both passive and active learning, collaboration and reflection.
The functionality of the design has created a diverse range of internal spaces of varying sizes and shapes including informal spaces, nooks and larger spaces to gather in large or smaller groups.
Law architects have successfully executed a design that is totally reflective of the learning culture envisioned by the school. The building is well connected both visually and aesthetically to its natural surroundings and has created a learning community that welcomes all.”
COMMENDATION – 2022 LEARNING ENVIRONMENTS AUSTRALASIA, VICTORIAN AND TASMANIAN CHAPTER AWARDS, FOR EXCELLENCE IN EDUCATION FACILITY DESIGN
SPECIAL MENTION – 2023 ARCHITIZER A+ AWARDS PRIMARY & HIGH SCHOOLS
“As Project Cost Management Group (PCMG) celebrate the achievements of the OACC Yirramboi Campus Middle School Project, we extend our heartfelt appreciation to each Team Member for their indispensable role in this journey. Their contributions have not only elevated the project to new heights of success but have also enriched our collective experience, leaving an indelible mark on the Cost Management Field of excellence.
”Don Leelarathne FAIQS, CQS Director, Project Cost Management Group (PCMG)This article will consider the differences between mitigation, acceleration, and constructive acceleration. The recent case of V601 v Probuild1 is of interest, as it demonstrates that a constructive acceleration claim can be successful in certain circumstances.
First, let’s understand the consensus regarding mitigation.
Generally, the contractor is required, as far as reasonably practicable, to minimise the effect of a delaying event without spending additional money or resources.
Similarly, where the contractor was able to reduce the impact of the employerrelated delaying event but did not, the contractor will not be able to recover costs incurred from the effects of the events that it could have reasonably avoided.
This is reinforced by several standard forms of contract clauses regarding mitigation:
AS4300 1995:
“In determining a reasonable extension of time for an event causing delay, the Superintendent shall have regard to whether the contractor has taken all reasonable steps to preclude the occurrence of the cause and minimise the consequences of the delay.”
“What if the contractor and employer do not agree on an EOT?”
AS2124 1992:
“The contractor shall take all reasonable steps to limit, reduce and otherwise mitigate any loss or damage and the contractor shall, unless the Superintendent otherwise directs, take such emergency action as may be required to mitigate the loss or damage.”
FIDIC 2017:
“All reasonable endeavours to minimise any delay in the performance of the contract.”
To paraphrase, to claim an extension of time (EOT), it is a condition precedent of the contract that reasonable steps are taken to mitigate the potential impact of the alleged delaying event.
Acceleration is the execution of the planned scope of work in a shorter time than the originally planned duration.
Acceleration usually incurs an extraover cost to the contractor, whereas mitigation does not. Generally, before any acceleration measures are undertaken, the employer and contractor must agree to the proposed acceleration measures and their (likely) cost, as reinforced by the following excerpt from The Society of Construction Law (SCL) Protocol2 :
“Where the contract provides for acceleration, payment for the acceleration should be based on the terms of the contract. Where the contract does not provide for acceleration but the contractor and the employer agree that accelerative measures should be undertaken, the basis of payment should be agreed before the acceleration is commenced.”
1 V601 Developments Pty Ltd v Probuild Constructions (Australia) Pty Ltd (2021) VSC 849.
2 Society of Construction Law, Delay and Disruption Protocol, 2017, pg. 41.
Mitigation necessitates an actual delay event to occur that impacts progress and the date(s) for completion, whereas acceleration does not.
The employer can instruct the contractor to accelerate, regardless of whether the project is likely to be delayed (or not).
For example, the employer may require the use of the completed project earlier than contractually defined i.e., an earlier date than the contractual date for completion, requiring the contractor to accelerate.
However, if the contractor is in delay, the employer may direct the contractor to accelerate (at its own cost) to meet the contractually agreed date(s) for completion.
Before agreeing on the acceleration strategy (and cost), an entitlement to an EOT will have been determined in line with the relevant conditions of the contract.
The SCL Protocol defines constructive acceleration as:
“Acceleration following failure by the employer to recognise that the contractor has encountered employer delay for which it is entitled to an extension of time and which failure required the contractor to accelerate its progress to complete the works by the prevailing contract completion date.”
What if the contractor and employer do not agree on an EOT?
In the case of Motherwell Bridge v Micafil3, Motherwell accelerated its scope of work to accommodate the earlier days of Micafil so the date for completion could be maintained.
Motherwell notified Micafil of the three week critical path delay and provided an acceleration strategy. Motherwell was not instructed to accelerate, nor were they given an extension of time. Rather, Motherwell, at its own cost, accelerated its program.
His Honour Judge Toulmin awarded Motherwell an EOT to the date for completion, had it not been for the accelerated program i.e., after the actual date of completion. Motherwell was also entitled to claim the associated prolongation costs between the date of and for completion. Interestingly, Motherwell was not entitled to recover the associated acceleration costs.
The Motherwell Bridge v Micafil case highlights that, although Motherwell was entitled to an extension of time, they were not entitled to acceleration costs; even though Micafil agreed to the proposed acceleration strategy, they did not issue an instruction to accelerate.
In the case of Perini Corporation v Commonwealth of Australia4, Perini submitted several EOT claims that were subsequently rejected by the Director of Works. Moreover, the Director of Works took an excessive amount of time to make his decisions regarding the EOT claims.
Perini accelerated their works to meet the date for completion and to avoid liquidated damages. Justice Macfarlan found that the failure of the Director of Works to respond to Perini’s EOT claims in a reasonable time was a breach of contract.
Perini effectively constructively accelerated their works and they were successful in claiming the associated acceleration costs.
“EOT claims should be assessed as close to the time that the delaying event(s) occurred.”
The case of V601 Developments Pty Ltd v Probuild Constructions (Australia) Pty Ltd is similar to Perini v Commonwealth of Australia in that it was the Principal’s breach of contract that resulted in the successful constructive acceleration claim.
Failure by the employer to grant an EOT, where it should have, does not necessarily give rise to a constructive acceleration claim.
Similarly, when a contractor does accelerate, they are not entitled to claim the associated costs unless explicitly directed to accelerate as a result of an employer delay event(s).
The ‘wait and see’ approach is not the best way to manage EOT claims.
EOT claims should be assessed as close to the time that the delaying event(s) occurred.
3 Motherwell Bridge Construction Ltd v Micafil Vakuumtechnik (2002) CILL 1913
4 Perini Corporation v Commonwealth of Australia (1969) 2 NSWR 530
5 SCL Delay and Disruption Protocol 2nd Edition: February 2017, pg. 41.
“...The contractor should seek the approval of the relevant EOT claim.”
Before implementing any acceleration measures to expedite an employerrelated delay, the contractor should seek the approval of the relevant EOT claim. As per the SCL Protocol recommendation that:
“Where the contractor is considering implementing acceleration measures to avoid the risk of liquidated damages as a result of not receiving an EOT that it considers is due to it, and then pursuing a constructive acceleration claim, the contractor should first take steps to have the dispute or difference about entitlement to EOT resolved in accordance with the contract dispute resolution provisions. Otherwise, there is the risk that it will not be entitled to compensation for those acceleration measures.
In any event, before pursuing any such acceleration measures, the contractor should provide notice with the particulars of the intended acceleration measures to the CA. The contractor should then include such measures in a revised programme.”5
Stay on top of project schedules and keep construction moving forward.
Construction is one of the largest industries in Australia, providing approximately 9% of our GDP and generating nearly 40% of our annual global carbon emissions. According to the Federal Government’s 2020 National Waste Report, Australia produces 27 million tonnes of annual waste in the building industry alone, which is 44% of all waste generated in Australia annually.
Of this waste, 20 million tonnes end up in landfills each year, which can lead to serious environmental issues such as polluted water. Considering how much the building sector generates in terms of waste and pollution, I wanted to explore various subsectors within the industry to understand how our old ways of working can be improved to reduce costs, complexities, and environmental impact.
While construction touches every facet of modern society, rail is an important sector that underpins economic growth with the potential to support responsible consumption and a circular economy in the face of increasing urbanisation and population growth. Rail reduces road congestion and carries more customers and freight while using less energy and producing less emissions than most other modes of transport.
I’ve seen various positive examples of how rail can be more sustainable and creative in how it develops and uses building materials that minimise environmental impact. In Southeast Queensland, around 40,000 tonnes of glass end up in landfill every year. Cross River Rail is addressing this waste in partnership with Enviro Sands and Brisbane City Council, using sand made from recycled glass as pipe bedding fill for stormwater pipe relocation works.
This innovative material has already seen successful trials at Boggo Road and Mayne Yard, with further plans to use the product on other Cross River Rail sites as part of the Rail, Integration and Systems Works package. This initiative will also see Cross River Rail use recycled quarry products, integrate lower-carbon concrete, and develop pits from recycled HDPE plastic.
Cross River Rail is also using recycled plastic fibre reinforcement for concrete known as eMesh, which is more sustainable, safer, and cost-effective than typical steel reinforcement used in large projects, as it requires less effort in handling and cutting. The material is made from 100% recycled Australian plastic waste and can even be reused in the future.
Additionally, Fibrecon, the company behind eMesh, uses National Disability Insurance Scheme workers to pack the concrete fibres, supporting about 90 jobs.
Over 80% of the spoil generated on the project so far has been reused or is being stockpiled for reuse. Furthermore, Austral Bricks is using 60,000 cubic metres of the Cross River Rail spoil to make bricks for housing.
“The way energy is generated, distributed and used brings an array of challenges...”
Another example came in 2018 when Downer Group partnered with Hume City Council, Close the Loop, and REDcycle to develop the first Australian road using a newly developed soft plastic and glass asphalt. The asphalt mix uses over 25% recycled plastic and glass that would otherwise end up in landfill. On average, every one kilometre of two-lane road used 200,000 recycled plastic bags; 63,000 recycled glass bottles; toner from 4,500 used printer cartridges; and 250 tonnes of reclaimed asphalt road, with 20% Reclaimed Asphalt Pavement.
Compared to standard VicRoads asphalt, plastic- and glass-modified asphalt provides a 60% improvement in fatigue for longer-life pavements and superior deformation resistance for withstanding heavy vehicular traffic.
Considering an estimated 170,000 tonnes of soft plastic waste is created in Victoria alone annually, with only 10% recovered – this is an important project in reducing waste and developing more sustainable construction materials. The success of this project led Downer to construct a soft-plastic asphalt road in Craigieburn, which is now available across Australia with current use by seven local governments in Victoria and councils in NSW and SA.
This year we’re also seeing Australia’s first recycled kerbs being trialled at the Pakenham Level Crossing Removal project, delivered by Victoria’s Big Build in partnership with the University of Melbourne and Porous Lane, a company that recycles tyres.
The kerb forms a barrier between the road pavement and the nature strip, aiming to direct rain into stormwater drains and protect the edge of the road from erosion. One section of the kerb in the new East Pakenham Station car park has been made from a mixture of granulated waste tyres and crushed rock, which is bound together using an epoxy binder, thereby requiring zero cement.
Another important aspect of sustainability that is critical to my work is water supply and use, which needs to be economically feasible, socially responsible, and environmentally conscious. However, these purposes can sometimes compete when resources are limited; for example, water is needed to meet the demands of an increasingly urban population and the needs of rural agriculture.
Water-smart agriculture includes farming practices that optimise water use efficiency while maintaining or enhancing crop productivity. This approach combines traditional agricultural techniques with modern innovations such as drip irrigation, precision agriculture, and droughtresistant crop varieties.
Promoting agroforestry (the integration of trees into agricultural landscapes) can also help improve water retention in soils and reduce evaporation rates. These practices not only conserve water resources but also increase biodiversity and enhance ecosystem resilience.
Additionally, fostering a culture of water stewardship supported by advanced technologies can help ensure water quality and security for years to come. For example, in California, the company WaterSmart uses AI-powered analytics to help water utilities identify high water usage patterns and develop targeted conservation campaigns for their customers.
Another example is the Israeli startup Utilis, which uses satellite imagery and AI algorithms to detect underground leaks in water distribution systems. In agriculture, companies like Prospera Technologies provide AI-driven insights to help farmers optimise irrigation scheduling, saving water while maintaining crop yields.
Locally, Water for Victoria is making legislative and policy reforms to improve strategic water planning and management; sustainability and resilience of Victoria’s water sector; and improved reporting, monitoring, and evaluation of water supply investments to provide robust, evidence-based planning while addressing the impacts of water extraction on the environment and communities.
Energy consumption remains a critical component of sustainability discussions that impacts various aspects of our daily lives. The way energy is generated, distributed and used brings an array of challenges, particularly in terms of environmental impact, waste management, and the ongoing debate about transitioning to renewables.
One compelling case study worth highlighting is Sweden’s use of waste to replace fossil fuels and produce a sustainable source of energy. The country generates USD 100 million annually by importing rubbish and recycling the waste produced by other countries.
Consequently, just 1% of Sweden’s rubbish is sent to landfills, another 52% is converted into energy, and the remaining 47% gets recycled. The amount of energy generated from waste alone provides heating to one million homes and electricity to 250,000. By converting its waste into energy, Sweden has reduced its carbon dioxide emissions by 2.2 million tonnes per year.
Sweden has made recycling easy, accessible, and convenient. A recycling station can be found within at most 300 meters of any residential area. Swedish citizens are incentivised by discount vouchers for using nearby recycling machines. Furthermore, in new urban developments like those in Stockholm, waste chutes have been designed to channel rubbish straight into waste-toenergy incinerators, so residents’ waste produced is directly transformed into energy for their own homes.
I have a vested interest in seeing more projects that push for sustainable construction methods and materials.
As a member of the Infrastructure Sustainability Council, I’ve been working to get my accreditation in Infrastructure Sustainability rating, which is a voluntary third-party assured standard that evaluates the governance, economic, environmental, and social performance of infrastructure assets.
I hope to see this rating system become a standard across private and public works, especially as more asset owners recognise the value in sustainable practices – not only from a financial performance viewpoint but as a longterm investment in our planet’s ongoing survival. Building more sustainable infrastructure sets a stronger foundation for future generations to grow and thrive.
This article was written by Andy Day MAIQS, CQS from Infravisory.Last year I undertook a postgraduate course in construction planning and scheduling. The course commenced with an analysis of the construction of the Sydney Opera House and posed the question: why was it such a big failure? The reasons were numerous, including chronically delayed design, structural solutions that would take years to resolve, and funding issues following a change of state government.
The original budget was AUD 7 million. With an outturn cost of AUD 102 million (equivalent to approximately AUD 1 billion today), the Sydney Opera House was 1400% over budget and 11 years late. By any measure, it was a project management disaster.
Half a century on, the Opera House is a national treasure. Arguably, it defines a country more than any other building. You could sketch it in outline and struggle to find anyone who could not identify what you just drew. In international public consciousness, it ranks alongside kangaroos and koalas as one of Australia’s greatest national emblems.
In their 2023 report ‘Valuing 50 years of Australia’s Icon’, Deloitte Access Economics estimated The Opera House’s social value* at an astonishing AUD 11.4 billion. It created AUD 1.2 billion worth of value to the Australian economy in 2022/23 alone.
The project management disaster that was the Sydney Opera House was ultimately an incredible development success. The benefits have outweighed the costs by many multiples.
The Opera House’s development could be seen as a vivid example of two opposing theoretical principles of project management – the Planning Fallacy and the Hiding Hand.
The first of these relates to the tendency to underestimate the time required to undertake a given task. Take an example: how much of what you set out to achieve this week have you accomplished? If there’s a shortfall there, you are not alone – we habitually underrate the time it takes to complete work. This optimism bias is incredibly common and poses a serious threat to project budgets and delivery.
In his 2023 book ‘How Big Things Get Done’, Bent Flyvbjerg provides some bleak statistics on budget blowouts and project delays. From his broad database of megaproject metrics, we learn that construction projects (buildings) have a mean cost overrun of 62%. Further, for 39% of building projects, this overrun exceeds 50%. Flyvbjerg calls this his ‘Iron law of megaprojects’, one that produces results that are “over budget, over time, over and over again”.
Conversely, the inclination to underrate risks and challenges may be essential to getting work underway. If all the downside risks of our developments were properly considered, ambitious projects may never get built at all. The Hiding Hand principle supposes that, once a project is underway, our tendency to underestimate risks is balanced by our ability to creatively resolve previously unforeseen problems. The Opera House project team worked through numerous major issues and evolved incredible solutions.
The Opera House started life as a visionary but unbuildable design. It took pre-eminent structural engineer Ove Arup years to develop buildable solutions, designed concurrently with the construction process.
Whilst it is quite normal for projects to require some design development during the building phase, the builders of the Opera House started digging with only scant preliminary design. They could have avoided much cost, uncertainty, and risk if they had invested more in progressing the design solutions beforehand.
Flyvbjerg is a proponent of planning slowly and acting fast. He likens the planning stage of a project to a ‘safe harbour’, and the delivery phase as, “venturing across the storm-tossed seas”. Once we start digging, our risks tend to increase considerably, so why not do as much as we possibly can before? Sound advice for large and complex projects that can afford the upfront time investment.
Another useful insight from Flyvbjerg is the need for deep domain experience. Architect Jørn Utzon was only 38 years old when he won the competition to design the Opera House. Nothing in his nascent career would have prepared him for what lay ahead, and he would never have predicted his resignation seven years prior to the building’s completion. As Mark Twain opined, a man who carries a cat by the tail learns something he can learn in no other way. Issues relating to lack of expertise may be a significant problem for New Zealand infrastructure development too – according to Auckland’s City Rail Link’s Dr Sean Sweeney (quoted in the NZ Herald, December 1st 2023), there is “almost no major project experience in the public sector”.
Those involved with the feasibility analyses of large projects often have to contend with political ambition.
Power dynamics that incentivise the underestimation of cost and time, whilst overestimating benefits are commonplace in large, public projects.
As early as 1954, New South Wales Premier Joseph Cahill advocated for a new, dedicated opera house, and announced an international design competition the following year. He would later proclaim the project would be, “an outstanding example of modern architecture” and, “a monument to democratic nationhood in its fullest sense.” Such statements tend to cement commitment, irrespective of objective cost-benefit considerations.
In the UK, the highly-politicised Millennium Dome was predicated on visitor numbers of 12 million in the first (and only) year of operation. That equated to one-fifth of the entire population of Britain – a gross overestimation (the ultimate visitor figure was 6.5 million). The Channel Tunnel was an engineering marvel, but in its first year of operation, the actual passenger numbers were less than 20% of those forecast. There are numerous such examples. The tendency to provide naively optimistic, ‘best case’ scenarios may be honestly irrational, or strategically disingenuous.
Project management failures that result in significant delays not only give rise to direct costs. As well as an elongated opportunity for things to go wrong (more time sailing on Flyvbjerg’s ‘rough seas’), there is a deferment of utility. During a decadeand-a-half of construction upheaval, the Opera House’s prime harbour-side location provided zero utility for half a generation of Sydneysiders.
How can we objectively evaluate project costs and benefits and avoid the insidious effects of optimism bias, whilst backing ourselves to resolve at least some of the issues that may arise once a project is launched?
It would be useful to appraise ourselves of the dynamics of optimism bias (whether accidental or intentional) and have some awareness of a perceived conflict of interest inherent in prejudiced feasibility evaluation. We should observe the statistics and know the issues. Though, we may have limited influence on contentious costbenefit analyses and be pressured to align with overly optimistic assessments. Ultimately, it highlights the need to balance pragmatism, ethics, and professionalism in such situations.
In a 2013 paper entitled ‘The CostBenefit Fallacy: Why Cost-Benefit Analysis Is Broken and How to Fix It’, Flyvbjerg suggests holding the authors of erroneous estimates to account. He goes so far as to suggest that originators of ‘grossly misrepresented’ forecasts be sued for damages. There have indeed been prosecutions for negligent forecasting on large projects, including Sydney’s infamous Lane Cove toll tunnel. Whilst the diligent application of reasonable skill and care can still provide erroneous results, project forecasters having more ‘skin in the game’ could lead to improved objective assessments. Additionally, independent analysts with zero attachment to the success of the project can be usefully deployed in audit and review services, to balance the negative impacts of our optimism bias.
In summary, estimating cost, time and benefits with any degree of accuracy is incredibly complex and there are human factors at play. The incidence of getting it wrong is more common than we are prepared to admit. There is tension between relying on creativity and ingenuity to solve unforeseen problems, and not spending enough time on objective and honest costbenefit analysis.
Few would seriously suggest that Sydney Opera House should not have been built. If the business case had foreseen all the issues that arose, it might never have been. To simply ‘start digging’ is nearly always an unsound strategy, but if we stay in that safe harbour too long, we might (to paraphrase Shakespeare) miss the flood tide and lose our ventures.
*That ‘social value’ is made up of ‘transaction value’ (events plus food and beverage revenue), Consumer Surplus (the amount of money customers would be prepared to pay over and above the actual price paid), ‘Existence Value’ (the value to Australia in just having it there), and Digital Value (the time expended interacting with the Opera House’s digital content). It is, in part, these ‘externalities’ that distinguish comprehensive Cost Benefit Analysis from straightforward profitand-loss accounting. For the curious quantity surveyors amongst us, Deloitte Access Economics valued the building and associated land at AUD 3 billion.
A quantity surveyor has a dynamic role and can be an essential partner to a project manager. Quantity surveyors hold many skills (outside of just costing and measuring), such as contracts, procurement, and tendering. Internationally, the quantity surveyor is frequently the superintendent and executes the contract, meaning the role of the quantity surveyor globally is far more extensive than in Australia.
By engaging a quantity surveyor from feasibility, clients can begin with a realistic budget for their project brief. Currently, the market is seeing significant prolongation of design phases, as the forecast costs and budgets are not aligning.
The value management process is frustrating, time-consuming, and expensive for the client, who will need to pay various consultants for additional work to align the design to the budget. The value a quantity surveyor can provide is exponential at the beginning of a project and reduces as the project progresses and the design elements are approved.
Full-service quantity surveying services, where the quantity surveyor is engaged to set the budget and is from then an active member through the design phases, are key. Collaboration saves time and money.
If a quantity surveyor is used only at milestones to complete estimates, they will have missed the design journey, and implicit information may not be transferred. This is not a reflection of the skill of the quantity surveyor but of the service purchased.
Quantity surveyors typically have multiple projects running at a given time, meaning they deal with contractors and design teams more frequently than other disciplines. Therefore, we have a broad range of exposure and insights to add that exceed the price of structural steel.
The Australian construction industry is facing incredible short- and long-term generational challenges. This comes at a time when growth and expansion of the industry are required to match the significant demand of the infrastructure pipeline.
Current growth is mirrored by and partly due to a large pipeline of public and commercial infrastructure projects, and an optimised industry increases project delivery schedule and budget certainty.
The industry is projected to experience an average annual growth rate of 3% between 2025 and 2027.
This increase is anticipated due to the government’s ongoing commitment to infrastructure development and investments in several sectors including transit, housing, renewable energy, health, education, and manufacturing.
In August 2023, the federal government approved the development of 1.2 million residential properties within five years, commencing in 2025. Additionally, the government budget for the fiscal year 2022–2023 allocated a total of AUD 17.9 billion over 10 years towards significant infrastructure initiatives, encompassing substantial investments in road and rail projects nationally.
It is anticipated that the aggregate investment in significant public infrastructure projects will surpass AUD 218 billion during the period spanning from 2021 to 2025.
It’s important to recognise that private infrastructure projects add significantly more to this too.
Communities stand to gain advantages from the implementation of nationally significant infrastructure, including enhanced travel experiences characterised by reduced travel times and increased safety. Additionally, the development of more habitable cities, suburbs, and regions will contribute to the overall well-being of these communities.
The question is: Can our construction industry keep up with demand, whilst delivering safe, quality, sustainable and trustworthy infrastructure? The short answer is: no.
Unless there are fundamental changes to the way our industry operates, the pipeline of infrastructure projects and the challenges they exacerbate threaten to substantially disrupt the industry. As we learn from global best practice case studies it has become apparent that the delivery of large pipelines must be collaborative between government and private sector organisations.
Whilst transformation in and of itself invites resistance, there are small incremental changes that can have positive effects, both operationally and economically for organisations, whilst simultaneously providing sustainable outcomes for communities and the environment.
Like any successful implementation of change, early engagement of impacted stakeholder groups is a must but even before that, a comprehensive business analysis must be completed to understand the holistic nature of the intended transformation targets.
The dynamic nature of the industry exhibits similarities to those of other industries. Below are some of the prominent problems that the industry faces. Importantly, these issues are predominantly outside the industry’s control and can be regarded as factors that the sector must work with rather than resist. Organisations will be hit hard and as we have seen, insolvencies have ensued.
• The COVID-19 pandemic and the war in Ukraine have caused significant disruptions in the supply chain.
• The presence of extreme weather events and climatic phenomena contributes to the extension of construction delays.
• The rapid increase in inflation has resulted in a significant rise in the costs of materials, creating difficulties in the tendering process for projects, budgeting for continuing activities, and eventually attaining profitability. Whilst events like the ones mentioned above have the potential to affect the industry, they are largely outside the scope of control. Instead, the challenges that can be effectively managed and mitigated should be focused on through public and private collaborative efforts.
Australia’s construction industry is at a crossroads. Trustworthiness is at an all-time low, and outcomes appear bleak as cost-cutting and shoddy workmanship are at an all-time high. Government agencies like the Office of the NSW Building Commissioner continue to make inroads into this issue but unless they bring private industry on board with ideas, there will always be a disconnect between policy and industry capacity for adoption and long-term compliance. The following manageable challenges currently burden the industry:
Given the current characteristics of construction work, it is inevitable that accidents will occur. Hazards include falls and slips, manual lifting and straining, as well as machinery and material mismanagement. The presence of a heightened risk of accidents does not inherently imply a corresponding increase in the rate of casualties.
Based on research conducted by Safe Work Australia, it is evident that employers and employees share a common perception regarding worker carelessness as the primary cause of injuries within the sector. However, it is noteworthy that almost one-third of employees hold the belief that inadequate safety education and training significantly contribute to such incidents.
The implementation of safety enhancements has the potential to mitigate absenteeism, enhance productivity, provide cost savings, bolster employee retention, and recruit skilled professionals in the construction industry.
According to job mobility data released by the Australian Bureau of Statistics (ABS), approximately 136,000 individuals employed in the construction industry voluntarily departed from their positions over the period spanning from February 2022 to February 2023. This figure represents the fourth-highest turnover rate among the 14 sectors examined in the study.
The observed high turnover rates in this sector might potentially be attributed to several factors, including the extensive working hours, the physically strenuous nature of the job, the absence of hybrid work arrangements, and little job security. These challenges arise from the prevalence of contract and subcontracted labour as well as a casual workforce within the industry.
To address the negative aspects associated with construction employment, the construction industry must provide favourable industry and environmental factors that facilitate job satisfaction.
These may include the opportunity to earn a wage while acquiring valuable knowledge and skills, the flexibility in working hours, and importantly, the ability to work in a comfortable environment.
The construction sector in Australia is characterised by a significant gender imbalance, with males being the majority of its workforce. However, in response to persistent labour shortages, there is a growing movement advocating for increased female representation in the industry’s future.
The National Association of Women in Construction (NAWIC) set a target of achieving a 25% representation of women in the construction industry by the year 2025.
The current representation of women in the building and construction industry’s employment stands at 13%, with a further breakdown revealing that 2% of this subset is engaged in trades. In addition, it should be noted that the remaining 11% of women are employed in administrative and support positions.
There is no one-size-fits-all answer. The construction industry is equally intricate and complex. In terms of a solution, we know answers need to be holistic. A positive outcome in one aspect cannot come at the expense of another aspect. Unfortunately, more often than not, the cost is that ‘other aspect’.
Therefore, the approach should be based on fast-tracking innovation implementation into the industry.
A potential solution that has been highlighted is Modern Methods of Construction (MMC). The first thing that needs to be established is that MMC is not a comprehensive solution. However, under certain circumstances, it becomes a very feasible solution (in part) and some large developers have shown that it’s possible to produce positive project outcomes like cost savings, faster construction, improved quality control, sustainability, reduced disruption, and better safety. The question remains, what can the government do to make the approach more feasible for industry under a larger set of circumstances?
In terms of broader tax channels and regulated industry, the approach from government should also focus on identifying value in past, current and future infrastructure. Australia has tens to hundreds of billions of dollars of value sitting in material value however, it is constrained by an industry that isn’t mature enough to process it yet. The government should be simultaneously analysing, identifying, and developing this value database. By developing this database, the government can then standardise the methods by which construction and demolition materials are tracked, managed, and disposed of.
An example of innovation implementation comes from New South Wales, which introduced a new regulation taking effect from 1 October 2023. Broadly, it states that applicants for non-residential development types must complete the NABERS Embodied Emissions Material Form.
If the two proposed solutions are effectively implemented and fiscally supported through both government and private industry backing, the industry should see significant positive changes over the next five to ten years.
The infrastructure pipeline will become a more realistic target and the workforce will see manageable growth. Additionally, Australia will see the ignition of an added subprimary industry in circular reuse. This means more jobs in the economy, more regulated tax channels for the government, more cost recovery for developers and better sustainable outcomes for the environment.
Doing things correctly the first time is always cheaper than re-doing them in the future, but unfortunately, the Australian market mostly favours approaches that focus on short-term fiscal savings over long-term holistic benefits.
As the move to higher environmental ratings for our built structures continues, the importance of accurate carbon accounting grows.
WoodSolutions’ new design guide on The Role of Wood Products in Zero Carbon Buildings serves as a valuable resource for design professionals who aim to incorporate sustainable materials. Find case studies, information on Australia's embodied carbon policies, frameworks, green building certifications, and more tools.
Prepare for the future and download your free copies today with the QR code on this page.
The construction sector contributes significantly to the global Gross Domestic Product (GDP) and anticipates a 42% growth in global construction output by the year 20301. This rapid development requires innovative technologies to cater to the increasingly significant demands of the industry. Accordingly, the construction industry is transforming into a technology-driven industry through the adoption of ideas and technologies of Construction 4.0, which includes technologies such as Building Information Modelling (BIM), artificial intelligence, 3D printing, augmented and virtual reality, big data, cloud computing, blockchain, and the Internet of Things.
The Digitalisation of Construction Report by the NSW Government suggests that class two designers and builders could take ten years to achieve a significant level of ‘smart’ digital maturity2 . This maturity would entail the widespread adoption of advanced technologies like BIM and Digital Twins. These technologies offer a range of advantages to construction projects, such as time-saving in construction project delivery, increased productivity, increased speed of work, increased document quality, speeding up of response time, security, and more simple working methods. In addition, these innovative technologies could also enable dispute minimisation in construction projects.
On the other hand, the rapid digitalisation and use of modern construction methods will also have far-reaching consequences for the industry and its major stakeholders.
3
4
5
In projects using BIM, ambiguities arise due to vague determination of integration and design responsibilities among stakeholders. The integration of stakeholders on a single platform often blurs design responsibilities. The absence of standardised contract forms and reliance on supporting documents contribute to contractual ambiguity. Current versioning applications and Common Data Environment (CDE) rely on a centralised database, which incurs cybersecurity risks of data manipulation and single-point failure, resulting in a loss of data traceability and design liability, which may cause further legal disputes.
Disputes in construction may also arise when using blockchain platforms due to the lack of legal regulations, data privacy concerns, scalability issues, and interoperability issues. There could be room for legal dispute due to mistakes and misrepresentations arising from coding errors in smart contracts. Given the complexity of construction projects and the industry’s technological advancements, effective management of disputes becomes imperative, necessitating comprehensive strategies that address both technological vulnerabilities and the project ecosystems.
Disputes in the construction industry are often considered an inherent feature due to the complex and competitive nature of construction projects, which involve numerous stakeholders with different interests, intricate processes, and substantial resources.
Disputes have a monetary trait attached to them and none of the project participants are ever ready to absorb such magnitude.
A recent global construction dispute report by Arcadis in 2022 found that the average value of disputes remains at historically high levels (USD 52 million) during the years 2020 and 20213. The average time taken to resolve disputes increased significantly (by 15 months) in 2021, by almost 15%, compared to the years 2019 and 2020. Thus, construction disputes critically impact the cost and time of projects, which are considered two of the three constraints in the iron triangle of construction performance. In addition, disputes cause many negative effects, such as disturbing the relationships between stakeholders, loss of professional reputation, loss of profit and rework. Payment disputes could have a destructive domino effect down the contractual payment chain.
Abandonment of the project and insolvency of the contracting firm are serious sequences of disputes. These disputes are highly technical and involve legal aspects, which require highly specialised skills and proof documents. Therefore, construction professionals have directed their attention towards the effective management of disputes.
The construction industry appears to have finally realised that prevention is better than treatment. In the construction sector, there is a growing recognition that proactive rather than reactive tactics are the way to go. As a result, the concept of dispute management has gained popularity. Developing systems, procedures, and abilities to reduce the likelihood of disputes occurring and efficiently managing disputes that do occur to resolve them quickly, cheaply, and
without unnecessary escalation is the goal of dispute management.
Relational contracts, project team integration, and innovative technologies and communication tools could be utilised as ways to mitigate disputes which lead to binding dispute resolution methods. Party-to-party negotiation, adjudication and mediation are commonly utilised globally to resolve disputes as alternatives to litigation. Contract and specification reviews, proper contract documentation, risk management, constructability reviews of design, appointing an adjudicator from the beginning of the project, allocating fair contract risk, use of relationship contracting, and early contractor involvement are recommended strategies to avoid disputes.
Addressing the common causes of contractual disputes relevant to clauses in standard contracts could reduce contractual disputes.
The most critical causes leading to disputes occur due to: payment delays and scope changes by clients, ambiguities in contractual documents by consultants, or poor quality of work and progress delays by contractors.
The potential dispute causes are extremely likely to influence the occurrence of other dispute causes, and then the combination of them leads to a dispute. For example, the poor performance of the contractors, combined with payment delays constituted the majority of disputes.
Construction professionals are prioritising the understanding of causal relationships and co-occurrences of dispute causes to address issues at an early stage, aiming to proactively prevent disputes from arising.
Although, construction professionals adopt different ways to manage disputes from different perspectives: the sources of disputes that lead to disputes; causal models; litigation and alternative dispute resolutions to resolve disputes; and dispute avoidance strategies to avoid them beforehand, the recent construction projects are struggling with a prevalence of disputes.
This necessitates an innovative mechanism that combines digital technology with prominent dispute management techniques to establish automation and mitigate disputes effectively in construction projects.
Artificial intelligence (AI) is increasingly becoming a mainstream technology for many industries and professions. AI is not only bringing about radical and unprecedented changes in the way individuals live and work, but it is also setting the stage for even greater transformations in the future.
AI challenges the notion that communication should be exclusively human-to-human, offering opportunities for humans to engage in conversations with machines. AI represents the pinnacle of scientific exploration into replicating cognitive abilities, with machine learning serving as its foremost implementation.
Machine learning algorithms work by searching through a set of possible prediction models for the model that best captures the relationship between the descriptive features and the target feature in a data set. They are subsequently employed to forecast future data or facilitate decisionmaking in situations characterised by uncertainty.
Machine learning has become a big business in recent years: companies are leveraging it to make a profit, applied research is flourishing in both industrial and academic settings, and curious developers everywhere are looking to enhance their machine learning skills. Even governments across the globe are motivating firms through policies to tap into the machine learning arena, as it promises opportunities for growth, productivity and efficiency.
Today, we are in the era of opensource abundance, with high-quality implementations of many machine learning algorithms easily accessible on GitHub.
In addition, machine learning enables the creation of automated processes that enable predictions of occurrences. The machine learning model learns from the analyses of the successful solutions while learning from the mistakes of unsuccessful solutions with limited interferences and the use of underlying algorithms.
Machine learning typically involves several stages, which primarily include data collection, data set processing, model construction, model evaluation and model deployment, as depicted in Figure 1 below.
Machine learning applications are predominant in the fields of healthcare, finance, information technology, agriculture, retail, manufacturing, marketing and transportation. Machine learning algorithms are used for disease detection and diagnosis, personalised treatment plans, predicting patient outcomes, and analysing medical images like MRI scans and X-rays in the healthcare sector. Especially, DeepMind’s AI system has been used to detect eye diseases like diabetic retinopathy.
Banks and financial institutions employ machine learning to detect fraudulent transactions, while e-commerce giants like Amazon and Netflix leverage these algorithms to recommend products and content based on user behaviour and preferences. Google Maps utilises machine learning to deliver real-time traffic updates and suggest optimal routes to users, while companies such as Tesla use machine learning to enable self-driving cars to perceive their surroundings and navigate safely.
There is no doubt that the construction industry is increasingly recognising the potential of machine learning applications to enhance its overall effectiveness and performance.
Machine learning technologies offer a range of benefits in construction, helping to address various challenges and optimise processes.
For example, predicting the cost of construction projects, the occurrences of accidents on construction sites, the likely outcomes of accidents, capabilities for the compressive strength of high-performance concrete, delays in construction projects, measuring the sizes of asbuilt components in built assets, and early warning analysis using relevant machine learning methods for the safety risk of the tower crane.
In addition, machine learning algorithms are utilised in predicting dispute resolution outcomes, dispute resolution methods, and dispute probability. Thus, machine learning shows the potential to predict and thereby mitigate disputes effectively in construction projects.
Applying machine learning to reallife construction industry problems goes beyond just prototyping predictive models. It entails intensive activities that, besides training robust machine learning models, provide a comprehensive framework for answering questions asked by construction stakeholders when intelligent solutions are deployed at their premises to facilitate their decision-making tasks.
Accordingly, we can assess the potential for disputes in construction projects. Machine learning methodologies can be used to identify ways of capturing and predicting the likelihood of disputes in construction projects.
The industrial sector emerged as a big winner from the pandemic, fuelled by the e-commerce juggernaut – demand for data, fast delivery and the freshest food and pharmaceuticals. Now, more than ever, the need to speed is transforming supply chains, and driving developers towards multi-level industrial.
Around 10% of Australian purchases are now made online1, and some analysts estimate we will need 1.8 million extra square metres of industrial and logistics space to accommodate the next five years of e-commerce growth. 2 Australia also has the lowest industry vacancy rate in Asia Pacific, with a national average of 0.6% for prime space.3
In Sydney, the nation’s tightest and most expensive industrial rental market, there is limited serviced industrial
land available, and the vacancy rate is hovering at 0.3%.
Research shows around a quarter of customers abandon online shopping carts because estimated delivery times are too slow.4 To this effect, Australia Post has just launched its ultra-fast delivery service, with ‘next day’ delivery now possible in most capital cities.5 But customers in many markets, notably China, now expect delivery to their door within 30 minutes. That’s where the trendline is pointing.
Facilities close to the customer can deliver significant savings, as up to 50% of supply chain costs are correlated with transport (compared to up to 10% on real estate).6
But the carbon savings could be even more significant. Around 18% of Australia’s emissions come from transport7, and a modern facility in the right location can make big inroads into a company’s emissions footprint.
MIT’s Real Estate Innovation Lab has found transportation emissions from an urban fulfilment centre are around half that of an out-of-town hub.8
All these drivers are propelling property developers towards multilevel warehousing – but how tall are we talking? Multi-storey facilities are typically three or four levels, although Hong Kong’s GrandTech Centre soars to 22 storeys.9
In April, ESR Group Limited (ESR) completed the world’s largest multistorey distribution centre in Tokyo, with a gross floor area of 349,000 square metres (m2) across nine storeys (and on just 77,725 m2 of land near Haneda airport).10 Closer to home, ESR recently acquired a 4.8-hectare site in South Sydney, with plans to develop an AUD 300 million multi-storey warehouse facility.11
1 Australian Bureau of Statistics 2024, Retail Trade, Australia, ABS, <abs.gov.au/statistics/industry/retail-and-wholesale-trade/retail-tradeaustralia/latest-release>.
2 House, K. 2022, ‘Australia’s 1,800,000sqm e-commerce challenge’, CBRE, 27 September, <cbre.com.au/press-releases/australias1800000sqm-e-commerce-challenge>.
3 Schlesinger, L. 2023, ‘Low vacancy rates to lift industrial rents another 14pc’, Australian Financial Review, 21 June, <afr.com/property/ commercial/low-vacancy-rates-to-lift-industrial-rents-by-another-14pc-20230621-p5di8w>.
4 van Gelder, K. 2023, ‘Main reasons why consumers abandon their orders during the checkout process in the United States in 2023’, Statista, 9 October, <statista.com/statistics/1228452/reasons-for-abandonments-during-checkout-united-states/>.
5 Elmas, M. 2023, ‘Australia Post’s next-day delivery helps Myer, Adore and Rebel take on Amazon’, The New Daily, 15 August, <thenewdaily. com.au/finance/finance-news/2023/08/15/australia-post-same-day-delivery>.
6 Crawford, L. 2021, ‘Multi-level warehousing in Australia’, Colliers, report, 15 July, <f.hubspotusercontent40.net/hubfs/5081193/Australia/ Corporate%20Marketing/Landing%20pages/Research/Multi-level%20Warehousing/Multi%20Level%20Warehousing%20Insight%20 White%20Paper-2.pdf>.
7 Climate Change Authority 2021, ‘Fact Sheet – Transport’, Australian Government, February, <climatechangeauthority.gov.au/sites/default/ files/2021-03/2021Fact%20sheet%20-%20Transport.pdf>.
8 Briseño, D.F., Chegut, A., Glennon, E., Scott, J. & Yang, J. 2021, ‘Retail Carbon Footprints: Measuring Impacts from Real Estate and Technology’, MIT Real Estate Innovation Lab, <realestateinnovationlab.mit.edu/wp-content/uploads/2021/01/FINAL_Retail-carbon-footprintsreport_011221.pdf>.
9 Mapletree Logistics n.d., Grandtech Centre Hong Kong SAR, <mapletree.com.sg/MLT/Asset-Portfolio/Property.aspx?currentProperty=/AllProperties/MLT/Hong%20Kong%20SAR/Grandtech-Centre>.
10 Realty Plus 2023, ‘ESR builds the tallest logistics facility in Japan’, Realty Plus, 28 April, <rprealtyplus.com/international/esr-builds-thetallest-logistics-facility-in-japan-110445.html>.
11 Schlesinger, L. 2023, ‘ESR planning multi-storey warehouse at $143m South Sydney super site’, Australian Financial Review, 21 June, <afr. com/property/commercial/esr-planning-multi-storey-warehouse-at-143m-south-sydney-super-site-20230621-p5di8c>.
The story of Sydney, given its tight industrial vacancy rate, is particularly interesting. CBRE expects at least six multi-storey facilities will be built in Sydney over the next two years and says around 15% of total new industrial floorspace delivered in the city between now and 2027 will be multi-storey.12
“...The obvious question is: how much does it cost?”
Goodman Group has invested AUD 700 million in two inner-city Sydney sites and promises to introduce “a new building typology”. The first is a 30-metre-high, three-level facility in St Peters, which will hold around 47,000 m2 of warehousing space.13 Semi-trailers up to 20 metres will access the levels via a 55-metre diameter spiral ramp.
The second is a two-level project that is 20,000 square metres (m2) in Alexandria.14 Designed by acclaimed architect FJMT, the building, Goodman Group says, “balances raw industrial style with refined premium aesthetic”. The building boasts state-of-the-art, end-of-trip facilities, is adjacent to a park and is targeting a 5-star Green Star rating.
These are all features that are attractive to workers and will create an appealing aesthetic and amenity within the local neighbourhood.
If the future multi-storey facility is much more than a grey box, the obvious question is: how much does it cost?
The height of an industrial facility might stack up, but does the feasibility? Industrial developers must also consider that moving to multi-storey isn’t simply a matter of multiplying a single-storey m2 rate. With the current volatility in the market, we’re seeing varied tender returns for multi-level industrial units; however, these are all significantly higher than typical, single-storey projects that may have been considered for benchmarking in the past, but don’t apply to this form of construction.
Moreover, low supply in cities like Sydney is contributing to higher rental rates and, therefore, may impact the feasibility of projects and, subsequently, the construction supply in the Sydney area.
The structure, depending on the ground conditions, may require stronger columns and a thicker slab. Extra floors require more mechanical services and space for plant and equipment. Reticulation of services is more complex and costly.
A building’s façade accounts for around 30% of the cost of a commercial project, and we are beginning to see designs for multi-storey industrial buildings that mirror the quality of commercial offices.
An attractive façade can enhance the local neighbourhood, but it can also come at a significant cost. Preliminaries are also much higher on multi-storey –think 20%, rather than 10%.
Then there are additional costs for cranes and scaffolding, labour, site and traffic management, staging requirements and safety. These factors, as you can surely guess, contribute to higher construction costs.
The bottom line? The industrial sector has benchmarked buildings based on single-storey construction – and using these numbers for feasibilities could end up in failure. That doesn’t mean we shouldn’t be moving to multi-storey industrial. It just means understanding the implications. The higher the building, the bigger the budget.
This article was written by Barry McBeth from Altus Group.
12 J-Baleh, S. & Badgery, D. 2023, ‘Rise of multi-storey warehousing update’, CBRE Research, October, <mktgdocs.cbre.com/2299/bb769666fa5e-4b7d-a0b2-b8a26d8e2cb2-1826307085.pdf>.
13 Lenaghan, N. 2022, ‘Goodman goes high with multi-storey warehouses in Australia’, Australian Financial Review, 21 November, <afr.com/ property/commercial/goodman-goes-high-with-multi-storey-warehouses-in-australia-20221118-p5bzhy>.
14 Goodman n.d., ‘Axis Alexandria’, Goodman, <au.goodman.com/our-properties/properties-for-lease/axis-alexandria>.
Major project delivery can present a range of complexities and challenges. However, by setting projects up for success through a strategic, data-driven process, organisations can ensure smooth delivery and successful outcomes.
By Adrian McLay and Dean MillsWith the complexity of major projects and demands for quicker, cheaper and more sustainable delivery rising, major projects require a different approach to be successful. Despite its critical importance, the strategy, planning and set-up phase often receives insufficient time and resources, leading to the project not realising its potential benefits.
The Federal Government’s recent announcement to defund AUD 7 billion worth of infrastructure projects across Australia is a lesson to be learnt from. This is primarily due to unrealistic timelines, budgets or misalignment with government priorities, which underscores the opportunity for organisations to rethink their approach to major project set-up and re-evaluate their strategies.
Ensuring stakeholders are engaged early and often can prevent fallout, such as misalignment with Federal Government priorities. Similarly, ensuring early on that project briefs align with available budgets and realistic timelines can be instrumental in avoiding major setbacks, such as the high-profile cancellation of the 2026 Commonwealth Games by the Victorian Government due to budget overspending.
Australia’s construction industry requires a delivery model for major projects that combines leadership with data-driven tools to assist in aligning scope with project success criteria – spanning time, cost and quality. A strong delivery model comprises a strategic three-step process: setting up a strategy for success, implementing controls, and providing assurance.
The below explores how optimising strategy and set-up of major project delivery enables major projects to be delivered on time, within budget and to meet stakeholder priorities.
During the first month of major project preparation, it is critical to thoroughly diagnose and understand the project’s scale, complexities and limitations. Defining the project brief and scope, assembling a team and determining resource requirements, all while establishing clear boundaries, objectives, and constraints and understanding stakeholder expectations are key to delivering a successful outcome.
Analysing project metrics, such as schedule, cost, risk and quality enables proactive identification and rectification of potential issues. Aligning these metrics fosters effective communication and collaboration among project stakeholders, ensuring a shared understanding of project goals and expectations.
“Major projects present an opportunity to leverage supply chain purchasing power to enhance operational efficiency and mitigate later risks...”
Developing a robust work breakdown structure (WBS), to define project deliverables, tasks and dependencies, serves as a blueprint for project execution, guiding resource allocation, scheduling and risk management efforts. The WBS also determines the necessary specialist skills needed within the team and enables leadership to evaluate trade-offs while ensuring alignment with strategic objectives.
As projects grow in complexity and scale, they demand a high level of specialisation and a tailored delivery approach. Specialist major project experts should be deployed to accommodate the unique size, risks and client confidential requirements of each project. Additionally, complex projects often require a project controls-led approach to managing traditional workstreams.
The Castle Towers, Sydney redevelopment of a live operating shopping centre, delivering three mixed-use towers on top of the existing trading centre, exemplifies how a 90day start-up plan can ensure major project success.
Adequate time was taken at the outset to assign clear business goals and objectives, understand the client and enable alignment of desired outcomes. A 90-day start-up plan was mobilised, deploying experts who possess a broad sector background and diverse skillsets, to prepare the delivery strategy, informed by deep design, construction planning, logistics, and construction knowledge, paired with current market information and data.
By strategically reviewing and allocating specialised expertise and structured workstreams, project execution can be streamlined, and the risk of bottlenecks or inefficiencies can be mitigated. The creation of stronger data and fostering a culture of positive collaboration to achieve success is a key advantage of this approach. This, combined with project expertise and leadership, can drive optimal outcomes.
Conducting early and comprehensive supply chain analysis is essential to inform the procurement strategy, mitigate project lead time risks and enhance project outcomes.
“Strategic procurement planning... Can ensure optimal resource allocation and risk mitigation.”
Major projects present an opportunity to leverage supply chain purchasing power to enhance operational efficiencies and mitigate later risks, such as material shortages and lead time or budget constraints.
Strategic procurement planning, vendor evaluation and contract negotiations can ensure optimal resource allocation and risk mitigation.
Adopting a portfolio approach to supply chain analysis anticipates the project’s key demands and provides a holistic evaluation of project requirements. Major projects entail significant investments, where they can often influence the local economy and demand for resources. For instance, disaster recovery efforts often involve substantial rebuild spending within urgent time frames, which can stimulate a regional economy to the point of driving up costs for individual businesses.
In contrast, taking a portfolio approach to supply chain management could result in greater certainty in pricing. As an example, consolidating concrete demand requirements to fund a portfolio-level concrete batching or precast manufacturing plant will enable cost certainty for the supply of the entire project’s requirement. However, accountability is often confined to individual package levels and lacks integration across the entire project, hindering the optimisation of purchasing power at the business case stage to secure these outcomes.
Conducting supply chain analysis as part of the set-up phase enables the identification of opportunities for innovation and optimisation, such as modular construction techniques, prefabrication or outsourcing non-core activities.
“Major projects entail significant investments, where they can often influence the local economy and demand for resources.”
Strategically and proactively procuring high-quality resources early in the project lifecycle, even before design confirmation, can streamline project delivery, minimise disruptions and significantly enhance project success.
Major projects demand a unique, tailored approach and a blend of specialist expertise to ensure success. By adopting a comprehensive strategy to align project scope, metrics and requirements, before implementation, organisations can mitigate risks, enhance efficiency and achieve sustainable success in today’s dynamic construction environment.
This article was written by Adrian McLay and Dean Mills from Turner & Townsend.Navigating the maze of employment laws in Australia can be confusing for small businesses that don’t employ Human Resources professionals. This article explores the most important sources of employment law you need to know about, to support you to be legally compliant in relation to your workforce.
The starting point is understanding where our employment laws come from. Three sources of law may apply to a person’s employment:
1. legislation,
2. industrial instruments, and
3. the contract of employment.
Legislation consists of acts and regulations made by the federal parliament and the state or territory parliament in your jurisdiction. The most important examples for national system employers are the Fair Work Act 2009 (Cth) (Fair Work Act) and the Fair Work Regulations 2009. However, employers also have to comply with various state or territory laws in their jurisdiction.
Industrial instruments, such as modern awards and enterprise agreements, are also a form of statutory regulation.
They are made by industrial tribunals such as the Fair Work Commission and set minimum terms about remuneration and working conditions. An employee who is not covered by a modern award or enterprise agreement is sometimes called an award/agreement-free employee.
The contract of employment is the agreement between the employer and the employee. It may consist of terms and conditions that are in writing, oral or implied, or a mix of all three. The common law (judge-made law) contains important legal principles that apply to employment contracts.
An important principle regarding these sources of law is that it is generally unlawful for an employer to provide entitlements less than those required under an applicable award, enterprise agreement or statute.
However, an employer can, such as by a term in a contract or a workplace policy, give an employee more than the statutory minimum; for example, by providing five weeks’ annual leave instead of the usual four weeks. On the other hand, it would be an unlawful arrangement (and unenforceable) to agree to only accrue three weeks of annual leave per annum since it is less than the legal minimum under statute.
By far the most significant legislation in the national employment system is the Fair Work Act, which is currently undergoing significant reform with the Albanese Government’s Closing the Loopholes legislation.
Importantly, the Fair Work Act incorporates the National Employment Standards (NES), which are minimum employment entitlements for all employees in the national employment system, such as maximum ordinary hours of work, flexible working arrangements, casual conversion, provision of fair work information statements, and most types of leave.
As well as containing the NES, the Fair Work Act also:
• defines important terms, such as who is a casual employee
• provides that it is unlawful to contravene a provision of the NES or a term of a modern award or enterprise agreement
• protects defined employees from unfair dismissal
• protects national system employees generally relating to their workplace rights and other protected attributes such as sex or disability
• confers jurisdiction on the Fair Work Commission and the courts to deal with matters under the Fair Work Act.
The above is not an exhaustive list, by any means.
Some of the sections of the Fair Work Act are civil remedy provisions. If such a provision is contravened, the Court can make civil remedy orders against an individual (including a corporation), such as an injunction, an order for the payment of compensation, and reinstatement of a person to their employment.
The Court also has the power to impose a pecuniary penalty order on a person who has contravened a civil remedy provision. This is a monetary fine to deter the person from repeating their contravention and generally to deter others from doing the same thing.
Currently, a corporation that contravenes a civil remedy provision may be liable to pay a maximum pecuniary penalty of AUD 93,900 per contravention. An individual may be liable to pay a maximum pecuniary penalty of AUD 18,780 per contravention.
However, a serious contravention (where the Court finds that the person knew they were contravening the law as part of a systematic pattern of conduct affecting one or more people), attracts a pecuniary penalty as high as AUD 939,000 per contravention.
We can’t overlook other federal legislation that regulates employment.
This includes anti-discrimination statutes such as the Sex Discrimination Act 1984 (Cth), Disability Discrimination Act 1992 (Cth), Racial Discrimination Act 1975 (Cth) and the Age Discrimination Act 2004 (Cth).
It is less well-known that an employer can be found liable for misleading or deceptive conduct relating to employment under the Australian Consumer Law
Employers also need to be aware of numerous state or territory laws that cover employment. These may include laws relating to long service leave, discrimination and harassment, and work health and safety.
It is vital to identify any industrial instruments that cover your business and any of your employees since it is unlawful to contravene a term of a modern award.
A modern award supplements the NES and may set out entitlements such as minimum pay rates, hours of work, overtime, allowances, and more. Modern awards are occupation-based or industry-based. Determining whether a particular employer and employee are covered by a modern award can be a complicated exercise and is sometimes the subject of disputes.
Equally, interpreting award clauses, such as employee classifications, shift provisions and penalty rates, can be a vexing matter and may necessitate getting professional advice.
A common myth is that an award won’t apply if an employee is paid above the minimum award rate of pay. However, there are only limited circumstances where award provisions can be lawfully excluded.
Although written employment agreements are usually not mandated under Australian law, it is sound practice to commit important terms in writing with your employees. The more senior the role, the more critical it is to cover matters such as duties, confidential information, intellectual property, termination of employment, and protection of business interests.
It’s worth having your employment agreements reviewed periodically to ensure they are up-to-date and consistent with legislation and any applicable industrial instrument.
The good news is that you are not alone! Even if you do not employ a dedicated human resource management specialist, consider obtaining the services of a human resources consultancy or specialist employment lawyer.
The Fair Work Ombudsman has information and free resources available on its website and can provide assistance, advice, and guidance for employers and employees.
With the Closing the Loopholes legislation, national system employers are facing a raft of legislative changes in employment law. Ignorance of the law is no excuse and the penalties for contraventions can be severe.
Now is as good a time as any to inform yourself of your legal obligations to your employees and achieve compliance.
This article was written by Adrian Barwick from WilliamsonBarwick.The Australian housing market is currently navigating through a period marked by recessionary pressures, challenging the affordability, availability, and overall economic stability of housing nationwide. Stakeholders from all sectors are looking for innovative approaches to address the increasing gap between supply and demand, rising material prices, and labour constraints. Prefabricated (or ‘prefab’) construction is one such approach that is gaining popularity because of its efficacy, affordability, and sustainability.
This piece examines how prefab construction is a strategic reaction to the downturn in the housing market and has the potential to completely transform the way Australians see house ownership and construction. Prefab construction methods are a viable remedy for the current market downturn. We demonstrate this by investigating recent trends and data, which include a noticeable decline in housing starts and shifts in consumer preferences towards more affordable and sustainable housing options.
The real estate market downturn in Australia is due to a variety of factors, including pressures from local and global economies. According to the Australian Bureau of Statistics (ABS), there has been a notable fall in dwelling starts, with an estimated 15% reduction in only the most recent fiscal year.1 In addition, many Australians find it extremely challenging to get house financing due to banking institutions’ tighter lending rules.
Global economic downturns have made foreign investment in Australia’s real estate market less prevalent, which has accelerated the market’s fall. Meanwhile, due to tariffs and interruptions in global supply chains, the Housing Industry Association reports that material prices have increased by more than 20% in only the last two years. 2 Another significant issue is a lack of labour, with the Department of Jobs and Small Business reporting that the vacancy rate in the construction industry is twice as high as the national average.3
These tendencies have significant repercussions. The rate of home ownership has dropped to its lowest point in decades, which has a particularly adverse impact on young families and first-time buyers. Low- and middle-class families are under additional pressure in the rental market, where vacancy rates are at all-time lows and rental costs are rising.
Because housing has historically been a vital source of economic development, this scenario has not only negatively impacted the quality of life for many Australians, but has also presented severe obstacles to financial stability.
Based on a comparative analysis of past recessions, it is feasible to recover with the right actions. A comparable recession occurred in the early 2000s, and the market bounced back thanks to a variety of governmental initiatives, including interest rate reductions and first-time buyer incentives.
But the present environment, with its unique problems – such as the fallout from the worldwide pandemic – calls for creative solutions that go beyond conventional fiscal and monetary measures.
Prefab construction offers a potential solution to address Australia’s housing shortage since it uses components that are made off-site and assembled on-site. This technique comes in a variety of forms, each with its own advantages in terms of efficiency and customisability, such as panellised structures, pre-cut construction, and modular houses. According to the Modular Building Institute, one major benefit of prefab building is its ability to drastically cut build times by up to 50%, which would help meet the pressing demand for housing supply.4 Furthermore, by reducing waste and maximising labour utilisation, prefab techniques can minimise building costs and increase the financial viability of housing projects.
Around the world, nations like Sweden and Japan have effectively incorporated prefabricated buildings into their housing markets, leading to significant increases in sustainability and affordability. In Sweden, for instance, government regulations encouraging innovation and green building techniques have allowed the
prefab industry to develop to about 84% of the residential construction market. In addition to improving quality and efficiency, Japan’s use of robotics technology and precise engineering in prefab building has increased resilience against natural disasters – a factor that is especially pertinent to Australia.5
“...Prefab has the capacity to effectively alleviate the housing need.”
These global examples provide valuable insight into how to use prefab building to develop more resilient, cost-effective, and environmentally friendly housing markets. They also offer a roadmap that Australia may want to take into consideration and modify to suit its own particular economic and environmental conditions.
Despite its benefits, prefabrication is still relatively new in Australia, where it makes up just 5% of all residential construction projects. Still, the industry is expanding because more people are becoming aware of its advantages and because there is a rising need for sustainable construction methods. Prefab construction is being positively supported by the Australian government, as seen by recent efforts
2 McSweeney, N. 2023, ‘Australian construction material price outlook’, Altus Group, 20 November, <altusgroup.com/insights/australianconstruction-material-price-outlook/>.
3 Australian Bureau of Statistics 2024, Job Vacancies, Australia, ABS, <abs.gov.au/statistics/labour/jobs/job-vacancies-australia/latestrelease>.
4 Modular Building Institute 2023, ‘The rise of modular construction methods’, Utilities One, 3 November, <utilitiesone.com/the-rise-ofmodular-construction-methods>.
5 Sweet, R. 2015, ‘Why Sweden beats the world hands down on prefab housing’ Global Construction Review, 28 May, <globalconstructionreview.com/why-sweden-beats-world-h8an0ds-4d2own0-6p4r2e0f8ab/>.
such as tax incentives for construction technology innovation and subsidies for green building projects.6
Success stories from throughout the country already demonstrate that prefab has the capacity to effectively alleviate the housing need.
For example, a Melbourne-based project used modular construction to finish a 57-unit complex in only 18 days, greatly lowering the time required for construction and labour expenses. But there are still issues to be resolved, such as getting over the industry’s historical mistrust, revising building rules to better allow prefab techniques, and making sure there is a trained staff.
“...Prefab building may save project costs overall by as much as 16%...”
Australia can fully realise the promise of prefab building to not only ease the present housing crisis but also set the standard for creative, sustainable housing solutions by tackling these issues via targeted regulations and industry partnerships.
Prefab building is considerably more affordable than conventional techniques, according to comparative economic research. For example, a University of Melbourne research discovered that prefab building may
save project costs overall by as much as 16%, mostly due to decreased labour expenses and less waste during construction.7 Financial gains may also be realised from time savings because accelerated project completion enables earlier income generating from sales or rents.
Large-scale adoption of prefab construction might have larger economic effects, such as strengthening the building industry, generating employment, and boosting GDP. The integration of prefab construction, especially during downsizing housing projects, offers economic efficiency by optimising resources, minimising waste and simplifying operations. Furthermore, housing may promote social fairness and sustainable urban development by being more accessible and costeffective. However, achieving these advantages will cost capital upfront for training, technology, and regulatory changes.
Prefab construction aligns closely with the Life Cycle Assessment (LCA) approach, which emphasises the importance of considering both environmental and economic impacts throughout the entire life cycle of a building. To move the project forward within a certain budget, it is very easy to shift the emphasis between these two aspects during the design and construction process. However, once completed, a building’s performance is tied to inherent geometries that will exist for decades to come.
“...Legislators, business executives, and the community must work together.”
This makes prefab a natural fit with LCA’s iterative principle of continuous improvement. The efficiency of the prefab construction process reduces waste and minimises embodied energy, and a faster time to completion results in lower energy consumption and greenhouse gas emissions during the construction phase. Public-private partnerships, government-backed finance programmes, and incentives for private investment in prefab manufacturing facilities are some examples of investment methods to promote prefab projects. These kinds of programmes would not only help the housing market in Australia, but they would also encourage competition and innovation in the construction sector.
The key advice for policymakers is to invest in R&D to promote prefab technology, create financial incentives for adopting prefab techniques, and update building rules to facilitate prefab construction. To foster innovation, industry participants should concentrate on expanding their capacity for prefab production, educating their personnel, and cultivating alliances with IT companies.
6 Australian Government 2024, ‘Built environment sector guide for the R&D Tax Incentive’, business.gov.au, 18 January, <business.gov.au/ grants-and-programs/research-and-development-tax-incentive/sector-guides-for-r-and-d-tax-incentive-applicants/built-environment>.
7 Ngo, T. 2023, ‘Transforming pre-fabricated housing for the better’, University of Melbourne, 6 September, <research.unimelb.edu.au/ partnerships/case-studies/transforming-pre-fabricated-housing-for-the-better>.
To increase demand and acceptability, prospective homeowners and investors need to be made aware of the advantages of prefab dwellings, such as their affordability, environmental friendliness, and higher performance.
“A profitable, sustainable future for the Australian housing industry may lie in prefab building investments and strategic government intervention...”
The prefab sector has an optimistic outlook in Australia due to material and technological advances that will only make it more appealing. Prefab houses may be made even more economical, environmentally friendly, and efficient with the use of innovations like 3D printing, smart home technology integration, and the use of sustainable materials. Additionally, prefab construction has the potential to alleviate more general social challenges, including building infrastructure that is disaster-resilient and providing affordable homes for marginalised people.
To fully realise this potential, legislators, business executives, and the community must work together. Australia can address its present housing issues and establish itself as a worldwide leader in creative and sustainable building techniques by adopting prefab construction as a major tactic to combat the housing market downturn.
Prefab construction is not only a revolutionary but also a crucial component of Australia’s housing market recovery plan. Prefab construction’s promises of sustainability, affordability, and efficiency make it an ideal fit with the National Reconstruction Fund’s (NRF) objectives to diversify and reshape the national economy. Making use of the NRF’s guarantees, equity investments, and loans might spur major developments in prefab building, cutting costs and shortening build schedules. Because of this congruence, policymakers have an exceptional opportunity to utilise the NRF as a means of prioritising investments in prefab technologies – especially those that help achieve low-emission and renewable energy objectives. By doing this, the government will be able to assist Australia’s shift to a net-zero economy and meet urgent housing requirements while also cultivating a robust and creative building industry. A profitable, sustainable future for the Australian housing industry may lie in prefab-building investments and strategic government intervention at this critical juncture.
In the ever-evolving landscape of residential construction, the implications of the Home Building Act 1989 (HBA) extend directly to the core responsibilities of quantity surveyors (QSs). Given their pivotal role in cost management and project delivery, QSs must navigate the HBA’s provisions with precision and expertise. This necessity arises from their involvement in preparing contract documents, which must align with the HBA’s licensing, insurance, and contracting requirements to ensure legal compliance and protect project stakeholders.
Quantity surveyors are pivotal in guiding projects through the regulatory landscape set by the HBA. Their expertise in contract documentation, aligned with HBA requirements, safeguards projects from legal disputes and financial penalties, ensuring both compliance and cost certainty. This article elaborates on specific areas of the HBA relevant to the QS, accentuating the Act’s integral role in their professional practice.
The HBA underpins the financial and legal framework within which QSs operate, providing a structured approach to managing project costs and risks associated with residential construction. The Act’s detailed stipulations on contractor licensing, insurance obligations, and contractual conditions form the backbone of the cost planning and contractual advice QSs provide. By ensuring compliance with the HBA, QSs safeguard the projects from potential legal disputes, fines, and work stoppages that can arise from non-compliance, thereby ensuring cost certainty and project viability.
The cornerstone of regulatory compliance within the residential building sector lies in the licensing and insurance obligations mandated by the HBA 1989.
Sections 4 and 5 of the Act underscore the stringent requirements placed upon builders and tradespersons, emphasising the necessity of holding the appropriate licences and maintaining requisite insurance coverage.
This legal framework is vital for QSs, who must verify compliance to protect stakeholders and manage risks associated with residential construction.
Under Section 4 of the HBA 1989, a stark prohibition is established:
“A person must not contract to do any residential building work... Except as or on behalf of an individual, partnership or corporation that is the holder of a contractor licence authorising its holder to contract to do that work.”
This unequivocal statement serves as a deterrent against unlicensed contracting, safeguarding the integrity of the industry.
Moreover, Section 5 reinforces the gravity of non-compliance by outlining penalties for individuals or entities engaging in unlicensed activities. It stipulates that individuals, partnerships, officers of corporations, or corporations themselves cannot represent readiness to undertake residential building work without the requisite contractor licence. Failure to adhere to these provisions can result in penalties of up to 500 penalty units or imprisonment for up to 12 months.
QSs must understand the significant legal and financial consequences of non-compliance (Sections 7, 7AAA and 7E). Non-compliance with the Act’s contracting requirements or contracting to do residential building work while unlicensed can lead to significant legal and financial repercussions:
• The offending party cannot claim damages or enforce any remedy for a contract breach. Section 10 denotes, “a person who contracts to do any residential building work… In contravention of Section 4… Is not entitled to damages or to enforce any other remedy in respect of a breach of the contract committed by the other party to the contract…”
• The contract becomes unenforceable for the party if the party fails to comply.
• A fine of up to AUD 8,800 can be imposed for contracting without meeting the act’s stipulated requirements (Sections 7, 7AAA, and 7E).
Contracting requirements vary depending on the contract value:
1. Contracts not exceeding AUD 5,000 (incl. GST)
2. Contracts over AUD 5,000 but not exceeding AUD 20,000 (incl. GST)
3. Contracts exceeding AUD 20,000 (incl. GST).
Certain situations are exempt from these contracting requirements, including:
• Emergency works where compliance would hinder prompt action necessary for health, safety, or property protection (Section 6(2)).
• Contracts between parties holding relevant Contractor Licenses or contracts for specialist work that is not classified as residential building work (Section 7(8), Section 7AAA(5)).
The HBA’s universal contracting mandates are crucial areas where QSs provide guidance.
The maximum deposit that can be legally demanded or accepted for residential building work is capped at 10% of the contract price. This is stipulated under Section 8 of the Act.
Prohibition on creating interest in land (Section 7D (1)): Contracts cannot create an interest in land; such provisions are void.
Exception for charges related to contract work (Section 7D (3)): Charges over land are valid if they relate to the land where the work is or was to be carried out, and secure payment for the contractor licensed holder as ordered by a Court or Tribunal.
The invalidity of Arbitration Requirement (Section 7C): Any contract clause mandating arbitration for disputes is void.
Mandatory Insurance Requirement (Section 92 (1)): A Contract of Insurance under the Home Building Compensation Fund must be in force before work commences.
Consequences for Non-Compliance (Section 94 (1), (1A)): Contractors without appropriate insurance cannot enforce contract breaches or recover money for work done.
Offence related to unauthorised payments (Section 8A (4)): It is an offence to demand or receive progress payments not authorised by Section 8A (4).
Types of authorised payments (Section 8A (2)): Payments upon completion of specific stages or for labour and materials already provided.
Section 18B of the HBA establishes crucial implied warranties in every contract for residential building work. These warranties are inherent and serve to protect the interests of both parties involved.
The following warranties are automatically implied in residential building contracts:
1. Due Care and Skill: The work will be executed with due care and skill, strictly adhering to the plans and specifications outlined in the contract.
2. Quality of Materials: All materials supplied by the contractor will be of good quality and suitable for their designated purpose. Unless otherwise stated, these materials will be new.
3. Legal Compliance: The work will be conducted in accordance with the HBA and all other relevant laws.
4. Timely Completion: The work will be completed diligently and within the stipulated time frame. If no specific time is mentioned, completion will occur within a reasonable period.
5. Fit for Dwelling Purpose: For projects involving the construction, alteration, or repair of a dwelling, the completed work will result in a dwelling reasonably fit for occupation.
6. Fit for Specified Purpose: The work and associated materials will be reasonably fit for the specified purpose or result. This is contingent upon the owner expressing the purpose or desired outcome explicitly, indicating reliance on the contractor’s skill and judgement.
Applicability in Subcontractor Contracts: Importantly, these warranties extend to contracts between principal contractors and subcontractors engaged in residential building work.
Incorporation of Implied Warranties into Contracts:
• Contractual Considerations: Parties should be cognisant that these warranties are automatically part of the contract, reinforcing the importance of aligning contractual terms with these statutory warranties.
• Potential Implications of Breach: A breach of these warranties may lead to legal consequences and claims for rectification or damages.
Statutory Time Frames: Section 18E of the HBA governs the limitation periods for initiating proceedings related to breaches of statutory warranties in residential building work. It is crucial for the parties involved to understand these time frames to protect their rights.
Two Distinct Periods: Proceedings for a breach of a Statutory Warranty must be initiated within specific time frames, which are as follows:
1. Major Defects: Six years from the completion of the work if the breach results in a major defect in residential building work.
2. Other Cases: Two years from the completion of the work in any other case.
Major Defects: The Act defines a ‘major defect’ as a defect in a major element of a building that causes or is likely to cause severe consequences such as the inability to inhabit the building, destruction of the building, threat of collapse, or as prescribed by regulations.
Major Elements: ‘Major elements’ include essential load-bearing components, fire safety systems, waterproofing, or other elements specified in the regulations.
Commencement of Warranty Period: The warranty period begins upon the completion of the work, or if the work is incomplete, on the termination of the contract, cessation of work, or the contract date.
Determining Completion: Completion is defined by the contract, and if absent, it is deemed to be when the work achieves ‘practical completion’ – ready for its intended purpose with only minor omissions or defects.
Practical Completion Criteria: The Act provides criteria for practical completion, including possession handover, contractor’s last site attendance, issuance of an Occupation Certificate, or, for owner-builder work, 18 months after the Owner-Builder Permit.
Two situations may extend the commencement period:
1. Late Awareness: If the party entitled to the warranty becomes aware of the breach within the last six months of the applicable warranty period, proceedings can be commenced within six months after the warranty period ends.
2. Building Bond: If a building bond is lodged under the Strata Schemes Management Act 2015 (NSW), the two-year period is extended until 90 days after the required final inspection report.
Successor Rights: Successors in title and landowners (not parties to the contract) have the same rights as the original party entitled to the statutory warranty.
Consistency in Enforcement: Enforcement of a warranty for a particular deficiency does not preclude enforcing the same warranty for a different deficiency if brought within the relevant limitation period and the deficiency was unknown during the earlier warranty enforcement.
The HBA’s emphasis on statutory warranties and progress payments underlines the QS’s role in quality assurance and financial management. QSs leverage their expertise to incorporate statutory warranties into contracts, safeguarding client interests and upholding construction standards.
Additionally, their guidance on authorised progress payments ensures transparent and fair financial transactions, pivotal for project cash flow and stakeholder protection. Thus, the HBA is instrumental in enabling QSs to deliver their services effectively, contributing to the integrity, quality, and success of residential construction projects. Through their compliance with and application of the HBA, QSs play a vital role in promoting a culture of excellence and trust within the construction industry.
• Consumer Building Guide Requirement (Section 7AA (1)): Contractors must provide the Consumer Building Guide March 2020 before contract formation.
• Written Contract Mandate (Section 7 (1)) and Specific Content Requirements (Sections 7 (2), 7 (4), 7 (5)): Contracts must be in writing, dated, signed, and contain specific information.
• Inclusion of Checklist and Mandatory Terms (Section 7 (3), 7E (1)): A checklist from the Home Building Regulation 2014 and terms from Schedule 2 of the Act are mandatory.
• Cooling Off Period and Rights (Section 7BB (2)): Contracts must contain a statement about the cooling off period, with rights to rescind under certain conditions.
• Provision for Progress Payments (Section 8A): Contracts must include provisions for authorised progressive payments.
• Delivery of Contract Copy (Section 7B): A signed contract copy must be provided within five business days after the contract is entered into.
• Written Contract Requirement (Section 7aaa (2)): Written contracts are obligatory, along with date and signature requirements.
• Content Requirements (7AAA (3)): Contracts must include specific details such as parties’ names, Contractor Licence number, work description, and contract price if known.
• Consumer Guide Inclusion (Section 7AAA(4), Regulation 6): Inclusion of the Consumer Building Guide March 2015 is compulsory.
• Absence of stringent requirements: No prescribed contracting requirements, but Australian Consumer Guarantees apply.
• Recommendations for Contractual Clarity: Written contracts are recommended to avoid disputes, encompass important terms, and limit or exclude liability for consequential losses.
• Variation management: Documenting and signing any variations in written form is advised to prevent disputes related to scope changes and associated costs.
QSs utilise their understanding of the HBA to:
• Ensure that all contractual documents adhere to HBA requirements, offering legal and financial protection to construction projects.
• Advise on and manage compliance with licensing and insurance obligations, crucial for mitigating risk.
• Navigate statutory warranties and progress payment regulations, ensuring quality standards and fair financial practices are held.
The HBA is more than regulatory legislation for quantity surveyors working within New South Wales’ residential construction sector. It is a foundational element that influences their approach to cost management, risk assessment, and contract administration. Through a comprehensive understanding of the HBA, QSs ensure projects not only comply with the law but also meet the highest standards of quality and financial integrity. Thus, the HBA is indispensable in promoting a culture of excellence and trust within the construction industry, underpinning the professional practices that transform houses into safe, reliable homes built to last.
THE BUILDING COST INDEX IS PUBLISHED IN THE PRINT VERSION OF THE BUILT ENVIRONMENT ECONOMIST.
IT CONTAINS DATA THAT CAN BE USED AS A PREDICTOR FOR THE ESTIMATED TIMES FOR DESIGN AND CONSTRUCTION AND INCLUDES A SUMMARY OF THE PAST, PRESENT AND ESTIMATED FUTURE CONSTRUCTION COSTS.