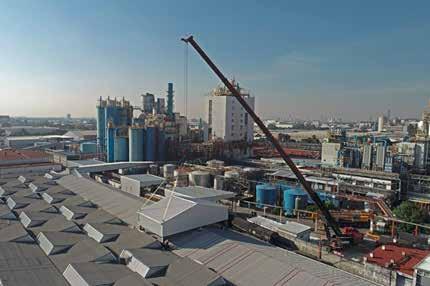
5 minute read
Dupont y P&G juntos por la economía circular del agua
from AGUAS LATINOAMÉRICA
Procter & Gamble reusará 5.000 millones de litros de agua para el 2030
La megaempresa de productos de consumo masivo tiene como meta reusar cinco mil millones de litros de agua al año para 2030 y para ello consultaron al mercado sobre la tecnología de vanguardia. Compartieron con las audiencias de ALADYR el paso a paso de esta ambición de sustentabilidad.
Advertisement
Procter & Gamble es un gigante de productos de consumo masivo y su planta de detergentes de Vallejo en Ciudad de México es la más grande que tiene la compañía para producir este insumo. En 2009 se dispusieron a reducir la huella hídrica de cada producto en un 20%, meta que alcanzó con relativa rapidez, pero sus iniciativas de eficiencia hídrica van más allá. Para 2030 esperan aumentar su eficiencia hídrica en un 35% y generar al menos 5 mil millones de litros de agua al año partir de fuentes circulares. Hugo Ruiz, director de ingeniería de detergentes para América Latina le dijo a ALADYR que para lograrlo, él lideró un grupo encargado de captar la tecnología de vanguardia en el mercado. “Si ahorita, del 100% del agua que entra a la planta sólo el 40% se queda en el producto y el otro 60% se desperdicia, la meta es que un 75% o un 80% del recurso que usamos se vaya directo en el producto” lo que supondría mayor cantidad de detergente por litro de agua empleado. A manera de referencia mencionó que en la elaboración del detergente en polvo se usan torres de evaporación porque su constitución inicial es una pasta con una humedad promedio del 30% cuya agua termina yéndose a la atmósfera. Entonces, parte de lo que busca la empresa es cómo recuperar esa agua evaporada o cómo reducir la humedad en su estado inicial. “El reto de recuperar los 5 mil millones de litros año es el mayor. A la planta de Vallejo, por ser tan grande, le corresponde recircular unos 1500 aproximadamente”.
La ruta a las metas
El primer paso de P&G para establecer y superar sus metas de eficiencia hídrica es el mapeo para entender el consumo del recurso. Para ello se emplean las 6W2H, que consiste en preguntarse a dónde se va el agua, quién la utiliza, cómo lo hace, qué cantidad, cuándo y por qué. “Hay que comenzar por las piedritas. La sostenibilidad no se trata sólo de grandes inversiones sino de saber cómo se emplean los recursos” dice Ruiz. En su opinión esto es algo que cualquiera puede hacer sin necesidad de llenar de sensores la planta: “Se trata de agua y flujos, sólo hay que calcular para tener un acercamiento bastante real”. “Debes inspeccionar cada uno de tus equipos desde el suministro hasta la descarga e ir colocando cada bloque como una unidad individual” agrega Erik Cañamar, líder de arranque para proyectos de agua en la planta de Vallejo. El segundo paso tiene que ver con las condiciones básicas y consiste en diagnosticar los sistemas en busca de fugas e ineficiencias y obsolescencias. “Se trata de hacer seguimientos y trakear el agua” agrega. El tercer punto tiene que ver con los expertos y para ello se acercaron a los líderes del mercado en tecnologías de agua y explicarle sobre sus condiciones, procesos y necesidades para poder obtener una asesoría completa. La mayor parte del suministro de agua de la planta proviene de un pozo que es pasado por proceso de ósmosis inversa (OI) para ser empleada como agua de producto. Antes de aplicar las 6W2H los técnicos pensaban que las mayores pérdidas estaban en la evaporación para los detergentes en polvo o en el lavado y limpieza para los detergentes líquidos pero luego
identificaron el rechazo de OI como la mayor oportunidad de reúso. Según informaron, no se hacía más que donar el efluente de la OI al Gobierno pero luego que se dispusieron a hacer reúso contactaron a una de las compañías de Dupont, empresa socia ALADYR, para que los ayudara a integrar la economía circular a su gestión hídrica.
Proceso de reúso La solución para revalorizar el rechazo de la ósmosis inversa consistió en determinar su calidad y solicitar el diseño a Dupont y se instaló un sistema de pretratamiento de filtros multimedia con una etapa de suavizado para que vuelva a pasar por la OI. El resultado fue un agua de alta calidad y muy baja conductividad que les permitió reintegrar el recurso al proceso de producción. “El equipo tiene una eficiencia mucho más confiable que tener dos o tres ósmosis en serie y nos está funcionando bien tanto en Brasil como en Vallejo” añadió Cañamar. Para los siguientes años se enfocarán en la recuperación a partir de torres de secado, calderas y lubricación de equipos que usan agua. Para esto las plantas de P&G asumirán diferentes tareas experimentales para luego validados los procesos y tecnologías, se integren en el resto de las plantas.
Preguntas y respuestas la calidad del agua alimentación para no tener tal incremento. ¿Con qué calidad de agua iniciaban como agua cruda y con qué calidad terminaban? Es decir TDS inicial y final. Vemos la calidad en términos de conductividad. La de entrada está entre los 5 mil y 6 mil microsiemens y a la salida de todo el proceso sale en 500. ¿Qué concentración de sílice manejan? Eso es lo que más padecemos. Llega a ser bastante alta en el concentrado de rechazo de la ósmosis con 250 a 300 partes por millón. A la salida del permeado sale a 10 o 20 partes por millón. ¿Con qué equipos están midiendo la calidad del agua para asegurar su retorno? Estamos usando un equipo que se llama DR900. Medimos la mayor cantidad de parámetros que podemos como cloro, ph, conductividad, hierro dureza y tenemos otros sensores en línea. Si la ósmosis detecta un ph muy alto se detiene para evitar daños. ¿En qué tiempo hacen el recambio de membrana de ósmosis? En Brasil lo están haciendo cada seis meses con una extensión de cada caño. En nuestro caso como nuestra calidad de agua es un poco peor es cada tres o cuatro meses pero igual le estamos tratando de hacer una extensión.
¿Han tenido problemas por la concentración de sales en la ósmosis inversa? ¿Han tenido que incrementar la frecuencia en las limpiezas químicas? No hemos tenido problemas. De hecho, los últimos analíticos para descarga industrial han salido bien. No hemos tenido alteraciones en la frecuencia de las limpiezas químicas para la OI. Sí debemos cuidar
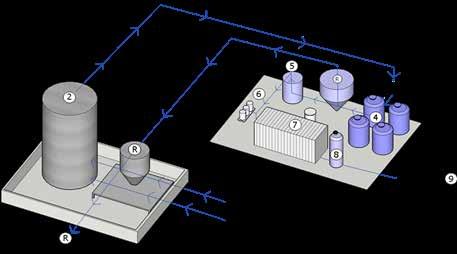